この論文概要は、[MDPI発行]で発表された論文 Aluminium Foam and Magnesium Compound Casting Produced by High-Pressure Die Casting に基づいて作成されています。
1. 概要:
- タイトル: Aluminium Foam and Magnesium Compound Casting Produced by High-Pressure Die Casting(高圧ダイカストで製造されたアルミニウムフォームとマグネシウム複合鋳造)
- 著者: イバン・ビカリオ、イグナシオ・クレスポ、ルイス・マリア・プラザ、パトリシア・カバレロ、イオン・ケパ・イドイアガ
- 発表年: 2016年
- 掲載ジャーナル/学会: Metals、MDPI発行
- キーワード: 高圧ダイカスト (HPDC); ハイブリッドマグネシウムアルミニウムフォーム鋳造複合材; アルミニウムフォームコア; マグネシウム鋳造複合材
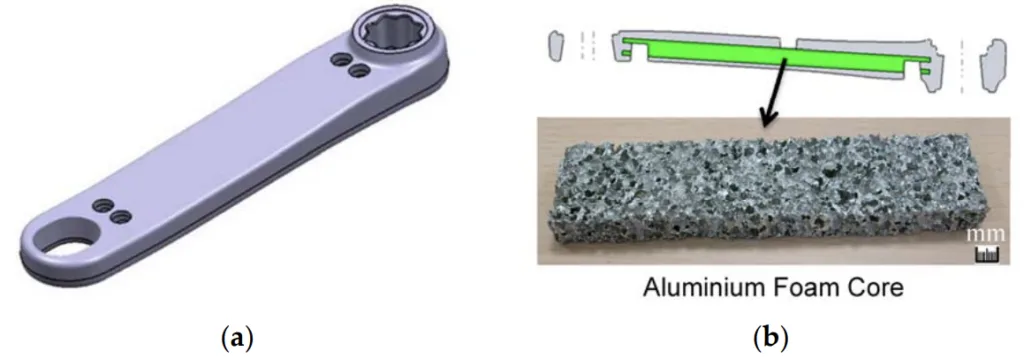
2. 研究背景:
今日、自動車および輸送産業において、燃料消費量と二酸化炭素排出量は車両設計における主要な焦点であり、軽量材料を使用して車両の重量を削減することが推進されています。鋼鉄や鉄鋳物部品を、プラスチック、炭素繊維、アルミニウム、マグネシウム合金などのより軽量な代替材料に置き換えることが重要な傾向となっています。特に自転車産業では、高性能自転車において炭素繊維が鋼鉄、アルミニウム、チタンに取って代わる傾向が顕著です。
高圧ダイカスト (HPDC) で製造されたマグネシウム部品は、すでに自動車や自転車の用途で使用されています。しかし、業界はマグネシウム軽量構造が提供する軽量性と機械的特性のバランスを活用できる新しい部品を継続的に探しています。HPDC は、大量生産 (年間約 5,000〜10,000 個以上) に経済的に実現可能な高生産性プロセスです。
既存の研究および HPDC の応用には限界があります。HPDC の主な欠点は、金属注入中の乱流によって生じる内部気孔です。この気孔は熱処理を複雑にし、他の鋳造方法よりも達成可能な機械的特性を低下させます。また、異種材料で複合鋳物を製造することにも課題があります。アルミニウム-マグネシウム複合材が研究されていますが、アルミニウムフォームコアとマグネシウム間の金属結合を達成することは、アルミニウムフォーム表面のアルミナ層のために困難です。HPDC で中空部品を作成するために塩コアを使用するなどの代替方法も、コア材の除去の複雑さを招き、部品設計を制限する可能性があります。したがって、これらの限界を克服し、HPDC 部品の性能をさらに向上させるための革新的なアプローチを模索する必要性があります。
本研究は、マグネシウム鋳物内部にアルミニウムフォームコアを使用することにより、HPDC における部品重量を削減する必要性に対処します。このアプローチは、重量削減と機械的特性の間の妥協点を達成することを目的としています。
3. 研究目的と研究課題:
研究目的:
本研究の主な目的は、さまざまな種類のアルミニウムフォームと高圧ダイカスト (HPDC) 射出パラメータが、マグネシウム複合鋳物の特性に及ぼす影響を評価することです。目標は、アルミニウムフォームをマグネシウム鋳物部品内のコアとして使用することにより、重量削減と許容可能な機械的特性のバランスをとる健全な複合鋳物を製造することです。
主な研究課題:
- HPDC で製造されたマグネシウム-アルミニウムフォーム複合鋳物の品質に、さまざまなアルミニウムフォームタイプ (Alporas、Formgrip、Alulight) はどのように影響するか?
- マグネシウム-アルミニウムフォーム複合部品の最終鋳造品質に、金属温度、プランジャ速度、増圧などの HPDC 射出パラメータはどのような影響を与えるか?
- HPDC で製造されたマグネシウム-アルミニウムフォーム複合材は、自転車部品などの構造用途に適した許容可能な機械的特性を維持しながら、大幅な軽量化を達成できるか?
研究仮説:
明示的に仮説として述べられてはいませんが、研究は以下の前提の下に進められています。
- アルミニウムフォームコアのタイプを慎重に選択し、HPDC 射出パラメータを最適化することにより、健全なマグネシウム-アルミニウムフォーム複合鋳物を製造することが可能である。
- マグネシウム鋳物にアルミニウムフォームコアを使用すると、ソリッドマグネシウム部品と比較して大幅な軽量化をもたらすだろう。
- 複合鋳物の機械的特性は、アルミニウムフォームコアのタイプと HPDC プロセスパラメータによって影響を受けるだろう。
4. 研究方法論
研究デザイン:
本研究では、HPDC を使用したマグネシウム-アルミニウムフォーム複合鋳物の製造を調査するために、実験的研究デザインを採用しました。研究は、最終鋳造品質および特性に及ぼす影響を評価するために、アルミニウムフォームコアのタイプと主要な HPDC 射出パラメータを体系的に変更することを含みました。
データ収集方法:
製造された複合鋳物の品質は、以下を使用して評価されました。
- 目視検査: 鋳物を目視で検査し、表面欠陥と全体的な形状を確認しました。
- 放射線検査 (RX): 160kV で General Electric X-cube 44XL を使用して X 線分析を実施し、内部健全性を評価し、気孔を検出し、マグネシウムマトリックス内のアルミニウムフォームコアの完全性と位置を確認しました。
- 引張試験: 機械的特性は、5mm/min のクロスヘッド速度で Instron 3369 電気機械式試験機を使用して室温で UNE-EN ISO 6892-1 B:2010 規格に従って実施された引張試験を通じて評価されました。引張応力、極限引張強度 (UTS)、および伸びを測定しました。
分析方法:
- 定性的分析: 目視および RX 検査データを使用して、鋳造品質を定性的に評価し、短絡、冷間接合、ガス気孔、フォームコアの完全性などの欠陥に焦点を当てました。
- 定量的分析: 引張試験データを定量的に分析して、ソリッド AM60B マグネシウム合金鋳物とマグネシウム-アルミニウムフォーム複合鋳物の機械的特性を決定しました。統計分析を使用して、特性を比較し、アルミニウムフォームコアの影響を評価しました。
研究対象と範囲:
- 材料:
- マグネシウム合金: AM60B が鋳造マグネシウム合金として使用されました。
- アルミニウムフォーム: 3 種類の独立気泡アルミニウムフォームが評価されました。
- Alporas ALPO-PLA-03 (Alcan)
- Formgrip ベースフォーム (Tecnalia 加工)
- Alulight 0.4% TiB2 AlSi12 フォーム (Alulight)
- プロセス: 高圧ダイカスト (HPDC)
- 部品: 自転車ロード部品が、複合鋳造アプローチの妥当性と利点を評価するためのデモンストレーション部品として選択されました。
- 変更されたパラメータ:
- アルミニウムフォームタイプと密度
- 金属鋳造温度 (680 °C および 720 °C)
- 射出圧力 (プラスチック射出シミュレーションの場合は 16〜40 MPa、HPDC の場合は 20〜80 MPa)
- プランジャ速度 (第 1 段階 0.25 m/s、第 2 段階 20〜80 m/s)
- コア配置 (金属の流れに対して水平および垂直)
- スクイズピンの適用
5. 主な研究結果:
主な研究結果:
- 健全な複合鋳造の達成: 本研究では、HPDCを用いて健全なマグネシウム-アルミニウムフォーム複合鋳物を製造することに成功しました。
- フォームスキンと配置の重要性: アルミニウムフォームコアの外部連続スキンと、ダイカストキャビティ内のフォームの正しい配置が、高品質の部品を得るために重要であることがわかりました。スキンは、マグネシウム注入中のガス放出とフォームの崩壊を防ぎます。金属の流れに対するフォームコアの垂直配置は、水平配置よりも優れていました。
- アルライトフォームの性能: 試験したフォームの中で、外部スキンを持つアルライトフォームが、HPDCプロセスをサポートし、その完全性を維持する上で最高の性能を示しました。
- 軽量化: マグネシウム-アルミニウムフォーム複合自転車部品は、固体マグネシウム部品と比較して約35%の軽量化を達成しました。
- 最適化されたパラメータ: マグネシウム合金の最小注湯温度720 °C、第2段階射出速度80 m/s、特定圧力80 MPaの標準HPDCパラメータが、健全な複合鋳物を製造するのに適していることが特定されました。増圧ピンはフォームコアを損傷することがわかりました。
統計/定性分析結果:
- 鋳造温度の影響 (図8): AM60Bを680 °Cで鋳造すると、「ショートフィル/コールドシャット」欠陥とガス気孔が発生しました。温度を720 °Cに上げると、これらの欠陥が解消されました。
- プラスチック射出シミュレーション (表4、図10): HPDC圧力をシミュレートしたプラスチック射出試験では、アルライトフォーム (密度 0.54-1.55 Kg/dm³) が崩壊することなく40 MPaの圧力に耐えることができましたが、アルポラス (0.25-0.4 Kg/dm³) とフォームグリップ (0.4-0.55 Kg/dm³) フォームは、16 MPaと40 MPaの両方で破損しました。
- 増圧ピンの影響 (図14): 増圧ピン圧力 (最大200 MPa) をアルミニウムフォームコアに直接加えると、密度に関係なくフォームが破壊されました。
- コア配置の影響 (図15 & 16): 金属の流れに対するフォームコアの水平配置は、フォームのせん断破壊につながりました。垂直配置は損傷を最小限に抑え、わずかな収縮気孔のみが発生しました。
- 射出速度の影響 (図18 & 19): 第2段階射出速度を20 m/sに下げると、「非常に充填不良」が発生しました。第2段階速度80 m/sの標準HPDCパラメータでは、良好な充填とわずかな凝固気孔のみの部品が製造されました。
- 機械的特性 (表5):
- AM60B (固体): 耐力 (YS) = 141 ± 4.3 MPa、極限引張強度 (UTS) = 219 ± 3.6 MPa、伸び = 3 ± 0.5%。
- 複合材: YS = 79 + 1.75 MPa、UTS = 122 ± 2.16 MPa、伸び = 3 + 0.5%。
- 外挿複合材特性 (面積削減率47%): YS = 149 ± 3.3 MPa、UTS = 230 ± 4.1 MPa、伸び = 3 ± 0.5%。
データ解釈:
結果は、HPDCによるマグネシウム-アルミニウムフォーム複合鋳物の製造は実現可能であるが、アルミニウムフォームの種類を慎重に選択し、プロセスパラメータを最適化する必要があることを示しています。外部スキンを持つアルライトフォームは、HPDC圧力に耐え、ガス気孔を防ぐ能力があるため、この用途に適しています。コア配置と射出速度は、鋳造品質に影響を与える重要なパラメータです。大幅な軽量化が達成されましたが、複合材の初期機械的特性は固体マグネシウムよりも低くなっています。ただし、外挿値は、最適化された設計と材料利用により、複合材が引張強度に関して固体マグネシウムの機械的性能に匹敵するか、わずかに上回る可能性がありながら、大幅な軽量化を提供できることを示唆しています。
図のリスト:
- 図1: 最も一般的に使用されているアルミニウムフォームの製造プロセスの一部。
- 図2: (a) 3Dロッド設計; および (b) アルミニウムフォームコアの配置と例の詳細。
- 図3: アルライトアルミニウムフォームを製造するための金属ダイカスト金型。
- 図4: アルミニウムフォーム上にマグネシウムをダイカストするための金属ダイカスト金型。
- 図5: アルミニウムフォームを備えたプラスチック射出成形金型。
- 図6: マグネシウム-アルミニウムフォームコア複合材を得るためのHPDCプロセス。
- 図7: アルミニウムフォームを配置するための固定ダイカストキャビティの固定ピンの詳細。
- 図8: (a) ショートフィルおよびコールドシャット欠陥; および (b) ガス気孔欠陥。
- 図9: AM60Bで覆われた中央アルミニウムコア。
- 図10: アルミニウムフォーム上へのプラスチック射出のための異なる構成。
- 図11: (a) アルポラスフォーム (0.25~0.4 Kg/dm³); および (b) フォームグリップフォーム (0.4~0.65 Kg/dm³)。
- 図12: 完全に破壊されたアルミニウムフォームを備えたHPDC部品。
- 図13: (a) スキン付きフォームとダイカスト内のスキンなし領域の配置; および (b) スキンなし領域のフォームからのガス放出。
- 図14: 増圧ピン適用後の1.55 Kg/dm³アルミニウムフォーム。
- 図15: コアの金属の流れに対する水平配置。
- 図16: 水平コア配置から金属の流れへ。
- 図17: アルミニウムフォームの内部コアを備えたマグネシウムHPDC製ロッド。
- 図18: 減速された第2段階速度 (20 m/s) HPDC鋳造部品。
- 図19: 標準パラメータでのコアフォームを備えた射出HPDC。
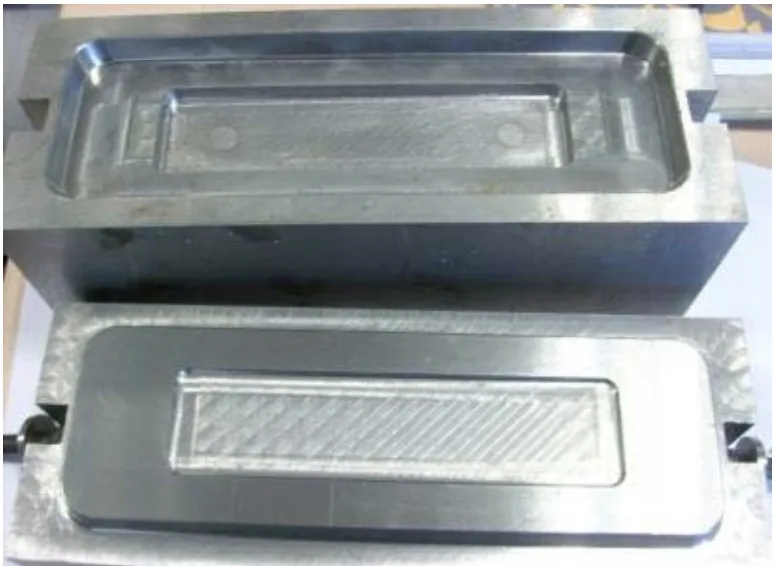
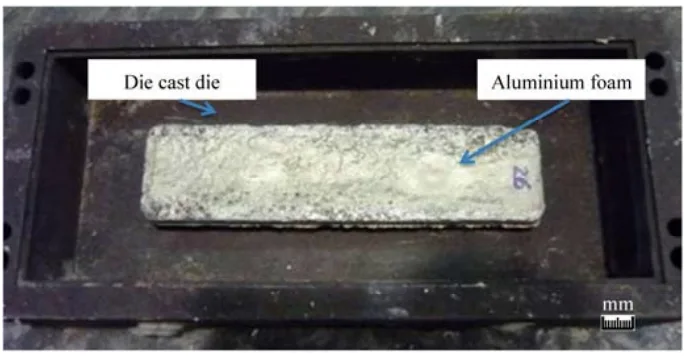
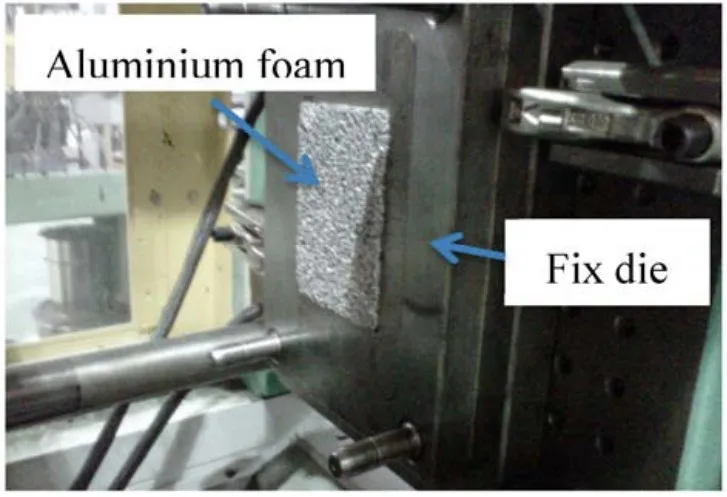
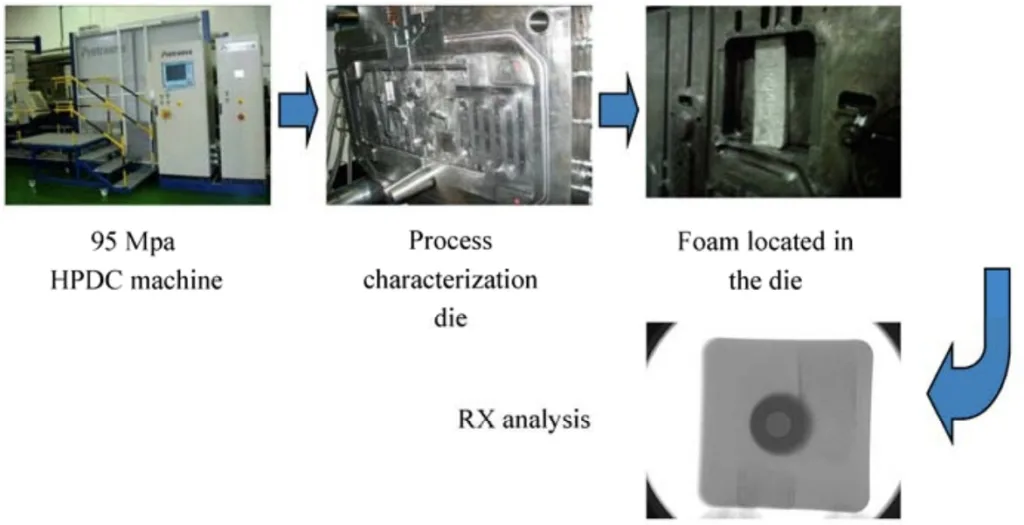
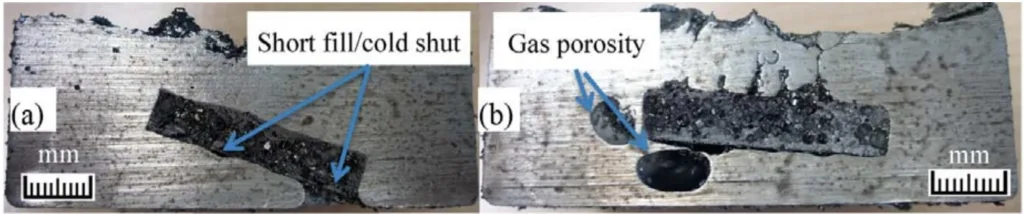
6. 結論と考察:
主な結果の要約:
本研究では、高圧ダイカスト (HPDC) を用いたマグネシウム-アルミニウムフォーム複合鋳物の製造の実現可能性を実証しました。この研究では、外部スキンを特徴とするアルライトタイプのアルミニウムフォームが、このプロセスに適したコア材料であることを特定しました。マグネシウム注湯温度720 °C、第2段階射出速度80 m/s、フォームコアの垂直配置などの最適化されたHPDCパラメータは、健全な鋳物を達成するために不可欠です。このアプローチを用いて、35%の軽量化を実現した自転車ロッド部品が製造に成功しました。
研究の学術的意義:
本研究は、HPDCを用いた軽量金属マトリックス複合材を作成するための実行可能な方法を実証することにより、学術分野に貢献しています。HPDC条件下でのマグネシウム鋳造環境におけるアルミニウムフォームコアの挙動の理解を深め、フォームの種類、スキンの有無、コア配置、射出パラメータの重要性を強調しています。
実際的な意義:
この知見は、特に輸送分野において、軽量化ソリューションを求める産業界にとって大きな実際的な意義があります。開発されたHPDCマグネシウム-アルミニウムフォーム複合鋳造プロセスは、自転車部品などの軽量部品を製造するための道筋を提供し、固体アルミニウム、チタン、鋼などの重い材料に取って代わる可能性があります。これにより、車両の燃費が向上し、自転車などの用途での性能が向上する可能性があります。自転車ロッドにアルミニウムフォームを使用した場合の材料費と製造費の見積もりは約0.3ユーロ/個であり、経済的な実現可能性を示唆しています。
研究の限界:
- 化学結合の欠如: 本研究では、フォーム上のアルミナ層のために、アルミニウムフォームコアとマグネシウム合金の間に化学結合がないことを認めています。この結合の欠如は、複合材の全体的な機械的性能を制限する可能性があります。
- 機械的特性の低下: 軽量化は著しいものの、複合鋳物の初期機械的特性は、固体AM60Bマグネシウム合金よりも低くなっています。外挿値は改善の可能性を示唆していますが、さらなる最適化が必要です。
- アルライトフォームの引張試験データの限定性: 本研究では、特にアルライトタイプのフォームの引張試験値の増加が限定的であったことを指摘しており、より詳細な機械的特性評価の必要性を示唆しています。
7. 今後のフォローアップ研究:
今後のフォローアップ研究の方向性:
今後の研究では、アルミニウムフォームとマグネシウム間の化学結合の限界に対処することに焦点を当てる必要があります。アルミニウムフォームコアの表面処理を検討することが重要な方向性です。
さらなる探求が必要な分野:
具体的には、アルミニウムフォームコアへのZnベースのコーティングなどの表面処理の適用を調査することをお勧めします。これにより、アルミニウムフォームと鋳造マグネシウムの間に連続的な界面が作成され、結合強度と機械的インターロックが向上する可能性があります。今後の研究では、さまざまな用途における振動減衰、騒音制御、衝突性能、または圧縮特性を改善する上でのアルミニウムフォームコアの潜在的な利点も探求できます。
8. 参考文献:
- [1] Schultz, R. Aluminium Association Auto and Light Truck Group 2009 Update on North American Light Vehicle Aluminium Content Compared to the other Countries and Regions of the World. Phase II; Ducker Worlwide LLC: Troy, MI, USA, 2008; pp. 8–19.
- [2] Bonollo, F.; Urban, J.; Bonatto, B.; Botter, M. Gravity and low pressure die casting of aluminium alloys: A technical and economical benchmark. Metall. Ital. 2005, 97, 23-32.
- [3] Luo, A.A. Magnesium casting technology for structural applications. J. Magnes. Alloys 2013, 1, 2-22.
- [4] Gertsberg, G.; Nagar, N.; Lautzker, M.; Bronfin, B. Effect of HPDC parameters on the performance of creep resistant alloys MRI153M and MRI230D. SAE Tech. Pap. 2005, 1, 1–7.
- [5] Otarawanna, S.; Laukli, H.I.; Gourlay, C.M.; Dahle, A.K. Feeding mechanisms in high-pressure die castings. Metall. Mater. Trans. A 2010, 41, 1836-1846.
- [6] Bonollo, F.; Gramegna, N.; Timelli, G. High-pressure die-casting: Contradictions and challenges. JOM 2015, 67, 901-908.
- [7] Yim, C.D.; Shin, K.S. Semi-solid processing of magnesium alloys. Mater. Trans. 2003, 44, 558–561.
- [8] Sabau, A.S.; Dinwiddie, R.B. Characterization of spray lubricants for the high pressure die casting processes. J. Mater. Process. Technol. 2008, 195, 267–274.
- [9] Kimura, R.; Yoshida, M.; Sasaki, G.; Pan, J.; Fukunaga, H. Characterization of heat insulating and lubricating ability of powder lubricants for clean and high quality die casting. J. Mater. Process. Technol. 2002, 130–131, 289-293.
- [10] Puschmann, F.; Specht, E. Transient measurement of heat transfer in metal quenching with atomized sprays. Exp. Therm. Fluid Sci. 2004, 28, 607-615.
- [11] Rogers, K.J.; Savage, G. In-cavity pressure sensors-errors, robustness and some process insights. Die Cast Eng. 2000, 44, 76-80.
- [12] Kong, L.X.; She, F.H.; Gao, W.M.; Nahavandi, S.; Hodgson, P.D. Integrated optimization system for high pressure die casting processes. J. Mater. Process. Technol. 2008, 201, 629-634.
- [13] Keber, K.; Bormann, D.; Möhwald, K.; Hollander, U.; Bach, W. Compound casting of aluminium and magnesium alloys by High Pressure Die Casting. In Proceedings of the Magnesium 8th International Conference on Magnesium Alloys and Their Applications, Weimar, Germany, 26-29 October 2009; pp. 390-397.
- [14] Kunst, M.; Fischersworring-bunk, A.; Liebscher, C.; Glatzel, U.; Esperance, G.L.; Plamondon, P.; Baril, E.; Labelle, P. Microstructural characterization of Die Cast Mg-Al-Sr (AJ) Alloy. In Proceedings of the Magnesium: Proceedings of the 7th International Conference on Magnesium Alloys and Their Applications, Dresden, Germany, 6–9 November 2006; pp. 498-505.
- [15] Vicario, I. Study of high pressure die cast AZ91D magnesium alloy with surface treated aluminium 6063 cores for Al-Mg multi-material. In Proceedings of the 2nd Annual World Congress of Advanced Materials, Suzhou, China, 5-7 June 2013; pp. 7–21.
- [16] Yaokawa, J.; Miura, D.; Anzai1, K.; Yamada, Y.; Yoshii, H. Strength of salt core composed of alkali carbonate and alkali chloride mixtures made by casting technique. Mater. Trans. 2007, 5, 1034–1041.
- [17] Moschini, R. Production of Hollow Components in HPDC through the Use of Ceramic Lost Cores; XXXI Congreso Tecnico di Fonderia: Vincenza, Italy, 2012; pp. 1–33.
- [18] Yamada, Y.; Yaokawa, J.; Yoshii, H.; Anzai, K.; Noda, Y.; Fujiwara, A.; Suzuki, T.; Fukui, H. Developments and application of expendable salt core materials for high pressure die casting to apply closed-deck type cylinder block. SAE Int. 2007, 32-0084, 1–5.
- [19] Vicario, I.; Egizabal, P.; Galarraga, H.; Plaza, L.M.; Crespo, I. Study of an Al-Si-Cu HPDC alloy with high Zn content for the production of components requiring high ductility and tensile properties. Int. J. Mater. Res. 2013, 4, 392-397.
- [20] Benedick, C. Production and application of aluminium foam, past product potential revisited in the new millennium. Light Met. Age 2002, 60, 24-29.
- [21] Bausmesiter, J.; Weise, J. Structural Materials and Processes in Transportation, Metal Foams; John Wiley & Sons: Hoboken, NJ, USA, 2013; pp. 415-440.
- [22] Banhar, J. Metal foams: Production and stability. Adv. Eng. Mater. 2006, 9, 781–794.
- [23] Coleto, J.; Goñi, J.; Maudes, J.; Leizaola, I. Applications and manufacture of open and closed cell metal foams by foundry routes. In Proceedings of International Congress Eurofond, La Rochelle, France, 2–4 June 2004; pp. 1-10.
- [24] Körner, C.; Hirschmann, M.; Wiehler, H. Integral Foam Moulding of Light Metals. Mater. Trans. 2006, 47, 2188-2194.
- [25] Baumeister, J.; Weise, J. Application of aluminium-polymer hybrid foam sandwiches in battery housings for electric vehicles. Procedia Mater. Sci. 2014, 4, 301-330.
- [26] Vesenjak, M.; Borovinšek, M.; Fiedler, T.; Higa, Y.; Ren, Z. Structural characterisation of advanced pore morphology (APM) foam elements. Mater. Lett. 2013, 110, 201-203.
- [27] Miyoshi, T.; Itoh, M.; Akiyama, S.; Kitahara, A. Aluminium foam, “ALPORAS": The production process, properties and application. In Materials Research Society Symposium Proceedings, Boston, MA, USA, 1-3 December 1998; 1998; pp. 133-137.
- [28] Miyoshi, T.; Itoh, M.; Akiyama, S.; Kitahara, A. Alporas aluminum foam: Production process, properties, and applications. Adv. Eng. Mater. 2000, 2, 179–183.
- [29] Gegerly, V.; Clyne, T.W. The formgrip process: Foaming of reinforced metals by gas release in precursors. Adv. Eng. Mater. 2002, 2, 175–178.
- [30] Gergely, V.; Curran, D.C.; Clyne, T.W. Advances in the melt route production of closed cell aluminium foams using gas-generating agents. In Proceedings of Global Symposium of Materials Processing and Manufacturing Processing & Properties of Lightweight Cellular Metals and Structures, Seattle, WA, USA, 17-21 February 2002; pp. 3-8.
- [31] Baumeister, J. Production technology for aluminium foam/steel sandwiches. In Proceedings of the International Conference on Metal Foams and Porous Metal Structures, Bremen, Germany, 14-16 June 1999; pp. 113-118.
- [32] Seeliger, H.W. Cellular Metals: Manufacture, properties, applications. In Proceedings of the MetFoam, Berlin, Germany, 23-25 June 2003; pp. 5-12.
- [33] Kováãik, J.; Simančík, F.; Jerz, J.; Tobolka, P. Reinforced aluminium foams. In Proceedings of the International Conference on Advanced Metallic Materials, Smolenice, Slovakia, 5–7 November 2003; pp. 154–159.
- [34] Braune, R.; Otto, A. Tailored blanks based on foamable aluminium sandwich material. In Proceedings of the International Conference on Metal Foams and Porous Metal Structures, Bremen, Germany, 14-16 June 1999; pp. 119-124.
- [35] Gutiérrez-Vázquez, J.A.; Oñoro, J. Fabricación y comportamiento de espumas de aluminio con diferente densidad a partir de un precursor AlSi12. Rev. Metal. 2010, 46, 274–284.
9. 著作権:
この資料は、イバン・ビカリオ、イグナシオ・クレスポ、ルイス・マリア・プラザ、パトリシア・カバレロ、イオン・ケパ・イドイアガの論文に基づいています: 高圧ダイカスト法によるアルミニウムフォームとマグネシウム複合鋳造。
論文ソース: doi:10.3390/met6010024
この資料は上記の論文に基づいて要約されたものであり、商業目的での無断使用は禁止されています。
著作権 © 2025 CASTMAN. 無断複写・転載を禁じます。