本要約の内容は、「China Foundry」によって発行された論文「Mechanism of die soldering during aluminum die casting」に基づいています。
![Figure 1: Schematic illustration showing possible aluminum composition and temperature profiles at the die surface, and the resulting phases for the case of pure aluminum cast in an iron die. Three regions at the die surface can be identified. Soldering occurs in Region I [4].](https://castman.co.kr/wp-content/uploads/image-1853-png.webp)
1. 概要:
- タイトル(Title): Mechanism of die soldering during aluminum die casting
- 著者(Author): Q. Han
- 発行年(Year of publication): 2015
- 発行学術誌/学会(Journal/academic society of publication): China Foundry, vol. 12, no. 2, pp. 136-143.
- キーワード(Keywords): 溶損(Soldering), 焼付き(die sticking), アルミニウム合金(aluminum alloys), ダイカスト(die casting)
2. 抄録 (Abstract):
溶損(Soldering)は、アルミニウム合金のダイカストまたは金型鋳造に関連する特有の鋳造欠陥である。これは、溶融アルミニウムが金型鋼の表面に付着または溶着し、鋳物の突き出し後もそこに残り、鋳物の表面欠陥や寸法不正確さを引き起こし、機械のダウンタイムを増加させる現象である。溶損は、無処理の金型鋼金型を使用してアルミニウム合金をダイカストする場合に容易に発生する。溶融アルミニウムが臨界温度よりも高い温度で金型鋼と接触すると、鉄とアルミニウムの原子が互いに拡散し、一連の金属間化合物相と液体のアルミニウムリッチなfcc相を形成する。この液相は金属間化合物相の間に存在する。冷却時に、液体のfcc相は金属間化合物相上で凝固し、鋳物内部に成長して溶損を引き起こす。臨界温度は、相図のアルミニウムコーナー付近の共晶温度である。金型が非反応性のセラミックコーティングで保護されている場合、溶損は局所的なコーティング破壊が発生する場所から始まる。溶融アルミニウムはコーティング破壊箇所を通じて金型鋼と接触し、鋼マトリックスを侵食して小さなピットを形成する。これらの小さなピットが成長するにつれて、コーティングは徐々に除去され、溶損はより深刻になる。無処理の鋼製金型およびコーティングされた金型材料における金型溶損のステップの詳細について議論する。
3. 緒言 (Introduction):
ダイカスト(Die casting)、または高圧ダイカスト(HPDC)は、高圧を用いて溶融金属を鋼製の金型に射出する100年の歴史を持つプロセスである。この費用対効果の高いプロセスは、迅速な生産速度と高い金型あたり金属収率でネットシェイプ製品を生産することができる。他の金属鋳造プロセスでは、これほど多様な形状、微細なデザインの複雑さ、または厳密な寸法公差を許容するものはない。今日、ダイカストプロセスは全金属鋳物の3分の1以上を生産するために使用されており、そのほとんどがアルミニウム鋳物である[1]。
アルミニウムダイカストの生産性を制限する主要な問題の1つは、金型溶損(die soldering)である。溶損または焼付き(die sticking)は、溶融アルミニウムが金型表面に「溶接」される現象である。深刻な条件下では、金型溶損はわずか数回の鋳造サイクル後に発生し、機械のダウンタイム増加、鋳物の表面品質および圧力または漏れ気密性に関連するスクラップ、そして金型は一般的に高価でありダウンタイムは生産損失をもたらすためコスト増加を引き起こす。金型溶損は、低圧永久鋳型鋳造を含む他の金属金型鋳造プロセスにも関連している。
溶融金属に囲まれた金型の小さな形状部は、ダイカストプロセスの各実行中に金型本体よりも通常高い温度に加熱されるため、溶損形成が起こりやすい。鋳物に小さな穴を形成するために使用されるコアピン(Core pins)は、ダイカストプロセス中に溶損が発生しやすい金型のそのような形状部である。コアピンの使用は、鋳物に穴を開ける必要性を減らし、鋳造プロセスをより費用対効果の高いものにする。典型的なダイカストマシンは約10から100本のピンを使用する。ダイカスト業界は、H-13鋼がヒートチェックと摩耗に耐性があるという事実のために、金型とコアピンの製造にH-13鋼を使用している。
ダイカスト業界では2種類の溶損が主張されている。1つは、溶融アルミニウム合金と金型との間の化学的/冶金学的反応により高温で発生し[2]、もう1つは機械的相互作用により低温で発生する[3]。北米のダイカスト業界が厳しい国際競争に直面した1990年代まで、金型溶損を調査するための体系的な研究は限られていた。ダイカスターが生き残るためにはダウンタイムを最小限に抑え、生産性を向上させることが不可欠となったが、北米のほとんどのダイカスターは研究資源が不足している中小企業である。その結果、金型溶損に関する研究は、産業団体や政府機関によって後援されてきた。化学反応によって発生する金型溶損の理解には大きな進展があった。機械的相互作用による溶損についてはほとんど理解されていない。
本稿では、化学的相互作用の結果として発生する金型溶損について議論する。このタイプの溶損は、金型表面の保護膜の「ウォッシュアウト」と密接に関連していると一般的に認識されている[2]。ウォッシュアウトは、溶融アルミニウム合金が金型の保護膜(コーティングまたは潤滑剤)を破壊するときに発生する。その後、溶融アルミニウムは金型表面と接触し、通常H-13鋼である金型材料と反応する。金型潤滑剤は溶融金属によって容易に破壊される可能性があるが、コーティング、特に物理蒸着(PVD)プロセスを使用して作られたコーティングは、多くの鋳造サイクルの間、金型上に留まることができる。金型潤滑剤の大部分が除去されると、溶損は溶融金属と無処理の金型鋼との間の直接的な化学反応によって制御される。金型に強力なPVDコーティングがある場合、溶損はコーティングの局所的な破壊によって制御される。本稿では、無処理の鋼製金型およびコーティングされた金型またはコアピンにおける溶損について説明する。
4. 研究の概要 (Summary of the study):
研究テーマの背景 (Background of the research topic):
溶融アルミニウムが金型表面に付着する金型溶損は、アルミニウム高圧ダイカスト(HPDC)の生産性に対する重大な障害である。これは、鋳造欠陥(表面欠陥、寸法不正確さ)、金型メンテナンスのための機械ダウンタイム増加、スクラップ率の上昇、高価な金型および生産損失に関連するコスト増加につながる。通常H-13鋼で作られるコアピンのような形状部は、より高い動作温度のため特に影響を受けやすい。
先行研究の状況 (Status of previous research):
金型溶損に関する体系的な調査は1990年代まで限られていた。研究では、化学的/冶金学的反応による高温溶損と機械的相互作用による低温溶損が区別されている。溶融アルミニウム合金による保護膜(潤滑剤またはコーティング)の「ウォッシュアウト」または破壊としばしば関連付けられる化学反応メカニズムの理解には大きな進展があった[2]。PVDコーティングのような耐久性のあるコーティングが溶損を軽減する役割は認識されているが、局所的なコーティング破壊時には依然として溶損が発生する可能性がある。機械的溶損に関する理解は依然として限られている。
研究の目的 (Purpose of the study):
本研究は、溶融アルミニウム合金と金型鋼(特にH-13)との間の化学的相互作用の結果として発生する金型溶損のメカニズムを解明することを目的とする。無処理の鋼表面と非反応性セラミックコーティングで保護された表面の両方について、溶損を引き起こす条件と金型損傷の進行プロセスを詳述する。
中核研究 (Core study):
本研究の中核は、化学反応に基づく金型溶損の基本メカニズムを分析することである。無処理の鋼製金型については、アルミニウムの鋼への拡散と鉄のアルミニウムへの拡散を調査し、金属間化合物相の形成を導く。重要な側面は、金型表面温度が臨界温度(Tc、純Al-Feの場合は共晶温度655°Cと同定)を超えると、液体のアルミニウムリッチなfcc相が形成されることである。この液相は凝固時に鋳物と金型との間の結合を促進する。コーティングされた金型については、研究は5段階の破壊メカニズムを概説する:(1)局所的なコーティング破壊(亀裂/剥離)、(2)露出した鋼での反応によるピット形成、(3)金属間化合物およびAlリッチfcc相形成を含むピットの深さ方向および横方向の成長、(4)隣接するピットの接続、(5)破壊領域での侵食による逆勾配またはアンダーカットの形成。純アルミニウムおよびA380合金に対する臨界温度の概念を検証するために、実験的な浸漬試験が実施された。使用済みコアピンの微細構造分析は、コーティングされた表面上で提案されたメカニズムの証拠を提供した。
5. 研究方法論 (Research Methodology)
研究設計 (Research Design):
本研究は、相図(Al-Fe系)および冶金学的原理(拡散、反応速度論、相変態)に基づく理論的分析と実験的検証を組み合わせて実施された。2つの主要なシナリオが調査された:無処理の鋼表面における溶損、およびコーティングされた鋼表面(特にコアピン)における溶損の開始と進行。
データ収集および分析方法 (Data Collection and Analysis Methods):
- 無処理鋼の分析:
- 純アルミニウムおよびA380アルミニウム合金の溶湯に浸漬した軟鋼シリンダー(直径12mm、長さ25mm)を使用して、単純な浸漬および浸漬コーティング試験を実施した。
- 試料表面温度は溶接された熱電対を使用して監視し、溶湯への浸漬または炉内での保持を調整することによって(±3°C)制御した。
- それぞれの融点/液相線温度の上下の様々な表面温度(純Al: 630°C~740°C; A380: 500°C~680°C)で、異なる時間保持して試験を実施した(Table 1)。
- 試験後の試料は、金属間化合物層の形成や冶金学的結合を含む溶損の存在と性質を評価するために、断面を切断し金属組織学的に検査したと推定される(Figure 3から示唆される)。
- 結果はAl-Fe相図(Figure 1)と関連付けられ、液相形成のための臨界温度を特定した。
- コーティングされた金型/コアピンの分析:
- 様々な期間、工業用ダイカストマシンで使用されたコアピンを収集した。
- 走査型電子顕微鏡(SEM)を使用してこれらのピンの表面を検査した。
- SEMイメージングにより、溶損の様々な段階が記録された:初期のコーティング破壊モード(亀裂、剥離 - Figure 4)、ピット形成と成長(Figure 5)、確立された溶損領域の形態(Figure 6a, Figure 7)、およびアンダーカットの証拠(Figure 8)。
- エネルギー分散型X線分光法(EDS)ラインスキャン(Figure 6b, 6cから示唆される)を使用して、ピット内のH-13マトリックス、反応ゾーン(金属間化合物)、およびAl合金領域にわたる元素分布(Al, Fe, Si, Cr, Cu)を分析し、相の同定と拡散プロセスの理解を可能にした。
研究トピックと範囲 (Research Topics and Scope):
本研究は、化学的/冶金学的相互作用から生じるアルミニウムダイカストにおける金型溶損のメカニズムにのみ焦点を当てた。範囲には以下が含まれる:
- 純アルミニウムおよびA380合金について、無処理の鋼表面での溶損開始の条件(臨界温度)の定義。
- 形成された金属間化合物相と液体Alリッチfcc相の役割の特性評価。
- セラミックコーティングされたH-13鋼コアピン上で、局所的なコーティング破壊から始まり深刻な金型損傷(アンダーカット)に至る溶損発生の連続的なステップの詳細説明。
- コーティングされた表面でのピット形成と成長に関連する微細構造の進化と元素拡散の調査。
- 本研究は、機械的相互作用によって引き起こされる溶損は調査していない。
6. 主要な結果 (Key Results):
主要な結果 (Key Results):
- 無処理鋼における金型溶損は、金型表面温度(TD)が臨界温度(Tc)を超えると発生し、これによりFe-Al金属間化合物反応層内にアルミニウムリッチな液体fcc相が形成される(Region I, Figure 1)。この液相の凝固により、鋳物と金型との間に冶金学的結合が生成される(Figure 2)。
- 鉄/鋼に対して鋳造された純アルミニウムの場合、臨界温度TcはAl-Fe共晶温度である655°Cに対応する。実験的な浸漬試験により、表面温度が661°C以上で溶損が発生し、643°C以下では発生しないことが確認された(Table 1, Figure 3)。
- 鋼に対して鋳造されたA380合金の場合、溶損の臨界温度はデンドライトコヒーレンシー温度(約560°C)または液相線温度(575°C)のいずれかに関連すると示唆される。実験では575°Cで溶損が発生したが、550°Cでは発生しなかった(Table 1)。
- セラミックコーティングされたH-13鋼金型/コアピンでは、亀裂やコーティングが基材から剥離した領域など、局所的なコーティング破壊箇所で溶損が開始する(Figure 4)。
- 溶融アルミニウムはこれらの破壊箇所に浸透し、下地のH-13鋼と反応して、鉄アルミニドを含む小さなピットまたは反応領域を形成する(Figure 5)。
- これらのピットは横方向に成長して隣接するコーティングを弱体化させ、また鋼マトリックス内部へ深さ方向に成長する。この成長には、複雑な鉄アルミニド(例:Al12Fe6Si5, Al15Fe6Si5, Al4FeSi)および特に反応領域の外縁におけるAlリッチfcc相の形成が伴う(Figure 6)。
- Alリッチfcc相は、ダイカスト温度で液体である可能性があり(Al含有量が61.5 wt%を超え、T > 655°Cの場合)、金属間化合物のさらなる侵食を促進し、拡散を強化してピット成長を加速させる。
- 隣接するピットは最終的に接続し、しばしばジグザグ形状を示す、より大きく連続した溶損領域を形成する(Figure 7)。
- コーティングが完全に除去された深刻な影響を受けた領域では、衝突する溶融アルミニウムによる鋼マトリックスの継続的な侵食と溶解が、金型表面に逆勾配またはアンダーカットの形成を引き起こす可能性があり(Figure 8)、鋳物の突き出しを著しく妨げ、潜在的に損傷を引き起こす。
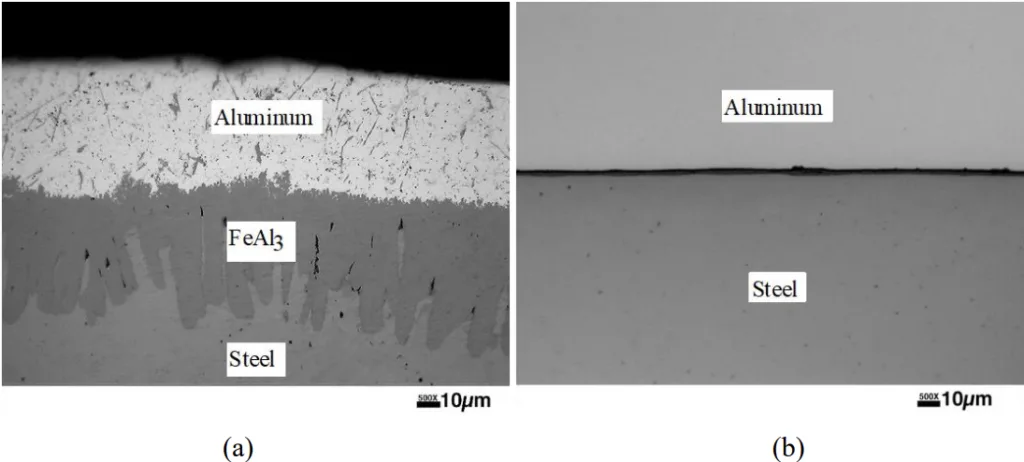
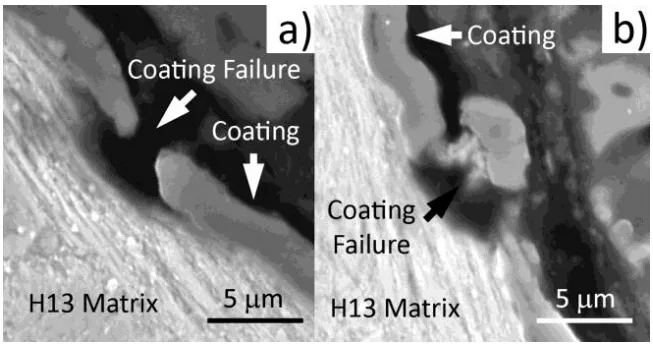
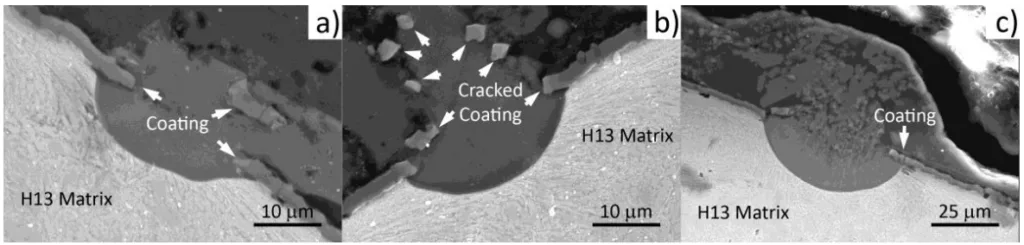
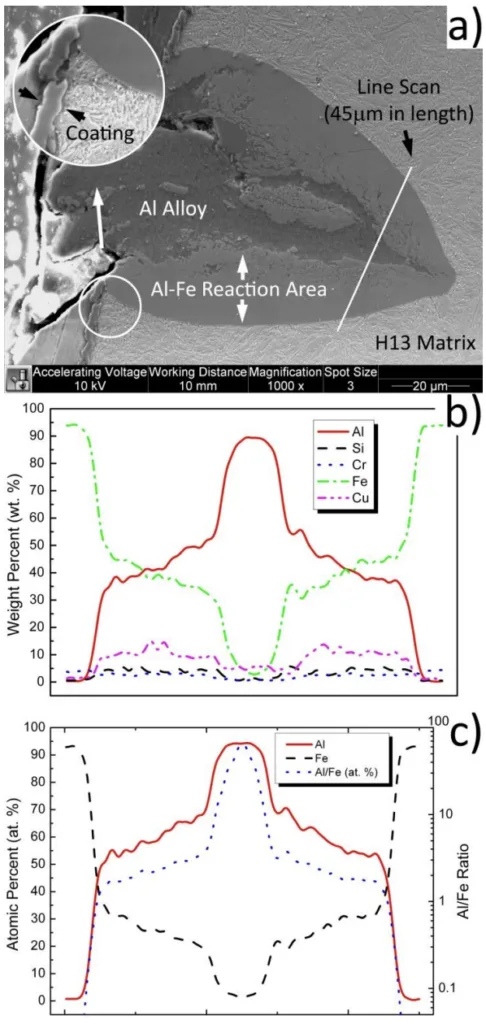
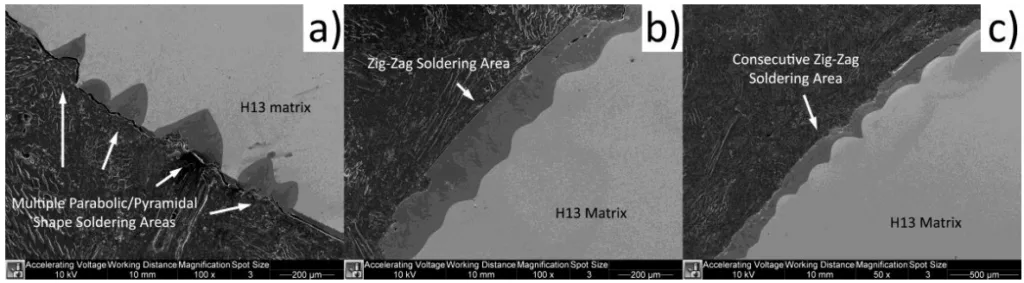
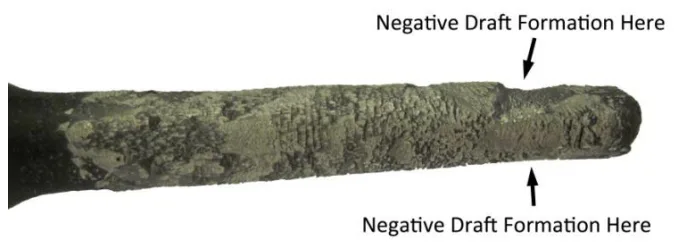
図のリスト (Figure Name List):
- Figure 1: Schematic illustration showing possible aluminum composition and temperature profiles at the die surface, and the resulting phases for the case of pure aluminum cast in an iron die. Three regions at the die surface can be identified. Soldering occurs in Region I [4].
- Figure 2. Schematic illustration of the mechanism of die soldering, indicating (a) the presence of liquid at the die surface when the temperature at the surface is higher than a critical temperature, 655°C, and (b) the formation of a joint between the casting and the die on solidification of this liquid phase.
- Figure 3. Typical microstructures observed at the die surface for three cases: (a) metallurgical bond resulting in soldering, and (b) absence of reaction between steel and aluminum.
- Figure 4: SEM images illustrating coating failure in two ways: (a) cracked and (b) detached.
- Figure 5 SEM images of the reaction areas: (a) coating broken by lateral growth in soldering area, (b) coating cracked and migrated away, and (c) coating washed out.
- Figure 6: Typical pit or soldering area with parabolic/pyramidal shape: (a) the SEM image and line scan location, (b) weight percentage curves of five elements along the scanned line and (c) atomic percentage curves and the ratio of Al/Fe curve.
- Figure 7: SEM images of soldering area: (a) multiple pits of parabolic/pyramidal shape, (b) and (c) two views of soldering area with a consecutive zigzag shape.
- Figure 8: Schematic of negative draft or undercut formation on a core pin (arrow showed).
7. 結論 (Conclusion):
化学的相互作用によって駆動されるアルミニウムダイカストにおける金型溶損は、金型表面温度が臨界閾値(Tc)を超えると発生し、金型-鋳物界面のFe-Al金属間化合物層内にAlリッチ液相の形成を導く。この液相は凝固して鋳物を金型に結合させる。鋼に対する純アルミニウムの場合、TcはAl-Fe共晶温度(655°C)である。A380のような合金の場合、Tcは液相線またはデンドライトコヒーレンシー温度に関連する。無処理鋼では、このプロセスはTc以上で直接この液相形成を導く拡散と反応を含む。コーティングされた金型(例:H-13鋼上のセラミック)では、局所的なコーティング欠陥(亀裂、剥離)によって開始される進行性の破壊メカニズムに従う。溶融アルミニウムは露出した鋼と反応し、横方向および深さ方向に成長するピットを形成する。この成長は、鉄アルミニドおよびAlリッチfcc相の形成を含み、液体の場合、侵食およびさらなる反応を加速する。ピットは最終的に合体し、深刻な侵食はアンダーカットまたは逆勾配を引き起こし、部品の突き出しを妨げる可能性がある。Alリッチfcc相の存在と挙動は、無処理およびコーティングされたシナリオの両方において溶損メカニズムの中心である。
(注:元の論文には「4. Conclusions」という見出しが含まれていますが、その下に本文はありません。この結論は、論文全体で提示された抄録と主要な調査結果から合成されたものです。)
8. 参考文献 (References):
- [1] NADCA website, http://www.diecasting.org/].
- [2] Y.L. Chu, P.S. Cheng and R. Shivpuri, Transactions (Rosemont, Illinois: North American Die Casting Association, 1993), pp.361-371
- [3] D. Argo, R.J. Barnhurst, and W. Walkington, “NADCA Sponsored Research: The cause of Soldering in Zinc Die Casting,” Transactions (Rosemont, Illinois: North American Die Casting Association, 1997), pp. 77-82
- [4] Q. Han and S. Viswanathan, “Analysis of the Mechanism of Die Soldering in Aluminum Die Casting," Metall. Mater. Trans., 2003, 34A, pp. 139-46.
- [5] H. Baker et al. (Eds), ASM Handbook, vol.3, Alloy Phase Diagrams (Materials Park, OH: ASM International), 1992.
- [6] W. Kajoch and A. Fajkiel, “Testing the Soldering Tendencies of Aluminum Die Casting Alloys," Transactions (Rosemont, Illinois: North American Die Casting Association, 1991), pp.67-74.
- [7] S. Shankar and D. Apelian, "Die Soldering – A Metallurgical Analysis of the Molten Aluminum/Die Interface Reactions,” Transactions (Rosemont, Illinois: North American Die Casting Association, 1997), pp. 243-251.
- [8] V.G. Rivlin and G.V. Raynor, “Critical Evaluation of Constitution of Aluminum-Iron-Silicon System,” Int. Met. Rev., 26 (1981) pp. 133-152.
- [9] R.W. Richards, R.D. Jones, P.D. Clements and H. Clarke, “Metallurgy of Continuous Hot Dip Aluminizing,” Int. Mat. Rev., 39 (1994) pp. 191-212.
- [10] J. Wallace, D. Schwam, Y. Zhu, S. Birceanu, “Soldering Characteristics of Die Materials and the Effect on Cooling Link Placement on Die Life,” Transactions of the North American Die Casting Association, Rosemont, IL, 2002, T03-041.
- [11] G. Engleman, S. Viswanathan, C.A. Blue, Q. Han, and N.B. Dahotre, “High Density Infrared Coatings for Soldering Resistance,” Transactions of the North American Die Casting Association, Rosemont, IL, 2002, T02-43.
- [12] J. Moore, S. Carrera, J. Lin, O. Salas, B. Mishra, G. Mustoe, and P. Ried, “The Development of Surface Engineered Coating Systems for Aluminum Pressure Die Casting Dies: An Evaluation of Six Commercial Coatings,” Transactions of the North American Die Casting Association, Rosemont, IL, 2003, T03-025.
- [13] L. Arnberg, L. Bäckerud, and G. Chai, Solidification Characteristics of Aluminum Alloys, vol.3, Dendrite Coherency (American Foundrymen's Society, Inc., 1996), 115
- [14] Z. W. Chen and M. Z. Jahedi, Die Erosion and Its Effect on Soldering Formation in High Pressure Die Casting of Aluminum Alloys, Materials and Design, 1999, vol. 20, pp.303-309.
- [15] J. Song, T. Denouden, and Q. Han, “Mechanisms of Soldering Formation on Coated Core Pins," Metall Mater Trans, 2012, 43A, pp. 415-421.
- [16] S. Shankar, and D. Apelian, “Die Soldering: Mechanism of the Interface Reaction between Molten Aluminum Alloy and Tool Steel,” Metall. Mater. Trans., 2002, 33B, pp. 466-476.
- [17] J. V. Skoff, "A New Approach to the Cause of High Pressure Die Steel Erosion, Pitting and Breakout", NADCA Transactions, 2010, pp. T10-051.
9. 著作権 (Copyright):
- 本資料は「Q. Han」氏による論文です。「Mechanism of die soldering during aluminum die casting」に基づいています。
- 論文出典: https://doi.org/10.1007/s41230-015-1116-6
本資料は上記の論文に基づいて要約されており、商業目的での無断使用は禁じられています。
Copyright © 2025 CASTMAN. All rights reserved.