この論文概要は、Z. Fan、S. Ji、G. Liu 著の論文「Development of the Rheo-Diecasting Process for Mg-Alloys」(Materials Science Forum Vols. 488-489 (2005), pp. 405-412)に基づいて作成されています。
1. 概要:
- タイトル: マグネシウム合金のレオダイカストプロセスの開発 (Development of the Rheo-Diecasting Process for Mg-Alloys)
- 著者: Z. Fan, S. Ji, G. Liu
- 発表年: 2005年
- 掲載ジャーナル/学会誌: Materials Science Forum Vols. 488-489
- キーワード: セミソリッド (Semisolid)、レオダイカスト (Rheo-diecasting)、微細組織 (Microstructure)、機械的特性 (Mechanical properties)
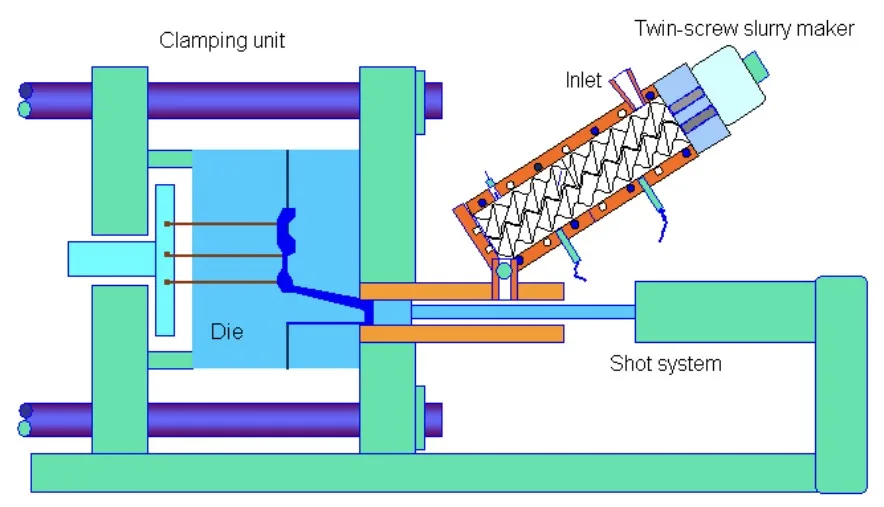
2. 研究背景:
- 研究テーマの社会的/学術的背景:
- 環境意識の高まりとCO2排出規制の強化により、自動車産業において車両重量の削減と燃費の向上がますます重要になっています。
- マグネシウム合金は、最も軽量な構造材料として、自動車産業におけるこれらの目標達成に非常に適しています。
- 近年、自動車産業におけるマグネシウムの使用量は大幅に増加しており、この傾向は今後も継続し、航空宇宙、エレクトロニクス、ヘルスケアなどの分野にも拡大すると予想されます。
- 現在、これらの用途のほとんどは高圧ダイカスト (HPDC) によって実現されており、主にAZ91やAM60などの合金に限定されています。
- 既存研究の限界:
- マグネシウム合金のさらなる用途拡大は、既存の加工技術、特にHPDCの限界、すなわち高品質で低コストの部品製造と、より高い動作温度を持つ新しい合金の使用を可能にすることにおいて制約を受けています。
- 従来のHPDCプロセスは、高度なマグネシウム合金用途に望ましい微細組織と機械的特性を達成するために最適ではない可能性があります。
- 研究の必要性:
- HPDCの限界を克服できるマグネシウム合金の新しい加工技術の開発が必要です。
- 特に、高品質で費用対効果の高い、性能特性が向上したマグネシウム部品を製造するための新しいセミソリッド加工技術が求められています。
- このような技術の開発は、特に高い安全性と構造的完全性が要求される厳しい用途において、様々な産業におけるマグネシウム合金のより広範な採用を促進するでしょう。
3. 研究目的と研究課題:
- 研究目的:
- マグネシウム合金用の新しいセミソリッド加工技術であるレオダイカスト (RDC) プロセスを開発すること。
- AZ91Dマグネシウム合金を用いてレオダイカストプロセスを最適化すること。
- レオダイカストAZ91Dマグネシウム合金の微細組織と機械的特性を評価し、他の加工方法で製造されたものと比較すること。
- 主な研究課題:
- 層状金型充填と微細で均一な微細組織を達成するための、セミソリッド金属 (SSM) 加工に理想的なセミソリッドスラリーの特性は何か?
- セミソリッド加工における凝固中の効果的な核生成を促進し、球状成長を促進するために必要な条件は何か?
- ツインスクリュースラリーメーカーを利用したレオダイカスト (RDC) プロセスは、従来のHPDCや他のセミソリッド加工技術と比較して、AZ91Dマグネシウム合金の微細組織にどのような影響を与えるか?
- レオダイカストAZ91Dマグネシウム合金の機械的特性はどのようなものか、また他の加工方法で達成された特性と比較してどうか?
- 研究仮説:
- 凝固中の均一な温度と化学組成、高いせん断速度、および高い乱流強度によって核生成と成長プロセスを制御することにより、理想的なセミソリッドスラリーを製造できる。
- ツインスクリュースラリーメーカーに基づくレオダイカスト (RDC) プロセスは、気孔率がほぼゼロで、微細で均一な微細組織を持つAZ91Dマグネシウム合金部品を製造する。
- レオダイカストAZ91Dマグネシウム合金部品は、従来のHPDCや他のセミソリッド加工技術で製造された部品と比較して、機械的特性、特に延性が向上する。
4. 研究方法
- 研究デザイン:
- 本研究では、実験的調査アプローチと強制対流下での凝固の理論的解析を組み合わせました。
- レオダイカスト (RDC) プロセスの開発と実装が含まれていました。
- レオダイカストAZ91Dマグネシウム合金試料の微細組織特性評価と機械的特性評価を実施しました。
- 文献で報告されている他の加工技術で製造された試料との比較分析を実施しました。
- データ収集方法:
- 材料: MEL (マンチェスター、英国) から供給されたAZ91D (Mg-8.8Al-0.67Zn-0.22Mn-0.03Si, wt.%) マグネシウム合金。
- レオダイカストプロセス: 新しいレオダイカスト (RDC) プロセスを開発し、ツインスクリュースラリーメーカーと従来のHPDCマシンを組み合わせました。
- AZ91D合金インゴットをN2+0.5vol.% SF6ガス混合雰囲気下で675℃で溶解し、630℃でスラリーメーカーに供給しました。
- スラリーメーカーの温度範囲は、0〜0.5の固相率範囲に対応していました。
- 280トンのコールドチャンバーダイカストマシンを鋳造に使用しました。
- 微細組織観察: 光学顕微鏡および走査型電子顕微鏡 (SEM) を使用して、レオダイカスト試料の微細組織を特性評価しました。詳細な微細組織観察にはEDX分析も使用しました。
- 機械的特性試験: 特別に製造された金型を使用して鋳造された標準的な引張試験片で引張試験を実施し、レオダイカストAZ91D合金の機械的特性を評価しました。
- 分析方法:
- 微細組織分析: 顕微鏡写真の定性的および定量的な分析により、気孔率、結晶粒径、初晶粒子と共晶相の形態、および微細組織の均一性を評価しました。
- 機械的特性分析: 引張試験データから、耐力、引張強度、伸びを決定しました。
- 比較分析: レオダイカストAZ91Dの微細組織と機械的特性を、HPDC、チクソキャスティング、チクソモールディング、およびニューレオキャスティング (NRC) によって加工されたAZ91D合金について文献で報告されているものと比較しました。
- 研究対象と範囲:
- 本研究は、マグネシウム合金、特にAZ91D合金のレオダイカスト (RDC) プロセスの開発と最適化に焦点を当てました。
- 範囲には、RDCプロセスパラメータがAZ91D合金の微細組織と機械的特性に及ぼす影響の調査が含まれていました。
- RDCプロセスの信頼性と一貫性を評価するために、部品製造トライアルを実施しました。
5. 主な研究結果:
- 主な研究結果:
- レオダイカスト (RDC) プロセスは、従来のHPDCや他のセミソリッド加工技術と比較して、微細組織と機械的特性が大幅に向上したAZ91Dマグネシウム合金試料の製造に成功しました。
- レオダイカスト試料は、気孔率がほぼゼロ (0.5 vol.% を大幅に下回る) でした。
- 微細組織は試料全体で微細かつ均一であり、偏析は観察されませんでした。
- 初晶粒子は微細 (約50µm)、球状、かつ均一に分散していました。
- 酸化物粒子は微細 (数ミクロン)、球状、良好に分散し、均一に分布していました。
- 機械的特性は大幅に向上し、特に延性はHPDC加工試料の約2倍でした。
- 統計的/定性的分析結果:
- 気孔率: レオダイカスト試料の気孔率は一貫して0.5 vol.% を大幅に下回り、気孔はまれにしか観察されず、時折サイズが小さい (ミクロンレベル) 気孔が観察されました。凝固収縮による微小気孔は大幅に減少または排除されました。
- 微細組織:
- 初晶粒子は試料全体に均一に分布していました。
- 鋳造品全体にわたって化学的偏析は観察されませんでした。
- SSMスラリー中の残りの液体は、高い冷却速度で凝固し、非常に微細なα相 (<10µm) を生成しました。
- 共晶凝固によって形成されたMg17Al12 β相は不規則な形態を示し、結晶粒界に位置し、共晶成長の証拠はなく、離婚共晶凝固を示唆していました。
- 機械的特性: 表1は、機械的特性の比較を示しています。 表 1. 異なる加工技術で製造されたAZ91D合金の機械的特性 プロセス 耐力 (MPa) 引張強度 (MPa) 伸び (%) 参考文献 HPDC 146 212 3.3 [10] チクソキャスティング 134 223 3.6 [11] チクソモールディング -- 150-241 3-5 [12] ニューレオキャスティング (NRC) -- 230 5.5 [13] レオダイカスト (RDC) 145 248 8.9 本研究
- レオダイカスト (RDC) は、HPDC (3.3%)、チクソキャスティング (3.6%)、およびチクソモールディング (3-5%) と比較して、大幅に高い伸び (8.9%) を示しています。引張強度もHPDCおよびチクソキャスティングと比較して向上しています。
- データ解釈:
- RDCプロセスによって達成された微細で均一な結晶粒、気孔率の低減、および良好に分散した酸化物粒子を特徴とする改善された微細組織は、機械的特性の向上、特に延性の大幅な増加に直接的に寄与しています。
- ツインスクリュースラリーメーカーは、高いせん断速度と乱流を通じて核生成と球状成長を効果的に促進し、望ましいセミソリッドスラリー特性と、その後のレオダイカスト部品の微細組織の微細化につながります。
- RDCにおける層状金型充填は、ガス巻き込みを最小限に抑え、低い気孔率レベルに貢献しています。
- 図表リスト:
- 図 1. レオダイカスト (RDC) プロセスの概略図。 (Schematic illustration of the rheo-diecasting (RDC) process.)
- 図 2. 金型充填中の層状流フロントを示す写真と顕微鏡写真。 (Photograph and micrographs showing the laminar flow front during mould filling.)
- 図 3. φ6引張試験棒の全断面におけるレオダイカストAZ91D合金の微細組織。 (Microstructure of the rheo-diecast AZ91D alloy through the entire cross-section of the φ6 tensile test bar.)
- 図 4. 異なる加工温度で製造されたレオダイカストAZ91D合金の微細組織。(a) 585℃; (b) 589℃; (c) 593℃; (d) 600℃。 (Microstructures of rheo-diecast AZ91D alloy produced at different processing temperatures. (a) 585°C; (b) 589°C; (c) 593°C; (d) 600°C.)
- 図 5. 残りの液体の二次凝固によって形成された初晶粒子の形態と、共晶凝固によって形成されたMg17Al12 β相の詳細な形態を示すレオダイカストAZ91D合金のSEM顕微鏡写真。 (SEM micrographs of rheo-diecast AZ91D alloy showing the morphology of primary particles formed through the secondary solidification of the remaining liquid and the detailed morphology of the Mg17Al12 β-phase formed through eutectic solidification.)
- 図 6. 異なる位置におけるレオダイカストLM24部品の微細組織を示す光学顕微鏡写真。 (Optical micrographs showing the microstructure of rheo-diecast LM24 components at different locations.)
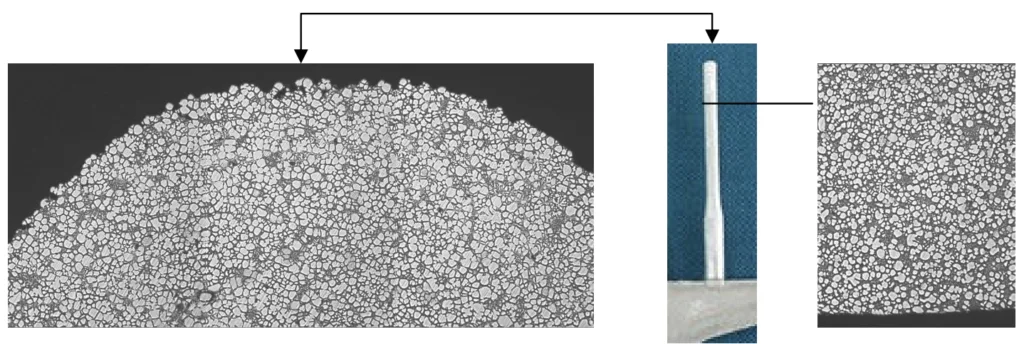

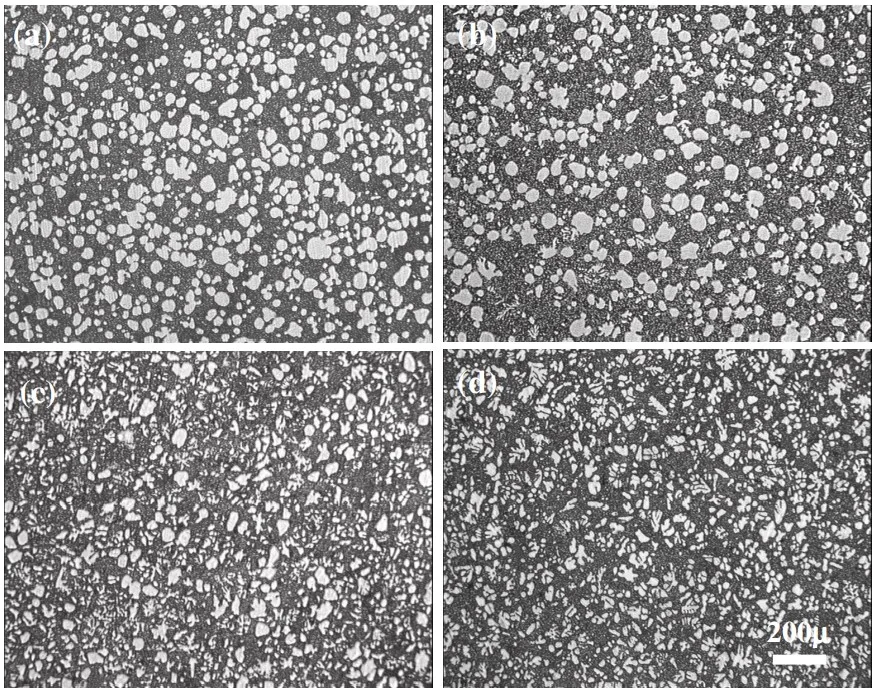


6. 結論と考察:
- 主な結果の要約:
- 本研究では、高インテグリティマグネシウム合金部品を製造するための新しいセミソリッド金属加工技術であるレオダイカスト (RDC) を開発することに成功しました。
- RDCプロセスは、セミソリッドスラリーのレオロジーと、理想的なセミソリッドスラリーを達成するための条件、すなわち凝固中の均一な温度と化学組成、高いせん断速度、および高い乱流強度の理解に基づいています。
- AZ91Dマグネシウム合金を用いた実験結果は、RDCが気孔率がほぼゼロで、微細で均一な微細組織、および大幅に向上した機械的特性、特に延性を備えた試料を製造することを示しました。
- 部品製造トライアルは、RDCプロセスの信頼性と一貫性をさらに確認しました。
- 研究の学術的意義:
- 本研究は、核生成と球状成長を促進するための重要な条件を特定することにより、SSM加工用の理想的なセミソリッドスラリーの開発に関する貴重な洞察を提供します。
- ツインスクリュースラリーメーカーがこれらの条件を達成し、レオダイカスト (RDC) プロセスの実装を成功させる上で効果的であることを示しています。
- 本研究は、セミソリッド凝固とその高度な金属加工への応用に関する基礎的な理解に貢献しています。
- 実用的な意義:
- レオダイカスト (RDC) プロセスは、高性能マグネシウム合金部品を製造するための従来のHPDCおよび他のセミソリッド加工技術に代わる、実行可能で有利な代替案を提供します。
- RDCは、特に自動車産業において、軽量化と構造的完全性が重要な、高い安全性、気密性、および高応力部品の製造に特に適しています。
- このプロセスは、生産性の向上と欠陥の削減により、スクラップ率の低下、材料歩留まりの向上、および全体的な部品製造コストの削減という潜在的な利点を提供します。
- スラリーメーカーをコールドチャンバーHPDCマシンに取り付けるだけでRDCを実装できるため、産業界での採用が現実的で魅力的になります。
- 研究の限界:
- 本研究は主にAZ91Dマグネシウム合金に焦点を当てました。他のマグネシウム合金や異なる部品形状および複雑さに対するRDCプロセスの適用性を評価し、最適化するためには、さらなる研究が必要です。
- 部品製造トライアルは実施されましたが、RDCプロセスの大量生産環境における実用的な実現可能性を完全に評価するには、さらなる産業規模での検証と費用対効果分析が必要です。
7. 今後のフォローアップ研究:
- 今後のフォローアップ研究の方向性:
- 微細組織と機械的特性をさらに向上させるためのレオダイカスト (RDC) プロセスパラメータのさらなる最適化。
- 高性能合金や高温特性が向上した合金など、より広範囲のマグネシウム合金に対するRDCプロセスの調査。
- さまざまな産業分野向けの、より大型で複雑なマグネシウム合金部品を製造するためのRDCの応用の探求。
- レオダイカストマグネシウム合金部品の熱処理応答の詳細な調査と、表面品質と寸法精度を損なうことなく機械的性能を最大化するための熱処理手順の最適化。
- さらなる探求が必要な分野:
- さまざまな使用条件下でのレオダイカストマグネシウム合金部品の長期性能と信頼性評価。
- 生産量、材料費、エネルギー消費などの要因を考慮した、従来のHPDCおよび他の競合する製造技術と比較したRDCプロセスの包括的な費用対効果分析。
- 産業環境で一貫した高品質の部品製造を保証するための、RDCプロセスの高度な制御システムと自動化の開発。
8. 参考文献:
[1] H. Fridrich, and S. Schumann: in Proc. 2nd Israeli Inter. Conf. Mg Science and Technology, Dead Sea, Israel, (2000), 9.
[2] H. Fridrich and S. Schumann: in Proc. IMA 2001 Magnesium Conf., Brussels, Belgium, (2001), 8.
[3] S. Ji, Z. Fan, G. Liu, X. Fang and S.H. Song, in in “Proc. 7th Inter. Conf. Semisolid Metal Processing", Tsukuba, Japan, Sept. 25-27, 2002, eds. Y Tsutsui et al, pp683-688
[4] J.Y. Chen and Z. Fan: Mater. Sci. Tech., 18 (2002), 237, 243, 250, 258.
[5] P.D. Lee, Private communication, Department of Materials, Imperial College, London, 2003.
[6] A Das and Z Fan, Mat. Sci. Tech., 19 (2003) 573-580.
[7] A. Das, S. Ji and Z. Fan, Acta Materialia, 50 (2002), 4571-4585.
[8] S. Ji and Z. Fan, Met. Mater. Trans. 33A (2002), 3511-3520.
[9] S. Ji, Z. Fan and M. J. Bevis: Mater. Sci. Eng., A299 (2001), 210-217
[10]C. Pitsaris, T.Abbott, C.H.J. Davies and G. Savage, in Magnesium: Proc. 6th Inter. Conf. Magnesium Alloy and Their Application, ed. By K.U. Kainer, (Weinheim, Wiley-VCH, Verlay GmbH & Co. KGaA, 2003), 694.
[11]J. Aguilar, T. Grimming and A. Bührig-Polaczek, in Magnesium: Proc. 6th Inter. Conf. Magnesium Alloy and Their Application, ed. By K.U. Kainer, (Weinheim, Wiley-VCH, Verlay GmbH & Co. KGaA, 2003), 767.
[12]F. Czerwinski, et al., Acta Materialia, 49 (2001), 1225-1235
[13]H. Kaufmann and P.J. Uggowitzer, in Magnesium Alloy and Their Application, ed. By K.U. Kainer, (Weinheim, Wiley-VCH, Verlay GmbH & Co. KGaA, 2000), 533.
9. 著作権:
*この資料は、Z. Fan, S. Ji, G. Liu の論文:「Development of the Rheo-Diecasting Process for Mg-Alloys」に基づいています。
*論文ソース: http://dx.doi.org/10.4028/www.scientific.net/MSF.488-489.405
この資料は上記の論文に基づいて要約されたものであり、商業目的での無断使用は禁止されています。
Copyright © 2025 CASTMAN. All rights reserved.