本論文概要は、学術誌「Int J Adv Manuf Technol」に掲載された論文「Development of a die design system for die casting」に基づいて作成されました。
1. 概要:
- タイトル: ダイカスト金型設計システムの開発 (Development of a die design system for die casting)
- 著者: Y. K. Woon, K. S. Lee
- 発行年: 2004年
- 発行学術誌/学会: Int J Adv Manuf Technol (International Journal of Advanced Manufacturing Technology, 国際先端製造技術ジャーナル)
- キーワード: ダイカスト (Die casting)、金型設計システム (Die design system)、フィーチャーベース (Feature-based)、制約ベース (Constraint-based)、パラメトリック設計 (Parametric design)、B-repモデル (B-rep model)
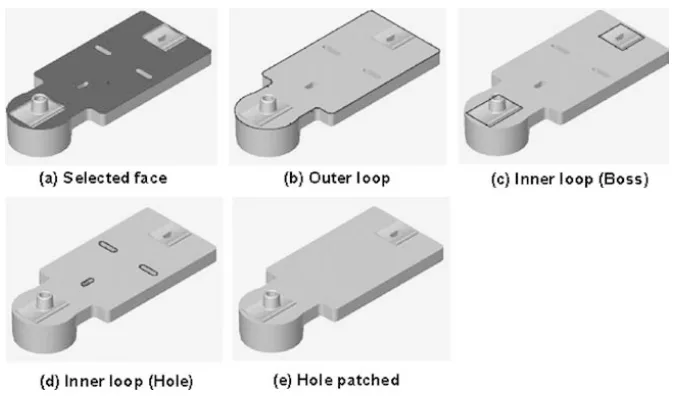
2. 研究背景:
研究テーマの背景:
ダイカストプロセスは、精密な寸法とシャープな形状の金属部品を製造するための主要な方法の一つです。ダイカスト金型の設計は、複数の段階を経るプロセスであり、本質的に多くの時間を要します。初期金型設計が許容可能なレベルに達するまでの複雑さから、反復的な修正が必要となり、設計サイクルがさらに長期化します。
既存研究の現状:
既存の研究は、個々の金型要素の自動または半自動設計、特にゲートシステムの設計に焦点が当てられてきました。P-Q²手法とフィーチャーベースのパラメトリック設計を活用したゲートシステムプロトタイプ設計や、加圧ダイカスト用のゲートおよびランナーシステム設計を専門とするDiEdiFiceのような商用アプリケーションがその例です。しかし、DiEdiFiceは、エジェクタおよびコアキャビティインサートの作成まではサポートしていません。AutoCADベースなどの既存の完全な金型設計システムは、単純な形状およびアンダーカットのない単一印象金型への適用に限定されています。シミュレーション解析を用いた金型形状およびプロセスパラメータ最適化のための統合CAD/CAEシステムの研究も進められています。IMOLDのような特殊なソフトウェアパッケージは、半自動射出成形金型設計のために存在しますが、ダイカストゲートシステムの複雑さの増加により、ダイカスト設計に直接適用することは困難です。
研究の必要性:
ダイカスト業界は、様々な金型設計段階を統合し、設計編集を容易にするアプリケーションソフトウェアから大きな恩恵を受けることができます。3D CADが金型設計にますます採用されるにつれて、視覚化を向上させ、設計修正作業を効率化するシステムの必要性が強調されています。したがって、金型設計時間を短縮するコンピュータ支援金型設計システムの開発が非常に重要です。
3. 研究目的と研究課題:
研究目的:
本研究の実質的な目的は2つあります。
(1) 様々な金型設計段階を統合するシステムを開発すること。
(2) 金型設計プロセス中およびプロセス後にダイカスト設計の編集を容易にすること。
主要な研究課題:
本研究は、ユーザーフレンドリーなダイカスト金型用コンピュータ支援設計システムを構築することに焦点を当てています。このシステムは、経験豊富な設計者と初心者設計者の両方が、製品部品モデルから効率的に金型を設計できるようにすることを目指しています。
研究仮説:
フィーチャーベースおよび制約ベースモデリング、パラメトリック設計、B-repモデルからの幾何学的/位相情報抽出技術を統合した金型設計システムは、ダイカスト金型設計プロセスの自動化、効率性、品質、費用対効果を向上させることができるという仮説を立てています。
4. 研究方法
研究設計:
本研究では、以下の手法を組み合わせたアプローチを採用しています。
(1) フィーチャーベースおよび制約ベースモデリング (Feature-based and constraint-based modelling)。
(2) パラメトリック設計 (Parametric design)。
(3) B-rep (Boundary Representation, 境界表現) モデルからの幾何学的および位相情報抽出技術 (Geometric and topological information extraction technique)。
データ収集方法:
本論文では、伝統的な意味での経験的データ収集のような特定のデータ収集方法を明示的に詳細に説明していません。しかし、プロトタイプシステムの開発と検証には、システム性能、ユーザーインタラクション、および設計結果に関連するデータが暗黙的に含まれていますが、これらのデータは論文内で正式なデータセットとして提示されていません。押しボタンハウジングのケーススタディは、システムの機能を示すデモデータの形態を提供します。
分析方法:
本論文は、金型設計システムの開発と機能デモンストレーションに焦点を当てています。分析は主に質的であり、設計段階の統合、設計編集の容易さ、金型設計タスクの自動化に対するシステムの能力を評価します。ケーススタディは、システムの実用的な応用とワークフローの実例を提供します。設計時間短縮や品質向上などの定量的な性能指標は、本論文では明示的に測定または分析されていません。
研究対象と範囲:
本研究は、一般的なダイカスト金型設計に適用可能なプロトタイプ金型設計システムの開発に焦点を当てています。システムの範囲は、キャビティインサート、コアスライド、金型ベース、ゲートシステム、エジェクタシステム、および標準部品を備えた金型設計を含みます。システムは、SolidWorks 2001プラットフォーム上でVisual C++を使用して実装されました。ケーススタディは、押しボタンハウジング金型設計へのシステムの適用を示しています。
5. 主な研究結果:
主要な研究結果:
- 7つの異なるモジュールで構成されるダイカスト用プロトタイプコンピュータ支援金型設計システムが開発されました。
- このシステムは、鋳造設計からエジェクタシステム設計まで、様々な金型設計段階を単一の環境に統合します。
- システムは、フィーチャーベースおよび制約ベースモデリング、パラメトリック設計、およびB-repモデル情報抽出を統合しています。
- システムには、スライド、ゲート要素、およびエジェクタピンなどのコンポーネント用のユーザー定義ダイカストフィーチャーライブラリが含まれています。
- パーティング面を作成するための「穴埋め (hole patching)」などのタスクアルゴリズムが、幾何学的および位相情報を使用して実装されました。
- システムアーキテクチャはモジュール式であり、プロジェクト管理、キャビティインサートビルダー、金型ベース設計、ゲートシステム構築、エジェクタシステム構築、コアスライド設計、および標準部品統合を可能にします。
- ケーススタディを通じて、キャビティインサート、コアスライド、ゲートおよびランナーシステム、金型ベース、およびエジェクタシステムを含む押しボタンハウジング用の2キャビティ金型を設計するシステムの能力を実証しました。
データ解釈:
開発されたプロトタイプシステムは、様々なダイカスト金型設計段階をまとまりのあるCAD環境に統合することが可能であることを示しています。フィーチャーベースおよび制約ベースのアプローチは、パラメトリック設計と組み合わせることで、効率的で柔軟な金型設計と修正を可能にします。モジュール式アーキテクチャとユーザー定義フィーチャーライブラリは、システムの使いやすさと様々な金型設計要件への適応性を向上させます。ケーススタディは、複雑なダイカスト金型設計におけるシステムの実用的な応用を示しています。
図のリスト:
- Fig. 1 ダイカスト金型設計システムのフローチャート (Flowchart of the die design system for die casting)
- Fig. 2 位相制約の例 - トッププレートの上面とリーダーピンの上面を整列 (Example of a topological constraint—top face of leader pin align with top face of top plate)
- Fig. 3a-e グラフィックイラストレーション:「穴埋め (hole patching)」アルゴリズム (Graphical illustration: "hole patching" algorithm)
- Fig. 4 システムアーキテクチャとメニューオプション (System architecture and menu options)
- Fig. 5 プロジェクトマネージャモジュールと新規プロジェクトインターフェース (Project manager module and the new project interface)
- Fig. 6a,b キャビティインサートビルダーモジュール。 a ボルスタビルダーインターフェース。 b ボルスタブレーカーインターフェース (Cavity insert builder module. a Bolster builder interface. b Bolster breaker interface)
- Fig. 7a,b ゲートシステムデザイナーモジュール。 a ゲートインターフェース。 b オーバーフローインターフェース (Gating system designer module. a Gates interface. b Overflows interface)
- Fig. 8a,b 金型ベースデザイナーモジュール。 a ロードN構成インターフェース。 b 厚さインターフェース (Die base designer module. a Load N configure interface. b Thickness interface)
- Fig. 9 a スライドコアデザイナーモジュール:ヘッド設計インターフェース。 b 標準部品インターフェース (Slide core designer module: head design interface. b Standard component interface)
- Fig. 10 押しボタンハウジング (Push-button housing)
- Fig. 11a-c キャビティインサートビルダー: a パーティング面ジェネレータインターフェース。 b カバーキャビティインサート。 c エジェクタキャビティインサート (Cavity insert builder: a Parting face generator interface. b Cover cavity insert. c Ejector cavity insert)
- Fig. 12 a アンダーカット形状。 b コアスライドヘッド (Undercut feature. b Core slide head)
- Fig. 13a,b コアスライドデザイナー: a ボディ設計インターフェース。 b コアスライド機構付きキャビティインサート (Core slide designer: a Body design interface. b Cavity inserts with core slides mechanism)
- Fig. 14 2キャビティレイアウト、キャビティ間距離500mm (2-cavity layout with 500 mm distance between cavity inserts)
- Fig. 15 a ゲートシステム - ビスケット;ゲート;ランナー;オーバーフロー。 b 拡大されたキャビティインサートビュー (Gating system-biscuit; gate; runner; overflow. b Enlarged view of cavity insert)
- Fig. 16 DME金型ベースDシリーズ (DME Die base D series)
- Fig. 17 a 一般的なエジェクタピン。 b 強化エジェクタピン (Typical ejector pin. b Reinforced ejector pin)
- Fig. 18 a エジェクタシステムコンストラクタインターフェース。 b 2種類の10個のエジェクタピンを備えたキャビティインサート (Ejector system constructor interface. b Cavity insert with the 10 ejector pins of two different types)
- Fig. 19 提案されたシステムを使用した押しボタンケースのダイカスト用金型設計 (Die design for die casting of the push button casing using the proposed system)
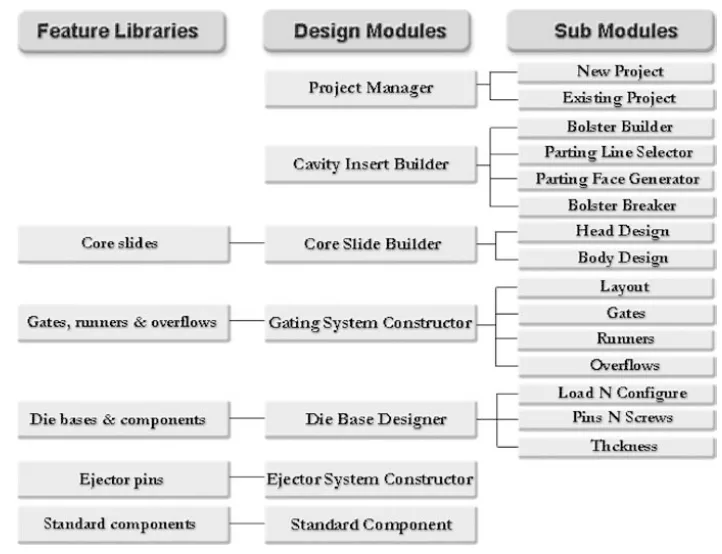

6. 結論:
主な結果の要約:
本研究では、ダイカスト用のプロトタイプコンピュータ支援金型設計システムを首尾よく開発しました。このシステムは、フィーチャーベースおよび制約ベースモデリング、パラメトリック設計、およびB-repモデル情報を統合して、金型設計プロセスを自動化および効率化します。初期プロジェクト設定からエジェクタシステム設計まで、金型設計のすべての重要な段階を網羅するモジュールと、カスタマイズ可能なフィーチャーライブラリが含まれています。ケーススタディでは、複雑なダイカスト金型の設計におけるシステムの実用的な応用を実証しました。
研究の学術的意義:
本研究は、多段階設計を統合し、高度なCAD技術を活用する包括的なシステムを提示することにより、コンピュータ支援金型設計の分野に貢献します。フィーチャーベースおよび制約ベースモデリングの適用と、幾何学的および位相情報抽出は、複雑な金型設計タスクを自動化するための堅牢なフレームワークを提供します。モジュール式アーキテクチャとカスタマイズ可能なフィーチャーライブラリは、ダイカスト金型設計のための柔軟で適応可能なプラットフォームを提供します。
実用的な意義:
開発された金型設計システムは、ダイカスト業界に大きな実用的な意義をもたらします。設計段階を統合し、設計修正作業を容易にすることで、システムは金型設計リードタイムを大幅に短縮し、設計品質を向上させ、設計コストを削減する可能性を秘めています。ユーザーフレンドリーなインターフェースとモジュール式設計により、システムは経験豊富な金型設計者と初心者金型設計者の両方がアクセスできるようになり、金型設計ワークフローの生産性と効率性が向上します。
研究の限界
プロトタイプシステムに含まれるフィーチャーライブラリは網羅的ではなく、より広範なダイカスト部品および設計シナリオを網羅するために、さらなる拡張が必要です。さらに、現在のシステムには、ダイカスト金型設計の重要な側面である冷却システム設計モジュールが組み込まれていません。システムの性能は単一のケーススタディを通じて実証されており、システムの堅牢性と一般的な適用性を完全に評価するには、多様で複雑な金型設計による追加の検証が必要です。設計時間短縮と品質向上に関する定量的な指標は、正式には評価されていません。
7. 今後のフォローアップ研究:
- 今後の研究の方向性
今後の研究の方向性には、以下が含まれます。- より広範なダイカスト部品および設計バリエーションを網羅するようにフィーチャーライブラリを拡張すること。
- 冷却システム設計モジュールを開発し、システムに統合すること。
- キャビティ充填時間解析、ベント解析、およびゲートシステム最適化のための計算能力をシステムに強化すること。
- 設計時間短縮、品質向上、およびシステムの堅牢性を定量化するために、多様で複雑な金型設計を使用して包括的な性能評価を実施すること。
- さらなる探求が必要な領域
さらなる探求が必要な領域は、以下のようなものがあります。- プロセスシミュレーションと設計最適化のためのCAE解析ツールをシステム内に統合すること。
- 特に複雑な形状に対する自動パーティングラインおよびパーティング面生成のための、より高度なアルゴリズムを開発すること。
- 金型設計プロセスをさらに自動化および最適化するための、知識ベースエンジニアリングの原則と設計ルールを組み込むこと。
- ユーザーエクスペリエンスとシステムの適応性を向上させるための、ユーザーインターフェースの機能強化とカスタマイズオプションを開発すること。
8. 参考文献:
- [1] Wu SH, Lee KS, Fuh JY (2002) Feature-based parametric design of a gating system for a die-casting die. Int J Adv Manuf Technol 19:821-829
- [2] http://www.diedifice.com
- [3] Choi JC, Kwon TH, Park JH, Kim JH, Kim CH (2002) A study on development of a die design system for die-casting. Int J Adv Manuf Technol 20:1-8
- [4] Zhang WS, Xiong SM, Liu BC (1997) Study on a CAD/CAE system of die casting. J Mater Process Tech 63:707-711
- [5] Lee KS, Fuh JYH, Zhang YF, Nee AYC, Li Z (1997) IMOLD: An intelligent plastic injection mold design and assembly system. In: Proceedings of the 4th international conference on die and mold technology, 4-16 June 1997, Kuala Lumpur, Malaysia, pp 30-37
- [6] Shimizu S, Numao M (1997) Constraint-based design for 3D shapes. Artif Intell 91:51-69
- [7] Roller D (1991) An approach to computer-aided parametric design. Comput Aided Des 23(5):385-391
- [8] Anderl R (1994) Parametrics for product modelling. J. Hoschek and Teubner, Stuttgart
- [9] Herman EA (1996) Gating die casting dies. North American Die Casting Association
- [10] Chen YM, Wei CL (1997) Computer-aided feature-based design for net shape manufacturing. Comput Integr Manuf Syst 10(2):147-164
- [11] Hoffmann CM, Joan-Arinyo R (1998) On user-defined features. Comput Aided Des 30(5):321-332
9. 著作権:
- 本資料は "Y. K. Woon K. S. Lee" の論文: "Development of a die design system for die casting" に基づいています。
- 論文ソース: DOI 10.1007/s00170-003-1754-3
本資料は上記の論文に基づいて要約されたものであり、商業目的での無断使用は禁止されています。
Copyright © 2025 CASTMAN. All rights reserved.