この論文概要は、['CHINA FOUNDRY']が発行した論文「['高圧ダイカストプロセスにおける界面熱伝達係数の決定とその応用']」に基づいて作成されました。
1. 概要:
- タイトル: 高圧ダイカストプロセスにおける界面熱伝達係数の決定とその応用 (Determination of interfacial heat transfer coefficient and its application in high pressure die casting process)
- 著者: Cao Yongyou, Guo Zhipeng, Xiong Shoumei
- 発行年: 2014年
- 発行ジャーナル/学会: CHINA FOUNDRY
- キーワード: 高圧ダイカスト (high pressure die casting); 界面熱伝達係数 (interfacial heat transfer coefficient); 逆解析法 (inverse method)
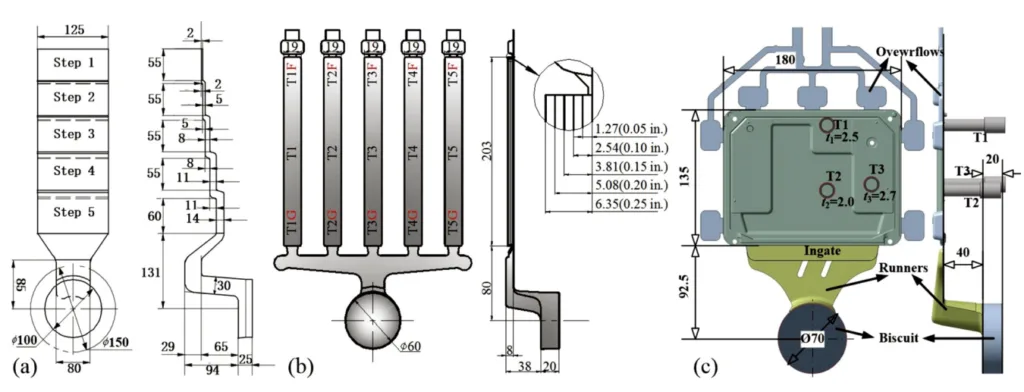
2. 抄録または序論
本論文では、高圧ダイカスト(HPDC)における界面熱伝達の研究進捗をレビューします。界面熱伝達係数(IHTC)の決定、鋳造厚さの影響、プロセスパラメータ、および鋳造合金がIHTCに及ぼす影響に関する結果を要約し、考察します。熱境界条件モデルは、2つの相関関係、すなわち(a)IHTCと鋳造凝固率、(b)IHTCピーク値と初期金型表面温度に基づいて開発されました。次に、境界モデルをHPDCにおける温度場決定に適用し、優れた一致が確認されました。
3. 研究背景:
研究トピックの背景:
高圧ダイカスト(HPDC)は、薄肉部品を製造するためのネットシェイププロセスです。ダイカストの優れた特性により、ダイカスト製品は自動車、航空宇宙、医療、電子機器、およびその他の産業でますます使用されています。金型充填、凝固、および金型内部の温度分布を予測する数値シミュレーション技術は、鋳造技術および鋳造製品開発において非常に重要になっています。しかし、シミュレーションの有効性は、材料特性の精度と、金属-金型境界およびシミュレーションソフトウェアの初期条件に依存します。金属-金型界面での熱伝達挙動を特徴づける界面熱伝達係数(IHTC)は、コンピュータシミュレーションにおける凝固プロセス中の最も重要なパラメータの1つと考えられています。IHTCの決定と応用は、現在研究者にとって重要な課題となっています。
既存研究の現状:
IHTCを決定するための既存の方法は、(1)純粋解析的アプローチ、(2)経験的相関関係に基づく半解析的アプローチ、(3)数値的アプローチに分類されます。純粋解析的および半解析的アプローチは、IHTCが一定であると仮定していますが、これは重大な制限です。数値的アプローチ、特に逆熱伝導問題(IHCP)は、界面を横切る熱流束履歴をより完全に探求する方法を提供します。過去の研究では、1970年代からHPDCにおけるIHTCが調査されてきましたが、温度測定は依然として困難な課題であり、不適切な熱電対の設置は不確実性につながる可能性があります。
研究の必要性:
HPDCにおいてIHTCを正確に決定することは、鋳造プロセスと製品開発を最適化するために不可欠な数値シミュレーションの精度を向上させるために非常に重要です。HPDCにおける過渡的な熱伝達の性質と直接測定の困難さから、IHTCの決定とプロセスモデリングへの応用に関する堅牢な方法に関するさらなる研究が必要です。
4. 研究目的と研究課題:
研究目的:
本論文は、高圧ダイカスト(HPDC)における界面熱伝達係数(IHTC)の決定に関する研究進捗をレビューし、清華大学グループの実験的知見に基づいた熱境界条件モデルを提示することを目的としています。
主要な研究内容:
- HPDCにおけるIHTC決定のための既存の方法(解析的、半解析的、数値的)のレビュー。
- 鋳造厚さ、プロセスパラメータ、および鋳造合金を含む、IHTCに影響を与える要因の要約。
- IHTCと鋳造凝固率の間の相関関係、およびIHTCピーク値と初期金型表面温度に基づいて熱境界条件モデルを開発。
- 開発された境界モデルをHPDCの温度場決定に適用し、実験結果との比較検証。
研究仮説:
明示的に仮説として述べられていませんが、本研究は以下の前提に基づいています。
- HPDCのIHTCは一定ではなく、凝固プロセス中に変化します。
- 数値的方法、特にIHCPは、正確なIHTC決定に不可欠です。
- IHTCは、鋳造厚さ、プロセスパラメータ(射出速度、金型温度、圧力)、および鋳造合金の影響を受けます。
- IHTC相関関係に基づく熱境界条件モデルは、HPDCシミュレーションで温度場を正確に予測できます。
5. 研究方法
研究デザイン:
本論文は、既存の文献と著者の独自の研究を要約したレビュー論文です。清華大学グループが実施したダイカスト実験からの実験的知見を組み込み、熱境界条件モデルの開発と検証を裏付けています。
データ収集方法:
本論文では、著者および他の研究者による過去の研究からの実験データをレビューします。清華大学グループの実験では、特別に設計された「ステップ形状」、「フィンガー形状」、「カバープレート形状」の鋳造品(図1)を利用しました。温度測定は、ダイカスト界面から1、3、6mm離れた位置で、特殊な温度センサーユニット(TSU)を使用して行われました。
分析方法:
本論文では、IHTC決定のためのさまざまな解析的、半解析的、および数値的方法について考察します。清華大学グループは、逆解析法を用いて熱伝達係数を評価しました。相関分析および回帰分析法を使用して、IHTC、プロセスパラメータ、鋳造凝固率、および金型表面温度間の関係を確立しました。
研究対象と範囲:
本研究は、高圧ダイカスト(HPDC)における界面熱伝達に焦点を当てています。範囲は以下を含みます。
- HPDCにおけるIHTC決定方法に関する文献レビュー。
- HPDCにおけるアルミニウム合金(ADC12、AM50、AM60B、B390)を用いた実験的研究。
- 鋳造厚さ、プロセスパラメータ(射出速度、金型温度、圧力)、および鋳造合金がIHTCに及ぼす影響の調査。
- HPDCシミュレーションのための熱境界条件モデルの開発と応用。
6. 主な研究結果:
主要な研究結果:
- IHTC決定方法: 純粋解析的、半解析的、および数値的(逆解析法)アプローチを含む、IHTC決定方法のレビュー。数値的方法、特にIHCPが、過渡的な熱伝達を捉えるのに効果的であることを強調しています。
- IHTCに影響を与える要因: 鋳造厚さ、プロセスパラメータ(射出速度、初期金型温度、圧力)、および鋳造合金(ADC12、AM50、AM60B、B390)がIHTCに及ぼす影響を要約。速い射出速度と初期金型温度が顕著な影響を与えることがわかりました。圧力の影響は議論の余地があり、鋳造厚さに依存します。
- IHTC進化段階: HPDC中のIHTC進化の4つの段階、すなわち初期増加段階、高値維持段階、急速減少段階、および低値維持段階を特定しました。
- 熱境界条件モデル: (a)IHTCと鋳造凝固率、および(b)IHTCピーク値と初期金型表面温度の2つの相関関係に基づいて、熱境界条件モデルを開発しました。モデルは、4つのIHTC進化段階のそれぞれの方程式によって記述されます(図6)。
- (i) h = hmax: 初期増加段階以前および段階中
- (ii) h = hmax - fs / fsF ×(hmax - ho): 高値維持段階
- (iii) h = ho+khf ×(1-fs)ε: 急速減少段階
- (iv) h = ho: 低値維持段階
- モデル検証: 開発された熱境界条件モデルをカバープレート形状鋳造品の温度場および熱平衡のシミュレーションに適用し、実験結果と優れた一致を示しました(図7および8)。
提示されたデータの分析:
- IHTCプロファイル(図2): IHTCはショット後に急速に増加し、最大値に達し、高いレベルを維持してから急激に減少します。ADC12合金はAM50よりも高いIHTCを示します。薄いステップは、よりスリムなIHTCプロファイルを示しています。
- 初期金型温度の影響(図3、4、5): IHTCピーク値(hmax)は、一般に初期金型表面温度(ODI)の増加とともに減少します。相関分析により、ln(hmax/ODI²)とln(ODI)の間の関係が明らかになりました(式4および5)。
- モデルの応用(図7、8): 開発された熱境界条件モデルを使用したシミュレーションは、鋳造サイクル中の鋳造品および金型表面温度の変化を正確に予測し、HPDCにおける過渡的な熱伝達挙動を捉えるモデルの能力を実証しました。
図リスト:
- 図 1: (a) ステップ形状鋳造、(b) フィンガー形状鋳造、(c) カバープレート形状鋳造の構成
- 図 2: AM50およびADC12合金のステップ1〜5で計算された熱伝達係数プロファイル
- 図 3: AM50およびADC12合金のステップ1〜5の初期金型温度の関数として計算されたIHTCピーク [24]
- 図 4: B390合金のフィンガー形状鋳造の初期金型温度の関数として計算されたIHTCピーク [8]
- 図 5: AM60B合金のカバープレート形状鋳造の初期金型温度の関数として計算されたIHTCピーク [7]
- 図 6: 熱境界条件モデルの熱伝達係数の4つの段階
- 図 7: カバープレート形状鋳造の1サイクル中の鋳造表面温度変化
- 図 8: カバープレート形状鋳造の1サイクル中の金型表面温度変化
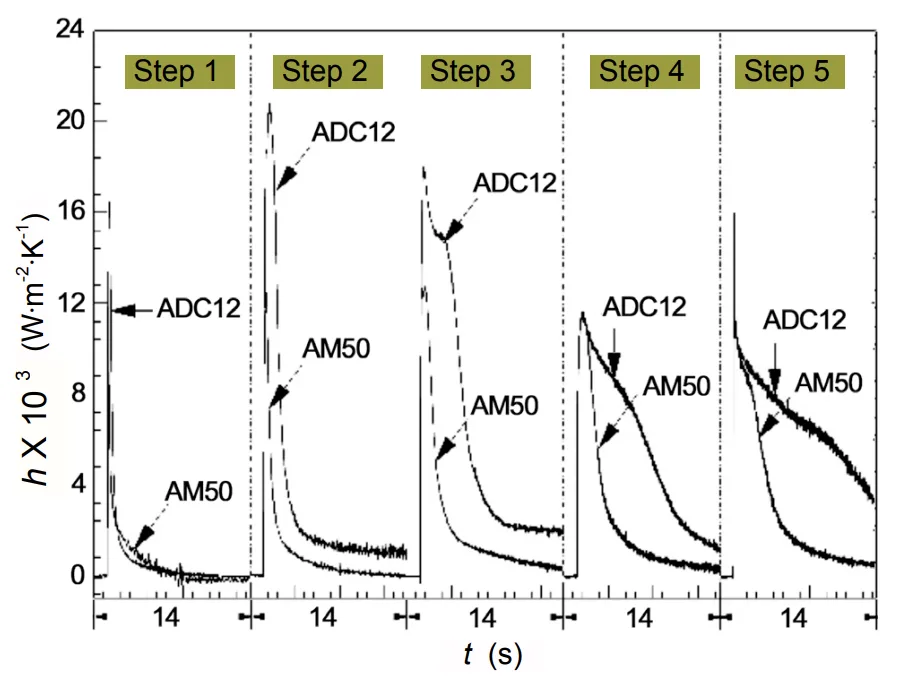
![Fig. 3: Calculated IHTC peaks as a function of initial die temperature of steps 1 to 5 for AM50 and ADC12 alloys [24]](https://castman.co.kr/wp-content/uploads/image-973-png.webp)
![Fig. 4: Calculated IHTC peaks as a function of initial die temperature of finger-shape casting for B390 alloy[8]](https://castman.co.kr/wp-content/uploads/image-974-1024x705.webp)
![Fig. 5: Calculated IHTC peaks as a function of initial die temperature of cover-plate casting for AM60B alloy [7]](https://castman.co.kr/wp-content/uploads/image-975-1024x729.webp)
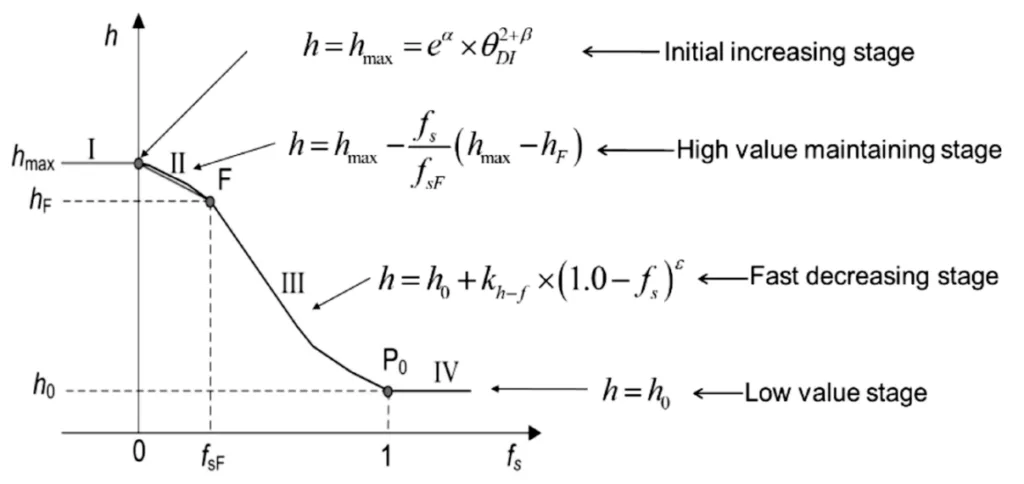
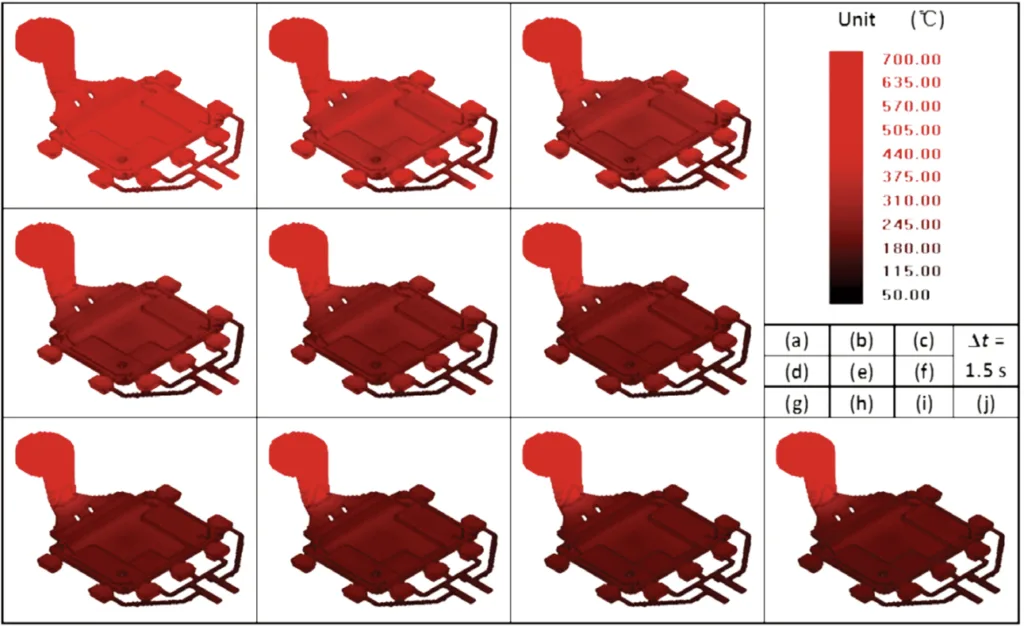
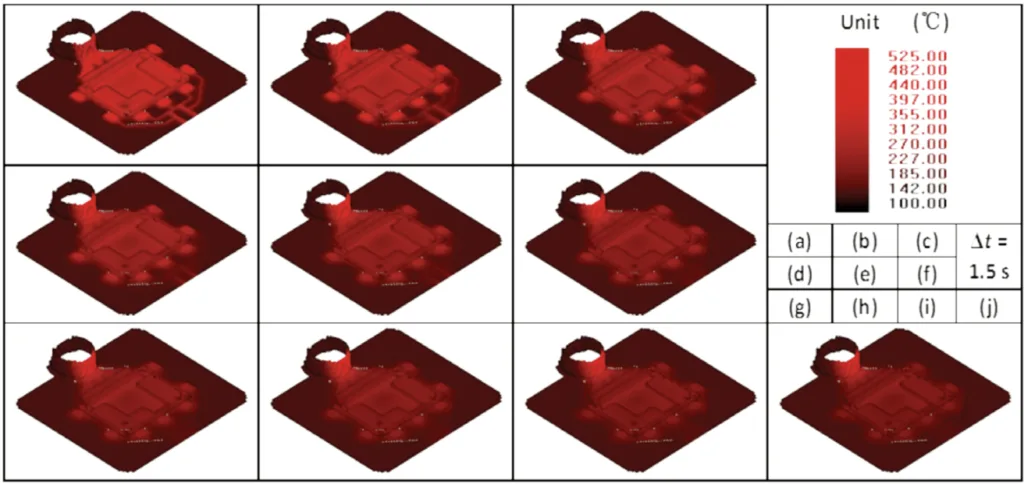
7. 결론:
7. 結論:
主な調査結果の要約:
本論文では、高圧ダイカスト(HPDC)における界面熱伝達係数(IHTC)の決定に関する研究進捗をレビューしました。IHTC決定のための3つの主要なアプローチを要約し、HPDCにおける正確な温度測定の課題を強調しました。清華大学グループの研究進捗を提示し、IHTC、鋳造凝固率、および初期金型表面温度間の相関関係に基づく熱境界条件モデルを開発しました。モデルはシミュレーションを通じて検証され、実験データと優れた一致を示しました。
研究の学術的意義:
本レビューは、HPDCにおけるIHTC研究の包括的な概要を提供し、決定方法と影響要因に関する知識を統合します。開発された熱境界条件モデルは、HPDCシミュレーションにおける金属-金型界面での熱伝達をより正確に表現することに貢献し、鋳造プロセスモデリングの分野を前進させます。
実用的な意義:
検証された熱境界条件モデルは、HPDCプロセスシミュレーションに実際に適用して、温度場と凝固挙動の予測を改善できます。これは、金型設計、プロセスパラメータ、そして最終的には産業用HPDCアプリケーションにおける鋳造品質と効率を最適化するのに役立ちます。
研究の限界と今後の研究分野:
本論文は、主にアルミニウム合金と特定の鋳造形状に焦点を当てています。今後の研究では、以下が必要です。
- より広範囲の鋳造合金と複雑な形状に対する熱境界条件モデルの検証。
- IHTCに対する他のプロセスパラメータと金型コーティング条件の影響の調査。
- ギャップ形成や表面粗さ効果など、金属-金型界面でのより複雑な現象を考慮に入れるためのモデルの改良。
- HPDCにおける実験的なIHTC決定の精度を向上させるための高度な温度測定技術の探求。
8. 参考文献:
- [1] Nelson C W. Nature of heat transfer at the die face. In: Proceedings of 6th SDCE International Die Casting Congrass; Cleveland, OH, 1970: 1-8.
- [2] Garcia A and Prates M. Mathematical model for the unidirectional solidification of metals: I. Cooled molds. Metallurgical Transaction B, 1978, 9(3): 449-457.
- [3] Garcia A, Clyne T, and Prates M. Mathematical model for the unidirectional solidification of metals: II. Massive molds. Metallurgical Transactions B, 1979, 10(1): 85-92.
- [4] Prates M and Biloni H. Variables affecting the nature of the chill zone. Metallurgical Transactions, 1972, 3(6): 1501-1510.
- [5] Beck J V. Nonlinear estimation applied to the nonlinear inverse heat conduction problem. International Journal of Heat and Mass Transfer, 1970, 13(4): 703-716.
- [6] Beck J V, Blackwell B, and Clair C R. Inverse Heat Conduction: III-posed problems, 1985.
- [7] Cao Y, Guo Z, and Xiong S. A Study on Heat Transfer at Metal/ Die Interface during High Pressure Die Casting of AM60B Alloy. In: Proceedings of the 8th Pacific Rim International Congress on Advanced Materials and Processing (Pricm 8). Waikoloa, Hawaii, US, TMS (The Minerals, Metals & Materials Society), 2013: 3041-3049.
- [8] Cao Y, Guo Z, and Xiong S. Determination of the metal/die interfacial heat transfer coefficient of high pressure die cast B390 alloy. IOP Conference Series, Materials Science and Engineering, 2012, 33(1): 012010.
- [9] Guo Z P, Xiong S M, Liu B C, et al. Effect of Process Parameters, Casting Thickness, and Alloys on the Interfacial Heat Transfer coefficient in the High-Pressure Die-Casting Process. Metallurgical and Materials Transactions A: Physical Metallurgy and Materials Science, 2008, 39A(12): 2896-2905.
- [10] Guo Z P, Xiong S M, Liu B C, et al. Determination of the heat transfer coefficient at metal-die interface in high pressure die casting process of AM50 alloy. International Journal of Heat and Mass Transfer. 2008, 51(25-26): 6032-6038.
- [11] Guo Z P, Xiong S M, Murakami M, et al. Study on interfacial heat transfer coefficient as metal/die interface during high pressure die casting process of AZ91D alloy. China Foundry, 2007, 4(1): 5-9.
- [12] Hamasaiid A, Dour G, Dargusch M et al. Heat transfer at the casting /die interface in high pressure casting - Experimental results and contribution to modeling. In: Proceedings of MCWASP XI: Modeling of Casting, Welding and Advanced Solidification Processes, Opio, France: Minerals, Metals and Materials Society (TMS), 2006, 2: 1205-1212.
- [13] Dour G, Daugusch M, Davidson C, et al. Development of a non-intrusive heat transfer coefficient gauge and its application to high pressure die casting; Effect of the process parameters. Journal of Materials Processing Technology, 2005, 169(2): 223-233.
- [14] Hallam C P and Griffiths W D. A model of the interfacial heat-transfer coefficient for the aluminum gravity die-casting process. Metallurgical and Materials Transactions B: Process Metallurgy and Materials Processing Science, 2004, 35(4): 721-733.
- [15] El-Mahallawy N A, Taha M A, Pokora E, et al. On the influence of process variables on the thermal conditions and properties of high pressure die-cast magnesium alloys. Journal of Materials Processing Technology, 1998, 73(1-3): 125-138.
- [16] Papai J and Mobley C. Die thermal fields and heat fluxes during die casting of 380 aluminum alloy in H-13 steel dies. NADCA Transactions, 1991: 377-384.
- [17] Ho K and Pehlke R D. Metal-mold interfacial heat transfer. Metallurgical Transactions B (Process Metallurgy), 1985, 16B(3): 585-594.
- [18] Sekhar J A, Abbaschian G J, and Mehrabian R. Effect of pressure on metal-die heat transfer coefficient during solidification. Materials Science and Engineering, 1979, 40(1): 105-110.
- [19] Hong S, Backman D, and Mehrabian R. Heat transfer coefficient in aluminum alloy die casting. Metallurgical Transactions B, 1979, 10(2): 299-301.
- [20] Backman D, Mehrabian R, and Flemings M. Die thermal behavior in machine casting of partially solid high temperature alloys. Metallurgical Transactions B, 1977, 8(2): 471-477.
- [21] Ho K and Pehlke R D. Transient methods for determination of metal-mold interfacial heat transfer. In: Proceedings of Transactions of the American Foundrymen's Society, Proceedings of the Eighty-seventh Annual Meeting, Rosemont, II, USA, AFS, 1983, 91: 689-698.
- [22] Dour G, Dargusch M, and Davidson C. Recommendations and guidelines for the performance of accurate heat transfer measurements in rapid forming processes. International Journal of Heat and Mass Transfer, 2006, 49(11-12): 1773-1789.
- [23] Hamasaiid A, Dour G, Dargusch M S, et al. Heat-transfer coefficient and in-cavity pressure at the casting-die interface during high-pressure die casting of the magnesium alloy AZ91D. Metallurgical and Materials Transactions A - Physical Metallurgy and Materials Science, 2008, 39A(4): 853-864.
- [24] Guo Z P, Xiong S M, Liu B C, et al. Development of thermal boundary condition model at metal/die interface of high pressure die casting process. International Journal of Cast Metals Research, 2011, 24(3-4): 151-157.
9. 著作権:
- この資料は、"Cao Yongyou, Guo Zhipeng, and Xiong Shoumei"の論文:「高圧ダイカストプロセスにおける界面熱伝達係数の決定とその応用」に基づいています。
- 論文ソース: [https://doi.org/](DOI URLは論文に記載されていないため、もしあれば追記してください)
この資料は上記の論文を要約したものであり、商業目的での無断使用は禁止されています。
Copyright © 2025 CASTMAN. All rights reserved.