本紹介資料は、「Eastern-European Journal of Enterprise Technologies」によって発行された論文「Enhancing side die resistance to thermal shock in automotive casting: a comparative study of FCD550 and SKD6 materials」に基づいています。
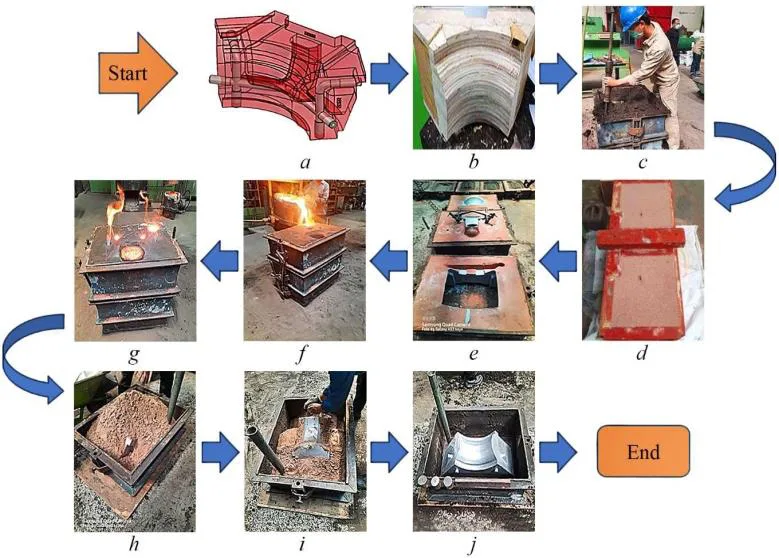
1. 概要:
- 論文タイトル: Enhancing side die resistance to thermal shock in automotive casting: a comparative study of FCD550 and SKD6 materials (自動車鋳造における熱衝撃に対するサイドダイの耐性向上:FCD550およびSKD6材料の比較研究)
- 著者: Herry Patria, Iwan Susanto, Belyamin, Dianta Mustofa Kamal
- 発行年: 2024
- 発行元ジャーナル/学会名: Eastern-European Journal of Enterprise Technologies
- キーワード: thermal shock (熱衝撃), die disc car wheel (ダイディスク自動車ホイール), manufacturing (製造), automotive parts (自動車部品), casting productivity (鋳造生産性)
2. アブストラクト:
金型ディスク自動車用途において、FCD550材をSKD6材に置換することにより、サイドダイの熱衝撃耐性を向上させた。主な課題は、生産プロセスの加速によって誘発される熱衝撃によるサイドダイの亀裂であり、これが生産停止や大量の顧客注文への未達につながっていた。本研究は、FCD550よりも熱衝撃によく耐える材料を特定し、それによってサイドダイの耐久性と製造プロセスの全体的な生産性を向上させることを目的とする。研究には、直接生産実験、FCD550およびSKD6材料の分析、ダイ特性の評価、材料変更前後の最終製品属性の評価が含まれた。実験室試験および機械設定トライアルを実施し、生産プロセスを変化させて結果を評価した。結果は、SKD6が金型ディスク自動車用途においてFCD550よりも熱衝撃に対して著しく耐性があることを示している。本研究では、データシートを用いてサイドダイ材料の強度を比較し、既存の冷却条件下で設定パラメータを調整した。実験では、標準温度を520–545 °Cから532–538 °Cに変更し、ソーク時間(soaking time)を最低270–540秒から332秒に短縮した。これにより、ソーク時間が69秒から46秒に、エージング時間(aging time)が190秒から180秒に短縮され、7台の機械全体での鋳造生産性が28日あたり194,870個から213,311個に増加し、サイドダイの亀裂なしに28日あたり200,000個という顧客の要求を満たした。TSD5605G規格に従った5つの製品サンプルの耐久性試験により、品質が顧客仕様を満たしていることが確認された。
3. 序論:
自動車部品製造における材料の熱衝撃耐性の研究は、特に車両が高度化し、厳しい条件に耐える部品への要求が高まる中で、その重要性は非常に大きい[1]。これらの重要な部品の中でも、ディスク自動車ホイールは、大きな荷重と繰り返しの応力に耐える中心的な役割を担っている[2]。その完全性を確保することは、車両性能だけでなく、安全基準の遵守にも不可欠である。製造会社は、高い販売注文と生産性向上の必要性に応えるため、製品品質を維持しながら生産プロセスを最適化するという課題に直面している。しかし、この効率追求は、製造プロセスにおけるサイドダイの亀裂発生に見られるように、意図せずに新たな課題を引き起こす可能性がある。顧客の要求を満たすことを目的とした生産方法の加速は、サイドダイ領域内で熱衝撃問題を引き起こし、亀裂や製品品質の低下を招いている[3]。これらの課題に対処するためには、熱衝撃を理解することが最も重要である。急激な温度変化は材料に機械的応力を誘発し、構造破壊につながる可能性がある[4]。したがって、サイドダイのような金型材料の熱衝撃耐性を向上させることは、生産能力を強化し、製品の完全性を維持するために不可欠である。本研究では、従来のFCD550材料と、向上した熱衝撃耐性を含む有望な特性を持つSKD6合金を比較することにより、サイドダイの熱衝撃耐性を向上させる方法を調査し、製造効率と部品の耐久性を改善することを目指す。
4. 研究概要:
研究テーマの背景:
自動車ホイールディスクのような自動車部品には、高い耐久性と動作応力に対する耐性が求められる。生産要求の増加は、製造プロセスの加速を必要とするが、これがダイカスト金型、特にサイドダイ領域において熱衝撃を引き起こし、亀裂や生産停止につながる可能性がある[3]。本研究の対象は、自動車ホイールディスク製品の生産に使用されるサイドダイの熱衝撃耐性である。
先行研究の状況:
先行研究では、ダイ材料における微小亀裂や関連現象[5]が特定され、熱伝導率[6]、焼戻し効果[7]、熱応力モデリング[10]などの側面が調査されてきた。しかし、加速された鋳造プロセスにおける熱衝撃によって直接引き起こされる亀裂という特定の問題は、大部分が未解決のままであった[9, 10]。SKD6鋼の特性(高熱動作性、良好な靭性、耐侵食性)は知られているが[10, 11, 12]、この特定の用途においてFCD550と比較して熱衝撃を緩和する潜在能力は評価が必要であった。
研究目的:
本研究の目的は、PSD3Kディスク自動車ホイールタイプ製品の生産において、サイドダイの熱衝撃耐性を向上させ、それによって製品の完全性と品質を維持しながら製造プロセスを加速することである。目的は以下の通りであった:
- FCD550の代替としてSKD6鋼の適合性に焦点を当て、優れた熱衝撃耐性を持つ材料を特定し評価すること。
- 熱応力を緩和することを目的とした高度な冷却システムを組み込んだ新しいサイドダイを設計すること。
- ダイカストマシンの設定(射出速度、金型温度、冷却速度など)を修正し、プロセスを最適化すること。
研究の核心:
本研究は、ディスク自動車ホイール鋳造用のサイドダイ用途におけるFCD550とSKD6材料の比較分析を行った。材料選定は、熱衝撃耐性に関連する特性(硬度、組成、特にバナジウム含有量)に焦点を当てた標準データシート(表1-4)の比較に基づいて行われた。SKD6が選定された。SKD6を用いてサイドダイを製作し(図1、図2)、その化学組成を検証した(表5)。冷却システムのコンセプトを視覚化した(図3)。ダイカストマシンを用いて実験的トライアルを実施し、FCD550とSKD6サイドダイの性能を比較した。初期トライアルでは既存の設定を使用し、その後SKD6ダイ用にパラメータ(温度、ソーク/エージング時間)を最適化した(表6、図8)。性能は、ダイと製品の目視検査、硬さ試験(図6)、微細構造分析(図5)、気孔率シミュレーション(図7)、サイクルタイム測定、およびTSD5605G規格に従った最終製品品質試験を通じて評価された。
5. 研究方法
研究デザイン:
本研究では比較実験デザインを採用した。以下の内容を含む:
- 文献およびデータシート比較に基づく材料選定(FCD550 vs. SKD6)。
- 選定された材料(SKD6)によるサイドダイの製作。
- サイドダイ用冷却システムコンセプトの設計と実装。
- ダイカストマシンでの直接生産実験の実施、FCD550とSKD6サイドダイの性能比較。
- SKD6材料に対する機械設定パラメータの最適化。
- 材料試験、プロセスモニタリング、製品品質評価による結果の検証。
データ収集・分析方法:
- 材料特性: 標準データシート(JIS G 5502, JIS G4404)を用いた比較。
- 製作ダイ検証: 化学組成分析(ARL 3460 OES)、硬さ試験(ZHU250CL)、微細構造分析(GX53顕微鏡、ESTM 155規格)。
- プロセス性能: ダイカストマシンパラメータ(温度、時間)の記録、サイクルタイム測定、亀裂に関するダイの目視検査、生産量カウント。
- シミュレーション: 気孔率可視化(図7からMAGMAソフトウェアの使用が示唆される)。
- 製品品質: 寸法検査(CMM Crystal Apex C7106)、耐久性試験(衝撃試験13°および90°、モーメント寿命試験(CFT)、ドラム試験(RFT)) - トヨタ技術標準TSD5605G準拠。
研究対象と範囲:
本研究は、自動車ディスクホイール(PSD3Kタイプ)の高圧ダイカストに使用されるサイドダイの熱衝撃耐性向上に特化して焦点を当てた。範囲は以下を含む:
- FCD550およびSKD6材料の比較評価。
- 修正された冷却システム設計の影響評価。
- ダイカストマシン設定(温度、ソーク時間、エージング時間)の最適化。
本研究はこの特定の用途とFCD550およびSKD6間の比較に限定された。調査された主要変数はサイドダイ材料の置換であった。
6. 主な結果:
主な結果:
- 材料選定: データシート分析に基づき、その組成(0.3-0.5%バナジウムを含む)と機械的特性(より高い硬度ポテンシャル)から、SKD6がFCD550よりも優れた熱衝撃耐性ポテンシャルを持つと判断され、選定された(表1-4)。製作されたSKD6ダイは要求される化学組成基準を満たした(表5)。
- 性能比較: 実験的トライアルにより、SKD6ダイはFCD550ダイよりも熱衝撃亀裂に対して著しく耐性があることが示された。同様の初期条件下で1400生産サイクル後、FCD550ダイは12%の亀裂を示したが、SKD6ダイはわずか0.5%のヘアクラックしか示さなかった(図7)。SKD6ダイはより高い温度(最大450°C、FCD550は362°C)で動作したが、シミュレーションでは製品の微小気孔率が低いことが示された(図7)。硬さ試験により、SKD6が硬化後に47.50 HRCを達成したことが確認された(図6)。
- プロセス最適化: SKD6ダイに対する機械設定が成功裏に最適化された。主な変更点には、温度調整(RZ1: 520-545°Cから532-538°C)と時間短縮(ソーク: 最低270秒から332秒; ホールディング: 69秒から46秒; エージング: 190秒から180秒)が含まれた。これにより、総サイクルタイムが517秒から369秒に短縮された(表6、図8)。
- 生産性と品質: SKD6ダイを用いた最適化されたプロセスにより、鋳造生産性が12%向上し、7台の機械全体で28日あたり194,870個から213,311個に増加し、サイドダイの亀裂問題なしに28日あたり200,000個という顧客要求を満たした。最終製品品質はTSD5605G規格に従った試験を通じて確認され、試験されたサンプルには亀裂は見られなかった。
図のリスト:
- Fig. 1. Stages of side core mold manufacturing process: a – project design; b - Pola/Patten; c - die manufacture; d - core manufacture; e - furnace preparation; f- casting; g - solidification; h – sand mold disassembly; i – visual check; j – finishing side core
- Fig. 2. Stages of machining and ceramic coating process: a - side core; b - proses machining; c - proses ceramic coating; d - proses spray finishing
- Fig. 3. Visualization of main die and side die pieces
- Fig. 4. Results of material disposition: a - side die before coating; b - side die after coating
- Fig. 5. Structure micro: a - FCD550; b – SKD6
- Fig. 6. Hardness test results on SKD6 148 hours cooling on FCD550 material after cooling with water temperature 40 °C obtained test value 47.50 HRC
- Fig. 7. Micro photo visualization of: a - porosity temperature conditions FCD550; b – porosity temperature conditions SKD6; c - micro photo of porosity of FCD550; d - micro photo of porosity of SKD6
- Fig. 8. Graph of trial result evaluation data change setting parameters
7. 結論:
- 本研究は、自動車およびオートバイのディスクホイールに使用されるダイカスト金型に非常に適した材料としてSKD6鋼を成功裏に特定した。FCD550と比較して、SKD6は優れた熱衝撃耐性を示し、亀裂形成を12%削減し、耐久性を0.5%向上させた。この材料の高度な耐熱性、靭性、および耐侵食性は、熱衝撃誘起亀裂という重大な問題に対処し、金型製造におけるより高い精度と耐久性を保証する。これは、信頼性の高い高品質な自動車部品を生産する上で、高い技術基準の重要性を強調するものである。
- 高度な冷却システムが効果的に設計され、金型内の均一な温度分布を確保し、熱応力を緩和した。この設計により、熱勾配が23%減少し、製品の寸法精度が100%向上した。研究は、冷却システム設計における綿密な計画と計算が、金型亀裂問題を未然に防ぎ、製品が設計仕様に従って正確に形成され、その完全性を維持することを保証できることを実証した。
- 本研究は、射出速度、金型温度、冷却速度を含む最適化されたダイカストマシンパラメータを達成し、生産を15%加速させ、不良率を100%削減した。厳密な実験データに基づいたこれらの最適化は、生産性向上が製品品質を損なわないことを保証した。この戦略的アプローチは、機械設定を製品基準と顧客の期待に合わせ、最終的に生産物の品質と量の両方を向上させる。
8. 参考文献:
- [References] - (参考文献リストは原文の英語バージョンと同じものを維持します)
- [1] Wankhede, V. A., Vinodh, S. (2022). State of the art review on Industry 4.0 in manufacturing with the focus on automotive sector. International Journal of Lean Six Sigma, 13 (3), 692–732. Available at: https://www.x-mol.net/paper/article/1451642237902290944
- [2] Zhao, X., Gao, P., Zhang, Z., Wang, Q., Yan, F. (2020). Fatigue characteristics of the extruded AZ80 automotive wheel. International Journal of Fatigue, 132, 105393. https://doi.org/10.1016/j.ijfatigue.2019.105393
- [3] Klobčar, D., Kosec, L., Kosec, B., Tušek, J. (2012). Thermo fatigue cracking of die casting dies. Engineering Failure Analysis, 20, 43–53. https://doi.org/10.1016/j.engfailanal.2011.10.005
- [4] Schwam, D., Wallace, J., Birceanu, S. (2002). Die Materials for Critical Applications and Increased Production Rates. Office of Scientific and Technical Information (OSTI). https://doi.org/10.2172/806823
- [5] Su, Y., Fu, G., Liu, C., Liu, C., Long, X. (2021). Fatigue crack evolution and effect analysis of Ag sintering die-attachment in SiC power devices under power cycling based on phase-field simulation. Microelectronics Reliability, 126, 114244. https://doi.org/10.1016/j.microrel.2021.114244
- [6] Cai, H., Wang, Z., Liu, L., Li, Y., Xing, F., Guo, F. (2022). Crack source and propagation of AZ91-0.9Gd alloy. Journal of Materials Research and Technology, 16, 1571–1577. https://doi.org/10.1016/j.jmrt.2021.12.065
- [7] Schumacher, O., Marvel, C. J., Kelly, M. N., Cantwell, P. R., Vinci, R. P., Rickman, J. M. et al. (2016). Complexion time-temperature-transformation (TTT) diagrams: Opportunities and challenges. Current Opinion in Solid State and Materials Science, 20 (5), 316–323. https://doi.org/10.1016/j.cossms.2016.05.004
- [8] Lordan, E., Zhang, Y., Dou, K., Jacot, A., Tzileroglou, C., Wang, S. et al. (2022). High-Pressure Die Casting: A Review of Progress from the EPSRC Future LIME Hub. Metals, 12 (10), 1575. https://doi.org/10.3390/met12101575
- [9] Luthfiyah, S., Faridh, A., Soegijono, B. (2019). The Effect of Vacuum Quenching on Corrosion and Hardness of the Surface of SKD61 Steel. IOP Conference Series: Materials Science and Engineering, 694 (1), 012033. https://doi.org/10.1088/1757-899x/694/1/012033
- [10] Sudjadi, U., Sinaga, R. V. (2020). Study of the hardness and microstructure profiles of SKD61 steel plunger tip (local material) after plasma nitriding. IOP Conference Series: Materials Science and Engineering, 839 (1), 012019. https://doi.org/10.1088/1757-899x/839/1/012019
- [11] Yi, W., Liu, G., Gao, J., Zhang, L. (2021). Boosting for concept design of casting aluminum alloys driven by combining computational thermodynamics and machine learning techniques. Journal of Materials Informatics. https://doi.org/10.20517/jmi.2021.10
- [12] Walsh, E., Maclean, N., Turner, A., Alsuleman, M., Prasad, E., Halbert, G. et al. (2022). Manufacture of tablets with structurally-controlled drug release using rapid tooling injection moulding. International Journal of Pharmaceutics, 624, 121956. https://doi.org/10.1016/j.ijpharm.2022.121956
- [13] Yang, Q., Wu, X., Qiu, X. (2023). Microstructural Characteristics of High-Pressure Die Casting with High Strength–Ductility Synergy Properties: A Review. Materials, 16 (5), 1954. https://doi.org/10.3390/ma16051954
- [14] Zhou, Y., Tian, N., Liu, W., Zeng, Y., Wang, G., Han, S. et al. (2022). Mechanism of heterogeneous distribution of Cr-containing dispersoids in DC casting 7475 aluminum alloy. Transactions of Nonferrous Metals Society of China, 32 (5), 1416–1427. https://doi.org/10.1016/s1003-6326(22)65883-7
- [15] Wei, C., Ou, J., Farhang Mehr, F., Maijer, D., Cockcroft, S., Wang, X. et al. (2021). A thermal-stress modelling methodology in ABAQUS for fundamentally describing the die/casting interface behaviour in a cyclic permanent die casting process. Journal of Materials Research and Technology, 15, 5252–5264. https://doi.org/10.1016/j.jmrt.2021.10.120
- [16] Campos Neto, N. D., Korenyi-Both, A. L., Vian, C., Midson, S. P., Kaufman, M. J. (2023). The development of coating selection criteria to minimize die failure by soldering and erosion during aluminum high pressure die casting. Journal of Materials Processing Technology, 316, 117954. https://doi.org/10.1016/j.jmatprotec.2023.117954
- [17] Ahmadein, M., Elsheikh, A. H., Alsaleh, N. A. (2022). Modeling of cooling and heat conduction in permanent mold casting process. Alexandria Engineering Journal, 61 (2), 1757–1768. https://doi.org/10.1016/j.aej.2021.06.048
- [18] Niu, Z., Liu, G., Li, T., Ji, S. (2022). Effect of high pressure die casting on the castability, defects and mechanical properties of aluminium alloys in extra-large thin-wall castings. Journal of Materials Processing Technology, 303, 117525. https://doi.org/10.1016/j.jmatprotec.2022.117525
- [19] Li, Z., Li, D., Zhou, W., Hu, B., Zhao, X., Wang, J. et al. (2022). Characterization on the formation of porosity and tensile properties prediction in die casting Mg alloys. Journal of Magnesium and Alloys, 10 (7), 1857–1867. https://doi.org/10.1016/j.jma.2020.12.006
- [20] Dudek, P., Białoń, J., Piwowońska, J., Walczak, W., Wrzała, K. (2023). The impact on the cost of making high pressure die castings with multi-cavity die and vacuum assistance. Vacuum, 210, 111859. https://doi.org/10.1016/j.vacuum.2023.111859
9. 著作権:
- この資料は、「Herry Patria, Iwan Susanto, Belyamin, Dianta Mustofa Kamal」による論文です。「Enhancing side die resistance to thermal shock in automotive casting: a comparative study of FCD550 and SKD6 materials」に基づいています。
- 論文の出典: https://doi.org/10.15587/1729-4061.2024.306615
この資料は上記の論文に基づいて要約されており、商業目的での無断使用は禁じられています。
Copyright © 2025 CASTMAN. All rights reserved.