이 기술 브리핑은 Tri Pujadi 외 저자가 2021년 IEOM Society International에서 발표한 학술 논문 "[Preventive Maintenance Modeling on Die Casting Machines with Information Systems]"을 기반으로 합니다. HPDC 전문가를 위해 CASTMAN의 전문가들이 요약 및 분석했습니다.
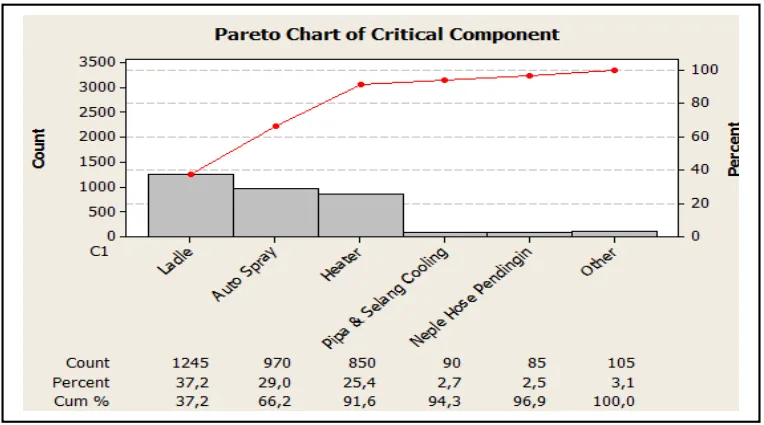
키워드
- 주요 키워드: 다이캐스팅 기계 예방 정비
- 보조 키워드: 가용성, 신뢰성, 다운타임, 고장 분석, MTTF, MTTR, 정보 시스템
핵심 요약
(30초밖에 없는 바쁜 전문가를 위한 핵심 내용 요약)
- 문제점: 빡빡한 생산 일정으로 인해 예방 정비가 제대로 이루어지지 않고, 기계가 갑자기 고장 났을 때만 부품을 교체하여 예측 불가능한 다운타임이 발생합니다.
- 해결 방법: 고장 데이터를 정량적으로 분석하여 핵심 기계(DC-07)와 중요 부품(레이들, 자동 스프레이, 히터)을 식별하고, MTTF(평균 고장 시간) 및 MTTR(평균 수리 시간)을 계산하여 최적의 부품 교체 주기를 도출했습니다.
- 핵심 성과: 제안된 예방 정비 모델을 적용한 결과, 레이들 부품의 신뢰성은 92.44%, 자동 스프레이는 129.25% 향상되었으며, 전체 다운타임은 53.04% 감소했습니다.
- 결론: 경험이 아닌 데이터에 기반한 예방 정비는 기계 가용성과 신뢰성을 크게 높이고, 총 다운타임과 관련 비용을 줄이는 가장 효과적인 방법입니다.
문제점: 이 연구가 HPDC 전문가에게 왜 중요한가?
제조 현장에서 생산 목표를 달성하기 위해 생산 공정의 원활함은 무엇보다 중요합니다. 하지만 많은 다이캐스팅 공장에서는 생산 일정에 쫓겨 기계 유지보수 활동이 뒷전으로 밀리는 경우가 많습니다. 이 연구에서 다룬 자동차 부품 제조사 역시 마찬가지였습니다. 이 회사는 예방 정비보다는 기계가 갑작스럽게 고장 났을 때 수리하는 '사후 정비'에 의존하고 있었습니다. 이러한 접근 방식은 예측 불가능한 생산 중단, 막대한 수리 비용, 납기 지연 등 심각한 문제로 이어집니다. 특히 16대의 다이캐스팅 기계는 핵심 부품 생산에 필수적인 역할을 하므로, 이 기계들의 잦은 고장은 회사 전체의 생산성에 직접적인 타격을 주었습니다. 이 연구는 이러한 고질적인 문제를 해결하기 위해 시작되었습니다.
접근법: 방법론 분석
연구팀은 이 문제를 해결하기 위해 정량적 데이터 분석에 기반한 예방 정비 방법론을 채택했습니다.
- 데이터 수집: 2019년 1월부터 2020년 12월까지의 기계 고장 데이터, 수리 시간, 운영 비용 데이터를 수집했습니다.
- 핵심 기계 및 부품 식별: 수집된 데이터를 바탕으로 파레토 분석을 실시하여 가장 많은 다운타임을 유발하는 '핵심 기계'와 해당 기계의 '핵심 고장 부품'을 식별했습니다.
- 통계적 분석: 식별된 핵심 부품에 대해 MTTF(평균 고장 시간)와 MTTR(평균 수리 시간)을 계산했습니다. 이를 통해 각 부품의 수명 분포를 파악하고 최적의 교체 시점을 예측하는 '수명 교체(Age Replacement)' 모델을 적용했습니다.
- 정보 시스템 설계: 분석 결과를 바탕으로, 데이터 수집, 성능 계산, 고장 정보 알림 등을 자동화하여 예방 정비 활동을 지원하는 정보 시스템을 설계했습니다.
이러한 체계적인 접근법을 통해, 연구팀은 '언제' 부품을 교체해야 하는지에 대한 명확하고 데이터에 기반한 해답을 찾고자 했습니다.
핵심 성과: 주요 발견 및 데이터
분석 결과는 매우 명확했으며, 데이터 기반 예방 정비의 효과를 극적으로 보여주었습니다.
- 핵심 기계 식별: 총 16대의 다이캐스팅 기계 중 'DC-07' 기계가 전체 다운타임의 12.20%를 차지하며 가장 큰 문제를 일으키는 핵심 기계로 확인되었습니다 (Table 1).
- 핵심 부품 식별: DC-07 기계의 고장 원인을 분석한 결과, '레이들(Ladle)', '자동 스프레이(Auto Spray)', '히터(Heater)' 세 가지 부품이 전체 고장의 91.6%를 차지하는 핵심 부품으로 나타났습니다 (Figure 2).
- 최적 교체 주기 도출: 수명 교체 모델 분석 결과, 최소의 다운타임을 보장하는 최적의 예방 정비 교체 주기는 레이들 108시간, 자동 스프레이 506시간, 히터 320시간으로 계산되었습니다 (Table 4).
- 신뢰성 및 가용성 대폭 향상: 제안된 예방 정비 주기를 적용했을 때, 부품 신뢰도는 기존 대비 레이들 92.44%, 자동 스프레이 129.25%, 히터 80.07%까지 극적으로 향상되었습니다 (Table 6).
- 다운타임 및 비용 절감: 이 모델을 통해 연간 총 다운타임을 4,258시간에서 2,258시간으로 53.04% 줄일 수 있었으며, 월간 유지보수 비용은 부품에 따라 24.73%에서 38.90%까지 절감되는 것으로 나타났습니다 (Table 7, Table 8).
HPDC 제품을 위한 실질적인 시사점
이 연구 결과는 실제 다이캐스팅 생산 환경에 다음과 같은 중요한 시사점을 제공합니다.
- 공정 엔지니어: 논문의 "Calculation" 섹션에서 제시된 방법론은 귀사의 고장 데이터를 분석하여 가장 문제가 되는 기계와 부품을 식별하는 데 적용될 수 있습니다. 이를 통해 제한된 유지보수 자원을 가장 효과적인 곳에 집중할 수 있습니다.
- 품질 관리: Figure 2의 파레토 차트에서 볼 수 있듯이, 소수의 핵심 부품이 대부분의 고장을 유발합니다. 이 부품들의 상태를 집중적으로 모니터링하고 예방적으로 교체함으로써 생산 안정성을 높이고 예측 불가능한 품질 문제를 줄일 수 있습니다.
- 설비 관리자: 이 연구는 기존의 경험 기반 또는 사후 정비 방식에서 벗어나 데이터 기반의 예방 정비로 전환해야 하는 명확한 근거를 제시합니다. Table 8에 나타난 비용 절감 효과는 예방 정비 도입을 위한 투자 수익률(ROI)을 입증하는 강력한 자료가 될 수 있습니다.
논문 상세 정보
Preventive Maintenance Modeling on Die Casting Machines with Information Systems
1. 개요:
- 제목: Preventive Maintenance Modeling on Die Casting Machines with Information Systems
- 저자: Tri Pujadi, Bahtiar H. Simamora, Vikas Kumar, Yulia Magdalena, Witarsjah, Yunita Kartika Sari, Satya Windy
- 발행 연도: 2021
- 발행처: Proceedings of the International Conference on Industrial Engineering and Operations Management
- 키워드: Risk, procurement, supply chain, failure mode effect analysis, mitigate risk, scrm
2. 초록:
회사 관찰 결과, 주요 문제는 빡빡한 생산 일정으로 인해 유지보수 활동이 제대로 수행되지 않는다는 점이었습니다. 이는 기계가 갑자기 손상되었을 때만 부품을 교체하는 이유입니다. 본 연구의 목적은 정기적인 유지보수가 필요한 기계 유형과 핵심 부품을 결정하고, 정보 시스템을 통해 적용될 경우 신뢰도가 얼마나 되는지를 파악하는 것입니다. 사례 연구 방법은 예방 정비에 따라 데이터를 처리하는 정량적 방법으로 수행되었습니다. 분석은 엔진과 핵심 부품을 결정한 다음, 평균 고장 시간(MTTF)과 평균 수리 시간(MTTR)을 계산하여 수명 교체, 가용성, 신뢰성 및 다운타임 값을 얻는 방식으로 수행됩니다. 달성된 결과는 레이들, 자동 스프레이 및 히터 부품에 대한 제안된 예방 정비를 구현함으로써 가용성과 신뢰성이 증가하고 총 다운타임이 감소한 것입니다.
3. 서론:
제조 회사는 시기적절한 생산 공정 수행, 원자재 공급 통제, 유통업체에 제품을 제시간에 배포함으로써 성능을 개선하고 고객 서비스를 향상시키기 위해 다양한 노력을 기울였습니다. 생산 공정은 좋은 스케줄링, 자재 통제를 기반으로 하여 고객에게 서비스 향상을 보장했습니다. 이러한 노력은 정보 기술을 사용하여 유통업체의 판매 주문 기록, 자재 재고 관리, 공급업체에 대한 구매 주문 생성, 회사 내 재무제표 생성 등을 지원할 경우 달성될 수 있습니다.
4. 연구 요약:
연구 주제의 배경:
제조 회사에서 생산 공정의 원활함은 목표 달성에 영향을 미칩니다. 좋은 성능을 얻기 위해 기계는 최적의 작동을 할 수 있는 유지보수 시스템을 갖추어야 합니다. 그러나 실제로는 많은 제조 산업이 여전히 생산 공정에 더 집중하고 생산 과정 중 기계 손상을 줄이기 위한 예방 조치에는 덜 주의를 기울입니다. 연구 대상은 자동차 산업에 종사하는 회사로, 빡빡한 생산 일정으로 인해 유지보수 활동의 우선순위가 낮아지고, 기계 고장 시에만 부품을 교체하는 문제가 있었습니다. 이로 인해 다이캐스팅 기계가 자주 고장 나 생산에 차질을 빚고 있었습니다.
이전 연구 현황:
논문은 기존 연구를 직접적으로 나열하기보다는, 연구 대상 회사의 현재 상태를 문제로 정의합니다. 즉, 예방 정비가 체계적으로 구현되지 않고 사후 정비에 의존하는 것이 기존의 방식이었습니다.
연구 목적:
본 연구의 목적은 다음과 같습니다.
1. 정기적인 유지보수가 필요한 기계 유형을 결정합니다.
2. 고장을 유발하는 핵심 부품을 식별합니다.
3. 제안된 예방 정비를 정보 시스템을 통해 적용했을 때 신뢰도가 얼마나 향상되는지 파악합니다.
4. 가장 높은 다운타임을 가진 기계와 부품을 찾아내고, 예방 정비를 통해 신뢰도 증가폭을 확인하며, 관련 정보를 제공하는 정보 시스템을 구축합니다.
핵심 연구:
핵심 연구는 정량적 데이터를 사용하여 다이캐스팅 기계의 최적 예방 정비 모델을 수립하는 것입니다. 이를 위해 특정 기계(DC-07)와 그 핵심 부품(레이들, 자동 스프레이, 히터)의 고장 데이터를 분석하여 MTTF와 MTTR을 계산하고, 이를 바탕으로 최적의 교체 주기, 신뢰도, 가용성, 다운타임 감소 효과를 도출했습니다.
5. 연구 방법론
연구 설계:
이 연구의 방법론은 기술적 분석(descriptive analytic)입니다. 연구는 조달 및 보관을 담당하는 단위에서 수행되었습니다. 연구 순서는 예비 연구, 예방 정비 범위 설정, 데이터 수집 및 분석, 예방 정비 제안, 구현/계산의 순서로 진행되었습니다.
데이터 수집 및 분석 방법:
2019년 1월부터 2020년 12월까지의 기계 손상 및 다이캐스팅 부품 데이터, 수리 및 운영 비용 데이터를 수집했습니다. 수집된 데이터는 수명 교체(age replacement), 신뢰성, 가용성, 다운타임 값을 계산하는 데 사용되었습니다. 기존 문제점은 수명 교체 방법을 사용한 예방 정비로 해결되었으며, 분석 결과는 정보 시스템 설계에 활용되었습니다.
연구 주제 및 범위:
연구 주제는 다이캐스팅 기계의 예방 정비 모델링입니다. 범위는 유지보수 간격과 수리 시간에 대한 문제로 한정되었습니다. 특히 가장 고장 빈도가 높은 DC-07 기계와 그 핵심 부품에 초점을 맞추었습니다.
6. 주요 결과:
주요 결과:
- 핵심 기계: DC-07 기계가 가장 높은 고장 빈도를 가진 핵심 기계로 식별되었습니다.
- 핵심 부품: DC-07 기계에서 레이들, 자동 스프레이, 히터가 핵심 고장 부품으로 파악되었습니다.
- 최적 교체 주기: 레이들은 108시간, 자동 스프레이는 506시간, 히터는 320시간마다 예방적으로 교체하는 것이 최적임이 밝혀졌습니다.
- 신뢰도 향상: 예방 정비 시행 후 신뢰도는 레이들 92.44%, 자동 스프레이 129.25%, 히터 80.07% 증가했습니다.
- 다운타임 감소: 총 다운타임이 53.04% 감소했습니다.
- 비용 절감: 월간 유지보수 비용이 24.73% ~ 38.90% 절감되었습니다.
Figure Name List:
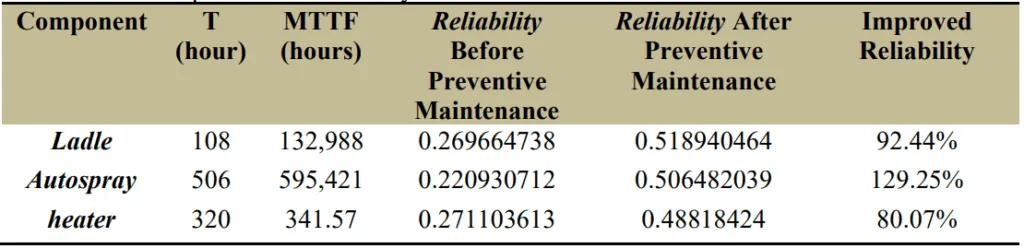


- Figure 1 Methodology Research
- Figure 2. The critical components of damage
- Figure 4 Use Case Diagram
7. 결론:
예방 정비 계산에 기초하여, 다이캐스팅 기계-07이 선택된 핵심 부품인 레이들, 자동 스프레이, 히터를 가진 구속력 있는 기계임이 밝혀졌습니다. 또한, 손상 방지 교체와 같은 예방 정비 조치는 레이들 부품이 108시간, 자동 스프레이 부품이 506시간, 히터 부품이 320시간의 서비스 수명에 도달한 후에 수행되는 것으로 알려졌습니다. 더욱이, 예방 정비를 수행함으로써 레이들 부품의 신뢰도 곡선은 92.44%, 자동 스프레이는 129.25%, 히터 부품은 80.07%의 증가를 보였습니다. 정보 시스템 애플리케이션의 적용은 데이터 수집 및 엔진 및 부품 성능 계산 측면에서 엔진 유지보수 활동을 지원할 수 있습니다. 회사는 DC-07 엔진과 그 부품에 더 많은 주의를 기울여 엔진 성능을 항상 정상 상태로 유지해야 합니다.
8. 참고문헌:
- Ab-samat, H., L. N. Jeikumar, E. I. Basri, N. A. Harun, “Effective Preventive Maintenance Scheduling: A Case Study," Proc. 2012 Int. Conf. Ind. Eng. Oper. Manag. Istanbul, Turkey, pp. 1249–1257, 2012.
- Angius, A., M. Colledani, L. Silipo, A. Yemane, “Impact of Preventive Maintenance on the Service Level of Multi-stage Manufacturing Systems with Degrading Machines,” IFAC-PapersOnLine, vol. 49, no. 12, pp. 568–573, 2016, doi: 10.1016/j.ifacol.2016.07.696. 2016
- Basri, E.I., I. H. A. Razak, H. Ab-Samat, S. Kamaruddin, “Preventive maintenance (PM) planning: A review,” J. Qual. Maint. Eng., vol. 23, no. 2, pp. 114-143, doi: 10.1108/JQME-04-2016-0014. 2017
- Duarte, J.A.C., J. C. T. A. Craveiro, T. P. Trigo, "Optimization of the preventive maintenance plan of a series components system,” Int. J. Press. Vessel. Pip., vol. 83, no. 4, pp. 244-248, doi: 10.1016/j.ijpvp.2006.02.016. 2006
- Hardt, F., M. Kotyrba, E. Volna, R. Jarusek, “Innovative approach to preventive maintenance of production equipment based on a modified tpm methodology for industry 4.0," Appl. Sci., vol. 11, no. 15, 2021, doi: 10.3390/app11156953. 2021
- Purnama, C., “Analyze Machine Maintenance Cost With Corrective Method and Preventive Method To Increase Production Result," Int. J. Bus. Rev. (The Jobs Rev., vol. 2, no. 1, pp. 1–8, 2019, doi: 10.17509/tjr.v2i1.15307. 2019
- Qian, F., K. Dong, “The Open Cybernetics & Systemics Optimizing Preventive Maintenance of Used Equipment for Lease Abstract :," no. Cm, doi: 10.2174/1874110X0171101008 2017
- Zahedi, Z., A. Salim, “Integrating Preventive Maintenance Scheduling As Probability Machine Failure And Batch Production Scheduling," ComTech Comput. Math. Eng. Appl., vol. 7, no. 2, p. 105, doi: 10.21512/comtech.v7i2.2247. 2016
전문가 Q&A: 가장 궁금한 질문에 대한 답변
Q1: 이 연구에서 기계 가용성 향상을 위해 식별된 가장 중요한 단일 요소는 무엇이었나요?
A1: 연구는 데이터 분석을 통해 가장 문제가 되는 기계(DC-07)와 핵심 부품(레이들, 자동 스프레이, 히터)을 식별하고, 이 부품들에 대해 계산된 최적 교체 주기에 따라 예방 정비를 실행하는 것이 가장 중요하다고 결론 내렸습니다. 이는 논문의 "Conclusion" 섹션에 명시되어 있으며 Table 4와 Table 6의 데이터가 이를 뒷받침합니다.
Q2: 이 연구는 기존의 문제 해결 방식과 어떻게 다른가요?
A2: 논문의 "Introduction" 섹션에 따르면, 기존 방식은 '기계가 갑자기 고장 났을 때만' 부품을 교체하는 사후 정비에 의존했습니다. 반면 이 연구는 고장 데이터를 정량적으로 분석하여 최적의 교체 시점을 미리 결정하는 데이터 기반의 '예방 정비' 접근법을 도입했으며, 이를 통해 다운타임을 53% 이상 줄일 수 있음을 입증했습니다.
Q3: 이 연구 결과는 모든 종류의 다이캐스팅 기계에 적용 가능한가요, 아니면 특정 기계에만 해당되나요?
A3: "Methodology" 섹션에 설명된 바와 같이, 이 연구는 특정 자동차 부품 회사의 다이캐스팅 기계, 특히 'DC-07' 기계를 대상으로 수행되었습니다. 따라서 다른 기계나 다른 환경에 적용하기 위해서는 해당 환경의 데이터를 기반으로 한 추가적인 분석이 필요합니다.
Q4: 연구원들은 이 결론에 도달하기 위해 어떤 구체적인 측정 또는 분석 기법을 사용했나요?
A4: 연구원들은 "Research Methodology" 섹션에 설명된 대로, 고장 및 수리 데이터를 수집하여 MTTF(평균 고장 시간)와 MTTR(평균 수리 시간)을 계산하는 정량적 방법을 사용했습니다. 또한, 최적의 교체 주기를 찾기 위해 '수명 교체(age replacement)' 모델을 적용했습니다.
Q5: 논문에 따르면, 이 연구의 주요 한계점이나 향후 연구 분야는 무엇인가요?
A5: 논문의 "Conclusion" 섹션에서는 명시적인 한계점을 언급하기보다는, "회사는 DC-07 엔진과 그 부품에 더 많은 주의를 기울여 엔진 성능을 항상 정상 상태로 유지해야 한다"고 제언합니다. 이는 제안된 모델의 지속적인 적용과 모니터링이 중요하며, 이를 다른 기계로 확장하는 것이 향후 과제가 될 수 있음을 시사합니다.
Q6: 이 논문이 다이캐스팅 공장에 주는 직접적이고 실용적인 교훈은 무엇인가요?
A6: 핵심 교훈은 레이들(108시간), 자동 스프레이(506시간), 히터(320시간)와 같은 특정 부품의 교체 주기를 데이터에 기반하여 최적화함으로써, 기계 신뢰도를 100% 가까이 향상시키고 총 다운타임을 절반 이상 줄일 수 있다는 것입니다. 이는 논문 "[Preventive Maintenance Modeling on Die Casting Machines with Information Systems]"의 전반적인 결과가 강력하게 뒷받침하는 결론입니다.
결론 및 다음 단계
이 연구는 HPDC 공정에서 기계 가용성을 높이고 다운타임을 줄이기 위한 귀중한 로드맵을 제공합니다. 연구 결과는 품질을 개선하고, 결함을 줄이며, 생산을 최적화하기 위한 명확하고 데이터에 기반한 경로를 제시합니다.
CASTMAN은 고객의 가장 까다로운 다이캐스팅 문제를 해결하기 위해 최신 산업 연구를 적용하는 데 전념하고 있습니다. 이 백서에서 논의된 문제가 귀사의 운영 목표와 관련이 있다면, 저희 엔지니어링 팀에 연락하여 이러한 고급 원칙을 귀사의 부품에 적용하는 데 어떻게 도움을 드릴 수 있는지 논의해 보십시오.
저작권
- 이 자료는 "[Tri Pujadi et al.]"의 논문입니다. "[Preventive Maintenance Modeling on Die Casting Machines with Information Systems]"을 기반으로 합니다.
- 논문 출처: [https://www.researchgate.net/publication/356133105PreventiveMaintenanceModelingonDieCastingMachineswithInformationSystems]
이 자료는 정보 제공 목적으로만 사용됩니다. 무단 상업적 사용을 금합니다.
Copyright © 2025 CASTMAN. All rights reserved.