1. 概要:
- タイトル: マグネシウム合金自動車部品のOEMへの開発と応用:レビュー (Development and application of magnesium alloy parts for automotive OEMs: A review)
- 著者: Bo Liu, Jian Yang, Xiaoyu Zhang, Qin Yang, Jinsheng Zhang, Xiaoqing Li
- 発表年: 2023年
- 掲載ジャーナル/学会: Journal of Magnesium and Alloys
- キーワード: マグネシウム合金 (Magnesium alloy); 純正機器メーカー (Original equipment manufacturer); 自動車用途 (Automotive application); 開発プロセス (Development process)
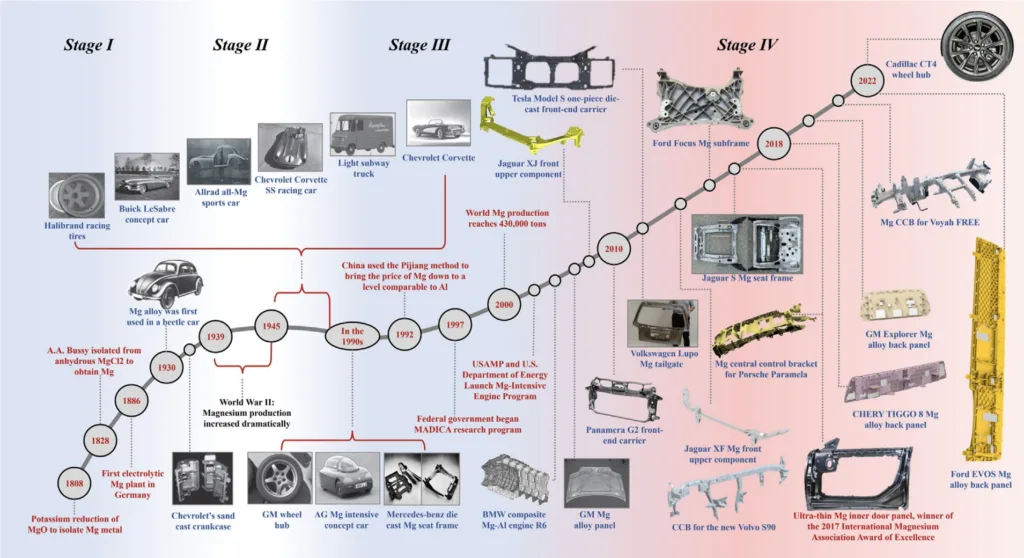
2. 研究背景:
- 研究テーマの社会的/学術的背景:
中国は現在、「省エネと排出削減」および「二酸化炭素排出量ピークアウトとカーボンニュートラル」戦略を積極的に推進しています。中国で最も資源に恵まれた軽金属材料であるマグネシウム(Mg)合金は、自動車、鉄道輸送、航空宇宙、医療、電子製品への応用を拡大しています。重慶大学、上海交通大学、オーストラリア国立大学などは、Mg合金の製造、特性、プロセスに関する広範な研究を実施してきました。過去20年間で、自動車産業におけるMg合金の割合は徐々に拡大していますが、現在、自動車用Mg合金部品の設計と開発に関する報告はほとんどありません。 - 既存研究の限界:
Mg合金の利用は増加しているものの、特に自動車用Mg合金部品の設計と開発を詳細に記述した報告は不足しています。Mg合金部品の全開発プロセスと性能要件に関する情報は限られています。 - 研究の必要性:
本レビューは、Mg合金の応用モデルと代表的な部品事例を、車体システム、シャシーシステム、パワートレインシステム、内外装システムの4つの主要システムを中心にまとめる必要性に対応しています。信頼性の高いダイカストMg合金部品の開発ロジックをOEM向けに紹介することを目的としています。自動車分野でのMg合金の応用に対する信頼と意欲を高めるために、自動車OEMがMg合金部品を開発する際の方法、プロセス、および注意すべき点を共有することを目指しています。最後に、Mg合金材料が直面する複数の課題と、これらの課題にどのように対処するかを特定し、議論することを目的としています。
3. 研究目的と研究課題:
- 研究目的:
本レビューの主な目的は、自動車部品用のさまざまなMg合金シリーズの開発における歴史的経緯と最近の進歩をまとめることです。既存の研究文献の批判的分析を伴います。最も重要なことは、実際の製造事例を通じて、ダイカストMg合金の全プロセス開発技術ルートを明らかにすることです。これは、OEMが新しいMg部品を開発する自信を高めることを目的としており、自動車軽量化研究に取り組む企業や製造業者にとって価値のあるものと考えられます。さらに、本レビューでは、国の政策と規制、環境エネルギー保護、消費者のニーズを踏まえ、Mg合金材料が直面するさまざまな課題と、これらの課題を克服する方法について議論し、将来の見通しを示します。 - 主な研究課題:
本研究は、暗黙のうちに次のような疑問に取り組んでいます。- 自動車の4つの主要システムにおいて、Mg合金部品の典型的な用途とモデルは何ですか?
- 自動車OEM向けの信頼性の高いダイカストMg合金部品を作成するための段階的な開発プロセスは何ですか?
- 自動車分野におけるMg合金のより広範な応用を妨げている主な障害は何ですか?
- 研究仮説:
根底にある仮説は、Mg合金の応用に関する包括的なレビューと、OEMの成功事例を詳細に示し、開発プロセスを説明することで、OEMの信頼性を大幅に高め、自動車製造におけるMg合金の採用を促進できるということです。
4. 研究方法:
- 研究デザイン:
本研究では、既存の文献と自動車OEMからの実際の事例研究から情報を統合するレビューベースの研究デザインを採用しています。 - データ収集方法:
本研究は、自動車用途におけるマグネシウム合金に関する学術出版物および業界レポートの包括的な文献レビューに依拠しています。また、実際のOEMアプリケーションの事例研究を取り入れ、開発プロセスを説明しています。 - 分析方法:
分析には、既存の文献の要約と批判的分析が含まれます。事例研究分析は、自動車製造におけるMg合金部品の実用的な応用と開発プロセスを理解するために使用されます。 - 研究対象と範囲:
レビューの範囲は、自動車部品におけるさまざまなMg合金シリーズの応用を網羅しています。車体、シャシー、パワートレイン、内外装トリムの4つの主要な車両システムを中心に構成されています。本研究では、主にダイカストを主要な製造プロセスとして焦点を当て、OEMの事例研究を検討して、開発技術ルートを詳細に説明しています。
5. 主な研究成果:
- 主な研究成果:
本レビューでは、Mg合金の応用モデルと代表的な部品事例を、4つの主要な車両システム全体にわたってまとめることに成功しました。信頼性の高いダイカストMg合金部品の開発ロジックを示すために、2つのOEM事例研究が提示されました。また、現在自動車産業におけるMg合金のより広範な採用を妨げている複数の課題を特定して分類し、潜在的な解決策について議論しました。 - 統計的/定性的分析結果:
論文では、表と図の形で定量的なデータを示しています。- 表1: 「Mg合金の機械的特性の比較」。この表は、Mg、AZ91、AM50、AS41、AE42、AISI8Cu3合金の密度、比熱、熱伝導率、融点、引張強度、降伏点、伸び率、弾性率、ブリネル硬さを提供しています。
- 表2: 「車体におけるMg合金シリーズの応用分野」。この表は、Mg合金シリーズ(AZ、AM、AS、AE、AXE、AJ)、その性能上の利点、特定の分類(例:AZ91D、AM60B)、用途(例:中央制御ブラケット、シートフレーム)、およびダイカストプロセスをリストアップしています。
- 表3: 「Mgフロントエンドキャリアとフロントアッパーコンポーネントのいくつかのモデルの例」。この表は、車両タイプ、期間、重量/kg、およびJaguar XJ、Jaguar XF、Benz AMG GT、Lincoln MKT、Tesla Model S、NIO ES8、Range Rover、Porsche Panamera G2、Changan ENDO EV460の部品と車両タイプの画像を提供しています。
- 表4: 「自動車用途における代表的なMg CCBのいくつかの事例」。この表は、車両タイプ、重量/kg、CCBの写真、およびRongwei 550、Ford Explorer、Dodge Caliber、LandRover LWB 5.0、LandRover LR3、ARCFOX-1(C11CB)、Mercedes-Benz M-Class、Mini Cooper、Mercedes-Benz E-Class、Voyah FREEの車両タイプの写真をリストアップしています。
- 表5: 「強度およびモーダル解析の結果」。この表は、さまざまなフロントカバーロックの剛性、荷重制限、極限引張強度、強度、ラジエーターシステムモジュールの取り付け点剛性、ヘッドライトブラケット剛性、モーダル解析、および加速衝撃試験の結果を示し、結果が適格かどうかを示しています。
- 表6: 「金型流れ解析パラメータ設定」。この表は、3ラウンドの金型流れ解析における材料温度、金型温度、圧力室長、材料ケーキ厚さ、充填率、臨界速度、および高速を示しています。
- 重量削減率については、Aston Martin DB9のサイドドア部品で「43%減」、Chrysler Pacificaのテールゲートで「50%」の重量削減など、特定の部品について言及されています。
- データ解釈:
レビュー全体で提示および分析されたデータは、Mg合金が自動車用途において大きな軽量化の可能性を提供することを一貫して示しています。OEMの事例研究は、ダイカストMg合金部品の使用の実現可能性と利点を示しています。ただし、コスト、腐食、技術的な成熟度に関連する課題は、より広範な採用のために克服すべき重要なハードルとして残っています。 - 図のリスト:
- 図 1. 自動車部品の歴史的プロセスにおけるMg合金。
- 図 2. 自動車ドアにおけるMg合金の開発と応用。
- 図 3. フロントエンドキャリアとフロントアッパーコンポーネントにおけるMg合金の開発と応用。
- 図 4. ルーフ、フード、トランクリッドにおけるMg合金の開発と応用。
- 図 5. ホイールにおけるMg合金の開発と応用。
- 図 6. ステアリングホイールにおけるMg合金の開発と応用。
- 図 7. サブフレームにおけるMg合金の開発と応用。
- 図 8. パワートレイン用途におけるMg合金。
- 図 9. オイルパンにおけるMg合金の開発と応用。
- 図 10. シートフレームにおけるMg合金の応用。
- 図 11. Mg合金CCBのいくつかの応用例。
- 図 12. Mg合金センターブラケットのいくつかの応用例。
- 図 13. 自動車用のその他のMg合金部品。
- 図 14. MASFの全プロセス解析プロセスと結果。
- 図 15. MAFCの全プロセス解析プロセスと結果。
- 図 16. MASFの詳細な開発プロセス。
- 図 17. MAFCの詳細な開発プロセス。
- 図 18. Mg合金の腐食保護ソリューション。
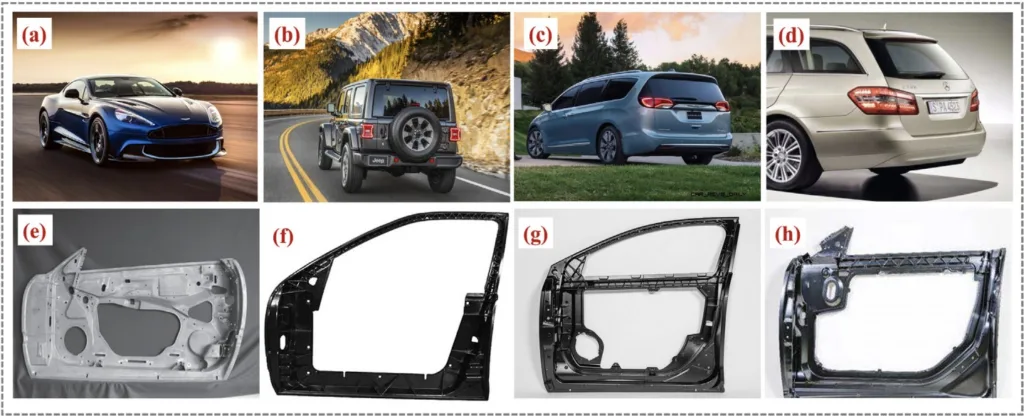
Mercedes-Benz E-Class T-Model featuring the hybrid Mg-Al hatch back; (e) Inner door frame of the Daimler-Chrysler SL Roadster; (f) Ford’s concept die-cast Mg door inner with an open architecture; (g) Integrated Mg die-cast door inner designed as part of a DOE sponsored project led by GMC; (h) Ultra-thin and ultra-light Mg alloy door inner.
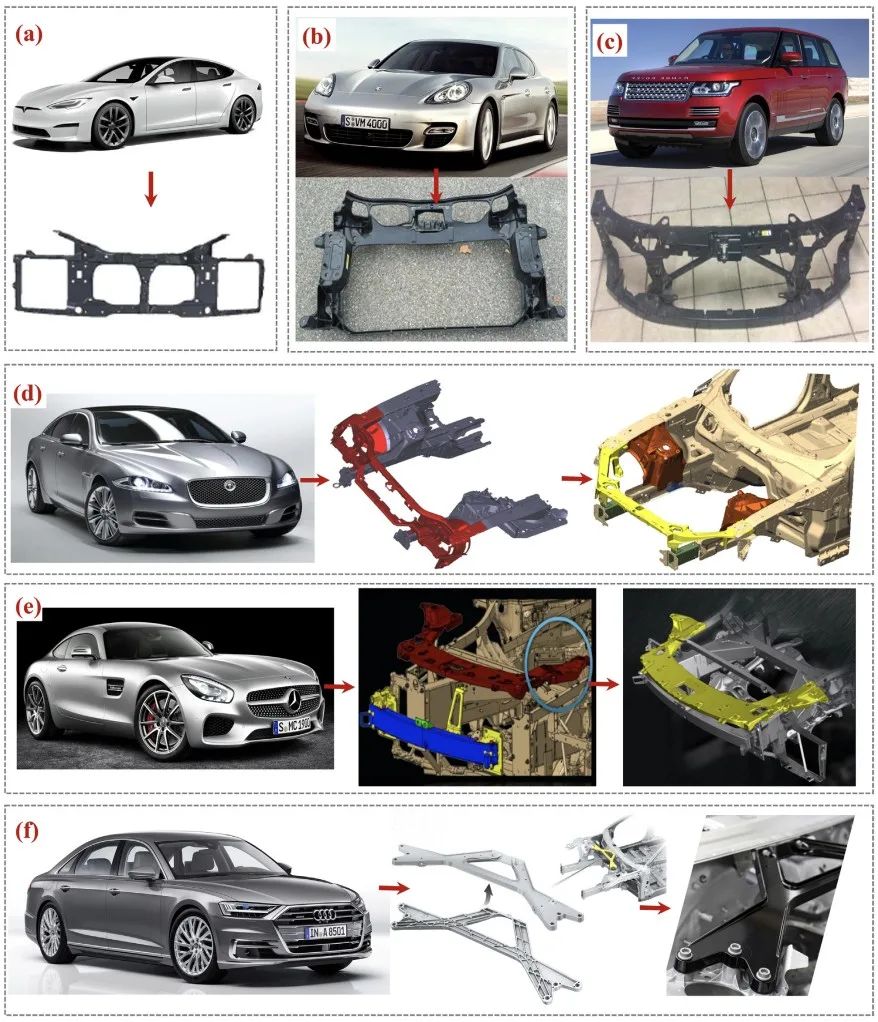
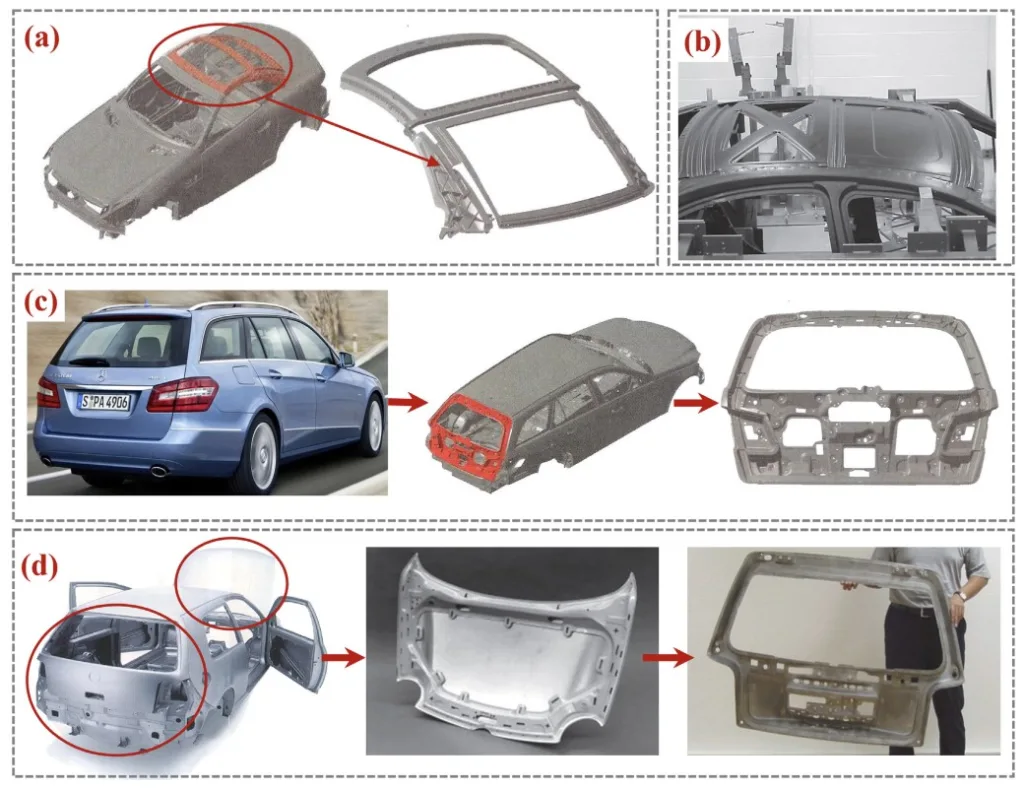
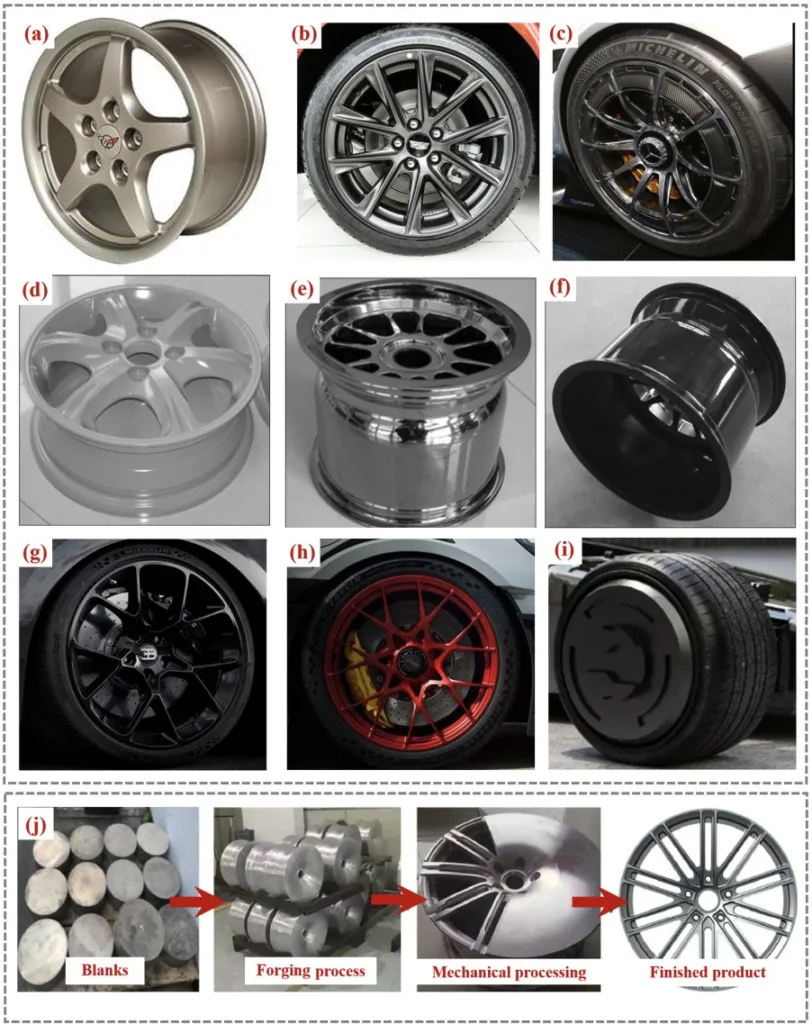
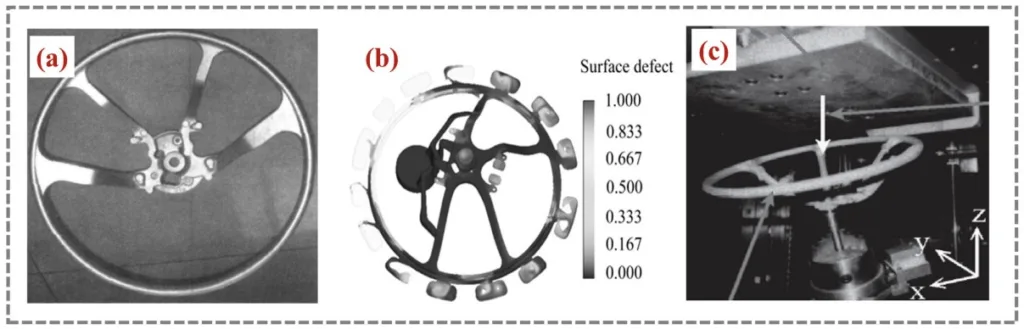
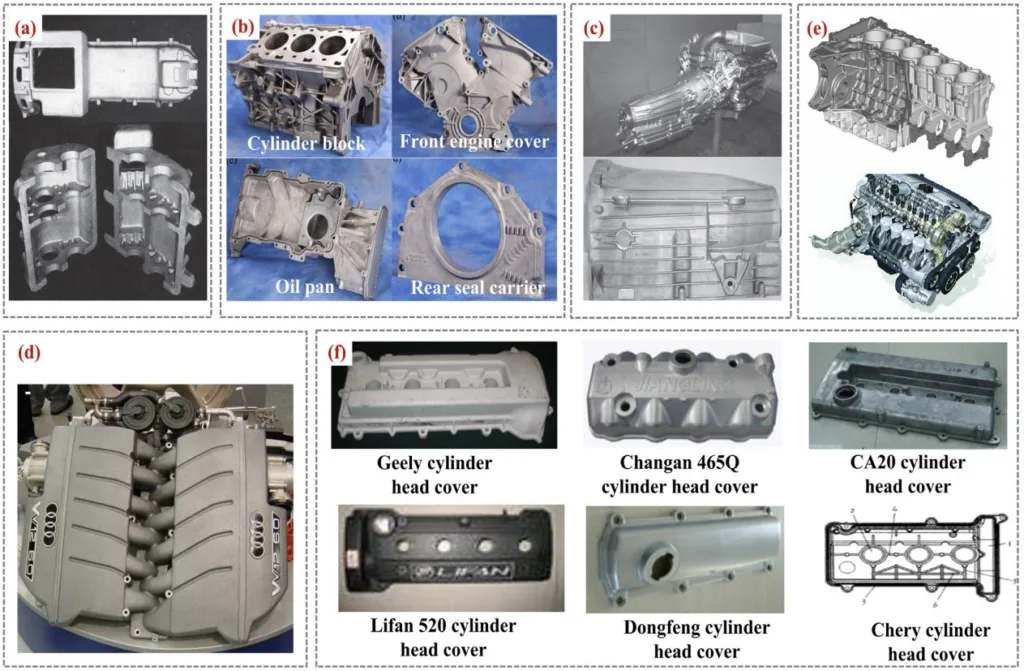
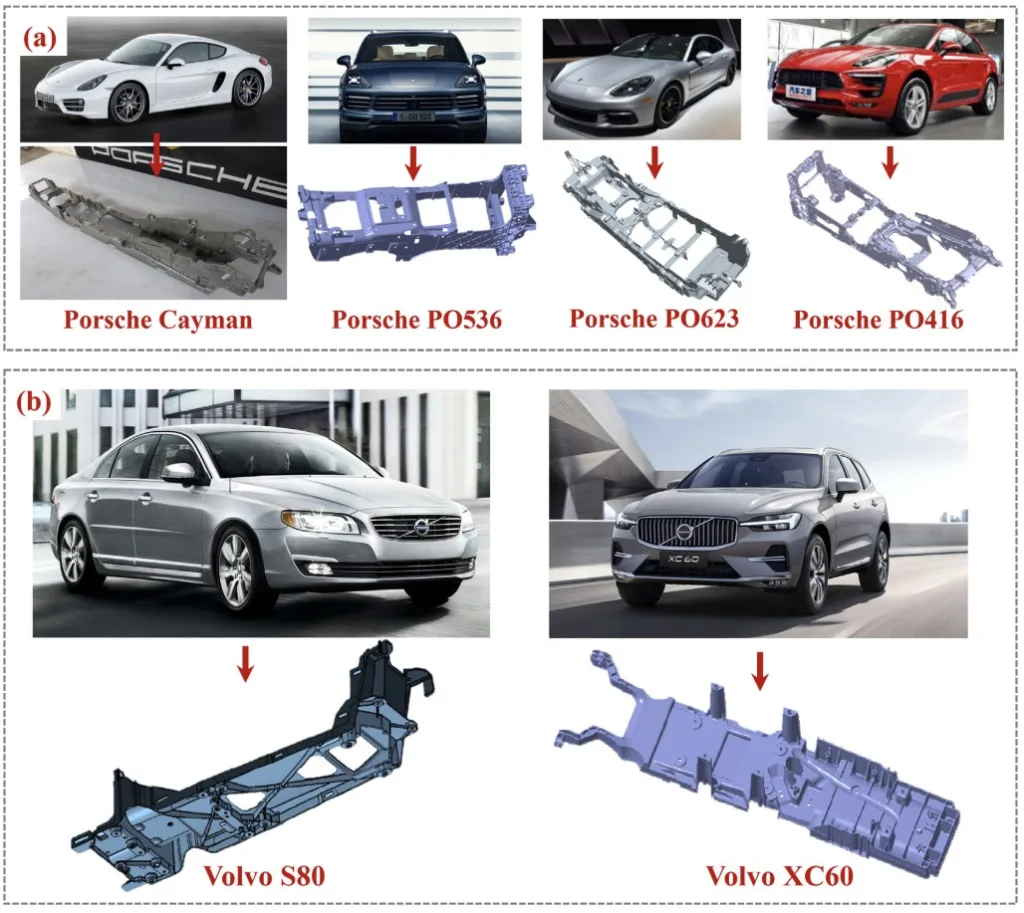
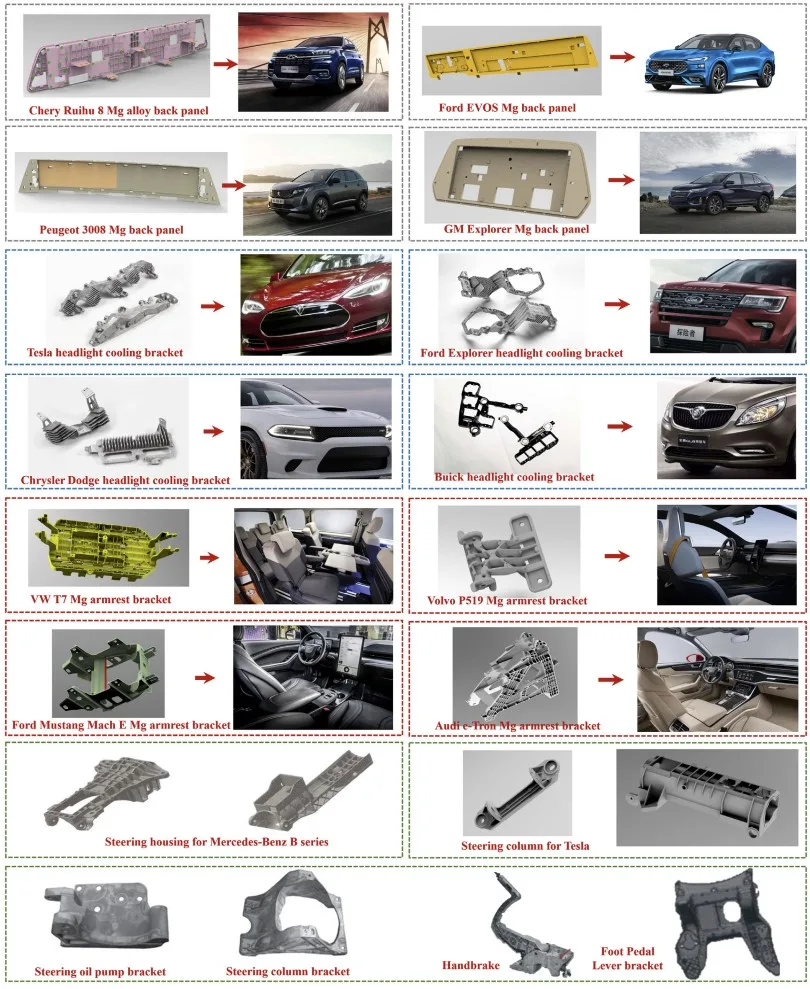
6. 結論と考察:
- 主な結果の要約:
レビューの結論として、マグネシウム合金は、その有利な特性により、自動車産業において貴重なエンジニアリング材料としての地位を確立しました。本論文では、OEMの製造事例を通じて、ダイカストMg合金の開発技術ルートを強調しました。また、自動車におけるMg合金の幅広い応用範囲を示し、OEMがこれらの材料を新しい部品設計に採用する自信を高めることを目的としています。Mg合金の応用は、「適材適所」の原則に従い、軽量性と優れた流動性などの利点を活用し、低強度や腐食しやすいなどの欠点を回避しようとしています。レビューでは、AM50/60およびAZ91DシリーズのMg合金が主流材料であり、ダイカストが最も一般的な成形プロセスであると特定しています。Mg合金は、高荷重のかかる梁構造部品ではなく、骨格やブラケットの形で一般的に使用され、ガルバニック腐食を起こしにくい環境で応用されています。構造設計と最適化は、コスト削減に不可欠です。 - 研究の学術的意義:
本レビューは、自動車分野におけるMg合金の応用に関する包括的かつ最新の概要を提供します。現在の研究開発の状況に関する貴重な学術的洞察を提供し、将来の研究の参考資料として、またこの分野の研究者にとって統合されたリソースとして役立ちます。 - 実用的な意義:
本レビューは、自動車OEMにとって重要な実用的な意義を持っています。OEMの成功事例を紹介し、開発プロセスを詳細に説明することで、新しい部品開発にMg合金を採用するOEMの自信を高めることを目的としています。Mg合金部品を開発するための実用的な参考資料を提供し、自動車軽量化における将来のイノベーションのための主要な課題と機会を強調しています。 - 研究の限界:
レビューの範囲は、主にダイカストプロセスとOEMの事例研究に焦点を当てています。自動車におけるMg合金のすべての可能な応用を包括的に網羅しているわけではなく、他の製造技術を詳細に検討しているわけでもありません。
7. 今後のフォローアップ研究:
- 今後の研究の方向性:
論文では、今後の研究で探求すべき方向性として、以下を提案しています。- Mg合金アディティブマニュファクチャリング技術。
- Mg合金の水素貯蔵応用。
- 包括的なMg合金材料データベースと性能評価システムの開発。
- Mg合金製造のプロセスとコストの最適化への取り組み。
- 技術革新のギャップと産業構造の矛盾の克服。
- さらなる探求が必要な分野:
今後の研究は、以下に焦点を当てる必要があります。- 車両のさらなる軽量化を達成するための斬新なMg合金構造と技術の開発。
- 持続可能でリサイクル可能なMg生産のためのグリーン電力電解Mg技術の推進。
- Mg合金の開発と応用におけるグローバルな課題に対処するための大学、政府、研究機関間の連携強化。
8. 参考文献:
- [1] C. Moosbrugger, L. Marquard, Engineering Properties of Magnesium Alloys, ASM International, 2017.
- [2] F. Tong, X. Chen, S. Wei, et al., J. Magn. Alloys 9 (6) (2021) 1967-1976.
- [3] R. Li, Q. Liu, R. Zhang, et al., Energy Storage Mater. (2022).
- [4] S.H. Kang, D.W. Han, H.K. Kim, J. Magn. Alloys 8 (1) (2020) 241-251.
- [5] G. Ma, H. Xiao, J. Ye, et al., Mater. Sci. Technol. 36 (6) (2020) 645-653.
- [6] M.K. Kulekci, Int. J. Adv. Manuf. Technol. 39 (2008) 851-865.
- [7] G.L. Song, A. Atrens, Adv. Eng. Mater. 1 (1999) 11-33.
- [8] M. Grassel, M. Koch, South Dakota Med. 75 (5) (2022).
- [9] O. Myagmarjav, M. Zamengo, J. Ryu, et al., Appl. Therm. Eng. 91 (2015) 377-386.
- [10] Y. Yang, J. Zhang, B. Li, Ekoloji, 28 (107) (2019) 4827-4833.
- [11] J.S. Hoksbergen, M. Ramulu, P. Reinhall, et al., Appl. Compos. Mater. 16 (5) (2009) 263-283.
- [12] J.S. Binoj, N. Manikandan, P. Thejasree, et al., in: Investigations on Wire Electrical Discharge Machining of Magnesium Alloy AZ31B by Taguchi's Approach. Recent Advances in Materials and Modern Manufacturing, Springer, Singapore, 2022, pp. 923-931.
- [13] G. Sasaki, in: Material Mechanical Properties and Microstructure of Magnesium Alloy Matrix Composites Fabricated by Casting Process, 426, Materials Science Forum. Trans Tech Publications Ltd., Zurich-Uetikon, Switzerland, 2003, pp. 2015-2019.
- [14] Z.Q. Huang, H.Y. Lai, H.B. Zhou, et al., J. Min. Metall. B: Metall. 58 (1) (2022) 1-10.
- [15] N.P. Papenberg, S. Gneiger, I. Weissensteiner, et al., Materials (Basel) 13 (4) (2020) 985.
- [16] Z Zeng, M Salehi, A Kopp, et al., J. Magn. Alloys 10 (6) (2022) 1511-1541.
- [17] A.A Luo, J. Magn. Alloys 1 (1) (2013) 2-22.
- [18] T. Xu, Y. Yang, X. Peng, et al., J. Magn. Alloys 7 (3) (2019) 536-544.
- [19] J.A. Santamaría, J. Sertucha, A. Redondo, et al., Metals (Basel) 12 (4) (2022) 656.
- [20] F. D'Errico, D. Casari, La Metall. Ital. 36 (2022).
- [21] S.R. Golroudbary, I. Makarava, E. Repo, et al., Proc. CIRP 105 (2022) 589-594.
- [22] A.A Luo, Fundam. Magn. Alloy Metall. 266 (2013) 316.
- [23] S Prithivirajan, G M Naik, S Narendranath, et al., Int. J. Lightw. Mater. Manuf. 6 (1) (2023) 82-107.
- [24] A. Dziubińska, A. Gontarz, M. Dziubiński, et al., Adv. Sci. Technol. Res. J. 10 (31) (2016).
- [25] G.G. Wang, J.P Weiler, J. Magn. Alloys (2022).
- [26] Y. Yang, X. Xiong, J. Chen, et al., J. Magn. Alloys 9 (3) (2021) 705-747.
- [27] A.G Morachevskii, Russ. J. Appl. Chem. 92 (10) (2019) 1325-1335.
- [28] M.O. Pekguleryuz, A.A Kaya, Adv. Eng. Mater. 5 (12) (2003) 866-878.
- [29] J. Tan, S. Ramakrishna, Appl. Sci. 11 (15) (2021) 6861.
- [30] Alias J., Bakar N.F.A., Romzi M.A.F., et al. Development of Mg-Graphene composites and effect on microstructure and mechanical properties-a review. Enabling industry 4.0 through advances in manufacturing and materials, 2022: 139-149.
- [31] G.R Chapman, Min. Process. Extract. Metall. 111 (2) (2002) 49-52.
- [32] J. Li, B. Li, H. Shao, et al., Catalysts 8 (2) (2018) 89.
- [33] X. Tang, L. Guo, Q. Liu, et al., Cryst. Res. Technol. 50 (3) (2015) 203-209.
- [34] I. Kabdaşlı, A. Demirbilek, T. Ölmez, Fresenius Environ. Bull. 13 (10) (2004) 951-955.
- [35] MLQLH Guo, XQ B G F Ye, Z. Wu, Progr. Chem. 21 (11) (2009) 2358.
- [36] G. Long, P. Ma, M. Chu, in: Ammoniation Technology For Dehydration of Hydrated Magnesium Chloride in China, 488, Materials Science Forum. Trans Tech Publications Ltd, 2005, pp. 95-98.
- [37] F. Wang, J.J. Wang, Q.S. Li, et al., Adv. Mater. Sci. Eng. 2022 (2022).
- [38] D.B Zhao, in: The FEA Comparison of the Front Sub Frame in a Car between JDM2 Magnesium and steel. Applied Mechanics and Materials, 538, Trans Tech Publications Ltd, 2014, pp. 87-90.
- [39] R. Lu, K. Jiao, Y. Zhao, et al., Materials (Basel) 13 (20) (2020) 4654.
- [40] R. Senthilkumar, P. Ponnusamy, M. Prakash, SAE Int. J. Adv. Curr. Pract. Mob. 3 (2020) 831-835 (2020-28-0425).
- [41] Y.Z. Li, D.W. Fan, J.M Chen, Adv. Mat. Res. 211 (2011) 705-709.
- [42] J. Lyu, A. Lider, V. Kudiiarov, Metals (Basel) 9 (7) (2019) 768.
- [43] D.T. Nguyen, S.W. Song, J. Power Sources 368 (2017) 11-17.
- [44] J. Chen, L. Tan, X. Yu, et al., J. Mech. Behav. Biomed. Mater. 87 (2018) 68-79.
- [45] SAE J 465-1983, Magnesium Casting Alloys.
- [46] Pantelakis S.G., Alexopoulos N.D., Chamos A.N. Mechanical performance evaluation of cast magnesium alloys for automotive and aeronautical applications. 2007.
- [47] B.R. Powell, A.A. Luo, P.E Krajewski, Woodhead Publishing, 2012, pp. 150-209.
- [48] S. Ando, N. Harada, M. Tsushida, et al., Key Eng. Mater. 345 (2007) 101-104.
- [49] T. Li, J. Rao, J. Zheng, et al., J. Magn. Alloys 10 (6) (2022) 1581-1597.
- [50] D. Wenbo, Q. Yaling, Y. Zhenjie, et al., Rare Met. Mater. Eng. 38 (10) (2009) 1870-1875.
- [51] R.B. Figueiredo, M.T.P. Aguilar, P.R. Cetlin, et al., Processing magnesium alloys by severe plastic deformation. IOP conference series: materials science and engineering, 63, IOP Publishing, 2014.
- [52] S.S. Wu, J.W. Zhao, L. Wan, et al., in: Numerical Simulation of Mould Filling in Rheo-Diecasting Process of Semi-Solid Magnesium alloys. Solid State Phenomena, 116, Trans Tech Publications Ltd, 2006, pp. 554-557.
- [53] H. Yan, T. Wang, M.F Fu, Mater. Sci. Forum 575 (2008) 32-36.
- [54] F. Czerwinski, in: Selected Aspects of Semisolid Forming Magnesium alloys. Materials science Forum, 539, Trans Tech Publications Ltd, 2007, pp. 1644-1649.
- [55] F. Czerwinski, Materials (Basel) 14 (21) (2021) 6631.
- [56] Y. Zhang, Q. Zhu, C. Su, et al., Front. Chem. 10 (2022).
- [57] R. Kong, F. Xue, J. Wang, et al., Res. Policy 52 (2017) 19-28.
- [58] Y. Yu, Auto Manuf. Eng. 3 (11) (2020).
- [59] B.R. Powell, P.E. Krajewski, A.A Luo, Magnesium Alloys for Lightweight Powertrains and Automotive Structures, in: Materials, Design and Manufacturing for Lightweight Vehicles, Elsevier, Amsterdam, The Netherlands, 2021, pp. 125-186.
- [60] M.A Shand, The Chemistry and Technology of Magnesia, John Wiley & Sons, 2006.
- [61] D.A Kramer, Magnesium, its Alloys and Compounds, in: Magnesium, its Alloys and Compounds, 1, US Geological Survey Open-File Report, 2001, p. 341.
- [62] J. Durlach, in: Overview of Magnesium research: History and Current trends. New Perspectives in Magnesium Research, Springer, London, 2007, pp. 3-10.
- [63] B.J.C. Luthringer, F. Feyerabend, R. Willumeit-Römer, Magn. Res. 27 (4) (2014) 142-154.
- [64] B.B Clow, in: History of Primary Magnesium Since World War II. Essential Readings in Magnesium Technology, Springer, Cham, 2016, pp. 85-87.
- [65] USAMP teamMagnesium Vision 2020: A North American Automotive Strategic Vision For Magnesium, USCAR, 2006.
- [66] C. Blawert, N. Hort, K.U Kainer, Trans. Indian Inst. Met 57 (4) (2004) 397-408.
- [67] T.K. Aune, H. Westengen, T. Ruden, SAE Trans. (1994) 553-557.
- [68] Hawke D., Gaw K. Effects of chemical surface treatments on the performance of an automotive paint system on die cast magnesium. SAE Technical Paper, 1992.
- [69] G.D. Tong, H.F. Liu, Y.H Liu, Trans. Nonferrous Met. Soc. China 20 (2010) s336-s340.
- [70] R. Seetharaman, B. Lavanya, N. Niharika, et al., Mater. Today: Proc. 4 (6) (2017) 6743-6749.
- [71] Y.G. Liu, Z.H. Huang, H. Ding, et al., Key Eng. Mater. 353 (2007) 1614-1616.
- [72] Jacques R.P., DasGupta R., Shearouse J.D. Hot chamber diecasting of magnesium alloy AM50A for automotive interior structural components. SAE Technical Paper, 1996.
- [73] Grebetz J.C. A comparison of the impact characteristics of several magnesium die casting alloys. SAE Technical Paper, 1993.
- [74] J. Jekl, J. Auld, C. Sweet, et al., Development of a Thin-Wall Magnesium Side Door Inner Panel for Automobiles, General Motors LLC, Detroit, MI (United States), 2015.
- [75] Murray R.W., Hillis J.E. Magnesium finishing: chemical treatment and coating practices. 1990.
- [76] S. Annamalai, S. Periyakgoundar, K. Paramasivam, et al., Adv. Mater. Sci. Eng. 2020 (2020).
- [77] Durairaj S.R.N., Ganesan T., Rao P.C. Vibration analysis on magnesium alloy housing and analysis of resonant frequency on the housing between magnesium and aluminium alloy. SAE Technical Paper, 2017.
- [78] Luo A.A., Forsmark J., Sun X., et al. Mechanical and thermophysical properties of magnesium alloy extrusions. SAE Technical Paper, 2010.
- [79] Verma R., Carter J.T. Quick plastic forming of a decklid inner panel with commercial AZ31 magnesium sheet. SAE Technical Paper, 2006.
- [80] Kim S.W., Lee Y.S. Warm forming of 3t Mg alloy sheet for an automotive electronic compressor case. SAE Technical Paper, 2014.
- [81] Aune T.K., Westengen H., Ruden T. Mechanical properties of energy absorbing magnesium alloys. SAE Technical Paper, 1993.
- [82] S.V. Galatanu, M. Scano, D. Pietras, et al., Proc. Struct. Integr. 26 (2020) 269-276.
- [83] Effect of Section Thicknesses On Tensile Behavior and Microstructure of High Pressure Die Cast Magnesium Alloy AM50. Pacific Rim International Conference On Advanced Materials and Processing (PRICM 5) pt.1. Dept. of Mechanical, Automotive & Materials Engineering University of Windsor Windsor, Ontario, Canada, 2005 N9B 3P4; Manufacturing System Department, Ford Research Laboratory, Ford Motor Company, Dearborn, MI, USA 48121; Dept. of Mechanical, Automotive & Material.
- [84] H. Alves, U. Koster, E. Aghion, et al., Mater. Technol. 16 (2) (2001) 110-126.
- [85] Sadayappan K., Vassos M. Evaluation of a thixomolded magnesium alloy component for automotive application. SAE Technical Paper, 2010.
- [86] Hubbert T., Chen X., Li N., et al. 2005 Ford GT magnesium I/P structure. SAE Technical Paper, 2004.
- [87] S. Kim, H. Yoo, Y. Kim, Magn. Technol. (2002).
- [88] Y.Q. Ma, R. Chen, E.H Han, Mater. Sci. Forum 488 (2005) 265-268.
- [89] Gerken R.T., Ghaffari B., Sachdev A.K., et al. Low-cost magnesium alloy sheet component development and demonstration project. SAE Technical Paper, 2022.
- [90] M.O. Pekguleryuz, E. Baril, in: Development of Creep Resistant Mg-Al-Sr alloys. Essential readings in Magnesium Technology, Springer, Cham, 2016, pp. 283-289.
- [91] H. Westengen, P. Bakke, Mater. Sci. Forum. 419 (2003) 35-42.
- [92] M.A. Easton, S. Zhu, T.B. Abbott, et al., Adv. Eng. Mater. 18 (6) (2016) 953-962.
- [93] S. Gavras, S. Zhu, M.A. Easton, et al., Front. Mater. 6 (2019) 262.
- [94] Y. Xue, M.F. Horstemeyer, D.L. McDowell, et al., Int. J. Fatigue 29 (4) (2007) 666-676.
- [95] D. Argo, M. Lefebvre, Melt protection for the AJ 52 magnesium strontium alloy, in: Magnesium Technology 2003 as held at the 2003 TMS Annual Meeting, 2003, pp. 15-21.
- [96] Burns J., Han L., Hu H., et al. Effects of section thicknesses on tensile properties of permanent mould cast magnesium alloy AJ 62. Minerals, metals and materials society/AIME, 420 Commonwealth Dr., P. O. Box 430 Warrendale PA 15086 USA. [np]. 14-18 Feb, 2010.
- [97] Blanchard P.J., Bretz G.T., Subramanian S., et al. The application of magnesium die casting to vehicle closures. SAE Technical Paper, 2005.
- [98] L. Riopelle, Magnesium Applications, in: International Magnesium Association (IMA) Annual Magnesium in Automotive Seminar, April 20, 2004 Livonia, MI.
- [99] Eng L. An assessment of mass reduction opportunities for a 2017-2020 model year vehicle program. 2010.
- [100] Aston Martin global website, 2018.
- [101] Daimler Global Media, media.daimler.com, 2017.
- [102] FCA North America media, media.fcanorthamerica.com, 2017.
- [103] S. Gibbs, Metal Casting Design and Purchasing (July/August 2010) 29e33.
- [104] IMA, Magn. Showcase 12 (2010) 2.
- [105] J.P Weiler, Next generation magnesium liftgate-utilizing advanced technologies to maximum ass reduction in a high volume vehicle application. International magnesium association's 73rd annual world magnesium conference, 2016.
- [106] Blawert C., Heitmann V., Hche D., et al. Design of hybrid Mg/Al components for the automotive body-Preventing general and galvanic corrosion. ibekor com, 2011.
- [107] J.P Weiler, J. Magn. Alloys 7 (2) (2019) 297-304.
- [108] Balzer J.S., Dellock P.K., Maj M.H., et al. Structural magnesium front end support assembly. SAE Technical Paper, 2003.
- [109] A.A. Luo, R.C. McCune, Magnesium Front End Projects, V.S. Department of Energy, Automotive Lightweighting Materials, FY, 2008 2006 Progress Report, TMS 2008.
- [110] C. Blawert, N. Hort, K.U Kainer, Trans.- Indian Inst. Met. 57 (4) (2004) 397-408.
- [111] S. Logan, A. Kizyma, C. Patterson, et al., SAE Trans. (2006) 469-486.
- [112] F. Moll, M. Mekkaoui, S. Schumann, et al., Application of Mg sheets in car body structures, in: Magnesium: Proceedings of the 6th International Conference Magnesium Alloys and Their Applications, Wiley-VCH Verlag GmbH & Co. KGaA, Weinheim, FRG, 2003, pp. 936-942.
- [113] J.T. Carter, P.E. Krajewski, R. Verma, JOM 60 (11) (2008) 77-81.
- [114] Reuters, G.M. Tests magnesium sheet metal to make cars lighter, Oct. 2012.
- [115] A.A. Luo, A.K. Sachdev, B.R Powell, China Foundry 7 (4) (2010) 463-469.
- [116] A.K. Rodriguez, G. Ayoub, G. Kridli, et al., Phys. Proc. 55 (2014) 46-52.
- [117] W.H. Zhu, Z.X. Zheng, J.Z. Feng, et al., Adv. Mater. Res. 118 (2010) 930-934.
- [118] M. Gobbi, G. MASTINU, F. Ballo, et al., SAE Int. J. Passeng. Cars-Mech. Syst. 8 (1) (2015) 119-127.
- [119] M. Graf, M. Ullmann, R. Kawalla, Proc. Eng. 81 (2014) 546-551.
- [120] Wang J., Chen H. A preparation method for wheel hub production by positive and negative extrusion: CN102581053A. 2012.
- [121] P.H. Fu, L.M. Peng, W.J. Ding, Chin. J. Eng. Sci. 20 (1) (2018) 84-89.
- [122] Y.H. Peng, D.Y. Li, Y.C. Wang, et al., Mater. Sci. Forum. 488 (2005) 393-396.
- [123] R. Shang, W. Altenhof, H. Hu, et al., SAE Int. J. Mater. Manuf. 1 (1) (2009) 9-15.
- [124] G.F. Quan, S.D Liu, Ordnance Mater. Sci. Eng. 35 (04) (2012) 26-31.
- [125] W. Qiang, Z. Zhang, X. Zhang, et al., Trans. Nonferrous Met. Soc. China 20 (2010) s599-s603.
- [126] W. Qiang, Z.M. Zhang, X. Zhang, et al., Trans. Nonferrous Met. Soc. China 18 (2008) s205-s208.
- [127] Nayak S., Garg A.K., Chaturvedi M., et al. Performance evaluation of PU over-molded thermoplastic steering wheel. SAE Technical Paper, 2010.
- [128] Garg A., Surisetty G., Chaturvedi M., et al. High performance thermoplastic steering wheel. SAE Technical Paper, 2009.
- [129] W. Ames, W. Altenhof, SAE Trans. (2000) 390-399.
- [130] P.L. Mao, L.I.U. Zheng, C.Y. Wang, et al., Trans. Nonferrous Met. Soc. China 18 (2008) s218-s222.
- [131] D.Y Kwak, A study on performance evaluation and improvement of steering wheel with Mg die casting core, in: Transactions of Korean Society of Automotive Engineers Annual Autumn Conference, 2003, pp. 1185-1190.
- [132] W.J. Altenhof, W. Ames, P.R. Frise, et al., Int. J. Crashworth. 8 (3) (2003) 237-246.
- [133] J. Liao, Adv. Mat. Res. 328 (2011) 213-219.
- [134] K.J. Kim, H.J. Kim, C.Y Jeong, Mater. Res. Innov. 18 (sup2) (2014) S2-666-S2-672.
- [135] Wickberg A., Ericsson R. Magnesium in the Volvo LCP 2000. SAE Technical Paper, 1985.
- [136] Aragones J., Goundan K., Kolp S., et al. Development of the 2006 Corvette Z06 structural cast magnesium crossmember. SAE Technical Paper, 2005.
- [137] N. Li, R. Osborne, B. Cox, et al., SAE Trans. (2005) 79–88.
- [138] Chen X., Wagner D., Heath G., et al. Cast magnesium subframe development-bolt load retention. SAE Technical Paper, 2021.
- [139] H. Friedrich, S. Schumann, J. Mater. Process. Technol. 117 (3) (2001) 276-281.
- [140] F.H. Froes, D. Eliezer, E. Aghion, JOM 50 (9) (1998) 30-34.
- [141] B.R. Powell, Magnesium Powertrain Cast Components, U.S. Department of Energy, Washington, D.C, April 2009 Published in FY2008 Annual Progress Report for Automotive Lightweighting Materials.
- [142] B.R. Powell, L.J. Ouimet, J.E. Allison, et al., SAE Trans. (2004) 250-259.
- [143] J. Greiner, C. Doerr, H. Nauerz, et al., Comfort Fuel Econ. SAE Trans. (2004) 283-293.
- [144] Bavarian Motor Works (2007) Magnesium fosters rebirth of an automotive engine. International magnesium association: the global voice for magnesium (May):1-3.
- [145] Hoeschl M., Wagener W., Wolf J. BMW's magnesium-aluminium composite crankcase, state-of-the-art light metal casting and manufacturing. SAE Technical Paper, 2006.
- [146] H.W. Shin, Y.J Chung, Trans. Korean Soc. Autom. Eng. 17 (2) (2009) 141-149.
- [147] H.W. Shin, Int. J. Precis. Eng. Manuf. 13 (11) (2012) 2011–2016.
- [148] M. Pekguleryuz, P. Labelle, D. Argo, Magnesium die casting alloy AJ62x with superior creep resistance, ductility and die castability, SAE 2003 World Congress & Exhibition, 2001 2003-01-0190.
- [149] Hines J.A., McCune R.C., Allison J.E., et al. The USAMP magnesium powertrain cast components project. SAE Technical Paper, 2006.
- [150] S. Mantovani, G.A. Campo, A. Ferrari, Proc. Inst. Mech. Eng., Part C: J. Mech. Eng. Sci. 235 (10) (2021) 1703-1723.
- [151] Y. Kuwano, Y. Sakamoto, A. Uno, et al., Honda R D Tech. Rev. 20 (1) (2008) 46.
- [152] S.F. Wang, W.W. Hu, Z.H. Gao, et al., The application of magnesium alloy in automotive seat design, in: Applied Mechanics and Materials, 395, Trans Tech Publications Ltd, 2013, pp. 266-270.
- [153] J.M Willekens, Magnesium seat-frames: history and evaluation, in: Proceedings of the Third International Magnesium Conference, 1996, pp. 207-211.
- [154] Sikora S.P., Beeh E., Jäger A., et al. Concepts for manufacturing a seat backrest structure dominated by an extruded magnesium alloy. SAE Technical Paper, 2021.
- [155] Abate M., Willman M. Use of cast magnesium back frames in automotive seating. SAE Technical Paper, 2005.
- [156] Hector B., Heiss W. Magnesium die-castings as structural members in the integral seat of the new mercedes-benz roadster. SAE Technical Paper, 1990.
- [157] P. Koltun, A. Tharumarajah, Mater. Sci. Forum 618 (2009) 17-20.
- [158] B. Liu, Z.C. Qiu, Q. Yang, et al., Mater. Sci. Forum 877 (2017) 668-673.
- [159] W.J. Joost, P.E Krajewski, Scr. Mater. 128 (2017) 107-112.
- [160] I.J Polmear, Mater. Sci. Technol. 10 (1) (1994) 1-16.
- [161] E. Baril, P. Labelle, M. Pekguleryuz, JOM 55 (11) (2003) 34-39.
- [162] E. Aghion, B. Bronfin, F. Von Buch, et al., JOM 55 (11) (2003) 30-33.
- [163] S. Novotny, M. Geiger, J. Mater. Process. Technol. 138 (1-3) (2003) 594-599.
- [164] Liu B., Zhan Z., Zhao X., et al. A research on the body-in-white (BIW) weight reduction at the conceptual design phase. SAE Technical Paper, 2014.
- [165] B. Liu, J. Yang, Z. Zhan, et al., SAE Int. J. Mater. Manuf. 8 (3) (2015) 616-622.
- [166] B. Liu, C. Yan, H. Wang, Proc. Inst. Mech. Eng., Part B: J. Eng. Manuf. 234 (3) (2020) 621-628.
- [167] Y.K. Gao, D.W. Gao, Y.H Gao, Adv. Mat. Res. 156 (2011) 245-251.
- [168] S. Chandra, M. Maeder, J. Bienert, et al., Mech. Syst. Signal. Process. 187 (2023) 109945.
- [169] G. Dao, S. Youhong, L. Guanyu, et al., Mech. Syst. Signal. Process. 185 (2023) 109768.
- [170] G.G. Wang, J. Bos, J. Magn. Alloys 6 (2) (2018) 114-120.
- [171] M.H. Yoo, J.H. Song, J.H. Oh, et al., Robot Comput. Integr. Manuf. 55 (2019) 154-159.
- [172] B. Liu, P. Liu, Z.T Zhu, Adv. Mater. Res. 1063 (2015) 207-210.
- [173] G. Li, W. Jiang, Z. Fan, et al., Int. J. Adv. Manuf. Technol. 91 (1) (2017) 1355-1368.
- [174] B. Dybowski, R. Jarosz, A. Kiełbus, Solid State Phenom. 197 (2013) 125-130.
- [175] Y.K. Shen, J.J. Liu, C.T. Chang, et al., Int. Commun. Heat Mass Transf. 29 (1) (2002) 97-105.
- [176] L. Bichler, C. Ravindran, Mater. Sci. Forum. 638 (2010) 1591-1595.
- [177] F.W. Bach, M. Rodman, A. Rossberg, Adv. Mater. Res. 6 (2005) 665-672.
- [178] K. Strobel, M.A. Easton, V. Tyagi, et al., Int. J. Cast Met. Res. 23 (2) (2010) 81-91.
- [179] S. Das, A. Dubreuil, L. Bushi, et al., A Life Cycle Assessment of a Magnesium Automotive Front End, Oak Ridge National Lab. (ORNL), Oak Ridge, TN (United States), 2009.
- [180] S.V.S. Prasad, S.B. Prasad, K. Verma, et al., J. Magn. Alloys (2021).
- [181] H. Haferkamp, R. Boehm, U. Holzkamp, et al., Mater. Trans. 42 (7) (2001) 1160-1166.
- [182] P.S. Sreejith, B.K.A Ngoi, J. Mater. Process. Technol. 101 (1-3) (2000) 287-291.
- [183] S. Agarwal, J. Curtin, B. Duffy, et al., Mater. Sci. Eng.: C 68 (2016) 948-963.
- [184] K.S. Tseng, G.L. Sheu, S.T Huang, Mater. Sci. Forum. 488 (2005) 49-52.
- [185] J. Song, J. She, D. Chen, et al., J. Magn. Alloys 8 (1) (2020) 1-41.
- [186] R. Shah, V. Mittal, E. Matsil, et al., Adv. Mech. Eng. 13 (3) (2021) 16878140211003398.
9. 著作権:
- この資料は、Bo Liu, Jian Yang, Xiaoyu Zhang, Qin Yang, Jinsheng Zhang, Xiaoqing Liの論文:「Development and application of magnesium alloy parts for automotive OEMs: A review」に基づいています。
- 論文ソース: https://doi.org/10.1016/j.jma.2022.12.015
この資料は上記の論文に基づいて要約されたものであり、商業目的での無断使用は禁止されています。
Copyright © 2025 CASTMAN. All rights reserved.