1. 개요:
- 제목: 고압 다이캐스팅을 이용한 알루미늄 중공 서브프레임 개발(Development of Aluminium Hollow Subframe Using High-Pressure Die Casting)
- 저자:
- 아키히코 아사미 (Akihiko Asami)
- 토모유키 이마니시 (Tomoyuki Imanishi)
- 유키오 오카자키 (Yukio Okazaki)
- 토모히로 오노 (Tomohiro Ono)
- 켄이치 테츠카 (Kenichi Tetsuka)
- 발행 연도: 2016년
- 발행 학술지/학회: SAE 기술 논문 (SAE Technical Paper)
- Keywords:
- 고압 다이캐스팅 (High-Pressure Die Casting, HPDC)
- 알루미늄 중공 서브프레임 (Aluminium Hollow Subframe)
- 경량화 (Weight Saving)
- 사형 주조 코어 (Sand Core)
- Al-Mg-Si 합금 (Al-Mg-Si Alloy)
- 박육 부품 (Thin-walled Parts)
2. 연구 배경:
- 연구 주제의 사회적/학문적 맥락:
- 자동차 경량화에 대한 요구는 탄소 배출 감소 및 에너지 절약을 통해 지구 환경 보호에 기여하기 위해 증가하고 있습니다.
- 경량화는 또한 연비 향상 및 차량의 동적 성능 향상에도 기여합니다.
- 고장력 강판과 경량 알루미늄은 자동차 서브프레임의 경량화를 달성하기 위해 사용되는 재료입니다.
- 폐쇄 단면 구조는 개방 단면 구조에 비해 부품 강성을 효율적으로 높이기 위해 일반적으로 사용됩니다.
- 알루미늄 중공 서브프레임은 이미 실용화되었으며, 사형 주조 코어를 사용하여 중력 다이캐스팅 (Gravity Die Casting, GDC) 또는 저압 다이캐스팅 (Low-Pressure Die Casting, LPDC) 공정으로 제조됩니다.
- 기존 연구의 한계점:
- 사형 주조 코어를 사용하는 기존의 알루미늄 중공 주조 방식인 GDC 또는 LPDC는 제품 두께를 줄이는 데 한계가 있습니다.
- GDC 또는 LPDC에서 두께가 감소하면 주조 중 알루미늄 용탕의 유속이 감소합니다. 금형과 사형 주조 코어가 알루미늄 용탕에서 열을 빼앗아 알루미늄이 응고되는 경향이 있습니다.
- GDC 및 LPDC의 이러한 두께 감소의 한계는 상당한 경량화 달성을 방해합니다.
- 용접 알루미늄 서브프레임과 관련된 높은 비용 (재료비, 금형비, 용접비 포함)은 광범위한 채택을 방해합니다.
- 연구의 필요성:
- 기존 방법의 한계를 극복하고 차량 중량을 더욱 줄이기 위해 경량 박육 알루미늄 중공 서브프레임을 생산할 수 있는 제조 방법이 필요합니다.
- 대형 코어를 성형하고 우수한 유동 성능을 나타내는 재료를 개발하는 기술이 이 기술을 실현하는 데 필수적입니다.
3. 연구 목적 및 연구 질문:
- 연구 목적:
- 박육화에 적합한 제조 방법인 고압 다이캐스팅 (HPDC)을 사용하여 경량 중공 서브프레임 기술을 개발합니다.
- HPDC 조건에 맞춰 압력 저항과 붕괴성을 균형 있게 유지하는 사형 주조 코어 기술을 개발하여 서브프레임과 같은 대형 부품의 중공 주조를 가능하게 합니다.
- 비용을 절감하면서 서브프레임에 적합한 주조성 및 기계적 특성을 보장하기 위해 비열처리 Al-Mg-Si 합금을 사용합니다.
- 핵심 연구 질문:
- 최적화된 사형 주조 코어 기술 및 재료 선택과 결합된 HPDC는 기존 강철 서브프레임에 비해 상당한 경량화를 달성하면서 필요한 구조적 무결성 및 성능을 유지하는 박육 알루미늄 중공 서브프레임을 효과적으로 생산할 수 있을까요?
- 연구 가설:
- 새롭게 개발된 사형 주조 코어 기술과 최적화된 비열처리 Al-Mg-Si 합금을 HPDC와 함께 사용하면 구조적 성능을 저하시키지 않으면서 기존 용접 강판 서브프레임보다 훨씬 가벼운 중공 알루미늄 서브프레임을 제조할 수 있습니다.
4. 연구 방법론
- 연구 설계:
- 본 연구는 HPDC를 사용한 알루미늄 중공 서브프레임의 새로운 제조 공정 개발 및 실험적 검증에 초점을 맞추었습니다.
- 연구에는 양산 서브프레임의 형상을 기반으로 중공 알루미늄 서브프레임용 제품 금형 및 코어 금형을 설계하고 제조하는 과정이 포함되었습니다.
- 개발된 중공 알루미늄 서브프레임의 성능을 정적 파괴 시험 및 내구성 시험을 통해 기존 강철 서브프레임과 비교했습니다.
- 데이터 수집 방법:
- 주조 실험: 다양한 주조 조건, 사형 주조 코어 재료, 베이킹 조건 및 Al-Mg-Si 합금 조성으로 HPDC 실험을 수행했습니다.
- 기계적 특성 시험:
- 인장 시험을 수행하여 Si 함량을 달리한 개발된 Al-Mg-Si 합금의 강도와 연신율을 평가했습니다.
- 정적 파괴 시험 및 내구성 시험을 제조된 중공 다이캐스트 알루미늄 서브프레임에 수행하여 실제 차량 입력 조건을 시뮬레이션하는 조건에서 구조적 성능을 평가했습니다.
- 치수 정확도 측정: 주조 제품의 치수 정확도를 평가하여 코어 고정 방법 및 용탕 흐름 최적화의 효과를 평가했습니다.
- 분석 방법:
- 기계적 특성 분석: 인장 시험, 정적 파괴 시험 및 내구성 시험 결과를 분석하여 개발된 재료 및 서브프레임의 기계적 성능을 평가했습니다.
- 비교 분석: 개발된 중공 알루미늄 서브프레임의 중량 및 성능을 기존 강철 서브프레임과 비교하여 경량화 및 성능 특성을 정량화했습니다.
- 공정 변수 최적화: 주조 조건, 사형 주조 코어 변수 및 합금 조성이 주조 서브프레임의 품질 및 성능에 미치는 영향을 분석하여 제조 공정을 최적화했습니다.
- 연구 대상 및 범위:
- 본 연구는 자동차용 알루미늄 중공 서브프레임 개발에 초점을 맞추었습니다.
- 범위는 다음을 포함합니다:
- HPDC에 적합한 사형 주조 코어 기술 개발.
- HPDC 중공 주조를 위한 비열처리 Al-Mg-Si 합금의 재료 선택 및 최적화.
- 중공 서브프레임의 HPDC용 금형 설계 및 제조.
- 정적 파괴 및 내구성 시험을 통한 개발된 서브프레임의 기계적 성능에 대한 실험적 검증.
- 중량 및 성능 측면에서 개발된 알루미늄 서브프레임과 기존 강철 서브프레임의 비교.
5. 주요 연구 결과:
- 핵심 연구 결과:
- 대형 박육 부품을 위한 HPDC를 이용한 경량 중공 서브프레임 기술이 성공적으로 개발되었습니다.
- HPDC에 적합한 사형 주조 코어 기술이 확립되어 사형 주조 코어의 압력 저항과 붕괴성의 균형 문제를 해결했습니다.
- 최적화된 비열처리 Al-Mg-Si 합금에 Si를 첨가하여 HPDC 중공 주조를 위한 주조성 및 기계적 특성을 향상시켰습니다.
- 개발된 중공 알루미늄 서브프레임은 기존 용접 강판 서브프레임에 비해 약 40%의 중량 감소를 달성했습니다 (그림 1).
- 개발된 중공 다이캐스트 알루미늄 서브프레임은 정적 파괴 및 내구성 시험에서 모든 설정 조건을 충족하여 양산 부품으로서의 적합성을 입증했습니다.
- 통계적/정성적 분석 결과:
- 정적 파괴 시험 결과 (표 1): 중공 다이캐스트 알루미늄 서브프레임은 다양한 위치와 방향에서 정적 파괴 시험에서 설정 조건을 초과하는 클리어런스율을 입증했습니다. 예를 들어, "하부 암 장착 섹션 FT+"에서 클리어런스율은 최대 및 항복 조건 모두에서 207%였습니다.
- 내구성 시험 결과 (표 2): 중공 다이캐스트 알루미늄 서브프레임은 서스펜션 어셈블리 내구성, 토크 로드 장착 섹션, 스티어링 기어 박스 장착 섹션, 스태빌라이저 장착 섹션 및 서스펜션 충격 시험을 포함한 모든 내구성 시험에서 설정 조건을 충족했습니다. 모든 결과는 "OK"로 표시되었습니다.
- Al-Mg-Si 합금의 기계적 특성 (그림 10, 그림 15):
- Al-5Mg 재료에 Si를 첨가하면 기계적 특성이 향상되었습니다.
- Al-5Mg-1.8Si 조성은 연신율과 강도 사이의 균형을 달성하는 최적의 조성으로 밝혀졌습니다. 이 조성은 5% 이상의 연신율과 150MPa 이상의 강도를 안정적으로 실현할 수 있게 했습니다.
- 판형 시험 금형을 사용한 주조 시험에서 약 2.0%의 Si 첨가로 강도와 연신율 사이의 균형이 서브프레임에 최적인 것으로 판단되었습니다 (그림 10).
- 데이터 해석:
- HPDC는 개발된 사형 주조 코어 기술 및 최적화된 Al-Mg-Si 합금과 결합될 때 경량 고성능 알루미늄 중공 서브프레임을 제조하는 데 실행 가능하고 효과적인 방법입니다.
- 개발된 중공 알루미늄 서브프레임이 달성한 40%의 중량 감소는 기존 강철 서브프레임에 비해 상당한 개선을 나타내며, 차량 중량 감소 및 연비 향상에 기여합니다.
- 정적 파괴 및 내구성 시험 조건의 성공적인 충족은 자동차 응용 분야를 위한 개발된 중공 알루미늄 서브프레임의 구조적 무결성 및 신뢰성을 입증합니다.
- Figure Name List:
- Figure 1. 개발된 중공 알루미늄 서브프레임
- Figure 2. 오토바이 프레임 부품 (CBR600RR)
- Figure 3. 각 제조 방법의 주조 조건 비교
- Figure 4. 제조 공정
- Figure 5. 1차 베이킹 후 코어 단면
- Figure 6. 온도 변화 및 페놀 수지 용융 점도
- Figure 7. 온도 변화 및 잔류 페놀 수지량
- Figure 8. 두꺼운 코어 중심부 베이킹 시간
- Figure 9. 게이트 속도와 강도 관계
- Figure 10. Al-Mg 재료의 기계적 특성 변화에 대한 Si 첨가량의 영향
- Figure 11. 제품 형상 및 코어 형상
- Figure 12. 보드 위치
- Figure 13. 코어 홀딩 핀 및 사형 제거 창 위치
- Figure 14. 시험편 절단 위치
- Figure 15. 서브프레임에서 절단한 시험편의 기계적 특성
- Figure 16. 정적 파괴 시험 및 내구성 시험
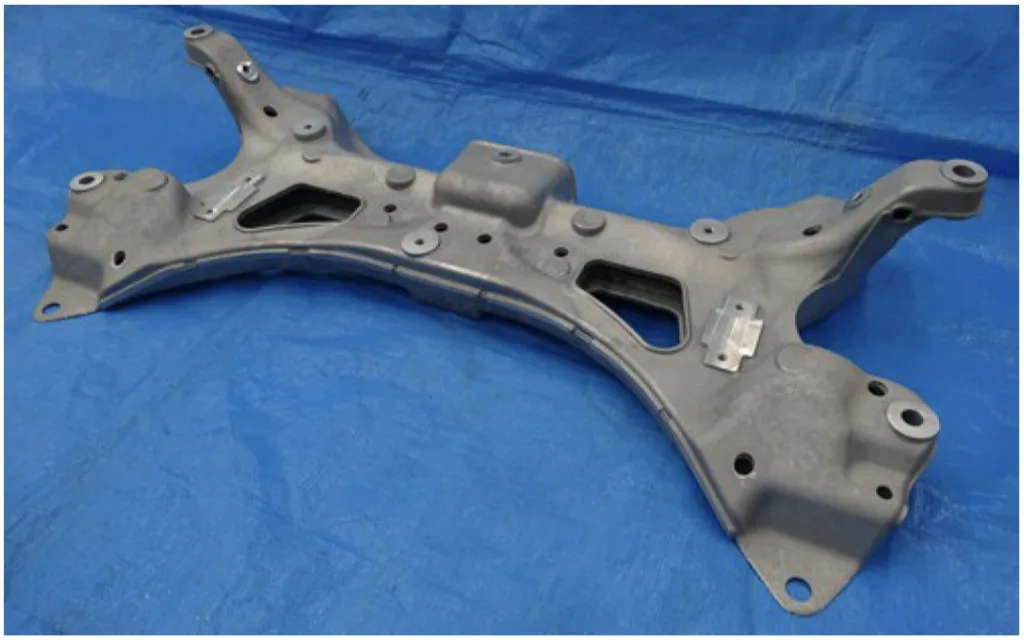
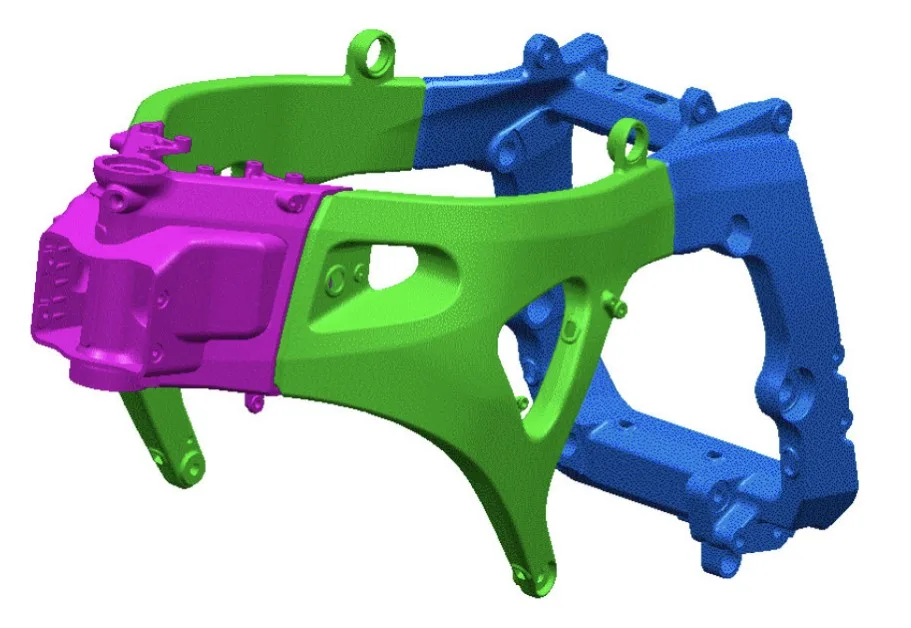
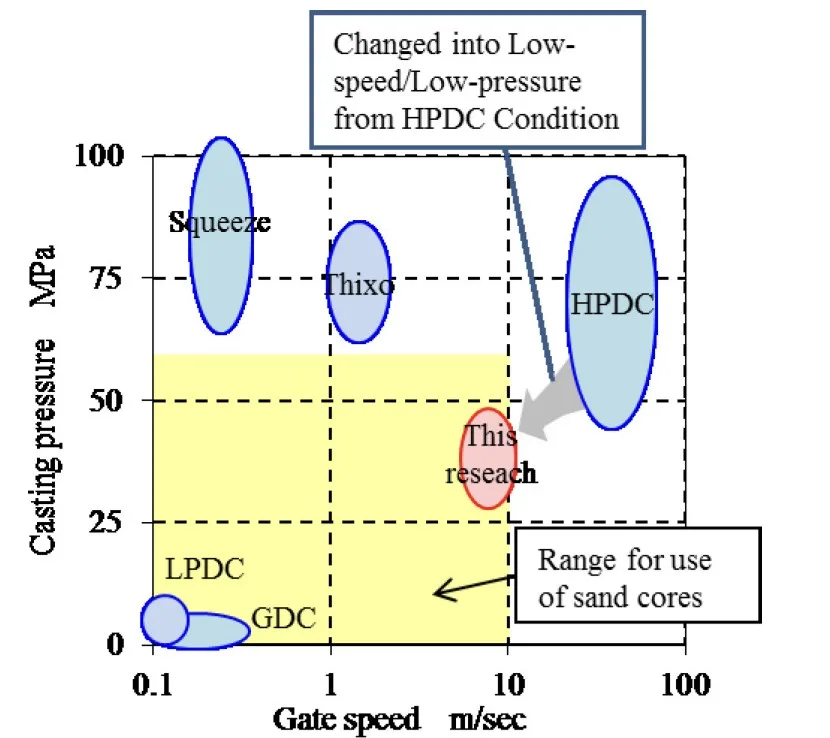
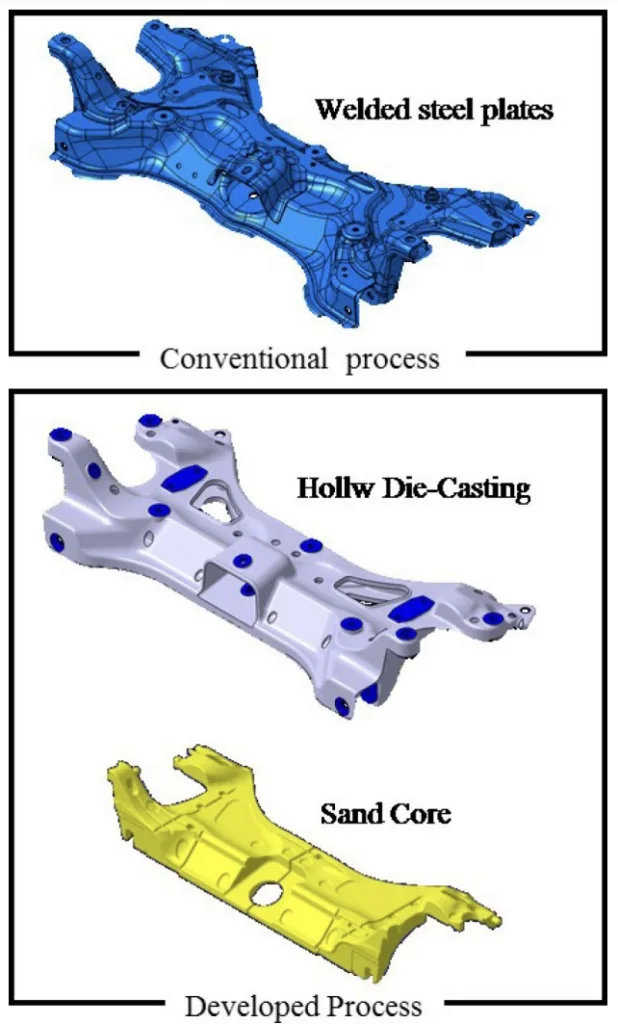
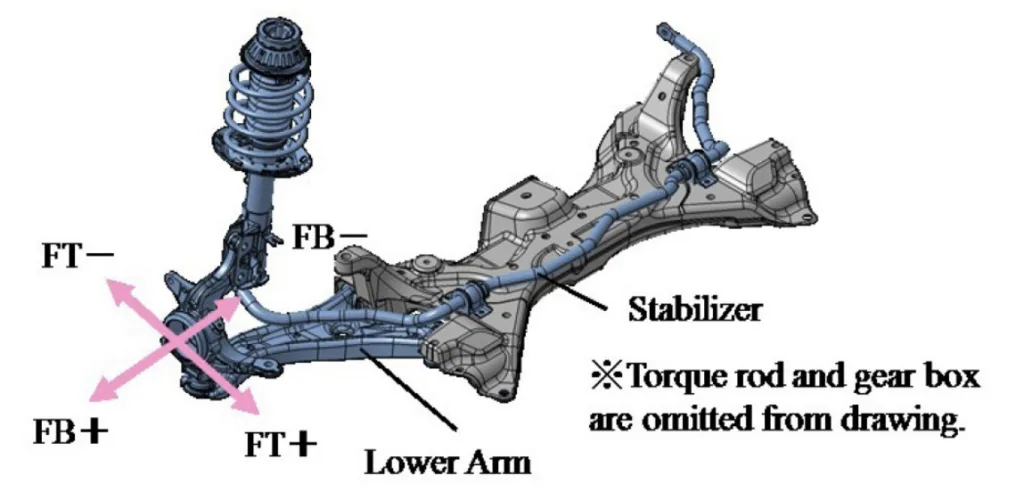
6. 결론 및 논의:
- 주요 결과 요약:
- 본 연구에서는 대형 박육 알루미늄 서브프레임 제조를 위한 HPDC를 이용한 중공 주조 기술을 성공적으로 개발했습니다.
- 주요 혁신 사항으로는 HPDC에 적합한 사형 주조 코어 기술과 Si 첨가된 비열처리 Al-Mg-Si 합금의 최적화가 포함됩니다.
- 개발된 중공 알루미늄 서브프레임은 정적 파괴 및 내구성 시험에서 모든 성능 요구 사항을 충족하면서 기존 강철 서브프레임에 비해 상당한 40%의 중량 감소를 달성했습니다.
- 연구의 학술적 의의:
- 본 연구는 HPDC가 서브프레임과 같은 복잡한 중공 자동차 구조 부품 생산에 사용될 수 있는 가능성과 효율성을 입증합니다.
- HPDC에 특화된 사형 주조 코어 기술 개발은 이 생산성이 높은 주조 방법의 적용 범위를 확장합니다.
- 최적화된 Al-Mg-Si 합금은 주조성, 기계적 특성 및 비용의 균형을 맞추는 경량 알루미늄 주조를 위한 비용 효율적인 재료 솔루션을 제공합니다.
- 실무적 시사점:
- 개발된 HPDC 중공 주조 기술은 자동차 산업용 경량 알루미늄 서브프레임을 생산하기 위한 실행 가능한 제조 솔루션을 제공합니다.
- 달성된 상당한 중량 감소는 연비 향상, 탄소 배출 감소 및 차량 성능 향상에 기여합니다.
- 비열처리 Al-Mg-Si 합금의 사용은 생산 비용을 최소화하는 데 도움이 되어 알루미늄 중공 서브프레임을 더 넓게 채택하는 데 경제적으로 매력적입니다.
- 연구의 한계점:
- 본 연구는 특정 서브프레임 설계 및 재료 조성에 초점을 맞추었습니다. 개발된 기술의 다른 서브프레임 설계 또는 알루미늄 합금에 대한 일반화 가능성은 추가 조사가 필요할 수 있습니다.
- 본 연구는 주로 기계적 성능에 초점을 맞추었습니다. 부식 저항 및 실제 차량 작동 조건에서의 장기 내구성과 같은 다른 측면은 추가로 탐구할 수 있습니다.
7. 향후 후속 연구:
- 후속 연구 방향:
- 생산성 및 주조 품질을 향상시키기 위해 사출 속도, 주조 압력 및 냉각 조건을 포함한 HPDC 공정 변수의 추가 최적화.
- HPDC 중공 주조 서브프레임의 기계적 특성, 주조성 및 비용 효율성을 더욱 향상시키기 위한 다른 알루미늄 합금 및 조성 탐색.
- 개발된 HPDC 중공 주조 기술을 다른 자동차 부품 및 구조 부품에 적용하여 차량 전체의 중량 감소 및 성능 이점을 극대화합니다.
- 추가 탐구가 필요한 영역:
- 개발된 중공 알루미늄 서브프레임의 장기 성능 및 신뢰성을 검증하기 위한 장기 내구성 연구 및 실제 차량 테스트 수행.
- 재료비, 제조비 및 성능 이점을 고려하여 대량 생산의 경제적 타당성을 평가하기 위한 포괄적인 비용 효율성 분석 수행.
- 중공 서브프레임 구조 및 토폴로지의 설계 최적화를 통해 추가적인 중량 감소 가능성 조사.
8. 참고문헌:
- Koya, E., Suzuki, T., Nakagawa, M., Fujimoto, G. et al., "Development of Hollow, Weld-able Die-Cast Parts for Aluminum Motorcycle Frames," SAE Technical Paper 2003-32-0055, 2003, doi:10.4271/2003-32-0055.
9. Copyright:
- 본 자료는 아키히코 아사미, 토모유키 이마니시, 유키오 오카자키, 토모히로 오노, 켄이치 테츠카의 논문: 고압 다이캐스팅을 이용한 알루미늄 중공 서브프레임 개발을 기반으로 작성되었습니다.
- 논문 출처: doi:10.4271/2016-01-0406
본 자료는 위 논문을 바탕으로 요약 작성되었으며, 상업적 목적으로 무단 사용이 금지됩니다.
Copyright © 2025 CASTMAN. All rights reserved.