この記事では、Elsevierによって出版された論文「Efficiency and agility of a liquid CO2 cooling system for molten metal systems」を紹介します。
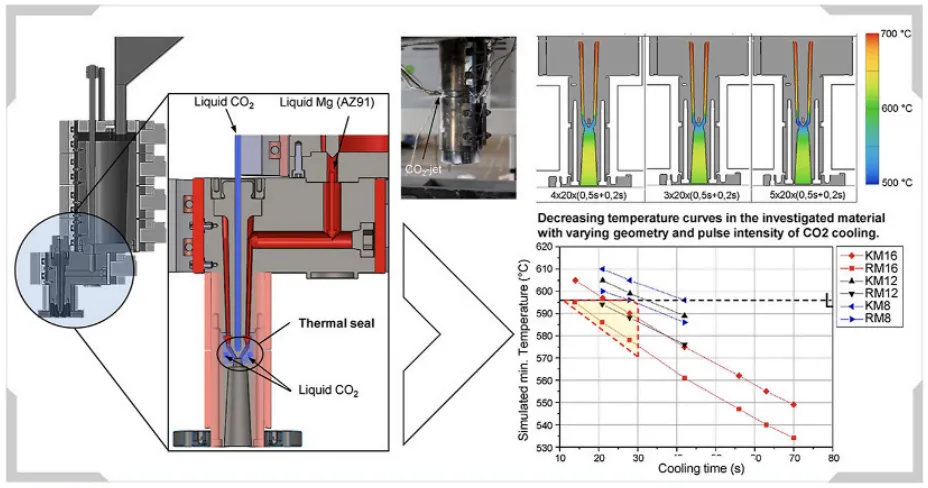
1. 概要:
- タイトル: 液体CO2冷却システムの効率と俊敏性:溶融金属システム (Efficiency and agility of a liquid CO2 cooling system for molten metal systems)
- 著者: J. Glueck, A. Schilling, N. Schwenke, A. Fros, M. Fehlbier
- 出版年: 2021年9月 (September 2021)
- 出版ジャーナル/学会: Case Studies in Thermal Engineering
- キーワード: CO2冷却 (CO2 cooling), マグネシウム (Magnesium), ホットランナー (Hot runner), サーマルシール (Thermal seal), シミュレーション (Simulation), 冷却速度 (Cooling rates)
2. 概要または序論
本研究では、マグネシウムホットランナーチャンネルにサーマルシールを形成するために、キャピラリーチューブによって液体CO2を供給されるエキスパンションボアを使用する液体CO2冷却システムの効率と俊敏性に関する調査をテストリグで実施しました。温度測定を介して、さまざまな冷却パラメータセットの性能をテストし、さまざまなノズル形状に依存する冷却速度を特定しました。測定値を検証するために、テストは熱シミュレーション研究でモデル化されました。液体CO2冷却の適用可能性は、エンジニアリング目的で実証されました。適切なプロセス時間は、アニュラーギャップとして直径16mmを使用しながら達成でき、これは最大4.8°C/秒の冷却速度をもたらします。テストはシミュレーションモデルによって検証されました。シミュレーションは、テストリグの内部プロセスを示しており、冷却プロセスの温度曲線比較は良好な相関関係を示しています。
3. 研究背景:
研究トピックの背景:
マグネシウムのような金属軽量材料を使用した軽量設計の利用が絶えず推進されています。マグネシウム合金は、コスト効率の高いプロセスで加工されれば、アルミニウムや鋼鉄のような構造材料を置き換える大きな可能性を提供します。自動車構造部品の製造では、コールドチャンバーダイカストが重要な技術であり、広く使用されています。しかし、従来のダイカストプロセスでは、大量の内部サイクル材料が生成され、エネルギー集約的な再溶解が必要になります。鋳造ランナーシステムを最小限に抑えることは、リサイクル材料とCO2排出量を削減するために重要です。プラスチック射出成形で既に確立されているホットランナー技術は、溶融金属を鋳造チャンバーからゲートまで液体の状態で導き、マグネシウムダイカスト部品の内部サイクル材料を潜在的に削減する方法を提供します。
既存研究の状況:
ダイカストにおける従来の冷却技術は、熱伝達媒体として水または油を使用し、最大2500 W/m²KのCTEを達成します。脈動熱伝達媒体バリアントは、わずかに高いCTEを提供しますが、サーマルクロージャーシステムの要件に対しては依然として緩慢です。蒸発による二相熱伝達に基づく新しい技術(例えば、水蒸発を利用したニアコンタースプレー冷却)が有望です。CuやAl2O3のようなハイブリッドナノ粒子を含むナノ流体は、熱伝導率をさらに高めることができます。CO2は急速冷却に使用される冷媒として認識されており、ジュール=トムソン効果を利用して集中的な冷却を達成します。しかし、マグネシウムホットランナーシステムでサーマルシールを形成するための液体溶融マグネシウム合金への応用は、まだ探求されていない新しい分野です。
研究の必要性:
液体マグネシウムの反応性により、水性冷媒は不適切です。CO2冷却とジュール=トムソン効果は知られていますが、マグネシウムホットランナーシステムでサーマルシールを形成するための応用は未開拓です。特に内部サイクル材料を削減し、マグネシウム合金のダイカストプロセスを改善する上で、液体CO2冷却の効率と俊敏性を調査する必要があります。本研究は、マグネシウムホットランナーアプリケーション向けの液体CO2冷却システムをテストおよび検証することにより、このギャップに対処することを目的としています。
4. 研究目的と研究課題:
研究目的:
本研究の目的は、ダイカスト用のマグネシウムホットランナーシステムにおいて、サーマルシールを形成するための液体CO2冷却システムの効率と俊敏性を評価することです。本研究は、さまざまな冷却パラメータとノズル形状でのシステム性能をテストし、産業鋳造アプリケーションのエンジニアリング目的への適用可能性を検証することに焦点を当てています。
主要な研究課題:
- エキスパンションボアとキャピラリーチューブを使用して、マグネシウムホットランナーにサーマルシールを作成する液体CO2冷却システムの効率と俊敏性の調査。
- さまざまな冷却パラメータセットの性能テストと、さまざまなノズル形状に基づく冷却速度の特定。
- 熱シミュレーション研究による実験測定値の妥当性検証。
- ダイカストのエンジニアリング目的への液体CO2冷却の適用可能性の実証。
- アニュラーギャップ16mmを使用して達成可能なプロセス時間と、結果として得られる冷却速度の評価。
- シミュレーションと実験の温度曲線を比較して相関関係を評価。
研究仮説:
- 液体CO2冷却は、マグネシウムホットランナーシステムで効果的にサーマルシールを作成できます。
- さまざまな冷却パラメータとノズル形状は、冷却速度とサーマルシール形成の効率に大きな影響を与えます。
- シミュレーションモデルは、テストリグにおけるCO2冷却システムの熱的挙動を正確に予測および検証できます。
- 液体CO2冷却システムは、ダイカストの産業アプリケーションに適したプロセス時間を達成できます。
5. 研究方法
研究デザイン:
本研究では、マグネシウムホットランナーシステムをシミュレーションするように設計されたテストリグを使用する実験的アプローチを採用しています。テストリグは重力駆動式であり、ホットランナー部品の実際の形状に基づいています。温度測定は、さまざまな条件下でのCO2冷却システムの性能を評価するために行われます。実験結果を検証し、テストリグの内部プロセスを分析するために、シミュレーションモデルが開発されています。
データ収集方法:
温度測定は、データロガーと、ノズルのアニュラーギャップおよびピンチップ内の特徴的な位置に配置されたNiCr-Ni熱電対を使用して継続的に記録されます。パルス数、パルス持続時間、パルス間隔などの冷却パラメータの変動を、さまざまなノズル形状(内径8mm、12mm、16mmのコーン)についてテストします。溶融金属温度は640°Cに制御し、AZ91Dマグネシウム合金を使用します。
分析方法:
収集された温度データを分析して、さまざまな冷却パラメータとノズル形状で達成された冷却速度と最低温度を決定します。実験データを熱シミュレーションモデルの結果と比較して、モデルの精度を検証し、シミュレーションされた温度曲線と測定された温度曲線間の相関関係を評価します。また、冷却パラメータ、ノズル形状、冷却速度、サーマルシール形成の関係についても調査します。
研究対象と範囲:
本研究は、AZ91Dマグネシウム合金を使用したマグネシウムホットランナーシステムをシミュレーションするテストリグに焦点を当てています。範囲には、サーマルシール形成と冷却効率に対するさまざまなCO2冷却パラメータとノズル形状の影響の調査が含まれます。本研究は、この特定のテストリグ設定および材料で実施された実験テストとシミュレーションに限定されます。
6. 主要な研究結果:
主要な研究結果:
- マグネシウムホットランナーにおけるサーマルシールへの液体CO2冷却の適用可能性が実証されました。
- 最大4.8°C/秒の冷却速度で、アニュラーギャップ直径16mmを使用して適切なプロセス時間が達成されました。
- テストはシミュレーションモデルによって検証され、温度曲線間に良好な相関関係が示されました。
- 最低温度は、ノズル直径とほぼ線形の相関関係を示しました。
- 直径16mmのノズルは、より小さい直径と比較して、より高い熱的俊敏性を示しました。
- 冷却速度は、すべての直径で冷却時間の増加とともに指数関数的に減少しました。
- シミュレーション結果は実験データとよく一致し、モデルとアプローチを検証しました。
提示されたデータの分析:
- 冷却速度: 図10は、すべてのノズル直径(8mm、12mm、16mm)について、冷却時間の増加に伴い冷却速度が指数関数的に減少する傾向を示しています。16mmノズルが最高の冷却速度を達成しました。
- 最低温度: 図9は、最低温度がノズル直径とほぼ線形に相関していることを示しています。16mmノズルは、冷却時間の増加に伴い最低温度が線形に減少する傾向を示しました。
- 温度分布: 図8は、CO2の局所的に制限された冷却効果を示しており、熱冷却能力は冷却穴からの距離が遠くなるにつれて指数関数的に減少します。
- シミュレーション検証: 図11は、平均実験温度曲線とシミュレーション曲線の適合性を示しており、特に測定位置1と2で適合しています。位置3と4ではオフセットが観察されましたが、これは熱伝達係数のわずかな偏差に起因すると考えられます。図13は、溶融金属チャネルとアニュラーギャップの中心でシミュレーションされた最低温度を示しており、温度勾配を示し、テストの観察結果を確認しています。
図のリスト:
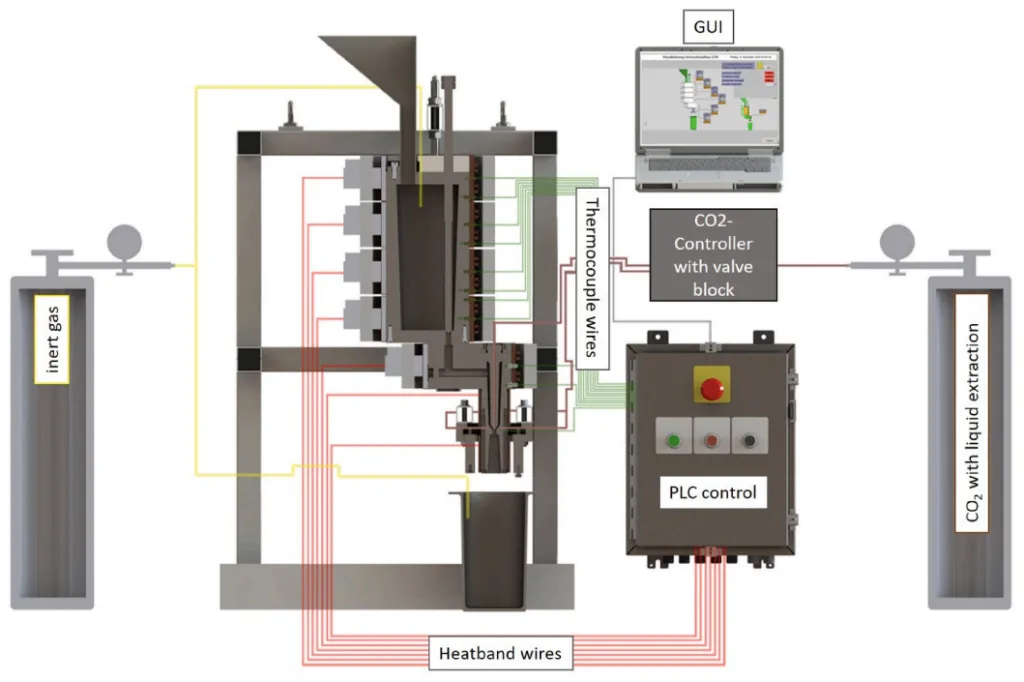
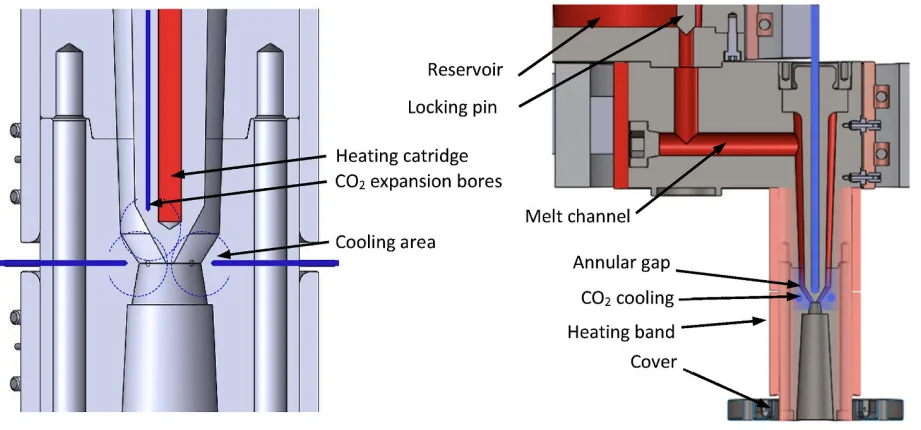
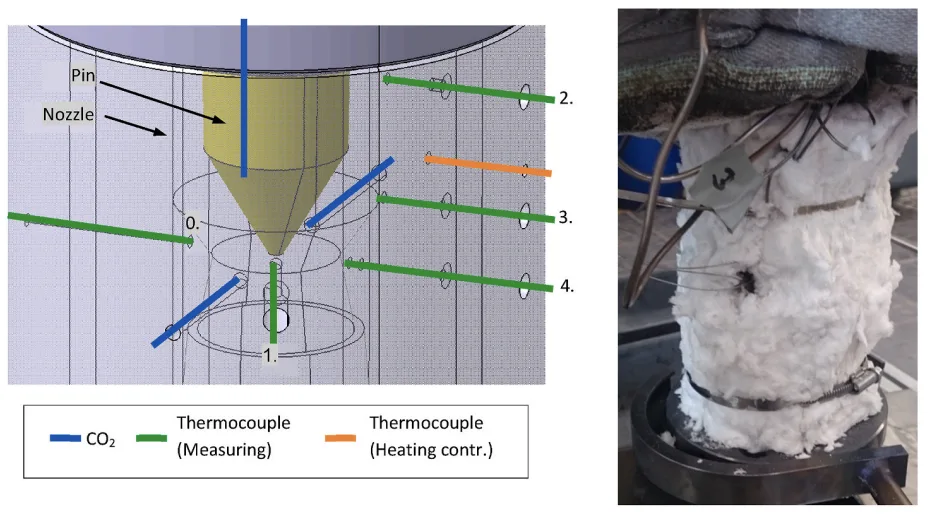
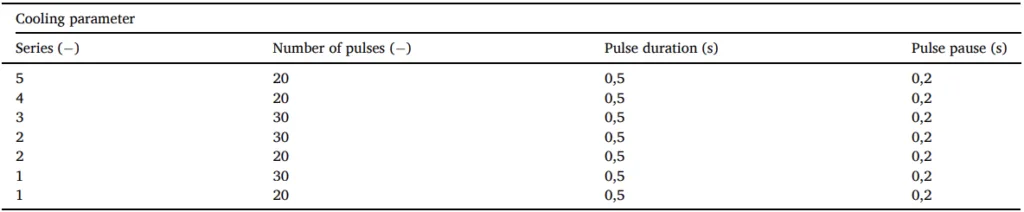
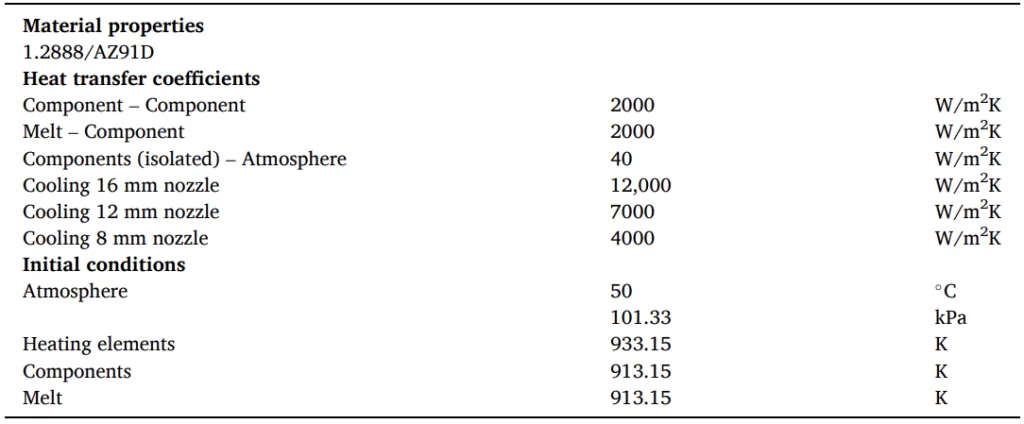
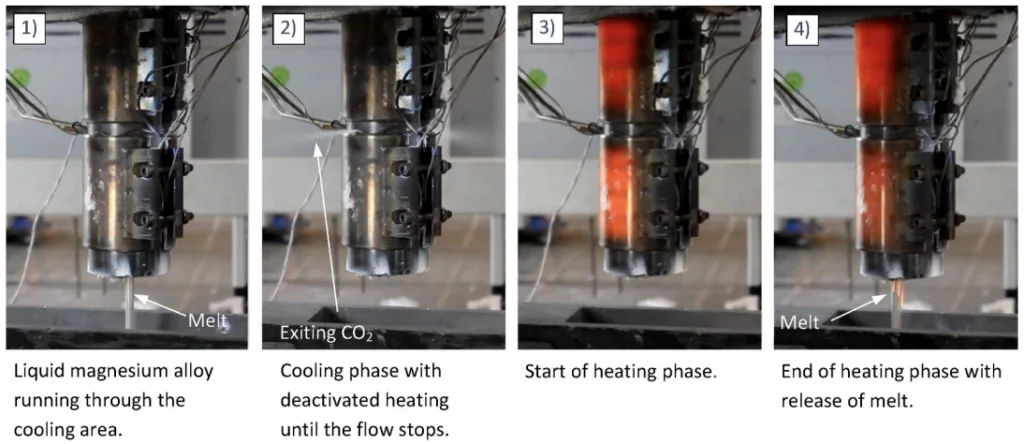
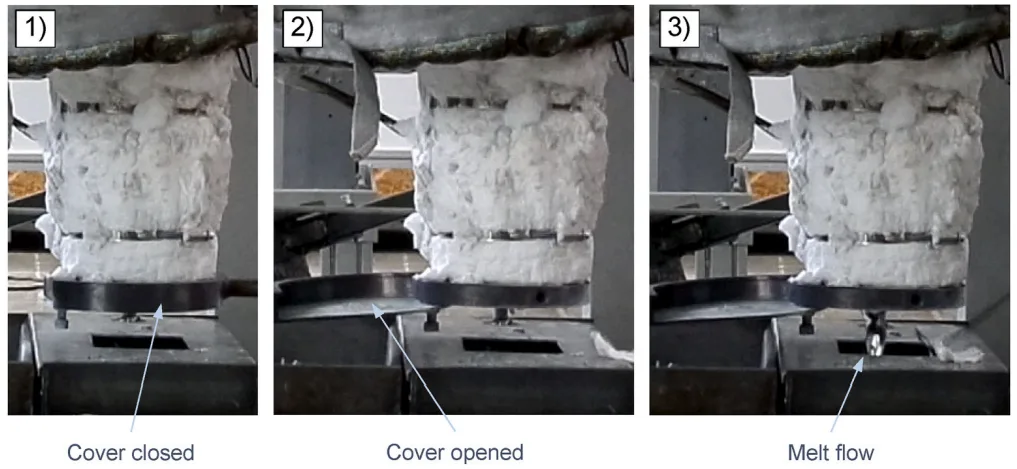
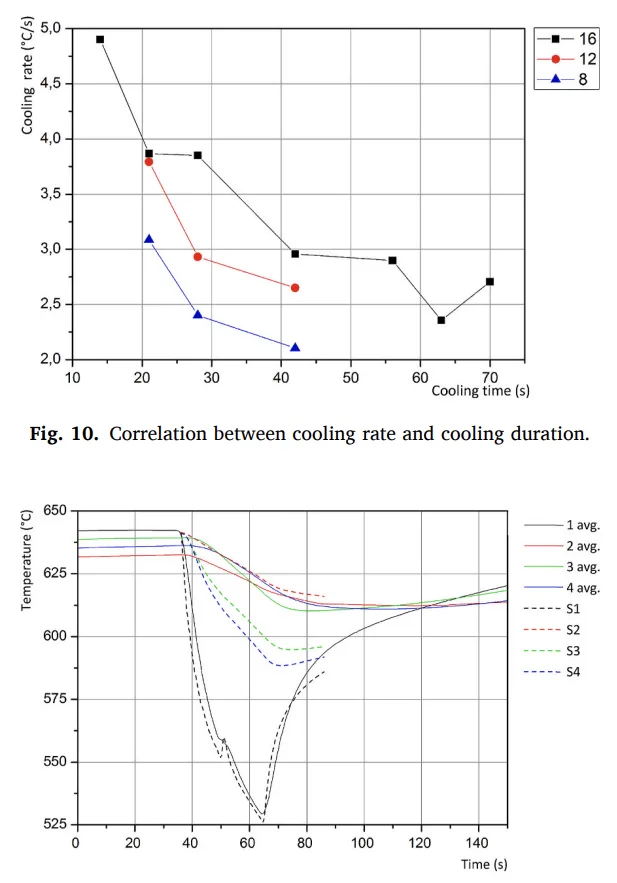
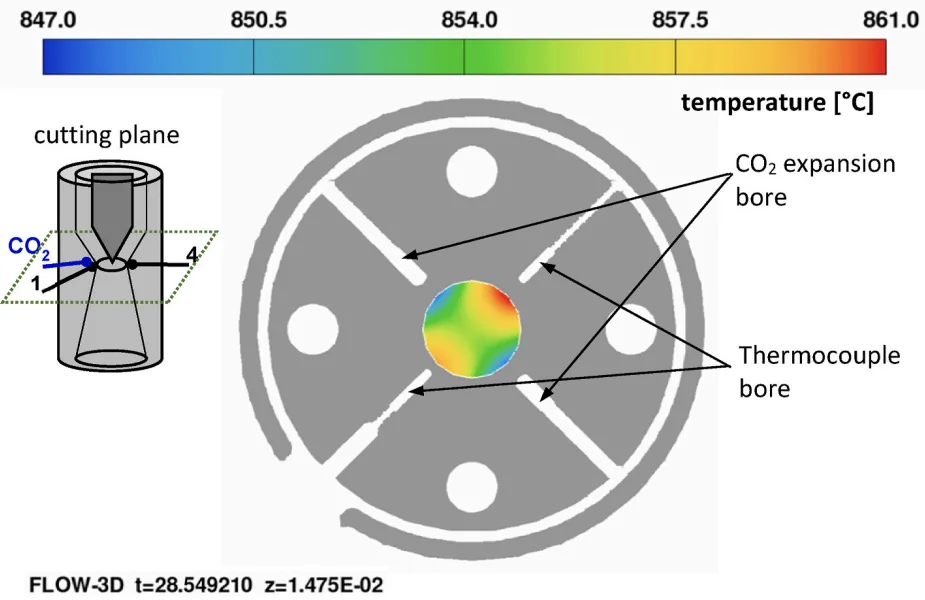
- Fig. 1. 供給および制御装置を備えたテストリグ構造の断面図。
- Fig. 2. ピンに加熱カートリッジを備えたノズルのアニュラーギャップ構造の断面図と、CO2冷却位置(左)およびリザーバーとノズル領域間の接続としての溶融金属チャネルの内部構造(右)の表現。
- Fig. 3. 加熱制御(オレンジ)、測定(緑)、CO2冷却の供給(青)用に色分けされた熱電対を備えたピンチップ周辺の測定範囲のCAD表現。ホットランナーの中央のピンは黄色で示されています。ピン周辺のアニュラーギャップは円錐形です(左)。セラミック断熱材とカバーを備えたテストリグに取り付けられた状態のノズルの表現(右)。(この図の凡例の色参照の解釈については、記事のWebバージョンを参照してください。)
- Fig. 4. シミュレーションされた熱電対の位置を備えたシミュレーションモデルのノズル構造。
- Fig. 5. 冷却テストの初期手順。
- Fig. 6. 時間の特性点における定義されたパラメータに従ったテストのシーケンス表現。
- Fig. 7. ノズル温度の特性曲線[測定点0、パラメータ5x20x(0.5秒+ 0.2秒)]。
- Fig. 8. CO2冷却からの時間と距離に対する測定点1、2、3における温度曲線の補間[パラメータ2x30x(0.5秒+ 0.2秒)]。
- Fig. 9. 冷却段階における最低温度と平均加熱時間。
- Fig. 10. 冷却速度と冷却時間の相関関係。
- Fig. 11. 測定位置1〜4の平均温度曲線と、ノズル直径16mmのパラメータ2x20x(0.5秒+ 0.2秒)のシミュレーションされた温度曲線。
- Fig. 12. 溶融金属中の色スケール温度を備えたノズルの断面図。(この図の凡例の色参照の解釈については、記事のWebバージョンを参照してください。)
- Fig. 13. すべてのノズル直径に対する溶融金属チャネルの中心とアニュラーギャップの中心における最低温度のシミュレーション。
7. 結論:
主要な調査結果の要約:
本研究では、マグネシウムホットランナーシステムでサーマルシールを作成するための液体CO2冷却システムの効率と俊敏性を実証することに成功しました。直径16mmのノズルが最高の性能を示し、最大4.8°C/秒の冷却速度と適切なプロセス時間を達成しました。シミュレーションモデルは実験結果を検証し、良好な相関関係を示し、局所的なサーマルクロージャーを必要とするホットランナーアプリケーションに対する直径16mmのノズルの適合性を確認しました。また、本研究では、冷却効率とサーマルシール形成に対するノズル形状と冷却パラメータの影響を強調しました。
研究の学術的意義:
本研究は、ダイカスト、特にマグネシウム合金およびホットランナーシステムにおける液体CO2冷却の基本的な理解に貢献します。CO2冷却プロセスを分析および最適化するための貴重な実験データと検証済みのシミュレーションモデルを提供します。本研究は、ダイカストにおける熱管理の知識を進歩させ、冷却パラメータ、ノズル形状、冷却性能の関係に関する洞察を提供します。
実用的な意味合い:
本研究の結果は、ダイカスト産業、特にマグネシウム部品製造にとって重要な実際的な意味合いを持っています。実証された液体CO2冷却の適用可能性は、コールドチャンバーダイカストにおいて内部サイクル材料を削減し、プロセス効率を向上させるための有望な技術を提供します。最適化されたCO2冷却パラメータを備えた直径16mmのノズルを使用すると、サイクル時間を短縮し、材料の無駄を削減できます。この技術は、高品質のマグネシウムダイカストの生産を向上させるために産業環境で実装できます。
研究の限界と今後の研究分野:
本研究は、特定のテストリグ設定とAZ91Dマグネシウム合金に限定されています。他のマグネシウム合金や、より複雑な産業用ダイカスト金型におけるCO2冷却システムの性能を調査するには、さらなる研究が必要です。産業環境におけるCO2冷却システムの長期的な動作安定性と堅牢性も評価する必要があります。今後の研究では、冷却効率を最大化し、CO2消費を最小限に抑えるために、冷却パラメータ、ノズル設計、および制御戦略のさらなる最適化を検討できます。脈動CO2冷却とさまざまなキャピラリーチューブ構成の効果を調査することも有益です。
8. 参考文献:
- [1] C. Herrmann, H. Pries, G. Hartmann, Energie- und ressourceneffiziente Produktion von Aluminiumdruckguss, Springer Vieweg, Heidelberg, 2013, ISBN 978-3-642-39852-0.
- [2] V. Goryany, P.J. Mauk, O. Myronova, Magnesium als Leichtbauwerkstoff - Eigenschaften, Anwendungen, Entwicklungspotential, Giesserei-Rundschau 53 (2006) 9-10.
- [3] A. Lohmüller, M. Scharrer, C. Rauber, et al., Neue Entwicklungen beim Thixospritzgießen von Magnesium, Neue Materialien Fürth GmbH, Fürth, 2007.
- [4] D.V. Rosato, M.G. Rosato. Injection Molding Handbook 3, Springer Science & Business Media, 2012.
- [5] R. Spina, Injection moulding of automotive components: comparison between hot runner systems for a case study, J. Mater. Process. Technol. 155-156 (2004) 1497-1504, https://doi.org/10.1016/j.jmatprotec.2004.04.359.
- [6] A. Demirer, Y. Soydan, A.O. Kapti, An experimental investigation of the effects of hot runner system on injection moulding process in comparison with conventional runner system, Materials and Design 28 (5) (2007) 1467-1476, https://doi.org/10.1016/j.matdes.2006.03.015.
- [7] J. Glück, A. Schilling, M. Fehlbier, J. Röse, A. Gebauer-Teichmann. Düse für Metall-Druckgussanwendungen, DE102015224410B4, 2020, DPMA German Patent.
- [8] J. Glück; A. Schilling; M. Fehlbier; J. Röse; A. Gebauer-Teichmann. Rückschlagventil. 2019, 1-11. DE102015224411B4.
- [9] J. Glück; A. Schilling; M. Fehlbier; J. Röse; A. Gebauer-Teichmann; Gusseinrichtung; DPMA German Patent. 2017, 1-19. DE102015224414A1.
- [10] L. Reiche, Entwicklung einer geregelten und energieeffizienten Werkzeugtemperierung im Dauerformguss unter Einsatz einer Sprühkühlung mit Wärmerückgewinnung, Dissertation, Universität Kassel, Kassel, 2019, https://doi.org/10.17170/kobra-202007281500.
- [11] W. Kotzab, Methoden der Impulstemperierung, in: In: Kunststoffe, Hanser Verlag, München, 2006, 8/2006.
- [12] W. Steinko, C. Bader, Optimierung von Spritzgießprozessen, Hanser, München, 2008, ISBN 978-3-446-40977-4.
- [13] N. Abbas, S. Nadeem, A. Saleem, Computational analysis of water based Cu - Al2O3/H2O flow over a vertical wedge, Adv. Mech. Eng. 12 (11) (2020) 1-10, https://doi.org/10.1177/1687814020968322.
- [14] S. Nadeem, N. Abbas, A.U. Khan, Characteristics of three dimensional stagnation point flow of Hybrid nanofluid past a circular cylinder, Results in physics 8 (2018) 829-835, https://doi.org/10.1016/j.rinp.2018.01.024.
- [15] X.C. Liu, Y.F. Sun, H. Fujii, Clarification of microstructure evolution of aluminum during friction stir welding using liquid CO2 rapid cooling, Mater. Des. 129 (2017) 151-163, https://doi.org/10.1016/j.matdes.2017.05.013.
- [16] Nan Xu, Rintaro Ueji, Yoshiaki Morisada, Hidetoshi Fujii, Modification of mechanical properties of friction stir welded Cu joint by additional liquid CO2 cooling, Mater. Des. 6 (2014) 20-25, https://doi.org/10.1016/j.matdes.2013.10.076 (1980-2015).
- [17] N. Hanenkamp, S. Amon, D. Gross, Hybrid supply system for conventional and CO2/MQL-based cryogenic cooling, Procedia CIRP 77 (2018) 219-222, https://doi.org/10.1016/j.procir.2018.08.293.
- [18] Huihong Liu, Kohsaku Ushioda, Hidetoshi Fujii, Elucidation of microstructural evolution of beta-type titanium alloy joint during friction stir welding using liquid CO2 cooling, Mater. Char. 145 (2018) 490-500, https://doi.org/10.1016/j.matchar.2018.09.005.
- [19] Zaman Ziabakhsh-Ganji, Henk Kooi, Sensitivity of Joule-Thomson cooling to impure CO2 injection in depleted gas reservoirs, Appl. Energy 113 (2014) 434-451, https://doi.org/10.1016/j.apenergy.2013.07.059. ISSN 0306-2619.
- [20] C.M. Oldenburg, Joule-Thomson cooling due to CO2 injection into natural gas reservoirs, Energy Convers. Manag. 48 (6) (2007) 1808-1815, https://doi.org/10.1016/j.enconman.2007.01.010. ISSN 0196-8904.
- [21] G. Walker, Joule-thomson cooling systems, in: Cryocoolers. The International Cryogenics Monograph Series, Springer, Boston, MA, 1983, https://doi.org/10.1007/978-1-4899-5286-8_6.
- [22] K.-P. Tucan, R. Gschwandtner, P. Hofer, G. Schindelbacher, P. Schumacher, Vergleich der Wirkung von lokalen Temperiermaßnahmen in Druckgießformen, Giesserei-Rundschau 59 (2012) 211-216, 7/8.
9. 著作権:
- この資料は、"J. Glueck et al."の論文:「Efficiency and agility of a liquid CO2 cooling system for molten metal systems」に基づいています。
- 論文ソース: https://doi.org/10.1016/j.csite.2021.101485
この資料は上記論文を紹介するために作成されたものであり、商業目的での無断利用は禁止されています。
Copyright © 2025 CASTMAN. All rights reserved.