본 소개 자료는 Giesserei-Verlag에서 발행한 "High-speed computer tomography employed in pressure die casting" 논문의 연구 내용을 담고 있습니다.
![Figure 1: In a high-speed, automatic helix in-line CT unit the gantry, which accommodates the x-ray tube and the
multi-line detector arranged opposite, rotates about the specimens on the conveyor belt [6]](https://castman.co.kr/wp-content/uploads/image-1540-1024x808.webp)
1. 개요:
- 제목: High-speed computer tomography employed in pressure die casting (고속 컴퓨터 단층 촬영을 이용한 고압 다이캐스팅)
- 저자: Eberhard Ambos, Oliver Brunke, Dirk Neuber, Holger Lux, Ingo Stuke, Wolfgang Besser, Mike Ziesemann, Christian Heikel and Andrea Huxol
- 출판년도: 2012
- 게재 저널/학회: Casting Plant & Technology
- 키워드: 논문에서 명시적으로 사용하지 않음. (컴퓨터 단층 촬영, CT, 압력 다이캐스팅, 비파괴 검사, 기공, 품질 보증, 치수 정확도)
2. 초록
자동차 산업은 연비 향상과 환경 영향 감소를 위해 지속적으로 노력하고 있으며, 이는 알루미늄 합금 다이캐스팅에도 영향을 미치고 있습니다. 이 논문은 세계 최초로 압력 다이캐스팅에 고속 컴퓨터 단층 촬영(CT)을 적용하여 양산 준비를 위한 특정 사례를 제시하고 그 결과와 경험을 소개합니다.
3. 연구 배경:
연구 주제 배경:
- 자동차 산업의 연비 향상 및 환경 영향 감소 노력으로 인해 더 얇은 벽을 가진 경량 다이캐스팅 부품이 요구되고 있습니다.
- 부품은 점점 더 커지고 복잡해지며, 기능 통합이 증가하고 있습니다.
- 재료 강도, 특히 동적 강도에 대한 요구 사양이 더욱 엄격해지고 있습니다.
선행 연구 현황:
- 기존 연구는 결함을 고려하여 고응력 Al 압력 다이캐스팅에 대한 계산 절차 개발에 중점을 두었습니다 [1-4].
- 일반적인 2D X-ray 검사는 주조에 대한 빠르고 포괄적인 정보를 제공하기에 충분하지 않습니다.
- 기존 산업용 컴퓨터 단층 촬영 시스템은 자동차 제조업체가 운영하는 대규모 주조 공장에서만 사용이 제한되었습니다.
연구 필요성:
- 다이캐스팅 공장 고객들 사이에서 주조물의 기공(위치, 부피, 크기) 이해의 중요성에 대한 인식이 높아지고 있습니다.
- 제조 역학 및 납품 성능 요구를 충족하기 위해 더 빠르고 효율적인 비파괴 검사 기술이 필요합니다.
- 패턴 개발에서 양산까지의 시간을 최소화해야 합니다.
4. 연구 목적 및 연구 질문:
연구 목적:
- 생산 조건에서 다이캐스트 부품 테스트에 고속 CT의 적합성을 확인합니다.
- 기공의 정확한 위치와 부피에 대한 데이터를 제공하여 주조물의 기공 시뮬레이션을 개선합니다.
- 새로 개발된 고속 CT 시스템에서 얻은 측정값의 치수 정확도를 평가합니다.
핵심 연구:
본 논문의 핵심 연구는 다음과 같습니다.
- 고속 CT가 다이캐스팅에서 기공 및 치수 정확도에 대한 정확하고 시기적절한 데이터를 제공할 수 있습니까?
- 기공 시뮬레이션 결과는 고속 CT 스캔의 단층 촬영 결과와 얼마나 잘 일치합니까?
5. 연구 방법
- 연구 설계: 실험 및 비교 연구
- 데이터 수집: 알루미늄 다이캐스팅(오일 펌프용 받침대)의 고속 CT 스캔, 금속 조직 검사, 프린지 패턴 투영 및 접촉 프로브 측정.
- 분석 방법: 단층 촬영 결과와 시뮬레이션 결과 비교, 금속 조직 검사를 통한 결함 검증, CT 측정값을 접촉 프로브 및 프린지 투영 데이터와 비교하여 치수 정확도 평가.
- 연구 주제 및 범위: 알루미늄 다이캐스팅에서 기공 탐지 및 치수 측정을 위한 고속 CT 평가.
- 사용 장비: 초기에는 실험실 규모의 고속 CT 장치(그림 2)를 사용했고, 이후 산업용 규모의 장치(그림 3)를 사용했습니다. 엑스레이 튜브를 수용하는 갠트리 어셈블리(스캐닝 유닛)는 테스트 대상 주물을 중심으로 회전하고, 컨베이어 벨트는 주물을 저속으로 갠트리를 통과하여 이동시킵니다(그림 1).
6. 주요 연구 결과:
주요 연구 결과 및 제시된 데이터 분석:
- 고속 CT 스캔 속도는 기존 CT 시스템보다 수백 배 빠릅니다.
- 시스템은 나선형 모드(다중 평면 또는 다중 라인 나선형 CT)로 작동하여 프로세스 속도를 높이고 움직임으로 인한 인공물을 줄입니다 [5].
- 산업용 장치는 최대 시험편 크기, 고용량 X선 튜브 사양, 재구성 속도 및 일반적인 세부 해상도(복셀 크기)를 포함한 특정 기술 데이터를 갖습니다(4페이지).
- 핫스팟 식별(그림 5) 및 기공 시각화(그림 6)에 대한 시뮬레이션 결과가 단층 촬영 결과와 비교되었습니다.
- 시험편의 투명 3D 모델은 다양한 정도의 기공을 보여주었습니다(그림 7).
- 부품 수에 대한 총 기공률을 측정했으며 0.2491% ~ 0.4667% 범위였습니다(그림 8).
- 금속 조직 검사를 통해 단층 촬영에서 발견된 결함을 확인했습니다(그림 9 및 10).
- 단층 촬영의 치수 편차는 프린지 투영 기반 측정(그림 11)과 비교되었으며, 선택된 공칭 거리는 두 가지 방법을 사용하여 측정되었습니다(그림 12).
- CT 데이터, 접촉 프로브 측정(±10 µm 정확도) 및 프린지 투영 데이터 간에 높은 일치성이 발견되었습니다.
- 고속 CT 시스템은 "at-line"(그림 13) 또는 "in-line"(그림 14) 방식으로 통합될 수 있습니다.
그림 목록:
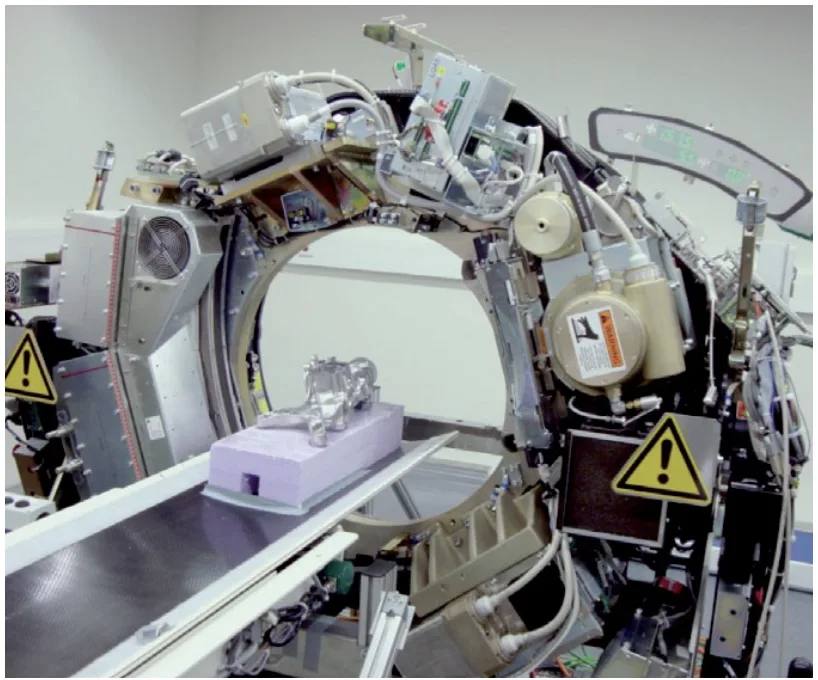
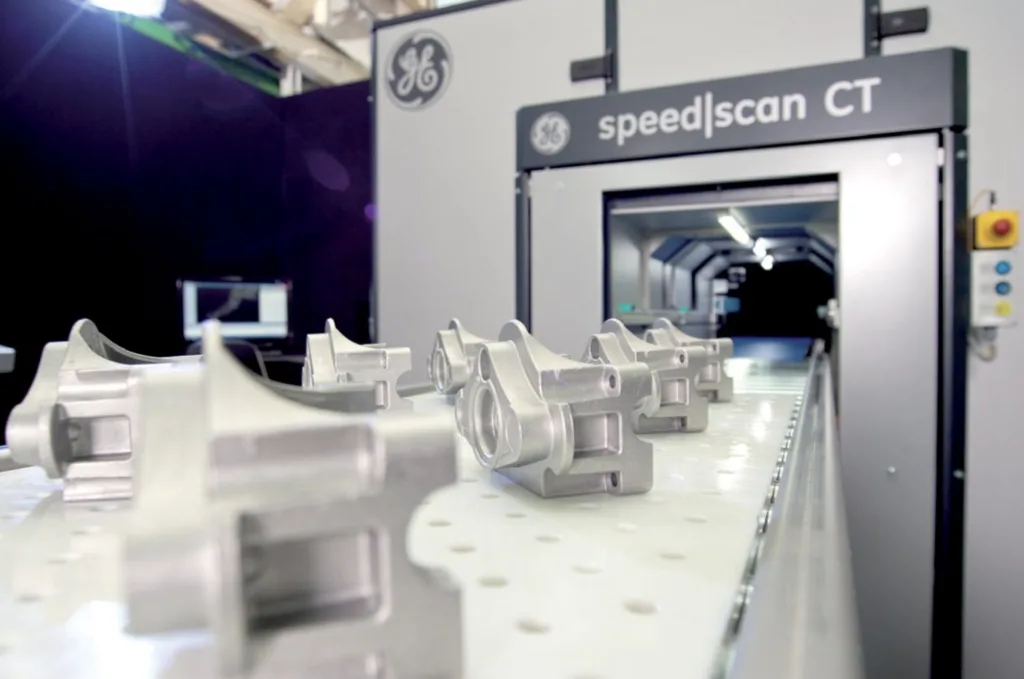
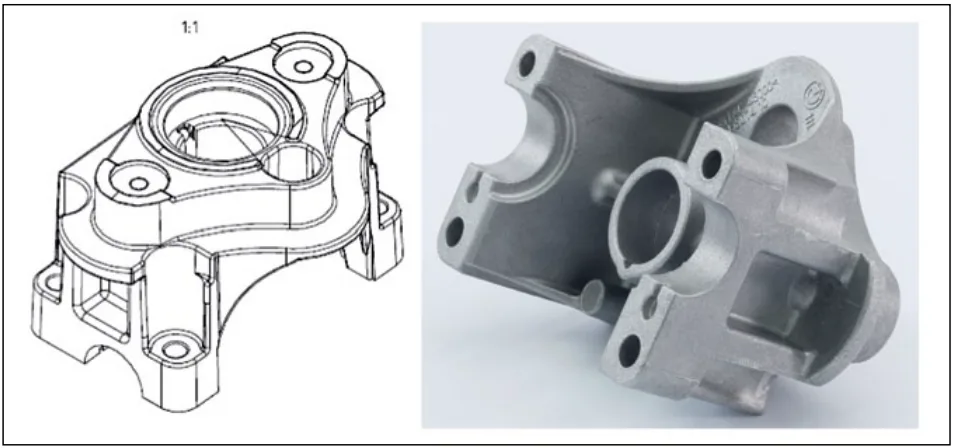
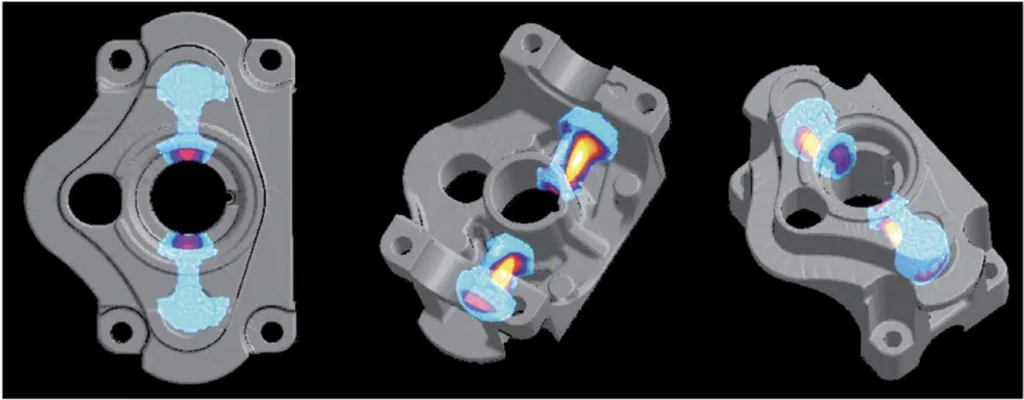
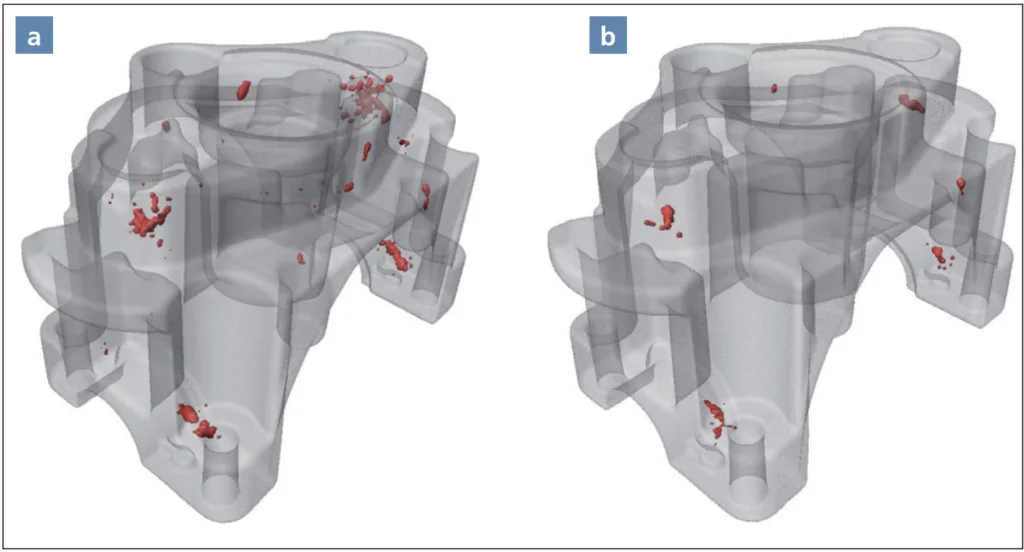
- 그림 1: 고속 자동 헬릭스 인라인 CT 장치에서 갠트리(X선 튜브와 반대쪽에 배열된 다중 라인 검출기를 수용)는 컨베이어 벨트 위의 표본을 중심으로 회전합니다[6].
- 그림 2. 실험실 규모의 고속 CT로 다이캐스팅 스캔
- 그림 3: 시리즈형 고속 CT 장치
- 그림 4: 스캔된 알루미늄 다이캐스팅
- 그림 5: 부품의 여러 평면에서 핫스팟 식별을 위한 시험편 시뮬레이션(수축으로 인한 부피 결손의 예측 위치, 색상 척도: 청록색 약 18초 후, 옅은 빨간색 약 20초 후, 노란색 약 21초 후)
- 그림 6: 부품의 여러 평면에서 기공을 시각화하는 시험편 시뮬레이션(빨간색: 기공 형성 확률 약 50%, 노란색: 75~85%, 흰색 100%)
- 그림 7: 시험편의 투명 3D 모델: a) 가장 높은 기공률(부품 번호 4) 및 b) 가장 낮은 기공률(부품 번호 10)
- 그림 8: 부품 수에 따른 총 기공률
- 그림 9: 그림 7a에서 기공률이 가장 높은 부품 번호 4의 금속 조직 검사
- 그림 10: 그림 7b에서 기공률이 가장 낮은 부품 번호 10의 금속 조직 검사
- 그림 11: 단층 촬영의 치수 편차 대 프린지 투영 기반 부품 번호 5 측정
- 그림 12: 고속 CT 및 프린지 투영으로 측정한 91.000mm의 선택된 공칭 거리
- 그림 13: At-line 방식의 고속 CT 시스템
- 그림 14: In-line 방식의 고속 CT 시스템: (1) 롤러 테이블, (2) 레벨 조정을 위한 리프팅 시스템이 있는 롤러 테이블, (3) 슬라이드 게이트(방사선 차폐), (4) 스캐닝 유닛(갠트리), (5) 표본, (6) 방사선 차폐 캐빈
7. 결론:
주요 결과 요약:
- 고속 CT는 생산 조건에서 다이캐스트 부품을 테스트하는 데 적합하며 기공 및 치수 정확도에 대한 정확하고 시기적절한 데이터를 제공합니다.
- 시뮬레이션 결과, 단층 촬영 및 금속 조직 검사 사이에 높은 수준의 일치성이 있습니다.
- 이 시스템은 결함 부피 측정에 대해 높은 반복 정확도를 제공합니다.
- 고속 CT는 생산 흐름에 통합되어 품질 관리 프로세스를 간소화하고 시뮬레이션 정확도를 높일 수 있습니다.
연구 결과 요약, 연구의 학술적 의의 및 실용적 시사점:
- 이 기술은 산업 생산에 적합하며 매우 효율적입니다.
- 이 연구는 알루미늄 다이캐스팅의 강도 계산을 정교화하기 위해 고속 컴퓨터 단층 촬영을 사용할 수 있음을 보여줍니다.
향후 확장 연구 가능 분야:
- 개별 기공 및 최소 치수의 검출 한계를 결정하기 위한 추가 연구가 필요합니다.
- 향후 개발은 더 큰 부품을 테스트하기 위해 표본 수용 공간을 확대하는 데 중점을 둘 수 있습니다.
- 기술 및 응용 분야를 더욱 발전시키기 위해 추가 파트너와의 지속적인 연구 및 협력이 계획되어 있습니다.
8. 참고 문헌:
- [참고 문헌] www.giesserei-verlag.de/cpt/references
9. 저작권:
- 본 자료는 "Eberhard Ambos, Oliver Brunke, Dirk Neuber, Holger Lux, Ingo Stuke, Wolfgang Besser, Mike Ziesemann, Christian Heikel and Andrea Huxol"의 "High-speed computer tomography employed in pressure die casting" 논문을 기반으로 합니다.
- 논문 출처: www.giesserei-verlag.de/cpt/references
본 자료는 위 논문을 소개하기 위해 제작되었으며, 상업적 목적으로 무단 사용하는 것을 금합니다. Copyright © 2025 CASTMAN. All rights reserved.