本論文概要は、['ダイカストプロセスにおけるシミュレーションによる鋳造製品の欠陥予測']と題された論文に基づいており、['International Journal of Production Research']に掲載されました。
1. 概要:
- タイトル:シミュレーションによる鋳造製品の欠陥予測(ダイカストプロセスにおいて)(Simulation-enabled casting product defect prediction in die casting process)
- 著者:M.W. Fu & M.S. Yong
- 出版年:2009年
- 出版ジャーナル/学会:International Journal of Production Research
- キーワード:CAEシミュレーション (CAE simulation); 高圧ダイカスト (high pressure die casting); 製品品質保証 (product quality assurance); 欠陥予測 (defect prediction)
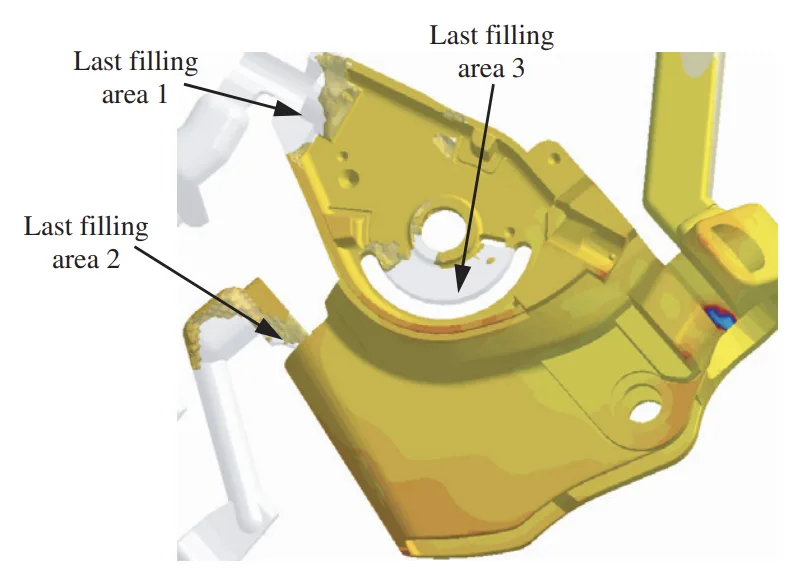
2. 研究背景:
研究テーマの背景:
現代の鋳造業界では、製品開発パラダイムが、従来のワークショップでの試行錯誤から、CAE(Computer-Aided Engineering)を活用したシミュレーションとコンピュータによる「概念実証(proof-of-concept)」手法へと移行しています。この製品開発パラダイムの転換は、経験的なノウハウと経験重視から、より科学的なシミュレーション、評価、分析、計算へと移行することを意味します。CAEシミュレーションは、鋳造プロセス全体をモデル化し、実際の稼働条件下での鋳造システムの動的挙動を明らかにする上で重要な役割を果たします。さらに、シミュレーションを通じて製品品質の全体像と製品欠陥を探求することで、鋳造欠陥の根本原因を特定し、それらを回避するための解決策を決定することができます。現在、特に高圧ダイカスト(HPDC)製品は、ニアネットシェイプまたはネットシェイプ特性、高い生産性、複雑な形状と特徴により、多くの産業分野で広く使用されています。市場がより短い設計および製造リードタイム、優れた寸法精度、全体的な製品品質、迅速な製品設計変更を要求するにつれて、従来の製品開発パラダイムは、競争の激しい市場環境において明らかに限界に直面しています。
既存研究の現状:
従来のCAD(Computer-Aided Design)およびCAM(Computer-Aided Manufacturing)技術は、設計意図を表現し、物理的な実現を支援する効率的な支援技術として重要な役割を果たしてきました。これらの技術は、設計品質を大幅に向上させ、リードタイムを短縮することに貢献しています。しかし、CAD/CAM技術だけでは、鋳造プロセス設計、金型構造、製品特性構成、包括的な品質管理と品質保証といった重要な側面に対処するには不十分です。既存の鋳造シミュレーション研究は、主に単一的なアプローチであり、シミュレーションを活用した製品欠陥予測パラダイムを体系的に提示していません。これらの研究は、CAEシミュレーションが欠陥予測と回避にどのように役立つか、CAEからどのような情報を得られるか、どのような種類の情報が対応する欠陥を特定するために必要なのか、充填および凝固プロセスでどのような欠陥が発生する可能性があるのか、シミュレーションによって提供された情報に基づいて製品欠陥回避のための対策をどのように考案するのかを十分に明らかにしていません。
研究の必要性:
従来の方法論と断片的な研究の限界を克服するためには、CAEシミュレーション技術に支えられた効率的な製品開発パラダイムが喫緊に必要です。これは、プロセス構成と製品品質に対する要求の高まりによって引き起こされる鋳造生産業界のボトルネックに対処するために非常に重要です。CAEシミュレーション技術は、鋳造製品の品質と欠陥の分析、予測、評価のための技術的に効率的で費用対効果の高いソリューションとして登場しており、物理的な試行錯誤への依存を減らし、製品開発サイクルを加速することに貢献できます。
3. 研究目的と研究課題:
研究目的:
本研究の主な目的は、CAE技術をダイカストプロセスにおける鋳造プロセスシミュレーションと製品欠陥予測のための重要なツールとして提示することです。本研究は、鋳造プロセスのモデリングを明確にし、重要なシミュレーションの問題点を詳細に説明し、CAEシミュレーションが充填、凝固、および射出後の挙動に関連する情報をどのように明らかにするかを説明することを目的としています。産業界のケーススタディを通じて、CAEシミュレーションがプロセス関連の欠陥を特定し予測する上で有効であることを示し、製品品質保証を向上させる上でのCAEシミュレーションの全体的な効率性を検証することを目的としています。
主要な研究課題:
本研究は、以下の主要な側面に焦点を当てています。
- 数値解析法を用いて鋳造プロセスをモデル化し、実際のプロセス、モデリング、シミュレーション、および出力変数間の関連性を確立する方法。
- シミュレーションプロセスとソリューション生成サイクルにおける情報フローを明確に説明する方法。
- 鋳造欠陥の予測のためのプロセスベースのシミュレーションパラダイムを提案する方法。
- シミュレーションによって明らかにされる情報と、この情報に基づいて予測できる欠陥カテゴリを分類する方法。
- ケーススタディを通じて、シミュレーションプロセス、手順、および特定されたシミュレーションパラメータに基づいて鋳造プロセスで欠陥が発生するメカニズムを分析する方法。
研究仮説:
中心となる仮説は、CAEシミュレーション技術がダイカストプロセスにおける鋳造製品の欠陥を予測するための堅牢で効果的な方法論を提供することです。鋳造プロセスを正確にモデル化し、シミュレーション出力を分析することで、プロセス関連の欠陥を特定、理解、そして最終的には回避することができ、製品品質の向上と製造コストの削減につながると仮定します。さらに、体系的なプロセスベースのシミュレーションパラダイムを開発および検証して、ダイカストにおける欠陥予測とプロセス最適化を促進できると仮説を立てています。
4. 研究方法論
研究デザイン:
本研究では、鋳造欠陥予測のためのプロセスベースのシミュレーションフレームワークを採用しています。このフレームワークは、製品設計仕様とCAEシミュレーションの統合を中心に構成されており、鋳造プロセスを分析および最適化します。研究デザインには、CAE環境内で鋳造形状、プロセスルート、およびパラメータ決定を含む鋳造システム全体をモデル化することが含まれます。この方法論は、高圧ダイカスト(HPDC)プロセスに焦点を当てた産業界のケーススタディを通じて検証されます。
データ収集方法:
本研究のデータは、主に商用鋳造シミュレーションソフトウェアであるMagmasoftを使用して実施されたCAEシミュレーションから得られます。シミュレーションの入力データには、鋳造形状のCAD STLモデル、鋳造合金(AlSi9Cu3)および金型材料(X38CrMoV5)の材料特性、HPDCに関連するプロセスパラメータが含まれます。産業界のケーススタディは、シミュレーション結果に対する実際的な背景と検証を提供します。溶融金属の流れパターン、温度分布、凝固順序、応力-ひずみ解析などのシミュレーション出力は、欠陥予測のために収集された主要なデータを構成します。
分析方法:
分析方法は、CAEシミュレーション結果を解釈して鋳造欠陥を予測および理解することに重点を置いています。CAEソフトウェア内では、有限要素法(FEM)および有限差分法(FDM)などの数値解析法が活用され、鋳造システムの物理的挙動を定量的に表現します。分析には以下が含まれます。
- 溶融金属先端前進(MFA)分析を実施し、潜在的な空気巻き込みと充填の不均衡を特定します。
- 凝固時の温度分布分析を実施し、収縮空孔とホットスポットの発生可能性を予測します。
- 射出後の応力とひずみの分布評価を実施し、変形と残留応力を評価します。
- シミュレーションで予測された欠陥と、産業界のケーススタディで観察された実際の欠陥を比較し、シミュレーション方法論を検証します。
研究対象と範囲:
研究対象は、産業界の高圧ダイカスト(HPDC)プロセスであり、特に4キャビティダイカスト構成に焦点を当てています。2つの産業界のケーススタディが詳細に提示されています。研究範囲は、充填、凝固、および熱応力に起因する欠陥を含む、HPDCにおけるプロセス関連の欠陥に限定されます。調査対象の材料は、鋳造材料としてAlSi9Cu3、金型材料としてX38CrMoV5であり、これらはダイカスト用途で一般的に使用される材料を代表しています。シミュレーション分析は、金型充填、凝固と冷却、および射出後の鋳造品の応力とひずみ分布を網羅しています。
5. 主な研究結果:
主要な研究結果:
本研究は、CAEシミュレーションがダイカストプロセスに関する重要な情報を効果的に明らかにし、製品欠陥の予測を可能にすることを実証しています。主な研究結果は以下の通りです。
- 充填プロセスシミュレーション: CAEシミュレーションは、溶融金属先端位置、乱流、および充填の滑らかさを正確に描写します。潜在的な空気巻き込み領域を特定し、ベントの必要性を評価します。シミュレーションはまた、熱的挙動、温度分布、充填順序、および溶融金属速度分布を明らかにし、これらは金型浸食と表面仕上げ品質を予測する上で重要です。分割溶融流れや未充填などの望ましくない充填挙動も識別可能です。
- 凝固プロセスシミュレーション: シミュレーションは、凝固順序、鋳造品と金型の温度分布を解明し、最終凝固領域と潜在的なホットスポットを特定します。冷却システム設計、ランナーシステム設計の評価、および収縮空孔と多孔性分布の予測に役立ちます。CAEシミュレーションは、多孔性のない鋳造品のためのフィーダーサイズと位置の決定も支援します。
- 鋳造品応力解析: CAEシミュレーションは、射出後の温度分布と変形、残留応力分布、および応力に関連する潜在的な製品欠陥を予測します。鋳造システム設計の最適化と、金型寿命と鋳造精度を向上させるための金型応力解析をサポートします。
データ解釈:
シミュレーション結果は、特定のシミュレーション出力と潜在的な鋳造欠陥を関連付けるために解釈されます。たとえば、不均衡なMFAパターンは、不均一な充填と空気巻き込みに起因する欠陥に関連付けられます。凝固シミュレーションで特定されたホットスポットは、潜在的な収縮空孔とオレンジスキン欠陥を示唆しています。応力解析で予測された高い応力集中は、変形または疲労破壊が発生しやすい領域を示唆しています。ケーススタディは、シミュレーションで予測された欠陥と、産業界の鋳造品で観察された実際の欠陥との間に強い相関関係を示すことで、これらの解釈を検証します。たとえば、ケースIでは、MFA分析によりボス形状での空気巻き込みが予測され、これは鋳造品分析によって確認されました。ケースIIでは、シミュレーションにより、非合理的な流れと温度分布がオレンジスキンおよび破断欠陥につながると予測され、これらは実際の部品でも観察されました。
図のリスト:
- Figure 1. Modelling of the casting process from physical and mathematical perspectives: action-behaviour-property relationship.
- Figure 2. Association among the process, modelling, simulation and output variables.
- Figure 3. The process-based simulation paradigm for prediction of casting defects.
- Figure 4. The layout of the casting filling system in Case I.
- Figure 5. The MFA positions in the filling process. (a) Filling at 85% of the whole process; (b) filling at 90% of the whole process.
- Figure 6. The layout of the casting filling system in Case II.
- Figure 7. The melt-front advancement position in filling process.
- Figure 8. Unreasonable filling pattern and the defect caused. (a) Simulation predicted irrational flow; (b) the real defect revealed by experiment.
- Figure 9. Defect caused by the unreasonable temperature distribution in the solidification process. (a) Simulation result; (b) real part.
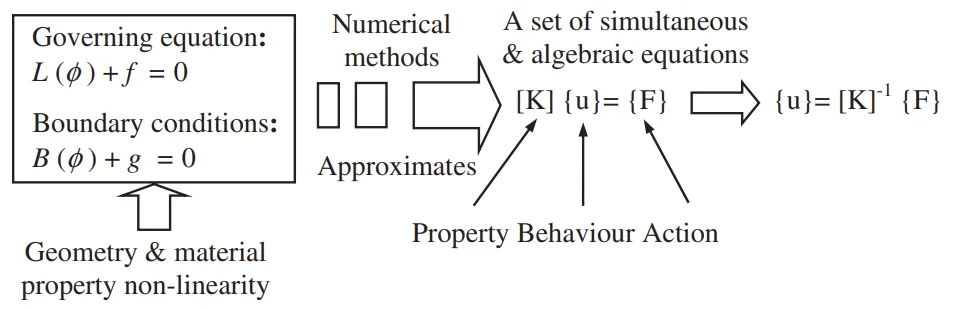
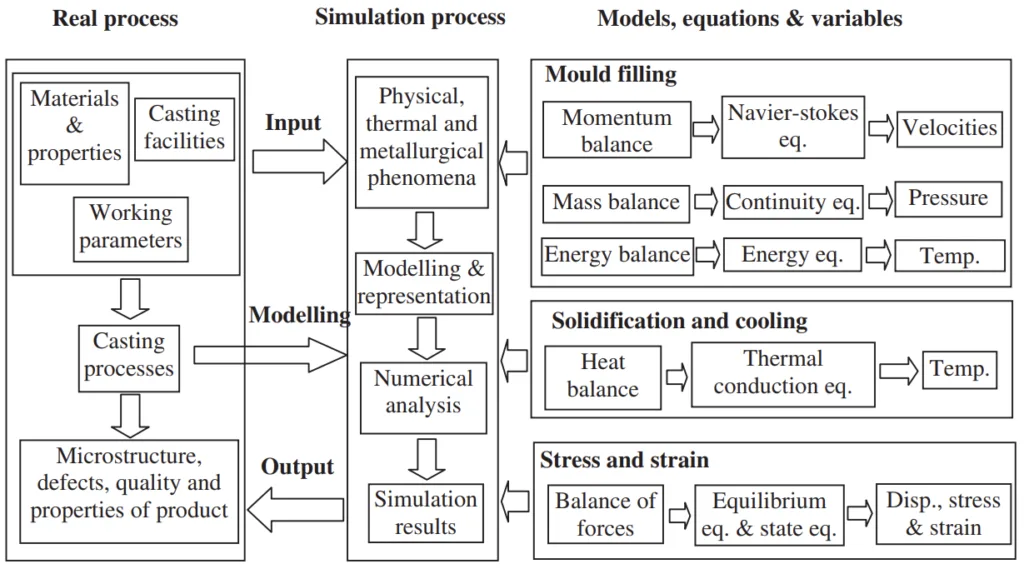
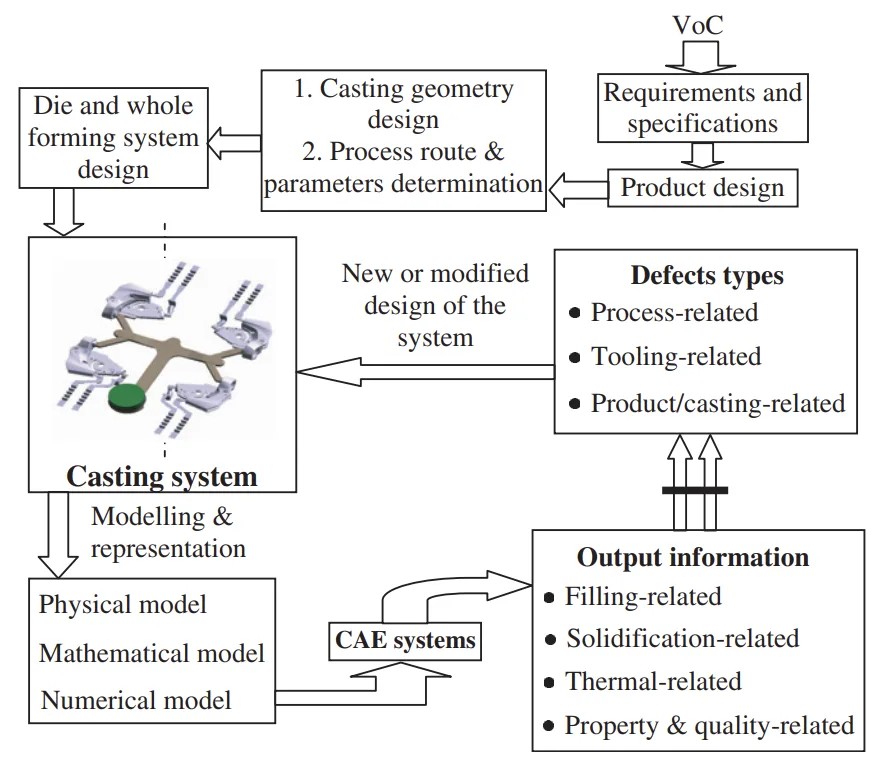
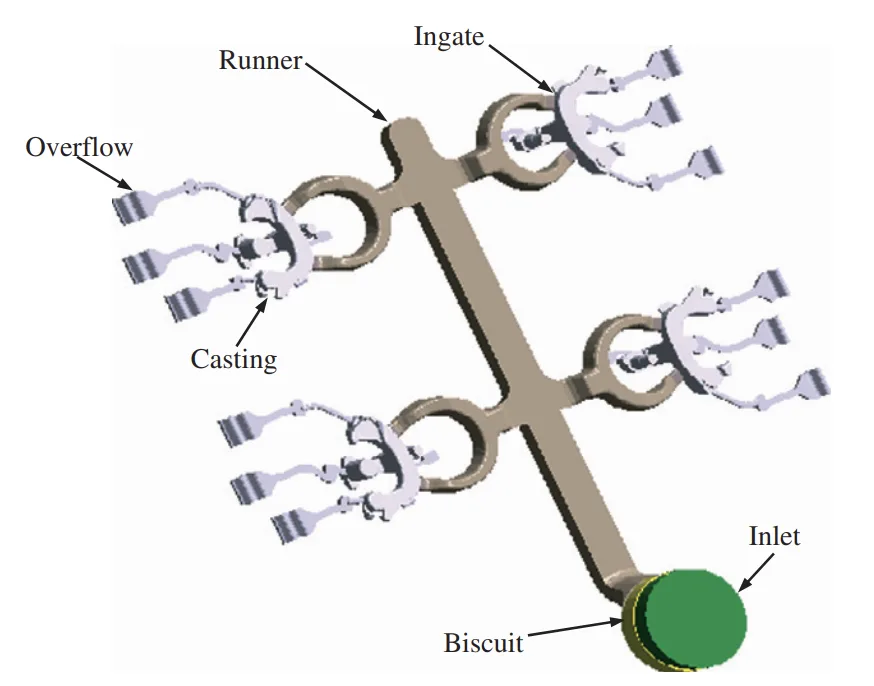
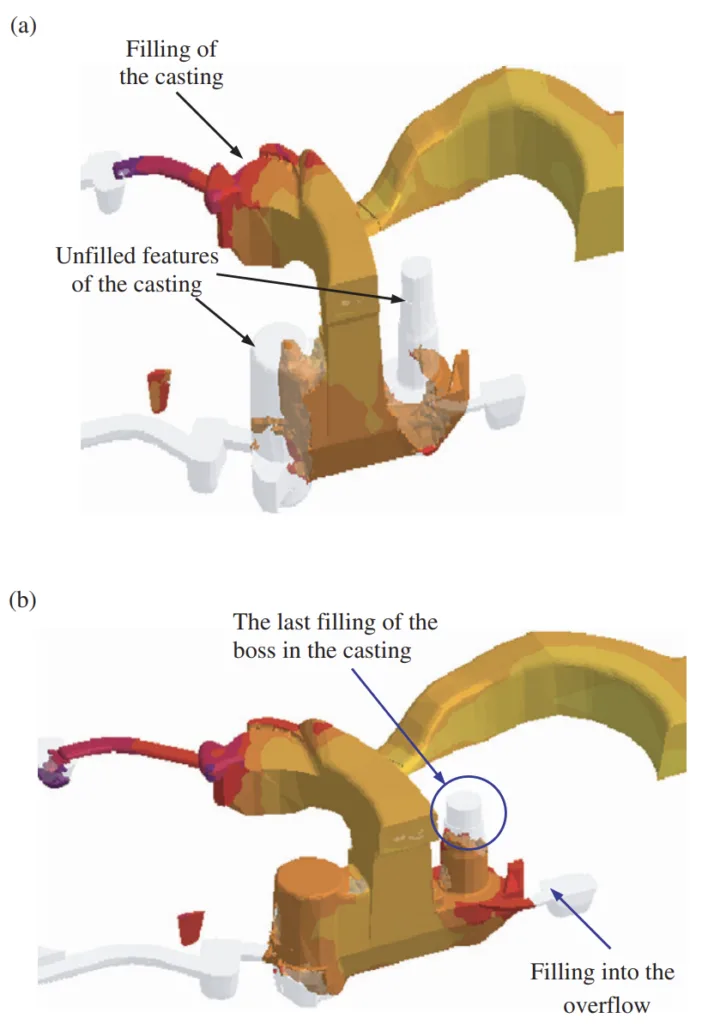
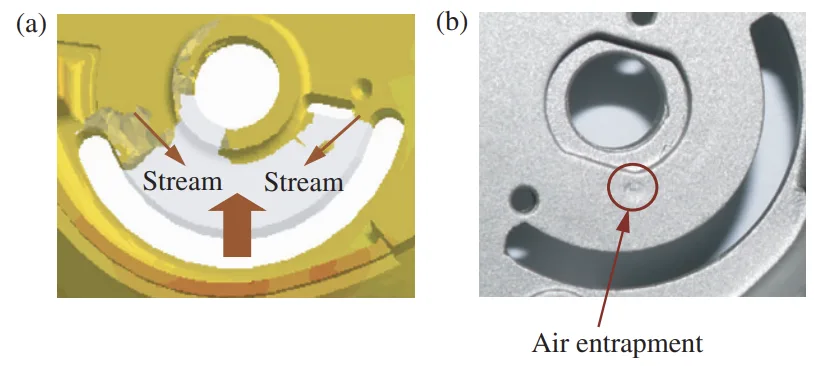
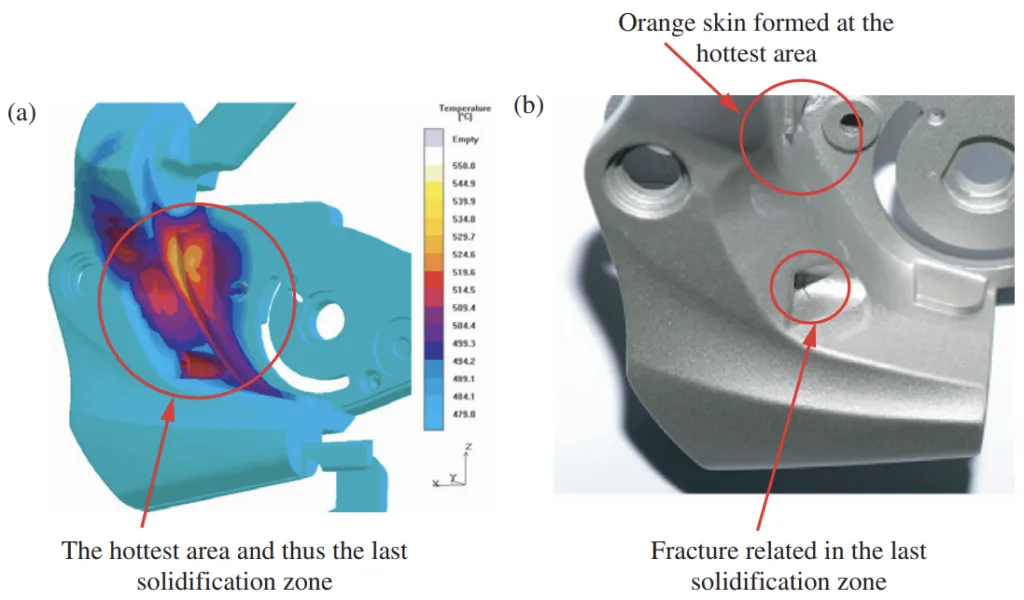
6. 結論:
主な結果の要約:
本研究は、ダイカストプロセスにおけるシミュレーションによる鋳造製品の欠陥予測の有効性を決定的に実証しています。CAEシミュレーションを採用することにより、充填、凝固、射出後の挙動など、複雑な鋳造プロセスを仮想的に実現し、分析することができます。本研究は、産業界のケーススタディを通じて検証された、シミュレーションによる欠陥予測のための包括的なフレームワーク、手順、およびプロセスを明確に提示します。研究結果は、CAEシミュレーションがプロセス関連の欠陥を特定および予測するための強力なツールであることを確認しており、これにより、鋳造製品開発における従来の試行錯誤法への依存を減らすことができます。
研究の学術的意義:
本研究の学術的意義は、CAEシミュレーションをダイカスト製品開発パラダイムに統合するための体系的なアプローチにあります。単一的なアプローチを超えて、鋳造プロセスに関する全体的な視点を提供する構造化された欠陥予測方法論を提示します。本研究は、CAEシミュレーションが重要なプロセスパラメータとダイカストにおける欠陥形成との関係を明らかにするためにどのように効果的に活用できるかについての理論的理解を深めます。シミュレーション出力を分類し、それらを特定の欠陥タイプと関連付けることで、本研究は鋳造プロセス最適化と品質保証のための科学的基盤を強化します。
実用的な意義:
本研究の実用的な意義は、ダイカスト業界に大きな影響を与えることです。本研究で提示されたCAEシミュレーション技術の応用は、以下の道筋を提供します。
- 試行錯誤の削減: 鋳造プロセスを仮想的にシミュレーションすることにより、製造業者は、ワークショップでのコストがかかり時間がかかる物理的な実験を最小限に抑えることができます。
- 製品開発コストの削減: シミュレーションによる潜在的な欠陥の早期発見と軽減は、ダウンストリームの再作業、スクラップ率、および全体的な生産コストを大幅に削減できます。
- 製品化までの時間短縮: CAEベースの設計最適化によって促進される合理化された製品開発サイクルにより、鋳造製品をより迅速に市場に投入できます。
- 鋳造品質の向上: シミュレーションを通じて欠陥メカニズムとプロセスパラメータに関する理解を深めることで、製品品質、寸法精度、および機能性能の向上が実現します。
- 鋳造設計とプロセスの最適化: CAEシミュレーションは、鋳造形状、金型設計、プロセスパラメータ、および冷却戦略を最適化するための実行可能な洞察を提供し、より効率的で堅牢な鋳造プロセスを実現します。
研究の限界
本研究はCAEシミュレーションの能力を効果的に実証していますが、潜在的な限界に注意することが重要です。ケーススタディは、主に4キャビティHPDCプロセスと特定の材料(AlSi9Cu3およびX38CrMoV5)に焦点を当てています。研究結果の一般化可能性を他の鋳造プロセス(例:重力ダイカスト、低圧ダイカスト)およびより広範囲の材料に適用するには、さらなる調査が必要になる場合があります。さらに、シミュレーション結果の精度は、材料特性やプロセスパラメータなどの入力データの忠実度に左右されます。これらの限界にもかかわらず、本研究は、ダイカスト欠陥予測におけるCAEシミュレーションのより広範な応用のための強力な基盤を提供します。
7. 今後のフォローアップ研究:
- 今後のフォローアップ研究の方向性
今後の研究では、HPDCを超えて、重力ダイカストや低圧ダイカストなど、より広範な鋳造プロセスへの提示されたCAEシミュレーションフレームワークの適用を拡大することに焦点を当てる必要があります。鉄合金や非鉄合金を含む多様な鋳造材料に対する方法論の有効性を調査することも重要です。追加の研究では、リアルタイムプロセスモニタリングおよび制御システムとCAEシミュレーションを統合して、生産中の適応型プロセス最適化を可能にする方法を検討できます。 - さらなる探求が必要な領域
さらなる探求が必要な領域には、CAEソフトウェア内でのより洗練された予測可能な欠陥モデルの開発、特に熱間割れや疲労関連の破損などの複雑な欠陥タイプに対するモデル開発が含まれます。より迅速なターンアラウンドタイムと迅速な製品開発サイクルへの統合を可能にするために、シミュレーションの計算効率を向上させることも不可欠です。欠陥予測精度とプロセス最適化機能を向上させるために、マルチフィジックスシミュレーションや機械学習アルゴリズムなどの高度なシミュレーション技術の使用を調査することは、将来の研究のための有望な道筋を示しています。
8. 参考文献:
- Barriere, T., Liu, B., and Gelin, J.C., 2003. Determination of the optimal process parameters in metal injection molding from experiments and numerical modeling. Journal of Materials Processing Technology, 143–144 (December), 636-644.
- Bird, R.B., Stewart, W.E., and Lightfoot, E.N., 1960. Transport Phenomena. New York: J. Wiley & Sons.
- Cleary, P., et al., 2002. Flow modeling in casting processes. Applied Mathematical Modeling, 26, 171-190.
- Dai, X., et al., 2003. Effects of runner system design on the mechanical strength of Al-7Si-Mg alloy castings. Materials Science and Engineering: A, 354 (1), 315–325.
- Fuh, J.Y.H., et al., 2004. Computer-aided Injection Mould Design and Manufacture. New York: Marcel Dekker.
- Guo, Z., et al., 2005. Modelling of materials properties and behavior critical to casting simulation. Materials Science and Engineering: A, 413-414, 465-469.
- Hsu, Y.L. and Yu, C.C., 2006. Computer simulation of casting process of aluminum wheels a case study. Proceedings of the I MECH E Part B Journal of Engineering Manufacture, 220 (2), 203-211.
- Hu, B.H., et al., 2000. Design and optimization of runner and gating systems for the die casting of thin-walled magnesium telecommunication parts through numerical simulation. Journal of Materials Processing Technology, 105 (1), 128-133.
- Krimpenis, A., et al., 2006. Simulation-based selection of optimum pressure die-casting process parameters using neural nets and genetic algorithms. International Journal of Advanced Manufanuring Technology, 27 (5–6), 509–517.
- Lewis, R.W. and Ravindran, K., 2000. Finite element simulation of metal casting. International Journal for Numerical Methods in Engineering, 47 (1–3), 29–59.
- Louvo, A., 1997. Casting simulation as a tool in concurrent engineering. In: International ADI and simulation conference, 28–30 May, Espoo, Finland.
- McMillin, T., Hartmann, G., and Egner-Walter, A., 2002. CAE opens new frontier in casting design. Engineered Casting Solutions, Spring 2002, 29–31.
- Midea, A., et al., 2000. Using computer modeling to optimize casting processes. Modern Casting, 90, May 2000, 4-10.
- Mirbagheri, S.M.H., et al., 2002. Simulation of melt flow in coated mould cavity in the casting process. Journal of Materials Processing Technology, 142 (2), 493–507.
- Mochnacki, B., Lara, S., and Pawlak, E., 2005. Multiscale model of segregation process. Journal of Materials Processing Technology, 162–163, May 2005, 766–769.
- Monroe, C. and Beckermann, C., 2005. Development of a hot tear indicator for steel castings. Materials Science and Engineering: A, 413-414, 30-36.
- Naher, S., Brabazon, D., and Looney, L., 2003. Simulation of the stir casting process. Journal of Materials Processing Technology, 143-144, 567–571.
- Neumann, L., et al., 2005. Prediction of texture induced anisotropy by through-process modelling. Materials Science Forum, 495–497, 1657–1662.
- Peng, Y.H., et al., 2005. Numerical study on the low pressure die casting of AZ91D wheel hub. Materials Science Forum, 488-489, 393-396.
- Sequeira, W., et al., 2001. Optimization of die casting part design, process parameters and process control using newly die casting simulation tool. In: proceedings of die casting in the 21th century, Cincinnati, Ohio.
- Sturm, J.C., et al., 2001. Optimized development for castings and casting processes. In: 19th CAD-FEM users' meeting 2001, international congress on FEM technology, 17–19 October, Postdam, Germany.
- Ulysse, P., 1999. Optimal extrusion die design to achieve flow balance. International Journal of Machine Tools and Manufacture, 39 (7), 1047–1064.
- Venkatesan, A., Gopinath, V.M., and Rajadurai, A., 2005. Simulation of casting solidification and its grain structure prediction using FEM. Journal of Materials Processing Technology, 168 (1), 10-15.
- Zhang, X.P., Xiong, S.M., and Xu, Q.Y., 2006. Numerical methods to improve the computational efficiency of solidification simulation for the investment casting process. Journal of Materials Processing Technology, 173 (1), 70–74.
9. 著作権:
- 本資料は "M.W. Fu & M.S. Yong" の論文:「ダイカストプロセスにおけるシミュレーションによる鋳造製品の欠陥予測」に基づいています。
- 論文ソース:http://dx.doi.org/10.1080/00207540801935616
本資料は上記の論文に基づいて要約されたものであり、商業目的での無断使用は禁止されています。
Copyright © 2025 CASTMAN. All rights reserved.