本紹介資料は、「International Journal of Precision Engineering and Manufacturing」に掲載された論文「Mould Design for Clutch Housing Parts using a Casting Simulation of High Pressure Die Casting」に基づいています。
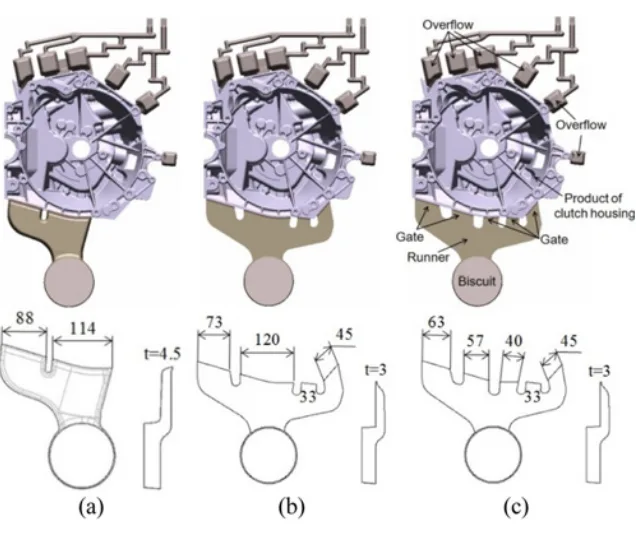
1. 概要:
- 論文タイトル: Mould Design for Clutch Housing Parts using a Casting Simulation of High Pressure Die Casting (高圧ダイカストの鋳造シミュレーションを用いたクラッチハウジング部品の金型設計)
- 著者: Seong Il Jeong, Chul Kyu Jin, Hyung Yoon Seo, Jong Deok Kim, and Chung Gil Kang
- 発行年: 2016
- 掲載学術誌/学会: International Journal of Precision Engineering and Manufacturing
- キーワード: High pressure die casting (高圧ダイカスト), Gate system (ゲートシステム), Casting simulation (鋳造シミュレーション), Casting aluminium alloy (鋳造アルミニウム合金), Casting defects (鋳造欠陥)
2. 抄録:
高圧ダイカストを適用した自動車用クラッチハウジング部品を製造するために、以下の3つのゲートシステム設計が考慮されました。これらのゲートシステム設計を実際の実験で採用するにはコストと時間がかかりすぎるため、代わりに鋳造シミュレーションプログラムが使用されました。金型を充填する要素としての流動挙動が解析されました。溶湯が金型に完全に充填された後の空気圧とエアポケットに基づいて、最終的なゲートシステム設計が選択されました。5つのゲートを持つ3番目のゲートシステム設計は、他の設計よりも欠陥が少なく、均一であると予想されました。冷却チャネルとチルベントが設計されました。実際の鋳造試験では、合計5つの製品が製造されました。すべて健全であり、充填不足箇所や表面欠陥はありませんでした。実際の試験では、解析に基づいて引け巣の発生が予想されましたが、実際に引け巣が発生した製造品のそれらとは正確には一致しませんでしたが、類似していました。硬さは場所に関わらず約84 HVでした。
3. 緒言:
高圧ダイカストは、高速・高圧を用いる鋳造プロセスです。非鉄金属を金型に急速に充填し、その後凝固させ、鋳物を金型から取り出します。この方法は、複雑で精密な形状を持ち、均一な品質を持つ製品の大量生産に適しています。さらに、薄板タイプの製品を製造することも可能です。適用分野は拡大し続けています。高圧ダイカストはアルミニウム合金にしばしば適用され、最近では、自動車メーカーがマグネシウム合金を用いた高圧および高真空ダイカストの適用による大量生産の研究を行っています。
高圧ダイカストで発生しうる欠陥には、空気や他の物質の巻き込みなどの流動欠陥、充填プロセス中の微小気孔(ブローホールやピンホール)、凝固プロセス中の引け巣などがあります。過去の金型設計では、金型設計者や現場技術者の試行錯誤法に多くの困難がありましたが、最近の高圧鋳造金型設計では、初期開発段階から充填および凝固プロセスに対してComputer Aided Engineering (CAE)を採用しており、製品品質の予測と評価に基づいて最適な金型設計計画を確立することが可能になっています。さらに、多くの設計者が現場経験に基づいてCAEと組み合わせた金型設計手法を採用するにつれて、不良率はコスト削減と開発期間短縮とともに減少しています。この分野で発表された論文のほとんどは、鋳造シミュレーションや鋳造技術、および大量生産の方法で製造コストを削減するための改善方法に焦点を当てています。対照的に、製品の品質を決定する金型設計に関する研究はほとんどありません。
本研究では、鋳造ソフトウェアであるMAGMAを用いて、自動車エンジンの動力を制御または伝達するクラッチハウジング製品の鋳造シミュレーションを含みます。まず第一に、充填および凝固プロセスにおける潜在的な鋳造欠陥を予測または防止することにより、製品を大量生産するための最適なゲートシステム設計と鋳造条件が求められました。データベースに基づいて、鋳造コストを最小化する方法が次に求められました。最適なゲートシステム設計が金型設計に適用され、金型製作後、鋳造プロセスにおける欠陥を最小限に抑えた可能な限り最高の品質の製品が製造されました。
4. 研究の概要:
研究テーマの背景:
高圧ダイカスト(HPDC)は、複雑で精密、かつ均一な品質の部品、特に自動車産業向けのアルミニウムやマグネシウムなどの非鉄合金製の薄肉部品の大量生産に広く用いられる製造プロセスです。しかし、HPDCプロセスは、流動欠陥(空気巻き込み)、微小気孔(ブローホール、ピンホール)、引け巣などの欠陥が発生しやすい傾向があります。
従来の研究状況:
従来、金型設計は設計者や技術者の試行錯誤の経験に大きく依存していました。近年では、初期設計段階から充填および凝固プロセスをシミュレーションするために、Computer Aided Engineering(CAE)ツールがますます採用されています。これにより、金型設計の予測、評価、最適化が可能となり、欠陥、コスト、開発期間の削減につながっています。多くの研究がシミュレーション技術やコスト削減に焦点を当てていますが、金型設計が製品品質にどのように影響するかに特化した研究は比較的少ないです。
研究の目的:
本研究は、鋳造シミュレーションソフトウェア(MAGMAsoft)を利用して、HPDCによりALDC 12アルミニウム合金で製造される自動車用クラッチハウジング部品のための最適な金型を設計することを目的としました。具体的な目標は、最良のゲートシステム設計と鋳造条件を決定し、充填および凝固中の潜在的な鋳造欠陥を予測・防止し、シミュレーションデータに基づいて製造コストを最小化し、最終的に最適化された金型設計を通じて欠陥を最小限に抑えた高品質な部品を生産することでした。
研究の核心:
研究の核心は、Pro/ENGINEERとMAGMAsoftを使用してクラッチハウジング部品用の3つの異なるゲートシステム(Case I、II、III)を設計し、シミュレーションすることでした。Case Iは垂直ゲートを特徴とし、Case IIはサイドゲートを含む4つのゲートを使用し、Case IIIは流れを制御するためにCase IIを5つのゲートに変更したものです。冷却チャネルは計算された熱負荷(式1~8)に基づいて設計され、スポット冷却とライン冷却を組み合わせています。ガス排出を容易にするために、波形のチルベント(STD 61材)が設計されました。MAGMAsoftを使用して鋳造シミュレーションが実施され、定義されたHPDC条件下(ALDC 12合金、STD 61金型、特定の温度、速度、1600トンマシン)で各ゲート設計の充填挙動、温度分布、空気接触、空気圧、凝固パターンが解析されました。最も均一な充填と最も少ない欠陥を予測したシミュレーション結果に基づき、Case IIIが選択されました。最後に、Case IIIの金型設計を用いて実際の鋳造実験が行われ、部品を生産し、その品質(外観検査、ミクロ組織、硬さ)を分析し、予測された欠陥(引け巣)と実際の発生状況を比較することで、シミュレーション結果を検証しました。
5. 研究方法論
研究デザイン:
本研究では、計算シミュレーションと実験的検証を組み合わせた比較アプローチを採用しました。クラッチハウジング金型のための3つの異なるゲートシステム設計がモデル化され、シミュレーションされました。最良の結果をもたらすと予測された設計(Case III)が選択、製造され、実際の高圧ダイカスト試験で使用されて、シミュレーション予測を検証し、最終製品の品質を評価しました。
データ収集と分析方法:
- シミュレーション: MAGMAsoft鋳造シミュレーションソフトウェアが使用されました。解析は、流体の流れと熱伝達に関する支配方程式(質量保存則 式(9)、運動量保存則/Navier-stokes 式(10)、エネルギー保存則 式(11)、Volume of Fluid法 式(12))に基づいており、特定のメッシュ解像度(100万以上の金属セル)を持つ有限体積法(FVM)を用いて解かれました。解析されたシミュレーション出力には、溶湯流動パターン(充填挙動、速度)、温度分布、空気接触、空気圧分布、および凝固進行が含まれ、充填不足、空気巻き込み、引け巣などの潜在的な欠陥を予測しました。
- 実験: 実際のHPDCは、1600トンのコールドチャンバーマシン、ALDC 12アルミニウム合金、および最適化された金型(Case III設計)を使用して実施されました。プロセスパラメータはシミュレーション設定を反映しました。金型の予熱温度は、非接触サーモグラフィカメラを使用して測定されました。5つの鋳造部品が製造され、欠陥(充填不足、亀裂、フローマーク)について目視検査されました。充填されたチルベントの形状が検査されました。部品の平均厚さおよび厚肉部の断面についてミクロ組織分析が行われました。サンプル部品の7つの異なる位置で、200gの荷重を用いてビッカース硬さが測定されました。
- 比較: シミュレーション予測、特に充填均一性、欠陥位置(エアポケット、引け巣)が、実験鋳造から得られた結果と定性的および(該当する場合)定量的に比較されました。
研究トピックと範囲:
本研究は、ALDC 12アルミニウム合金を用いた高圧ダイカストで製造される自動車用クラッチハウジング部品の金型設計に焦点を当てました。範囲は以下の通りです:
- 3つの異なるゲートシステム(ランナー、ゲート、オーバーフロー)の設計と比較。
- 熱計算に基づく金型冷却チャネルの設計。
- ガス排出のためのチルベントの設計。
- MAGMAsoftを用いた充填、凝固、および潜在的欠陥を予測する鋳造シミュレーション。
- シミュレーション結果に基づく最適なゲートシステムの選択。
- 実際の鋳造試験(5ショット)による実験的検証。
- 鋳造製品の品質分析(外観検査、ミクロ組織、硬さ試験を含む)。
- シミュレーション予測(特に気孔)と実験結果との比較。
6. 主要な結果:
主要な結果:
- 3つのゲートシステム(Case I、II、III)のシミュレーション解析により、Case III(5ゲート)がCase IおよびCase IIと比較して最も均一な充填パターンと温度分布を提供し、潜在的により少ない空気接触とより良い空気圧管理を示すことがわかりました(Fig. 5, Fig. 6, Table 5)。
- Case IIIは、シミュレーションで予測された全体的な「良好(good)」な性能、特にCase Iと比較して潜在的な酸化物/介在物排出問題への対応、およびCase IIよりも均一な流れを提供することから、最適な設計として選択されました(Table 5)。
- 冷却チャネル設計計算により、ライン冷却とスポット冷却(スポット冷却の方が1.4~2.0倍効果的)の両方を考慮した必要な有効長さが得られました(Section 2.1.2, Fig. 2)。
- 異なる厚さ(1 mm、0.8 mm、0.6 mm)の8つの波とクッション部を持つ特定のチルベント設計が実装されました(Section 2.1.3, Fig. 3)。
- Case IIIの凝固シミュレーションでは、厚肉の中央部と左側領域での冷却が遅いことが予測され、そこに引け巣が発生する確率が高いことを示しました(Fig. 8)。
- Case IIIの金型設計を用いた実験鋳造では、充填不足や表面のフローマークなしに、5つの完全なクラッチハウジング部品が成功裏に製造されました(Fig. 11)。
- 最初の実験ショットにおけるチルベントは、4番目から5番目の波まで充填され、ガス抜きとしての機能を示しました(Fig. 12)。
- 実験的に鋳造された部品の厚肉部で引け巣が観察され、これはシミュレーションによって予測された位置と大まかには相関していましたが、完全に一致はせず、実際のプロセス変動の影響を示唆しました(Fig. 13)。
- ミクロ組織分析により、異なる凝固速度のため、平均厚さ部(共晶ネットワーク中の針状Si)と厚肉部(初晶α-Al相+不明瞭なSi粒子を持つ共晶相)との間に違いがあることが明らかになりました(Fig. 14)。
- ビッカース硬さ測定では、鋳造部品の様々な位置で約84.05 HVの一貫した硬さが示されました(Fig. 15)。
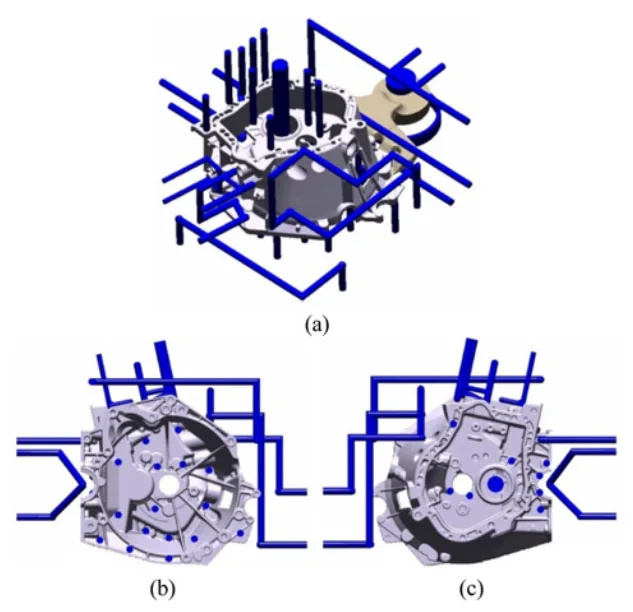
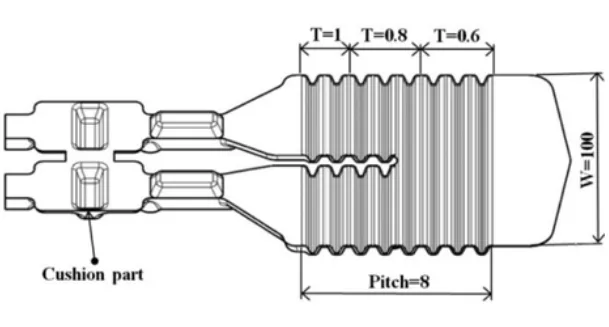
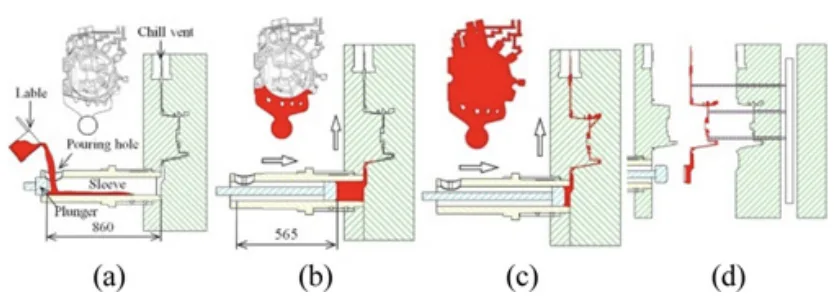
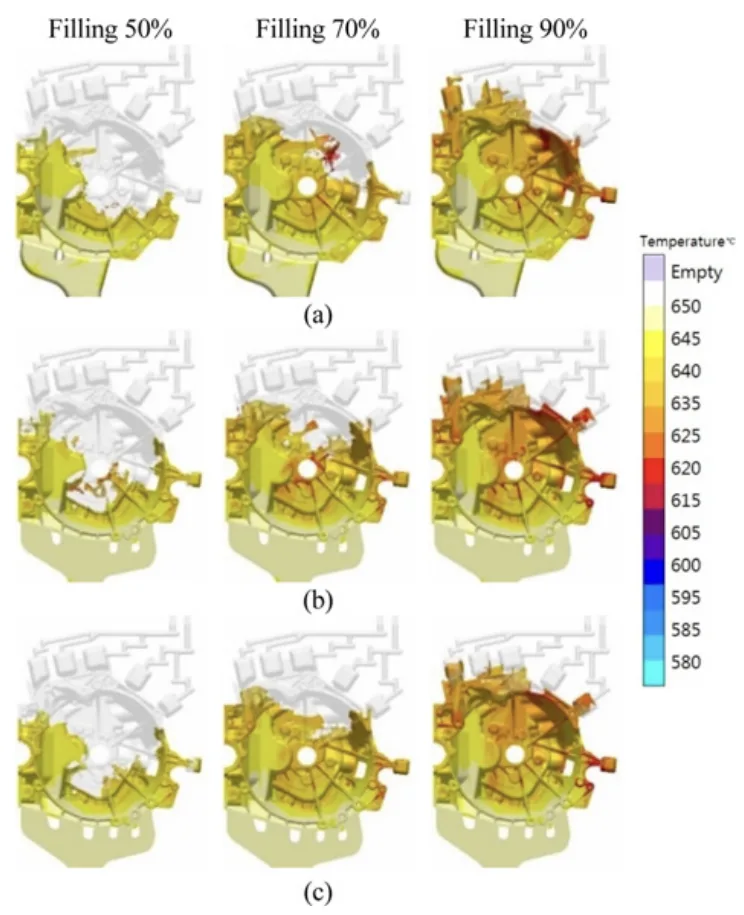
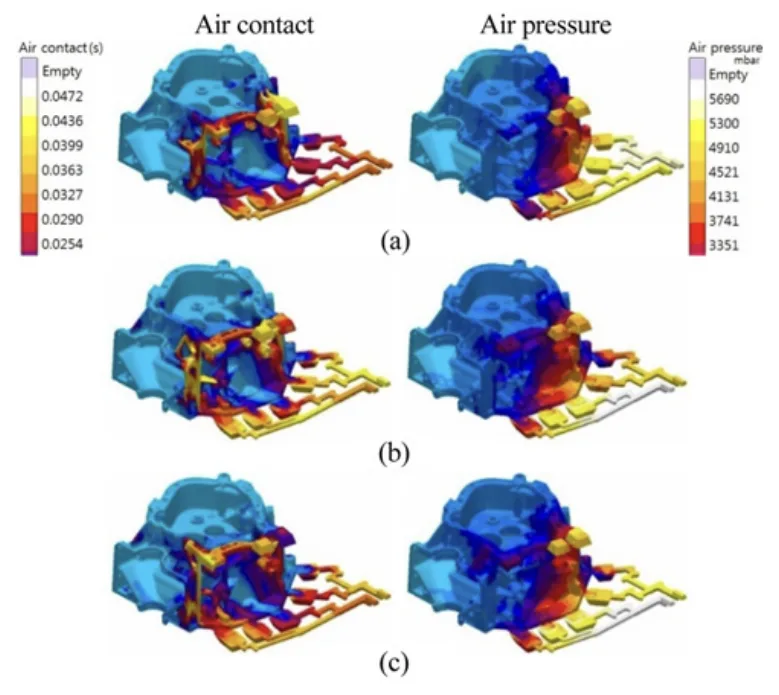
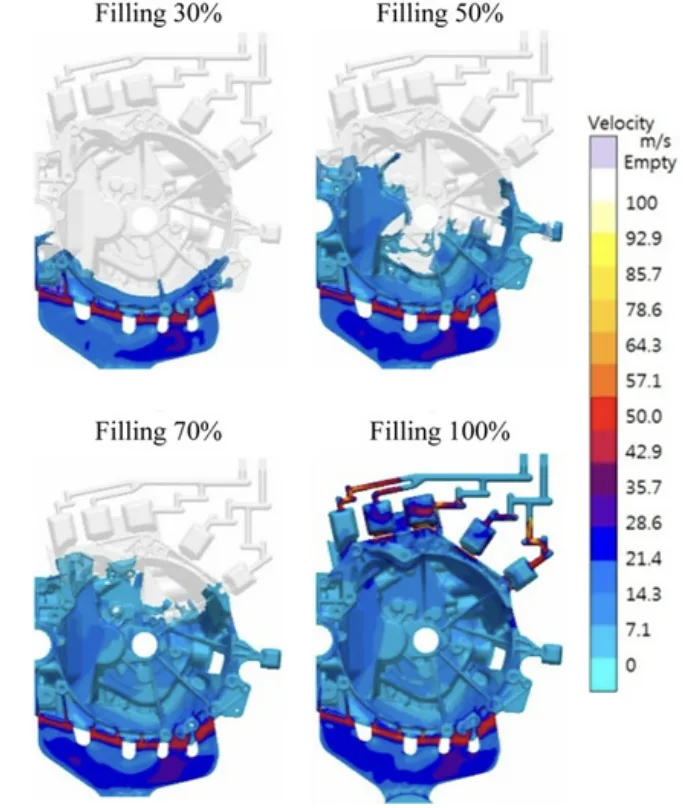
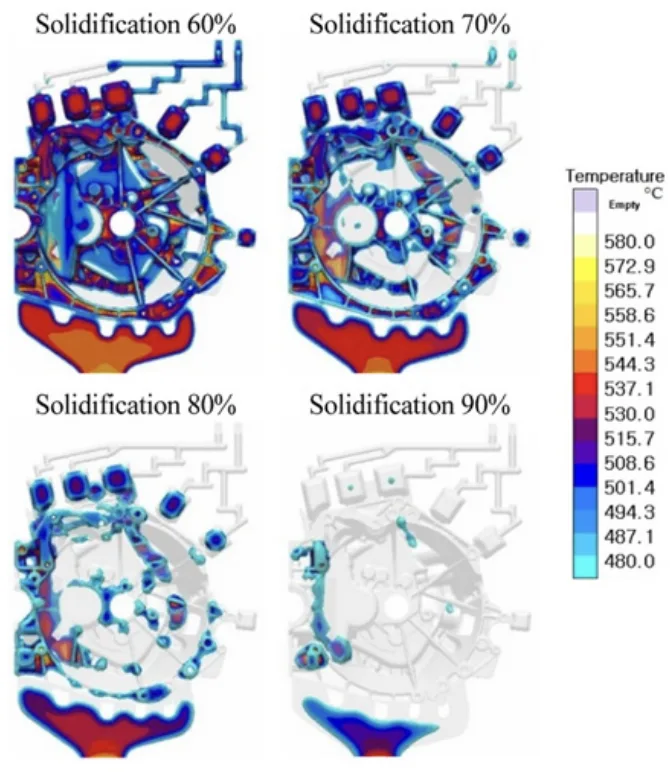
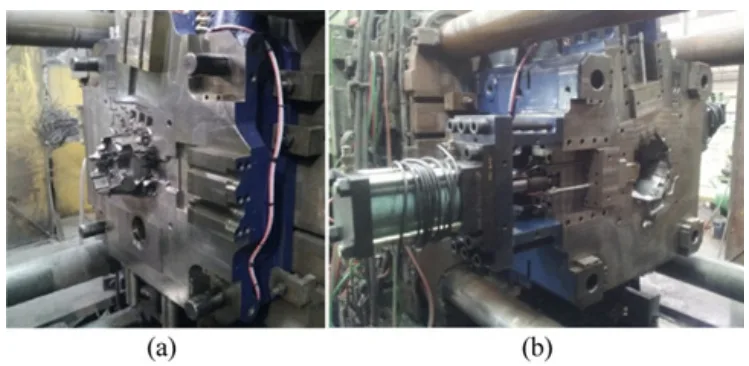
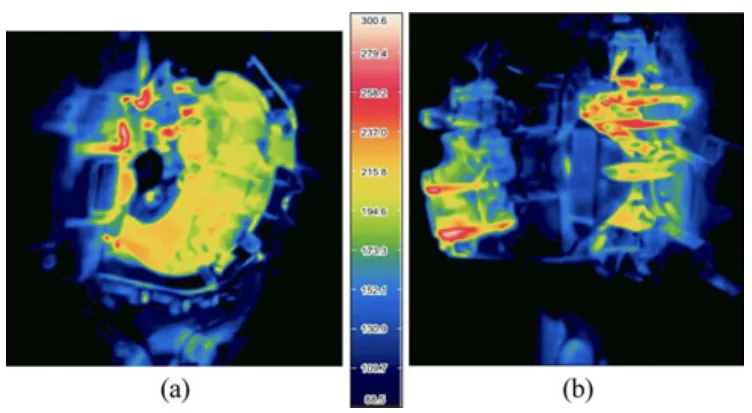
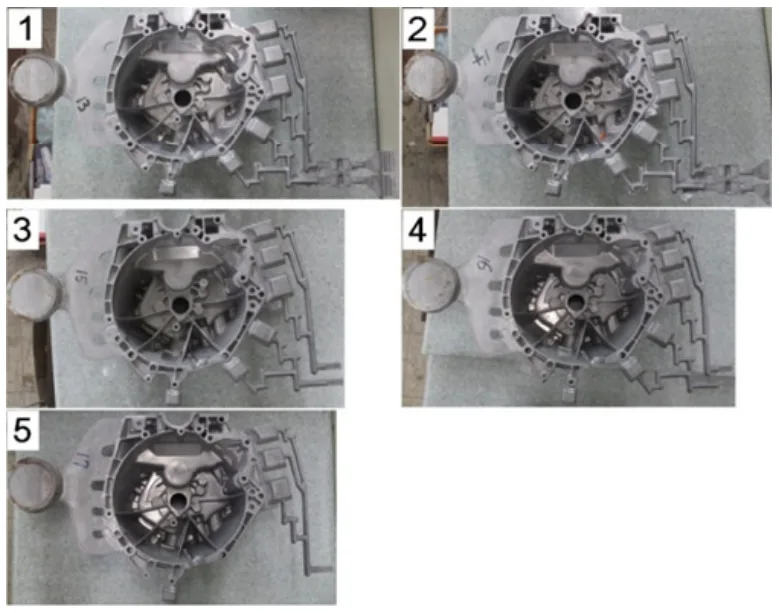
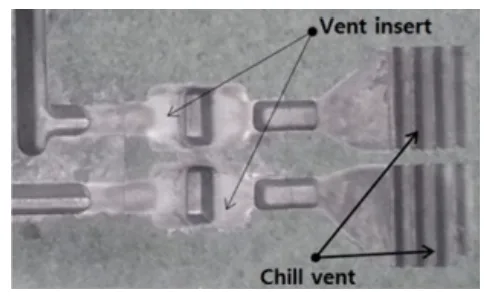
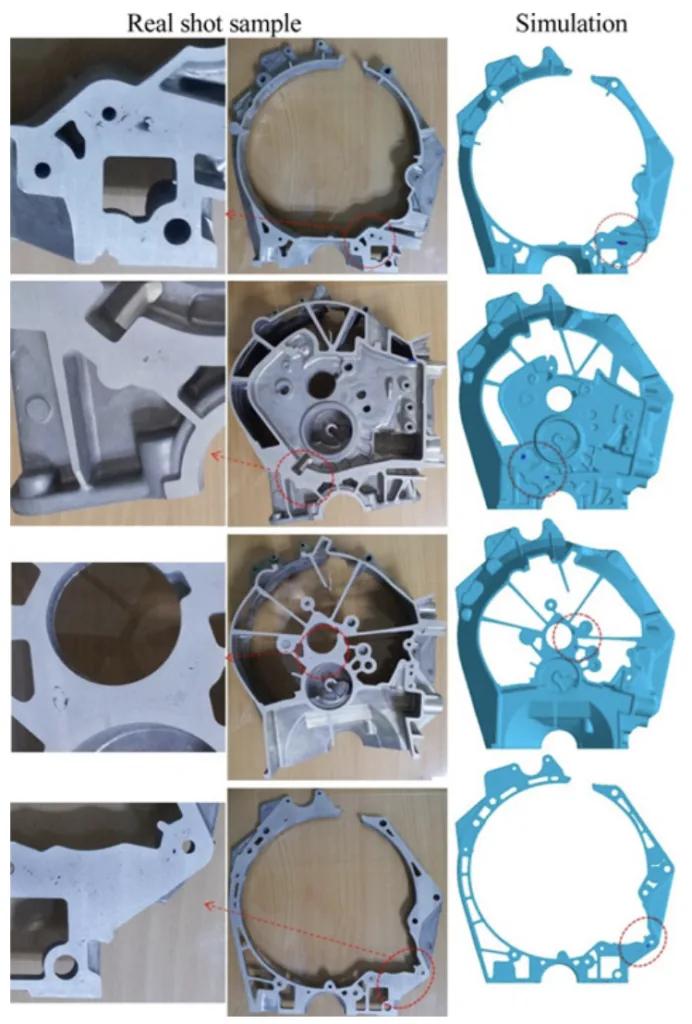
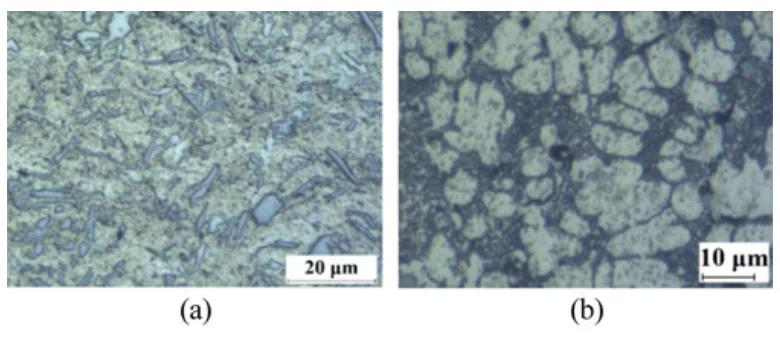
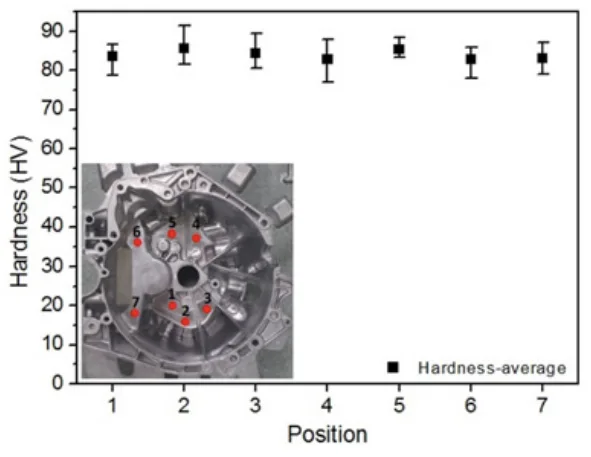
図の名称リスト:
- Fig. 1 Gating system design of clutch housing: (a) case I, (b) case II, and (c) case III
- Fig. 2 Cooling line of mould: (a) 3D view, (b) fixed mould view and (c) movable mould view
- Fig. 3 The chill vent for mould
- Fig. 4 Schematic diagram of the high pressure die casting process: (a) pouring melt, (b) slow shot, (c) fast shot, and (d) casting removal by ejector
- Fig. 5 Filling behavior by different gating systems: (a) case I, (b) case II, and (c) case III
- Fig. 6 Air contact and air pressure by different gating systems: (a) case I, (b) case II, and (c) case III
- Fig. 7 Velocity distribution of case III gating system
- Fig. 8 Solidification behavior of case III gating system
- Fig. 9 Moulds assembled high pressure die casting machine: (a) fixed mould and (b) movable mould
- Fig. 10 Block diagram of multi-modal chatter model of a high speed machining center: (a) fixed mould and (b) movable mould
- Fig. 11 Fabricated clutch housing castings: 1 first shot, 2 second shot, 3 third shot, 4 fourth shot and 5 fifth shot
- Fig. 12 Chill vent connected with first shot castings
- Fig. 13 Comparison of porosity distribution between simulation and real shot test
- Fig. 14 Microstructures of clutch housing in different positions: (a) normal thickness and (b) thick thickness
- Fig. 15 Vickers hardness at different positions
7. 結論:
本研究では、MAGMAsoftを用いてALDC12を使用した自動車用クラッチハウジング部品のゲートシステムを設計しました。実際のショットにより、充填不足箇所のない完璧なクラッチハウジングサンプルが製造されました。シミュレーションと実験の結果は以下のように要約されます:
- 鋳造シミュレーションプログラムを通じて、5つのゲートを持つゲートシステム設計が、2つおよび4つのゲートを持つ設計よりも製品をより徹底的かつ均一に充填し、製品全体で均一な温度分布をもたらし、他の設計よりも製品内のエアポケットが少ないことが実証されました。解析結果に基づき、5つのゲートを持つゲートシステム設計が選択されました。
- 金型に必要な冷却管の有効長さに関して、スポット冷却効率はライン冷却の1.4~2.0倍優れていました。したがって、全体にスポット冷却を適用することで引け巣欠陥を最小限に抑えることが期待されます。
- ショットテストを通じて製造されたオーバーフローを含む5つのクラッチハウジングサンプルはすべて、充填不足箇所なしに完全に形成されました。表面には亀裂やフローマークもありませんでした。ビッカース硬さは場所に関わらず約84HVでした。
- 製品の厚肉部では凝固が遅かったため、製品内部に引け巣が形成されました。引け巣の発生位置に関して、鋳造シミュレーションの結果は実際の発生位置とは異なりましたが、これはおそらく現場条件における様々な要因によるものです。結果が示すように、鋳造シミュレーションに絶対的に依存するのではなく、それを参照して傾向を把握し予測することが望ましいです。
8. 参考文献:
- [1] Jin, C. K. and Kang, C. G, "Fabrication Process Analysis and Experimental Verification for Aluminum Bipolar Plates in Fuel Cells by Vacuum Die-Casting," Journal of Power Sources, Vol. 196, No. 20, pp. 8241-8249, 2011.
- [2] Jin, C. K. and Kang, C. G., "Fabrication by Vacuum Die Casting and Simulation of Aluminum Bipolar Plates with Micro-Channels on Both Sides for Proton Exchange Membrane (PEM) Fuel Cells," International Journal of Hydrogen Energy, Vol. 37, No. 2, pp. 1661-1676, 2012.
- [3] Choi, S., Kim, Y., Cho, J., and Kang, C., "Influence of Die Casting Process Parameters on Castability and Properties of Thin Walled Aluminium Housings," International Journal of Cast Metals Research, Vol. 21, No. 1-4, pp. 330-333, 2008.
- [4] Dørum, C., Hopperstad, O., Berstad, T., and Dispinar, D., "Numerical Modelling of Magnesium Die-Castings using Stochastic Fracture Parameters," Engineering Fracture Mechanics, Vol. 76, No. 14, pp. 2232-2248, 2009.
- [5] Cho, C. Y., Uan, J. Y., and Lin, H. J., "Surface Compositional Inhomogeneity and Subsurface Microstructures in a Thin-Walled AZ91D Plate Formed by Hot-Chamber Die Casting," Materials Science and Engineering: A, Vol. 402, No. 1, pp. 193-202, 2005.
- [6] Timelli, G. and Bonollo, F., "Fluidity of Aluminium Die Castings Alloy," International Journal of Cast Metals Research, Vol. 20, No. 6, pp. 304-311, 2007.
- [7] Zhao, H. D., Wang, F., Li, Y. Y., and Xia, W., "Experimental And Numerical Analysis of Gas Entrapment Defects in Plate ADC12 Die Castings," Journal of Materials Processing Technology, Vol. 209, No. 9, pp. 4537-4542, 2009.
- [8] Tian, C., Law, J., Van Der Touw, J., Murray, M., Yao, J.-Y., Graham, D., and John, D.S., "Effect of Melt Cleanliness on the Formation of Porosity Defects in Automotive Aluminium High Pressure Die Castings," Journal of Materials Processing Technology, Vol. 122, No. 1, pp. 82-93, 2002.
- [9] Kim, Y.-C., Kang, C.-S., Cho, J.-I., Jeong, C.-Y., Choi, S.-W., and Hong, S.-K., "Die Casting Mold Design of the Thin-Walled Aluminum Case by Computational Solidification Simulation," Journal of Materials Science and Technology, Vol. 24, No. 3, pp. 383-388, 2008.
- [10] Chang, Q. M., Chen, C. J., Zhang, S. C., Schwam, D., and Wallace, J. F., "Effects of Process Parameters on Quality of Squeeze Casting A356 Alloy," International Journal of Cast Metals Research, Vol. 23, No. 1, pp. 30-36, 2013.
- [11] Hu, B. H., Tong, K. K., Niu, X. P., and Pinwill, I., "Design and Optimisation of Runner and Gating Systems for the Die Casting of Thin-Walled Magnesium Telecommunication Parts through Numerical Simulation," Journal of Materials Processing Technology, Vol. 105, No. 1-2, pp. 128-133, 2000.
- [12] Hangai, Y. and Kitahara, S., "Quantitative Evaluation of Porosity in Aluminum Alloy Die Castings by Fractal Analysis of Spatial Distribution of Area," Materials & Design, Vol. 30, No. 4, pp. 1169-1173, 2009.
- [13] Chen, J. H., Hwang, W. S., Wu, C. H., and Lu, S. S., "Design of Die Casting Process of Top Cover of Automobile Generator Through Numerical Simulations and Its Experimental Validation," International Journal of Cast Metals Research, Vol. 24, No. 3-4, pp. 163-169, 2011.
- [14] Domkin, K., Hattel, J. H., and Thorborg, J., "Modeling Of High Temperature-and Diffusion-Controlled Die Soldering in Aluminum High Pressure Die Casting," Journal of Materials Processing Technology, Vol. 209, No. 8, pp. 4051-4061, 2009.
- [15] Kim, G.-Y., "Die Casting Die Designing (3)-Design of Die Cooling," Journal of Korea Foundry Society, Vol. 19, No. 4, pp. 369-369, 1999.
- [16] Kang, B.-H., Kim, T.-B., and Kim, K.-Y., "Evaluation on Performance of Chill Vent In High Pressure Die Casting by using a Commercial Software," Journal of Korea Foundry Society, Vol. 32, No. 3, pp. 133-137, 2012.
9. 著作権:
- 本資料は「Seong Il Jeong et al.」による論文です。「Mould Design for Clutch Housing Parts using a Casting Simulation of High Pressure Die Casting」に基づいています。
- 論文の出典: https://doi.org/10.1007/s12541-016-0178-6
本資料は上記の論文に基づいて要約されたものであり、商業目的での無断使用は禁じられています。
Copyright © 2025 CASTMAN. All rights reserved.