agnesium casting technology for structural applications
- 研究の主要目的: 本研究の主要目的は、マグネシウム合金の溶解および鋳造プロセスを網羅的に概観し、特に自動車産業に焦点を当てた構造用マグネシウム鋳造の過去の進歩、現状、そして将来の可能性を検討することです。関連する技術的課題についても議論します。世界的なエネルギー需要の増加、環境保護への取り組み、政府規制の強化により、今後数十年間で軽量マグネシウム鋳造の応用が促進されることが予想されます。
- 主要な方法論: 本研究は、マグネシウム合金の溶解と鋳造プロセスに関する文献調査と分析を通じて行われます。マグネシウム鋳造技術の過去の進歩、現在の技術、自動車、航空宇宙、電動工具産業における構造的応用、技術的課題、そして機会を検討します。
- 主要な結果: 本研究は、様々なマグネシウム鋳造プロセス(高圧ダイカスト、低圧ダイカスト、真空補助ダイカスト、超真空ダイカスト、圧縮鋳造、消失泡鋳造、アブレーション鋳造、半固体鋳造など)の概要と、特に自動車産業におけるマグネシウムの構造的応用に関する詳細な分析を提供します。マグネシウム鋳造における技術的課題(多孔性、耐食性、疲労強度など)を議論し、これらの課題に対処するための代替鋳造プロセス(真空補助ダイカスト、超真空ダイカストなど)を提案します。統合計算材料工学(ICME)ツールの開発により、構造用途におけるマグネシウム鋳造の応用が加速されると予想されます。
![Fig. 19. Magnesium powertrain components from the USCAR magnesium powertrain cast components project; (a) LPDC cylinder block, (b) Thixomolded front engine cover, (c) HPDC oil pan and (d) HPDC rear seal carrier [54].](https://castman.co.kr/wp-content/uploads/image-108-png.webp)
研究者情報
- 所属機関: 論文には著者の所属機関が明確に記載されていません。
- 著者名: Alan A. Luo
- 主要な研究分野: マグネシウム鋳造技術
研究の背景と目的
- 研究が必要な産業的背景: 自動車、航空宇宙、電動工具産業など、様々な産業分野における軽量材料の需要増加。
- 具体的な技術的問題と課題: マグネシウム合金鋳造における技術的課題(高い多孔性、耐食性の低さ、疲労強度の不足など)。従来の保護ガス(例:SF6)の使用に伴う環境規制の問題。
- 研究目標: マグネシウム合金の溶解と鋳造プロセスを網羅的にレビューし、様々な鋳造方法を分析し、自動車産業を中心に構造用マグネシウム鋳造の過去の進歩と現状を分析し、技術的課題に対する解決策と将来展望を示すこと。
論文の主要な目標と研究内容
- 論文の主要な目標と研究内容: マグネシウム合金鋳造技術全般、特に自動車産業における構造的応用への重点を置いた包括的で体系的なレビュー。
- 問題点: マグネシウム鋳造における多孔性、耐食性の低さ、疲労強度の不足といった技術的問題と、SF6の使用に関連する環境規制の問題。
- 問題解決のための段階的アプローチ: 本研究は、以下の段階的なアプローチで問題に取り組みます。
- 高圧ダイカスト、低圧ダイカスト、真空補助ダイカスト、超真空ダイカスト、圧縮鋳造、消失泡鋳造、アブレーション鋳造、半固体鋳造など、様々なマグネシウム鋳造方法を紹介し、それぞれの特性、利点、欠点を分析します。
- 各鋳造方法の特徴と適用分野を、自動車産業を中心に説明します。
- マグネシウム鋳造における技術的課題(多孔性、耐食性、疲労強度)を詳細に分析します。
- 多孔性を低減させる真空補助ダイカスト、超真空ダイカストなどの代替鋳造プロセスと、耐食性を向上させるための表面処理技術を提案します。
- 統合計算材料工学(ICME)ツールの活用によるマグネシウム鋳造技術の進歩の展望を示します。
- 主要な図表: 論文には、マグネシウム鋳造プロセス、設備、そして結果として得られた部品の様々な側面を示す多数の図表が含まれています。これらの図表は、論文で議論されているプロセスと結果を理解するために不可欠です。(各図表のキャプションを参照)
![Fig. 1. Cross section of a stationary fuel-fired furnace used for the open crucible melting of magnesium alloys [2].](https://castman.co.kr/wp-content/uploads/image-90-png.webp)
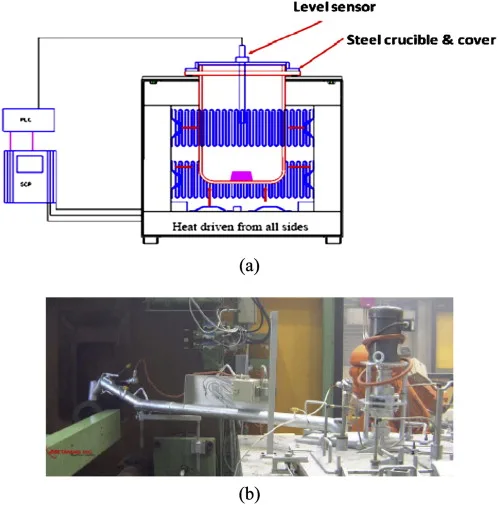
![Fig. 3. Schematics of hot chamber die casting [8].](https://castman.co.kr/wp-content/uploads/image-92-png.webp)
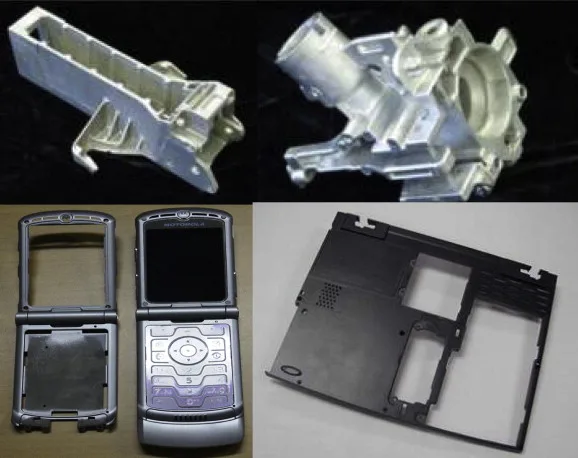
![Fig. 5. Schematics of cold chamber die casting [8].](https://castman.co.kr/wp-content/uploads/image-94-png.webp)

![Fig. 7. Gibbs vertical vacuum assisted die casting process (Courtesy of Gibbs Die Casting, Henderson, KY, USA [11]).](https://castman.co.kr/wp-content/uploads/image-96-png.webp)
![Fig. 8. A schematic diagram of a typical low pressure casting machine [17].](https://castman.co.kr/wp-content/uploads/image-97-png.webp)
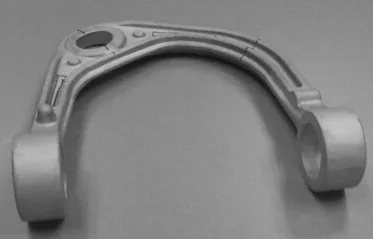
![Fig. 10. A schematic diagram of a Thixomolding machine [21].](https://castman.co.kr/wp-content/uploads/image-99-png.webp)
![Fig. 11. Schematic illustrating direct squeeze casting process operations: (a) melt into die cavity; (b) close tooling, solidify melt under pressure; and (c) eject casting [8].](https://castman.co.kr/wp-content/uploads/image-100-png.webp)
![Fig. 12. Schematic illustrating metal flow in (a) conventional die casting; and (b) indirect squeeze casting process [8].](https://castman.co.kr/wp-content/uploads/image-101-png.webp)
![Fig. 13. Ablation casting process for aluminum and magnesium casting [26].](https://castman.co.kr/wp-content/uploads/image-102-png.webp)
![Fig. 14. Pratt & Whitney F119 auxiliary casing in ELEKTRON WE43 alloy [37].](https://castman.co.kr/wp-content/uploads/image-103-png.webp)
![Fig. 15. Rolls Royce tray in ELEKTRON ZRE1 alloy [37].](https://castman.co.kr/wp-content/uploads/image-104-png.webp)
![Fig. 16. HPDC magnesium casting Lincoln MKT liftgate inner (photo courtesy of Meridian Lightweight Technologies) [49].](https://castman.co.kr/wp-content/uploads/image-111-png.webp)
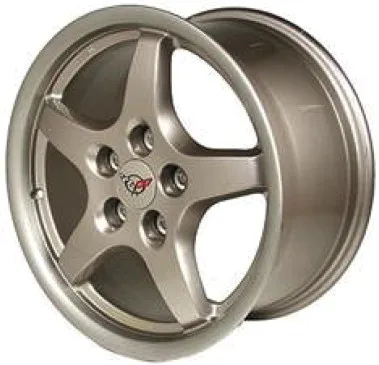
![Fig. 18. The BMW composite engine block showing a cutaway of the magnesium exterior revealing the aluminum interior [35].](https://castman.co.kr/wp-content/uploads/image-109-png.webp)
![Fig. 19. Magnesium powertrain components from the USCAR magnesium powertrain cast components project; (a) LPDC cylinder block, (b) Thixomolded front engine cover, (c) HPDC oil pan and (d) HPDC rear seal carrier [54].](https://castman.co.kr/wp-content/uploads/image-108-png.webp)
![Fig. 20. Aluminum isolator locations for Chevrolet Corvette Z06 magnesium cradle (bottom & top views) [50].](https://castman.co.kr/wp-content/uploads/image-107-png.webp)
![Fig. 21. USCAR demo structure build using (a) FSLW (friction stir linear welding); and (b) LSPR (laser-assisted self-pierce rivet) joining processes [67].](https://castman.co.kr/wp-content/uploads/image-106-png.webp)
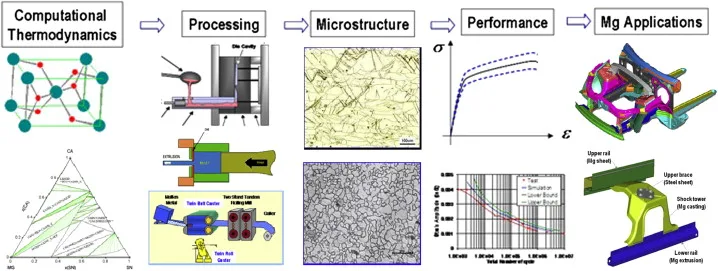
結果と成果
- 定量的結果: 本論文では、寸法公差、最小肉厚、鋳造/成形サイクル時間、型寿命、様々なマグネシウム合金と鋳造プロセスにおける引張特性(降伏強度、引張強度、伸びなど)など、多くの定量的データを示しています。(表1、表3、表4、表5を参照)
- 定性的結果: マグネシウム鋳造技術の発展過程、様々な産業(自動車、航空宇宙、電動工具など)における現在の応用事例、技術的課題、課題に対する解決策、将来展望についての詳細な定性的分析を提供しています。
- 技術的成果: 多孔性の低減、耐食性の向上、疲労強度の改善を目的とした技術的解決策を提案しています。統合計算材料工学(ICME)ツールの開発によるマグネシウム鋳造技術の発展についても展望を示しています。
著作権と参考文献
この資料は、Alan A. Luoによる論文「Magnesium casting technology for structural applications」に基づいて作成されました。
論文出典:https://doi.org/10.1016/j.jma.2013.02.002
この資料は上記の論文に基づいて要約されており、許可なく商業目的で使用することはできません。
References
- [1]A.A. Luo, K. SadayappanTechnology for Magnesium CastingsAmerican Foundry Society, Schaumburg, IL (2011)pp. 29–47Google Scholar
- [2]M.M. Avedesian, H. BakerMagnesium and Magnesium AlloysASM International, Materials Park, OH (1999)Google Scholar
- [3]J.W. Freuling, J.D. HanawaltTransactions of the American Foundrymen's Society, 77 (1969), pp. 159-164
- [4]J.W. Freuling, Protective Atmospheres for Molten Magnesium, Ph.D. Dissertation, University of Michigan, Ann Arbor, MI, USA, 1970.Google Scholar
- [5]J.F. King, Environmental Challenges Facing the Magnesium Industry – SF6 Replacement, in: Proceedings of the 60th Annual World Magnesium Conference, The International Magnesium Association, Wauconda, IL, USA, 10–16.Google Scholar
- [6]R.E. Brown, Future of Magnesium Developments in 21st Century, in: Presentation at Materials Science & Technology Conference, Pittsburgh, PA, USA, October 5–9, 2008.Google Scholar
- [7]T. Ruden, Magnesium vs. Plastics: A Comparative Study, (Paper G-T89-113), in: Presented at the 15th International Die Casting Congress & Exposition, St. Louis, MO, 1989.Google Scholar
- [8]E.J. VinarcikHigh Integrity Die Casting ProcessesJohn Wiley & Sons, Inc., New York, NY (2003)Google Scholar
- [9]M. Nehan, R. MaloneyMagnesium AM60B Instrument Panel Structure for Crashworthiness FMVSS 204 and 208 Compliance(1996)SAE Paper No. 960419, Warrendale, PAGoogle Scholar
- [10]Die Casting Industry Capability Directory, North American Die Casting Association, Rosemont, IL, USA (2000)
- [11]http://www.gibbsdc.com/.Google Scholar
- [12]A.A. Luo, P.H. Fu, Y.D. Yu, H.Y. Jiang, L.M. Peng, C.Q. Zhai, A.K. SachdevVacuum-assisted High Pressure Die Casting of AZ91 Magnesium AlloyNorth American Die Casting Association Transactions, T08-083(2008)Google Scholar
- [13]Z. Brown, B. Szymanowski, M. Musser, D. Saha, S. Seaver, Manufacturing of Thin Wall Structural Automotive Components Through High Vacuum Die Casting Technology, 2007 Metal Casting Congress.Google Scholar
- [14]H. Koch, A.J. FrankeDuctile Pressure Die Castings for Automotive ApplicationS.K. Das (Ed.), Automotive Alloys, TMS (The Minerals, Metals and Materials Society), Warrendale, PA (1997), pp. 185-198View in ScopusGoogle Scholar
- [15]Z. Brown, A.A. Luo, K. Sadayappan, L.J. Ouimet, J. Zindel, R. Beals, M. MusserDevelopment of Super Vacuum Die Casting Process for Magnesium AlloysNorth American Die Casting Association Transactions, T09-043(2009)Google Scholar
- [16]M. Sahoo, D. Weiss, M. Marlatt, Factors Affecting Successful Permanent Mold Casting of Magnesium, in: Presented at International Conference on Permanent Mold Casting of Al and Mg, February 11–12, 2008, Dallas, Texas, USA.Google Scholar
- [17]P. Fu, A.A. Luo, H. Jiang, L. Peng, Y. Yu, C. Zhai, A.K. SachdevJournal of Materials Processing Technology, 205 (2008), pp. 224-234View PDFView articleView in Scopus
- [18]H. Westengen, O. HoltaFoundry Trade Journal (1989), pp. 738-742
- [19]S.T. Robison, D. Weiss, G. Gegel, G. Woycik, M. Marlatt, B. CoxMagnesium Casting Process Development: Designing an Engine Cradle for Magnesium Semi-permanent Mold CastingAFS Paper 05-217American Foundry Society, Schaumburg, IL (2005)Google Scholar
- [20]A.A. Luo, P.H. Fu, Y.D. Yu, L.M. Peng, H.Y. Jiang, C.Q. Zhai, A.K. SachdevLow Pressure Die Casting of AZ91 and AM50 Magnesium AlloysAFS Paper 08-147American Foundry Society, Schaumburg, IL (2007)Google Scholar
- [21]S.E. LeBeau, M.W. Walukas, R.F. Decker, P. LaBelle, A.R. Moore, J.W. JonesEvaluation of Thixomolded Magnesium Alloy Components for Structural Automotive ApplicationsSAE Technical Paper 2004-01-0137SAE International, Warrendale, PA (2008)Google Scholar
- [22]S. Corbit, R. DasGuptaSqueeze Cast Automotive Applications and Squeeze Cast Aluminum Alloy PropertiesSAE Technical Paper 1999-01-0343SAE, Warrendale, PA (1999)Google Scholar
- [23]R. DasGupta, P. Burton, Z. BrownMicrostructure and Mechanical Properties of Squeeze Cast AZ91D Magnesium AlloySAE Technical Paper 2005-01-0330SAE, Warrendale, PA (2005)Google Scholar
- [24]B. Szymanowski, Magnesium Squeeze Casting Update, in: Presentation at the 111th Metalcasting Congress, Houston, TX, May 15–18, 2007.Google Scholar
- [25]Y. Fasoyinu, M. Sahoo, Lost Foam Casting of Magnesium Alloys for Automotive Applications, in: Proceedings of 64th Annual World Magnesium Conference, International Magnesium Association, Wauconda, IL, USA, 117–134.Google Scholar
- [26]J. Grassi1, J. Campbell, M. Hartlieb, F. MajorMaterials Science Forum, 618–619 (2009), pp. 591-594View in Scopus
- [27]B. Cox, J. Zindel, M. Maj, L. Ouimet, A. Luo, D. Osborne, M. Osborne, R. Beals, E. McCarty, S. Robison, D. Weiss, D. Penrod, High Integrity Magnesium Automotive Components (HIMAC), in: Presentation at the 111th American Foundry Society Metalcasting Congress, Houston, TX, USA, May 15–18, 2007.Google Scholar
- [28]A.I. Taub, P.E. Krajewski, A.A. Luo, J.N. OwensJournal of Metals, 59 (2) (February 2007), pp. 48-57CrossrefView in Scopus
- [29]A.A. LuoChapter 8. Applications: Aerospace, Automotive and Other Structural Applications of Magnesiumbook chapterFundamentals of Magnesium Alloy Metallurgy, Woodhead Publishing Ltd, Cambridge, UK (2012)pp. 393–426Google Scholar
- [30]K.U. KainerMagnesium – Alloys and TechnologiesWiley-VCH, Weinheim, Germany (2003)Google Scholar
- [31]A.A. LuoJournal of Metals, 54 (2) (2002), pp. 42-48View in Scopus
- [32]H.-H. Becker, Status, Potential & Challenges for Automotive Magnesium Applications from the Point of View of an OEM, in: Presentation at 65th Annual World Magnesium Conference, May 18–20, 2008, Warsaw, Poland.Google Scholar
- [33]Y. Michiura, Current Magnesium Research & Application in Automotive Industry in Japan, in: Presentation at International Automotive Body Congress, November 7–8, 2007, Troy, MI, USA.Google Scholar
- [34]J.S. Balzer, P.K. Dellock, M.H. Maj, G.S. Cole, D. Reed, T. Davis, T. Lawson, G. SimondsStructural Magnesium Front End SupportSAE Technical Paper 2003-01-0185SAE International, Warrendale, PA (2003)Google Scholar
- [35]M. Hoeschl, W. Wagener, J. WolfBMW's Magnesium–aluminium Composite Crankcase, State-of-the-art Light Metal Casting and ManufacturingSAE Technical Paper 2006-01-0069SAE International, Warrendale, PA (2006)Google Scholar
- [36]C.J. Duke, S. LoganLightweight Magnesium Spare Tire CarrierProceedings of the 64th Annual World Magnesium Conference, International Magnesium Association, Wauconda, IL 60084, USA (2007), pp. 75-80View in ScopusGoogle Scholar
- [37]G.D. Wardlow, A Changing World with Different Rules – New Opportunities for Magnesium Alloys?, in: Presentation at the 64th Annual World Magnesium Conference, Vancouver, BC, Canada, May 13th–15th, 2007.Google Scholar
- [38]O. Pashkova, I. Ostrovsky, Y. Henn, Present State and Future of Magnesium Application in Aerospace Industry, in: Presentation at New Challenges in Aeronautics, Moscow, 2007.Google Scholar
- [39]J. HillisThe Effects of Heavy Metal Contamination on Magnesium Corrosion PerformanceSAE Technical Paper No. 830523SAE International, Warrendale, PA, USA (1983)Google Scholar
- [40]R.E. Brown, E. LeeMagnesium Usage Grew Rapidly in 1930–1950W.J. Poole, K.U. Kainer (Eds.), Proceedings of 9th International Conference on Magnesium Alloys and Their Applications (July 8–12, 2012), pp. 453-460Vancouver, BC, CanadaCrossrefView in Scopus
- [41]B.R. Powell, P.E. Krajewski, A.A. LuoChapter 4: Magnesium Alloysbook chapterMaterials Design and Manufacturing for Lightweight Vehicles, Woodhead Publishing Ltd, Cambridge, UK (2010)pp. 114–168Google Scholar
- [42]E.F. EmleyPrinciples of Magnesium TechnologyPergamon Press (1966)Google Scholar
- [43]S. Schumann, H. FriedrichThe Use of Magnesium in Cars – Today and in the FutureB. Mordike, K. Kainer (Eds.), Magnesium Alloys and Their Applications, Werkstoff-Informationsgesellschaft, Frankfurt, Germany (1998), pp. 3-13Google Scholar
- [44]H. Friedrich, S. SchumannJournal of Materials Processing Technology, 117 (2001), pp. 276-281View PDFView articleView in Scopus
- [45]F. Hollrigl-RostaLight Metal Age (1980), pp. 22-29View in Scopus
- [46]A. Hector, W. HeissMagnesium Die-castings as Structural Members in the Integral Seat of the New Mercedes-Benz RoadsterSAE Technical Paper No. 900798SAE, Warrendale, PA (1990)Google Scholar
- [47]D. AlexanderAutomotive Engineering International (May 2004), pp. 22-24View in Scopus
- [48]L. Riopelle, Magnesium Applications, in: International Magnesium Association (IMA) Annual Magnesium in Automotive Seminar, Livonia, MI, April 20, 2004.Google Scholar
- [49]S. GibbsMetal Casting Design and Purchasing (July/August 2010), pp. 29-33View in Scopus
- [50]J. Aragones, K. Goundan, S. Kolp, R. Osborne, L. Ouimet, W. PinchDevelopment of the 2006 Corvette Z06 Structural Cast Magnesium CrossmemberSAE International Technical Paper No. 2005-01-0340SAE International, Warrendale, Pennsylvania (2005)Google Scholar
- [51]J. Greiner, C. Doerr, H. Nauerz, M. GraeveThe New ‘7G-TRONIC’ of Mercedes-Benz: Innovative Transmission Technology for Better Driving Performance, Comfort, and Fuel EconomySAE Technical Paper No. 2004-01-0649SAE International, Warrendale, PA, USA (2004)Google Scholar
- [52]S. Koike, K. Washizu, S. Tanaka, T. Baba, K. KikawaSAE Technical Paper No. 2000-01-1117SAE International, Warrendale, PA, USA (2000)Google Scholar
- [53]B. Powell, et al., Progress Toward a Magnesium-intensive Engine: The USAMP Magnesium Powertrain Cast Components Project, SAE 2004 Transactions, Journal of Materials & Manufacturing Paper No. 2004-1-0654, SAE International, Warrendale, PA, USA, 250–259.Google Scholar
- [54]B.R. PowellMagnesium Powertrain Cast ComponentsPublished in FY2008 Annual Progress Report for Automotive Lightweighting MaterialsU.S. Department of Energy, Washington, D.C (April 2009)
- [55]International Magnesium AssociationMagnesium's Tough Strength Endures Abuse to Protect Portable Electronic DevicesInternational Magnesium Association, Wauconda, IL, USA (2008)Google Scholar
- [56]International Magnesium AssociationLighter Magnesium Improves Power Tool PerformanceInternational Magnesium Association, Wauconda, IL, USA (2008)Google Scholar
- [57]C.L. Mendis, C.J. Bettles, M.A. Gibson, C.R. HutchinsonMaterials Science and Engineering A, 435/436 (2006), pp. 163-171View PDFView articleView in Scopus
- [58]A.A. Luo, P. Fu, L. Peng, X. Kang, Z. Li, T. ZhuMetallurgical and Materials Transactions A, 43A (2012), pp. 360-368CrossrefView in Scopus
- [59]P. Fu, L. Peng, H. Jiang, J. Chang, C. ZhaiMaterials Science and Engineering A, 486 (2008), pp. 183-192Crossref
- [60]A.A. Luo, R.K. Mishra, B.R. Powell, A.K. SachdevMaterials Science Forum, 706–709 (2012), pp. 69-82View in Scopus
- [61]A.A. Luo, W. Shi, K. Sadayappan, E.A. NybergMagnesium Front End Research and Development: Phase I Progress Report of a Canada–China–USA CollaborationProceedings of IMA 67th Annual World Magnesium Conference, International Magnesium Association (IMA), Wauconda, IL, USA (2010)Google Scholar
- [62]M. Easton, A. Beer, M. Barnett, C. Davies, G. Dunlop, Y. Durandet, S. Blacket, T. Hilditch, P. BeggsJOM, 60 (11) (2008), pp. 57-62CrossrefView in Scopus
- [63]F. Zhu, C.C. Chou, K.H. Yang, X. Chen, D. Wagner, S. Bilkhu, A.A. LuoInternational Journal of Crashworthiness, 17 (5) (2012), pp. 540-552CrossrefView in Scopus
- [64]S. Logan, A. Kizyma, C. Patterson, S. RamaLightweight Magnesium-intensive Body StructureSAE International Technical Paper No. 2006-01-0523SAE International, Warrendale, PA, USA (2006)Google Scholar
- [65]W. Wen, A.A. Luo, T. Zhai, Y. Jin, Y.-T. Cheng, I. HoffmannScripta Materialia, 66 (2012), 10.1016/j.scriptamat.2012.08.010View at publisher
- [66]H.A. Patel, N. Rashidi, D.L. Chen, S.D. Bhole, A.A. LuoMaterials Science and Engineering A, 546 (2012), pp. 72-81View PDFView articleView in Scopus
- [67]A.A. Luo, J.F. Quinn, Y.-M. Wang, T.M. Lee, R. Verma, D.A. Wagner, J.H. Forsmark, X. Su, J. Zindel, M. Li, S.D. Logan, S. Bilkhu, R.C. McCuneLight Metal Age (April 2012), pp. 54-58View in Scopus
- [68]National Research CouncilIntegrated Computational Materials Engineering: A Transformational Discipline for Improved Competitiveness and National SecurityThe National Academies Press, Washington, DC, USA (2008)Google Scholar
- [69]M. Li, A.A. Luo, Integrated Computational Materials Engineering for Magnesium, Published in FY2011 Annual Progress Report for Automotive Lightweighting Materials, U.S. Department of Energy, Washington, D.C., USA, http://www1.eere.energy.gov/vehiclesandfuels/pdfs/lm_11/4_usamp_cooperative_research.pdf.Google Scholar
- [70]T.M. PollockScience, 328 (2010), pp. 986-987View at publisherCrossrefView in Scopus