본 기술 요약은 S. Madhukar, A. Shravan, P. Vidyanand Sai, Dr. V.V. Satyanarayana가 International Journal of Mechanical Engineering and Technology (2016)에 발표한 학술 논문 "A critical review on cryogenic machining of titanium alloy (TI-6AL-4V)"를 기반으로 합니다. 이 내용은 HPDC 전문가를 위해 캐스트맨(CASTMAN) 전문가들이 Gemini, ChatGPT, Grok과 같은 LLM AI의 도움을 받아 분석하고 요약했습니다.
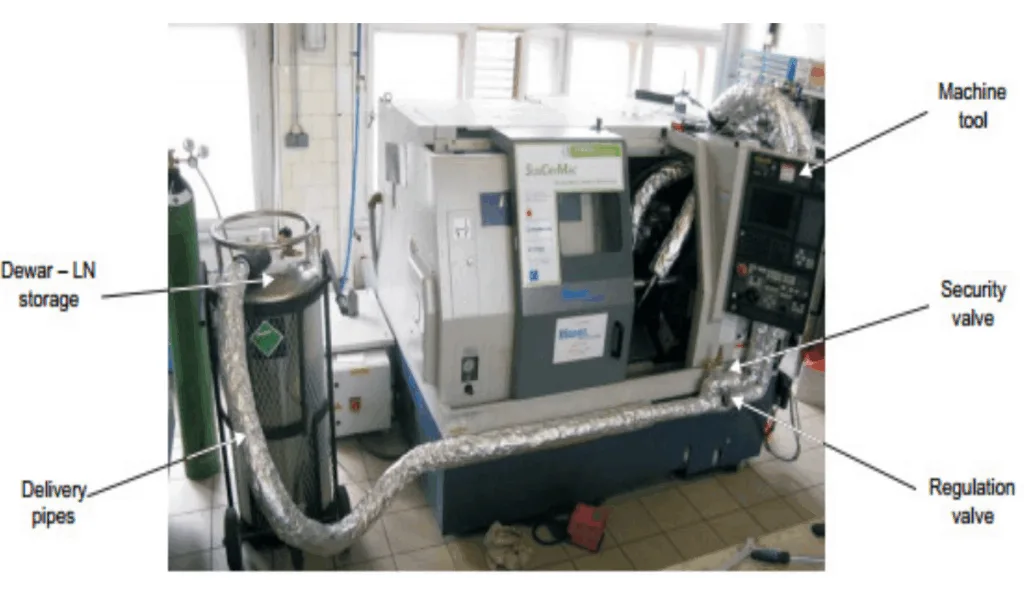
키워드
- 주요 키워드: 티타늄 합금의 극저온 가공
- 보조 키워드: Ti-6Al-4V, 액체질소 냉각제, 난삭재, 공구 수명, 항공우주용 합금, 지속가능한 가공, 표면 조도 개선
핵심 요약
- 과제: Ti-6Al-4V와 같은 티타늄 합금은 항공우주 및 기타 고성능 산업에서 매우 중요하지만, 가공이 매우 어려워 극심한 공구 마모와 낮은 표면 품질을 야기합니다.
- 연구 방법: 본 연구는 기존의 습식 절삭유를 대체하는 방안으로, 특히 액체질소(LN2)를 이용한 극저온 냉각 방식의 적용을 검토합니다.
- 핵심 연구 결과: 극저온 가공은 열을 효과적으로 제거하여 절삭 공구를 변형이나 구성인선(built-up edge) 형성으로부터 보호합니다. 그 결과, 기존 방식에 비해 우수한 표면 조도, 절삭 저항 감소, 더 높은 재료 제거율(MRR), 그리고 획기적으로 연장된 공구 수명을 달성할 수 있습니다.
- 핵심 결론: 액체질소를 냉각제로 사용하는 것은 경질 재료 가공에 있어 기술적으로 유리하고 환경친화적인 대안입니다. 이는 핵심 생산 지표를 개선할 뿐만 아니라, 석유 기반 오일과 관련된 환경적 유해성과 처리 비용을 제거합니다.
과제: 이 연구가 제조 전문가에게 중요한 이유
수십 년 동안 엔지니어들은 티타늄 합금과 같은 고강도 소재의 낮은 가공성과 씨름해 왔습니다. 논문의 서론에서 언급된 바와 같이, 이 합금들은 탁월한 강도 대 중량비와 내식성을 제공하지만, 그 특성 자체가 가공에 상당한 장애물이 됩니다. 절삭 지점에서 발생하는 높은 열과 응력은 공구의 급격한 마모를 유발하며, 특히 티타늄은 대부분의 공구 재료와 강한 화학적 친화력을 가지고 있어 문제를 더욱 악화시킵니다.
기존의 Al₂O₃ 같은 공구 코팅은 열전도율이 낮아 열 방출을 막기 때문에 효과가 없습니다. 마찬가지로, 티타늄 카바이드 및 질화물 코팅도 피삭재와의 화학적 반응성 때문에 적합하지 않습니다. 이로 인해 제조업체는 생산성을 저하시키고 비용을 증가시키는 낮은 절삭 속도를 사용할 수밖에 없었습니다. 이 논문은 이러한 문제의 근본 원인인 과도한 열을 해결하는 강력한 솔루션, 즉 극저온 가공을 검토합니다.
접근법: 연구 방법론 분석
이 논문은 극저온 가공에 대한 기존 연구들을 비평적으로 검토합니다. 이 기술의 핵심은 기존의 유수 에멀젼 절삭유를 절삭 영역에 직접 분사되는 액체질소(LN2) 제트로 대체하는 것입니다. 그림 1에서 볼 수 있듯이, 극저온 기술은 19세기 중반부터 발전해 왔으며, 1953년에 처음으로 가공 분야에 적용 사례가 보고되었습니다.
연구 방법론은 가압된 듀어(Dewar) 저장 탱크의 LN2를 특수 공급 시스템을 통해 공작 기계로 전달하는 과정을 포함합니다(그림 2 및 그림 3 참조). Air Products사의 ICEFLY와 같은 고급 시스템은 동축 이중관 기술을 사용하여 고압의 액체질소를 조기 증발 없이 절삭 날에 직접 전달함으로써 냉각 효율을 극대화합니다(그림 4). 본 연구는 극저온 가공의 결과(MRR, 절삭력, 표면 조도)를 기존의 수용성 절삭유를 사용했을 때와 비교합니다[1].
획기적인 발견: 주요 연구 결과 및 데이터
논문에 제시된 포괄적인 검토는 티타늄 합금에 극저온 냉각을 적용했을 때의 몇 가지 중요한 이점을 강조합니다.
- 결과 1: 우수한 냉각 및 공구 보호 효과: 가장 주된 이점은 효율적인 열 제거입니다. 논문은 액체질소의 극도로 낮은 온도가 엄청난 열 전달 능력을 제공하며, 이는 "절삭 공구를 변형과 구성인선 형성으로부터 보호하여 효과적이고 효율적인 냉각에 핵심적인 역할을 했다"고 결론 내립니다.
- 결과 2: 향상된 가공 성능: 논문에서 검토된 실험들은 극저온 냉각이 "수용성 냉각제와 비교했을 때 우수한 표면 조도, 감소된 절삭력, 그리고 더 높은 MRR"로 이어진다는 것을 일관되게 보여줍니다. 이를 통해 품질이나 공구 수명을 희생하지 않고도 더 공격적인 절삭 조건 설정이 가능해집니다.
- 결과 3: 상당한 환경 및 안전상의 이점: 극저온 가공은 지속 가능하고 깨끗한 공정입니다. 표 3에 자세히 설명된 바와 같이, 액체질소는 광유에 비해 거의 제로에 가까운 지구 온난화 지수(GWP)를 가지며, 더 적은 에너지를 필요로 하고 고형 폐기물을 생성하지 않습니다. 논문의 결론은 LN2 사용이 "환경적 유해성을 줄이고" "기존 절삭유와 처리 비용을 제거한다"고 강조합니다.
- 결과 4: 난삭재에 대한 입증된 효과: 이러한 이점은 이론에 그치지 않습니다. 본 연구는 과거에는 비용이 많이 드는 연삭 작업으로만 생산할 수 있었던 티타늄 및 그 합금 가공 시, 극저온 냉각을 성공적으로 적용하여 생산성과 공구 수명을 향상시킨 수많은 연구[5-14]를 문서화했습니다.
HPDC 제품에 대한 실질적 시사점
캐스트맨은 고압 다이캐스팅(HPDC) 전문 기업이지만, 많은 첨단 부품들이 최종 사양을 만족시키기 위해 2차 가공을 필요로 한다는 것을 잘 알고 있습니다. 이 논문에서 논의된 원칙들은 고성능 주조 부품을 포함하여 난삭재를 다루는 모든 작업에 매우 중요합니다.
- 공정 엔지니어를 위해: 주조 후 가공이 필요한 부품의 경우, 본 연구 결과는 극저온 냉각을 도입하면 처리량을 크게 늘릴 수 있음을 시사합니다. 8.2절에 언급된 바와 같이 더 높은 절삭 속도(예: 최대 150m/min)를 사용할 수 있는 능력은 사이클 타임을 단축하고 전반적인 생산 효율성을 높일 수 있습니다.
- 품질 관리팀을 위해: 결론에서 언급된 바와 같이, 극저온 냉각과 개선된 표면 조도 사이의 직접적인 상관관계는 우수한 부품 품질을 달성하기 위한 신뢰할 수 있는 방법을 제공합니다. 이를 통해 2차 연마나 마감 단계를 줄이거나 없앨 수 있어 시간과 비용을 절약할 수 있습니다.
- 운영 관리자 및 EHS 리더를 위해: 표 3에서 강조된 환경적 이점은 매우 강력합니다. 극저온 가공을 채택하면 지속 가능성 목표를 달성하고, 유해한 오일 미스트에 대한 작업자 노출을 줄이며, 기존 절삭유의 구매, 관리 및 폐기와 관련된 상당한 비용을 제거할 수 있습니다. 이는 현대적이고 책임감 있는 제조 시설을 위한 전략적으로 건전한 투자입니다.
논문 상세 정보
티타늄 합금(TI-6AL-4V)의 극저온 가공에 대한 비평적 고찰
1. 개요:
- 제목(Title): A Critical Review on Cryogenic Machining of Titanium Alloy (TI-6AL-4V)
- 저자(Author): S. Madhukar, A. Shravan, P. Vidyanand Sai, Dr. V.V. Satyanarayana
- 발행 연도(Year of publication): 2016
- 발행 학술지/학회(Journal/academic society of publication): International Journal of Mechanical Engineering and Technology (IJMET)
- 키워드(Keywords): 극저온 가공(cryogenic machining), 티타늄 합금(titanium alloy), 액체 냉각제(liquid coolant)
2. 초록(Abstract):
니켈, 코발트 티타늄, 텅스텐 합금은 초경질 합금 그룹에 속하며, 그중 티타늄은 항공우주 분야에서 가장 빠르게 성장하는 재료 중 하나입니다. 설계자들이 티타늄을 선택하는 주된 이유는 특정 강도 수준에서의 상대적으로 낮은 질량과 고온에 대한 상대적 저항성 때문입니다. 티타늄은 항공기 엔진 전면부에 오랫동안 사용되어 왔으며 앞으로도 계속 사용될 것입니다. 실제로, 그 특성 덕분에 티타늄 합금은 구조 및 랜딩기어 부품에서 그 어느 때보다 널리 보급되고 있습니다. 이 합금의 한 가지 단점은 낮은 가공성입니다. 특히 Ti-6Al-4V 티타늄 합금은 공구 수명이 극히 짧은 난삭재입니다. 이 문제를 극복하기 위해 티타늄 합금 가공에 첨단 기술이 적용되고 있으며, 그중 하나가 극저온 냉각입니다. 질소는 발생된 열을 발산시키는 데 비용 효율적이고, 안전하며, 불연성이고, 환경친화적인 가스이기 때문에 가공에 더 선호됩니다. 또한, 공작물을 오염시키지 않으며, 별도의 폐기 메커니즘이 필요 없습니다. 본 논문에서는 극저온 조건에서 티타늄 합금을 가공하는 것에 대한 검토를 수행합니다.
3. 서론(Introduction):
티타늄 합금은 티타늄과 다른 화학 원소의 혼합물을 포함하는 금속입니다(표 1). 이러한 합금은 매우 높은 인장 강도와 인성(극한 온도에서도)을 가집니다. 무게가 가볍고, 탁월한 내식성과 극한의 온도를 견디는 능력을 갖추고 있습니다. 이들은 우수한 강도 대 중량비, 뛰어난 내식성 및 고온 적용성 때문에 산업 응용 분야에서 중요한 엔지니어링 재료로 간주됩니다. 티타늄 합금은 고온에서 높은 강도를 유지하고 부식에 대한 높은 저항성 때문에 항공우주 및 항공 산업에서 널리 사용되어 왔습니다. 또한 화학 공정, 자동차, 생의학 및 원자력 산업에서도 점점 더 많이 사용되고 있습니다.
티타늄 및 그 합금은 가공에서 가장 어려운 재료 중 하나입니다. 절삭 공구 재료의 발전으로 많은 난삭재를 이제 더 높은 금속 제거율로 가공할 수 있게 되었습니다. 그러나 이러한 공구 재료 중 어느 것도 티타늄과의 화학적 친화력 때문에 티타늄 가공에 효과적인 것 같지 않습니다. 공구 코팅의 새로운 개발도 티타늄 가공에 도움이 되지 않습니다. Al₂O₃ 코팅은 텅스텐 카바이드 인서트보다 열전도율이 낮아 절삭 지점의 극도로 집중된 고응력 및 고온으로부터 열이 방출되는 것을 막습니다. 티타늄 카바이드 및 티타늄 질화물 코팅은 화학적 친화력 때문에 티타늄 합금 가공에 적합하지 않습니다. 따라서 절삭 온도를 낮추고 공작물과 공구의 화학적 안정성을 향상시키는 극저온 가공은 티타늄 및 그 합금 가공에서 생산성 수준을 크게 높일 것으로 기대됩니다. 티타늄 및 그 합금에 대한 대부분의 극저온 가공 연구[5-14]는 공작물을 동결시키거나 극저온 냉각제를 사용하여 공구를 냉각할 때 개선된 가공성을 문서화했습니다.
극저온 가공은 전통적인 윤활-냉각액(물에 오일을 유화시킨 것)을 액체질소 제트로 대체하는 가공 공정입니다. 극저온 가공은 공구 수명을 늘리기 위해 황삭 작업에 유용합니다. 또한, 정삭 가공 작업에서 가공된 표면의 무결성과 품질을 보존하는 데에도 유용할 수 있습니다. 극저온 가공 테스트는 수십 년 전부터 연구자들에 의해 수행되었지만, 실제 상업적 적용은 여전히 극소수의 회사에 국한되어 있습니다. 선삭 및 밀링에 의한 극저온 가공이 모두 가능합니다. MRR, 절삭력 및 표면 조도 값이 두 환경 모두에서 연구된 이 합금들에 대해 극저온 냉각제와 수용성 냉각제 하에서 가공성 연구가 수행되었습니다. 여기서 극저온 냉각제에 대해 얻은 결과가 수용성 냉각제보다 우수합니다[1].
4. 연구 요약:
연구 주제의 배경:
Ti-6Al-4V와 같은 티타늄 합금은 높은 강도 대 중량비와 내열성으로 항공우주와 같은 산업에 필수적입니다. 그러나 높은 열 발생과 절삭 공구와의 화학적 반응성으로 특징지어지는 낮은 가공성은 매우 짧은 공구 수명을 야기하고 제조 생산성을 제한합니다.
이전 연구 현황:
논문에서 인용된 이전 연구[5-14]는 극저온 냉각제를 사용하여 티타늄의 가공성이 향상되었음을 문서화했습니다. 수십 년 동안 연구가 수행되었으며, 극저온 방식의 MRR, 절삭력 및 표면 조도를 기존의 수성 냉각 방식과 비교한 결과, 극저온 방식이 우수함을 보여주었습니다[1]. 이 논문은 이 기술의 역사적 발전(그림 1), 적용 방법(그림 2, 3, 4), 그리고 이점을 검토합니다.
연구 목적:
이 논문의 목적은 티타늄 합금 가공의 어려움을 극복하기 위한 첨단 기술로서 극저온 가공을 비평적으로 검토하는 것입니다. 그 이점, 공정 변수 및 기존의 덜 효과적이고 환경에 유해한 냉각 방식을 대체할 가능성에 대한 연구 결과를 종합하는 것을 목표로 합니다.
핵심 연구:
이 연구의 핵심은 티타늄 가공에서 액체질소(LN2)를 냉각제로 사용하는 것에 관한 문헌 분석입니다. 극저온 냉각이 공구 수명, 표면 조도 및 재료 제거율을 개선하는 메커니즘을 탐구합니다. 또한 LN2의 환경적 영향을 다른 냉각제와 비교하고(표 3), 유량 및 절삭 속도와 같은 실제 공정 변수에 대해 논의합니다(섹션 8).
5. 연구 방법론
연구 설계:
본 논문은 비평적 검토로서, 극저온 가공이라는 주제에 대한 기존의 학술 및 기술 문헌의 종합 및 분석을 기반으로 설계되었습니다. 새로운 실험 데이터를 제시하는 대신, 포괄적인 결론을 도출하기 위해 이전 연구 결과를 정리하고 평가합니다.
데이터 수집 및 분석 방법:
데이터는 학술지 논문, 학회 회보, 기술 가이드 등 다양한 출처[1-17]에서 수집되었습니다. 분석은 여러 연구의 결과를 비교하고 대조하여 일관된 경향, 이점 및 티타늄 합금의 극저온 가공을 위한 확립된 공정 변수를 식별하는 것을 포함합니다.
연구 주제 및 범위:
연구의 범위는 티타늄 합금의 특성 및 응용, 극저온 기술의 역사적 발전, 기계에 극저온 냉각제를 공급하는 방법, 잠재적 이점(기술적, 경제적, 환경적), 그리고 선삭 및 밀링 작업을 위한 주요 공정 변수를 포함합니다.
6. 주요 결과:
주요 결과:
- 액체질소를 이용한 극저온 냉각은 절삭 공구를 열 손상, 변형, 구성인선 형성으로부터 효과적으로 보호하여 공구 수명을 연장시킵니다.
- 기존의 수용성 냉각제와 비교하여, 극저온 가공은 더 나은 표면 조도, 더 낮은 절삭력, 그리고 더 높은 재료 제거율(MRR)을 보입니다.
- 액체질소 사용은 탄화수소 기반 오일을 제거하고, 에너지 사용을 줄이며, 표 3에서 보듯이 고형 폐기물을 생성하지 않는 환경친화적인 대안입니다.
- 이 기술은 ICEFLY 동축관(그림 4)과 같은 시스템을 사용하여 절삭 영역에 LN2를 공급하는 확립된 방법으로 잘 개발되어 있습니다.
- 극저온 냉각을 이용한 티타늄 합금의 일반적인 절삭 조건은 절삭 속도 70-150m/min, 이송 속도 0.10-0.25mm/rev 범위입니다 (8.2절).
그림 목록:
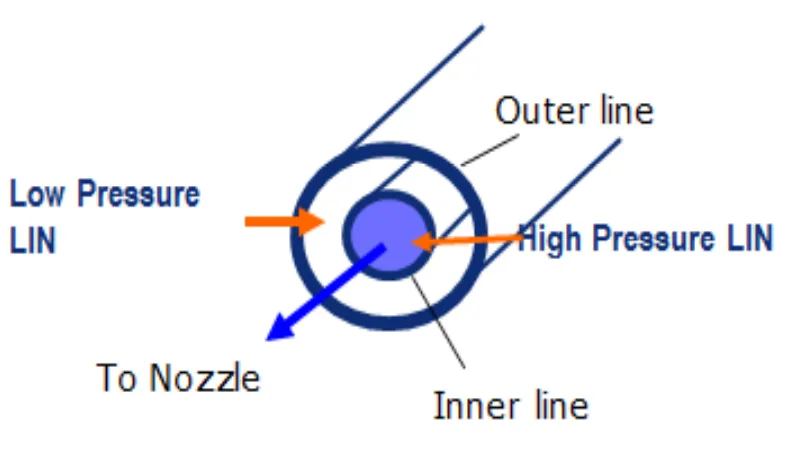
- Figure 1 극저온 기술의 초기 주요 단계 연대표
- Figure 2 극저온 냉각 장치 개략도
- Figure 3 극저온 가공 장치
- Figure 4 액체질소(LN₂) 분사 과정
7. 결론:
액체질소는 액체 상태에서 매우 낮은 온도로 인해 엄청난 열 제거 능력을 가지고 있습니다. 액체질소는 절삭 공구를 변형 및 구성인선 형성으로부터 보호함으로써 가공 중 효과적이고 효율적인 냉각에 핵심적인 역할을 했습니다. 수행된 실험들은 또한 수용성 냉각제와 비교했을 때 우수한 표면 조도, 감소된 절삭력, 더 높은 MRR을 가짐을 증명합니다. 액체질소는 경질 재료 가공을 위한 유리하고 대안적인 냉각제입니다. 액체질소의 사용은 석유 기반 광유에서 발생하는 탄화수소로 인한 환경적 피해를 줄이고, 기존 냉각제를 제거하며, 냉각제 처리 비용을 절감합니다.
8. 참고문헌:
- [1] [1]A.R. Machado, J. Wallbank, Machining of titanium and its alloys: a review, Proc. Inst. Mech.Eng. 204 (1990) 53.
- [2] [2]P.D. Hartung, B.M. Kramer, Tool wear in titanium machining, Ann. CIRP 31 (1982) 75–80.
- [3] [3]M.J. Donachie Jr., in: ASM (Ed.), Titanium, a Technical Guide, 1982, p. 163.
- [4] [4]R. Komanduri, B.F. von Turkovich, New observation on the mechanism of chip formation when machining titanium alloys, Wear 69 (1981) 179–188.
- [5] [5] E.H. Rennhack, N.D. Carlsted, Effect of temperature on the lathe machining characteristics of Ti-6-4, in: Ann.Trans. Technol. Conf., 1974, p. 467.
- [6] [6] D. Ulutan and T. Ozel, Machining induced surface integrity in titanium and nickel alloys: a review, International Journal of Machine Tools and Manufacture, vol. 51, pp. 250-280, 2011.
- [7] [7] E. Ezugwu, High speed machining of aero-engine alloys, Journal of the Brazilian society of mechanical sciences and engineering, vol. 26, pp. 1-11, 2004.
- [8] [8]V. I. Babitsky, V. V. Silberschmidt, A. Roy, and A. Maurotto, Analysis of machinability of Ti-and Ni-based alloys, Solid State Phenomena, vol. 188, pp. 330-338, 2012.
- [9] [9]A. Shokrani, V. Dhokia, and S. T. Newman, Environmentally conscious machining of difficult-to machine materials with regard to cutting fluids, International Journal of Machine Tools and Manufacture, vol. 57, pp. 83-101, 2012.
- [10] [10] D. Lung, F. Klocke, and A. Krämer, High Performance Cutting of Aerospace Materials, Advanced Materials Research, vol. 498, pp. 127-132, 2012.
- [11] [11]Y. Yildiz and M. Nalbant, A review of cryogenic cooling in machining processes, International Journal of Machine Tools and Manufacture, vol. 48, pp. 947-964, 2008.
- [12] Saravanan P Sivam, Dr. Antony Michael Raj and Dr. Satish Kumar S, “Influence Ranking of Process Parameters in Electric Discharge Machining of Titanium Grade 5 Alloy using Brass Electrode". International Journal of Mechanical Engineering and Technology (IJMET), 4(5), 2013,pp. 71–80.
- [13] [12]E. Ezugwu, J. Bonney, and Y. Yamane, An overview of the machinability of aeroengine alloys, Journal of Materials Processing Technology, vol. 134, pp. 233-253, 2003.
- [14] [13] E. Ezugwu and Z. Wang, Titanium alloys and their machinability—a review, Journal of Materials Processing Technology, vol. 68, pp. 262-274, 1997.
- [15] [14]C. Machai, A. Iqbal, D. Biermann, T. Upmeier, and S. Schumann, On the Effects of Cutting Speed and Cooling Methodologies in Grooving Operation of Various Tempers of β-Titanium Alloy, Journal of Materials Processing Technology, 2013.
- [16] Rajesh Nayak and Ravirajshetty, “Cutting Force and Surface Roughness in Cryogenic Machining of Elastomer”. International Journal of Mechanical Engineering and Technology (IJMET), 5(9), 2014, pp. 151-156.
- [17] [15]V. Venkatesh, T. T. Mon, J. Ramli, A. Jeefferie, and S. Sharif, Performance of cryogenic machining with nitrogen gas in machining of titanium Applied Mechanics and Materials, vol. 52, pp. 2003-2008, 2011.
전문가 Q&A: 가장 중요한 질문에 대한 답변
Q1: 기존의 습식(Flood) 냉각 방식이 티타늄 합금 가공에 효과적이지 않은 이유는 무엇인가요?
A1: 논문의 서론에 따르면, 기존 냉각 방식이 실패하는 두 가지 주된 이유가 있습니다. 첫째, 티타늄 합금은 열전도율이 매우 낮아 열이 공작물을 통해 분산되지 않고 절삭 지점에 집중됩니다. 둘째, 티타늄은 대부분의 공구 재료와 높은 화학적 친화력을 가지며, 이 반응성은 고온에서 가속화되어 빠른 공구 마모를 유발합니다. 기존 냉각제는 종종 이러한 문제를 예방할 만큼 빠르게 열을 제거하지 못합니다.
Q2: 극저온 가공으로 전환할 때의 주요 환경적 이점은 무엇인가요?
A2: 논문의 결론과 표 3은 명확한 답변을 제공합니다. 액체질소를 이용한 극저온 가공은 환경 유해물질이며 폐기 비용이 많이 드는 석유 기반 광유의 사용을 없앱니다. 표 3에서 볼 수 있듯이, 액체질소는 광유의 3.56kg CO₂eq에 비해 지구 온난화 지수(GWP)가 0.00kg CO₂eq이며 고형 폐기물을 생성하지 않습니다.
Q3: 액체질소(LN2)가 끓어 없어지기 전에 어떻게 절삭 영역에 효과적으로 적용되나요?
A3: 논문의 6절에서는 ICEFLY 시스템이라는 특수 공급 방법을 설명합니다. 이 시스템은 "동축 이중관 기술"을 사용하는데, 고압의 LN2가 내부 튜브를 통해 흐르고, 이 튜브는 외부 튜브의 저압 LN2 재킷으로 단열됩니다. 이 설계는 열 손실을 최소화하고 "액체가 커터에 분사될 수 있는 튜브 끝까지 도달하도록 보장합니다." 그림 4는 이 분사 과정을 보여줍니다.
Q4: 공구 수명 연장 외에 극저온 냉각으로 개선되는 다른 주요 성능 지표는 무엇인가요?
A4: 논문의 결론은 실험을 통해 극저온 냉각이 "수용성 냉각제와 비교했을 때 우수한 표면 조도, 감소된 절삭력, 그리고 더 높은 재료 제거율(MRR)"을 가져온다고 명시적으로 밝히고 있습니다. 이는 부품을 더 빠르고, 더 좋은 품질로, 그리고 공작 기계에 가해지는 스트레스를 줄이면서 가공할 수 있음을 의미합니다.
Q5: Ti-6Al-4V의 극저온 가공에 권장되는 절삭 속도와 이송 속도가 있나요?
A5: 예, 8.2절에서 검토된 문헌을 바탕으로 한 일반적인 매개변수를 제공합니다. 티타늄 기반 합금의 경우, 절삭 속도는 보통 70-150m/min 범위에서 테스트되었으며, 이송 속도는 0.10-0.25mm/rev 사이였습니다. 절삭 깊이는 일반적으로 0.30-2.00mm 범위였습니다.
결론 및 다음 단계
이 연구는 Ti-6Al-4V와 같은 난삭재의 가공성을 향상시키기 위한 귀중한 로드맵을 제공합니다. 연구 결과는 품질을 개선하고, 공구 수명을 연장하며, 더 안전하고 지속 가능한 제조 환경을 만들기 위한 명확하고 데이터에 기반한 경로를 제시합니다. 근본적인 문제인 열 발생을 원천에서 해결함으로써, 극저온 가공은 새로운 차원의 생산성을 열어줍니다.
캐스트맨(CASTMAN)은 최신 산업 연구 결과를 적용하여 고객의 가장 어려운 제조 문제를 해결하는 데 전념하고 있습니다. 세계 최고 수준의 다이캐스팅 부품은 종종 고정밀 2차 가공을 필요로 한다는 것을 잘 알고 있습니다. 이 논문에서 논의된 가공 문제가 귀사의 운영 목표와 관련이 있다면, 저희 엔지니어링 팀에 문의하여 부품의 전체 수명 주기를 최적화하는 데 어떻게 협력할 수 있는지 논의해 주십시오.
저작권
- 본 자료는 "S. Madhukar, A. Shravan, P. Vidyanand Sai, Dr. V.V. Satyanarayana"의 "A critical review on cryogenic machining of titanium alloy (TI-6AL-4V)" 논문을 기반으로 합니다.
- 논문 출처: 검토된 논문은 http://www.iaeme.com/ijmet/issues.asp?JType=IJMET&VType=7&IType=5 에서 확인 가능합니다.
본 자료는 정보 제공 목적으로만 사용됩니다. 상업적 무단 사용을 금합니다. Copyright © 2025 CASTMAN. All rights reserved.