1. 概要:
- タイトル: アルミニウム高圧ダイカストの金型への凝着を引き起こす熱機械的メカニズム (THERMOMECHANICAL MECHANISMS THAT CAUSE ADHESION OF ALUMINUM HIGH PRESSURE DIE CASTINGS TO THE DIE)
- 著者: アレックス・モンロー (Alex Monroe)
- 発行年: 2021年
- 発行ジャーナル/学会: ミシガン工科大学、Digital Commons @ Michigan Tech、学位論文、修士論文、およびレポート (Michigan Technological University, Digital Commons @ Michigan Tech, Dissertations, Master's Theses and Master's Reports)
- キーワード: HPDC、凝着、固着、半田付け、熱機械的、摩擦、金属間化合物 (HPDC, adhesion, sticking, soldering, thermomechanical, friction, intermetallic)
2. 研究背景:
- 研究テーマの社会的/学術的背景: 高圧ダイカスト (HPDC) は、複雑な非鉄鋳物、特に自動車部品のアルミニウム部品の製造に広く使用されている鋳造プロセスです。HPDC における重要な課題の 1 つは、鋳造材料が金型に付着する凝着現象であり、これは欠陥につながります。潤滑剤は凝着を軽減するために使用されますが、鋳造欠陥、ブリスター、金型寿命の短縮、機械摩耗の増加などの欠点をもたらします。
- 既存研究の限界: 従来の理論では、凝着はアルミニウムと鋼製金型間の速度論的に制御された金属間化合物形成が原因であるとされています。しかし、この理論に基づいて金型表面を非反応性材料でコーティングすることは、産業および実験室環境において部分的にしか効果的でないことが示されています。さらに、速度論的モデルでは、深刻な凝着が発生する領域を正確に特定できず、追加の説明メカニズムの必要性を示唆しています。
- 研究の必要性: HPDC における凝着欠陥の予測と削減を向上させるためには、速度論的に制御された金属間化合物形成理論に加えて、追加のメカニズムを調査し、理解することが重要です。本研究は、HPDC における固着と半田付けに寄与する重要なメカニズムでありながら、しばしば見過ごされてきた摩擦に焦点を当てて研究を進めます。
3. 研究目的と研究課題:
- 研究目的: 本研究は、アルミニウム高圧ダイカスト (HPDC) における凝着に寄与する熱機械的メカニズム、特に摩擦に焦点を当てて調査することを目的としています。本研究は、凝着が速度論的に制御された金属間化合物形成によって独占的に引き起こされるという従来の理解に挑戦し、摩擦ベースのメカニズムを提案します。
- 主要な研究課題:
- 鋳造物と金型間の熱機械的干渉から生じる摩擦は、HPDC における固着と半田付けにどの程度寄与しているか?
- 摩擦ベースのモデルは、金属間化合物形成速度論のみに基づいたモデルと比較して、HPDC における凝着現象をより正確に予測できるか?
- 研究仮説:
- 半田付けが主に速度論的に駆動される相形成の結果である場合、実験室拡散対実験は、産業用半田付けの観察結果を効果的に再現し、予測できるはずです。
- 摩擦が重要な要因である場合、金型コアの抜き勾配を大きくすると、排出方向の摩擦力成分の減少により、接触面積の減少よりも比例的に大きく排出力が減少するはずです。
- 半田付けが摩擦と材料強度に影響を受ける場合、排出温度を上げると、合金の強度が低下し、摩擦せん断応力に対する抵抗力が弱まるため、半田付けの可能性が高まるはずです。
4. 研究方法
- 研究デザイン: 本研究では、HPDC における凝着のメカニズムを分析するために、実験的調査と計算モデリングを組み合わせた混合手法アプローチを採用しました。これには以下が含まれます。
- 室温および高温での排出試験を含む実験的研究。排出力を測定し、半田付け現象を観察します。
- 鋳造物-金型界面での凝固、冷却、熱応力、および摩擦をシミュレーションするための 1 次元 (1D) および 3 次元 (3D) 数値モデリング。
- データ収集方法: データは以下を通じて収集されました。
- 室温排出試験用のオメガダインロードセルを備えたティニウスおよびオルセン引張試験機を使用した排出力の測定。
- 高温排出試験用の k 型熱電対による温度記録とロードセルによる排出力の測定。変位は LVDT で測定。
- 産業用鋳物の 3D モデリング用に MAGMASOFT から生成されたシミュレーションデータと、1D 熱機械モデリング用の MATLAB データ。
- 分析方法: 収集されたデータは、以下を使用して分析されました。
- 排出力と半田付けの可能性を予測するためのクーロンおよびトレスカ摩擦モデルの適用。
- さまざまな合金が排出力に及ぼす影響を比較するためのペアスチューデントの t 検定を含む統計分析。
- 界面強度、接触圧力、摩擦係数などのパラメータを決定するために、Excel ソルバーを使用して実験データを摩擦モデルにフィッティング。
- 摩擦ベースのアプローチの妥当性を検証するために、モデル予測と実験的観察および産業ケーススタディの比較。
- 研究対象と範囲: 研究は以下の点に焦点を当てました。
- 軸対称性を仮定してモデリングと実験を簡素化するための管状鋳物内の円筒形金型 (コア) 形状。
- アルミニウム合金: 主に A380 および A356、合金組成の影響を評価するための A362、A365、および A518 の追加シミュレーション。化学組成は表 4 に詳しく記載されています。
- 金型材料: H13 鋼、H13 High K 鋼、およびインコネルがシミュレーションで考慮されました (特性は表 5 に記載)。
- 調査対象の変数: 抜き勾配 (0.5°~25°)、排出温度 (室温~555°C)、合金組成、金型材料、鋳造厚さ、およびコア直径。
5. 主な研究結果:
- 主要な研究結果:
- 主要なメカニズムとしての摩擦: 室温排出試験では、排出力が本質的な凝着力を説明するための補正項を必要とせずに、摩擦モデルによって十分に予測される干渉嵌め合いのように振る舞うことが実証されました。「最適なフィッティングは、界面強度がゼロに設定され、接触圧力が 5.9 MPa、摩擦係数が 0.59 の場合に達成されます。最適なフィッティングは「摩擦モデル」線としてプロットされ、このアプローチは界面強度のみからの凝着を仮定してプロットされました。これは破線「凝着モデル」線であり、データへのフィッティングは不十分です。」 (図 20)。
- 抜き勾配効果: 抜き勾配を大きくすると、摩擦モデルの予測と一致して排出力が大幅に減少しました。「抜き勾配の増加に伴い排出力が減少する傾向を示すが、合金に及ぼす影響はわずかなすべての排出力測定値をプロットしたもの」が図 18 に示されています。
- 高温排出と半田付け: 高温排出試験により、高温で半田付けが発生することが確認されました。「仮説は、高温排出試験によって部分的に確認されました。単一の鋳造サイクル内でアルミニウムがコアに凝着することが示されています (図 30)。」
- 3D シミュレーション検証: トレスカ摩擦係数を使用した 3D シミュレーションは、産業用ダイカストの例で半田付け位置を予測することに成功し、生産ツーリングで観察された半田付けパターンと一致しました。「半田付けの位置と相対的な深刻度は、この摩擦ベースの予測を使用して十分に予測されます。」 (図 35)。
- コーティングは摩擦を低減: AlCrN コーティングは摩擦係数を低減し、コーティングが摩擦を低減することによって主に固着を軽減することを示唆しています。「コーティングは摩擦係数を 0.59 から 0.5 に 18% 減少させました。これは、コーティングが固着を低減する主な理由が摩擦を低減することであることを示唆しています。」
- 統計的/定性的分析結果:
- 室温での合金の無意味さ: ペアスチューデントの t 検定の結果、室温で合金 362 と 380 の間の排出力に有意差がないことが示されました。「2 つの合金のデータに対してペアスチューデントの t 検定を実施したところ、ペアテストの t 統計量は 0.94 と計算されました。これは、95% 有意水準を仮定した場合の臨界値 1.71 より小さい値です。これは、362 と 380 の排出力が異ならないことを意味します…」
- 摩擦モデルの適合性: 摩擦モデルは、凝着専用モデルと比較して、実験データにより優れた適合性を提供しました。「最適なフィッティングは「摩擦モデル」で達成され、凝着項を追加しても改善されません。凝着専用モデルはデータと一致しません。」 (図 20)。
- データ解釈: 結果は、熱機械的干渉から生じる摩擦が、HPDC における固着および半田付け現象を含むアルミニウム凝着を引き起こす主要なメカニズムであるという仮説を強く支持しています。実験およびシミュレーションの結果は、HPDC における凝着は、速度論ベースの金属間化合物形成理論のみを考慮するよりも、摩擦モデルによってよりよく説明されることを示しています。接触圧力と排出温度は、凝着に影響を与える重要な要因として特定されました。
- 図リスト:
- Figure 1: The moving half of a typical die casting die [2].
- Figure 2: (a) An example of sticking. Both images courtesy of Mercury Marine. (b) An example of soldering on a die insert.
- Figure 3: Temperature dependence of the proposed dimensionless ejection force, Fej * and ejection shear stress, Tr.
- Figure 4: (a) Conceptual plot of the Coulomb model where the ejection stress is low relative to the part strength at low temperatures, and the part sticks to the die. (b) Conceptual plot at high temperature where all ejection stresses are large relative to the part strength, and the part fails. Figure adapted from Widerøe and Welo [15].
- Figure 5: Stages of soldering as proposed by Chu et al. in 1993 [9].
- Figure 6: Soldering that occurs on a die that has a non-reactive coating identified by Wang et al. [8]. Lubricant spray was reduced, but the soldering (red circles) and sticking still occur (Image courtesy of Mercury Marine).
- Figure 7: Conceptual casting for developing a thermomechanical theory of soldering and sticking. Radii smaller than ri are the die steel core, and radii greater than ro are the die steel mold.
- Figure 8: Schematic of the common thermodynamics and kinetics-based theory of soldering and sticking.
- Figure 9: The predicted time to grow a 0.1 mm thick intermetallic layer [78]–[80], [83], [84]. A single activation energy of 190 kJ/mol provides good agreement with measured reaction rates both above and below the melting temperature of 660°C
- Figure 10: (a) Illustration of a typical aluminum iron diffusion couple [78]. (b) One dimensional intermetallic growth rate when the liquid is either initially pure or saturated with iron [85].
- Figure 11: (a) Static steel cylinder (12.7 mm diameter) dip tests in various aluminum alloys showed that pure aluminum dissolves steel more slowly than commercial casting alloys [89]. (b) Static steel cylinder (12.7 mm diameter) dip tests showed that the structural alloy Silafont 36 (A367) dissolves steel slower than the more common A390 diecasting alloy [88].
- Figure 12: Illustration of joints between steel and aluminum under the shear of the ejection force, Fe without (a,b) and with an intermetallic layer (c,d). When the bond strength is low a clean separation at the aluminum/steel interface is normally observed (a) Casting failure may occur due to the low strength of aluminum at elevated temperature. (b). Roll bonded, brazed, and friction stir welded joints typically fracture within the intermetallic layer when it is present (c), while HPDC conditions often contain an intermetallic layer with the fracture in die casting (d).
- Figure 13: A simplified schematic based on Figure 3 where only the sticking factor is considered.
- Figure 14: Conceptual model of the casting/die interface where Fej is the ejection force and Ac is the total contact area. tAl, tej, and tFe are the shear strength of the casting, interface, and die, respectively.
- Figure 15: Different factors that affect the local contact area in the die casting process.
- Figure 16: Schematic of room temperature ejection mold.
- Figure 17: Image of the fixture for measuring the ejection force. The top and bottom of the fixture could pivot by a few degrees to correct for misalignment.
- Figure 18: A plot of all ejection force measurements showing a trend of decreasing ejection force with increasing draft angle but little effect of alloy.
- Figure 19: Schematic of core denoting the contact area used to fit (eq. 6) to the experimental data (Figure 18).
- Figure 20: The best fit is achieved with the “Friction Model” and is not improved by adding the adhesion term. The adhesion only model does not match the data.
- Figure 21: Image of all 7 cores after over 10 casting cycles showing no buildup from the cast aluminum.
- Figure 22: Comparison of AlCrN coated cores showing no difference between the smooth (Diamond Polished) and rough (220 Grit Stoned) surface preparation.
- Figure 23: Friction model fit to the AlCrN coated cores versus the uncoated cores. The 95% confidence interval based on a minimum of 6 experiments for each data point is shown.
- Figure 24: HPDC soldering occurs when the Tresca friction factor is larger than a critical value, and it decreases with lower ejection temperatures, (subset of Figure 3).
- Figure 25: The L-H relationship as proposed in eqs. 9 through 12. UTS was calculated assuming the onset of necking where N(T)/1 – М(Т).
- Figure 26: Bulk stress state prior to ejection due to the thermal interference between the casting and core.
- Figure 27: Thermal strain compared to the yield strain as calculated using an 0.002 offset of elastic modulus in eq. 18.
- Figure 28: Predicted soldering likelihood of a cylindrical casting (eq. 21) based on the alloy described in eq. 9 versus the ejection temperature.
- Figure 29: General assembly view of the hot ejection test apparatus the casting, core, sand mold, and support plate.
- Figure 30: (a) Example of experimental rig prepared for casting. (b) Incipient soldering clearly shown on the case where ejection occurred at 550°C.
- Figure 31: Casting surface for hot ejection test showing surface shrinkage (casting) and aluminum buildup (core).
- Figure 32: Rectangular example showing that the contact pressure is proportional to the thickness of the casting relative to the bearing area, Ac, on the core.
- Figure 33: Example die simulated in MAGMASOFT to test the validity of the Tresca friction factor to predict HPDC soldering.
- Figure 34: Second industrial HPDC example for comparison of the Tresca friction factor with HPDC soldering.
- Figure 35: Comparison of the contact pressure scaled by UTS in MAGMA (a) and (c) with the production die casting die at the end of a production run (b) and (d).
- Figure 36: Predicted soldering friction factor (right hand axis) vs simulation time. The temperatures at the same locations are plotted on the left-hand axis. Both locations exhibit increasing then decreasing soldering tendency related to the local temperature of the casting.
- Figure 37: Strength vs test temperature of typical wrought aluminum alloys in the as cast state [97]. UTS was assumed to occur at the onset of necking.
- Figure 38: The limits of ejection to avoid sticking and soldering. This is the axis-symmetric case of the general conceptual model proposed in the introduction (Figure 3).
- Figure 39: Density (a) and enthalpy (b) of the alloys in Table 4 as predicted by ThermoCalc equilibrium calculations [75]. Cumulative heat release (c) during solidification and cooling of the alloys. (d) Linearized thermal conductivity vs temperature for both alloys based on available literature measurements [100], [101].
- Figure 40: (a) Average casting temperature for a 12 mm tube casting with a 100 mm inner diameter. (b) Modeled contact pressure vs ejection time.
- Figure 41: A schematic that illustrates the limits on acceptable ejection times.
- Figure 42: Predicted average casting temperature (a) and ejection force (b) of the alloys from Table 4.
- Figure 43: Main effects plots for prediction of the range of possible ejection times for a core in a tubular casting of various, thickness, casting alloy, core diameter, initial die temperature.
- Figure 44: The main effect if die materials for the full factorial simulation. Different die materials are discerned by their thermal conductivity in Table 5.
- Figure 45: Enthalpy release of alloys in on a per volume basis during solidification and cooling.
- Figure 46: Soldering severity ranking from the NADCA Product Design Standards indicating A518 is castable but it has the worst die filling capacity and anti-solder capability [103].
- Figure 47: Cumulative heat release during solidification for A380 with 0.2 wt% iron and 0.2 wt% manganese compared to the same alloy with 1 wt% iron and 0.3 wt% manganese. There is a 3% reduction in heat released when iron and manganese are lowered.
![Figure 1: The moving half of a typical die casting die [2].](https://castman.co.kr/wp-content/uploads/image-145-1024x726.webp)
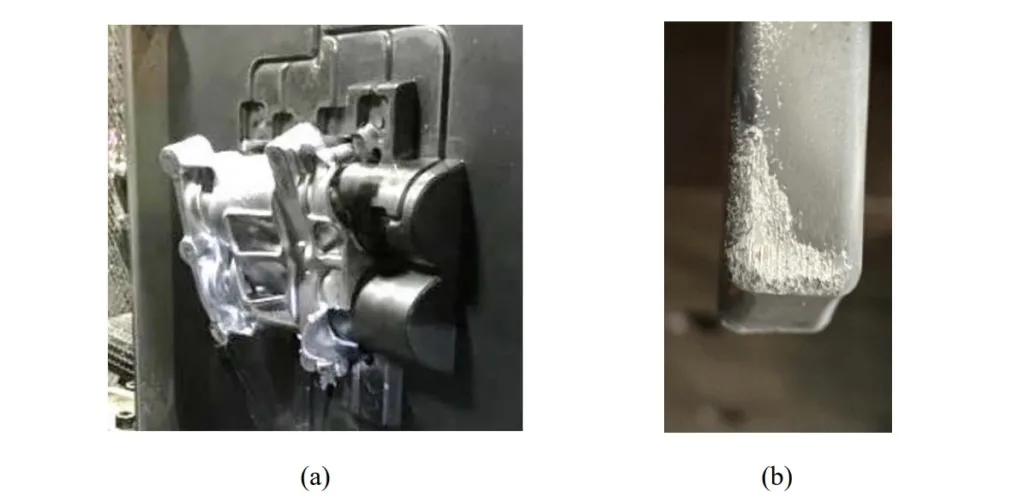
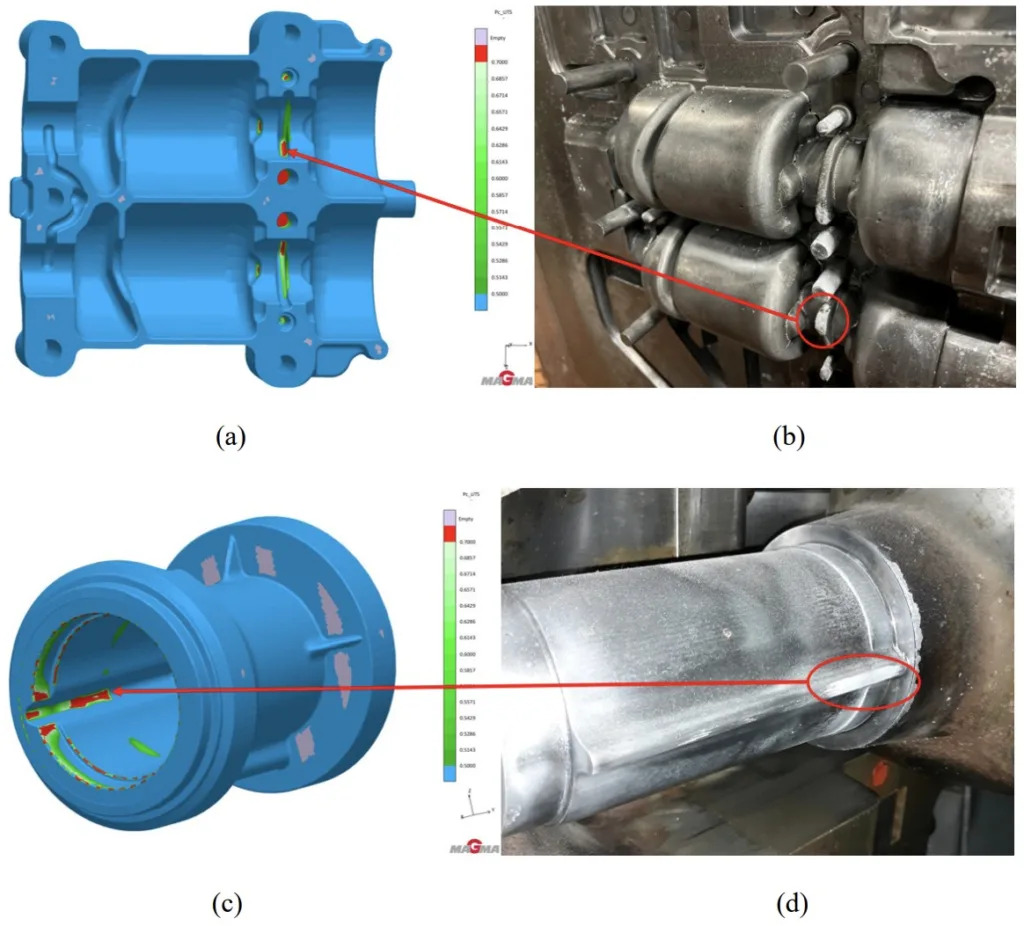
6. 結論と考察:
- 主な結果の要約: 本研究は、鋳造物と金型間の熱機械的干渉から生じる摩擦が、HPDC 金型へのアルミニウム凝着の主要なメカニズムであり、固着現象と半田付け現象の両方を包含するという結論に達しました。室温排出試験では、本質的な凝着力の証拠なしに、排出力が摩擦のような挙動を示すことが実証されました。高温排出試験と 3D シミュレーションは、半田付けが高いトレスカ摩擦係数に関連していることを示し、摩擦の役割をさらに検証しました。接触圧力を最小限に抑えることが、HPDC における凝着問題を軽減するための最も効果的な戦略として特定されました。
- 研究の学術的意義: 本研究は、速度論ベースの金属間化合物形成理論に有利なため、しばしば見過ごされてきた摩擦メカニズムの重要性を強調することにより、HPDC における凝着の理解に大きな変化をもたらします。本研究は、凝着を予測および軽減するための新しい熱機械的フレームワークを導入し、観察された現象に対するより包括的な説明を提供します。
- 実用的な意味合い: 本研究は、凝着を低減するために鋳造物排出温度を最大化し、接触圧力を最小化することに焦点を当てた HPDC プロセスのための最適な設計方法論を提供します。トレスカ摩擦係数を組み込んだ 3D シミュレーションツールの適用は、半田付け位置を予測し、金型とプロセス設計を最適化するために推奨されます。合金の選択とプロセスパラメータの調整は、摩擦モデルに基づいて、凝着を最小限に抑え、鋳造品質を向上させるように導くことができます。
- 研究の限界: 高温排出試験では、モデルで仮定した理想的な軸対称ケースから逸脱して、均一な接触を達成する上で課題に直面しました。高温排出実験でテストされた温度範囲は、ひずみ硬化係数の変動が限られており、それらの特定のテストにおける半田付け予測の感度に影響を与える可能性があります。
7. 今後のフォローアップ研究:
- 今後の研究方向: 今後の研究では、ダイ潤滑剤とコーティング、およびダイコアの表面仕上げの相互作用を調査して、凝着制御戦略をさらに洗練する必要があります。Al-Si 合金の高温機械的特性、特に鉄とマンガンの含有量を変化させた場合の特性に関するさらなる研究は、材料ベースの凝着低減ソリューションを強化するために保証されています。摩擦を低減することを目的としたダイコーティングの継続的な開発とテストも重要です。
- さらなる探求が必要な領域: 摩擦せん断応力に抵抗するために高温強度を高めることに焦点を当てた合金最適化戦略は、さらなる調査が必要な領域です。熱伝達を管理し、鋳造が困難な合金の固着傾向を低減するために、低熱伝導率の金型材料を利用する可能性について、さらに検討する必要があります。
8. 参考文献:
- [1] S. P. Udvardy, “2019 State of the Die Casting Industry,” Die Casting Engineer, no. January, p. 6, 2019.
- [2] 2018 Product Specification Standards for Die Castings, 2018th ed. North American Die Casting Association.
- [3] R. J. Donahue and G. K. Sigworth, “Die Casting Alloys that will Allow the Die Caster to Compete with Alloys A356, A357, 358 and 359 in PM Applications,” p. 17.
- [4] Aoyama, Shunzo, Akase, Makota, Sakamoto, Katsumi, and Umemura, Teruyoshi, “Die Lubricant Deposit and Its Effect on Ejection in Die Casting,” vol. T91-112.
- [5] R. A. Miller, “Fluidity from a Heat Transfer Perspective,” in NADCA Transactions, Ohio, Sep. 2016, vol. T16-081. Accessed: Apr. 10, 2018. [Online]. Available: https://www.diecasting.org/archive/transactions/T16-081.pdf
- [6] R. N. Lumley, I. J. Polmear, H. Groot, and J. Ferrier, “Thermal characteristics of heat-treated aluminum high-pressure die-castings,” Scr. Mater., vol. 58, no. 11, pp. 1006–1009, Jun. 2008, doi: 10.1016/j.scriptamat.2008.01.031.
- [7] D. Blondheim, Jr. and A. Monroe, “Macro Porosity Formation - A Study in High Pressure Die Casting,” Int. J. Met., 2021, doi: https://doi.org/10.1007/s40962-021-00602-x.
- [8] B. Wang, G. R. Bourne, A. L. Korenyi-Both, S. P. Midson, and M. J. Kaufman, “An investigation of the use of PVD die coatings to minimize or eliminate lubrication during high pressure die casting,” in North American Die Casting Congress, 2016, vol. T16-061.
- [9] Chu, Yeou-Li, Cheng, Patrick, and Shivpuri, Rajiv, “Soldering Phenomenon in Aluminum Die Casting: Possible Causes and Cures,” in North American Die Casting Congress, Cleveland, OH, Oct. 1993, pp. 361–372.
- [10] Tosa, Hiroki and Urakami, Akio, “Factors Influencing Die Casting Ejection," in North American Die Casting Congress, Chicago, IL, 1972, vol. T72-041.
- [11] B. Wang, G. R. Bourne, A. L. Korenyi-Both, A. K. Monroe, S. P. Midson, and M. J. Kaufman, “Method to evaluate the adhesion behavior of aluminum-based alloys on various materials and coatings for lube-free die casting,” J. Mater. Process. Technol., vol. 237, pp. 386–393, 2016, doi: 10.1016/j.jmatprotec.2016.06.031.
- [12] S.-B. Kim, Y.-H. Yim, and D.-H. Roh, “Prediction of Die Soldering in Die Casting by a Numerical Algorithm based on the Combination of Thermal and Fluid Factors Verified with Experimental Results,” in Die Casting Congress and Tabletop, Cleveland, OH, 2019, p. 9.
- [13] K. Domkin, J. H. Hattel, and J. Thorborg, “Modeling of high temperature- and diffusion-controlled die soldering in aluminum high pressure die casting,” J. Mater. Process. Technol., vol. 209, no. 8, pp. 4051–4061, 2009, doi: 10.1016/j.jmatprotec.2008.09.031.
- [14] D. Tabor, “Friction - the present state of our understanding,” J. Lubr. Technol., vol. 103, no. 2, pp. 169–179, Apr. 1981.
- [15] F. Widerøe and T. Welo, “Conditions for Sticking Friction between Aluminium Alloy AA6060 and Tool Steel in Hot Forming,” Key Eng. Mater., vol. 491, pp. 121-128, Sep. 2011, doi: 10.4028/www.scientific.net/KEM.491.121.
- [16] H. Wang and C. A. Loong, “Experimental Studies on Ejection FORCES of a die cast Aluminum Part,” in North American Die Casting Congress, Cleveland, OH, 1999, vol. T99-052.
- [17] M. J. Roy, D. M. Maijer, and L. Dancoine, “Constitutive behavior of as-cast A356," Mater. Sci. Eng. A, vol. 548, pp. 195–205, Jun. 2012, doi: 10.1016/j.msea.2012.03.106.
- [18] Shankar, Samantha and Apelian, Diran, “Die Soldering: Mechanism of the interface reaction between molten aluminum alloy and tool steel,” vol. 33B, no. June 2002, pp. 465–476, doi: 10.1007/s11663-002-0057-7.
- [19] ASM Handbook: Welding, Brazing, and Soldering, vol. 6. ASM International (R), Materials Park, Ohio, USA, 1993.
- [20] A. Long, D. Thornhill, C. Armstrong, and D. Watson, “Predicting die life from die temperature for high pressure dies casting aluminium alloy,” Appl. Therm. Eng., vol. 44, pp. 100–107, Nov. 2012, doi: 10.1016/j.applthermaleng.2012.03.045.
- [21] A. Long, D. Thornhill, C. Armstrong, and D. Watson, “Determination of the heat transfer coefficient at the metal–die interface for high pressure die cast AlSi9Cu3Fe," Appl. Therm. Eng., vol. 31, no. 17–18, pp. 3996–4006, Dec. 2011, doi: 10.1016/j.applthermaleng.2011.07.052.
- [22] Z. W. Chen, “Formation and progression of die soldering during high pressure die casting,” Mater. Sci. Eng. A, vol. 397, no. 1–2, pp. 356–369, 2005, doi: 10.1016/j.msea.2005.02.057.
- [23] Y. Zhu, D. Schwam, J. F. Wallace, and S. Birceanu, “Evaluation of soldering, washout and thermal fatigue resistance of advanced metal materials for aluminum die-casting dies,” Mater. Sci. Eng. A, vol. 379, no. 1–2, pp. 420–431, 2004, doi: 10.1016/j.msea.2004.03.020.
- [24] Chu, Yeou-Li, Balasubramaniam, Srikanth, Rajan, Rajendra, and Shivpuri, Rajiv, "A Study of the Cast Alloy-Die Surface Interactions in Aluminum Die Casting,” in North American Die Casting Congress, Minneapolis, MN, 1997, vol. T97-075. [Online]. Available: https://diecasting.org/wcm/Technology/Technical_Archive/wcm/Technology/Technical_Archive.aspx?hkey=62f825ba-424c-41c3-b10f-3b860771ffa4
- [25] S. Gulizia, M. Z. Jahedi, and E. D. Doyle, “Performance evaluation of PVD coatings for high pressure die casting,” Surf. Coat. Technol., vol. 140, no. 3, pp. 200-205, Jun. 2001, doi: 10.1016/S0257-8972(01)01037-4.
- [26] Hairy, P. and Richard, M., “Reduction of Sticking in Pressure Die Casting by Surface Treatment,” in North American Die Casting Congress, 1997, vol. T97-102.
- [27] K. Bobzin, T. Brögelmann, U. Hartmann, and N. C. Kruppe, "Analysis of CrN/AlN/Al2O3 and two industrially used coatings deposited on die casting cores after application in an aluminum die casting machine,” Surf. Coat. Technol., vol. 308, pp. 374-382, Dec. 2016, doi: 10.1016/j.surfcoat.2016.09.040.
- [28] Q. Han and S. Viswanathan, “Analysis of the Mechanism of Die Soldering in Aluminum Die Casting,” Metall. Mater. Trans. A, vol. 34A, no. January, pp. 139–146, 2003.
- [29] Shankar, Sumanth and Apelian, Diran, “Mechanism and Preventive Measures for Die Soldering during Al Casting in a Ferrous Mold,” JOM, vol. 54, no. August 2002, pp. 47–54, doi: 10.1007/BF02711867.
- [30] C. Mitterer, F. Holler, F. Üstel, and D. Heim, "Application of hard coatings in aluminium die casting – soldering, erosion and thermal fatigue behaviour,” Surf. Coat. Technol., vol. 125, no. 1–3, pp. 233–239, Mar. 2000, doi: 10.1016/S0257-8972(99)00557-5.
- [31] Norstrom, Lars-Ake, Klarenfjord, Bengt, and Svensson, Maths, “General Aspects on 'Washout' Mechanisms in Aluminum Die Casting Dies," 1993, vol. T93-075–1.
- [32] M. Yu, R. Shivpuri, and R. A. Rapp, “Effects of Molten Aluminum on H13 Dies and Coatings,” J. Mater. Eng. Perform., vol. 4, no. 2, pp. 175–181, Apr. 1995.
- [33] R. J. Barnhurst, D. Argo, and W. Walkington, “NADCA Sponsored Research: The Causes of Soldering in Zinc Die Casting,” in Die Casting Congress, 1997, vol. T97-033.
- [34] M. Stern, “PROGRESS_OF_DIE-CASTING_INDUSTRY,” in Transactions of the American Foundrymen's Association, 1930, vol. 37, pp. 723–733.
- [35] W. Bonsack, “Trends in Aluminum Casting Alloys,” in Transactions of the American Foundrymen's Association, 1950, vol. 76, pp. 69–75.
- [36] D. L. Colwell and E. Trela, “New Aluminum Die Casting Alloys,” in Transactions of the American Foundrymen's Association, 1954, vol. 93, pp. 359–364.
- [37] D. L. Colwell and O. Tichy, “Machinability of Aluminum Die Castings,” in Transactions of the American Foundrymen's Association, 1956, vol. 92, pp. 236–241.
- [38] S. U. Siena, “Die Casting Aluminum Alloys by the Cold Chamber Process,” 1944.
- [39] W. Bonsack, “Iron-The Problematic Factor in Quality Of Aluminum Alloy Die Castings," in Transactions of the American Foundrymen's Association, 1961, vol. 114, pp. 712-720.
- [40] Holz, Earl K., “Trouble Shooting Aluminum Die Casting Quality Problems,” in 7th SDCE International Die Casting Congress, Chicago, IL, 1972, vol. T72-043.
- [41] Kajoch, Wladyslaw and Fajkiel, Alexander, “Testing the Soldering Tendencies of Aluminum Die Casting Alloy,” in North American Die Casting Congress, Detroit, MI, Oct. 1991, vol. T91-034, pp. 67–74.
- [42] W. Jonsson, “THE EFFECT OF IRON AND MAGNESIUM ON TEH PROPERTIES OF ALUMINUM DIE CASTING ALLOYS,” Nov. 1964, p. 8.
- [43] Chu, Yeou-Li, Cheng, Patrick, and Shivpuri, Rajiv, “Investigation of the soldering problem in aluminum die casting - Phenomena, mechanism and protection,” National Science Foundation Engineering Research Center for Net Shape Manufacturing, NADCA Technical Archive, ERC/NSM-C-93-36, Sep. 1993.
- [44] Y. Tsuchiya, H. Kawaura, K. Hashimoto, H. Inagaki, and T. Arai, “Core Pin Failure in Aluminum Die Casting and the Effect of Surface Treatment,” in The Many Faces of Die Casting, Minneapolis, MN, 1997, vol. T97-103.
- [45] Z. W. Chen, D. T. Fraser, and M. Z. Jahedi, “Structures of intermetallic phases formed during immersion of H13 tool steel in an Al–11Si–3Cu die casting alloy melt," Mater. Sci. Eng. A, vol. 260, no. 1–2, pp. 188–196, Feb. 1999, doi: 10.1016/S0921-5093(98)00963-0.
- [46] R. J. Barnhurst, D. Argo, and W. Walkington, “NADCA Sponsored Research: The Causes of Soldering in Zinc Die Casting,” in Die Casting Congress, 1997, vol. T97-033.
- [47] J. Song, X. Wang, T. DenOuden, and Q. Han, “Evolution of Intermetallic Phases in Soldering of the Die Casting of Aluminum Alloys,” Metall. Mater. Trans. A, vol. 47, no. 6, pp. 2609–2615, 2016, doi: 10.1007/s11661-016-3454-2.
- [48] A. Duarte, F. J. Oliveira, and F. M. Costa, “Characterisation of interface formed at 650°C between AISI H13 steel and Al–12Si–1Cu aluminium melt," Int. J. Cast Met. Res., vol. 23, no. 4, pp. 231–239, Aug. 2010, doi: 10.1179/136404610X12665088537455.
- [49] S. Sumanth and A. Diran, “The Role of Aluminum Alloy Chemistry and Die Material on Die Soldering,” in North American Die Casting Congress, Cleveland, OH, 1999, vol. T99-083. [Online]. Available: https://diecasting.org/wcm/Technology/Technical_Archive/wcm/Technology/Technical_Archive.aspx?hkey=62f825ba-424c-41c3-b10f-3b860771ffa4
- [50] M. Vilaseca, S. Molas, and D. Casellas, “High temperature tribological behaviour of tool steels during sliding against aluminium,” Wear, 2011, doi: 10.1016/j.wear.2011.07.007.
- [51] P. Terek et al., “Effects of die core treatments and surface finishes on the sticking and galling tendency of Al-Si alloy casting during ejection,” Wear, vol. 356–357, pp. 122-134, Jun. 2016, doi: https://doi.org/10.1016/j.wear.2016.03.016.
- [52] H. Cagin, “Techniques for Removing Stuck Castings," in NADCA Transactions, Jun. 1981, vol. T81-025, p. 4.
- [53] P. Terek et al., “The Influence of CrAlN Coating Chemical Composition on Soldering Resistance in Contact with Al-Si-Cu Alloy,” Mater. Proc., vol. 2, no. 1, p. 28, May 2020, doi: 10.3390/CIWC2020-06837.
- [54] P. Terek, L. Kovačević, A. Miletić, D. Kukuruzović, S. Baloš, and B. Škorić, "Improved ejection test for evaluation of soldering tendency of cast alloy to die core materials,” J. Mater. Process. Technol., vol. 266, pp. 114–124, Apr. 2019, doi: 10.1016/j.jmatprotec.2018.10.038.
- [55] Chen, Z. W. and Jahedi, M. Z., “Die erosion and its effect on soldering formation in high pressure die casting of aluminum alloys,” Mater. Des., vol. 20, pp. 303-309, 1999.
- [56] J. Jerina and M. Kalin, “Initiation and evolution of the aluminium-alloy transfer on hot-work tool steel at temperatures from 20 °C to 500 °C,” Wear, vol. 319, no. 1–2, pp. 234-244, Nov. 2014, doi: 10.1016/j.wear.2014.07.021.
- [57] R. Kimura, M. Yoshida, G. Sasaki, J. Pan, and H. Fukunaga, “Characterization of heat insulating and lubricating ability of powder lubricants for clean and high quality die casting,” J. Mater. Process. Technol., vol. 130–131, pp. 289–293, Dec. 2002, doi: 10.1016/S0924-0136(02)00808-7.
- [58] N. Nishi, “Challenge to Ultra Thin-Wall Zinc Die Casting under 0.5 mm Thickness," Cast. Eng., no. September 2007, p. 5, 2007.
- [59] MAGMAsoft. Kackerstrasse 11, 52072 Aachen, Germany: MAGMA Gmbh, 2019.
- [60] T. Cedorge and J. Colton, “Draft angle and surface roughness effects on sterolighography molds," Polym. Eng. Sci. Newtown, vol. 40, no. 7, p. 1581, Jul. 2000.
- [61] A. E. Palmer and J. S. Colton, “Failure mechanisms in stereolithography injection molding tooling,” Polym. Eng. Sci., vol. 40, no. 6, pp. 1395–1404, Jun. 2000, doi: 10.1002/pen.11269.
- [62] G. T. Pham and J. S. Colton, “Ejection force modeling for stereolithography injection molding tools,” Polym. Eng. Sci., vol. 42, no. 4, pp. 681–693, Apr. 2002, doi: 10.1002/pen.10981.
- [63] B. Omar and K. Barney, “Prediction of Local Part-Mold and Ejection Force in Injection Molding,” Trans. ASME, vol. 127, no. August 2005, pp. 598–604, Aug. 2005, doi: 10.1115/1.1951785.
- [64] S. Tetsuo, K. Nobuhiro, S. Kenji, K. Yoshikazu, and T. Ayumu, “An experimental study on ejection forces of injection molding,” J. Int. Soc. Precis. Eng. Nanotechnol., vol. 24, pp. 270–273, 2000, doi: 0141-6359/00/.
- [65] M. Sorgato, D. Masato, and G. Lucchetta, “Effects of machined cavity texture on ejection force in micro injection molding,” Precis. Eng., vol. 50, pp. 440–448, 2017, doi: 10.1016/j.precisioneng.2017.06.019.
- [66] Monroe, Alexander, Gaddam, Deepika, and Glim, Beau, “Preliminary Study on Ejection Force Prediction,” NADCA Congr. Tabletop, vol. T16-083, 2016.
- [67] A. L. ALTIERI and P. H. STEEN, “Adhesion Upon Solidification and Detachment in the Melt Spinning of Metals,” Metall. Mater. Trans. B, vol. VOLUME 45B, pp. 2262-2268, Dec. 2014, doi: 10.1007/s11663-014-0128-6.
- [68] M. D. Hanna, “Tribological evaluation of aluminum and magnesium sheet forming at high temperatures,” Wear, vol. 267, no. 5–8, pp. 1046–1050, Jun. 2009, doi: 10.1016/j.wear.2009.01.007.
- [69] H. Kitano, K. Dohda, M. Kalin, and K. F. Ehmann, “Galling growth analysis in metal forming,” Manuf. Lett., vol. 16, pp. 32–35, Apr. 2018, doi: 10.1016/j.mfglet.2018.03.003.
- [70] E. Huttunen-Saarivirta, L. Kilpi, T. J. Hakala, J. Metsäjoki, and H. Ronkainen, "Insights into the behaviour of tool steel-aluminium alloy tribopair at different temperatures,” Tribol. Int., vol. 119, pp. 567–584, Mar. 2018, doi: 10.1016/j.triboint.2017.11.041.
- [71] L. Wang and H. Yang, “Friction in aluminium extrusion—part 2: A review of friction models for aluminium extrusion,” Tribol. Int., vol. 56, pp. 99–106, Dec. 2012, doi: 10.1016/j.triboint.2012.06.006.
- [72] X. Ma, M. de Rooij, and D. Schipper, “A load dependent friction model for fully plastic contact conditions,” Wear, vol. 269, no. 11–12, pp. 790–796, Oct. 2010, doi: 10.1016/j.wear.2010.08.005.
- [73] X. Ma, M. B. de Rooij, and D. J. Schipper, “Friction conditions in the bearing area of an aluminium extrusion process,” Wear, vol. 278–279, pp. 1–8, Mar. 2012, doi: 10.1016/j.wear.2011.11.001.
- [74] L. Wang, J. Zhou, J. Duszczyk, and L. Katgerman, “Friction in aluminium extrusion-Part 1: A review of friction testing techniques for aluminium
- [75] J. Shigley, C. Mischke, and R. Budynas, Mechanical Engineering Design, 7th Edition. McGraw-Hill, 2004.
- [76] MATLAB. Natick, Massachusetts: Mathworks, 2020.
- [77] J. O. Andersson, T. Helander, P. F. Shi, and B. Sundman, Thermo-Calc and DICTRA, Computational tools for material science. 2002.
- [78] H. Springer, A. Kostka, J. F. dos Santos, and D. Raabe, “Influence of intermetallic phases and Kirkendall-porosity on the mechanical properties of joints between steel and aluminium alloys,” Mater. Sci. Eng. A, vol. 528, no. 13–14, pp. 4630–4642, May 2011, doi: 10.1016/j.msea.2011.02.057.
- [79] H. Springer, A. Kostka, E. J. Payton, D. Raabe, A. Kaysser-Pyzalla, and G. Eggeler, “On the formation and growth of intermetallic phases during interdiffusion between low-carbon steel and aluminum alloys,” Acta Mater., vol. 59, no. 4, pp. 1586–1600, Feb. 2011, doi: 10.1016/j.actamat.2010.11.023.
- [80] V. Jindal, V. C. Srivastava, A. Das, and R. N. Ghosh, “Reactive diffusion in the roll bonded iron-aluminum system,” Mater. Lett., vol. 60, no. 13–14, pp. 1758–1761, Jun. 2006, doi: 10.1016/j.matlet.2005.12.013.
- [81] Z. W. Chen, “Formation and progression of die soldering during high pressure die casting,” Mater. Sci. Eng. A, vol. 397, no. 1–2, pp. 356–369, 2005, doi: 10.1016/j.msea.2005.02.057.
- [82] C. Z. W., J. M.Z., and L. J.A., “Metallurgical Phenomena in Die/Casting Interfacial Regions During High Pressure Die Casting of Aluminum Alloys,” in North American Die Casting Congress, Cleveland, OH, 1999, vol. T99-084.
- [83] A. Bouayad, C. Gerometta, A. Belkebir, and A. Ambari, “Kinetic interactions between solid iron and molten aluminium,” Mater. Sci. Eng. A, vol. 363, no. 1–2, pp. 53-61, Dec. 2003, doi: 10.1016/S0921-5093(03)00469-6.
- [84] F. Yin, M. Zhao, Y. Liu, W. Han, and Z. Li, “Effect of Si on growth kinetics of intermetallic compounds during reaction between solid iron and molten aluminum," Trans. Nonferrous Met. Soc. China, vol. 23, no. 2, pp. 556–561, Feb. 2013, doi: 10.1016/S1003-6326(13)62499-1.
- [85] G. Eggeler, W. Auer, and H. Kaesche, “REACTIONS BETWEEN LOW ALLOYED STEEL AND INITIALLY PURE AS WELL AS IRON-SATURATED ALUMINUM MELTS BETWEEN 670 AND 800-DEGREES-C," Z. Met., vol. 77, no. 4, pp. 239–244, 1986.
- [86] Makhlouf M. Makhlouf and Diran Apelian, “Casting Characteristics of Aluminum Die Casting Alloys,” DOE/ID/13716, 792701, Feb. 2002. doi: 10.2172/792701.
- [87] A. Zovi and F. Casarotto, “SILAFONT-36, THE LOW IRON DUCTILE DIE CASTING ALLOY DEVELOPMENT AND APPLICATIONS,” Metall. Ital., 2007, [Online]. Available: https://www.fracturae.com/index.php/aim/article/view/517/488
- [88] Chu, Yeou-Li, Balasubramaniam, Srikanth, Rajan, Rajendra, and Shivpuri, Rajiv, "A Study of the Cast Alloy-Die Surface Interactions in Aluminum Die Casting," vol. T97-075, 1997.
- [89] Yu, Mulong, Chu, Yeou-Li, and Shivpuri, Rajiv, “A Study of Corrosion of Die Materials and Die Coatings in Aluminum Die Casting,” in North American Die Casting Congress, Cleveland, OH, Oct. 1993, vol. T93-072, pp. 191–198.
- [90] M. Movahedi, A. H. Kokabi, and S. M. Seyed Reihani, “Investigation on the bond strength of Al-1100/St-12 roll bonded sheets, optimization and characterization,” Mater. Des., vol. 32, no. 6, pp. 3143–3149, Jun. 2011, doi: 10.1016/j.matdes.2011.02.057.
- [91] M. Roulin and J. W. Luster, “Strength and Structure of Furnace-Brazed Joints between Aluminum and Stainless Steel,” Weld. Res. Suppl., vol. 78, no. 5, pp. 151-155, May 1999.
- [92] J. Vrenken, C. Goos, T. Veldt, and W. Braunschweig, “Fluxless Laser Brazing of Aluminium to Steel,” Join. Automot. Eng., 2009, [Online]. Available: Fluxless Laser Brazing of Aluminium to Steel
- [93] Tosa, Hiroki and Urakami, Akio, “Factors Influencing Die Casting Ejection,” in North American Die Casting Congress, Chicago, IL, Oct. 1972, vol. T72-041.
- [94] "Buhler Evolution Die Casting Machine Brochure.” Buhler. Accessed: May 01, 2021. [Online]. Available: https://www.buhlergroup.com/content/buhlergroup/global/en/products/evolution_die-castingmachineevolution.html
- [95] J. Lu, Y. Song, L. Hua, P. Zhou, and G. Xie, “Effect of temperature on friction and galling behavior of 7075 aluminum alloy sheet based on ball-on-plate sliding test,” Tribol. Int., vol. 140, p. 105872, Dec. 2019, doi: 10.1016/j.triboint.2019.105872.
- [96] C. M. Estey, S. L. Cockcroft, D. M. Maijer, and C. Hermesmann, “Constitutive behaviour of A356 during the quenching operation,” Mater. Sci. Eng. A, vol. 383, no. 2, pp. 245-251, Oct. 2004, doi: 10.1016/j.msea.2004.06.004.
- [97] A. Alankar and M. A. Wells, “Constitutive behavior of as-cast aluminum alloys AA3104, AA5182 and AA6111 at below solidus temperatures,” Mater. Sci. Eng. A, vol. 527, no. 29–30, pp. 7812–7820, Nov. 2010, doi: 10.1016/j.msea.2010.08.056.
- [98] C. H. Cáceres, “A Rationale for the Quality Index of Al-Si-Mg Casting Alloys,” p. 17, 1998.
- [99] F. A. Nichols, “Plastic instabilities and uniaxial tensile ductilities,” Acta Metall., vol. 28, no. 6, pp. 663–673, Jun. 1980, doi: 10.1016/0001-6160(80)90144-3.
- [100] R. Overfelt, S. Bakhtiyarov, and R. Taylor, “Thermophysical properties of A201, A319, and A356 aluminium casting alloys,” High Temp.-High Press., vol. 34, no. 4, pp. 401–409, 2002, doi: 10.1068/htjr052.
- [101] R. Brandt and G. Neuer, “Electrical Resistivity and Thermal Conductivity of Pure Aluminum and Aluminum Alloys up to and above the Melting Temperature," Int. J. Thermophys., vol. 28, no. 5, pp. 1429–1446, Nov. 2007, doi: 10.1007/s10765-006-0144-0.
- [102] J. A. Dantzig and M. Rappaz, Solidification, 1 st. EPFL Press, 2009.
- [103] P. Brancaleon, “Specifications and Standards Development for Enhanced Casting Performance through Examination of Mechanical Properties versus Casting Section Thickness,” in NADCA Transactions, Virtual Event, 2020, p. 7.
9. 著作権:
- 本資料は、アレックス・モンローの論文: [論文タイトル] に基づいています。
- 論文ソース: DOI URL
本資料は上記の論文に基づいて要約されたものであり、商業目的での無断使用は禁止されています。
Copyright © 2025 CASTMAN. All rights reserved.