핫챔버 vs. 콜드챔버: 귀사의 마그네슘 다이캐스팅에 가장 적합한 공정은?
이 기술 브리핑은 Dr. Ing Norbert Erhard와 Bob Tracy가 작성한 FRECH 백서 "[Properties of Diecasting Alloys and a Comparison of Hot and Cold Chamber Processes for Magnesium Die Casting]"을 기반으로 합니다. HPDC 전문가를 위해 CASTMAN의 전문가들이 요약 및 분석하였습니다.
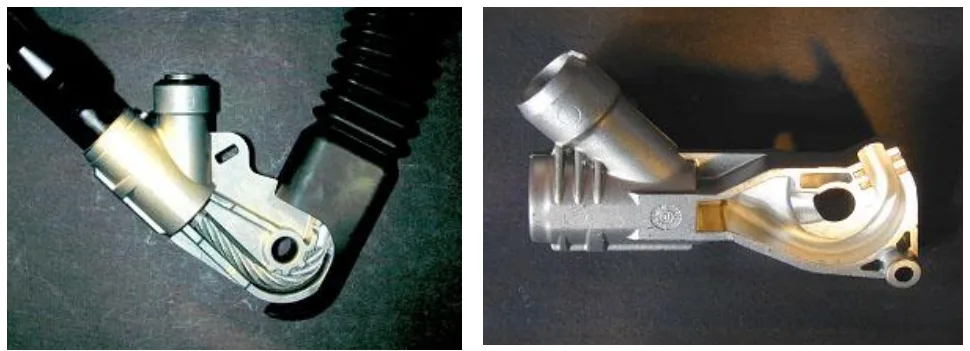
키워드
- 주요 키워드: 마그네슘 다이캐스팅 공정 비교
- 보조 키워드: 핫챔버 다이캐스팅, 콜드챔버 다이캐스팅, 박벽 주조, 다이캐스팅 합금 특성, AZ91, AM60 합금, 다이캐스팅 공정 최적화
Executive Summary
- 과제: 자동차 및 전자 산업에서 마그네슘 사용이 증가함에 따라, 특정 부품의 요구사항(예: 벽 두께, 기계적 특성)에 맞는 최적의 다이캐스팅 공정을 선택하는 것이 중요해졌습니다.
- 방법: 본 연구는 마그네슘 다이캐스팅에 사용되는 핫챔버(Hot Chamber)와 콜드챔버(Cold Chamber) 두 공정을 형체력, 사이클 타임, 비압, 온도 제어, 가스 혼입 등 다양한 기술 및 운영 파라미터를 기준으로 심층 비교 분석합니다.
- 핵심 돌파구: 1.2mm 미만의 박벽(thin-wall) 부품에는 핫챔버 공정이 더 경제적이고 우수한 품질을 제공하는 반면, 뚜렷한 기계적 특성이 요구되는 후벽(thick-wall) 부품이나 더 낮은 기공률이 필요한 주물에는 콜드챔버 공정이 더 적합하다는 사실을 명확히 했습니다.
- 결론: 성공적인 마그네슘 다이캐스팅의 핵심은 부품의 최종 용도와 요구되는 특성에 따라 핫챔버와 콜드챔버 공정 중 올바른 것을 선택하는 것입니다.
과제: 이 연구가 HPDC 전문가에게 중요한 이유
아연(Zn), 알루미늄(Al), 마그네슘(Mg) 합금의 전 세계적인 소비는 최근 몇 년간 꾸준히 증가해 왔습니다. 특히 알루미늄과 마그네슘 경금속 주물의 70% 이상이 자동차 산업에서 사용되고 있습니다. 마그네슘은 알루미늄보다 약 50% 가볍고 아연보다는 4배나 가벼워 경량화가 필수적인 분야에서 각광받고 있습니다 (Table 1).
그러나 단순히 가볍다고 해서 모든 부품에 적합한 것은 아닙니다. 복잡한 형상, 높은 치수 정밀도, 우수한 기계적 특성 및 비용 효율성을 모두 만족시켜야 합니다. 특히 마그네슘 다이캐스팅에서는 핫챔버와 콜드챔버라는 두 가지 주요 공정 중 하나를 선택해야 하는 과제에 직면합니다. 이 선택은 최종 제품의 품질, 생산성, 그리고 비용에 직접적인 영향을 미치기 때문에, 각 공정의 장단점을 명확히 이해하는 것은 모든 엔지니어와 생산 관리자에게 매우 중요합니다. 이 연구는 바로 그 선택의 기준을 제시합니다.
접근 방식: 방법론 분석
이 백서는 특정 실험을 설계하기보다는, 업계에서 축적된 광범위한 데이터와 경험을 바탕으로 핫챔버와 콜드챔버 마그네슘 다이캐스팅 공정을 종합적으로 비교 분석합니다. 연구는 다음과 같은 핵심적인 공정 변수들을 중심으로 두 방식을 대조합니다.
- 기계 및 공정 파라미터: 형체력(Locking force), 주조 용량, 사이클 타임, 사출 속도 및 비압(specific pressure)과 같은 기계적 사양을 비교합니다 (Table 2).
- 열 관리: 용탕 온도, 온도 변화, 산화물 형성 및 보호 가스 소비량을 분석하여 각 공정의 열적 안정성과 효율성을 평가합니다 (Table 3).
- 품질에 미치는 영향: 슬리브 내 공기량, 게이팅 방식, 금형 수명 등 주물 품질에 직접적인 영향을 미치는 요인들을 심층적으로 다룹니다 (Figures 7, 8, 9).
- 부품 특성: 최종 생산된 부품의 최소 벽 두께, 강도 및 연신율, 기공률, 표면 경도 등과 같은 핵심적인 기계적 및 물리적 특성을 비교합니다.
이러한 다각적인 접근을 통해, 연구는 어떤 조건에서 어떤 공정이 더 유리한지에 대한 명확하고 실용적인 가이드라인을 제공합니다.
돌파구: 주요 발견 및 데이터
이 비교 분석을 통해 각 공정이 특정 응용 분야에서 뚜렷한 장점을 가진다는 것이 밝혀졌습니다.
발견 1: 공정 압력과 기계 크기의 차이
핫챔버 공정은 160-250 bar의 상대적으로 낮은 비압을 사용하는 반면, 콜드챔버 공정은 400-1400 bar에 달하는 훨씬 높은 압력을 필요로 합니다 (Table 2). 이는 핫챔버 공정이 더 작은 형체력의 기계로도 운영될 수 있음을 의미하며, 이는 설비 투자 및 공간 활용 측면에서 이점을 가집니다.발견 2: 가스 혼입 및 주물 품질
핫챔버 공정에서는 구즈넥(gooseneck)이 항상 100% 용탕으로 채워져 있어 슬리브 내 공기 혼입이 거의 없습니다 (Figure 7). 반면, 콜드챔버 공정은 용탕을 국자(ladle)로 떠서 부분적으로 채워진(최대 2/3) 슬리브에 주입하므로 더 많은 공기와 산화물이 주물에 혼입될 가능성이 높습니다 (Figure 8). 이로 인해 박벽 부품의 경우 핫챔버가 더 우수한 품질을 보입니다.발견 3: 부품 특성에 따른 공정 적합성
핫챔버 공정은 0.5mm까지의 매우 얇은 벽을 주조하는 데 이상적입니다. 이는 전자 기기 하우징(Figure 6)과 같은 부품에 적합합니다. 그러나 2mm 이상의 두꺼운 벽을 가진 부품이나 높은 연신율과 같은 특정 기계적 특성이 요구될 경우, 콜드챔버 공정이 더 나은 결과를 제공합니다 (Parts Properties 섹션, 9페이지).발견 4: 효율성 및 비용
핫챔버는 사이클 타임이 더 짧고 기계가 차지하는 공간이 적어 생산성이 높습니다. 하지만 구즈넥, 피스톤 등 고가의 소모성 부품 교체에 더 많은 시간이 소요될 수 있습니다. 콜드챔버는 사이클 타임이 길지만, 소모품 교체는 상대적으로 간단합니다 (Cycle Time 및 Costs of Wear Parts 섹션).
귀사의 HPDC 운영을 위한 실질적인 시사점
이 연구 결과는 실제 생산 현장에서 다음과 같은 실질적인 이점을 제공할 수 있습니다.
공정 엔지니어: Figure 6에 보이는 것과 같은 박벽 전자 부품 하우징을 생산할 경우, 이 연구는 핫챔버 공정이 더 높은 생산성과 우수한 표면 품질을 달성하는 데 효과적임을 시사합니다. 반대로, 구조적 강도가 중요한 두꺼운 자동차 부품에는 콜드챔버 공정을 우선적으로 고려해야 합니다.
품질 관리: 콜드챔버 공정에서 가스 기공 발생 가능성이 더 높다는 점("Gas porosity" 섹션)은, 이 공정으로 생산된 부품의 경우 해당 결함에 대한 QC 검사를 더욱 강화해야 함을 의미합니다. 이는 불량률을 사전에 관리하는 데 중요한 지표가 될 수 있습니다.
금형 설계: 이 연구는 콜드챔버 공정의 금형 설계 시, 더 빠른 응고를 보상하기 위해 더 큰 게이트와 더 높은 금형 온도가 필요하다고 지적합니다("Gate thickness", "Die temperature" 섹션). 이는 금형 설계 단계에서부터 최종 제품의 품질을 확보하기 위해 반드시 고려해야 할 사항입니다.
논문 상세 정보
[Properties of Diecasting Alloys and a Comparison of Hot and Cold Chamber Processes for Magnesium Die Casting]
1. 개요:
- 제목: Properties of Diecasting Alloys and a Comparison of Hot and Cold Chamber Processes for Magnesium Die Casting
- 저자: Dr. Ing Norbert Erhard, Bob Tracy
- 발행 연도: N/A
- 저널/학회: FRECH White Paper
- 키워드: Magnesium, Die Casting, Hot Chamber, Cold Chamber, Diecasting Alloys
2. 초록:
전 세계적으로 자동차 산업을 중심으로 아연, 알루미늄, 마그네슘 다이캐스팅 합금의 소비가 증가하고 있다. 특히 마그네슘은 가장 가벼운 상용 다이캐스팅 합금으로, 경량화가 중요한 응용 분야에서 선호된다. 이 문서는 마그네슘 다이캐스팅에 사용되는 두 가지 주요 공정인 핫챔버와 콜드챔버 공정을 비교 분석한다. 각 공정의 물리적, 기계적 특성, 공정 파라미터, 장단점을 상세히 기술하여, 부품의 요구사항에 따라 최적의 공정을 선택할 수 있는 기술적 근거를 제공하는 것을 목표로 한다.
3. 서론:
아연(Zn), 알루미늄(Al), 마그네슘(Mg) 합금의 전 세계적인 소비는 지난 몇 년간 증가해왔다. 전체 알루미늄 및 마그네슘 경금속 주물의 70%가 자동차 산업에서 사용된다. 알루미늄은 마그네슘보다 약 50% 무겁고, 아연은 마그네슘보다 약 4배 무겁다(Table 1). 그러나 특정 기계적 특성이 요구되는 응용 분야에서는 이러한 재료들이 선호된다. 이 문서는 다이캐스팅 합금의 특성을 살펴보고, 특히 마그네슘 다이캐스팅의 핫챔버 및 콜드챔버 공정을 비교 분석한다.
4. 연구 요약:
연구 주제의 배경:
경량화가 핵심 경쟁력인 자동차 및 전자 산업에서 마그네슘 합금의 사용이 증가하고 있다. 마그네슘 다이캐스팅 부품을 생산하는 데에는 크게 핫챔버와 콜드챔버 두 가지 공정이 있으며, 어떤 공정을 선택하느냐에 따라 생산성, 품질, 비용이 크게 달라진다.
이전 연구 현황:
본 문서는 특정 선행 연구를 인용하기보다는, 업계에서 일반적으로 알려진 각 공정의 특성과 FRECH사의 다년간 축적된 경험 및 데이터를 기반으로 한 비교 분석을 제시한다.
연구 목적:
마그네슘 다이캐스팅에서 핫챔버와 콜드챔버 공정의 차이점을 다방면으로 비교하여, 다이캐스팅 업체가 특정 부품의 요구사항(벽 두께, 기계적 강도, 표면 품질 등)에 가장 적합한 공정을 선택할 수 있도록 돕는 실용적인 가이드를 제공하는 것이다.
핵심 연구:
핫챔버와 콜드챔버 공정을 기계 크기, 사이클 타임, 사출 압력, 용탕 온도 관리, 가스 혼입, 금형 수명, 소모품 비용, 그리고 최종 부품의 특성(벽 두께, 기공률, 기계적 성질) 등 다양한 측면에서 비교한다. 이를 통해 각 공정의 장단점을 명확히 하고, 적용 분야에 따른 최적의 선택 기준을 제시한다.
5. 연구 방법론
연구 설계:
본 연구는 통제된 단일 실험이 아닌, 두 공정 간의 포괄적인 비교 분석(Comparative Analysis) 방식을 채택했다. 실제 산업 현장에서 사용되는 공정 파라미터, 기계 사양, 그리고 그 결과로 나타나는 부품의 특성을 기반으로 두 공정을 대조한다.
데이터 수집 및 분석 방법:
데이터는 FRECH사의 다이캐스팅 기계 사양(Table 2), 일반적인 합금의 물리적/기계적 특성 데이터(Table 1), 합금별 권장 용탕 온도(Table 3), 그리고 공정 메커니즘을 설명하는 도식(Figures 7, 8, 9)을 통해 수집 및 제시되었다. 분석은 이러한 데이터를 바탕으로 각 공정의 효율성, 품질, 비용 측면의 장단점을 정성적, 정량적으로 비교하는 방식으로 이루어졌다.
연구 주제 및 범위:
연구는 마그네슘 다이캐스팅에 초점을 맞추고 있으며, 핫챔버와 콜드챔버 공정의 비교에 국한된다. 비교 항목은 공정 자체의 특성(압력, 속도, 온도), 금형 관련 이슈(수명, 게이팅), 그리고 최종 주조품의 품질(기공, 표면, 기계적 특성)을 포함한다.
6. 주요 결과:
주요 결과:
- 공정 선택: 박벽(< 1.2 mm) 부품에는 핫챔버가, 후벽 부품이나 특정 기계적 특성 및 저기공성이 요구될 때는 콜드챔버가 더 적합하다.
- 품질: 핫챔버는 슬리브가 항상 용탕으로 가득 차 있어 공기 혼입이 적고, 박벽 부품에서 더 나은 품질을 보인다. 콜드챔버는 공기 및 산화물 혼입 가능성이 더 높다.
- 효율성: 핫챔버는 사이클 타임이 짧고 기계가 작아 생산성이 높지만, 콜드챔버는 더 큰 부품을 생산할 수 있다.
- 비용: 핫챔버는 구즈넥 등 고가 소모품의 교체 비용과 시간이 더 많이 들 수 있다.
- 합금 제한: 핫챔버는 용탕 온도가 650°C를 초과하면 피스톤 링과 슬리브 사이의 누설 문제로 인해 사용 가능한 합금에 제한이 있다.
Figure 이름 목록:
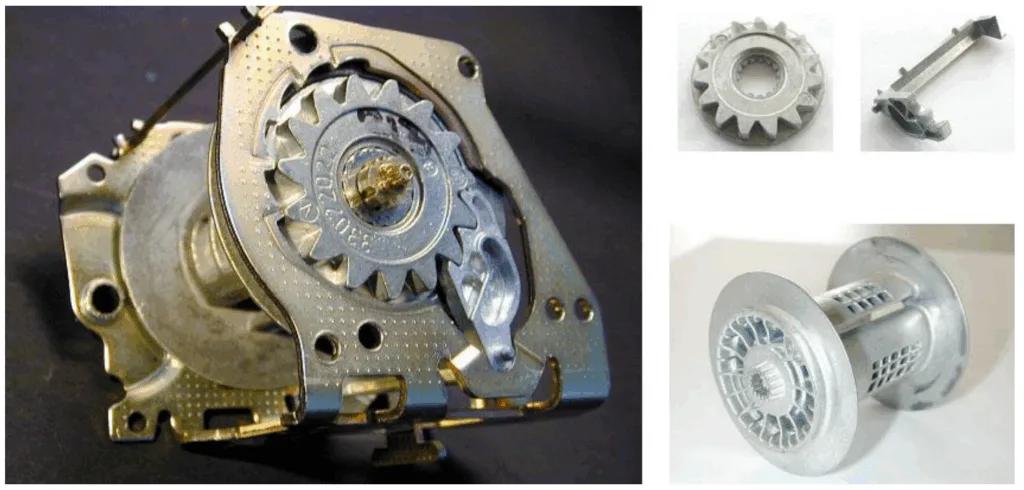
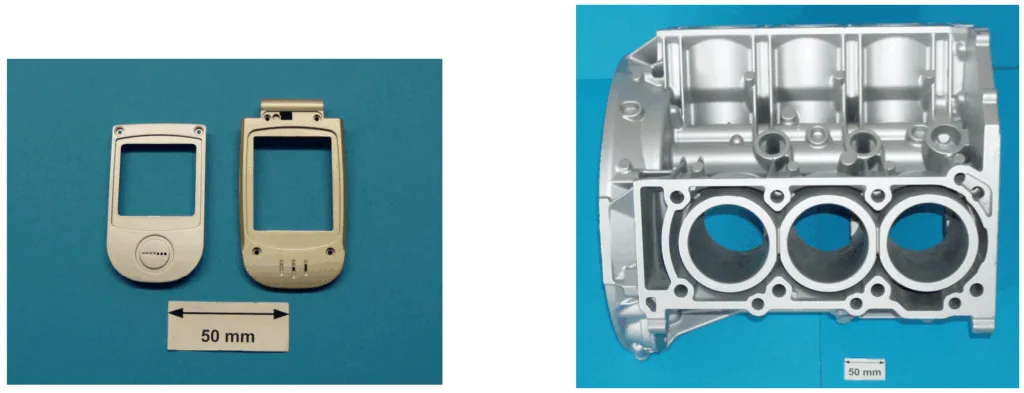
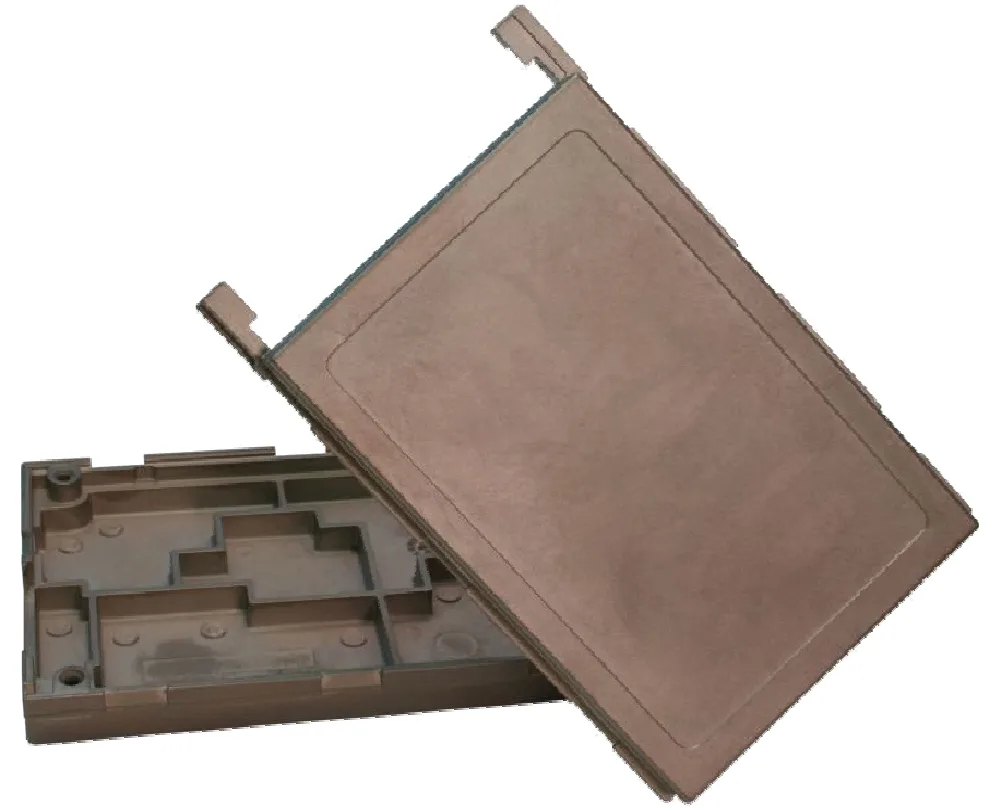
- Figure 1 - Casting „Belt-taut“ (Zinc) (source: Foehl, Germany)
- Figure 2 - Supporting Frame with wall thickness up to 0.6mm (project Fohl, Germany)
- Figure 3 - Belt roll (Zinc) (source: Foehl, Germany)
- Figure 4 - Mobile phone (Mg)
- Figure 5 - Zylinder crank housing (Al) (source: Honsel, Germany)
- Figure 6 - Electronic Device (Mg), Fishercast, CANADA
- Figure 7 - Ventilation of die in hot chamber process
- Figure 8 - Ventilation of die in cold chamber process
- Figures 9 - Gating for the hot chamber process
- Figures 9 - Gating for the cold chamber processes
7. 결론:
제시된 결과와 경험적 가치들은 1.2mm 미만의 박벽 부품은 핫챔버 기계에서 주조하는 것이 더 낫다는 것을 보여준다. 이것이 더 경제적이며 주물의 품질도 더 좋다. 후벽 부품에 대해 뚜렷한 기계적 특성이 요구되거나 더 적은 기공률을 가진 주물 품질이 요구된다면, 이러한 부품은 콜드챔버 기계에서 주조하는 것이 더 낫다. 핫챔버와 콜드챔버 공정의 비교는 다이캐스팅 업체가 요구되는 주조 특성에 따라 올바른 공정을 선택하는 데 도움이 될 것이다.
8. 참고 문헌:
- 본 문서에는 외부 참고 문헌이 명시되어 있지 않습니다.
결론 및 다음 단계
이 연구는 HPDC 공정에서 핵심적인 품질과 생산성을 향상시키기 위한 귀중한 로드맵을 제공합니다. 연구 결과는 품질 개선, 결함 감소, 생산 최적화를 위한 명확하고 데이터에 기반한 경로를 제시합니다.
CASTMAN은 최신 산업 연구를 적용하여 고객의 가장 까다로운 다이캐스팅 문제를 해결하는 데 전념하고 있습니다. 이 백서에서 논의된 문제가 귀사의 운영 목표와 관련이 있다면, 저희 엔지니어링 팀에 연락하여 이러한 고급 원칙을 귀사의 부품에 어떻게 구현할 수 있는지 논의해 보십시오.
전문가 Q&A: 자주 묻는 질문에 대한 답변
(참고: 답변은 반드시 논문 내 특정 출처를 인용해야 합니다.)
Q1: 이 연구에서 박벽 부품의 품질을 개선하는 데 가장 중요한 요인은 무엇이었습니까?
A1: 연구는 박벽 부품(< 1.2 mm)을 주조하는 데에는 핫챔버 공정이 더 경제적이고 품질이 우수하다고 결론 내렸습니다. 이는 10페이지의 "결론(Conclusion)" 섹션에 명시되어 있습니다.
Q2: 콜드챔버 공정이 핫챔버보다 가스 기공이 더 많이 발생하는 이유는 무엇입니까?
A2: 콜드챔버 공정에서는 슬리브가 최대 2/3까지만 채워지기 때문에 더 많은 공기가 갇히게 되기 때문입니다. 이는 8페이지의 "공기 배출(Air Vents)" 섹션과 Figure 8에서 명확하게 설명하고 있습니다.
Q3: 논문에 따르면 핫챔버 공정에서 선호되는 마그네슘 합금은 무엇입니까?
A3: 10페이지의 본문에 언급된 바와 같이, 핫챔버 공정에서는 여러 이유로 AZ91과 AM 60이 선호되는 합금입니다.
Q4: 핫챔버 공정의 핵심적인 기술적 한계는 무엇입니까?
A4: 핫챔버 공정의 한계는 용탕 온도입니다. 9페이지의 "마그네슘 합금(Magnesium alloy)" 섹션에 따르면, 온도가 650°C를 초과하면 피스톤 링과 슬리브 사이의 누설이 증가하여 공정 운영이 어려워집니다.
Q5: 두 공정에서 요구되는 비압(specific pressure)은 어떻게 비교됩니까?
A5: 5페이지의 Table 2에 따르면, 핫챔버 공정은 160-250 bar의 비압을 사용하는 반면, 콜드챔버 공정은 400-1400 bar의 훨씬 높은 비압을 사용합니다.
Q6: 다이캐스팅 시설을 위한 이 논문의 직접적이고 실용적인 조언은 무엇입니까?
A6: "[Properties of Diecasting Alloys...]" 논문에 근거한 핵심 조언은, 생산하려는 부품의 요구 특성(특히 벽 두께와 기계적 요구사항)에 따라 핫챔버와 콜드챔버 중 적합한 공정을 신중하게 선택해야 한다는 것입니다. 이는 10페이지의 결론에서 강력하게 뒷받침됩니다.
저작권
- 이 자료는 Dr. Ing Norbert Erhard와 Bob Tracy의 논문 "[Properties of Diecasting Alloys and a Comparison of Hot and Cold Chamber Processes for Magnesium Die Casting]"을 분석한 것입니다.
- 논문 출처: FRECH White Paper
- 이 자료는 정보 제공 목적으로만 사용됩니다. 무단 상업적 사용을 금합니다.
- Copyright © 2025 CASTMAN. All rights reserved.