この論文の要約は、"[論文タイトル]"と題された論文を、"[発行元]"にて発表されたものに基づいています。
1. 概要:
- タイトル: 鋳造欠陥の原因と対策 (Causes of Casting Defects with Remedies)
- 著者: Rahul T Patil, Veena S Metri, Shubhangi S Tambore
- 発表年: 2015年11月
- 掲載ジャーナル/学会: International Journal of Engineering Research & Technology (IJERT), Vol. 4 Issue 11
- キーワード: ダイカスト (Die Casting); 鋳造欠陥 (Defects in Casting); 鋳造欠陥の原因と対策 (Causes and Remedies for Casting Defects)
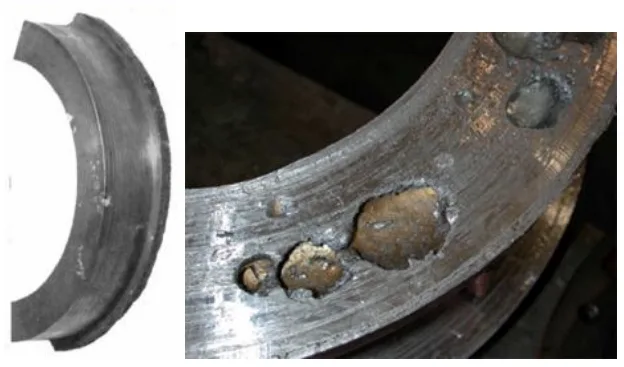
2. 研究背景:
- 研究トピックの社会的/学術的背景: ダイカストは、幾何学的に複雑な部品を効率的かつ経済的に製造できるプロセスとして強調されています。しかし、鋳造欠陥の発生は、このプロセスにおける認識された課題です。ダイカストの品質と効率を維持するためには、これらの欠陥を特定し、対処することが重要です。
- 既存研究の限界: 本論文では、既存研究の限界は明示的に述べられていませんが、特にアルミニウム合金ダイカストにおける鋳造欠陥、その原因、および対策を分類し、説明する統合されたリソースの必要性を示唆しています。
- 研究の必要性: 本研究は、アルミニウムダイカストにおける鋳造欠陥の構造化された理解を提供するために必要です。欠陥をその根本原因に基づいて分類し、対策を詳述することにより、本論文は、鋳造サプライヤーと顧客が欠陥を特定、分析、および修正するのを支援し、最終的に鋳造品質を向上させ、不良率を低減することを目的としています。
3. 研究目的と研究課題:
- 研究目的: 本論文の主な目的は、アルミニウム合金ダイカストで遭遇するさまざまな欠陥を特定し、これらの欠陥の原因とともに、その対策を提供することです。
- 主な研究課題: 本論文は、暗黙のうちに以下の研究課題に取り組んでいます。
- アルミニウム合金ダイカストで観察される一般的な欠陥は何ですか?
- これらの欠陥の根本原因は何ですか?
- これらの欠陥を軽減または排除するための効果的な対策は何ですか?
- 研究仮説: 本論文では、研究仮説は明示的に述べられていませんが、欠陥をその発生源によって分類し、対応する対策を提供することがダイカスト業界にとって有益であるという暗黙の仮説の下で運営されています。
4. 研究方法
- 研究デザイン: 本論文は、レビューおよび分類研究です。鋳造欠陥、原因、および対策に関する既存の知識をまとめ、分類し、特にアルミニウムダイカストに焦点を当てています。
- データ収集方法: 本研究は、ダイカスト欠陥に関連する既存の文献および業界知識のレビューに基づいています。論文は、情報源としてハンドブック、会議議事録、およびジャーナル記事を参照しています。
- 分析方法: 本論文では、定性的な分析手法を採用し、鋳造欠陥をその発生源(冶金学的欠陥、熱関連欠陥、および機械的誘導欠陥)に基づいて分類しています。各欠陥タイプについて、論文は原因を説明し、確立されたダイカストの原則とベストプラクティスに基づいて対策を提案しています。
- 研究対象と範囲: 本論文の範囲は、アルミニウムダイカストにおける鋳造欠陥に限定されています。議論される欠陥は、その発生源に基づいて分類され、表面欠陥と内部欠陥の両方が各カテゴリ内で考慮されています。
5. 主な研究結果:
- 主な研究結果: 本論文では、アルミニウムダイカストにおける鋳造欠陥を、その発生源に基づいて、冶金学的欠陥、熱による欠陥、および機械的誘導欠陥の3つの主要なカテゴリに分類しています。各カテゴリ内で、特定の欠陥タイプが、その原因と対策とともに特定されています。
- 統計的/定性的分析結果: 本論文は主に定性的であり、統計分析は提示されていません。結果は、欠陥、原因、および対策の構造化された分類と説明として提示されています。
- データ解釈: 本論文は、確立された冶金学および製造の原則に基づいて鋳造欠陥を解釈しています。原因は、プロセスパラメータ、材料特性、および設計要因の観点から説明されています。対策は、特定されたこれらの原因を修正することに基づいて提案されています。
- 図のリスト:
- 図 3.1 ガス孔 (Gas porosity)
- 図 3.2 引け巣 (Shrinkage Porosity)
- 図 3.3 ヒケ (Sinks)
- 図 3.4 ブリスター (Blister)
- 図 3.5 ソルダリング (Soldering)
- 図 3.6 偏析 (Segregation)
- 図 3.7 介在物 (Inclusion)
- 図 3.8 ドロス (Dross)
- 図 4.1 クラック (Crack)
- 図 5.1 ホットティア (Hot tears)
- 図 5.2 ホットティア (Hot tears) (部品)
- 図 6.1 コールドシャット (Cold shut) (部品)
- 図 7.1 ミスラン (Misrun) (部品)
- 図 8.1 熱疲労 (Thermal defect)
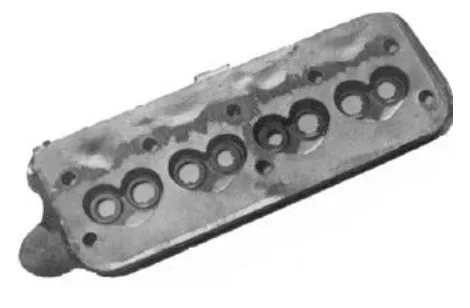
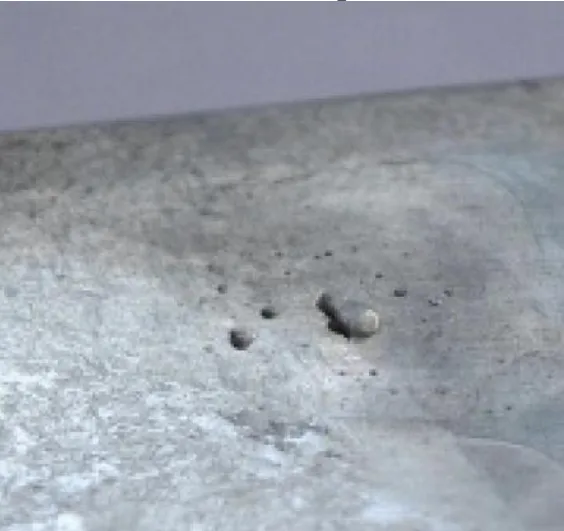
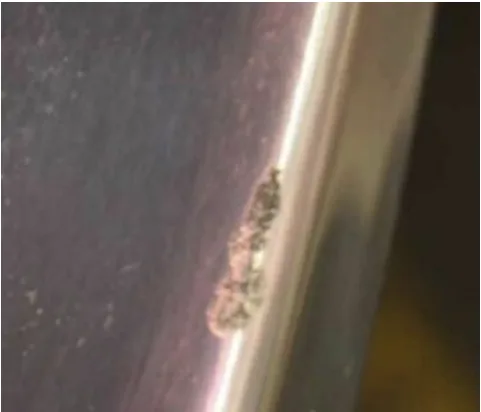
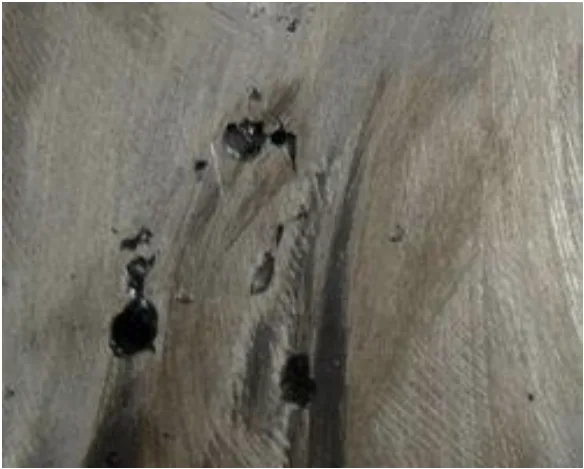
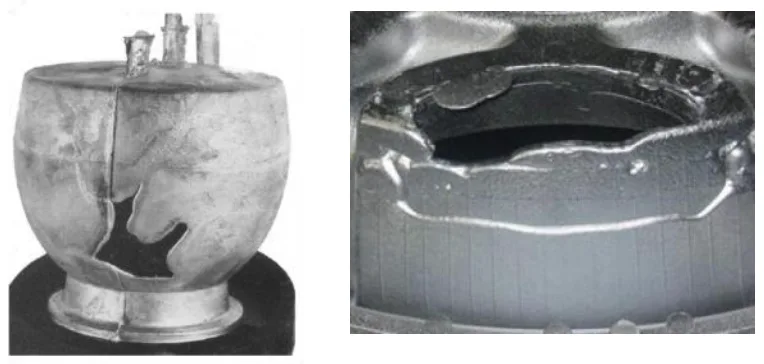
6. 結論と考察:
- 主な結果の要約: 本論文は、アルミニウムダイカストにおけるさまざまな鋳造欠陥を分類し、説明することに成功し、それらを発生源別に分類し、それぞれについて詳細な原因と対策を提供しています。分類には、冶金学的欠陥(ガス孔、ヒケ、介在物、ドロス、ソルダリング)、熱関連欠陥(ホットティア、コールドシャット、熱疲労)、および機械的誘導欠陥(表面傷、曲げ、アンダーカット)が含まれます。
- 研究の学術的意義: 本論文は、さまざまな情報源からの情報を構造化され、アクセスしやすい形式に統合し、鋳造欠陥に関する貴重なハンドブックレベルの要約を提供します。この分類アプローチは、ダイカスト分野の研究者や実務家にとって有用な参考資料として役立ちます。
- 実際的な意義: 各欠陥タイプの原因と対策の詳細な説明は、鋳造業界の品質管理部門に実用的なガイダンスを提供します。この情報を活用することで、ダイカストメーカーは、欠陥分析プロセスを改善し、プロセスパラメータを最適化し、生産性と鋳造歩留まりを向上させるための効果的な対策を実施できます。論文は、鋳造不良を最小限に抑えるには、欠陥の根本原因を理解し、対処することが重要であることを強調しています。
- 研究の限界: 本論文は、レビューおよび分類研究であり、提案された対策の経験的テストまたは検証は含まれていません。対策の有効性は、一般的なダイカストの原則と業界のベストプラクティスに基づいており、特定のケーススタディまたは実験的研究を通じてさらに検証する必要がある場合があります。
7. 今後のフォローアップ研究:
- 今後のフォローアップ研究の方向性: 今後の研究は、以下に焦点を当てる可能性があります。
- 産業環境における設計された実験とケーススタディを通じた、提案された対策の経験的検証。
- 欠陥低減に対するさまざまな対策の有効性の定量的分析。
- ダイカストプロセスにおけるリアルタイムの欠陥検出と分析のための高度な診断ツールと技術の開発。
- 引け巣対策の文脈で簡単に言及されているように、鋳造欠陥を予測および防止するためのシミュレーションソフトウェアの応用の調査。
- さらなる探求が必要な分野: 欠陥の発生を最小限に抑えるためのプロセスパラメータと合金組成の最適化、およびダイカストのためのより堅牢で自動化された品質管理システムの開発の分野で、さらなる探求が必要です。
8. 参考文献:
- [1] D.L cocks. “A proposed simple qualitative classification for die-casting"; 'Proc Die-casting Conference, Montreaux(1996)
- [2] ASM Handbook: Volume 15: Casting edition 9",2008,pp629-620.
- [3] J. Campbell, R.A hardening. "Casting technology", in TAIAT 2.0ncd-rom, EAA, Brussels, 2000
- [4] John Gilbert Kaunfman, Elwin L. Rooy," Aluminum alloy casting: Properties, Processes, and application", ASM international,pp47-54
- [5] R.Monroe," porosity in casting", AFS Transcation,2005,pp1-29.
- [6] Defect formation in cast iron LennartElmquist School of Engineering Jönköping University, SwedenTammerfors, Finland, November 8, 2012.
- [7] Analysis of Casting Defects and Identification of emedial Measures - A Diagnostic Study Dr D.N. Shivappal, Mr Rohit2, Mr. Abhijit Bhattacharya3 International Journal of Engineering Inventions ISSN: 2278-7461, www.ijeijournal.com Volume 1, Issue 6 (October2012) PP: 01-05
- [8] Casting Defect Analysis using Design of Experiments (DoE) and Computer Aided Casting Simulation Technique Uday A. Dabade* and Rahul C. Bhedasgaonkar,(2013) [5]. Reduction of defects in grey cast iron castings by six sigma approach Raguramsingh.M#1, SyathAbuthakeer.S*2 #ME Lean Manufacturing, PSG.
- [9] W.G WAlkington, “Gas Porosity: A guid t corrective the problem, North America die casting association, "1997.
9. 著作権:
*この資料は、"Rahul T Patil, Veena S Metri, Shubhangi S Tambore"氏の論文:"鋳造欠陥の原因と対策 (Causes of Casting Defects with Remedies)"に基づいています。
*論文ソース: www.ijert.org
この資料は上記の論文に基づいて要約されたものであり、商業目的での無断使用は禁止されています。
Copyright © 2025 CASTMAN. All rights reserved.