논문 요약: 고압 다이캐스팅 공정에서 제품 품질에 미치는 금형 온도 영향에 대한 실험적 및 이론적 연구
본 문서는 "Experimental and Theoretical Studies on the Effect of Die Temperature on the Quality of the Products in High-Pressure Die-Casting Process" 논문을 요약한 내용 입니다.
1. 개요:
- 제목: 고압 다이캐스팅 공정에서 제품 품질에 미치는 금형 온도 영향에 대한 실험적 및 이론적 연구 (xperimental and Theoretical Studies on the Effect of Die Temperature on the Quality of the Products in High-Pressure Die-Casting Process)
- 저자: Mohammad Sadeghi, Jafar Mahmoudi
- 발행 연도: 2012년
- 발행 학술지/학회: Advances in Materials Science and Engineering
- Keywords:
- 금형 온도 (Die temperature)
- 고압 다이캐스팅 (High-pressure die-casting, HPDC)
- A380 합금 (A380 alloy)
- 수치 시뮬레이션 (Numerical simulation)
- 실험적 관찰 (Experimental observation)
- ProCAST 소프트웨어 (ProCAST software)
- 래더 프레임 (Ladder frame)
2. 연구 배경:
- 사회적/학문적 맥락:
- 고압 다이캐스팅(HPDC) 공정은 높은 치수 정확도와 생산성으로 다양한 제품을 제조하는 데 널리 사용됩니다.
- HPDC는 다른 방법에 비해 생산 속도가 훨씬 빠르며 표면 조도가 낮고 치수 정확도가 높은 부품 생산에 경제적이고 효율적인 방법입니다.
- 주요 알루미늄 자동차 부품은 이 기술로 가공할 수 있습니다 [1-7].
- HPDC는 다른 금속 성형 공정보다 속도가 훨씬 빠르지만, 공정의 복잡성과 변수의 수로 인해 공정 최적화가 필수적입니다.
- 특히, 다음과 관련된 문제가 있습니다:
- 금형 온도 제어
- 부품의 응고
- 주조품 품질 관리
- 일관되고 통합된 시스템 개발 또는 사용
- 다이캐스팅 제품의 기계적 특성은 주로 다음 요소와 관련이 있습니다:
- 금형 온도
- 게이트에서의 금속 속도
- 인가된 주조 압력 [4]
- 주조 부품의 무결성은 다음의 조합에 의해 영향을 받습니다:
- 금형 온도
- 용융 금속의 유동성
- 부품의 기하학적 복잡성
- 다이캐스팅 중 냉각 속도
- 작동 중 금형의 열 프로파일은 고품질 부품 생산에 또 다른 중요한 요소입니다.
- 금형 온도가 너무 높으면 응고 시간이 길어져 사이클 시간이 연장됩니다.
- 금형이 너무 차가우면 표면 결함이 발생할 수 있습니다 [3, 8, 9].
- 기존 연구의 한계점:
- 이러한 연구의 대부분에서 부품의 형상이 단순하고 산업 현장에서 매우 복잡한 부품에 대한 연구는 거의 없습니다.
- 연구의 필요성:
- 본 연구의 목표는 시뮬레이션을 통해 복잡한 자동차 부품인 래더 프레임의 다이캐스팅 공정 변수를 최적화하는 것입니다.
3. 연구 목적 및 연구 질문:
- 연구 목적:
- 실험적 관찰 및 수치 시뮬레이션을 통해 A380 합금의 고압 다이캐스팅에서 금형 온도를 최적화합니다.
- 핵심 연구 질문:
- 고압 다이캐스팅 공정에서 제품 품질에 미치는 금형 온도의 영향은 무엇입니까?
- 이 합금에 적합한 금형 온도는 무엇입니까?
- 연구 가설:
- 이 합금에 적합한 금형 온도는 200°C 이상인 것으로 나타났습니다.
4. 연구 방법론:
- 연구 설계:
- 실험적 관찰과 수치 시뮬레이션의 조합.
- 금형 온도 및 용융 금속 온도에 대한 실험적 측정.
- ProCAST 소프트웨어를 사용한 수치 시뮬레이션.
- 실험적 측정을 통한 시뮬레이션 결과 검증.
- 데이터 수집 방법:
- 실험 데이터:
- 초기 단계와 최종 충전 위치에서 금형 온도를 측정했습니다.
- 이러한 값의 차이를 계산했습니다.
- 다이 표면에서 열전대 및 레이저 고온계(모델 chy 110)로 용융 금속 온도를 측정했습니다.
- "150°C, 200°C, 250°C"의 금형 온도에서 실험을 수행했습니다.
- 시뮬레이션 데이터:
- ProCAST 소프트웨어를 사용하여 유체 흐름 및 부품 응고 단계를 시뮬레이션했습니다.
- 합금의 재료 속성은 소프트웨어 데이터베이스에서 추출하여 표 1에 표시했습니다.
- 시뮬레이션에 사용된 초기 및 경계 조건은 표 2에 나와 있습니다.
- 실험 데이터:
- 분석 방법:
- 수치 시뮬레이션:
- ProCAST 소프트웨어를 사용하여 질량 보존, 운동량 보존 및 에너지 보존(엔탈피 공식)에 대한 지배 방정식을 풀었습니다.
- 자유 표면 모델링은 스칼라 변수 Φ를 사용하여 달성했습니다.
- 결과가 메쉬에 독립적인지 확인하기 위해 서로 다른 두 가지 메쉬 크기를 사용하고 시뮬레이션 결과를 비교했습니다.
- 실험적 검증:
- 결과는 실험적 측정을 통해 검증되었습니다.
- 수치 시뮬레이션:
- 연구 대상 및 범위:
- 재료: A380 재료.
- 부품 형상: 매우 복잡한 형상의 래더 프레임(새로운 모터 EF7의 부품 중 하나)(그림 1).
- 공정: 고압 다이캐스팅(HPDC).
- 금형 온도: "150°C, 200°C, 250°C".
- 용융 금속 온도: 래더 프레임에 대해 "680°C"의 초기 용융 금속 온도, "3m/s"의 샷 슬리브 속도, "55m/s"의 게이트 용융 속도를 가정했습니다.
- 기계: IDRA1600 다이캐스팅 기계.
5. 주요 연구 결과:
- 핵심 연구 결과:
- 이 합금에 적합한 금형 온도는 200°C 이상인 것으로 나타났습니다.
- "150°C"의 금형 온도에서 소프트웨어에서 예측한 최종 충전 위치에서 냉각 유동 표면 결함이 발생합니다(그림 5).
- 최종 응고 위치에서 수축 결함이 발생했으며, 이는 소프트웨어에서 예측한 것입니다(그림 12).
- 검증된 모델은 주조품에서 다공성 결함의 정확한 위치를 흥미롭게 나타냈습니다.
- 통계적/정성적 분석 결과:
- 용융 금속 온도 변화:
- 결과는 금형 온도가 "150~250°C"로 변하는 반면, 용융 금속 온도는 "660°C~680°C" 사이에서 변하는 것으로 나타났습니다(그림 2).
- 표 3은 샷 슬리브의 초기 주입 시 용융 금속 온도와 최종 충전 위치의 최종 주입 시 용융 금속 온도를 보여줍니다.
- 금형 온도 "150°C"에서 초기 주입 시 용융 금속 온도 °C는 "670, 669, 671"이었고 최종 주입 시 용융 금속 온도 °C는 "650, 649, 652"였습니다.
- 금형 온도 "200°C"에서 초기 주입 시 용융 금속 온도 °C는 "675, 676, 674"이었고 최종 주입 시 용융 금속 온도 °C는 "664, 666, 663"이었습니다.
- 금형 온도 "250°C"에서 초기 주입 시 용융 금속 온도 °C는 "679, 680, 679"이었고 최종 주입 시 용융 금속 온도 °C는 "671, 670, 668"이었습니다.
- 용융 금속 온도 감소:
- 초기 및 최종 공정에서 "250°C, 200°C, 150°C에서 두 용융 금속 온도 곡선의 차이는 각각 9.5°C, 10°C, 19.5°C입니다"(그림 3).
- 결함 관찰:
- 그림 5는 "150°C"의 금형 온도에서 생산된 부품에서 냉각 유동 표면 결함의 일반적인 예를 보여줍니다.
- 금속 주입 중 갇힌 공기로 인한 가스 기공이 그림 7에 나와 있습니다.
- 최종 응고 위치에서 수축 결함이 발생했으며, 이는 그림 12에 나와 있습니다.
- 용융 금속 온도 변화:
- 데이터 해석:
- 최종 주입 곡선에는 "200°C"의 금형 온도에서 분기점이 있습니다.
- 결함은 "200°C" 미만의 금형 온도에서 발생할 가능성이 더 높습니다.
- 이 분기점을 고려할 때 이 합금의 정상 금형 온도는 "200°C"인 것으로 볼 수 있습니다.
- 최대 온도는 특정 부품 생산을 위한 금형 냉각 시스템 및 최적화된 사이클 시간에 따라 달라집니다.
- 실험 및 시뮬레이션 결과를 비교하면 부품의 결함이 시뮬레이션에서 예측한 위치에 있는 것으로 나타났습니다.
- Figure Name List:
- FIGURE 1: 래더 프레임 제품의 형상.
- FIGURE 2: 금형 입구 및 초기 주입 시 용융 금속 온도 대 금형 온도.
- FIGURE 3: 금형 말단 및 최종 주입 시 용융 금속 온도 대 금형 온도.
- FIGURE 4: 초기 및 최종 주입 시 다양한 금형 온도에서 용융 금속 온도 감소.
- FIGURE 5: 최종 충전 위치에서 냉각 유동 표면 결함.
- FIGURE 6: 금형에 추가된 오버플로 위치.
- FIGURE 7: 일부 다공성 결함.
- FIGURE 8: 게이트 전면의 세 개 구멍에서 용융 금속의 속도 벡터.
- FIGURE 9: 용융 금속으로 채워진 단계 및 최종 지점 표시.
- FIGURE 10: 동일 시간에서 금형 온도 (a) 150°C 및 (b) 250°C에서 용융 금속의 유동 패턴. 시간 al = b1, a2 = b2, a3 = b3.
- FIGURE 11: 주조 결함에 취약한 응고 단계 말기의 핫스팟.
- FIGURE 12: 최종 응고 위치에서 발생한 결함.
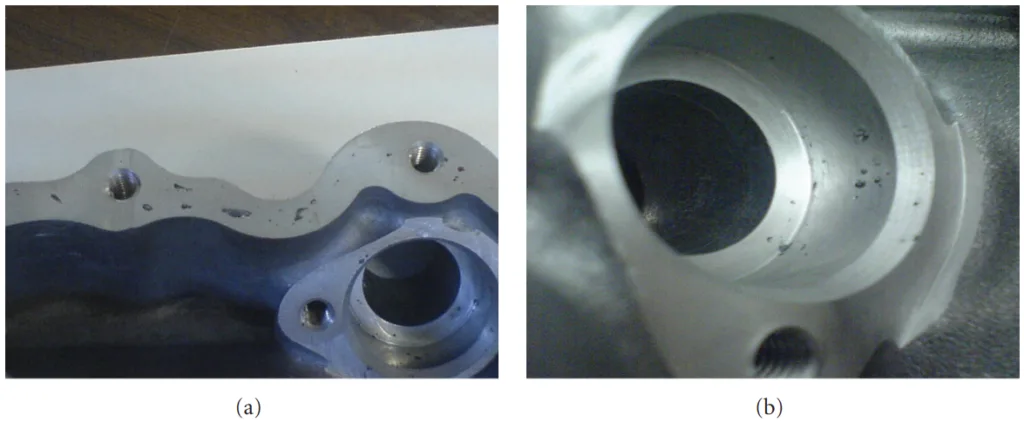
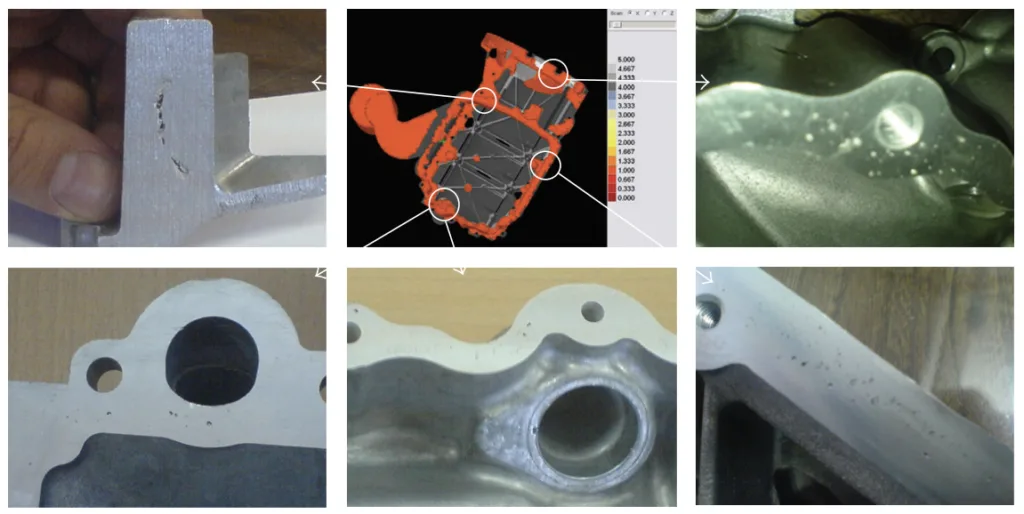
6. 결론 및 논의:
- 주요 결과 요약:
- 실험 및 시뮬레이션 결과를 비교하면 부품의 결함이 시뮬레이션에서 예측한 위치에 있는 것으로 나타났습니다.
- H13 금형 재료에 대한 A380 합금의 최적 금형 온도는 약 "200°C"입니다.
- 금형 온도를 최적 온도 범위에서 낮추면 냉각 유동 결함 및 기공 발생 가능성이 높아집니다.
- 시뮬레이션을 통해 최적화된 오버플로 위치를 결정함으로써 냉각 쇼트 및 기공과 같은 일부 주조 결함을 줄일 수 있었습니다.
- 학술적 의의:
- 본 연구는 A380 합금의 고압 다이캐스팅에 대한 최적 금형 온도를 실험적 및 이론적으로 결정했습니다.
- 본 연구는 고품질 다이캐스팅 제품을 얻는 데 금형 온도 제어의 중요성을 강조합니다.
- 수치 시뮬레이션(ProCAST 소프트웨어)의 사용은 다이캐스팅 공정을 최적화하고 결함 위치를 예측하는 효과적인 도구로 검증되었습니다.
- 실무적 시사점:
- HPDC에서 A380 합금 및 H13 금형 재료를 사용하여 부품을 제조하는 경우 결함을 최소화하고 제품 품질을 보장하기 위해 약 "200°C"의 금형 온도를 유지하는 것이 좋습니다.
- 본 연구 결과는 다이캐스터가 특히 200°C 미만의 금형 온도를 사용할 때 냉각 유동 결함 및 기공을 방지하기 위해 금형 온도를 신중하게 제어하고 모니터링해야 함을 시사합니다.
- 수치 시뮬레이션을 사용하여 다이 설계 및 공정 변수를 최적화할 수 있으며, 특히 결함을 완화하기 위해 오버플로의 효과적인 위치를 결정하는 데 사용할 수 있습니다.
- 연구의 한계점:
- 본 연구는 특정 합금(A380) 및 부품 형상(래더 프레임)에 초점을 맞추었습니다.
- 최적 금형 온도는 합금, 금형 재료 및 부품 설계에 따라 다를 수 있습니다.
- 다른 공정 변수 및 금형 냉각 시스템 설계의 영향력을 조사하기 위해 추가 연구가 필요할 수 있습니다.
7. 향후 후속 연구:
- 후속 연구 방향:
- HPDC에서 다른 알루미늄 합금 및 다양한 부품 형상에 대한 금형 온도의 영향을 조사하기 위해 추가 연구를 권장합니다.
- 균일한 금형 온도를 유지하고 사이클 시간을 개선하기 위해 금형 냉각 시스템 최적화를 탐색할 수 있습니다.
- 추가 연구에서는 금형 온도와 함께 주입 속도 및 압력과 같은 다른 공정 변수의 영향을 조사할 수 있습니다.
- 추가 탐구가 필요한 영역:
- 최적 금형 온도에 대한 다양한 금형 재료의 영향 조사.
- 다른 유형의 주조 결함을 예측하고 완화하기 위한 고급 시뮬레이션 기술 탐색.
- HPDC에서 금형 온도, 사이클 시간 및 제품 품질 간의 최적 균형을 결정하기 위한 경제성 분석 수행.
8. 참고문헌:
- [1] M. S. Dargusch, G. Dour, N. Schauer, C. M. Dinnis, and G. Savage, "The influence of pressure during solidification of high pressure die cast aluminium telecommunications components," Journal of Materials Processing Technology, vol. 180, no. 1-3, pp. 37-43, 2006.
- [2] Z. W. Chen and M. Z. Jahedi, "Die erosion and its effect on soldering formation in high pressure die casting of aluminium alloys," Materials and Design, vol. 20, no. 6, pp. 303-309, 1999.
- [3] P. W. Cleary, J. Ha, M. Prakash, and T. Nguyen, "3D SPH flow predictions and validation for high pressure die casting of automotive components," Applied Mathematical Modelling, vol. 30, no. 11, pp. 1406-1427, 2006.
- [4] K. J. Laws, B. Gun, and M. Ferry, "Effect of die-casting parameters on the production of high quality bulk metallic glass samples," Materials Science and Engineering A, vol. 425, no. 1-2, pp. 114-120, 2006.
- [5] D. McBride, T. N. Croft, and M. Cross, "A coupled finite volume method for the computational modelling of mould filling in very complex geometries," Computers & Fluids, vol. 37, no. 2, pp. 170–180, 2008.
- [6] C. C. Tai and J. C. Lin, “The optimal position for the injection gate of a die-casting die," Journal of Materials Processing Technology, vol. 86, no. 1-3, pp. 87–100, 1998.
- [7] S. W. Youn, C. G. Kang, and P. K. Seo, "Thermal fluid/solidification analysis of automobile part by horizontal squeeze casting process and experimental evaluation," Journal of Materials Processing Technology, vol. 146, no. 3, pp. 294-302, 2004.
- [8] J. X. Zhou, L. L. Chen, D. M. Liao, and R. X. Liu, "High pressure diecasting module of InteCAST software and its applications," Journal of Materials Processing Technology, vol. 192-193, pp. 249-254, 2007.
- [9] S. Yue, G. Wang, F. Yin, Y. Wang, and J. Yang, “Application of an integrated CAD/CAE/CAM system for die casting dies," Journal of Materials Processing Technology, vol. 139, no. 1-3, pp. 465-468, 2003.
- [10] A. Kermanpur, S. Mahmoudi, and A. Hajipour, "Numerical simulation of metal flow and solidification in the multi-cavity casting moulds of automotive components," Journal of Materials Processing Technology, vol. 206, no. 1-3, pp. 62-68, 2008.
- [11] S. Schneiderbauer, S. Pirker, C. Chimani, and R. Kretz, "Studies on flow characteristics at high-pressure die-casting," in Proceedings of the 3rd International Conference on Advances in Solidification Processes.
- [12] M. F. V. T. Pereira, M. Williams, and W. B. du Preez, "Reducing non value adding aluminium alloy in production of parts through high pressure die casting," in Proceedings of the Light Metals Conference, 2010.
- [13] J. K. Rai, A. M. Lajimi, and P. Xirouchakis, "An intelligent system for predicting HPDC process variables in interactive environment," Journal of Materials Processing Technology, vol. 203, no. 1-3, pp. 72-79, 2008.
- [14] B. S. Sung and I. S. Kim, "The molding analysis of automobile parts using the die-casting system," Journal of Materials Processing Technology, vol. 201, pp. 635-639, 2008.
- [15] V. Ilotte, "Die casting for chassis components," in Proceedings of the 4th International High Tech Die Casting Conference, Montichiari, Italy, April 2008.
- [16] Z. Brown, C. Barnes, J. Bigelow, and U. S. Contech, "Squeeze cast automotive applications and design considerations," in Proceedings of the 4th International High Tech Die Casting Conference, Montichiari, Italy, April 2008.
- [17] J. P. Papai, Contact heat transfer coefficients in aluminum alloy die casting: an experimental and numerical investigation? [Ph.D. thesis], The Ohio State University, 1994.
9. 저작권:
- 본 자료는 Mohammad Sadeghi 및 Jafar Mahmoudi의 논문: "Experimental and Theoretical Studies on the Effect of Die Temperature on the Quality of the Products in High-Pressure Die-Casting Process"를 기반으로 작성되었습니다.
- 논문 출처: https://doi.org/10.1155/2012/434605
본 자료는 위 논문을 바탕으로 요약 작성되었으며, 상업적 목적으로 무단 사용이 금지됩니다.
Copyright © 2025 CASTMAN. All rights reserved.