本紹介内容は、[韓国生産技術研究院、全北大学]が発行した["高圧ダイカスト用アルミニウム合金の熱伝導性と鋳造性に及ぼす添加元素の影響"]の研究内容です。
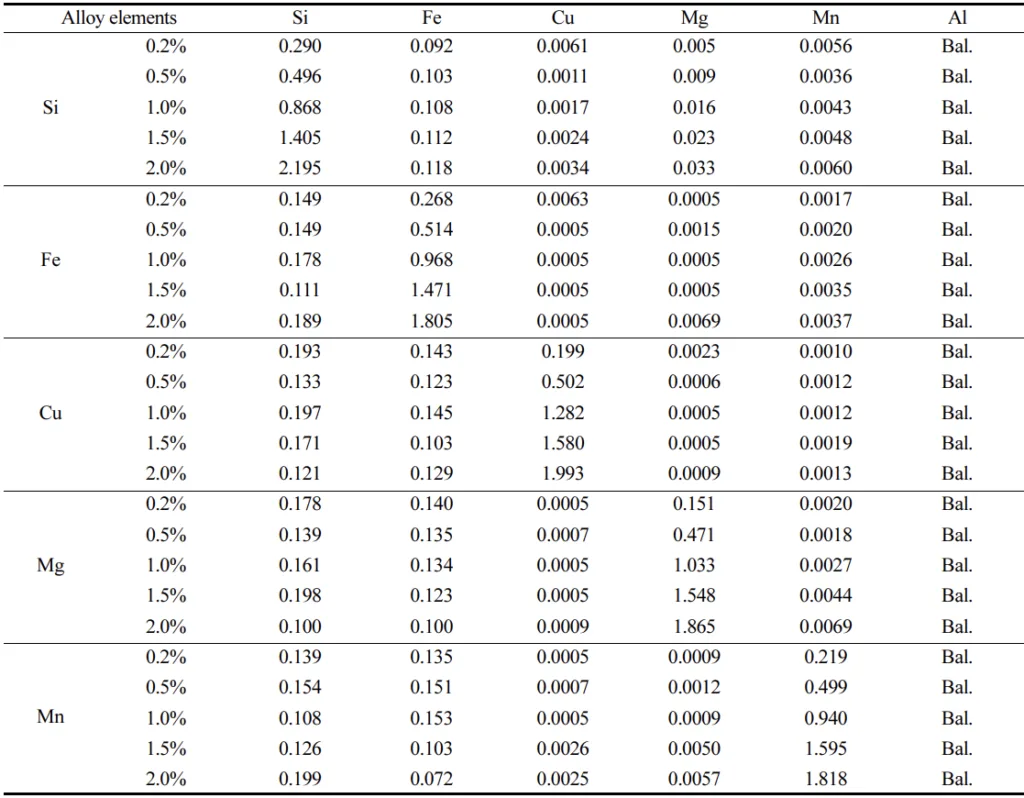
1. 概要:
- タイトル: 高圧ダイカスト用アルミニウム合金の熱伝導性と鋳造性に及ぼす添加元素の影響 (Effect of Alloying Elements on the Thermal Conductivity and Casting Characteristics of Aluminum Alloys in High Pressure Die Casting)
- 著者: 金哲佑, 金英燦, 金정한, 趙載益, 呉民錫 (Cheol-Woo Kim, Young-Chan Kim, Jung-Han Kim, Jae-Ik Cho, Min-Suk Oh)
- 発行年: 2018年
- 発行ジャーナル/学会: 大韓金属・材料学会誌 (Korean Journal of Metals and Materials)
- キーワード: thermal conductivity, heat sink, die-casting, radiation of heat
2. 概要 / 序論
概要:
高圧ダイカストは精密鋳造法の一つである。生産性が高く、複雑な形状と正確な寸法を持つ部品の製造に適している。近年、デバイスで発生する熱を制御し、製品の効率と寿命に直接影響を与える効率的な放熱部品の需要が増加している。高熱伝導率のダイカストアルミニウム合金は、この用途に特に必要とされている。本研究では、ダイカストアルミニウム合金に添加された元素がその熱伝導率に及ぼす影響を評価した。その結果、Mnはアルミニウム合金の熱伝導率を著しく低下させることがわかった。Cu含有量が増加すると、鋳造アルミニウム合金の引張強さが増加し、1 wt%のCuが鋳造アルミニウムの最小機械的特性を確保することが示された。Si含有量が増加すると、合金の流動長が比例して増加した。2 wt%のSiを含むアルミニウム合金の流動長は、ALDC12合金の約85%であった。表面クラックのないAl-1 wt%Cu-0.6 wt%Fe-2 wt%Siダイカスト合金の最適組成を用いて放熱部品を製造することに成功した。これは、Si組成が2 wt%未満の合金の凝固収縮に起因する粒界割れであることが判明した。
序論
高圧ダイカスト工法は、正確に機械加工された金型に溶融金属を注入し、必要な鋳造形状と完全に一致する鋳物を得る精密鋳造法である。ダイカスト工程を適用すると、精密で複雑な形状の部品を短時間で大量生産できるため、生産性が非常に高い [1,2]。近年、自動車や電気電子産業など、様々な分野で部品の高効率化や集積化などに起因する発熱問題が大きく浮上している。したがって、部品の温度上昇による製品の効率低下や寿命短縮を防ぐために、放熱特性に優れた部品開発が大きく求められている。一般的に放熱特性が要求される部品の場合、熱伝導率の高いAI展伸材合金や99 wt%以上のAIを利用した鋳造工法が適用されているが、低い流動性、劣悪な鋳造性及び金型焼付き抵抗性のためダイカスト工程には適用されていない。
3. 研究背景:
研究テーマの背景:
近年、自動車や電気電子産業において、部品の高効率化と集積化に伴い、発熱問題が顕著になっている。部品の温度上昇は、製品の効率低下や寿命短縮を招くため、優れた放熱特性を持つ部品の開発が不可欠となっている。一般的に放熱部品には、熱伝導率の高いアルミニウム展伸材合金や純アルミニウムを用いた鋳造法が用いられるが、ダイカスト工法への適用は、材料の流動性や鋳造性、金型焼付き抵抗性の問題から困難であった。
既存研究の現状:
ダイカスト用Al合金は、合金の鋳造性や製品の物理的・化学的特性を向上させるために添加される微量の金属元素によって、熱伝導率が低下する傾向がある。例えば、溶湯の流動性や鋳造性を向上させるためのSi添加 [4]、強度や被削性を向上させるためのCuやMn添加 [5-7]、金型の焼付き抵抗性を向上させるためのFe添加 [8] など、Alに添加される微量金属元素の量が増加するほど、製品の熱物性は劣化する。
研究の必要性:
ダイカスト工法を適用可能であり、かつ優れた放熱特性を有するAl合金の開発には、微量添加元素の組成最適化が不可欠である。既存のALDC12合金は、熱伝導率が99 W/m·kと純アルミニウム(234 W/m·k)に比べて非常に低く、従来の合金組成および製造方法では放熱部品の製造が不可能である [3]。したがって、高い熱伝導率だけでなく、ダイカスト鋳造が可能な高圧ダイカスト用Al合金の開発が非常に求められている。
4. 研究目的と研究課題:
研究目的:
本研究の目的は、高圧ダイカスト用Al合金の熱伝導性に及ぼす添加元素の影響を評価し、放熱特性に優れたAl合金開発のための最適合金組成を導き出すことである。
主要研究:
本研究では、添加する合金元素の種類と量を変化させ、熱伝導性および流動性に及ぼす影響を検討し、導き出された最適合金組成を用いて、実際の自動車用音響機器に適用される放熱部品を製作し、その性能を比較評価した。
5. 研究方法
研究デザイン:
本研究は、添加元素(Si、Fe、Cu、Mg、Mn)の含有量を変化させながら、Al合金の熱伝導性、流動性、機械的特性、および微細組織を分析する実験的研究として設計された。
データ収集方法:
- 成分分析: スパーク発光分光分析装置(Spark emission spectrometer, QUANTRON)を用いて、合金の化学組成を分析。
- 熱伝導率測定: レーザーフラッシュ法を用いた熱物性分析装置(LFA 477, Netzsch)を用いて熱伝導率を測定。
- 微細組織観察: 光学顕微鏡およびFE-SEM(JSM-7000F, JEOL)とEDSを用いて、微細組織、析出物、および微細構造を分析。
- 機械的特性評価: ASTM E8M規格に準拠した引張試験機(AG-IS, SHIMADZU)を用いて、引張強度および伸びを測定。
- 流動性測定: サーペンタイン(Serpentine)形状の金型を用いたダイカスト後、鋳造材の長さを測定。
分析方法:
測定された熱拡散率、比熱、および密度を用いて熱伝導率を計算し、添加元素の種類と含有量変化による熱伝導率、流動性、機械的特性、および微細組織の変化を分析した。image analysisを用いてAl-Cu析出物の面積分率を測定した。
研究対象と範囲:
本研究の研究対象は、様々な添加元素(Si、Fe、Cu、Mg、Mn)をそれぞれ0.2〜2 wt%添加したAl合金である。
6. 主な研究結果:
主要研究結果:
- Mn: Al合金の熱伝導率を著しく低下させることが明らかになった。
- Cu: Cu含有量が増加するにつれて、Al-Cu金属間化合物の析出量が増加し、引張強度が比例して増加した。1 wt% Cu添加で最小限の機械的特性が確保された。
- Si: Si含有量が増加するにつれて、Al合金の流動性が比例して増加した。2 wt% Si添加されたAl合金の流動長は、ALDC12合金の約85%水準であった。
- 最適合金組成: Al-1 wt%Cu-0.6 wt%Fe-2 wt%Si組成のダイカスト合金を用いて、表面クラックのない放熱部品の製作に成功した。
提示されたデータの分析:
- 熱伝導率: 図1(d)は、添加元素の含有量が増加するほど熱伝導率が低下することを示している。特にMn添加が熱伝導率の低下に最も大きな影響を与えた。Si含有量変化による熱伝導率の変化は図8(b)に示されており、Si含有量が増加するほど熱伝導率が低下する傾向が見られる。
- 機械的特性: 図2は、Cu含有量の増加に伴い、引張強度は増加し、伸びは減少することを示している。
- 流動性: 図7は、Si含有量の増加に伴い、流動長が増加することを示している。2 wt% Si添加時にALDC12 대비 約85%水準の流動性を示した。
- 微細組織: 図3、4、5は、Cu含有量の増加に伴い、Al-Cu析出物が増加することを示している。
図のリスト:
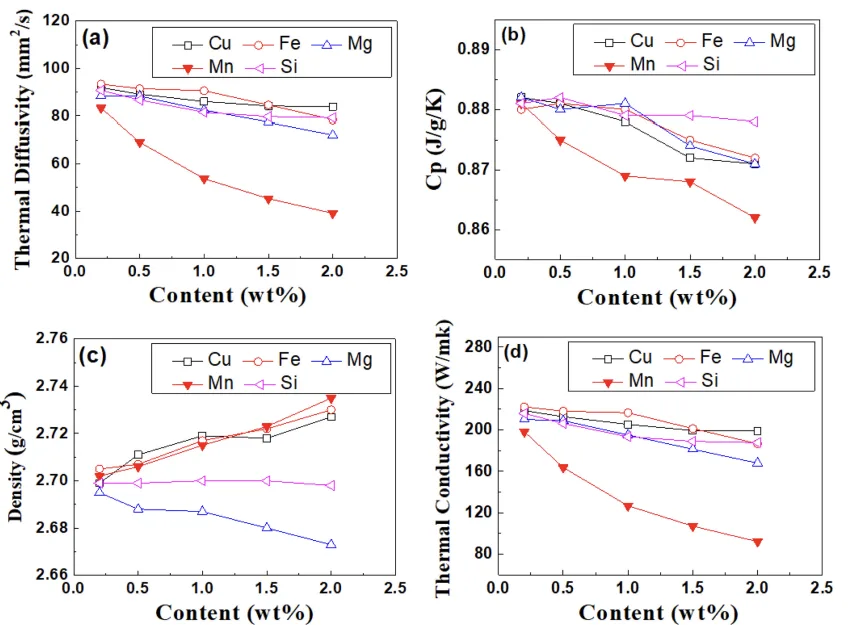
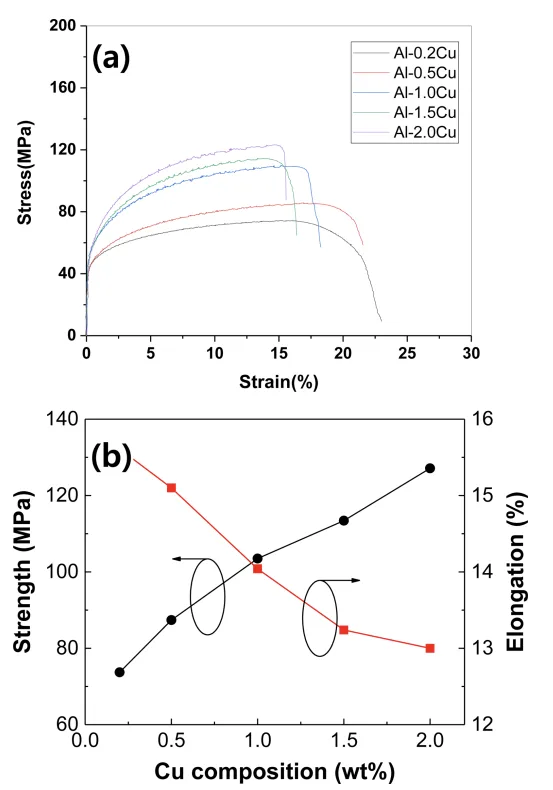
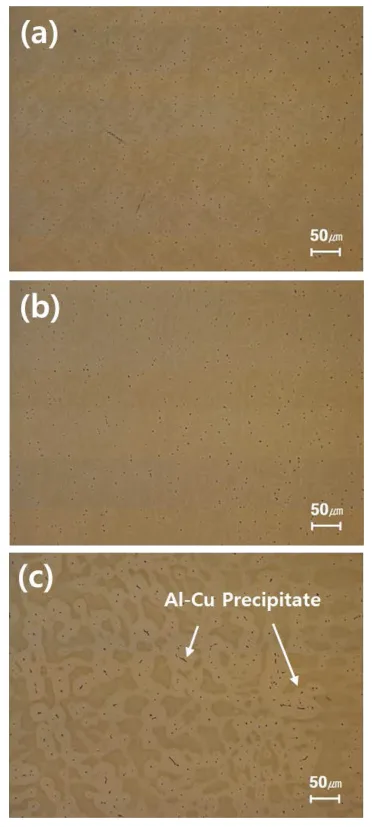
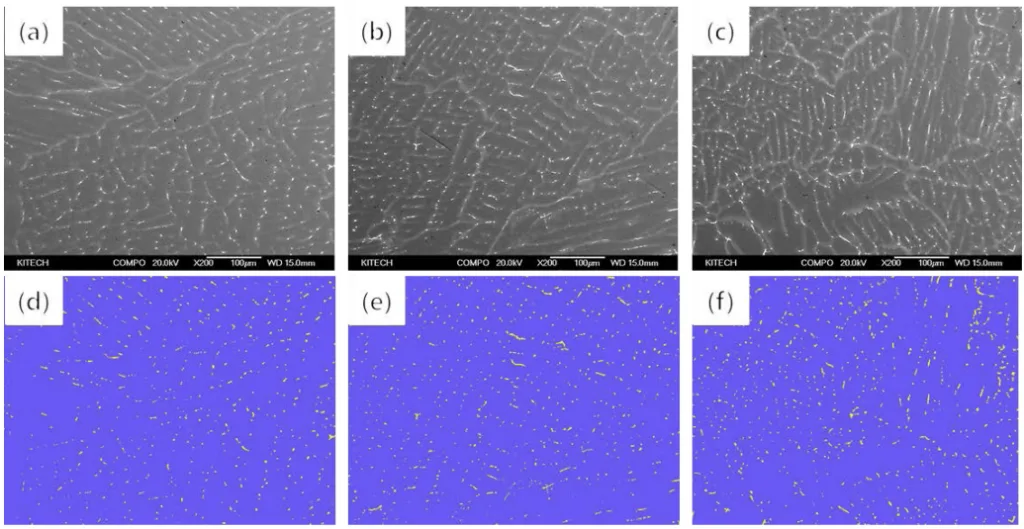
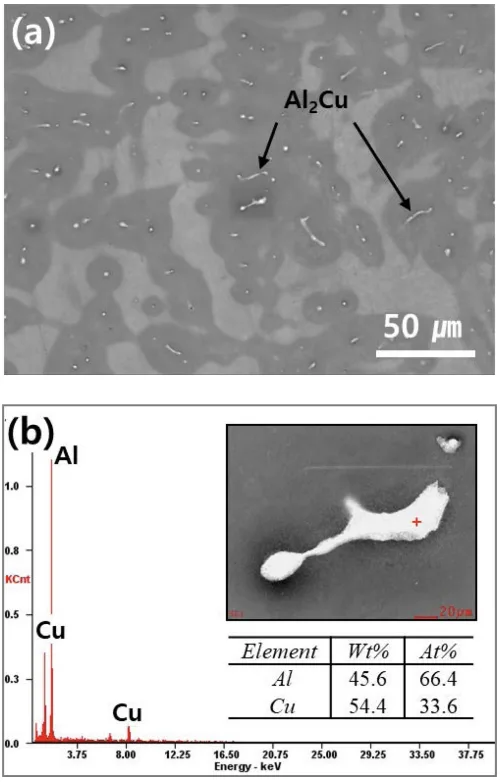
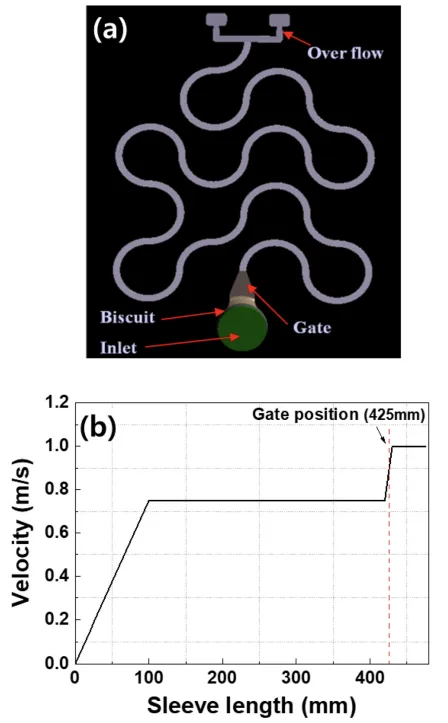
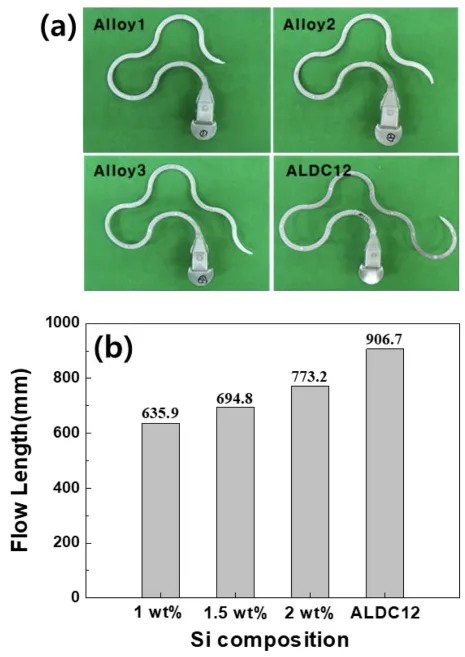
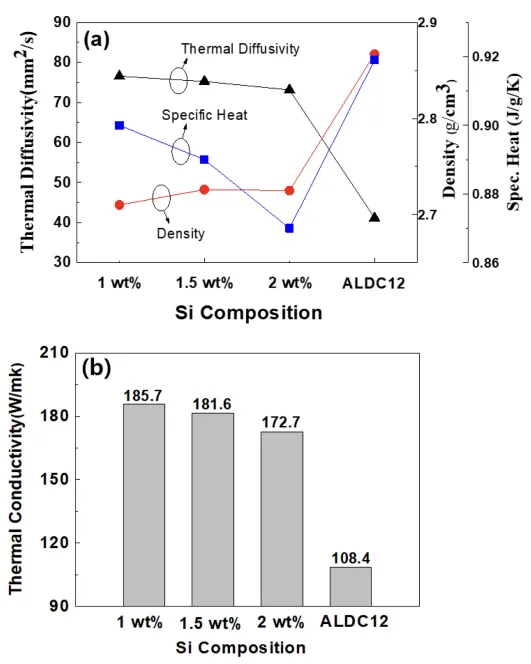
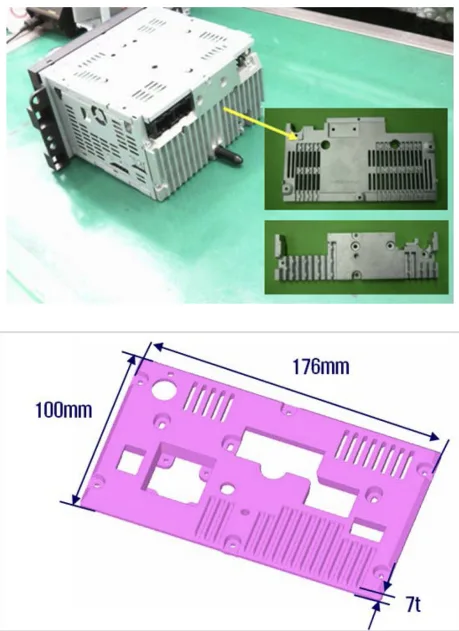
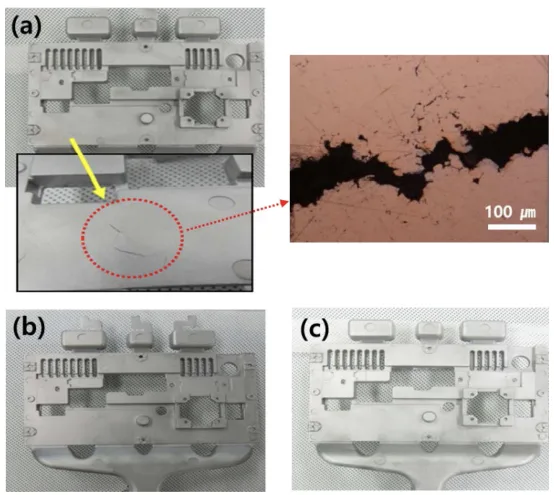
- Fig. 1. Thermal properties of alloys with different additive metals; (a) Thermal diffusivity, (b) Specific heat, (c) Density, (d) Thermal conductivity.
- Fig. 2. (a) Stress-strain curves and (b) change of tensile strength and elongation according to composition of Cu.
- Fig. 3. Microstructure of Al alloys with different Cu composition; (a) Al-1.0wt%Cu, (b) Al-1.5wt%Cu, (c) Al-2.0wt%.
- Fig. 4. SEM image of (a) Al-1wt%Cu, (b) Al-1.5wt%Cu and (c) Al-2wt%Cu (x200) and image analysis data of (d) Al-1wt%Cu, (e) Al-1.5wt%Cu and (f) Al-2wt%Cu (×200).
- Fig. 5. (a) SEM image and (b) EDS results of Al alloy with 2 wt% Cu.
- Fig. 6. (a) Schematic of metal mold and (b) injection speed profile for fluidity test.
- Fig. 7. Results of die casting fluidity test; (a) Schematic of die cast specimens, (b) flow length.
- Fig. 8. (a) Thermal properties and (b) Thermal conductivity of alloys with different additive metals.
- Fig. 9. Die cast heat sink component (car audio heat sink).
- Fig. 10. Diecast car audio heat sink component with various alloy compositions; (a) Al-1.0 wt%Cu-0.6 wt%Fe-1.5 wt%Si), (b) Al-1.0 wt%Cu-0.6 wt%Fe-2.0 wt%Si, (c) Al-2.5 wt%Cu-0.8 wt%Fe-11 wt%Si-0.2 wt%Mg-0.3 wt%Mn (ALDC12).
7. 結論:
主要な知見の要約:
本研究を通じて、高圧ダイカスト用Al合金の熱伝導性および鋳造性に及ぼす添加元素の影響を評価した結果、以下の結論を得た。MnはAl合金の熱伝導率を著しく低下させ、Cuは引張強度を増加させ、Siは流動性を向上させる。最適合金組成としてAl-1.0 wt%Cu-0.6 wt%Fe-2.0 wt%Si合金が導き出され、これはALDC12合金に比べて2倍以上の高い熱伝導率と約85%水準の流動性を示す。
研究の学術的意義:
本研究は、高圧ダイカスト用Al合金において、添加元素が熱伝導性および鋳造性に及ぼす影響に関する体系的なデータを提供し、高熱伝導率ダイカスト合金設計に関する学術的基盤を拡張した。
実用的な意義:
本研究で開発されたAl-1.0 wt%Cu-0.6 wt%Fe-2.0 wt%Si合金は、自動車用音響機器用放熱部品のように高放熱性能が要求されるダイカスト部品製造に活用でき、産業的に高効率放熱部品の開発に貢献できる。
研究の限界と今後の研究分野:
本研究は、特定の組成範囲内で添加元素の影響を評価しており、より優れたダイカスト鋳造のためには、添加元素および工程条件に関する追加的な最適化研究が必要である。また、開発された合金の信頼性および耐久性に関する追加研究が求められる。
8. 参考文献:
- K. P. Keller, IEEE, 10.1109/ITHERM, 112 (1998).
- K. Keller, IEEE, 10.1109/IEMTE, 113 (1998).
- J. R. Davis, ASM, 10.1361/autb, 351 (2001).
- C. R. Loper, Jr., AFS Trans. 533 (1992).
- C. Mascre, Fonderie, 108, 4330 (1995).
- H. Y. Kim, S. W. Han, and H. M. Lee, Mater. Lett. 60, 1880 (2006).
- S. S. Sreeja Kumari, R. M. Pillai, T. P. D. Rajan, and B. C. Pai, Mater. Sci. & Eng. A 460-461, 561 (2007).
- L. A. Naraynan, F. H. Samuel, and J. E. Gruzleski, Metall. Mater. Trans. A 26A, 2161 (2004).
- W. J. Parker, R. J. Jenkins, C. P. Butler, and G. L. Abbott, J. Appl. Phys. 32, 1679 (1961).
- R. D. Cowan, J. Appl. Phys. 34, 926 (1963).
- R. A. Goncalves, Procedia Manuf. 1, 683 (2015).
- L. F. Mondolfo, “Aluminum Alloys: Structure and Properties", Butter Worths (1976).
- H. J. Kim, C. M. Cho, and C. Y. Jeong, J.KFS, 29, 169 (2009).
- D. K. Lews, "Silicon and Its Effect on Fluidity of Aluminum Alloys.", A.S.&R. Co., Inc, Data Sheet.
9. 著作権:
- この資料は、"金哲佑・金英燦・金정한・趙載益・呉民錫"の論文:「高圧ダイカスト用アルミニウム合金の熱伝導性と鋳造性に及ぼす添加元素の影響」に基づいています。
- 論文ソース: DOI: 10.3365/KJMM.2018.56.11.805
この資料は、上記の論文を紹介するために作成されたものであり、商業目的での無断使用は禁止されています。
Copyright © 2025 CASTMAN. All rights reserved.