この紹介論文は、「[International Journal of Applied Engineering Research]」によって発行された論文「[Synthesis and Characterization of SiC p Reinforced Magnesium Alloy Based Metal Matrix Composite Through Vacuum Assisted Stir Casting Process]」に基づいています。
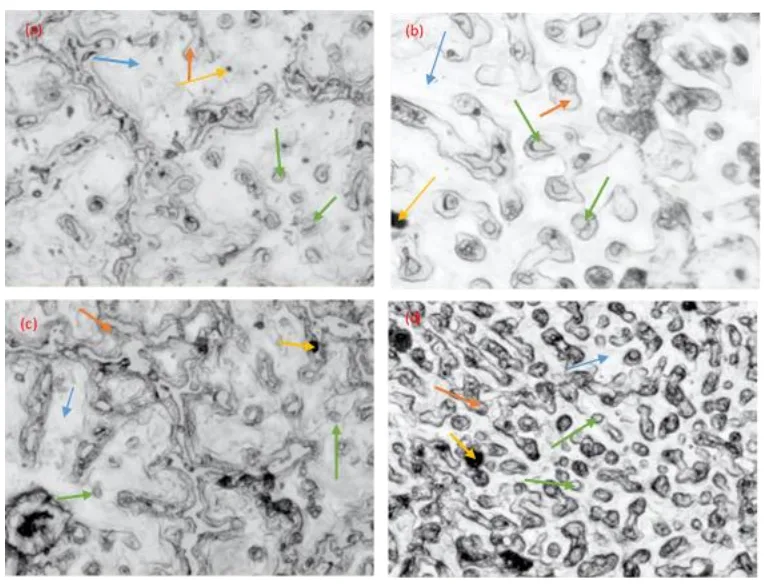
1. 概要:
- 論文名: Synthesis and Characterization of SiC p Reinforced Magnesium Alloy Based Metal Matrix Composite Through Vacuum Assisted Stir Casting Process
- 著者: Anil Kumar, Santosh Kumar and N. K. Mukhopadhyay
- 発行年: 2017
- 発行学術誌/学会: International Journal of Applied Engineering Research (Volume 12, Number 24 (2017) pp. 16087-16093)
- キーワード: Magnesium alloy, composite, particle reinforcement
2. 抄録:
軽量材料の開発は、すべてのエンジニアと科学者にとって挑戦的な課題の一つです。マグネシウムは軽量材料として、純粋な形態では高い腐食性と平均的な機械的特性のために用途が限られています。合金元素は、マグネシウム合金の腐食性および機械的特性を改善する傾向があります。マグネシウム合金の粒子強化金属基複合材料は、マグネシウムの有用性を向上させるための一つの解決策です。本論文では、商業用マグネシウム合金(AZ91)を母材として使用したSiC粒子強化金属基複合材料の特性評価を提示します。不活性雰囲気中での攪拌鋳造法によって調製された複合材料について、光学顕微鏡および走査型電子顕微鏡(SEM)を用いた微細構造観察が行われました。引張強度や硬度などの機械的特性が調査されました。降伏強度、極限強度、引張破面も本研究で評価されました。
3. 緒言:
金属基複合材料(MMC)の生産は、単一材料と比較してより魅力的な特性を提供するため、過去30年間で強化されてきました。自動車、航空宇宙、スポーツ、エレクトロニクス、医療分野など、あらゆる工学分野で軽量材料の需要が高まっています。マグネシウムは有望な軽量材料(すべての構造用金属の中で最も軽い)の一つであり、アルミニウムよりもさらに軽く、現在、工学用途では十分に活用されていません。マグネシウムの密度は1.74 g/cm³であり、鋼鉄より約70%、アルミニウムより35%軽いです。しかし、純粋なマグネシウムは開放雰囲気中での腐食性が高く、機械的特性が劣るため、その直接的な応用は限られています。これらの特性を補うために、マグネシウム合金が構造用途に使用されます。
マグネシウム合金ベースのMMCは、マグネシウム合金の利点(軽量)と強化された機械的特性を提供すると考えられています。SiC、Al2O3、TiC、MgOなどのセラミック粒子のような粒子状強化材をマグネシウム合金に添加すると、室温および高温での剛性と強度を大幅に向上させることができます。MMCの製造には、攪拌鋳造、ガス含浸、粉末冶金、スクイズ鋳造、スプレーデポジション、射出成形、in-situ技術など、さまざまな利用可能な技術が用いられてきました。これらのうち、攪拌鋳造プロセスは、マグネシウム合金ベースのMMCを製造するための最も経済的なプロセスの1つです。本研究は、真空補助攪拌鋳造によって製造されたSiCp強化AZ91マグネシウム合金複合材料の合成と特性評価に焦点を当てています。
4. 研究の概要:
研究トピックの背景:
エネルギー効率の向上や性能改善といった利点から、軽量材料に対する工学的需要は継続的に増大しています。最も軽量な構造用金属であるマグネシウムは、大幅な軽量化の可能性を提供します。しかし、純粋な形態では耐食性が低く機械的特性も劣るため、合金化や複合材料の開発が必要です。炭化ケイ素(SiC)などのセラミック粒子で強化されたマグネシウム基金属基複合材料(MMC)は、低密度を維持しつつ、剛性や強度といった機械的特性を向上させる道筋を提供します。
先行研究の状況:
マグネシウムMMCに関しては広範な研究が行われており、様々な強化材(例:SiC、Al2O3)や製造方法が探求されてきました。一般的な製造技術には、攪拌鋳造、粉末冶金、スクイズ鋳造、スプレーフォーミングなどがあります。攪拌鋳造は、粒子強化MMCの製造において、費用対効果と拡張性に優れていると広く認識されています。これまでの研究では、強化材の種類、サイズ、体積分率、およびプロセスパラメータが、マグネシウム複合材料の微細構造と機械的挙動に及ぼす影響が強調されてきました。
研究の目的:
本研究の主な目的は、真空補助攪拌鋳造プロセスを用いてSiC粒子(SiCp)強化AZ91マグネシウム合金金属基複合材料を合成することでした。この研究は、SiC粒子の重量パーセント(3%、6%、9%、12%)を変えることが、AZ91合金の微細構造および機械的特性(特に引張強度、降伏強度、硬度)に及ぼす影響を系統的に調査し、特性評価することを目的としました。さらに、開発された複合材料の破壊挙動を評価することも目指しました。
核心研究:
本研究の核心は、平均粒子径20ミクロンのSiC粒子を異なる重量パーセント(3、6、9、12 wt%)で強化したAZ91マグネシウム合金母材複合材料の製造を含みます。製造は真空補助攪拌鋳造法を用いて行われました。その後の特性評価には以下が含まれます:
- 光学顕微鏡(OM)およびエネルギー分散型X線分光法(EDS)を備えた走査型電子顕微鏡(SEM)を用いた、未強化AZ91合金およびSiCp強化複合材料の微細構造解析。
- 以下による機械的特性評価:
- 室温での引張試験による降伏強度および極限引張強度の決定。
- ビッカース微小硬度およびマクロ硬度試験による硬度および強化材分布の均一性の評価。
- 複合材料の破壊メカニズムを理解するためのSEMを用いた引張破面の解析。
5. 研究方法論
研究設計:
本研究では、SiCp強化AZ91マグネシウム合金MMCを合成し、その特性を評価するために実験的研究設計を用いました。独立変数はSiC粒子強化材の重量パーセント(0%、3%、6%、9%、12%)であり、従属変数は複合材料の微細構造的特徴と機械的特性でした。
データ収集および分析方法:
- 材料: 母材として市販のマグネシウム合金AZ91Dを使用しました。受領時のAZ91D合金の元素組成は、原著論文のTable 1に詳述されています。強化材として、平均粒子径20ミクロンの炭化ケイ素(SiC)粒子を使用しました。
- 複合材料の製造: 金属基複合材料は、AZ91合金を電気抵抗炉内の金属るつぼで700℃に溶解して製造しました。4種類の異なる重量パーセント(3、6、9、12パーセント)のSiC粒子を、真空補助攪拌鋳造技術を用いて母材に添加しました。溶湯は700℃で20分間保持された後、15分間機械的に攪拌されました。溶融した複合材料は、気孔を最小限に抑えるために不活性雰囲気中で底部注入設備を介して金型に注入されました。
- 微細構造観察: 微細構造観察用の試料は、ダイカスト複合材料から切り出し、機械的研削および研磨を行いました。鏡面研磨された試料は、エチルグリコール、蒸留水、硝酸を75:24:1の割合で混合して調製したエッチング液で5秒間エッチングしました。微細構造は、Leica光学顕微鏡(OM)および表面形状と元素組成分析用のEDSを備えた走査型電子顕微鏡(SEM)を用いて観察しました。
- 機械的試験:
- 引張試験: SiCp強化MMCおよび未強化AZ91合金の機械的特性を評価するために引張試験を実施しました。ASTM E8/E8M規格に従って、ゲージ長20 mm、ゲージ径8 mmの引張試験片を準備しました。試験は、Instron-4208万能試験機を用い、室温、初期ひずみ速度0.005 s⁻¹で実施しました。
- 硬度試験: ビッカース微小硬度試験は、研磨された複合材料の断面にわたり、荷重1.0 kgf、保持時間10秒で実施しました。マクロ硬度試験も、荷重3 kgf、保持時間10秒で複合材料に対して実施しました。これらの試験には、LECO'S LVシリーズ マクロビッカース硬度計を使用しました。
- 破面解析: AZ91/SiC粒子複合材料の引張破面は、SEMによって解析し、破面の形態を調査しました。
研究トピックと範囲:
本研究は、様々なSiC含有量(0 wt%~12 wt%)を持つAZ91/SiCp MMCの合成に焦点を当てました。研究範囲には、結果として得られる微細構造の特性評価が含まれ、特に結晶粒微細化とSiC粒子分布に焦点を当てました。本研究では、降伏強度、極限引張強度、ビッカース硬度(マイクロおよびマクロの両方)などの主要な機械的特性を調査しました。研究範囲の重要な部分は、SiC含有量、観察された微細構造、および結果として得られる機械的特性との関係を分析し、これらの複合材料の引張破壊挙動を調べることでした。
6. 主要な結果:
主要な結果:
- 微細構造:
- 光学顕微鏡観察により、SiC粒子の添加がマグネシウム合金母材の結晶粒径を減少させ、結晶粒微細化を示した(Figure 1)。
- FE SEMマイクログラフは、マグネシウム合金中のSiC粒子の分布がほぼ均一であることを示した(Figure 2)。
- マグネシウム合金複合材料の鋳造微細構造において、顕著なガス介在物や気孔は見られず、健全な鋳物が観察された。
- 降伏強度:
- AZ91合金の降伏強度は119.94 MPaであった。SiC強化材を添加すると、複合材料の降伏強度は初期に減少し(例:3% SiCで57 MPa)、その後、SiCの割合が3%から9%に増加するにつれて複合材料の降伏強度は増加した。AZ91/SiC複合材料の中で最も高い降伏強度は、9% SiC強化複合材料で観察された105.44 MPaであった。12% SiC複合材料は79 MPaの降伏強度を示した(Figure 3)。
- 極限引張強度 (UTS):
- 未強化AZ91合金のUTSは187.67 MPaであることがわかった。
- SiC粒子強化複合材料のUTSは、一般にSiC強化材の割合が増加するにつれて増加した。最も高いUTS値である193.96 MPaは、12% SiCを含む複合材料で記録された(Figure 4)。
- ビッカース硬度:
- 複合材料の平均マイクロビッカース硬度は、SiC粒子強化材の体積分率が増加するにつれて増加した。最も高い平均マイクロビッカース硬度は、12% SiC/AZ91複合材料で107 HVであった(Figure 6)。
- マクロビッカース硬度(3 kgf荷重で測定)も、SiC粒子含有量が増加するにつれて増加した(Figure 7)。
- マクロビッカース硬度値は、同じ複合材料に対してマイクロビッカース硬度値よりも一般的に高く、これは高荷重でより多くの強化粒子が圧痕に抵抗するためである。
- 破壊挙動:
- AZ91/SiC複合材料の引張破面のSEM分析(Figure 8.a - 8.d)は、マグネシウム母材の破壊挙動が脆性破壊と延性破壊の特徴を組み合わせたものであることを示した。
- SiCの割合が増加するにつれて、破面のディンプルサイズは減少した。形態はまた、強化材の体積分率が増加するにつれて、小さなサイズのディンプル、亀裂、収縮気孔、およびへき開破壊が増加することを示し、複合材料がより脆く、延性が低くなることを示唆している。
Figure 2. Scanning Electron Micrograph (a)3% SiC in AZ91(b)6% SiC in AZ91(c)9% SiC in AZ91(d)12% SiC in AZ91
Figure 7. Comparison of average macro -Vickers hardness of composites with AZ91
図のリスト:
- Figure 1. Optical Micrograph (a)3% SiC in AZ91(b)6% SiC in AZ91(c)9% SiC in AZ91(d)12% SiC in AZ91
- Figure 2. Scanning Electron Micrograph (a)3% SiC in AZ91(b)6% SiC in AZ91(c)9% SiC in AZ91(d)12% SiC in AZ91
- Figure 3. Yield Strength of Magnesium Alloy
- Figure 4. Ultimate Tensile strength with different percentage of SiC
- Figure 5. Vickers Hardness Value at different position of the composite (a) 3% SiC in AZ91 (b) 6% SiC in AZ91 (c) 9% SiC in AZ91 (d) 12% SiC in AZ91
- Figure 6. Comparison of average micro -Vickers hardness of composites with AZ91
- Figure 7. Comparison of average macro -Vickers hardness of composites with AZ91
- Figure 8. Tensile facture of the composite (a) 3% SiC in AZ91 (b) 6% SiC in AZ91 (c) 9% SiC in AZ91 (d) 12% in AZ91
(注: Table 1. Elemental Composition of alloy AZ91 は原著論文に記載されており、母材の化学組成を示しています。)
7. 結論:
AZ91/SiC金属基複合材料の実験的分析と特性評価から、以下の結論が得られました。
- 硬質強化材を添加すると、材料(AZ91)の降伏強度は低下するが、SiC粒子状物質の割合が増加するにつれて降伏強度は増加する。AZ91/SiC複合材料の降伏強度の最高値は105.44 M Paである。
- 極限引張強度も強化材の割合の増加とともに増加する。12% SiC強化複合材料の極限引張強度の最高値は193.96 M Paである。
- マイクロビッカース硬度値は複合材料の表面全体で均一ではないが、AZ91金属母材中のSiC粒子状物質の割合が増加するにつれて平均マイクロ硬度値は増加する。12% SiC/AZ91複合材料のマイクロビッカース硬度の最高値は107 HVである。
- マクロビッカース硬度値はマイクロビッカース硬度よりも高い。これは、より高い荷重(すなわち3 kgf)では圧痕面積がより大きく、この場合、より多くの強化粒子が圧痕に抵抗するためである。
- 引張試験片の破面組織写真から、ディンプルが非常に小さく、亀裂やへき開破壊の数が多いため、複合材料はより脆く、延性が低いことが明らかになった。
8. 参考文献:
- [1] J. F. King, “Magnesium: commodity or exotic?,” Mater. Sci. Technol., vol. 23, no. 1, pp. 1–14, 2007.
- [2] W. D. Callister "Materials Science and Engineering: An introduction". New York: Wiley, 2003
- [3] S. Jayalakshmi, S. V. Kailas, and S. Seshan, "Tensile behaviour of squeeze cast AM100 magnesium alloy and its Al2O3 fibre reinforced composites," Compos. Part A Appl. Sci. Manuf., vol. 33, no. 8, pp. 1135-1140, 2002.
- [4] M. Avedesian and H. Baker, “ASM Specialty Handbook:Magnesium and Magnesium Alloys,” ASM International, Materials Park, OH. p. 314, 1999.
- [5] S. F. Hassan and M. Gupta, “Development of high strength magnesium based composites using elemental nickel particulates as reinforcement,” J. Mater. Sci., vol. 37, no. 12, pp. 2467–2474, 2002.
- [6] B. L. Mordike and T. Ebert, "Magnesium Properties - applications - potential," Mater. Sci. Eng. A, vol. 302, no. 1, pp. 37-45, 2001.
- [7] K. Ponappa, S. Aravindan, and P. V. Rao, “Influence of Y2 O 3 particles on mechanical properties of magnesium and magnesium alloy (AZ91D),” J. Compos. Mater., vol. 47, no. 10, pp. 1231-1239, 2013.
- [8] K. Ponappa, S. Aravindan, and P. V. Rao, "Grinding of magnesium /Y 2 O 3 metal matrix composites," Proc. Inst. Mech. Eng. Part B J. Eng. Manuf., vol. 226, no. 10, pp. 1675-1683, 2012.
- [9] L. Lu, K. K. Thong, and M. Gupta, "Mg-based composite reinforced by Mg2Si," Compos. Sci. Technol., vol. 63, no. 5, pp. 627-632, 2003.
- [10] X. Zhang, Q. Zhang, and H. Hu, “Tensile behaviour and microstructure of magnesium AM60-based hybrid composite containing Al2O3 fibres and particles,” Mater. Sci. Eng. A, vol. 607, pp. 269–276, 2014.
- [11] D. Lu, Y. Jiang, and R. Zhou, "Wear performance of nano-Al2O3 particles and CNTs reinforced magnesium matrix composites by friction stir processing,” Wear, vol. 305, no. 1-2, pp. 286-290, 2013.
- [12] M. Paramsothy, X. H. Tan, J. Chan, R. Kwok, and M. Gupta, "Al2O3 nanoparticle addition to concentrated magnesium alloy AZ81: Enhanced ductility,” J. Alloys Compd., vol. 545, pp. 12–18, 2012.
- [13] H. Ferkel and B. L. Mordike, “Magnesium strengthened by SiC nanoparticles," Mater. Sci. Eng. A, vol. 298, no. 1–2, pp. 193–199, 2001.
- [14] M. Gui, J. Han, and P. Li, "Fabrication and Characterization of Cast Magnesium Matrix Composites by Vacuum Stir Casting Process,” J. Mater. Eng. Perform., vol. 12, no. 2, pp. 128–134, 2003.
- [15] H.P. Degischer, P.A. Schulz, W. Lacom, "Properties of continuous fibre reinforced Al and Mg-matrix composites produced by gas pressure infiltration”. Key Eng Mater;127-131:99-110,1996
- [16] K. S. Tun and M. Gupta, “Improving mechanical properties of magnesium using nano-yttria reinforcement and microwave assisted powder metallurgy method,” Compos. Sci. Technol., vol. 67, no. 13, pp. 2657–2664, 2007.
- [17] Y. B. LIU, S. C. LIM, L. LU, and M. O. LAI, “Recent development in the fabrication of metal matrix-particulate composites using powder metallurgy techniques,” J. Materals Sci., vol. 29, pp. 1999–2007, 1994.
- [18] H. Hu, "Squeeze casting of magnesium alloys and their composites". J Mater Sci; 33:1579-89, 1998.
- [19] H. Z. Ye and X. Y. Liu, "Review of recent studies in magnesium matrix composites," J. Mater. Sci., vol. 39, pp. 6153-6171, 2004.
- [20] N. H. Loh, S. B. Tor, and K. A. Khor, “Production of metal matrix composite part by powder injection molding," J. Mater. Process. Technol., vol. 108, no. 3, pp. 398-407, 2001.
- [21] H. Y. Wang, Q. C. Jiang, X. L. Li, and J. G. Wang, “In situ synthesis of TiC/Mg composites in molten magnesium," Scr. Mater., vol. 48, no. 9, pp. 1349-1354, 2003.
- [22] L. H. Dai, Z. Ling, and Y. L. Bai, “Size-dependent inelastic behavior of particle-reinforced metal-matrix composites," Compos. Sci. Technol., vol. 61, no. 8, pp. 1057-1063, 2001.
- [23] T. W. Clyne and P. J. Withers, “An Introduction to Metal Matrix Composites" Cambridge: Cambridge University Press, 1993
- [24] C. S. Goh, J. Wei, L. C. Lee, and M. Gupta, "Development of novel carbon nanotube reinforced magnesium nanocomposites using the powder metallurgy technique,” Nanotechnology, vol. 17, no. 1, pp. 7-12, 2006.
- [25] M. Kouzeli and A. Mortensen, “Size dependent strengthening in particle reinforced aluminium," Acta Mater., vol. 50, no. 1, pp. 39–51, 2002.
- [26] Z. Zhang and D. L. Chen, “Consideration of Orowan strengthening effect in particulate-reinforced metal matrix nanocomposites: A model for predicting their yield strength,” Scr. Mater., vol. 54, no. 7, pp. 1321–1326, 2006.
- [27] R. J. Arsenault and N. Shi, "Dislocation generation due to differences between the coefficients of thermal expansion," Mater. Sci. Eng., vol. 81, no. C, pp. 175-187, 1986.
- [28] V. C. Nardone and K. M. Prewo, "On the strength of discontinuous silicon carbide reinforced aluminum composites," Scr. Metall., vol. 20, no. 1, pp. 43-48, 1986.
- [29] N. Ramakrishnan, "An analytical study on strengthening of particulate reinforced metal matrix composites," Acta Mater., vol. 44, no. 1, pp. 69–77, 1996.
- [30] X. L. Zhong, W. L. E. Wong, and M. Gupta, "Enhancing strength and ductility of magnesium by integrating it with aluminum nanoparticles," Acta Mater., vol. 55, no. 18, pp. 6338-6344, 2007.
- [31] A. Luo, “Processing, microstructure, and mechanical behavior of cast magnesium metal matrix composites," Metall. Mater. Trans. A Phys. Metall. Mater. Sci., vol. 26A, no. 9, pp. 2445–2455, 1995.
- [32] X. J. Wang, K. B. Nie, X. J. Sa, X. S. Hu, K. Wu, and M. Y. Zheng, "Microstructure and mechanical properties of SiCp/MgZnCa composites fabricated by stir casting," Mater. Sci. Eng. A, vol. 534, pp. 60-67, 2012.
9. 著作権:
- この資料は、「Anil Kumar, Santosh Kumar and N. K. Mukhopadhyay」による論文です。「Synthesis and Characterization of SiC p Reinforced Magnesium Alloy Based Metal Matrix Composite Through Vacuum Assisted Stir Casting Process」に基づいています。
- 論文の出典: DOI URL
この資料は上記の論文に基づいて要約されており、商業目的での無断使用は禁止されています。
Copyright © 2025 CASTMAN. All rights reserved.