この論文概要は、['INTERNATIONAL JOURNAL OF RESEARCH IN ADVANCED ENGINEERING TECHNOLOGIES']によって発行された、['DESIGN AND WEIGHT OPTIMIZATION OF OIL PAN BY FE ANALYSIS']論文に基づいて作成されました。
1. 概要:
- タイトル:DESIGN AND WEIGHT OPTIMIZATION OF OIL PAN BY FE ANALYSIS (FE解析によるオイルパンの設計と重量最適化)
- 著者:SINGATHI SHARATH KUMAR, P. SUBRAMANYAM
- 発行年:2015年
- 発行ジャーナル/学会:INTERNATIONAL JOURNAL OF RESEARCH IN ADVANCED ENGINEERING TECHNOLOGIES (国際先端工学技術研究ジャーナル)
- キーワード:Oil pan (オイルパン), Manufacturing Methods (製造方法), Cost Analysis (コスト分析), Design (設計), Analysis (解析)
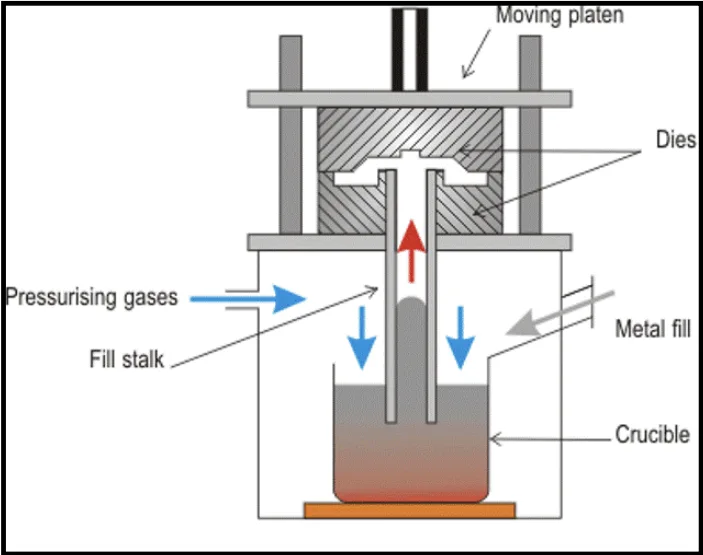
2. 抄録または序論
抄録 - 往復動型内燃機関において、オイルパンはクランクシャフトのハウジングです。この密閉構造はエンジン内で最大の空洞を形成し、マルチシリンダーエンジンでは通常、1つまたは複数のシリンダーブロックに統合されてシリンダーの下に配置されます。オイルパンはエンジンの下部に位置し、エンジンオイルを貯蔵するために使用されます。必要なときにオイルパンからエンジンにオイルがポンプで送られます。
本プロジェクトでは、潜水艦エンジンで使用されるオイルパンのモデリングを行います。本プロジェクトの目的は、CADソフトウェアを使用してオイルパンをモデル化し、適切な鋳造製造プロセスを選択して鋳造金型を設計し、CAMソフトウェアを使用してCNCプログラムを生成し、鋳造金型の不要な領域で重量を削減することです。
初期段階では、金型設計と解析条件に関するデータを収集します。次の段階では、さらなる研究のためにPro-Engineerを使用してモデルを生成します。金型アセンブリをモデル化するために金型設計計算を行います。金型準備後、オイルパンに適した材料を選択して金型構造を最適化し、重量を削減するために構造解析を行います。モデリング、金型設計、製造(CNC)はPro/Engineerソフトウェアを使用して行われます。
序論 - オイルパンについて
オイルパンは、一般的に自動車やその他の類似の用途における4ストローク内燃機関の底部をシールする部品です。米国ではオイルパンとして知られていますが、世界の他の地域ではオイルサンプと呼ばれることもあります。主な目的は、クランクケースの最下部を形成し、エンジンオイルがエンジン内を循環する前後にオイルを保持することです。オイルパンを取り外すと、通常、クランクシャフト、オイルピックアップ、およびディップスティックの下端部が現れます。
通常のエンジン運転中、オイルポンプはパンからオイルを吸い上げ、エンジン内を循環させます。オイルはそこで様々な部品を潤滑するために使用されます。オイルがエンジンを通過した後、オイルパンに戻されます。このようなウェットサンプシステムでは、エンジンが保持できるオイルの量は、オイルパンのサイズに直接関係しています。エンジンは、クランクシャフトが水没するとオイルがエアレーションを起こし、オイルポンプがエンジン内を循環させることが困難または不可能になるため、パンに収まる量以上のオイルを保持することはできません。
エンジンオイルを交換するために使用されるドレンプラグは、通常、オイルパンのどこかに配置されています。オイルドレンプラグを簡単に見つける方法は、パンを見つけてから最も低い点を探すことです。パンは傾斜していたり、片方の端が膨らんでいたり、エンジンの位置によってわずかに角度が付いている場合があります。この低い点が通常、ドレンプラグが配置され、パン内のオイルをほぼすべて排出できる場所です。
レースや高性能車などの特定のエンジンは、ドライサンプシステムとして知られるものを使用する場合があります。クランクケースにすべてのオイルを貯蔵する代わりに、これらのエンジンにはポンプで送り込まれる分離されたリザーバーがあります。これらのエンジンのオイルパンは、オイルが潤滑に使用された後にリザーバーに戻されるため、通常、ウェットサンプシステムのオイルパンよりもはるかに小さくなります。
3. 研究背景:
研究テーマの背景:
往復動型内燃機関において、オイルパンはクランクシャフトハウジングとして機能します。この密閉構造はエンジン内で最大の空洞を形成し、シリンダーの下に位置しています。オイルパンはエンジンの下部に配置され、エンジンオイルを貯蔵するために使用されます。
既存研究の現状:
このセクションでは明示的に言及されていません。
研究の必要性:
本プロジェクトでは、潜水艦エンジンで使用されるオイルパンのモデリングを行います。本プロジェクトの目的は、CADソフトウェアを使用してオイルパンをモデル化し、適切な鋳造製造プロセスを選択して鋳造金型を設計し、CAMソフトウェアを使用してCNCプログラムを生成し、鋳造金型の不要な領域で重量を削減することです。初期段階では、金型設計と解析条件に関するデータを収集します。次の段階では、さらなる研究のためにPro-Engineerを使用してモデルを生成します。金型アセンブリをモデル化するために金型設計計算を行います。金型準備後、オイルパンに適した材料を選択して金型構造を最適化し、重量を削減するために構造解析を行います。モデリング、金型設計、製造(CNC)はPro/Engineerソフトウェアを使用して行われます。
4. 研究目的と研究課題:
研究目的:
本プロジェクトの目的は、CADソフトウェアを使用してオイルパンをモデル化し、適切な鋳造製造プロセスを選択して鋳造金型を設計し、CAMソフトウェアを使用してCNCプログラムを生成し、鋳造金型の不要な領域で重量を削減することです。また、オイルパンに適した材料を選択して金型構造を最適化し、重量を削減することです。
主要な研究:
- CADソフトウェア(Pro-Engineer)を使用したオイルパンのモデリング。
- 鋳造金型の設計。
- 適切な鋳造製造プロセスの選択。
- CAMソフトウェアを使用したCNCプログラムの生成。
- 鋳造金型の不要な領域での重量削減。
- オイルパンに適した材料選択を比較して金型構造を最適化し、重量を削減するための構造解析。
研究仮説:
このセクションでは明示的に言及されていません。本研究は、仮説駆動型というよりも、探索的かつ設計に焦点を当てています。
5. 研究方法:
研究デザイン:
研究デザインには、ソフトウェアツールを使用したモデリング、設計、解析、最適化が含まれます。初期段階では、金型設計と解析条件に関するデータを収集します。次の段階では、さらなる研究のためにPro-Engineerを使用してモデルを生成します。金型アセンブリをモデル化するために金型設計計算を行います。金型準備後、オイルパンに適した材料を選択して金型構造を最適化し、重量を削減するために構造解析を行います。モデリング、金型設計、製造(CNC)はPro/Engineerソフトウェアを使用して行われます。
データ収集方法:
初期段階では、金型設計と解析条件に関するデータを収集します。
分析方法:
FE解析を使用して、オイルパンに適した材料選択を比較して金型構造を最適化し、重量を削減するために構造解析を行います。
研究対象と範囲:
潜水艦エンジンで使用されるオイルパンのモデリング。オイルパンの材料選択。鋳造金型の設計と製造。
6. 主な研究結果:
主要な研究結果:
- M.S. F26の変位値:最大 0.24694 mm
- M.S. F26のひずみ値:最大 0.0069591
- M.S. F26のフォンミーゼス応力値:133.38 N/mm²
- アルミニウム A360の変位値:最大 0.66136 mm
- アルミニウム A360のひずみ値:最大 0.0018799
- アルミニウム A360のフォンミーゼス応力値:132.43 N/mm²
- M.S. F26の安全率:2.186
- アルミニウム A360の安全率:2.12
- 既存モデルと修正モデルのコスト差:Rs. 2, 82,377/-
- 最適化された金型を使用することによる機械加工時間の節約:約68時間。
- アルミニウムを使用することによる部品コストの削減:約40%。
提示されたデータの分析:
解析結果は、安全率がどちらも2を超えているため、軟鋼F26とアルミニウムA360の両方が適切な材料であることを示しています。ただし、アルミニウムA360は、軟鋼F26と同等のフォンミーゼス応力値を持ちながら、より高い変位を示しています。アルミニウムA360を使用すると、大幅なコスト削減と重量最適化につながる可能性があります。最適化された金型設計も、製造コストと時間の節約に貢献します。
図のリスト:
- 図 3.4 冷間チャンバー技術の原理 (Fig. 3.4 Principle of Cold Chamber Technologies)
- 図 5-2 重力ダイカスト用の古典的な金型を構成する主要部品 (Fig. 5-2 the main parts constituting a classical mould for gravity die-casting)
- 組立ガイドライン用に選択された設計 (Selected design for assembly guidelines.)
- 組立ガイドライン用に選択された設計 (Selected design for assembly guidelines.)
- 重力ダイカスト (Gravity die casting)
- 要約されたダイカストプロセス (Die casting processes, as summarized)
- 冷間チャンバー技術の原理 (Principle of Cold Chamber Technologies)
- キャビティ部品の製図 (Drafting for cavity part)
- コア部品の製図 (Drafting for Core part)
- エジェクタープレートの製図 (Drafting for Ejector plate)
- リテーナープレートとピンの製図 (Drafting for Retainer plate and pins)
- ウォーターインレットノブ、25mmボルトの製図 (Drafting for Water inlet knob, 25mm Bolts)
- ガイドピラー、ガイドスリーブの製図 (Drafting for Guide Pillar, Guide Sleeve)
- バックプレートの製図 (Drafting for Back plate)
- エジェクターピンの製図 (Drafting for Ejector pins)
- ハウジングの製図 (Drafting for Housing)
- コア部品のモデル (Model of Core part)
- リテーナープレートのモデル (Model of Retainer plate)
- エジェクタープレートのモデル (Model of Ejector plate)
- バックプレートのモデル (Model of Back plate)
- 完全な金型アセンブリ (Complete Mould Assembly)
- 分解図 (Exploded View)
- キャビティのパーティング面 (Parting surface for Cavity)
- 抽出されたコア部品 (Extracted Core part)
- 抽出されたキャビティ部品 (Extracted Cavity part)
- キャビティ準備 (CAVITY PREPARATION)
- キャビティのモデル (Model of Cavity)
- 金型準備のための供給システムを備えたオイルパン (Oil pan with feed system for the preparation of mould)
- コアのパーティング面 (Parting surface for Core)
- 形状 (Geometry)
- モデルのメッシュ (Meshing for model)
- M.S. F26の変位値 (Displacement value for M.S. F26)
- M.S. F26のひずみ値 0.0069591 最大 (Strain Value 0.0069591 Max for M.S. F26)
- アルミニウム A360のひずみ値 0.0018799 最大 (Strain value 0.0018799 for Aluminum A360)
- M.S. F26のフォンミーゼス応力値 133.38 N/mm² (Von-misses stress value 133.38 N/mm² for M.S. F26)
- アルミニウム A360のフォンミーゼス応力値 132.43 N/mm² (Von-misses stress value 132.43 N/mm² for Aluminum A360)
- アルミニウム A360の変位値 (Displacement value for Aluminum A360)
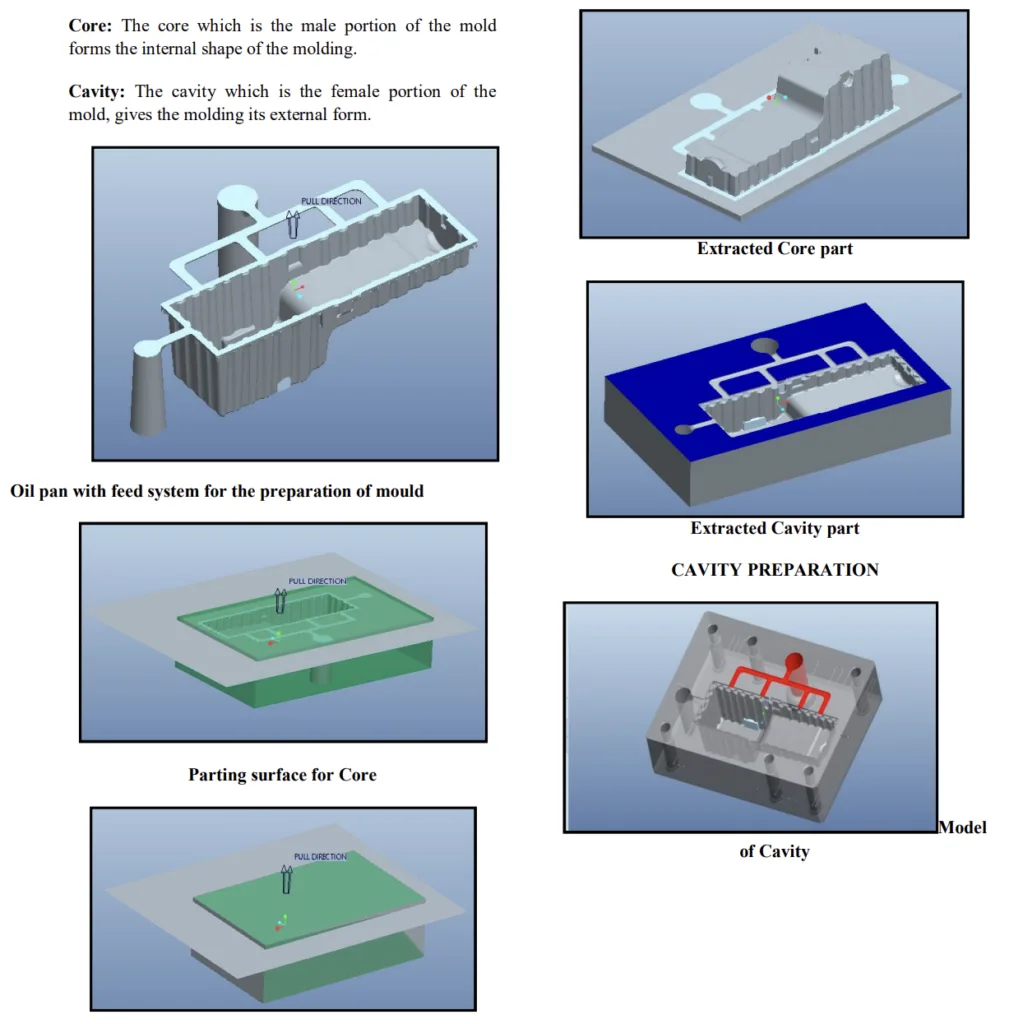
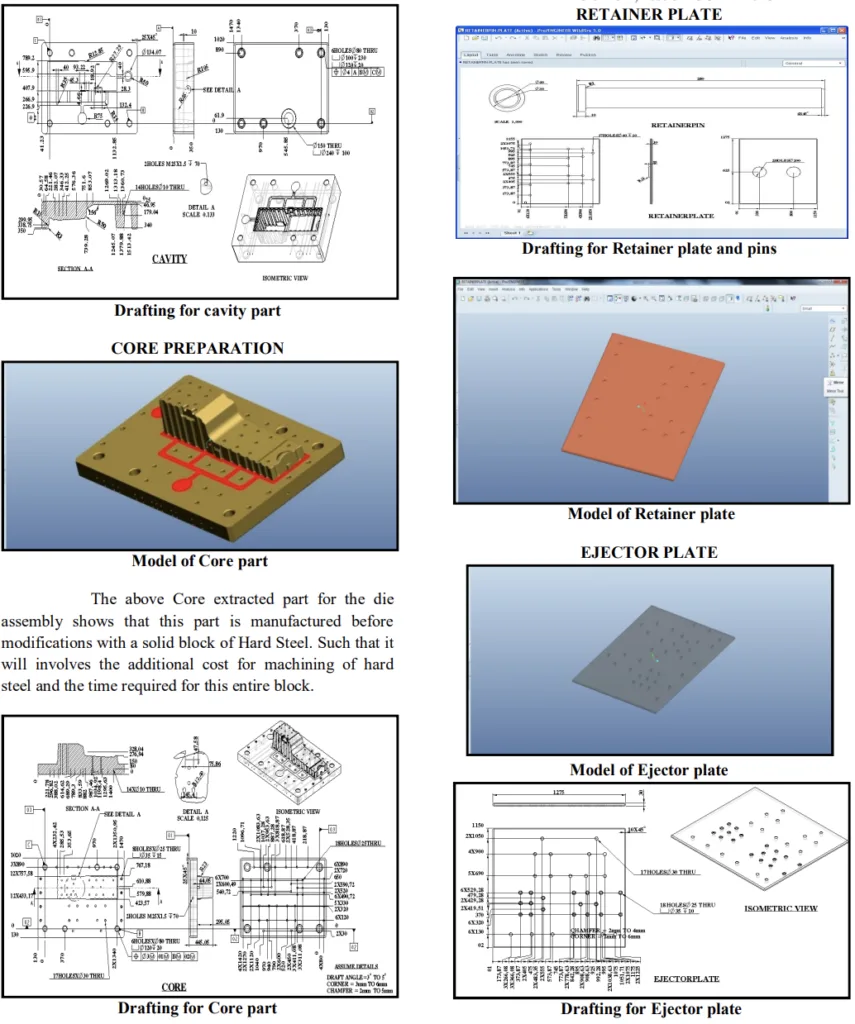
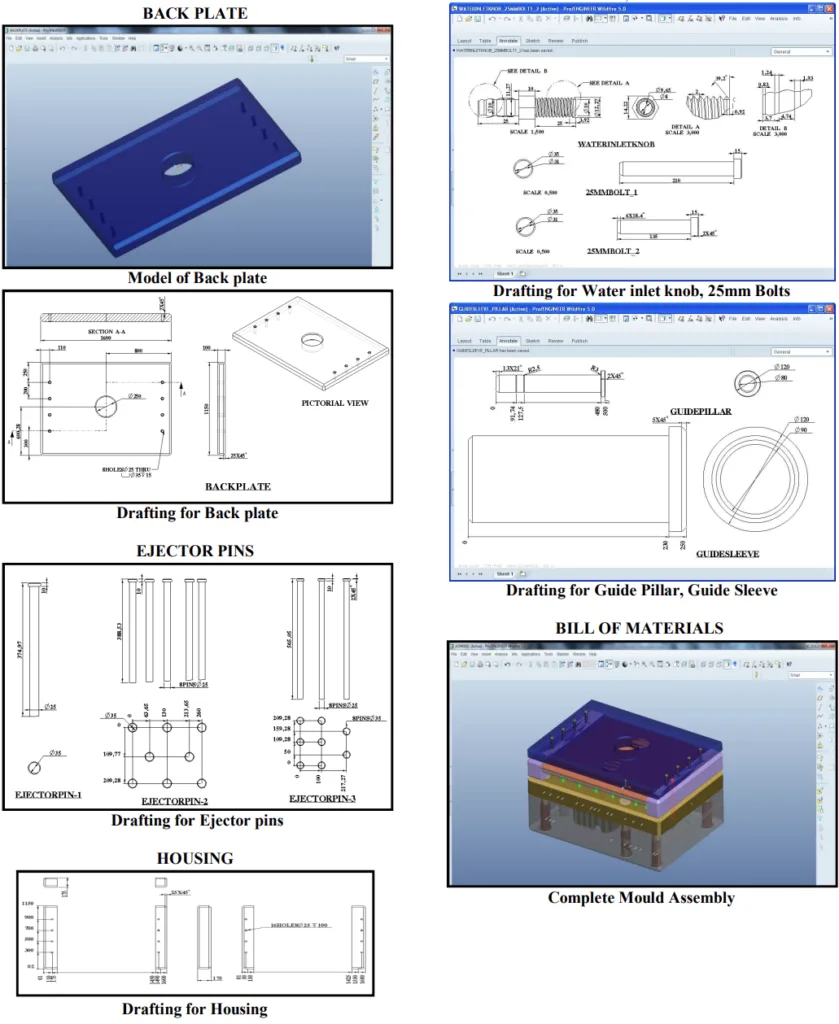
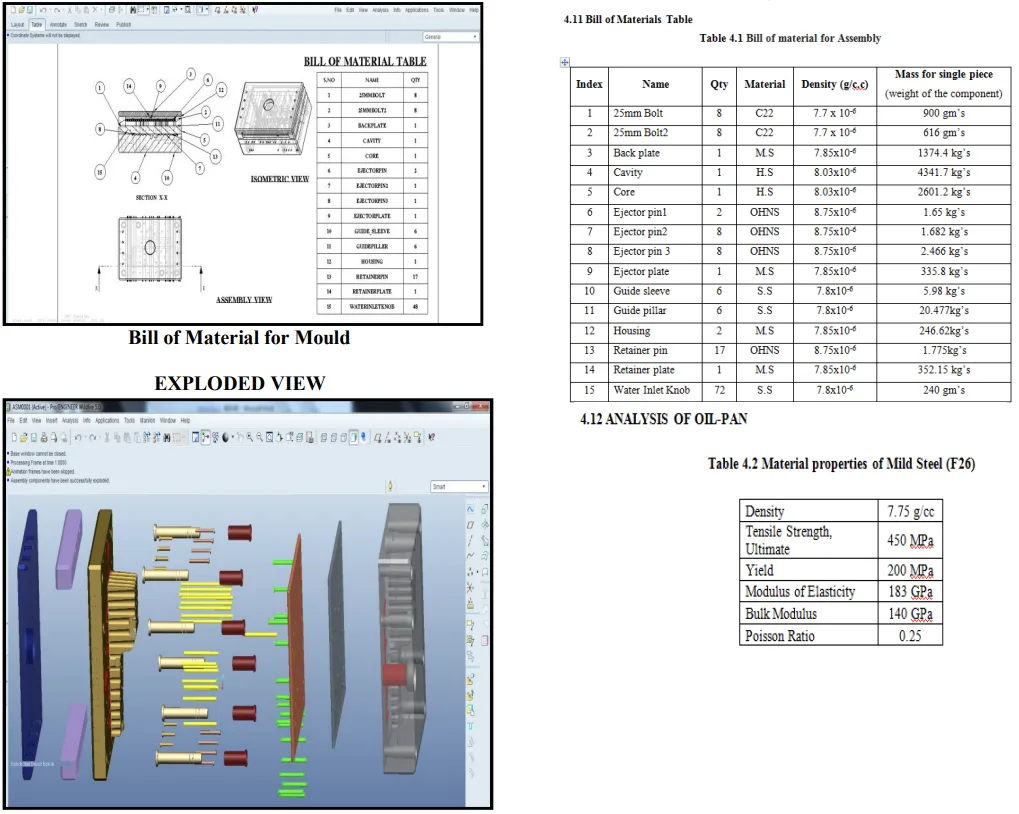
7. 結論:
主な調査結果の要約:
本プロジェクトでは、FE解析と設計変更により、オイルパンとそのダイカスト金型の設計を最適化することに成功しました。本研究では、材料として軟鋼F26とアルミニウムA360を比較し、アルミニウムA360が2.12の安全率で構造的完全性を維持しながら、重量とコストの利点を提供する適切な代替材料であることを発見しました。分割コアを組み込んだ最適化された金型設計は、材料使用量、機械加工時間(約68時間)、および全体的な製造コスト(2,82,377ルピーの削減)を削減し、アルミニウムを使用することによる部品コストの削減効果はほぼ40%に達します。
研究の学術的意義:
本研究は、ダイカストにおける重量およびコスト削減のためのFE解析と最適化された設計手法の応用を示しています。オイルパンなどの自動車部品製造における材料選択と金型設計の最適化に関するケーススタディを提供します。
実用的な意義:
本研究の結果は、ダイカストメーカーがオイルパンの製造において材料費、機械加工時間、および部品重量を削減するための実用的なガイドラインを提供します。最適化された金型設計と材料選択(アルミニウムA360)は、製造効率と製品性能を向上させるために直接実装できます。
研究の限界と今後の研究分野:
本研究は、潜水艦エンジン用の特定のオイルパン設計に焦点を当てています。今後の研究では、これらの最適化技術の一般化可能性を他のタイプのオイルパンおよびダイカスト部品に拡張することができます。解析を熱解析および疲労解析を含めるように拡張して、より包括的な評価を行うことができます。さまざまなアルミニウム合金と鋳造パラメータに関するさらなる調査も有益である可能性があります。
8. 参考文献:
- [1] Kennedy J, Eberhart RC (1995) "Particle swarm optimization". In: Proceedings of the 1995 IEEE International Conference on Neural Networks (ICNN'95), Perth, Australia, November/December 1995, vol 4, pp 1942-1948
- [2] Jerald J, Asokan P, Prabaharan G, Saravanan R (2005) "Scheduling optimisation of flexible manufacturing systems using particle swarm optimisation algorithm". International Journal Advance Manufacturing Technology 25:964-971
- [3] K. Vidyarthi and M.K. Tiwari “Machine loading problem of FMS: a fuzzy-based heuristic approach", International Journal of Production Research, 2001, 39(5), 953-979
- [4] M. K. Tiwari, B. Hazarika “Heuristic solution approach to the machine loading problem of an FMS and its Petri net model", International Journal of Production Research, 1997, 35(8), 2269-2284
- [5] Swarnkar R, Tiwari MK (2004) Modeling machine loading problem of FMSs and its solution methodology using a hybrid tabu search and simulated annealing-based heuristic approach. Robot Computer-Integrated Manufacturing 20(3):199–209
- [6] Nagarjuna N, Mahesh O, Rajagopal K (2006) A heuristic based on multi-stage programming approach for machine-loading problem in a flexible manufacturing system. Robot Computer-Integrated Manufacturing 22:342-352
- [7] S. G. Ponnambalam and Low Seng Kiat (2008) "Solving Machine Loading Problem in Flexible Manufacturing Systems Using Particle Swarm Optimization" World Academy of Science, Engineering and Technology 39
- [8] Sandhyarani Biswas, S. S. Mahapatra "Machine loading in Flexible manufacturing System: A swarm optimization approach" Eighth Int. Conference on Opers. & Quant. Management, 2007, NITR, 621-628
- [9] Kathryn E. Stecke, (1986), “A hierarchical approach to solving machine grouping and loading problems of FMS'S", European journal of operational research, 24, 369-378
- [10] M. K. Tiwari& N.K. Vidyarthi (2000): Solving machine loading problems in a flexible manufacturing system using a genetic algorithm based heuristic approach, International Journal of Production Research, 38:14, 3357-3384
- [11] Paul S. Andrews, An Investigation into Mutation Operators for Particle Swarm Optimization
- [12] Akhilesh kumar, prakash, MK Tiwari (2006), "Solving machine loading problem of a FMS with constraint based Genetic Algorithm”, European Journal of Operational Research (2006) 1043-1069 175
- [13] Sandhyarani Biswas, S. S. Mahapatra, “Modified particle swarm optimization for solving machine-loading problems in flexible manufacturing systems”. International Journal of Advanced Manufacturing Technology (2008) 39:931-942
9. 著作権:
- この資料は、"[SINGATHI SHARATH KUMAR, P. SUBRAMANYAM]"の論文:「"DESIGN AND WEIGHT OPTIMIZATION OF OIL PAN BY FE ANALYSIS"」に基づいています。
- 論文ソース:https://www.ijraet.com/wp-content/uploads/2024/01/IJRAET_2178.pdf
この資料は上記の論文を要約したものであり、商業目的での無断使用は禁止されています。
Copyright © 2025 CASTMAN. All rights reserved.