本紹介論文は、「Metals (MDPI)」により発行された論文「Experimental and Numerical Study of an Automotive Component Produced with Innovative Ceramic Core in High Pressure Die Casting (HPDC)」に基づいています。
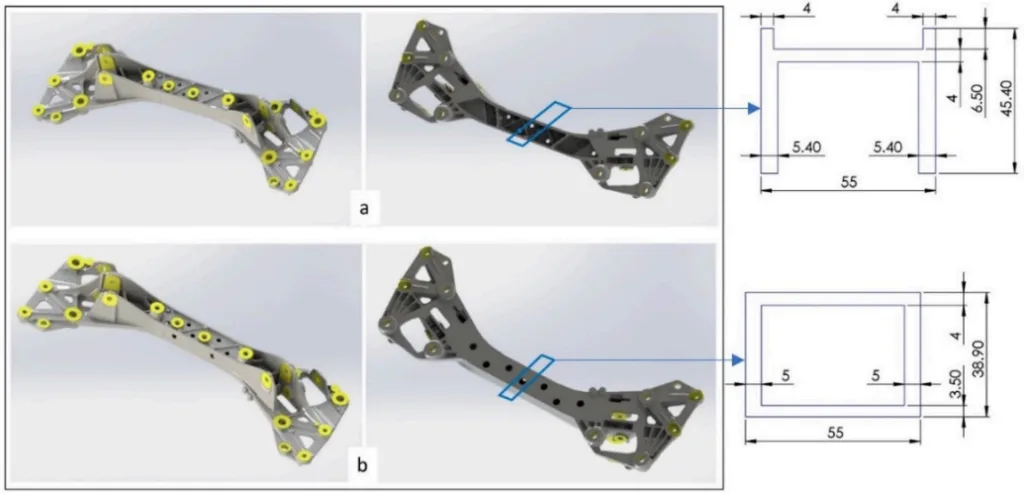
1. 概要:
- タイトル: Experimental and Numerical Study of an Automotive Component Produced with Innovative Ceramic Core in High Pressure Die Casting (HPDC)
- 著者: Giovanna Cornacchia, Daniele Dioni, Michela Faccoli, Claudio Gislon, Luigi Solazzi, Andrea Panvini and Silvia Cecchel
- 発行年: 2019
- 発行元ジャーナル/学会: Metals (MDPI)
- キーワード: non-ferrous alloys; ceramic core; FEA; HPDC; de-coring; material characterization
2. Abstract(要旨):
軽量化と材料置換は、自動車産業におけるトレンドとして増加しています。高圧ダイカスト(HPDC)は、軽合金の大量生産における従来の鋳造技術であり、近年、複雑で薄肉形状の自動車部品など、重要部品の製造に広く応用されています。しかし、この手頃な技術の主な制約は、中空断面やアンダーカットを持つ部品の設計・実現が困難であることです。HPDCの競争力をさらに高める革新的な方法は、HPDCで使用される高圧に耐えうる新しい消失中子(ロストコア)を使用して、複雑なアンダーカット形状の部品を成形することです。本稿では、HPDCによる乗用車用アルミニウムクロスビームの製造における、革新的なセラミック消失中子の使用について調査します。まず、クロスビームの設計を改善し、技術的特徴を確認するために、プロセスおよび構造シミュレーションを実施しました。その結果に基づき、プロセスパラメータを選定し、いくつかのプロトタイプを製造して最終的に特性評価を行いました。これらの分析により、セラミック中子を用いたHPDCによる中空部品製造の実現可能性が実証されました。
3. Introduction(はじめに):
自動車産業では、車両性能の向上、燃費削減、排出ガス低減のために、軽量部品の需要が高まっています。高圧ダイカスト(HPDC)は、大量生産、低コスト、ニアネットシェイプのアルミニウム部品に適した競争力のある技術です。しかし、HPDCでは従来、複雑な中空断面やアンダーカットを持つ部品の製造が困難でした。これらは通常、金属性の可動中子を必要とし、重力鋳造で使用される消失中子と比較して設計の自由度が制限されます。HPDCの高い圧力と流速に対応できる消失中子は、この制限を克服するために必要とされています。HPDC用の塩中子に関する研究は存在しますが、課題も残っています。本稿では、複雑形状と良好な公差を実現するために射出成形で作られ、HPDCの高圧(1000 bar超)に耐え、ガスを放出しない革新的なセラミック消失中子の使用を探求します。この研究は、これらのセラミック中子を用いたHPDCによる乗用車用アルミニウムクロスビームの再設計、製造、実現可能性の実証に焦点を当てており、従来の方法と比較して軽量化、ねじり剛性の向上、製造時間短縮などの利点を目指しています。
4. Summary of the study(研究概要):
Background of the research topic(研究背景):
自動車分野における軽量化の推進は、アルミニウムなどの軽合金を有利にしています。HPDCは、その高い生産性と費用対効果から、これらの合金の主要な製造方法です。しかし、優れた重量比剛性を提供する複雑な中空部品の製造は、従来のHPDCでは困難です。これは、アンダーカットや内部キャビティを従来の方法(金属性中子)で組み込むことの難しさ、または従来の消失中子(砂、塩など)が高圧の射出圧力に対応できないためです。
Status of previous research(従来研究の状況):
従来の研究では、鋳造プロセス用に様々な消耗型中子(砂、塩、金属、有機材料)が検討されてきました。塩中子はHPDC用途で注目されており、その強度やプロセスパラメータに関する研究が行われています。シリンダーブロックなどのHPDC部品に可溶性中子を使用するための特許も存在します。しかし、要求される強度とプロセスの信頼性を達成することは依然として課題です。射出成形によって製造されるセラミック中子は、良好な寸法公差、低い表面粗さ、鋳造中のガス放出がないといった利点を提供し、より高い機械的特性につながる可能性があります。浸出や高圧ウォータージェットなどの脱芯方法が存在しますが、複雑な内部キャビティから抵抗力のある中子を除去することは考慮が必要です。
Purpose of the study(研究目的):
主な目的は、革新的なセラミック消失中子を用いたHPDCによる複雑な中空自動車部品(アルミニウム製乗用車クロスビーム)の製造の実現可能性を調査し、実証することでした。これには、部品の再設計、プロセスと構造性能のシミュレーション、プロトタイプの製造、そして中子と最終鋳造部品の両方の特性評価が含まれます。
Core study(研究核心):
この研究では、既存のオープンプロファイルアルミニウムクロスビーム(EN AC-43500合金)を、セラミック中子(Al2O3 + SiO2 + K2Oベース)を使用して閉じた箱型断面に再設計しました。有限要素解析(FEA)を用いて、元の設計と修正された設計の構造性能(固有値解析、座屈)を比較しました。計算流体力学(CFD)シミュレーションを実施し、セラミック中子の熱特性を考慮して、両設計のHPDCプロセス(充填、凝固、空気巻き込み)を分析しました。実験作業には、異なる焼結温度で製造されたセラミック中子の特性評価(密度、脱芯方法、三点曲げによる機械的特性)が含まれました。選択されたタイプの中子を使用してHPDCプロトタイプが製造されました。最後に、鋳造されたプロトタイプは、微細構造解析(OM、SEM/EDS)およびビッカース微小硬さ試験によって特性評価されました。
5. Research Methodology(研究方法):
Research Design(研究設計):
この研究では、数値シミュレーションと実験的検証を組み合わせて実施しました。既存の自動車用クロスビーム設計を、セラミック中子によって可能になる中空断面を組み込むように修正しました。元のオープンプロファイル設計と新しいクローズドプロファイル(箱型)設計の間で、比較分析(数値的および暗黙的な実験的)を行いました。研究は、部品再設計 → 数値シミュレーション(構造FEAおよびプロセスCFD)→ セラミック中子材料の選択と特性評価 → HPDCによるプロトタイプ製造 → 最終部品特性評価、の順序で進められました。
Data Collection and Analysis Methods(データ収集・分析方法):
- 数値シミュレーション:
- 構造解析 (FEA): Autodesk Simulation® ソフトウェアを使用し、放物線ブリック要素で実施。自由-自由および固定境界条件下での固有値解析(固有振動数)、および印加された力とモーメント荷重下での座屈解析を実施。
- プロセスシミュレーション (CFD): PiQ2社のCastleBodyソフトウェアを使用し、圧縮性-非圧縮性二相流体積(VOF)法を用いて実施。アルミニウム合金(EN AC-43500)とセラミック中子インサートの両方の熱特性を考慮し、金型充填、凝固、空気巻き込み、潜在的な欠陥を分析。局所的な細分化を伴う六面体メッシュ(約1,000,000セル)を使用。
- 実験的特性評価:
- セラミック中子: エタノールを用いたピクノメーターで密度を測定。脱芯効果を化学的浸出(各種酸)および高圧ウォータージェットで試験。UNI EN 843-1およびUNI EN 843-3に従い、三点曲げ試験(Instron 3369)により機械的特性(曲げ強度 σf、ヤング率 E)を決定。
- HPDC部品: IDRA OLS2000 HPDCマシンでプロトタイプを製造。光学顕微鏡(OM - Leica DMI 5000M)およびエネルギー分散型分光法(EDS - Link Analytical eXL)を備えた走査型電子顕微鏡(SEM - LEO EVO 40)を用いて横断面の微細構造を分析。ASTM E92-16およびASTM E140-02に従い、Micro Duromat 4000 Reichert Jung装置を用いて断面全体のビッカース微小硬さ(HV0.3)を測定。
Research Topics and Scope(研究テーマ・範囲):
この研究は、自動車構造部品(クロスビーム)のためのHPDCプロセスにおける革新的なセラミック消失中子の応用に焦点を当てました。範囲には以下が含まれます:
- クロスビームのオープンプロファイルからクローズドプロファイルへの幾何学的再設計。
- 比較構造性能分析(剛性、座屈抵抗)。
- 流体の流れ、熱伝達、凝固、欠陥予測(空気巻き込み、湯境、引け巣)を含むHPDCプロセスの実現可能性シミュレーション。
- Al2O3 + SiO2 + K2Oベースのセラミック中子の特性評価(物理的、脱芯のための化学的耐性、機械的特性)。
- EN AC-43500アルミニウム合金を用いたプロトタイプの実験的製造。
- アルミニウム合金と残留セラミック/サーメット材料間の界面を含む、最終鋳造部品の冶金学的特性評価。
6. Key Results(主な結果):
Key Results(主要な結果):
- 閉じた箱型断面を持つ再設計されたクロスビームは、元のオープンプロファイルと比較してわずかな軽量化を達成しました(3.93 kg 対 3.95 kg)。
- FEAシミュレーションにより、新設計の優れた構造性能が実証されました:元の設計と比較して、より高い固有振動数(剛性の向上を示す、例:自由-自由条件下での最初のねじり振動数が約54.3%増加)および、力とモーメントの両方の荷重条件下で著しく高い座屈荷重係数。
- CFDプロセスシミュレーションにより、セラミック中子を用いたHPDCプロセスの実現可能性が確認されました。予測された鋳造品質(空気巻き込み、凝固パターン、潜在的な欠陥)は、中子のない従来のHPDCプロセスと非常に類似していました。シミュレーションパラメータ(例:充填時間約0.2秒、凝固時間約8.4秒)は、標準的なHPDCの実践と一致していました。
- セラミック中子の特性評価では、密度は約1.92-1.98 g/cm³でした。化学的浸出試験では、HF溶液のみがセラミックをエッチングしましたが、これらはアルミニウムに深刻な損傷を与えました。高圧ウォータージェットが効果的で損傷を与えない脱芯方法として特定されました。機械的試験(三点曲げ)では、焼結温度とともに曲げ強度とヤング率が増加することが示され、「c-1110 °C」バリアントがプロトタイプ用に選択されました。
- 選択されたセラミック中子を使用して、約100個の中空クロスビームプロトタイプがHPDCによって成功裏に製造され、その後ウォータージェットで脱芯されました。製造サイクルタイムは約70秒でした。
- プロトタイプの微細構造分析により、EN AC-43500合金に期待される構造(α-Alマトリックス、Al-Si共晶、α-Al15(Mn,Fe)3Si2などの金属間化合物)が明らかになりました。アルミニウムとセラミック中子の界面の一部の領域で、薄い(約100 µm)サーメット層(セラミック-金属混合物)が観察されましたが、アルミニウムとの良好な密着性を示し、用途に対して有害とは見なされませんでした。
- 部品断面全体のビッカース微小硬さ測定では、75〜90 HV0.3の範囲の値が得られ、これはこの合金とプロセスに典型的であり、中子の存在と薄いサーメット層がバルク材料全体の機械的特性に悪影響を与えなかったことを示しています。
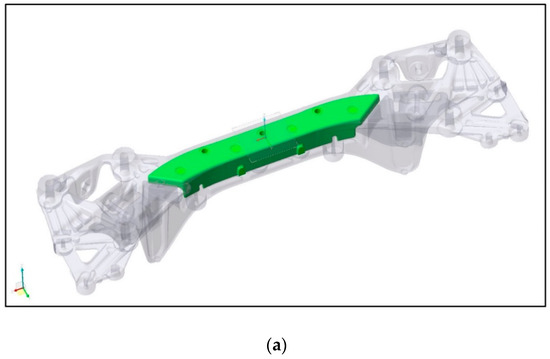
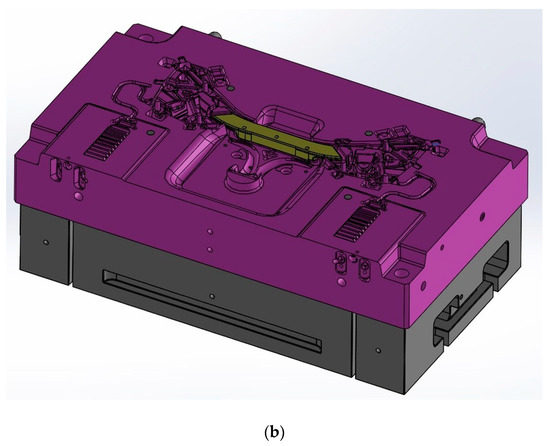
Figure 2. (a) 3D model of the closed profile crossbeam with ceramic core. (b) The geometry and the positioning solutions in the mold cavity adopted for the ceramic core.
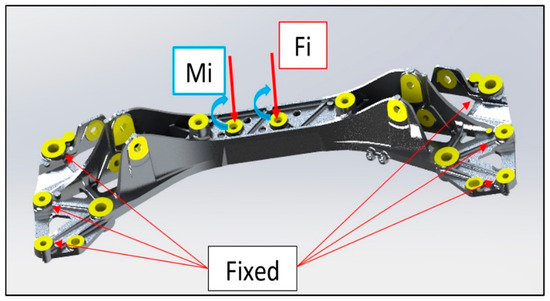
Figure 3. Buckling analysis model: boundary condition and load cases.Table 2. FEM simulation parameters.
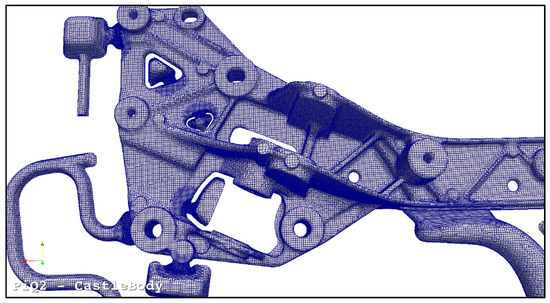
Figure 4. Local mesh refinement.
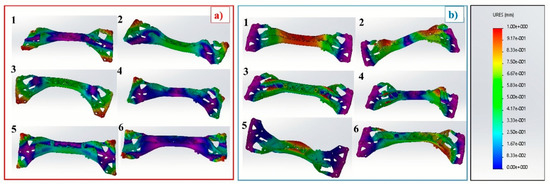
Figure 5. Displacement trend for the first six vibration modes for original geometry: (a) free-free boundary conditions and (b) fixed conditions.
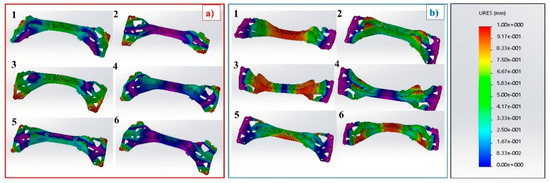
Figure 6. Displacement trend for the first six vibration modes for new geometry: (a) free-free boundary conditions and (b) fixed conditions.
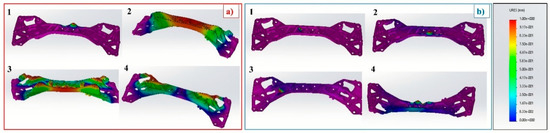
Figure 7. Displacement trend for the first four deformations for original geometry: (a) load case 1 (F); (b) load case 2 (M).
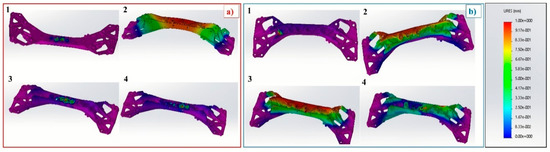
Figure 8. Displacement trend for the first four deformations for new geometry: (a) load case 1 (F); (b) load case 2 (M).
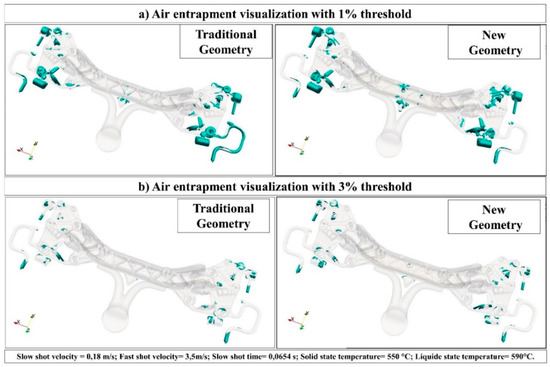
Figure 9. Air entrapment visualization (a) with 1% threshold and (b) with 3% threshold for traditional and new geometry.
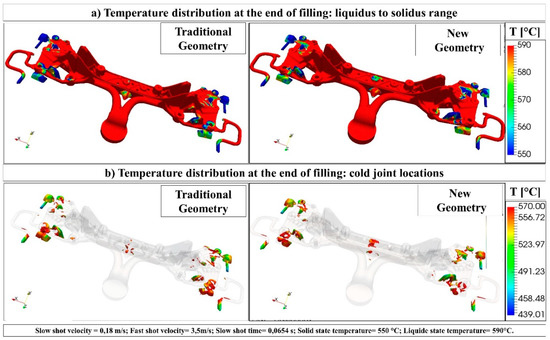
Figure 10. (a) Temperature distribution at the end of filling: liquidus to solidus range; (b) Temperature distribution at the end of filling: cold joint locations.

Figure 11. Results of solidification analysis.Figure 10a,b shows the temperature distribution of the alloy at the end of filling in the range between liquidus and solidus temperatures.
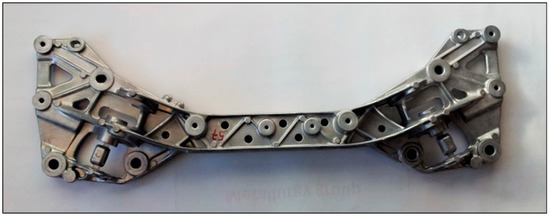
Figure 12. Hollowed aluminum high pressure die casting component.
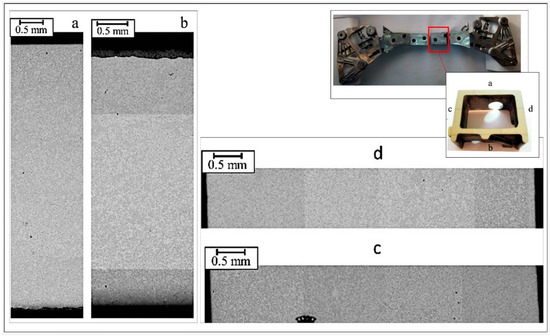
Figure 13. Collage of various micrographs of the transverse sections of the hollowed crossbeam.
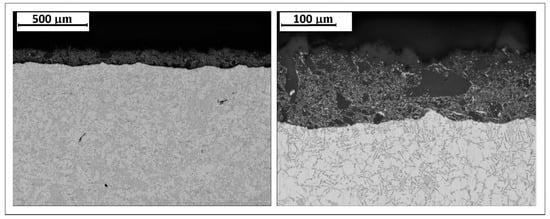
Figure 14. Optical microscope details of the transverse sections of the hollowed crossbeam.
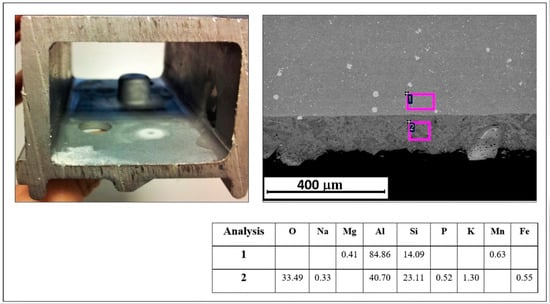
Figure 15. Visual inspection on cermet and SEM image with results of EDS analysis (wt%).
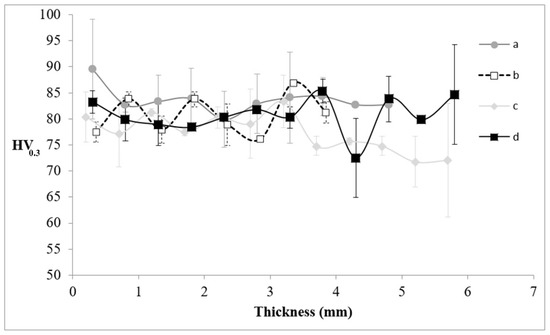
Figure 16. Vickers microhardness HV0.3 variation with respect to the thickness along the transverse section of .
Figure Name List(図リスト):
- Figure 1. 3D design and schematic sketch of the section profile of (a) original crossbeam (b) modified crossbeam. The dimensions are expressed in (mm).
- Figure 2. (a) 3D model of the closed profile crossbeam with ceramic core. (b) The geometry and the positioning solutions in the mold cavity adopted for the ceramic core.
- Figure 3. Buckling analysis model: boundary condition and load cases.
- Figure 4. Local mesh refinement.
- Figure 5. Displacement trend for the first six vibration modes for original geometry: (a) free-free boundary conditions and (b) fixed conditions.
- Figure 6. Displacement trend for the first six vibration modes for new geometry: (a) free-free boundary conditions and (b) fixed conditions.
- Figure 7. Displacement trend for the first four deformations for original geometry: (a) load case 1 (F); (b) load case 2 (M).
- Figure 8. Displacement trend for the first four deformations for new geometry: (a) load case 1 (F); (b) load case 2 (M).
- Figure 9. Air entrapment visualization (a) with 1% threshold and (b) with 3% threshold for traditional and new geometry.
- Figure 10. (a) Temperature distribution at the end of filling: liquidus to solidus range; (b) Temperature distribution at the end of filling: cold joint locations.
- Figure 11. Results of solidification analysis.
- Figure 12. Hollowed aluminum high pressure die casting component.
- Figure 13. Collage of various micrographs of the transverse sections of the hollowed crossbeam.
- Figure 14. Optical microscope details of the transverse sections of the hollowed crossbeam.
- Figure 15. Visual inspection on cermet and SEM image with results of EDS analysis (wt%).
- Figure 16. Vickers microhardness HV0.3 variation with respect to the thickness along the transverse section of Figure 13.
7. Conclusion(結論):
本研究は、革新的なセラミック消失中子を用いたHPDCにより、軽量化され構造的に改善された安全関連自動車部品(アルミニウムクロスビーム)の製造の実現可能性を成功裏に実証しました。再設計された箱型形状は、元のオープンプロファイル設計と比較して、動的挙動(より高い固有振動数)と座屈に対する抵抗が大幅に向上しました。プロセスシミュレーションにより、セラミック中子を用いたHPDCプロセスが従来の製造方法と同等の鋳造品質を達成できることが確認されました。実験的な特性評価により、適切なセラミック中子の特性と効果的な脱芯方法(高圧ウォータージェット)が特定されました。製造されたプロトタイプの分析により、中子と金属の界面に薄い非有害なサーメット層が存在するにもかかわらず、微細構造と硬度が標準的なHPDC部品と一致していることが確認されました。この結果は、複雑な中空ニアネットシェイプ部品を大量生産するためのセラミック消失中子を用いたHPDCの可能性を強調し、先進的な自動車用途におけるHPDCの競争力を高め、中空構造のさらなる軽量化と設計最適化の可能性を開くものです。
8. References(参考文献):
- [1] Chindamo, D.; Gadola, M. Reproduction of real-world road profiles on a four-poster rig for indoor vehicle chassis and suspension durability testing. Adv. Mech. Eng. 2017, 9, 1–10. [CrossRef]
- [2] Chiaberge, M. New Trends and Developments in Automotive Industry; InTech: London, UK, 2011; ISBN 978-953-307-999-8. [CrossRef]
- [3] Tempelman, E. Multi-Parametric study of the effect of materials substitution on life cycle energy use and waste generation of passenger car structures. Transp. Res. Part D Transp. Environ. 2011, 16, 479–485. [CrossRef]
- [4] Cecchel, S.; Chindamo, D.; Turrini, E.; Carnevale, C.; Cornacchia, G.; Gadola, M.; Panvini, A.; Volta, M.; Ferrario, D.; Golimbioschi, R. Impact of reduced mass of light commercial vehicles on fuel consumption, CO2 emissions, air quality, and socio-economic costs. Sci. Total Environ. 2018, 613–614, 409–417. [CrossRef] [PubMed]
- [5] Cecchel, S.; Ferrario, D.; Panvini, A.; Cornacchia, G. Lightweight of a cross beam for commercial vehicles: Development, testing and validation. Mater. Des. 2018, 149, 122–134. [CrossRef]
- [6] Cecchel, S.; Ferrario, D. Numerical and experimental analysis of a high pressure die casting Aluminum suspension cross beam for light commercial vehicles. La Metallurgia Italiana 2016, 6, 41–44.
- [7] Morello, L.; Rosti Rossini, L.; Pia, G.; Tonoli, A. The Automotive Body: Volume I: Components Design; Springer: New York, NY, USA, 2001; ISBN 978-94-007-0513-5.
- [8] Cecchel, S.; Cornacchia, G.; Panvini, A. Cradle-to-Gate Impact Assessment of a High-Pressure Die-Casting Safety-Relevant Automotive Component. JOM 2016, 8, 2443–2448. [CrossRef]
- [9] Cecchel, S.; Chindamo, D.; Collotta, M.; Cornacchia, G.; Panvini, A.; Tomasoni, G.; Gadola, M. Lightweighting in light commercial vehicles: Cradle-to-grave life cycle assessment of a safety relevant component. Int. J. Life Cycle Assess. 2018, 23, 1–12. [CrossRef]
- [10] Cecchel, S.; Collotta, M.; Cornacchia, G.; Panvini, A.; Tomasoni, G. A comparative cradle-to gate impact assessment: Primary and secondary aluminum automotive components case. La Metallurgia Italiana 2018, 2, 46–55.
- [11] Cecchel, S.; Cornacchia, G.; Gelfi, M. Corrosion behavior of primary and secondary AlSi High Pressure Die Casting alloys. Mater. Corros. 2017, 68, 961–969. [CrossRef]
- [12] Solazzi, L. Applied research for Weight Reduction of an industrial Trailer. FME Trans. 2012, 40, 57–62.
- [13] Solazzi, L. Wheel rims for industrial vehicles: Comparative and experimental analyses. Int. J. Heavy Veh. Syst. 2011, 18, 214–225. [CrossRef]
- [14] Hirsch, J. Aluminium in Innovative Light-Weight Car Design. Mater. Trans. 2011, 52, 818–824. [CrossRef]
- [15] Chindamo, D.; Lenzo, B.; Gadola, M. On the vehicle sideslip angle estimation: A literature review of methods, models and innovations. Appl. Sci. 2018, 8, 355. [CrossRef]
- [16] Henriksson, F.; Johansen, K. On Material Substitution in Automotive BIWs – From Steel to Aluminum Body Sides. Procedia CIRP 2016, 50, 683–688. [CrossRef]
- [17] Kelkar, A.; Roth, R.; Clark, J. Automobile Bodies: Can Aluminum Be an Economical Alternative To Steel? JOM 2001, 53, 28–32.
- [18] Zhoua, J.; Wana, X.; Lia, Y. Advanced aluminium products and manufacturing technologies applied on vehicles at the EuroCarBody conference. Mater. Proc. 2015, 2, 5015–5022. [CrossRef]
- [19] Fridlyander, I.N.; Sister, V.G.; Grushko, O.E.; Berstenev, V.V.; Sheveleva, L.M.; Ivanova, L.A. Aluminum alloys: Promising materials in the automotive industry. Met. Sci. Heat Treat. 2002, 44, 365–370. [CrossRef]
- [20] Dioni, D.; Cecchel, S.; Cornacchia, G.; Faccoli, M.; Panvini, A. Effects of artificial aging conditions on mechanical properties of gravity cast B356 aluminum alloy. Trans. Nonferrous Met. Soc. China 2015, 25, 1035–1042. [CrossRef]
- [21] Faccoli, M.; Dioni, D.; Cecchel, S.; Cornacchia, G.; Panvini, A. Optimization of heat treatment of gravity cast Sr-modified B356 aluminum alloy. Trans. Nonferrous Met. Soc. China 2017, 27, 1698–1706. [CrossRef]
- [22] Haracopos, B.; Fisher, T.P. The Technology of Gravity Die Casting; Hart Pub. Co.: Oxford, UK, 1968.
- [23] ASM. Metals Handbook, 10th ed.; ASM-Metals Park: Geauga, OH, USA, 1990.
- [24] Campbell, J.; Harding, R.A. Casting Technology; TALAT 2.0 [CD-ROM]; EAA: Bruxelles, Belgium, 2000.
- [25] Schleg, S.; Kamicki, D.P. Guide to casting and moulding processes. Engineered casting solutions. Technical Articles, 2000.
- [26] Brown, J.R. Foseco Non-Ferrous Foundryman’s Handbook; Elsevier: Oxford, UK, 1999; ISBN 9780080531878.
- [27] Street, A.C. The Diecasting Book, 2nd ed.; Portcullis Press: London, UK, 1990.
- [28] Nagendra Parashar, S.; Mittal, R.K. Elements of Manufacturing Processes; PHI learning Pvt. Ltd.: New Delhi, India, 2006.
- [29] Vinarcik, E.J. High Integrity Die Casting Processes; John Wiley & Sons: Hoboken, NJ, USA, 2002; ISBN 978-0-471-20131-1.
- [30] Andresen, W. Die Cast Engineering: A Hydraulic, Thermal, and Mechanical Process; CRC Press: Boca Raton, FL, USA, 2004.
- [31] Jelínek, P.; Adámková, E.; Mikšovský, F.; Beňo, J. Advances in technology of soluble cores for die castings. Arch. Foundry Eng. 2015, 15, 29–34. [CrossRef]
- [32] Pierri, D. Lost Core: New Perspectives in Die Casting. Available online: https://www.buhlergroup.com/northamerica/en/industry-solutions/die-casting/latest-news/details-7797.htm?title= (accessed on 9 February 2019).
- [33] Czerwinski, F.; Birsan, G.; Benkel, F.; Kasprzak, W.; Walker, M.J.; Smith, J.; Trinowski, D.; Musalem, I. Developing strong core technology for high pressure die casting. Automot. Mater. 2017, 8, 1–11.
- [34] Rupp, S.; Heppes, F. La rivoluzione nella pressofusione. Tecnico-Industria Fusoria 2017, 4, 72–76.
- [35] Donahue, R.J.; Degler, M.T. Congruent Melting Salt Alloys for Use as Salt Cores in High Pressure Die Casting. U.S Patent US9527131B1, 25 August 2014.
- [36] Radadiya, V.A.; Dave, K.G.; Patel, K.R. Design and analysis of salt core for a casting of alluminium alloys. Int. J. Adv. Eng. Res. Dev. 2015, 2, 344–348.
- [37] Jelinek, P.; Miksovsky, F.; Beoo, J.; Adamkova, E. Development of foundry cores based on inorganic salts. MTAEC9 2013, 47, 689–693.
- [38] Jelínek, P.; Adámková, E. Lost cores for high-pressure die casting. Arch. Foundry Eng. 2014, 14, 101–104. [CrossRef]
- [39] Yaokawa, J.; Miura, D.; Anzai, K.; Yamada, Y.; Yoshii, H. Strength of salt core composed of alkali carbonate and alkali chloride mixtures made by casting technique. Mater. Trans. 2007, 8, 1034–1041. [CrossRef]
- [40] Yaokawa, J.; Koichi, A.; Yamada, Y.; Yoshii, H. Strength of salt core for die casting. In Proceedings of the International Conference CastExpo ’05 NADCA, St. Louis, MO, USA, 16–19 April 2005; NADCA: St. Louis, MO, USA, 2005.
- [41] Fuchs, B.; Eibisch, H.; Körner, C. Core viability simulation for salt core technology in high-pressure die casting. Int. J. Metalcast. 2013, 7, 39–45. [CrossRef]
- [42] Fuchs, B.; Körner, C. Mesh resolution consideration for the viability prediction of lost salt cores in the high pressure die casting process. Prog. Comput. Fluid Dyn. 2014, 14, 24–30. [CrossRef]
- [43] Mizukusa, Y. Casting Apparatus and Casting Method for Producing Cylinder Block. U.S. Patent 5,690,159, 27 August 1996.
- [44] Ackerman, A.D.; Aula, H.A. Method of Making a Cast Aluminum Based Engine Block. U.S. Patent 4,446,906, 8 May 1984.
- [45] Brown, W.N.; Robinson, P.M. Soluble Metal Casting Cores Comprising a Water Soluble Salt and a Synthetic Resin. U.S. Patent 364,549, 22 July 1969.
- [46] Gibbons, W.A. Core or Filler of Fusible Material for Hollow Vulcanizable Articles. U.S. Patent 1,523,519, 20 January 1925.
- [47] Foreman, R.W. Mixture and Method for Preparing Casting Cores and Cores Prepared Thereby. U.S. Patent 4,840,219, 20 June 1989.
- [48] Sakoda, T. Water Soluble Core for Pressure Die Casting and Process for Making the Same. U.S. Patent 3,963,818, 15 June 1976.
- [49] Molina, R.; Moschini, R. Production of hollow components in high pressure die casting through the use of ceramic lost cores. In Proceedings of the International Conference High Tech Die Casting 2012, Vicenza, Italy, 9–10 April 2012.
- [50] Moschini, R.; Calzolaro, A.L. Method for Manufacturing Monolithic Hollow Bodies by Means of a Casting or Injection Moulding Process. Patent International Publication No WO 2011/061593 A1, 26 May 2011.
- [51] Solazzi, L. Innovative Bolted junction with high ductility for circular tubular element. J. Constr. Steel Res. 2015, 112, 175–182. [CrossRef]
- [52] Mats, G.; Larson, F.B. The Finite Element Method: Theory, Implementation and Applications; Springer: Berlin, Germany, 2010; ISBN 978-3-642-33286-9.
- [53] Dimitrios, G. Pavlou Essentials of Finite Element Method for Mechanical and Industrial Engineers; Elsevier: Amsterdam, The Netherlands, 2015; ISBN 978-0-12-802386-0.
- [54] Panvini, A.; Molin, D.; Gislon, C. Dual phase simulation for high pressure die casting: Overview and validation of its capabilities. In Proceedings of the HTDC Conference 2016, AIM, Venice, Italy, 22–23 June 2016.
- [55] Panvini, A.; Gislon, C. Air entrapment prediction in diecasting through dual phase simulation. In Proceedings of the Die Casting Congress Tabletop 2013, Louisville, KY, USA, 16–18 September 2013.
- [56] Miller, A. PQ2 and Gating Manual; NADCA: Arlington Heights, IL, USA, 2016.
- [57] UNI EN 843-1:2007. Advanced Technical Ceramics—Mechanical Properties of Monolithic Ceramics at Room Temperature—Part 1: Determination of Flexural Strength; NSAI: Dublin, Ireland, 2007.
- [58] UNI EN 843-2:2007. Advanced Technical Ceramics—Mechanical Properties of Monolithic Ceramics at Room Temperature—Part 2: Determination of Young’s Modulus, Shear Modulus and Poisson’s Ratio; NSAI: Dublin, Ireland, 2007.
- [59] Smith, J.H. An Introduction to Modern Vehicle Design; Elsevier: Oxford, UK, 2002; ISBN 07506 5044 3.
- [60] Pacejka, H.B. Tyre and Vehicle Dynamics, 2nd ed.; Butterworth-Heinemann: Oxford, UK, 2006; ISBN 0-7506-6918-7.
- [61] Franke, R.; Dragulin, D.; Zovi, A.; Casarotto, F. Progress in ductile aluminium high pressure die casting alloys for the automotive industry. La Metallurgia Italiana 2007, 5, 21–26.
- [62] Tinklepaugh, J.R.; James, R. Cermets; Reinhold Publishing Corporation: New York, NY, USA, 1960; ASIN B0007E6FO4.
- [63] Hanaor, D.A.H.; Hu, L.; Kan, W.H.; Proust, G.; Foley, M.; Karaman, I.; Radovic, M. Compressive performance and crack propagation in Al alloy/Ti2AlC composites. Mater. Sci. Eng. 2016, 72, 247–256. [CrossRef]
- [64] Bhattacharya, A.K.; Petrovic, J.J. Ductile phase toughening and R-curve behaviour in a B4C-AI cermet. J. Mater. Sci. 1992, 27, 2205–2210. [CrossRef]
9. Copyright(著作権):
- 本資料は、「Giovanna Cornacchia, Daniele Dioni, Michela Faccoli, Claudio Gislon, Luigi Solazzi, Andrea Panvini and Silvia Cecchel」による論文です。「Experimental and Numerical Study of an Automotive Component Produced with Innovative Ceramic Core in High Pressure Die Casting (HPDC)」に基づいています。
- 論文の出典: https://doi.org/10.3390/met9020217
本資料は上記の論文に基づき要約したものであり、商業目的での無断利用を禁じます。
Copyright © 2025 CASTMAN. All rights reserved.