연구의 핵심 목적: 고압 다이캐스팅 공정에서 금형 내부 압력 센서를 이용하여 공정 변수(집중 압력, 지연 시간, 주조 속도)가 최종 부품의 무결성에 미치는 영향, 특히 다이 캐비티 내 조건과 공정 매개변수 간의 관계를 규명하고, 이를 통해 기존의 고속 가공 방식에서 고압 다이캐스팅으로 전환하는 과정에서 발생하는 기공 문제를 해결하는 최적의 공정 매개변수를 도출하는 것.
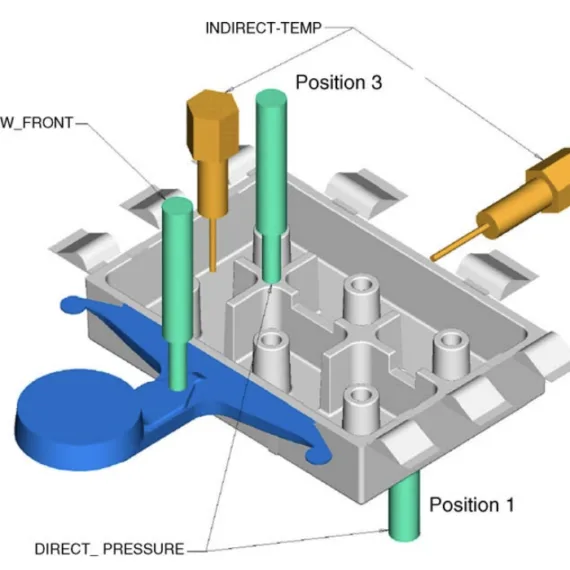
주요 방법론:
연구진은 금형 내부에 압력 센서를 설치하여 고압 다이캐스팅 공정 중 실시간 압력 변화를 측정하는 실험적 방법을 사용했습니다. 다양한 공정 변수(집중 압력, 지연 시간, 주조 속도)를 변화시키면서 얻은 데이터를 분석하여 최종 부품의 기공률과의 상관관계를 조사했습니다. 두 가지 다른 알루미늄 합금 (DA 401과 CA 313)을 사용하여 실험을 수행했으며, 제작된 부품의 기공률을 정량적으로 측정하여 분석에 활용했습니다. Buhler 53 D Evolution 530톤 냉각 챔버 고압 다이캐스팅 기계와 Buhler Shot Control 시스템을 이용하여 실험을 진행했습니다.
핵심 결과:
- 집중 압력의 영향: 집중 압력이 증가함에 따라 기공률은 감소하는 경향을 보였습니다. 이는 고압이 기공 형성을 억제하는 효과가 있음을 시사합니다. 합금 종류에 따라 다소 차이가 있었는데, CA 313 합금의 경우 압력 증가에 따른 기공률 감소 효과가 DA 401 합금보다 다소 불규칙적이었습니다.
- 지연 시간의 영향: 집중 압력 적용 전 지연 시간은 기공률에 큰 영향을 미치지 않았습니다. 하지만 CA 313 합금의 경우 지연 시간 증가에 따라 기공률이 증가하는 경향이 관찰되었으나, 통계적으로 유의미한 수준은 아니었습니다.
- 주조 속도의 영향: 주조 속도가 증가함에 따라 기공률이 증가하는 경향이 관찰되었습니다. 이는 고속 주조 시 난류가 발생하여 기공이 발생할 가능성이 높아짐을 시사합니다. 하지만 높은 압력에서는 주조 속도의 영향이 상대적으로 감소했습니다.
- 설정값과 실측값의 비교: 설정된 압력과 실제 금형 내부 압력 사이에는 차이가 존재했습니다. 압력이 증가할수록 이러한 차이는 더욱 커졌습니다. 또한 설정 주조 속도와 실제 주조 속도 사이에도 차이가 있었지만, 그 차이는 크지 않았습니다.
연구진 정보:
- 소속 기관: ªCRC for Cast Metals Manufacturing (CAST), The University of Queensland, Australia; ᵇEcole des Mines d'Albi-Carmaux, France; ᶜFerra Engineering Pty Ltd., Australia; ᵈCRC for Cast Metals Manufacturing (CAST), CSIRO Manufacturing and Infrastructure Technology, Australia
- 저자명: Matthew S. Dargusch, G. Dour, N. Schauer, C.M. Dinnis, G. Savage
- 주요 연구 분야: 고압 다이캐스팅, 금형 설계, 주조 공정 최적화, 재료 공학
연구 배경 및 목적:
알루미늄 자동차 부품 생산에 고압 다이캐스팅이 널리 사용되지만, 통신 부품과 같이 치수 허용 오차가 엄격하고 표면 품질이 높은 부품 생산에는 고속 가공이 주로 이용되어 왔습니다. 고속 가공은 소량 생산에는 적합하지만, 대량 생산에는 비효율적이고 비용이 많이 듭니다. 본 연구는 고압 다이캐스팅을 통해 통신 부품의 생산성을 높이고 제조 비용을 낮추는 것을 목표로 하며, 기공 문제와 같은 기술적 과제를 해결하기 위한 최적의 공정 매개변수를 찾는 것을 목표로 했습니다.
논문의 주요 목표와 연구내용:
본 연구의 주요 목표는 고압 다이캐스팅 공정의 최적화를 통해 고품질의 알루미늄 통신 부품을 생산하는 것입니다. 이는 다음과 같은 단계를 통해 수행되었습니다:
- 금형 내부 압력 측정: 금형 내부에 압력 센서를 장착하여 다이 캐비티 내 압력을 실시간으로 측정함으로써 공정 변수와 최종 제품의 품질 사이의 관계를 정확하게 파악하고자 했습니다.
- 공정 변수 최적화: 다양한 공정 변수 (집중 압력, 지연 시간, 주조 속도)를 체계적으로 변화시켜 가며, 각 변수가 기공 형성에 미치는 영향을 분석했습니다. 이를 통해 최적의 공정 조건을 도출하고자 하였습니다.
- 합금 종류의 영향 분석: 두 가지 다른 알루미늄 합금 (DA 401과 CA 313)을 사용하여 실험을 수행하여 합금 종류에 따른 공정 변수의 영향 차이를 비교 분석했습니다.
- 결과 분석 및 최적화: 얻어진 실험 데이터를 분석하여 각 공정 변수와 기공률 간의 상관관계를 정량적으로 분석하고, 이를 바탕으로 최적의 공정 조건을 제시하였습니다.
주요 Figure:
- Fig. 3: 금형 내부 압력 센서의 측정 결과. 시간에 따른 압력 변화를 보여줍니다.
- Fig. 4: 설정 집중 압력과 실측 최대 캐비티 압력의 비교 그래프.
- Fig. 5: 설정 주입 속도와 실측 주입 속도의 비교 그래프.
- Fig. 6, 7: 지연 시간과 기공률 간의 관계를 보여주는 그래프 (DA 401, CA 313 합금).
- Fig. 8, 9: 캐비티 위치 1에서의 최대 압력과 기공률 간의 관계를 보여주는 그래프 (CA 313, DA 401 합금).
- Fig. 10, 11: 캐비티 위치 3에서의 최대 압력과 기공률 간의 관계를 보여주는 그래프 (DA 401, CA 313 합금).
- Fig. 12, 13: 설정 집중 압력과 기공률 간의 관계를 보여주는 그래프 (DA 401, CA 313 합금).
- Fig. 14, 15: 실측 주조 속도와 기공률 간의 관계를 보여주는 그래프 (DA 401, CA 313 합금).
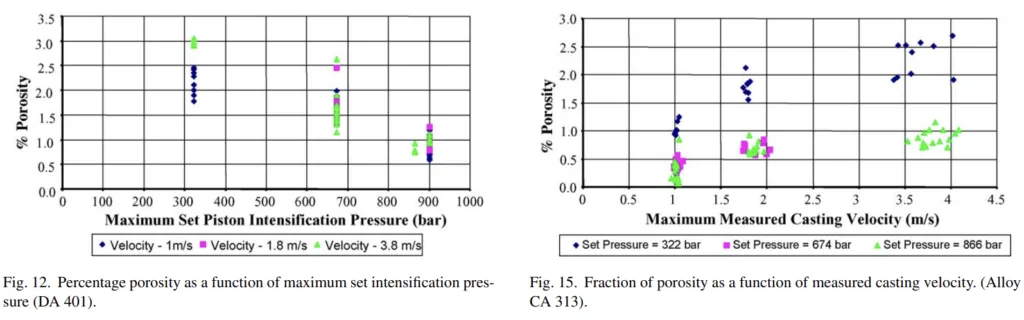
결과 및 성과:
- 정량적 결과: 다양한 공정 변수 조건에서 측정된 기공률 데이터를 통해 집중 압력 증가에 따른 기공률 감소, 주조 속도 증가에 따른 기공률 증가 등의 정량적 관계를 제시했습니다. 설정 압력과 실측 압력 간의 차이도 정량적으로 분석했습니다.
- 정성적 결과: 금형 내부 압력 센서를 이용한 실시간 압력 측정을 통해 고압 다이캐스팅 공정에 대한 이해를 심화시켰습니다. 설정된 공정 변수와 실제 공정 변수 간의 차이를 분석하여 공정 제어의 중요성을 강조했습니다. 최종적으로, 실험을 통해 제조된 부품은 균일한 기계적 특성을 보였습니다.
- 기술적 성과: 본 연구는 고압 다이캐스팅 공정의 최적화를 위한 새로운 방법론을 제시했습니다. 금형 내부 압력 센서를 이용하여 실시간 모니터링 및 제어를 통해 기공과 같은 결함을 최소화하고 제품 품질을 향상시킬 수 있음을 보여주었습니다. 이는 고압 다이캐스팅을 이용한 고품질 알루미늄 통신 부품의 대량 생산에 기여할 수 있는 기술적 성과입니다.
저작권 및 참고 자료:
본 자료는 Matthew S. Dargusch 등의 논문 "The influence of pressure during solidification of high pressure die cast aluminium telecommunications components"를 기반으로 작성되었습니다.
논문 출처: DOI: 10.1016/j.jmatprotec.2006.05.001
저작권 © 2006 Elsevier B.V. 모든 권리 보유. 본 자료는 위 논문을 바탕으로 요약 작성되었으며, 상업적 목적으로 무단 사용이 금지됩니다.