このページは、2018年にInternational Journal of Metalcastingに掲載された研究論文「モジュラー設計アプローチを用いた軽量ダイカスト金型の初期研究(AN INITIAL STUDY OF A LIGHTWEIGHT DIE CASTING DIE USING A MODULAR DESIGN APPROACH)」を要約したものです。本研究は、エネルギー消費を削減し、高圧ダイカスト(HPDC)プロセスの効率を向上させるためのモジュラー軽量ダイカスト金型設計の可能性を調査しています。
1. 概要:
- タイトル: AN INITIAL STUDY OF A LIGHTWEIGHT DIE CASTING DIE USING A MODULAR DESIGN APPROACH (モジュラー設計アプローチを用いた軽量ダイカスト金型の初期研究)
- 著者: Sebastian Müller, Klaus Dilger, Anke Müller, Felix Rothe, Klaus Dröder
- 発表年: 2018年
- 発表ジャーナル/学会: International Journal of Metalcasting, Volume 12, Issue 4
- キーワード: ダイカスト, プロセスモデリング, 金型たわみ, 軽量設計, モジュラーコンセプト, エネルギー削減 (die casting, process modeling, die deflections, lightweight design, modular concept, energy reduction)
2. 研究背景:
- 研究テーマの社会的/学術的背景:
高圧ダイカスト(HPDC)は、特にドイツの生産量の約70%を占める自動車産業において重要な産業プロセスです。HPDCは、幾何学的に複雑な部品を大量生産するのに適しています。しかし、従来のHPDC金型設計および製造は、いくつかの重大な欠点を抱えています。ダイカスト金型は通常、各部品ごとにカスタム設計および切削加工によって製造され、標準化が不足しています。設計の改善は、設計者の経験と数値解析手法によって漸進的に進められてきました。従来のアプローチは、鋳造プロセス中の高い安定性を確保するために、金型を大型に設計することを特徴としています。 - 既存研究の限界:
現在のダイカスト金型技術は、いくつかの限界に直面しています。- 高い投資コスト: プロセスを大量生産に限定する要因となります。
- 高いエネルギー消費: 大型金型の運転は、多大なエネルギー消費と遅い金型温度制御につながります。
- 高い総重量: 堅牢で重量のあるダイカストマシンと駆動ユニットが必要です。
- エネルギー集約的な生産: 焼入れおよび焼き戻しされた工具鋼は、高いCO₂排出量を引き起こします。
- 材料の無駄: ダイカスト金型、特にモールドベースは、使用後に廃棄されることが多く、材料の無駄に繋がります。
- 時間と材料集約的な加工: 工具鋼から成形フレームを製造することは、時間とコストのかかるプロセスです。
- 研究の必要性:
本研究は、従来のダイカスト金型設計および製造の限界を克服する必要性によって動機付けられました。以下の点を改善する必要性が明確に存在します。- 設計および製造プロセスの簡素化: ダイカスト金型の製作に関連する時間とコストを削減します。
- 製品バリエーションの迅速な実装: 個別化された製品に対する需要の高まりに対応するために、鋳造生産の柔軟性を高めます。
- エネルギー効率の向上: 金型の予熱および運転中のエネルギー消費を削減します。
- 材料消費の削減: 軽量設計を探求して、材料の使用量と廃棄物を最小限に抑えます。
3. 研究目的と研究課題:
- 研究目的:
主な研究目的は、モジュラー設計アプローチを用いた軽量ダイカスト金型の初期研究を実施することです。これには、この新しい金型設計の基本的な熱的および構造的特性を分析して、その実現可能性と潜在的な利点を評価することが含まれます。最終的な目標は、設計および製造の時間とコストを削減する、より効率的で柔軟なダイカスト金型設計原理への道を開くことです。 - 主要な研究課題:
本研究は、以下の主要な課題に対する回答を求めます。- モジュラー軽量ダイカスト金型のエネルギー消費量は、予熱および運転中に従来のダイカスト金型と比較してどのようですか?
- 鋳造プロセス中のモジュラー軽量ダイカスト金型の変形および応力特性は何ですか?また、従来の金型とどのように比較されますか?
- モジュラー軽量設計は、一般的なHPDCプロセス荷重下で十分な構造的完全性と寸法精度を維持できますか?
- エネルギー効率と構造性能の観点から、モジュラー軽量ダイカスト金型設計を実装する際の潜在的な利点と課題は何ですか?
- 研究仮説:
軽量構造とモジュール性の設計原理に基づいて、本研究は以下の仮説の下で進められます。- モジュラー軽量ダイカスト金型は、質量と材料の削減により、従来の金型と比較して予熱および運転中のエネルギー消費が著しく低くなるでしょう。
- 軽量設計において剛性と材料が減少するため、鋳造プロセス中の金型の計算された変形と応力は、従来の金型と比較してかなり高くなるでしょう。
- 潜在的に高い変形と応力にもかかわらず、モジュラー軽量ダイカスト金型は、HPDCプロセスに許容可能なレベルの寸法精度と構造的完全性を維持するように設計できるでしょう。
4. 研究方法論:
- 研究デザイン:
本研究では、有限要素解析(FEA)を用いて、軽量モジュラーダイカスト金型コンセプトの性能を従来のダイカスト金型と比較評価する比較研究デザインを採用しています。両方の金型設計は、同じ4mm厚の板状HPDC部品に対してモデル化され、熱的および構造的挙動を直接比較できるようにしました。 - データ収集方法:
データは、ANSYSソフトウェアを使用して実行された数値シミュレーションを通じて収集されました。シミュレーションモデルは、以下を使用して構築されました。- CADデータ: 軽量モジュラーダイカスト金型と従来のダイカスト金型の両方のCADモデルを作成しました。BUEHLER SC B53ダイカストマシンの固定および可動プラテンのCADデータは、製造元から提供されました。
- 境界条件: 熱解析と機械解析の両方の境界条件は、実際の生産プロセスパラメータと関連文献に基づいて慎重に定義されました。これらの条件は、論文の表1と表2に詳細に記載されています。
- 分析方法:
有限要素法を用いて、連成過渡熱および構造解析を実施しました。このアプローチにより、熱伝達と構造力学の同時シミュレーションが可能になり、鋳造プロセス中の熱負荷と機械的応力間の相互作用を捉えることができます。分析には以下が含まれていました。- 熱解析: 過渡熱シミュレーションを実行して、金型温度変化、冷却チャネルの熱出力、および予熱および鋳造サイクル中のエネルギー消費を分析しました。
- 構造解析: 静的構造シミュレーションを実施して、機械的負荷(締結力、射出圧力)および熱負荷を含むさまざまな負荷条件下での金型たわみ、壁厚偏差、および等価フォンミーゼス応力を評価しました。
- 研究対象と範囲:
本研究は、特定のHPDC部品である厚さ4mmの板状部品に焦点を当てました。この形状を選択した理由は次のとおりです。- 変形解析が容易です。
- 性能を実際のダイカスト金型と比較できます。
- キャビティが可動金型半分にのみ配置されているため、設計と解析が簡素化されます。
- 荷重が金型の中央に集中しているため、重要なアプリケーションを表しています。
5. 主な研究結果:
- 主な研究結果:
有限要素計算により、いくつかの重要な知見が明らかになりました。- エネルギー削減: モジュラー軽量ダイカスト金型は、従来の金型と比較して、予熱および運転中のエネルギー消費量が大幅に少なくなりました。総エネルギー需要は、鋳造ロットサイズに関係なく、約5.2倍減少しました(図5)。平均キャビティ温度200℃まで予熱するのに、軽量金型は4.2 MJの熱を必要とし、従来の金型は17.3 MJの熱を必要としました(図3)。
- 変形: 室温で荷重をかけた場合、軽量金型の計算された変形は従来の金型よりも大きくなりました(図6)。ただし、最大壁厚偏差の差は約0.05mmと比較的わずかでした。運転温度では、両方の設計コンセプト間の偏差は、プレートの中央で約0.05mmのままでした(図7)。興味深いことに、熱的および機械的負荷(設定#III)を組み合わせた条件下では、軽量設計は従来の設計と比較して壁厚偏差がより小さくなりました(図8)。
- 応力: 等価フォンミーゼス応力解析の結果、軽量荷重支持金属構造要素のノッチ、特に周辺領域の半径部分で高い応力集中が示されました(図10b)。最適化された3Dトラスで構成された空間フレームでも、局所的に高い応力が観察されました(図11)。
- 時間-温度曲線: 予熱および鋳造サイクル中の両方の金型設計の時間-温度曲線は類似していました(図3および図4)。従来の金型は、軽量金型(1558秒)と比較して、わずかに速い加熱時間(200℃到達時間965秒)を示しました。これは、質量が小さいにもかかわらず、軽量金型の冷却チャネル表面積がより小さいためであると分析されました。
- 統計的/定性的分析結果:
- 定量的なエネルギー節約: シミュレーションは、軽量モジュラー設計の大きなエネルギー節約の可能性を定量的に実証し、さまざまな鋳造ロットサイズにわたって総エネルギー需要で約5.2倍の一貫した削減率を示しました。
- 定性的な変形挙動: 変形パターンの定性分析の結果、軽量金型は室温での機械的負荷下でより大きな変形を示しましたが、運転温度では挙動が変化しました。結合された熱的および機械的負荷下では、軽量設計は従来の金型と比較して壁厚偏差が減少しました。
- 応力分布: 応力解析は、軽量設計において応力集中が激しい領域、特に荷重支持構造のノッチおよび半径部分と空間フレーム内で定性的に特定しました。
- データ解釈:
- エネルギー効率: 結果は、モジュラー軽量ダイカスト金型がHPDCプロセスでエネルギー消費を大幅に削減できるという仮説を強く支持しています。この削減は、主に軽量設計の質量が小さく、加熱に必要なエネルギーが少ないことに起因します。
- 構造性能: 軽量金型は特定のシナリオでより高い変形と応力を示しましたが、全体的な変形は比較的小さく、従来の金型と同等のレベルにとどまりました。現実的な鋳造条件(設定#III)では、軽量設計は変形性能が向上していることさえ示しました。応力解析は、慎重な材料選択と構造最適化が必要な領域を強調しました。
- モジュラー設計の実現可能性: 初期シミュレーション結果は、モジュラー軽量設計コンセプトが実現可能であり、ダイカスト金型の効率と柔軟性を向上させる可能性を秘めていることを示唆しています。
- 図のリスト:
- 図 1. 軽量設計金型の断面図(a)とアイソメトリック図(b)。
- 図 2. 有限要素モデルの境界条件の図解。(a)従来のダイカスト金型、(b)軽量設計ダイカスト金型。注釈1〜8については表1を参照。
- 図 3. 軽量および従来のダイカスト金型の予熱中の冷却チャネルの計算された過渡熱出力と平均キャビティ温度。
- 図 4. 20回の鋳造サイクル後の計算された過渡熱出力と平均キャビティ温度。
- 図 5. 3つの異なる鋳造ロットサイズに対する総エネルギー需要。
- 図 6. 境界条件Iに従った壁厚偏差のグラフ表示(表3を参照)。
- 図 7. 境界条件IIに従った壁厚偏差のグラフ表示(表3を参照)。
- 図 8. 境界条件IIに従った壁厚偏差のグラフ表示(表3を参照)。
- 図 9. 従来のダイカスト金型と軽量ダイカスト金型を備えた高圧ダイカストマシンの機能ユニットのy方向の計算された変位。#Ill、表3に従った境界条件。40倍の倍率。
- 図 10. 軽量設計金型の断面における等価応力のグラフによる可視化。
- 図 11. 軽量設計金型の空間フレームにおける等価応力のグラフによる可視化。
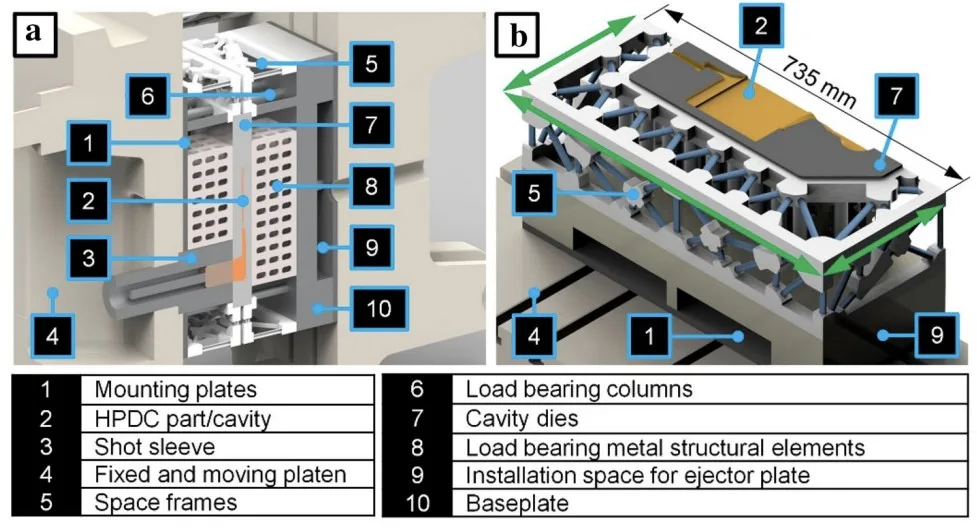
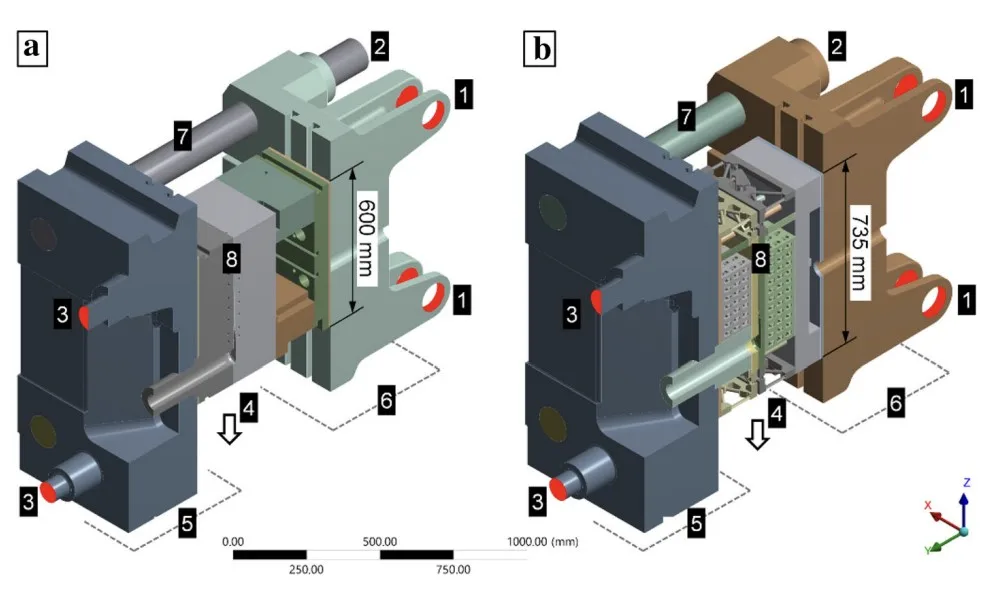
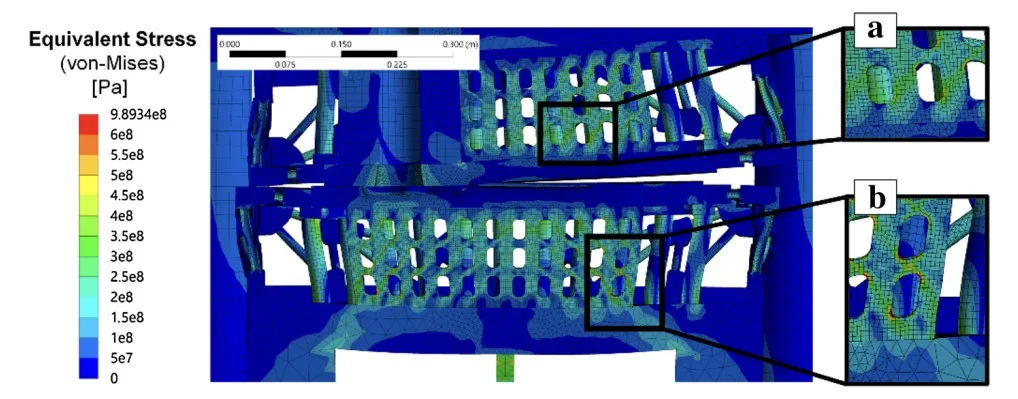
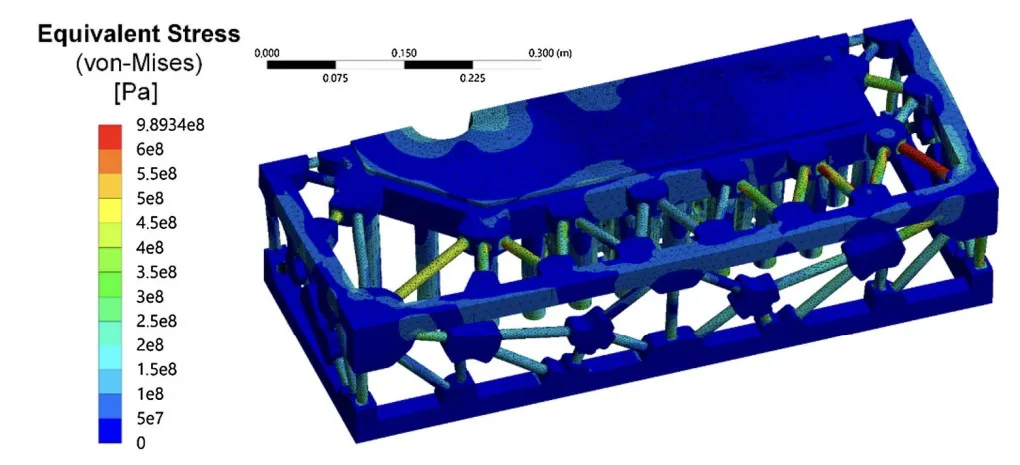
6. 結論と考察:
- 主な結果の要約:
本初期研究は、モジュラー軽量ダイカスト金型設計がHPDCプロセスにおけるエネルギー消費を大幅に削減する可能性を実証しました。シミュレーション結果は、従来の金型と比較して総エネルギー需要が約5.2倍減少することを示しました。計算された変形と応力は軽量設計でより高かったものの、管理可能な範囲内にとどまり、現実的な鋳造条件下では変形性能が向上することさえ示しました。 - 研究の学術的意義:
本研究は、軽量モジュラーダイカスト金型の実現可能性と性能特性に関する貴重な初期の洞察を提供します。エネルギー効率とモジュール性に焦点を当てた新しいアプローチを探求することにより、ダイカスト金型設計に関する学術的な理解に貢献します。本研究は、HPDCの文脈における軽量設計原理の可能性を強調し、この分野におけるさらなる研究開発のための基礎を提供します。 - 実用的な意味合い:
本研究の知見は、ダイカスト業界にとって重要な実用的な意味合いを持ちます。- エネルギーコストの削減: 軽量金型の大きなエネルギー節約の可能性は、特にエネルギー価格の上昇と環境問題への懸念が高まっている状況において、ダイカスト会社の運用コストの大幅な削減につながる可能性があります。
- 小ロットサイズ: エネルギー消費量の削減と、潜在的に製造コストの削減により、HPDCは小ロット生産サイズに対して経済的に実行可能になり、プロセスの柔軟性と適用性が向上する可能性があります。
- 持続可能な製造: エネルギー消費量と材料使用量の削減は、より持続可能で環境に優しいダイカストプロセスに貢献します。
- 低い電力要件: 軽量金型における冷却チャネルの熱出力の減少は、より低い電力要件の温度制御ユニットを使用できる可能性を示唆しています。
- 研究の限界:
本研究は初期調査であり、いくつかの限界があります。- シミュレーションベースの研究: 結果は数値シミュレーションに基づいており、実際の鋳造シナリオでの正確性と適用性を確認するには実験的検証が必要です。
- 特定の形状とプロセス条件: 解析は、特定の4mm板状形状とプロセス条件のセットに対して実施されました。他の部品形状や鋳造パラメータへの知見の一般化可能性については、さらなる調査が必要です。
- 簡略化された境界条件: インターフェース熱伝達係数や、滑りに対する無摩擦仮定など、特定の境界条件は、データの制約により簡略化されました。精度を向上させるためには、より洗練されたモデルと実験データが必要です。
- 有効キャビティ圧力結合: 有効キャビティ圧力は、シミュレーションで材料凝固と動的に結合されておらず、変形と応力の予測の精度に影響を与える可能性があります。
- 変形を超えた部品品質: 本研究は主に金型変形に焦点を当てました。多孔性や機械的特性など、HPDC部品品質の他の側面は直接評価されていません。
7. 今後のフォローアップ研究:
- 今後のフォローアップ研究の方向性:
今後の研究は、モジュラー軽量ダイカスト金型コンセプトをさらに発展させ、検証するために、以下の方向に焦点を当てる必要があります。- 実験的検証: プロトタイプモジュラー軽量ダイカスト金型を製造し、実験的な鋳造試験を実施して、シミュレーション結果を検証し、実際の生産環境での性能を評価します。
- 構造最適化: 軽量構造、特に荷重支持金属構造要素と空間フレームをさらに最適化して、応力集中を低減し、変形を最小限に抑えます。
- 高度な金型材料: 熱管理と構造的完全性をさらに向上させるために、熱伝導率と引張強度の高い高度な金型材料の使用を調査します。
- 高度な温度制御: 金型温度の均一性とサイクルタイムを最適化するために、等角冷却チャネルなどの高度な金型温度制御方法を検討し、統合します。
- 製造コンセプト: モジュラー軽量ダイカスト金型の費用対効果の高い生産のための製造コンセプトと戦略を開発し、設計の特定の要件を考慮します。
- さらなる探求が必要な領域:
以下の領域でさらなる探求が必要です。- 実際のダイカスト金型の実装とテスト: シミュレーションから現実世界の実装とテストに進むことは、コンセプトの実用的な実現可能性を評価するために非常に重要です。
- HPDC部品品質評価: 寸法精度、表面仕上げ、機械的特性など、軽量金型を使用して製造されたHPDC部品品質の包括的な評価。
- スライダーと複雑な形状の考慮: 産業用途で一般的なスライダーやアンダーカットのあるより複雑な部品形状に対応するように設計コンセプトを拡張します。
- 製造コスト分析: モジュラー軽量金型の製造コストを従来の金型と比較し、全体的な経済的利点を評価するために、詳細な製造コスト分析を実施します。
- キャビティ圧力と凝固の結合: 変形と応力の予測の精度を向上させるために、キャビティ圧力を材料凝固と動的に結合する、より洗練されたシミュレーションアプローチを実装します。
8. 参考文献:
- H. Lickfett, NE-Metallgießereien in Deutschland: Strukturentwicklung und Strategische Investitionen pro Standort Deutschland (Leichtbau in Guss, Saarbru¨cken, 2013)
- R. Scho¨ngrundner, W. Ecker, S. Marsoner et al., Development of a simulation aided design strategy for casting die frames. In: 9th International Tooling Conference, Leoben, Austria, (2012)
- C. Brecher, D. O¨ zdemir (eds.), Integrative Production Technology: theory and Applications (Springer, Cham, 2017)
- Y. Queudeville, T. Ivanov, C. Nußbaum et al., Decision and design methodologies for the lay-out of modular dies for high-pressure-die-cast-processes. in Materials Science Forum, (RWTH Aachen, Aachen, 2009), pp. 345–348
- B. Hummler-Schaufler, C. Schlumpberger, Produktentwicklung auf hohem Niveau. Druckgusspraxis 1, 39–42 (2004)
- Y. Queudeville, U. Vroomen, A. Bu¨hrig-Polaczek, Modularization methodology for high pressure die casting dies. Int. J. Adv. Manuf. Technol. 71(9–12), 1677–1686 (2014). https://doi.org/10.1007/s00170-013-5582-9
- O. Eitelwein, J. Weber, Unternehmenserfolg durch Modularisierung von Produkten, Prozessen und Supply Chains: WHU Benchmarking-Studie Modularisierung (Books on Demand, Norderstedt, 2011)
- J.H. Mikkola, O. Gassmann, Managing modularity of product architectures: toward an integrated theory. IEEE Trans. Eng. Manag. 50(2), 204–218 (2003). https://doi.org/10.1109/TEM.2003.810826
- H. Goehler, J. Meinert, T. Doll et al., Steel hollow sphere structures for energy efficient foaming tools. in Cellular Materials—CellMat (International Congress Center Dresden, Dresden, Germany, 2014)
- M.R. Barone, D.A. Caulk, A new method for thermal analysis of die casting. Trans. ASME J. Heat Transf. 115, 284–293 (1993)
- K. Hegde, H. Ahuett-Garza, G. Padiyar, NADCASponsored research: FEM analysis of die casting die deflections: Part I—modeling and simulation. in 18th International Die Casting Congress and Exposition, IN, USA, (1995)
- H. Ahuett-Garza, K. Hegde, R.A. Miller et al., NADCA-sponsored research: FEM analysis of die casting die deflections: Part ll—results. in 18th International Die Casting Congress and Exposition, IN, USA, (1995)
- H. Ahuett-Garza, R.A. Miller, The effects of heat released during fill on the deflections of die casting dies. J. Mater. Process. Technol. 142(3), 648–658 (2003). https://doi.org/10.1016/S0924-0136(03)00685-X
- A. Long, D. Thornhill, C. Armstrong et al., Stress correlation between instrumentation and simulation analysis of the die for high pressure die casting. Int. Metalcast 7(2), 27–41 (2013). https://doi.org/10.1007/BF03355551
- S.I. Jeong, C.K. Jin, H.Y. Seo et al., Mold structure design and casting simulation of the high-pressure die casting for aluminum automotive clutch housing manufacturing. Int. J. Adv. Manuf. Technol. 228(12), 1599 (2015). https://doi.org/10.1007/s00170-015-7566-4
- H. Yamagata, Y. Shigenaga, S. Tanikawa et al., Deflection simulation of a die installed in a highpressure die-casting machine. Trans. Jpn. Soc. Mech. Eng. 79(806), 3920–3929 (2013)
- C.V. Camp, M. Farshchin, Design of space trusses using modified teaching–learning based optimization. Eng. Struct. 62–63, 87–97 (2014). https://doi.org/10.1016/j.engstruct.2014.01.020
- M. Farshchin, C.V. Camp, M. Maniat, Multi-class teaching–learning-based optimization for truss design with frequency constraints. Eng. Struct. 106, 355–369 (2016). https://doi.org/10.1016/j.engstruct.2015.10.039
- B. Yalc¸in, M. Koru, O. Ipek et al., Effect of injection parameters and vacuum on the strength and porosity amount of die-casted A380 alloy. Int. Metalcast 11(2), 195–206 (2017). https://doi.org/10.1007/s40962-016-0046-2
- G. Dour, M. Dargusch, C. Davidson et al., Development of a non intrusive heat transfer coefficient gauge and its application to high pressure die casting. Metall. Sci. Technol. 22(1), 16–21 (2004)
- Y. Cao, Z. Guo, S. Xiong, Determination of the metal/ die interfacial heat transfer coefficient of high pressure die cast B390 alloy. IOP Conf. Ser.: Mater. Sci. Eng. 33, 12010 (2012). https://doi.org/10.1088/1757-899X/33/1/012010
- Z. Guo, S. Xiong, S. Cho et al., Interfacial heat transfer coefficient between metal and die during high pressure die casting process of aluminum alloy. Front. Mech. Eng. China 2(3), 283–287 (2007). https://doi.org/10.1007/s11465-007-0049-z
- Z. Guo, S. Xiong, B. Liu et al., Understanding of the influence of process parameters on the heat transfer behavior at the metal/die interface in high pressure die casting process. Sci. China Ser. E-Technol. Sci. 52(1), 172–175 (2009). https://doi.org/10.1007/s11431-008-0295-2
- Z.-P. Guo, S.-M. Xiong, B.-C. Liu et al., Effect of process parameters, casting thickness, and alloys on the interfacial heat-transfer coefficient in the highpressure die-casting process. Metall. Mater. Trans. A 39(12), 2896–2905 (2008). https://doi.org/10.1007/s11661-008-9640-0
- A. Hamasaiid, G. Dour, M.S. Dargusch et al., Heattransfer coefficient and in-cavity pressure at the casting-die interface during high-pressure die casting of the magnesium alloy AZ91D. Metall. Mater. Trans. A 39(4), 853–864 (2008). https://doi.org/10.1007/s11661-007-9452-7
- G. Zhi-peng, X. Shou-mei, L. Bai-cheng et al., Determination of the heat transfer coefficient at metal– die interface of high pressure die casting process of AM50 alloy. Int. J. Heat Mass Trans. 51(25–26), 6032–6038 (2008). https://doi.org/10.1016/ j.ijheatmasstransfer.2008.04.029
- M. Ciofalo, I. Di Piazza, V. Brucato, Investigation of the cooling of hot walls by liquid water sprays. Int. J. Heat Mass Trans. 42(7), 1157–1175 (1999). https://doi.org/10.1016/S0017-9310(98)00250-6
- G.W. Liu, Y.S. Morsi, B.R. Clayton, Characterisation of the spray cooling heat transfer involved in a high pressure die casting process. Int. J. Therm. Sci. 39(5), 582–591 (2000). https://doi.org/10.1016/S1290-0729(00)00207-6
- A.S. Sabau, R.B. Dinwiddie, Characterization of spray lubricants for the high pressure die casting processes. J. Mater. Process. Technol. 195(1–3), 267–274 (2008). https://doi.org/10.1016/j.jmatprotec.2007.05.021
- J.H. Hattel, P.N. Hansen, A 1-D analytical model for the thermally induced stresses in the mold surface during die casting. Appl. Math. Model. 18(10), 550–559 (1994). https://doi.org/10.1016/0307-904X(94)90140-6
- S. Mu¨ller, Ermittlung der Lebensdauer von Aluminium-Druckgießformen aufgrund thermischer Ermu¨dung. Zugl.: Braunschweig, Techn. Univ., Diss., 2015. Forschungsberichte des Instituts fu¨r Fu¨ge- und Schweißtechnik, Shaker, Aachen, 40 (2015)
- M. Ayabe, T. Nagaoka, K. Shibata et al., Effect of high thermal conductivity die steel in aluminum casting. Int. Metalcast 2(2), 47–55 (2008). https://doi.org/10.1007/BF03355427
- E. Kaschnitz, P. Hofer, W. Funk, Thermophysikalische Daten eines Warmarbeitsstahls mit hoher Wa¨rmeleitfahigkeit. GIESSEREI 97(9), 46–49 (2010)
- A. Armillotta, R. Baraggi, S. Fasoli, SLM tooling for die casting with conformal cooling channels. Int. J. Adv. Manuf. Technol. 71(1–4), 573–583 (2014). https://doi.org/10.1007/s00170-013-5523-7
- T. Kimura, H. Yamagata, S. Tanikawa, FEM stress analysis of the cooling hole of an HPDC die. IOP Conf. Ser.: Mater. Sci. Eng. 84, 12052 (2015). https://doi.org/10.1088/1757-899X/84/1/012052
- H. Hu, F. Chen, X. Chen et al., Effect of cooling water flow rates on local temperatures and heat transfer of casting dies. J. Mater. Process. Technol. 148(1), 57–67 (2004). https://doi.org/10.1016/j.jmatprotec.2004.01.040
- T. Kim, K. Jin, N. Kim et al., Numerical analysis and optimal design to reduce residual stresses and deformations of die casting baseplate after ejection. J. Mech. Sci. Technol. 29(7), 2949–2956 (2015). https://doi.org/10.1007/s12206-015-0625-9
- D. Klobcˇar, L. Kosec, B. Kosec et al., Thermo fatigue cracking of die casting dies. Eng. Fail. Anal. 20, 43–53 (2012). https://doi.org/10.1016/j.engfailanal.2011.10.005
- D. Klobcˇar, J. Tusˇek, B. Taljat, Thermal fatigue of materials for die-casting tooling. Mater. Sci. Eng. A 472(1–2), 198–207 (2008). https://doi.org/10.1016/j.msea.2007.03.025
- S. Naimi, S.M. Hosseini, Tool steels in die-casting utilization and increased mold life. Adv. Mech. Eng. 7(1), 286071 (2014). https://doi.org/10.1155/2014/286071
9. 著作権:
*この資料は、Sebastian Müller、Klaus Dilger、Anke Müller、Felix Rothe、Klaus Dröderの論文:AN INITIAL STUDY OF A LIGHTWEIGHT DIE CASTING DIE USING A MODULAR DESIGN APPROACH(モジュラー設計アプローチを用いた軽量ダイカスト金型の初期研究)に基づいています。
*論文ソース:https://doi.org/10.1007/s40962-018-0218-3
この資料は上記の論文に基づいて要約されたものであり、商業目的での無断使用は禁止されています。
Copyright © 2025 CASTMAN. All rights reserved.