この紹介記事は、[IOS Press]によって発行された論文「"Establishing Guidelines to Improve the High-Pressure Die Casting Process of Complex Aesthetics Parts"」の研究内容を紹介するものです。
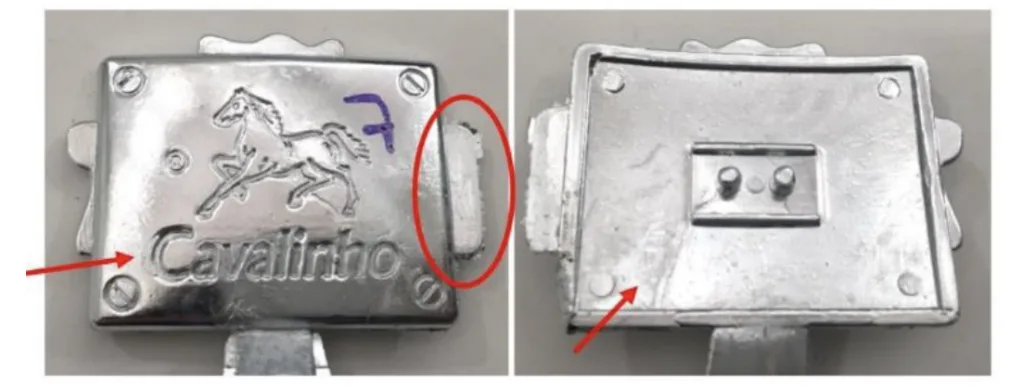
1. 概要:
- タイトル: Establishing Guidelines to Improve the High-Pressure Die Casting Process of Complex Aesthetics Parts
- 著者: F.J.G. SILVA, Raul D.S.G. CAMPILHO, Luís Pinto FERREIRA and Maria Teresa PEREIRA
- 発行年: 2018年
- 発行ジャーナル/学会: Transdisciplinary Engineering Methods for Social Innovation of Industry 4.0, M. Peruzzini et al. (編), IOS Press
- キーワード: Die casting, Casting, Casting defects, Zamak, Aesthetic parts.
2. 概要 / 導入
本論文は、仕上げ加工を最小限に抑えるためのザマック合金製美的部品のハイプレッシャーダイカスト(HPDC)プロセスの最適化という課題に取り組んでいます。ザマック合金は融点が低いため複雑な形状の部品に適していますが、美的用途で欠陥のない表面仕上げを実現するには、射出パラメータと金型構成を注意深く制御する必要があります。本研究では、複雑な美的ザマック部品の鋳造における改善された結果のためのガイドラインを確立するために、SolidCast™ソフトウェアを使用した数値シミュレーションと経験的試験を通じて、HPDCプロセスとパラメータを調査します。論文の構成は、文献レビュー、方法論、実験設定、結果と考察、および将来の研究のための提案を含む結論で構成されています。
3. 研究背景:
研究トピックの背景:
軽量材料で作られた複雑な部品の使用はますます一般的になっています。ハイプレッシャーダイカスト(HPDC)は、これらの部品を迅速かつ費用対効果の高い方法で製造するために頻繁に採用されています。軽量合金であるザマックは、機械部品に広く使用されており、複雑な仕上げ加工が必要な美的部品にも応用できます。主な目的は、美的部品にHPDCを利用し、それによって仕上げ加工を削減または排除し、最終コストを削減することです。
既存研究の現状:
既存の研究では、ダイカストが幾何学的に複雑な金属部品、特に自動車産業における主要な製造技術として認識されています[1]。HPDCプロセスには、溶融材料の温度、射出圧力、射出時間、オーバープレッシャー、凝固時間など、いくつかのパラメータが関係しています[11-13]。スプルー、ゲート、位置決め、潤滑、厚さ、冷却システムなどの金型設計要素も重要です[14]。先行研究では、ゲート設計[15]、熱流[16, 17]、離型プロセス[18]、射出条件の最適化[19]などが検討されています。有限要素法(FEM)[20]に基づくソフトウェアは、ダイカストプロセスのシミュレーションの精度を向上させています[22-24]。しかし、鋳造プロセスは依然として欠陥が発生しやすく、最適な結果を得るためには、パラメータ、熱伝達、材料の流れを相関させるさらなる研究が必要です[25-28]。
研究の必要性:
シミュレーションとプロセス最適化の進歩にもかかわらず、HPDC美的部品で高い表面品質を達成することは依然として困難であり、多くの場合、広範な仕上げ加工が必要です。表面欠陥を最小限に抑え、費用のかかる仕上げ加工を削減または排除するために、美的部品専用にHPDCパラメータと金型条件を最適化する必要があります。本研究は、単一の射出鋳造操作で欠陥のない美的ザマック部品を実現するための実用的なガイドラインを確立することを目的としています。
4. 研究目的と研究課題:
研究目的:
研究目的は、ザマック合金製の複雑な美的部品のハイプレッシャーダイカスト(HPDC)プロセスを改善するためのガイドラインを確立することです。目標は、射出パラメータと金型構成を最適化して、その後の仕上げ加工を最小限に抑えながら、単一の鋳造操作で良好な美的外観を備えた欠陥のない部品を取得することです。
主な研究課題:
主な研究課題は次のとおりです。
- ザマック美的部品の表面品質に対する射出パラメータ(圧力、射出時間、冷却時間)の影響を調査する。
- 数値シミュレーションを利用して、金型内の材料の流れを理解し、ランナーシステムやベントを含む金型設計を最適化する。
- 経験的試験と高度なシミュレーションを組み合わせたハイブリッド方法論を開発し、最適なプロセスパラメータと金型構成を特定する。
- 欠陥と仕上げ加工を最小限に抑えるための、複雑な美的ザマック部品のHPDCに関する実用的なガイドラインを確立する。
5. 研究方法
研究デザイン:
本研究では、「図1」に示すように、「経験的アプローチ(Empirical Approach)」と「高度なアプローチ(Advanced Approach)」を統合したハイブリッド方法論を採用しました。「経験的アプローチ」では、圧力、射出時間、冷却時間などの射出パラメータを調整することにより、体系的な実験を実施しました。「高度なアプローチ」では、SolidCast™ソフトウェアを使用した数値シミュレーションを利用して、材料の流れを分析し、金型設計を最適化しました。
データ収集方法:
経験的データは、PR METAL, Ltd.製のZM3装置を使用した一連のダイカスト試験を通じて収集されました。最初の射出試験のために確立されたパラメータを「表1」に示します。3!の要因計画法を使用し、パラメータセットごとに3回の試験を実施し、合計81回の試験を実施しました。数値シミュレーションデータは、SolidCast™ソフトウェアを使用して生成され、さまざまな金型およびランナー構成下での材料の流れと凝固をモデル化しました。
分析方法:
鋳造部品の品質は、主に表面欠陥と金型充填の完全性の目視観察によって評価されました。シミュレーション結果を分析して、材料の流れのパターンを理解し、潜在的な欠陥領域を特定し、金型設計の変更の影響を評価しました。「石川ダイアグラム(Ishikawa diagram)」(「図3」)を使用して、表面品質の問題に寄与する可能性のある要因を体系的に分析しました。
研究対象と範囲:
研究は、ザマック5合金のハイプレッシャーダイカストに焦点を当てました。材料組成は、3.8%Al、0.95%Cu、0.6%Mg、0.04%Fe、残部Znでした。ケーススタディ部品は、通常女性用財布に使用される美的部品でした。「図2」に示されているように、美的部品をケーススタディとして選択しました。実験は、単一キャビティ金型を使用して実施されました。この研究では、圧力、射出時間、冷却時間の影響を調査し、最初は金型形状、ゲート位置、ベントチャネルを一定に保ち、その後、シミュレーション結果に基づいて金型設計を変更しました。
6. 主な研究結果:
主な研究結果:
本研究により、美的ザマック部品のHPDCプロセスを改善するためのガイドラインが確立されました。「表2」は、最初の試験ラウンドからの特徴的な結果をまとめたもので、「充填不足(Lack of filling)」、「小さな表面のへこみと亀裂(Small surface depression and crack)」、「非常に悪い表面品質(Really bad surface quality)」などの欠陥が、異なるパラメータセットで示されています。シミュレーションと反復的な経験的試験を通じて、最適化されたパラメータと金型設計が特定されました。「表3」は、最適化された条件からの最も特徴的な結果を示しており、部品品質の改善を達成しています。「図6」は、最適化された金型設計とパラメータで得られた部品を示しており、コーティング前の仕上げ工程を省略するのに十分な改善された表面品質を示しています。
提示されたデータの分析:
最初の経験的試験(「表2」)では、冷却時間が短いと表面品質が低下することが明らかになりました。中程度の冷却時間でも欠陥が見られましたが、直接的な相関関係は不明確でした。射出時間も最初は明確な傾向を示しませんでしたが、射出時間を短縮すると、金属速度が速くなり、乱流が増加し、表面品質が低下しました。金型充填中の乱流を減らすためには、圧力を下げることが重要であることが特定されました。シミュレーション(「図4」と「図5」)では、金型位置を反転させ、中央ランナーを使用し、ライザーを組み込むことで、材料の流れが改善され、乱流が減少することが示されました。最適化されたパラメータ(圧力:2 bar、射出時間:0.5秒、冷却時間:1秒)と金型修正を組み合わせることで、表面品質が大幅に向上した部品が得られました。
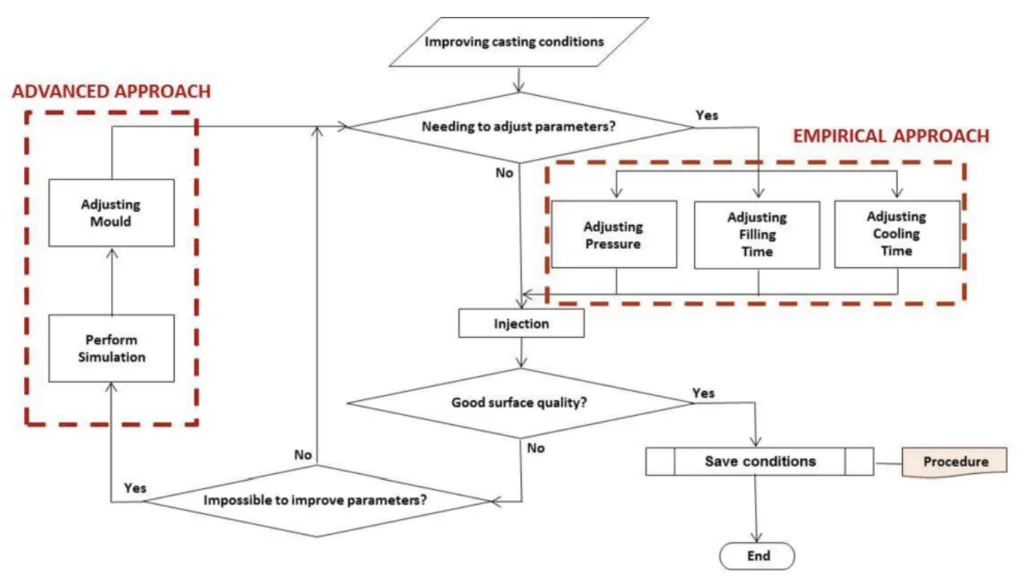
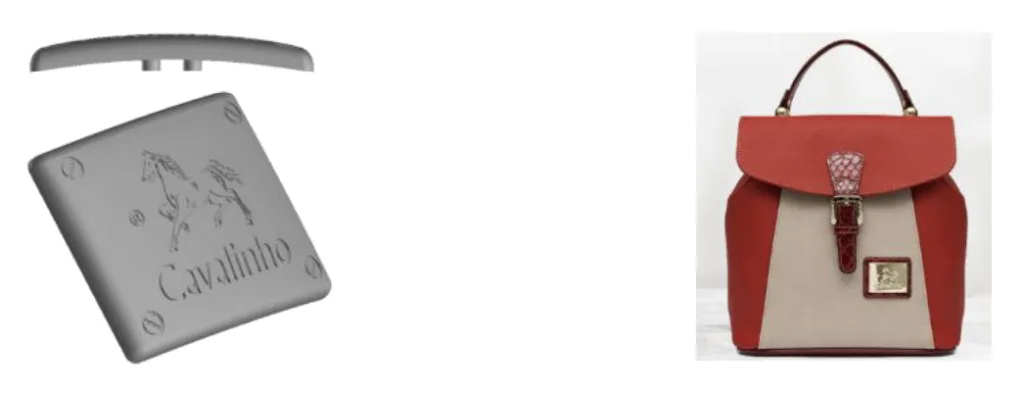
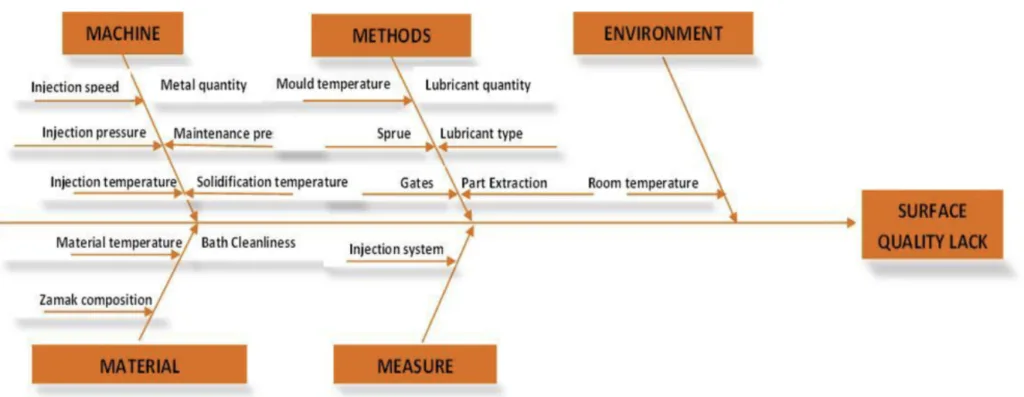
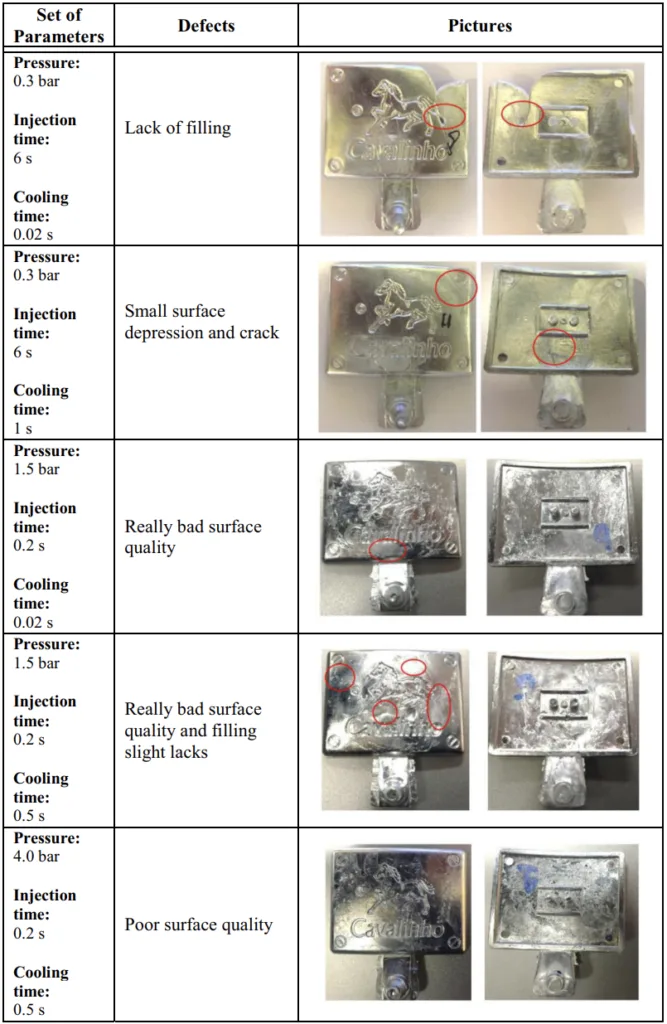
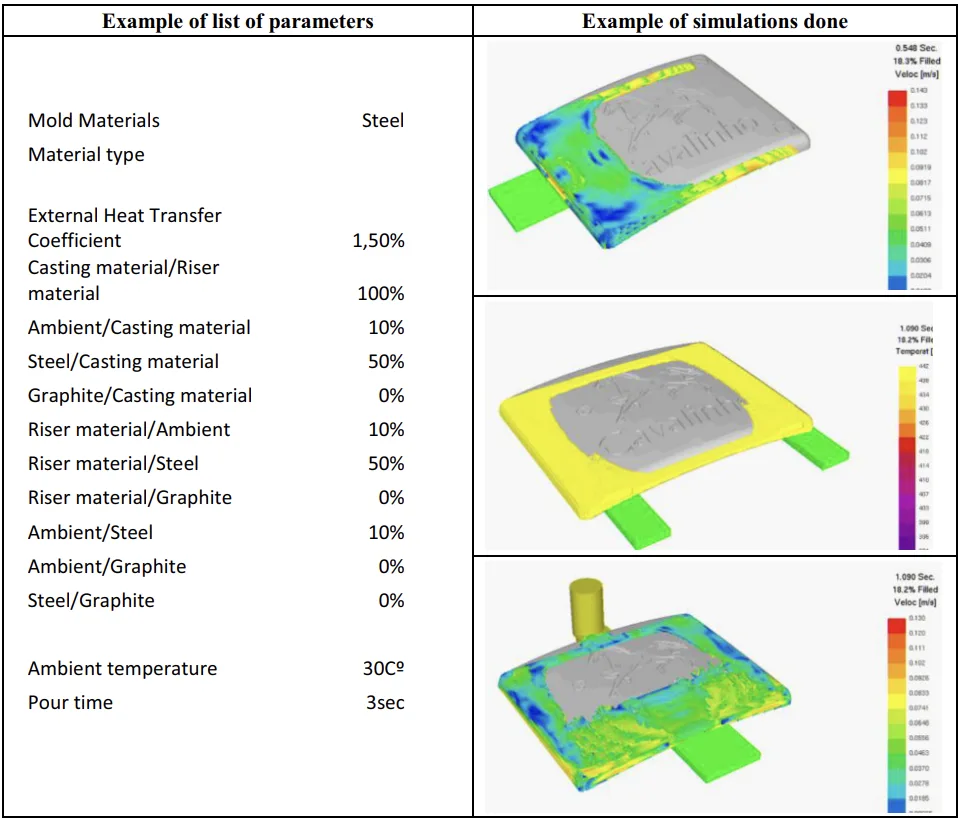
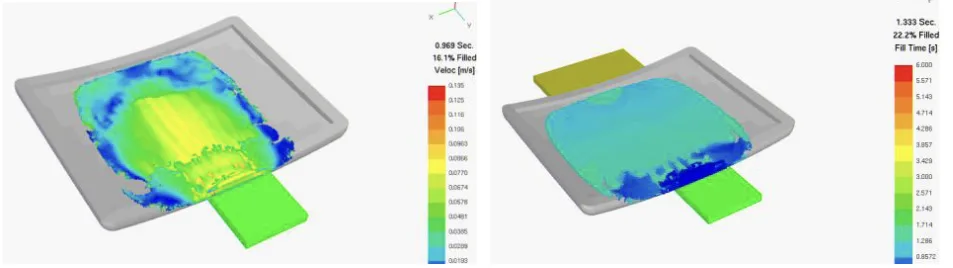
図の名前リスト:
- Figure 1. Flow diagram of the hybrid methodology used in this work.
- Figure 2. (a) Part used as case study in this work. (b) Contextualization of the part in the final product.
- Figure 3. Ishikawa diagram corresponding to problem root-causes analysis.
- Figure 4. Parameters used in the simulations process and some tests carried out with different runner positioning.
- Figure 5. (Right hand) Simulation after the mould has been inverted and using a central runner; (Left hand) Simulation after the mould has been inverted and using a central runner and a posterior riser.
- Figure 6. Parts obtained with the inverse positioning of the mould, central runner and three risers in the other sides of the part. The part is not perfect, but the quality is enough to avoid intermediate steps before coating.
7. 結論:
主な調査結果の要約:
本研究では、美的ザマック部品のHPDCパラメータを最適化するためのハイブリッドアプローチを開発し、検証することに成功しました。確立された主なガイドラインは次のとおりです。
- 材料の定義: 材料の流動性は充填プロセス中の材料分布に直接的な影響を与えるため、適切な材料の選択は非常に重要なステップです。
- 圧力: 特に複雑な部品形状の場合、乱流を最小限に抑えるために低い圧力が推奨されます。
- 充填時間: 部品重量に応じて、短い充填時間が適切です。ケーススタディで使用した約25グラムの部品の場合、約0.5秒しか必要ありません。
- 冷却時間: 部品の凝固には中程度の冷却時間が必要です。
- 金型設計: 曲面部品の場合、中央部分を下に向け、最初の材料の流れを受け取り、金型の上部領域に分配する必要があります。この場合、材料が金型にどのように流れ込むかを説明するためにシミュレーションが絶対に必要です。
- ランナー設計: 中央ランナーは、流れの合流点での乱流と溶接線の定義により、2つ以上のランナーよりも通常は好ましいです。
- ライザー: 乱流の影響を受けやすい部品(面積と厚さの比率が高い部分)では、ライザーの使用を検討する必要があります。
研究の学術的意義:
この研究は、HPDCのような複雑な製造プロセスを最適化するために、経験的試験と高度なシミュレーションを組み合わせたハイブリッド方法論の有効性を示しています。ダイカストにおける問題解決への構造化されたアプローチを提供し、美的部品の品質に対するパラメータの相互作用と金型設計の影響の理解に貢献します。
実際的な意義:
確立されたガイドラインは、ダイカストエンジニアと製造業者が美的ザマック部品のHPDCプロセスを改善するための実用的な洞察を提供します。これらのガイドラインを実装すると、次のことが可能になります。
- 鋳造部品の表面品質の向上。
- ブラストや手動研磨などの中間仕上げ加工の削減または排除。
- 生産における時間とコストの節約。
- HPDC部品で望ましい美的成果を達成する効率の向上。
研究の限界と今後の研究分野:
研究は限界を認め、今後の研究の方向性を示唆しています。
- 材料の流れをさらに最適化し、欠陥を減らすためのさまざまなベント位置の影響の調査。
- 部品表面品質を向上させるための金型キャビティの表面処理の調査。
- 今後の研究では、これらのガイドラインのさまざまな美的部品形状およびザマック合金への適用を検討することができます。
8. 参考文献:
- [1] V. Nunes, F.J.G. Silva, M.F. Andrade, R. Alexandre and A.P.M. Baptista Increasing the lifespan of high-pressure die cast molds subjected to severe wear, Surface and Coatings Technology, Vol. 332, 2017, pp. 319-331.
- [2] J. Santos, R.M. Gouveia and F.J.G. Silva, Designing a new sustainable approach to the change for lightweight materials in structural components used in truck industry, Journal of Cleaner Production, Vol. 64, 2017, pp. 115-123.
- [3] F.J.G. Silva, J. Santos and R. Gouveia Dissolution of Grain Boundary Carbides by the Effect of Solution Annealing Heat Treatment and Aging Treatment on Heat-Resistant Cast Steel HK30, Metals, Vol. 7, 2017, pp. 251-263.
- [4] F. Casarotto, A.J. Franke and R. Franke High-pressure die-cast (HPDC) aluminium alloys for automotive applications, Advanced Materials in Automotive Engineering, Vol. 6, 2012, pp. 109-149.
- [5] B. Zabala, A. Igartua, V. Scarpis, G. Timelli, F. Girot and R. Nevshupa Multiparametric study of Leidenfrost point and wettability of lubricants on high-pressure die-casting dies, International Journal of Thermal Sciences, 125, (2015). 66-73.
- [6] C. Favi, M. Germani and M. Mandolini, Analytical cost estimation model in High Pressure Die Casting, Procedia Manufacturing, Vol. 11, 2017, pp. 526-535.
- [7] W., Z. Yuan, Z. Guo and S. Xiong Characterization of A390 aluminum alloy produced at different slow shot speeds using vacuum assisted high pressure die casting, Transactions of Nonferrous Metals Society of China, Vol. 27(12), 2017, pp. 2529-2538.
- [8] H. Pinto and F. J. G. Silva, Optimisation of die casting process in Zamak alloys, Procedia Manufacturing, Vol. 11, 2017, pp. 517-525.
- [9] X. Li, Z. Guo and S. Xiong Influence of melt flow on the formation of defect band in high pressure die casting of AZ91D magnesium alloy, Materials Characterization, Vol. 129, 2017, 344-352.
- [10] K.Ch. Apparao, A.K Birru, QFD-Taguchi based hybrid approach in die casting process optimization, Transactions of Nonferrous Metals Society of China, Vol. 27(11), 2017, pp. 2345-2356.
- [11] L.X. Kong, F.H. She, W.M. Gao, S. Nahavandi and P.D. Hodgson Integrated optimization system for high pressure die casting processes, Journal of Materials Processing Technology, Vol. 201, 2008, pp. 629-634.
- [12] M.S. Dargusch, G. Dour, N. Schauer, C.M. Dinnis and G. Savage The influence of pressure during solidification of high pressure die cast aluminium telecommunications components, Journal of Materials Processing Technology, 180(1-3), 2006, pp. 37-43.
- [13] R.V. Rao, D.P.Rai, Optimization of Selected Casting Processes Using Jaya algorithm, Materials Today Proceedings, Vol. 4(10), 2017, pp. 11056-11067.
- [14] A. Hamasaiid, G. Dour, T. Loulou and M.S. Dargusch A predictive model for the evolution of the thermal conductance at the casting-die interfaces in high pressure die casting, International Journal of Thermal Sciences, Vol. 49(2), 2010, pp. 365-372.
- [15] S.H. Wu, J.Y.H. Fuh and K.S.Lee Semi-automated parametric design of gating systems for die-casting die, Computers & Industrial Engineering, Vol. 53(2), 2008, pp. 222-232.
- [16] R. Helenius, O. Lohne, L. Arnberg and H.I. Laukli The heat transfer during filling of a high-pressure die-casting shot sleeve, Materials Science and Engineering A, Vol. 413-414, 2005, pp. 52–55.
- [17] M.T. Alonso Rasgado and K. Davey Thermal models for copper-alloyed dies in pressure die casting, Applied Mathematical Modelling, Vol. 33, 2009, pp. 61–80.
- [18] P. Terek, L. Kovačević, A. Miletić, P. Panjan, S. Baloš, B. Škorić and D. Kakaš Effects of die core treatments and surface finishes on the sticking and galling tendency of Al-Si alloy casting during ejection, Wear, Vol. 356-357, 2016, pp. 122-134.
- [19] R.V. Rao, V.D. Kalyankar and G. Waghmare Parameters optimization of selected casting processes using teaching-learningbased optimization algorithm, Appl. Math. Modelling, 2014, doi: http://dx.doi.org/10.1016/j.apm.2014.04.036.
- [20] P.W. Cleary, J. Ha, M. Prakash and T. Nguyen Short shots and industrial case studies: Understanding fluid flow and solidification in high pressure die casting, Applied Mathematical Modelling, Vol. 34, 2010, pp. 2018-2033.
- [21] G.O. Verran, R.P.K. Mendes and L.V.O. DallaValentina DOE applied to optimization of aluminum alloy die castings, Journal of Materials Processing Technology, 200(1-3), 2008, pp. 120-125.
- [22] M.A. Martinez Page and S. Hartmann, Experimental characterization, material modeling, identification and finite element simulation of the thermo-mechanical behavior of a zinc die-casting alloy, Internacional Journal of Plasticity, 2017, doi: 10.1016/j.ijplas.2017.10.010.
- [23] K.-D. Bouzakis, G. Maliaris and A. Tsouknidas FEM supported semi-solid high pressure die casting process optimization based on rheological properties by isothermal compression tests at thixo temperatures extracted, Computational Materials Science, Vol. 59, 2011, pp. 133-139.
- [24] K. Domkin, J.H. Hattel and J. Thorborg Modeling of high temperature- and diffusion-controlled die soldering in aluminum high pressure die casting, Journal of Materials Processing Technology, Vol. 209, 2009, pp. 4051-4061.
- [25] H. Zhao, Y. Bai, X. Ouyang and P. Dong Simulation of mold filling and prediction of gas entrapment on practical high pressure die castings, Transactions of Nonferrous Metals Society of China, Vol. 20, 2010, pp. 2064-2070.
- [26] G.O. Verran, R.P.K. Mendes and M.A. Rossi Influence of injection parameters on defects formation in die casting All2Si1,3Cu alloy: Experimental results and numeric simulation, Journal of Materials Processing Technology, Vol. 179, 2006, pp. 190–195.
- [27] C. Tiana, J. Lawb, J. van der Touwc, M. Murraya, J.-Y. Yaod, D. Grahamd and D. St. John Effect of melt cleanliness on the formation of porosity defects in automotive aluminium high pressure die castings, Journal of Materials Processing Technology, Vol. 122, 2002, pp. 82-93.
- [28] S.G. Lee and A.M. Gokhale Formation of gas induced shrinkage porosity in Mg-alloy high-pressure die-castings, Scripta Materialia, Vol. 55, 2006, pp. 387-390.
9. 著作権:
- この資料は、"F.J.G. SILVA et al."の論文:「Establishing Guidelines to Improve the High-Pressure Die Casting Process of Complex Aesthetics Parts」に基づいています。
- 論文ソース: doi: 10.3233/978-1-61499-898-3-887
この資料は上記の論文を紹介するために作成されたものであり、商業目的での無断使用は禁止されています。
Copyright © 2025 CASTMAN. All rights reserved.