本論文概要は、['MDPI']発行の['高圧ダイカストで製造されたアルミニウムフォームとマグネシウム複合鋳造']論文に基づいて作成されました。
1. 概要:
- タイトル:高圧ダイカストで製造されたアルミニウムフォームとマグネシウム複合鋳造
- 著者:Iban Vicario, Ignacio Crespo, Luis Maria Plaza, Patricia Caballero, Ion Kepa Idoiaga
- 発行年:2016年
- 発行ジャーナル/学術団体:Metals
- キーワード:高圧ダイカスト (HPDC); ハイブリッドマグネシウムアルミニウムフォーム鋳造複合材; アルミニウムフォームコア; マグネシウム鋳造複合材
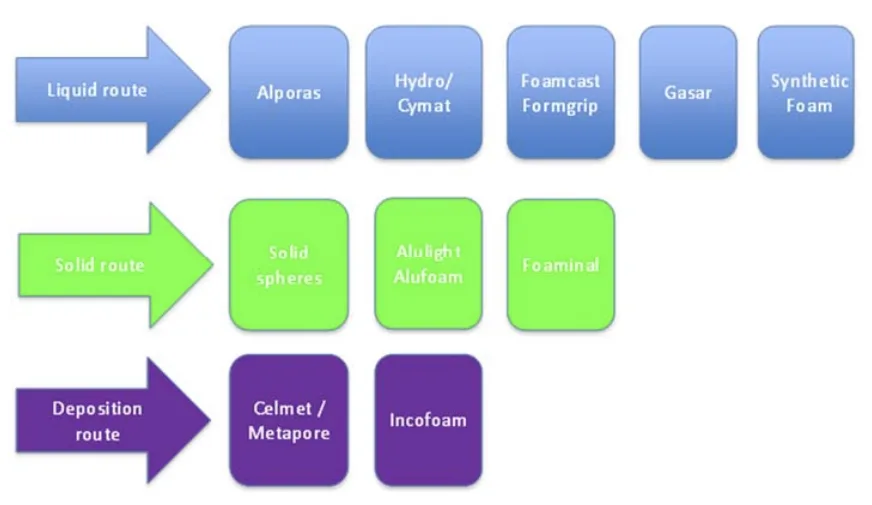
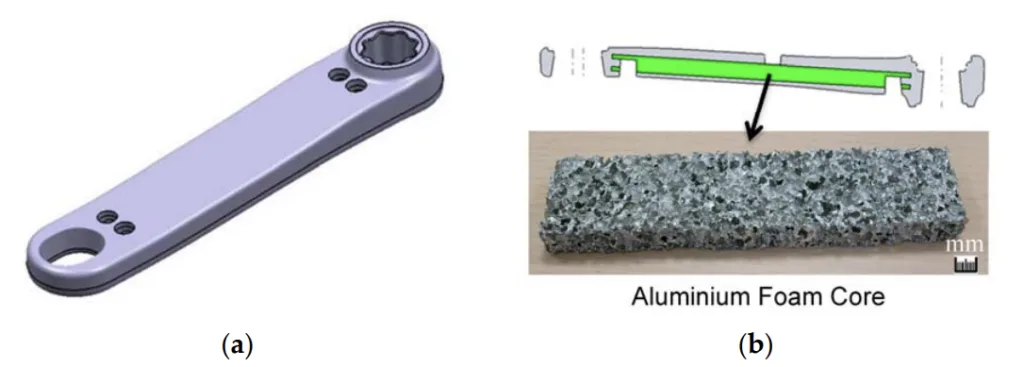
2. 抄録または序論
本研究は、軽量複合部品の製造における高圧ダイカスト(HPDC)技術を調査しています。本研究の目的は、マグネシウム鋳造部品にコアとして使用される様々なアルミニウムフォームとHPDC射出パラメータが、特性と重量に及ぼす影響を評価することです。本論文では、部品特性と軽量化のバランスを達成することに焦点を当て、HPDCマグネシウム部品の軽量化のためにアルミニウムフォームを使用することの妥当性を探求しています。研究では、最終的な鋳造製品の品質に対する様々なアルミニウムフォームと射出パラメータの影響を評価するために、アルミニウムフォームの種類と密度、金属温度、プランジャ速度、および増圧を適切な値の範囲内で変化させました。本研究では、アルミニウムフォームコアを使用して健全な複合鋳造品を製造することに成功し、特に自転車部品のデモンストレーション部品など、軽量化が求められる用途において、マグネシウム-アルミニウムフォーム複合材の製造におけるHPDCの可能性を実証しました。
3. 研究背景:
研究テーマの背景:
本研究の主な推進力は、燃料消費量と二酸化炭素排出量を削減するための車両設計、特に輸送産業における軽量化の需要の高まりです。鋼鉄や鉄などの重い材料を、プラスチック、炭素繊維、アルミニウム、マグネシウム合金などのより軽量な代替材料に置き換えることが主要な傾向です。自転車産業の場合、この傾向は、高性能自転車に炭素繊維を使用し、鋼鉄、アルミニウム、チタンを使用しない明確な傾向に現れています。HPDCによって製造されたマグネシウム部品は、すでに自動車および自転車分野で利用されており、業界は、マグネシウム軽量構造によって提供される軽量性と機械的特性のバランスが有利となる新たな用途を模索し続けています。HPDCは、年間5,000〜10,000個以上の大量生産に経済的に実現可能な高生産性プロセスとして強調されています [2]。
既存研究の現状:
既存の研究では、HPDCは鋳造品質に影響を与える多数のパラメータによって影響を受ける複雑なプロセスであることを認識しています [6]。主なパラメータには、射出パラメータ、金型温度、合金の鋳造性、部品形状、冷却速度、および装置の種類が含まれます。内部気孔はHPDC部品の既知の欠点であり、他の鋳造方法と比較して熱処理と機械的特性を制限します。気孔を緩和し、HPDC部品の性能を向上させるための戦略が模索されており、これには新しいHPDCバリアントが含まれます。アルミニウム-マグネシウム複合材を使用することは、軽量化戦略の1つであり [13]、BWMアルミニウム-マグネシウムブロック [14] がその例です。しかし、マグネシウムとアルミニウムコア間の金属結合を達成することは、アルミニウムのアルミナ表面層のために困難です [15]。軽量化のための代替方法には、塩コアを使用して中空部品を作成すること [16-18] や、改善された特性を持つ新しいHPDC合金を開発すること [19] があります。アルミニウムフォームの使用は重要な進歩として認識されており [20]、「図1. アルミニウムフォームの製造に最も多く用いられるプロセスの一部」に示され、「表1. 様々なフォーム製造ルートの長所と短所」に要約されている様々な製造方法があります。
研究の必要性:
HPDCを介してアルミニウムフォームコアを使用して複合鋳造品を得る際の主な課題は、高速および特定の圧力によるコアの変形または崩壊を防ぎながら、鋳造欠陥を回避することです。本論文では、アルミニウムフォームコア複合鋳造に特化したHPDCパラメータを理解し、制御することにギャップがあることを特定しています。したがって、アルミニウムフォームコアを使用して高品質の複合部品を得るためにHPDCパラメータを分析および制御する研究が必要であり、この特定の用途におけるコアの完全性と鋳造の健全性の課題に対処する必要があります。
4. 研究目的と研究課題:
研究目的:
主な研究目的は、機械的特性と軽量化の妥協点を達成する複合鋳造品を製造するために、様々なアルミニウムフォームとHPDC射出パラメータの影響を評価することです。最終的な目標は、現在、鍛造アルミニウム、チタン、マグネシウム、または炭素繊維などの材料を使用して製造されている自転車用ロッドを製造するためのHPDCプロセスを開発することです。HPDC機能に合わせて再設計された自転車用ロッドは、「図2. (a) 3Dロッド設計; および (b) アルミニウムフォームコアの配置と例の詳細」に示されています。
主要な研究課題:
主要な研究課題は、以下の最適な組み合わせを決定することに焦点を当てています。
- アルミニウムフォームの種類(Alporas ALPO-PLA-03 [27,28]、Formgripベースの加工フォーム [29,30]、および0.4%TiB2 AlSi12 Alulightフォーム [31-34])と密度。
- 金属温度、プランジャ速度、および増圧を含むHPDC射出パラメータ。
- コアの配置とスクイズピンの適合性。
これらの調査は、軽量構造用途に適したアルミニウムフォームコアを使用して、健全なマグネシウム-アルミニウム複合鋳造品を生成するパラメータを特定することを目的としています。
研究仮説:
正式な仮説として明示されていませんが、研究は以下の前提の下で実施されています。
- アルミニウムフォームの種類と密度を慎重に選択し、HPDCパラメータを最適化することにより、大幅な軽量化を実現した健全なマグネシウム-アルミニウム複合鋳造品を製造することが可能です。
- 外皮を有するアルミニウムフォームは、高い射出圧力に対する強度が高いため、HPDCにおいてコアとしてより優れた性能を示すでしょう。
- 適切なコア配置と制御された射出速度は、フォームの損傷を防ぎ、鋳造品質を確保するために重要です。
5. 研究方法論
研究デザイン:
本研究では、アルミニウムフォームの種類とHPDCプロセスパラメータの体系的な変化を伴う実験的デザインを採用しています。AM60B合金と3種類の異なるアルミニウムフォームコアを使用して鋳造品を製造しました。圧力効果がフォームの完全性に及ぼす影響を評価するために、ダイカスト、プラスチック射出、およびHPDCプロセスを使用した予備試験を実施しました。その後、マグネシウム-アルミニウムフォーム複合鋳造品を製造するために、950トンのHPDCマシンでHPDC試験を実施しました。
データ収集方法:
データ収集方法は以下の通りです。
- 目視検査:外部鋳造品質を評価し、肉眼で見える欠陥を特定します。
- 放射線検査(RX):論文で言及されているGeneral Electric X-cube 44XL(160 kV)を使用して、内部鋳造の健全性を評価し、気孔を検出し、アルミニウムフォームコアの完全性を検証します。
- 引張試験:複合ロッドの機械的特性を決定するために、クロスヘッド速度5 mm/minのInstron 3369マシンを使用して、室温でUNE-EN ISO 6892-1 B:2010規格に従って実施されました。
分析方法:
分析には以下が含まれていました。
- 定性的評価:目視およびRX検査の結果を定性的に分析して、鋳造欠陥、フォームの変形、およびコアの配置を評価しました。
- 定量的分析:引張試験データを使用して、引張応力、極限引張強度、および伸びを計算し、AM60B合金と複合鋳造品間の機械的特性を定量的に比較できるようにしました。
研究対象と範囲:
本研究は、以下の事項に焦点を当てました。
- 材料:AM60Bマグネシウム合金と3種類のクローズドセルアルミニウムフォーム:Alporas ALPO-PLA-03、Formgripベースのフォーム、およびAlulight 0.4%TiB2 AlSi12フォーム。
- プロセス:高圧ダイカスト(HPDC)。
- 部品:自転車用ロッドのデモンストレーション部品。
- パラメータ:アルミニウムフォームの種類と密度、金属鋳造温度(680℃および720℃)、射出圧力(16〜80 MPa、スクイズピンの場合は最大200 MPa)、および射出速度(20〜80 m/s)。
6. 主な研究結果:
主要な研究結果:
本研究の主な知見は以下の通りです。
- 金属鋳造温度:「図8. (a) 短絡充填および冷間接合欠陥; および (b) ガス気孔欠陥」で観察されたように、短絡充填/冷間接合欠陥を回避するためには、AM60B合金の最小注湯温度720℃が必要でした。
- アルミニウムフォームの完全性:「表4. プラスチック射出後のアルミニウムフォームの完全性」でわかるように、Alulightフォームは、AlporasフォームおよびFormgripフォームと比較して、HPDC圧力に対する優れた耐性を示しました。0.54〜1.55 Kg/dm³の密度のAlulightフォームは、40 MPaの圧力に耐えることができました。
- 外皮の重要性:「図9. AM60Bで覆われた中央アルミニウムコア」で説明されているように、Alulightのように外皮を有するアルミニウムフォームは、マグネシウムの過剰射出中にガス気孔とコアの崩壊を防ぎました。「図13. (a) ダイにスキン付きフォームとスキンなし領域を配置; および (b) スキンなし領域からのフォームからのガス放出」でわかるように、スキンがないフォームまたは損傷したスキンを有するフォームは、ガス気孔を引き起こしました。
- コアの配置:「図15. コアの金属流れに対する水平配置」および「図16. 金属流れに対する垂直コア配置」でわかるように、金属流れに対するアルミニウムフォームコアの垂直配置は損傷を最小限に抑えましたが、水平配置はせん断破壊を引き起こしました。
- 射出速度:「図18. 低減された二次速度(20 m/s)HPDC鋳造部品」および「図19. 標準パラメータでコアフォームで射出されたHPDC」でわかるように、低減された一次射出速度は部品品質に悪影響を及ぼしましたが、80 m/sの二次速度と80 MPaの圧力の標準HPDCパラメータは健全な部品を生成しました。
- 軽量化:0.56 Kg/dm³の密度のAlulightタイプアルミニウムフォームを使用すると、自転車用ロッドのデモンストレーション部品の重量が約35%減少しました。
- 機械的特性:「表5. 複合ロッドの取得された特性」は、AM60B、複合材、および外挿された複合材特性の引張特性を示しています。直接的な化学結合は達成されませんでしたが、複合ロッドは軽量化とともに合理的な機械的特性を示しました。
提示されたデータの分析:
データ分析により、Alulightフォーム、特にその外皮が、試験されたフォームの中でHPDCマグネシウム複合鋳造に最も適したアルミニウムフォームコアであることが明らかになりました。外皮は、射出圧力に耐えるために必要な強度を提供し、マグネシウム溶融物へのガス放出を防ぎます。720℃の金属温度と標準的な射出速度および圧力を含む最適なHPDCパラメータは、健全な複合鋳造品を製造するために重要です。スクイズピンは、過度の圧力のためにアルミニウムフォームコアの近くの領域には適していません。達成された35%の軽量化は、軽量部品製造に対するこのアプローチの可能性を実証しています。機械的特性分析は、複合材において降伏強度(YS)および極限引張強度(UTS)が固体AM60Bと比較して減少していることを示していますが、外挿された値は、最適化された設計と結合により、複合アプローチが重量と性能の実行可能なバランスを提供できることを示唆しています。
図のリスト:
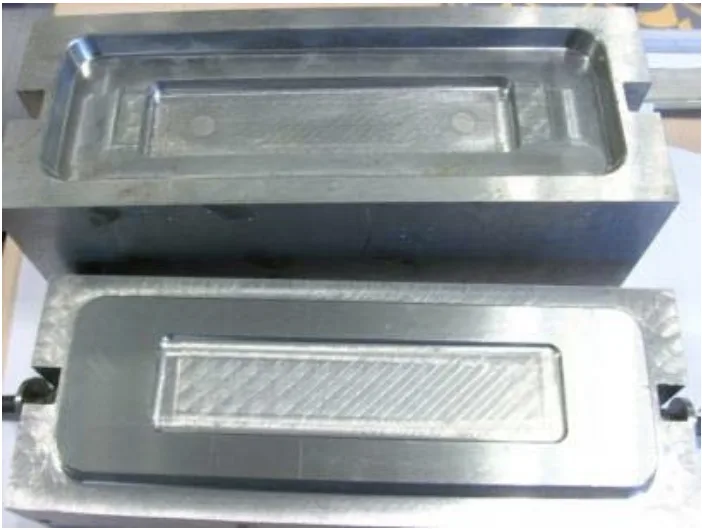
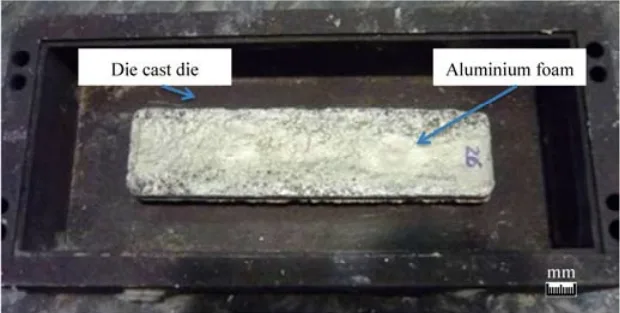
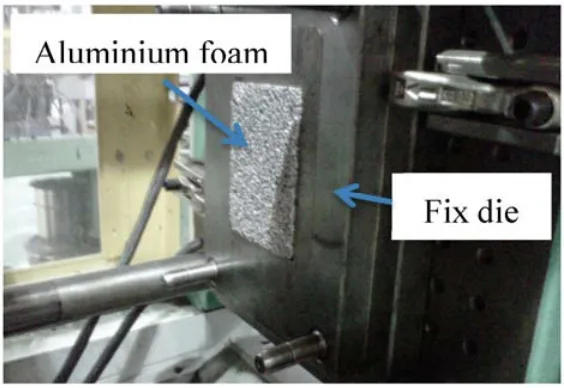
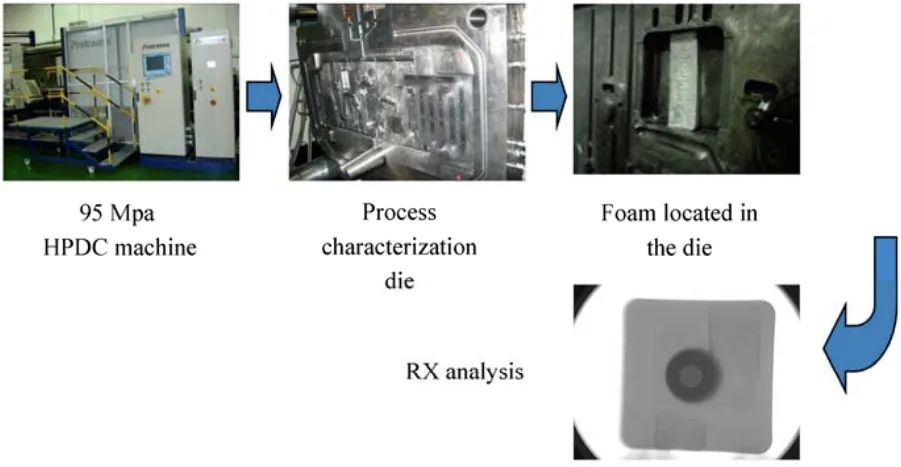
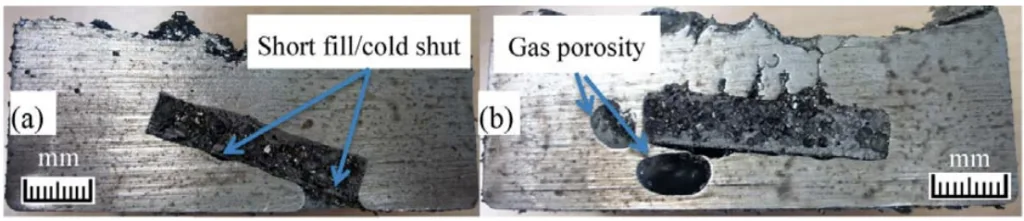
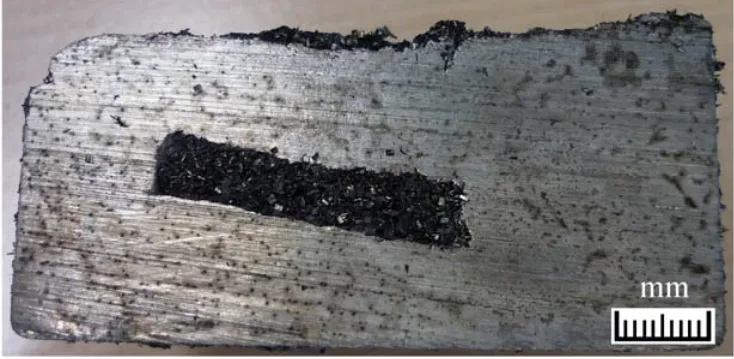
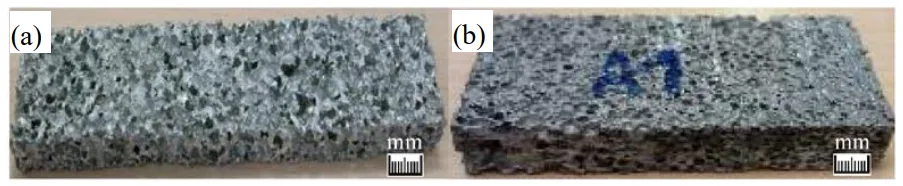
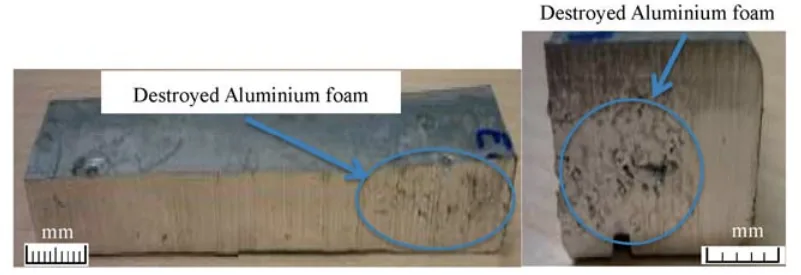
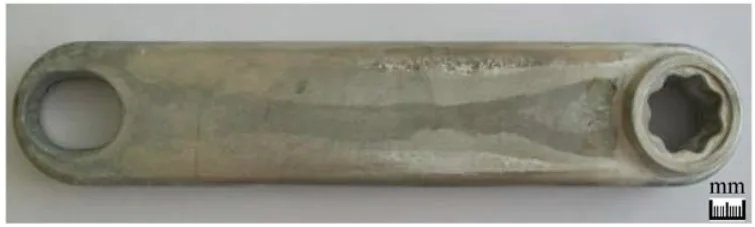
- 図1. アルミニウムフォームの製造に最も多く用いられるプロセスの一部。
- 図2. (a) 3Dロッド設計; および (b) アルミニウムフォームコアの配置と例の詳細。
- 図3. Alulightでアルミニウムフォームを製造する金属金型。
- 図4. アルミニウムフォーム上にマグネシウムをダイカストする金属金型。
- 図5. アルミニウムフォームを備えたプラスチック射出成形金型。
- 図6. マグネシウム-アルミニウムフォームコア複合材を得るためのHPDCプロセス。
- 図7. アルミニウムフォームを配置するための固定金型キャビティの固定ピンの詳細。
- 図8. (a) 短絡充填および冷間接合欠陥; および (b) ガス気孔欠陥。
- 図9. AM60Bで覆われた中央アルミニウムコア。
- 図10. アルミニウムフォームに対するプラスチック射出のための様々な構成。
- 図11. (a) Alporaのフォーム (0.25〜0.4 Kg/dm³); および (b) Formgripのフォーム (0.4〜0.65 Kg/dm³)。
- 図12. 完全に破壊されたアルミニウムフォームを備えたHPDC部品。
- 図13. (a) ダイにスキン付きフォームとスキンなし領域を配置; および (b) スキンなし領域からのフォームからのガス放出。
- 図14. スクイーズピン適用後の1.55 Kg/dm³アルミニウムフォーム。
- 図15. コアの金属流れに対する水平配置。
- 図16. 金属流れに対する垂直コア配置。
- 図17. アルミニウムフォーム内部コアを備えたマグネシウムHPDC製ロッド。
- 図18. 低減された二次速度(20 m/s)HPDC鋳造部品。
- 図19. 標準パラメータでコアフォームで射出されたHPDC。
7. 結論:
主な知見の要約:
本研究では、軽量化用途向けのHPDCマグネシウム-アルミニウムフォーム複合鋳造品の実現可能性を実証することに成功しました。クローズドセル構造と外皮を特徴とするAlulightタイプのアルミニウムフォームは、HPDCマグネシウム過剰射出に最も効果的なコア材料であることが証明されました。720℃のマグネシウム溶融温度を維持し、標準的な射出速度と圧力を採用することを含むHPDCパラメータを最適化することは、健全な鋳造品を達成するために重要です。この複合アプローチを使用して、自転車用ロッドのデモンストレーション部品で35%の軽量化が達成されました。
研究の学術的意義:
本研究は、HPDCにおける複合鋳造、特にマグネシウムマトリックス内のアルミニウムフォームコアの使用に関する学術的理解に貢献しています。アルミニウムフォームの特性(種類、密度、スキンの有無)とHPDCプロセスパラメータが、得られる複合鋳造品の品質に及ぼす影響に関する貴重な洞察を提供します。本研究は、HPDC中のコアの完全性に対するアルミニウムフォームの外皮の重要性を強調し、コアの配置と射出速度の制御に関するガイダンスを提供します。
実用的な意味合い:
本研究の知見は、製造業、特に軽量化ソリューションを求める分野において、重要な実用的な意味合いを持っています。マグネシウム-アルミニウムフォーム複合材用の実証済みのHPDCプロセスは、自動車、航空宇宙、およびスポーツ用品用途でより重い材料を置き換える可能性のある軽量部品の大量生産のための実行可能なルートを提供します。自転車用ロッドのデモンストレーション部品は、自転車産業における即時の適用可能性を示しています。
研究の限界と今後の研究分野:
特定された主な限界は、フォームのアルミナ層のために、アルミニウムフォームコアとマグネシウムマトリックスの間に化学結合が欠如していることです。この結合の欠如は、複合材の機械的特性の向上の可能性を制限する可能性があります。今後の研究は、以下に焦点を当てる必要があります。
- マグネシウムとの金属結合を促進し、界面強度を改善するための、Znベースのコーティングなどのアルミニウムフォームの表面処理の調査。
- 軽量化を最大化しながら、機械的性能を維持または向上させるためのHPDCパラメータと部品設計のさらなる最適化。
- より広範囲の部品形状および産業用途へのこの複合鋳造アプローチの適用性の探求。
8. 参考文献:
- [1] Schultz, R. Aluminium Association Auto and Light Truck Group 2009 Update on North American Light Vehicle Aluminium Content Compared to the other Countries and Regions of the World. Phase II; Ducker Worlwide LLC: Troy, MI, USA, 2008; pp. 8–19.
- [2] Bonollo, F.; Urban, J.; Bonatto, B.; Botter, M. Gravity and low pressure die casting of aluminium alloys: A technical and economical benchmark. Metall. Ital. 2005, 97, 23-32.
- [3] Luo, A.A. Magnesium casting technology for structural applications. J. Magnes. Alloys 2013, 1, 2-22. [CrossRef]
- [4] Gertsberg, G.; Nagar, N.; Lautzker, M.; Bronfin, B. Effect of HPDC parameters on the performance of creep resistant alloys MRI153M and MRI230D. SAE Tech. Pap. 2005, 1, 1–7.
- [5] Otarawanna, S.; Laukli, H.I.; Gourlay, C.M.; Dahle, A.K. Feeding mechanisms in high-pressure die castings. Metall. Mater. Trans. A 2010, 41, 1836-1846. [CrossRef]
- [6] Bonollo, F.; Gramegna, N.; Timelli, G. High-pressure die-casting: Contradictions and challenges. JOM 2015, 67, 901-908. [CrossRef]
- [7] Yim, C.D.; Shin, K.S. Semi-solid processing of magnesium alloys. Mater. Trans. 2003, 44, 558–561. [CrossRef]
- [8] Sabau, A.S.; Dinwiddie, R.B. Characterization of spray lubricants for the high pressure die casting processes. J. Mater. Process. Technol. 2008, 195, 267–274. [CrossRef]
- [9] Kimura, R.; Yoshida, M.; Sasaki, G.; Pan, J.; Fukunaga, H. Characterization of heat insulating and lubricating ability of powder lubricants for clean and high quality die casting. J. Mater. Process. Technol. 2002, 130–131, 289-293. [CrossRef]
- [10] Puschmann, F.; Specht, E. Transient measurement of heat transfer in metal quenching with atomized sprays. Exp. Therm. Fluid Sci. 2004, 28, 607-615. [CrossRef]
- [11] Rogers, K.J.; Savage, G. In-cavity pressure sensors-errors, robustness and some process insights. Die Cast Eng. 2000, 44, 76-80.
- [12] Kong, L.X.; She, F.H.; Gao, W.M.; Nahavandi, S.; Hodgson, P.D. Integrated optimization system for high pressure die casting processes. J. Mater. Process. Technol. 2008, 201, 629-634. [CrossRef]
- [13] Keber, K.; Bormann, D.; Möhwald, K.; Hollander, U.; Bach, W. Compound casting of aluminium and magnesium alloys by High Pressure Die Casting. In Proceedings of the Magnesium 8th International Conference on Magnesium Alloys and Their Applications, Weimar, Germany, 26-29 October 2009; pp. 390-397.
- [14] Kunst, M.; Fischersworring-bunk, A.; Liebscher, C.; Glatzel, U.; Esperance, G.L.; Plamondon, P.; Baril, E.; Labelle, P. Microstructural characterization of Die Cast Mg-Al-Sr (AJ) Alloy. In Proceedings of the Magnesium: Proceedings of the 7th International Conference on Magnesium Alloys and Their Applications, Dresden, Germany, 6–9 November 2006; pp. 498-505.
- [15] Vicario, I. Study of high pressure die cast AZ91D magnesium alloy with surface treated aluminium 6063 cores for Al-Mg multi-material. In Proceedings of the 2nd Annual World Congress of Advanced Materials, Suzhou, China, 5-7 June 2013; pp. 7–21.
- [16] Yaokawa, J.; Miura, D.; Anzai1, K.; Yamada, Y.; Yoshii, H. Strength of salt core composed of alkali carbonate and alkali chloride mixtures made by casting technique. Mater. Trans. 2007, 5, 1034–1041. [CrossRef]
- [17] Moschini, R. Production of Hollow Components in HPDC through the Use of Ceramic Lost Cores; XXXI Congreso Tecnico di Fonderia: Vincenza, Italy, 2012; pp. 1–33.
- [18] Yamada, Y.; Yaokawa, J.; Yoshii, H.; Anzai, K.; Noda, Y.; Fujiwara, A.; Suzuki, T.; Fukui, H. Developments and application of expendable salt core materials for high pressure die casting to apply closed-deck type cylinder block. SAE Int. 2007, 32-0084, 1–5.
- [19] Vicario, I.; Egizabal, P.; Galarraga, H.; Plaza, L.M.; Crespo, I. Study of an Al-Si-Cu HPDC alloy with high Zn content for the production of components requiring high ductility and tensile properties. Int. J. Mater. Res. 2013, 4, 392-397. [CrossRef]
- [20] Benedick, C. Production and application of aluminium foam, past product potential revisited in the new millennium. Light Met. Age 2002, 60, 24-29.
- [21] Bausmesiter, J.; Weise, J. Structural Materials and Processes in Transportation, Metal Foams; John Wiley & Sons: Hoboken, NJ, USA, 2013; pp. 415-440.
- [22] Banhar, J. Metal foams: Production and stability. Adv. Eng. Mater. 2006, 9, 781–794. [CrossRef]
- [23] Coleto, J.; Goñi, J.; Maudes, J.; Leizaola, I. Applications and manufacture of open and closed cell metal foams by foundry routes. In Proceedings of International Congress Eurofond, La Rochelle, France, 2–4 June 2004; pp. 1-10.
- [24] Körner, C.; Hirschmann, M.; Wiehler, H. Integral Foam Moulding of Light Metals. Mater. Trans. 2006, 47, 2188-2194. [CrossRef]
- [25] Baumeister, J.; Weise, J. Application of aluminium-polymer hybrid foam sandwiches in battery housings for electric vehicles. Procedia Mater. Sci. 2014, 4, 301-330. [CrossRef]
- [26] Vesenjak, M.; Borovinšek, M.; Fiedler, T.; Higa, Y.; Ren, Z. Structural characterisation of advanced pore morphology (APM) foam elements. Mater. Lett. 2013, 110, 201-203. [CrossRef]
- [27] Miyoshi, T.; Itoh, M.; Akiyama, S.; Kitahara, A. Aluminium foam, “ALPORAS": The production process, properties and application. In Materials Research Society Symposium Proceedings, Boston, MA, USA, 1-3 December 1998; 1998; pp. 133-137.
- [28] Miyoshi, T.; Itoh, M.; Akiyama, S.; Kitahara, A. Alporas aluminum foam: Production process, properties, and applications. Adv. Eng. Mater. 2000, 2, 179–183. [CrossRef]
- [29] Gegerly, V.; Clyne, T.W. The formgrip process: Foaming of reinforced metals by gas release in precursors. Adv. Eng. Mater. 2002, 2, 175–178.
- [30] Gergely, V.; Curran, D.C.; Clyne, T.W. Advances in the melt route production of closed cell aluminium foams using gas-generating agents. In Proceedings of Global Symposium of Materials Processing and Manufacturing Processing & Properties of Lightweight Cellular Metals and Structures, Seattle, WA, USA, 17-21 February 2002; pp. 3-8.
- [31] Baumeister, J. Production technology for aluminium foam/steel sandwiches. In Proceedings of the International Conference on Metal Foams and Porous Metal Structures, Bremen, Germany, 14-16 June 1999; pp. 113-118.
- [32] Seeliger, H.W. Cellular Metals: Manufacture, properties, applications. In Proceedings of the MetFoam, Berlin, Germany, 23-25 June 2003; pp. 5-12.
- [33] Kováãik, J.; Simančík, F.; Jerz, J.; Tobolka, P. Reinforced aluminium foams. In Proceedings of the International Conference on Advanced Metallic Materials, Smolenice, Slovakia, 5–7 November 2003; pp. 154–159.
- [34] Braune, R.; Otto, A. Tailored blanks based on foamable aluminium sandwich material. In Proceedings of the International Conference on Metal Foams and Porous Metal Structures, Bremen, Germany, 14-16 June 1999; pp. 119-124.
- [35] Gutiérrez-Vázquez, J.A.; Oñoro, J. Fabricación y comportamiento de espumas de aluminio con diferente densidad a partir de un precursor AlSi12. Rev. Metal. 2010, 46, 274–284. [CrossRef]
9. 著作権:
- この資料は、「Iban Vicarioら」の論文:「高圧ダイカストで製造されたアルミニウムフォームとマグネシウム複合鋳造」に基づいています。
- 論文ソース:https://doi.org/10.3390/met6010024
この資料は上記の論文を要約したものであり、商業目的での無断使用は禁止されています。
Copyright © 2025 CASTMAN. All rights reserved.