이 기술 브리핑은 Karthik S Murugesan, M.S.가 오하이오 주립대학교(2008)에서 발표한 학술 논문 "컴퓨터 모델링 및 차원 해석을 이용한 다이캐스팅에서의 파팅 평면 분리 및 타이바 하중 예측"을 기반으로 합니다. HPDC 전문가들을 위해 CASTMAN의 전문가들이 요약하고 분석했습니다.
![Figure 1.1: Schematic of an open-close die [5]](https://castman.co.kr/wp-content/uploads/image-2491.webp)
키워드
- 주요 키워드: 파팅 평면 분리 예측
- 보조 키워드: 타이바 하중 불균형, HPDC 컴퓨터 모델링, 다이캐스팅 차원 해석, 다이캐스팅 유한 요소 해석(FEA), 금형 변형, 금형 설계 최적화, 플래튼 강성
핵심 요약
- 과제: 고압 다이캐스팅에서 파팅 평면 분리 및 타이바 하중 불균형과 같은 금형 변형을 예측하고 제어하는 것은 플래시, 치수 부정확성, 조기 금형 파손과 같은 결함으로 이어지는 지속적인 과제입니다.
- 방법: 본 연구는 초기 설계를 위해 시간이 많이 소요되는 전체 유한 요소 해석(FEA)을 넘어, 간소화된 폐쇄형 "멱법칙 모델"을 개발했습니다. 이 모델들은 가장 중요한 구조적 변수를 식별하기 위해 차원 해석과 결합된 컴퓨터 FEA 실험을 사용하여 만들어졌습니다.
- 핵심 돌파구: 본 연구는 파팅 평면 분리와 타이바 하중 불균형 모두에 대한 예측 모델을 만들었습니다. 이 모델들은 금형 설계(예: 금형 크기, 두께, 서포트 필러 패턴) 및 기계 매개변수(예: 플래튼 두께)의 변화가 금형 성능에 어떻게 영향을 미칠지 정확하게 예측합니다.
- 결론: 이 연구는 다이캐스팅 전문가에게 초기 단계에서 구조적 금형 설계를 최적화하고, 첫 번째 샷 이전에 결함을 예방하며, 더 높은 부품 품질과 금형 수명을 보장할 수 있는 강력하고 빠르며 비용 효율적인 도구를 제공합니다.
과제: 이 연구가 HPDC 전문가에게 중요한 이유
수십 년 동안 다이캐스팅 엔지니어들은 금형과 기계 내에서 발생하는 힘의 복잡한 상호 작용과 씨름해 왔습니다. 금형을 닫는 형체력에서부터 캐비티를 채우는 사출 압력에 이르기까지 관련된 엄청난 압력은 금형의 탄성 변형을 유발합니다. 이러한 변형이 파팅 라인을 따라 발생하면 금형의 두 반쪽이 분리되어 용융된 금속이 빠져나가는 "플래시" 현상이 발생합니다. 플래시는 2차 제거 작업으로 인한 비용 증가, 불량률 증가, 잠재적인 금형 손상으로 이어집니다.
이와 관련하여 똑같이 중요한 문제는 타이바 하중 불균형입니다. 이상적으로는 형체력이 기계의 네 개의 타이바 전체에 고르게 분산되어야 합니다. 그러나 중심에서 벗어난 금형 배치나 캐비티 내의 불균일한 압력 분포와 같은 요인으로 인해 불균형한 하중이 발생할 수 있습니다. 이는 금형이 고르지 않게 닫히게 하여 플래시를 악화시키고, 심한 경우 비용이 많이 들고 위험한 사고인 조기 타이바 파손으로 이어질 수 있습니다. 이러한 현상을 예측하는 것은 일반적으로 복잡하고 시간이 많이 걸리는 FEA를 필요로 하며, 이는 초기 금형 설계의 빠른 반복 과정에서는 종종 실현 불가능합니다.
접근법: 방법론 분석
이 문제를 해결하기 위해 연구원은 보다 효율적인 예측 도구를 개발했습니다. 이 연구의 방법론은 현대 시뮬레이션의 힘과 공학 물리학의 기본 원리를 결합했습니다.
접근법의 핵심은 유한 요소법(FEM)에 기반한 일련의 컴퓨터 실험을 사용하는 것이었습니다. 금형, 인서트, 기계 플래튼, 타이바 및 토글 메커니즘을 포함하는 포괄적인 3D FEA 모델이 구축되었습니다. 실험 계획법(DOE) 접근 방식을 사용하여 금형 치수, 플래튼 두께 및 이젝터 서포트 필러 패턴과 같은 주요 구조 설계 매개변수를 체계적으로 변경하면서 수많은 시뮬레이션을 실행했습니다.
핵심 혁신은 차원 해석, 특히 버킹엄 파이 정리의 적용이었습니다. 이 고전적인 공학 방법은 복잡한 변수 집합을 물리적 거동을 지배하는 더 적은 수의 무차원 매개변수로 줄입니다. 차원 해석의 관점에서 FEA 결과를 분석함으로써 연구원은 설계 매개변수와 파팅 평면 분리 및 타이바 하중 결과 간의 관계를 설명하는 강력한 폐쇄형 방정식인 "멱법칙 모델"을 개발했습니다.
돌파구: 주요 발견 및 데이터
이 연구는 업계에서 직접 적용할 수 있는 몇 가지 강력한 결론과 예측 도구를 산출했습니다.
- 발견 1: 이젝터 측 분리는 서포트 구조에 의해 좌우됨. 연구의 멱법칙 모델은 이젝터 측의 파팅 평면 분리가 서포트 필러 지지대 사이의 비지지 스팬과 금형 두께의 비율에 가장 민감하다는 것을 밝혔습니다. 서포트 필러의 수와 배치가 중요한 역할을 하는 반면, 플래튼 두께는 1차적인 영향만 미칩니다.
- 발견 2: 고정 측 분리는 금형 크기와 플래튼 강성에 의해 주도됨. 고정 측에서 가장 중요한 요소는 플래튼 영역에 대한 금형의 면적입니다. 작은 금형은 플래튼이 금형 주위를 "감싸" 더 나은 지지를 제공하기 때문에 분리가 적게 발생합니다. 다음으로 중요한 요소는 고정 측 플래튼 두께와 타이바 사이의 거리입니다.
- 발견 3: 더 정확한 타이바 하중 모델. 기존 방법과 달리 플래튼 위 금형과 캐비티 압력 중심의 특정 위치를 모두 고려하는 새로운 멱법칙 모델이 개발되었습니다. 이는 하중 분포에 대한 훨씬 더 정확한 추정치를 제공하며, 이는 금형의 균형을 맞추고 플래시를 방지하는 데 중요합니다.
귀사의 HPDC 제품에 대한 실질적 시사점
논문의 결과와 결론에 엄격하게 근거하여, 이러한 발견은 제조 결과를 개선하는 데 직접적인 적용점을 가집니다.
- 공정 엔지니어: "5장"의 연구 결과는 타이바 하중 불균형이 주로 플래튼 위 금형의 위치에 의해 주도됨을 시사합니다. 개발된 멱법칙 모델을 사용하면 중심에서 벗어난 설정에 대한 이 불균형을 예측하고 하중 균형을 맞추기 위한 사전 조정을 수행하여 잠재적으로 필요한 최소 형체력을 줄이고 플래시를 방지할 수 있습니다.
- 품질 관리: 비지지 스팬과 파팅 평면 분리 사이의 상관관계는 플래시의 근본 원인을 진단하기 위한 새로운 프레임워크를 제공합니다. "4장"의 모델을 사용하여 금형의 구조 설계가 실행 중인 기계에 적합한지 판단하여 보다 효과적인 문제 해결로 이어질 수 있습니다.
- 금형 설계: 파팅 평면 분리에 대한 이 연구는 서포트 필러 패턴에 관한 설계 선택이 이젝터 측 안정성에 측정 가능한 영향을 미친다는 것을 의미합니다. 얇고 유연한 금형이 크고 두꺼운 플래튼 위에 놓였을 때 고정 측에서 더 나은 성능을 보인다는 결론은 설계 단계에서 금형과 기계의 조화를 최적화하기 위한 명확하고 데이터 기반의 원칙을 제공합니다.
논문 상세 정보
컴퓨터 모델링 및 차원 해석을 이용한 다이캐스팅에서의 파팅 평면 분리 및 타이바 하중 예측
1. 개요:
- 제목: 컴퓨터 모델링 및 차원 해석을 이용한 다이캐스팅에서의 파팅 평면 분리 및 타이바 하중 예측
- 저자: Karthik S Murugesan M.S.
- 발행 연도: 2008
- 발행 기관: 오하이오 주립대학교 (박사 학위 논문)
- 키워드: 파팅 평면 분리 예측, 타이바 하중 불균형, HPDC 컴퓨터 모델링, 다이캐스팅 차원 해석, 다이캐스팅 유한 요소 해석(FEA), 금형 변형, 금형 설계 최적화, 플래튼 강성.
2. 초록:
다이캐스팅 금형과 기계는 형체력, 캐비티 압력 하중, 열 하중을 받는 고성능 제품으로, 이로 인해 변형이 발생합니다. 이러한 하중을 견디는 금형의 능력은 구조 설계에 달려 있습니다. 일반적인 문제는 타이바 하중 불균형으로, 금형 및 캐비티 위치로 인해 형체력이 네 개의 타이바에 고르지 않게 분산되어 플래시 및 조기 타이바 파손과 같은 문제를 유발합니다. FEA와 같은 수치 해석 방법은 설계 단계에서 변형을 예측하는 데 효과적이지만 시간이 많이 걸릴 수 있습니다. 본 연구는 컴퓨터(FEA) 실험을 사용하여 주요 구조 설계 변수가 기계적 성능에 미치는 영향을 조사했습니다. 차원 해석을 사용하여 파생된 멱법칙 모델은 최대 파팅 평면 분리 및 타이바 하중을 예측하기 위해 개발되었습니다. 이 모델들은 시스템이 설계 변수에 얼마나 민감한지 설명하고 금형 구조를 개선하며 필요한 타이바 조정을 결정하는 데 사용될 수 있습니다.
3. 서론:
다이캐스팅은 용융된 금속을 고압으로 강철 금형에 사출하여 복잡한 형상의 부품을 생산하는 네트 셰이프(net shape) 제조 공정입니다. 치수 부정확성에 기여하는 주요 요인 중 하나는 열-기계적 하중으로 인한 금형 캐비티의 탄성 변형입니다. 이는 플래시와 같은 결함으로 이어져 사이클 타임과 비용을 증가시킬 수 있습니다. 또 다른 중요한 문제는 중심에서 벗어난 금형 또는 캐비티 배치로 인한 기계 타이바의 불균형 하중으로, 이는 불균일한 금형 닫힘 및 부품 고장을 유발할 수 있습니다. 금형 제조 비용이 비싸고 리드 타임이 길기 때문에 설계 단계에서 이러한 변형을 예측하고 제어하는 것이 중요합니다. 수치 모델링이 변형을 예측하는 가장 효율적인 방법이지만, 초기 설계 반복에는 너무 느릴 수 있습니다. 본 연구는 다이캐스팅 금형의 구조 설계를 위한 기성 도구 및 지침을 개발하는 것을 목표로 합니다.
4. 연구 요약:
연구 주제 배경:
다이캐스팅 금형 및 기계의 구조적 무결성은 치수적으로 정확한 부품을 생산하는 데 중요합니다. 하중 하에서의 금형 변형은 플래시로 이어지며, 불균형한 타이바 하중은 기계 안정성과 금형 닫힘을 저해합니다.
이전 연구 현황:
이전 연구에서는 FEA가 금형 변형을 예측하는 유효한 도구임을 입증했습니다. 그러나 이러한 연구들은 종종 이젝터 측 설계 변수(예: 서포트 필러)가 파팅 평면 분리에 미치는 영향을 완전히 탐구하지 않았습니다. 또한, Herman의 방법과 같이 타이바 하중을 추정하는 기존 방법들은 종종 완벽하게 강체라는 지나치게 단순한 가정에 의존하여 부정확한 예측을 초래했습니다.
연구 목적:
주요 목적은 다양한 구조 설계 변수가 금형 변형에 미치는 영향을 연구하고 금형 설계를 돕는 도구를 개발하는 것이었습니다. 여기에는 최대 파팅 평면 분리 및 타이바 하중을 예측하기 위한 폐쇄형 표현식(멱법칙 모델)을 만들어 초기 설계 단계에서 빠르고 정확한 추정을 가능하게 하는 것이 포함되었습니다.
핵심 연구:
본 연구는 유한 요소 해석(FEA)을 이용한 실험 계획법(DOE) 접근 방식을 사용하여 다양한 설계 매개변수가 금형 성능에 미치는 영향을 시뮬레이션했습니다. 그 결과는 차원 해석(파이 정리)과 함께 사용하여 주요 기하학적 및 물리적 변수의 함수로서 파팅 평면 분리 및 타이바 하중을 예측하는 비선형 멱법칙 모델을 개발하는 데 사용되었습니다.
5. 연구 방법론
연구 설계:
본 연구는 58회 실행 중앙 합성 반응 표면 설계를 이용한 컴퓨터 실험을 중심으로 설계되었습니다. 연구된 요인에는 플래튼 두께, 금형 치수, 금형 두께 비율, 필러 직경/패턴이 포함되었습니다.
데이터 수집 및 분석 방법:
데이터는 각 설계 지점에 대해 정적 유한 요소 해석(FEA)을 사용하여 생성되었습니다. 모델 출력(파팅 평면 분리, 타이바 하중)은 차원 해석 및 비선형 회귀 분석을 사용하여 멱법칙 모델에 맞게 분석되었습니다. 모델의 타당성은 추가 FEA 시뮬레이션 및 250톤 다이캐스팅 기계의 실험적 측정을 통해 검증되었습니다.
연구 주제 및 범위:
본 연구는 두 가지 주요 주제에 초점을 맞췄습니다: 1) 금형의 고정 측 및 이젝터 측에서 최대 파팅 평면 분리 예측, 2) 네 개의 기계 타이바에 대한 개별 하중 예측. 범위는 단일 캐비티, 개폐형 금형으로 제한되었으며 열 하중은 포함하지 않고 기계적 하중 하에서의 구조적 거동에만 초점을 맞췄습니다.
6. 주요 결과:
주요 결과:
본 연구는 최대 파팅 평면 분리 및 타이바 하중을 예측하기 위한 비선형 멱법칙 모델을 성공적으로 개발했습니다. 파팅 평면 분리의 경우, 이젝터 측 분리는 필러 사이의 비지지 스팬과 금형 두께에 가장 민감한 반면, 고정 측 분리는 전체 금형 크기와 플래튼 강성에 가장 민감하다는 것이 밝혀졌습니다. 타이바 하중 예측 모델은 플래튼 위 금형 위치가 하중 분포에 영향을 미치는 주요 요인임을 보여주었는데, 이는 더 간단한 산업 방법에서는 무시되는 요인입니다. 다양한 기계 플래튼의 강성을 특성화하는 방법론도 개발되어 모델을 다양한 기계에 적용할 수 있게 되었습니다.
그림 이름 목록:
![Figure 1.2: Schematic of a Hot Chamber Die Casting Machine [66]](https://castman.co.kr/wp-content/uploads/image-2492.webp)
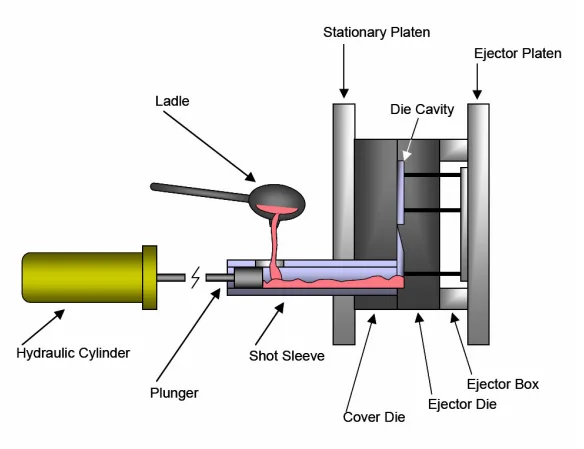
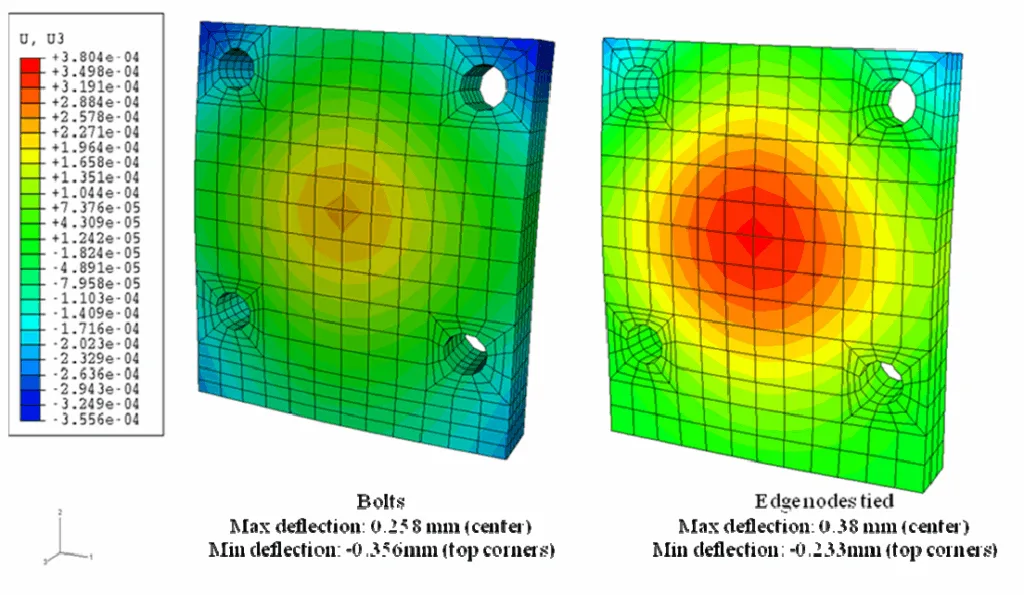
- 그림 1.1: 개폐형 금형의 개략도
- 그림 1.2: 핫챔버 다이캐스팅 기계의 개략도
- 그림 1.3: 콜드챔버 다이캐스팅 기계의 개략도
- 그림 1.4: 고정 및 이젝터 금형의 자유물체도
- 그림 1.5: 다이캐스팅 기계 및 금형의 자유물체도
- 그림 2.1: 토글 스프링 플래튼 모델의 개략도
- 그림 2.2:에서 고려된 모델의 개략도
- 그림 3.1: 연구에 사용된 부품의 형상
- 그림 3.2: 유한 요소 모델의 개략도
- 그림 4.1: 연구에 사용된 이젝터 금형의 측면도
- 그림 4.2: 연구에 사용된 필러 패턴의 개략도
- 그림 5.1: 고정 플래튼 내부에서 본 좌표계 및 타이바 라벨
- 그림 5.5: 회귀 모델의 예측 대 타이바 하중 측정값
- 및 논문의 "그림 목록"에 나열된 기타 모든 그림.
7. 결론:
본 연구는 다이캐스팅에서 파팅 평면 분리 및 타이바 하중을 예측하기 위한 경험적 멱법칙 모델을 성공적으로 개발하고 검증했습니다. 차원 해석과 FEA에서 파생된 이 모델들은 구조적 변수가 금형 성능에 어떻게 기여하는지에 대한 깊은 이해를 제공합니다. 주요 결론은 다음과 같습니다: 이젝터 측 분리는 서포트 필러 배열과 금형 두께에 가장 민감합니다; 고정 측 분리는 금형 크기와 플래튼 강성에 가장 큰 영향을 받습니다; 그리고 금형 위치는 타이바 하중 불균형의 주요 요인입니다. 이 연구는 또한 기계 강성을 특성화하는 방법을 제공하여 모델을 적용할 수 있게 만듭니다. 이러한 도구는 설계자가 설계 프로세스 초기에 구조적 성능을 최적화할 수 있도록 지원합니다.
8. 참고 문헌:
- Chayapathi, A., 1999, "Study of the Effect of Structural Variables of Die and Die Casting Machine on Die Deflections," Master’s Thesis, The Ohio State University.
- Herman, E.A., 1992, "Designing die casting dies," North American Die Casting Association, Rosemont, IL, USA.
- Arrambide, E., Ragab, A., Kabiri-Bamoradian, K., 2005, "Modeling Influence of the Die Casting Machine Components on Contact Load between Dies and Platens," NADCA Transactions.
- Vinarcik, E. J., 2003, "High Integrity Die Casting Process," John Wiley & Sons Publications, New York
- 172-177페이지에 나열된 논문의 기타 모든 참고 문헌.
전문가 Q&A: 자주 묻는 질문에 대한 답변
Q1: 이 연구에서 파팅 평면 분리를 개선하기 위해 확인된 가장 중요한 단일 요소는 무엇이었습니까?
A1: 이 연구는 이젝터 측에서 가장 중요한 요소는 서포트 필러 지지대 사이의 비지지 스팬과 금형 두께의 비율이라고 결론지었습니다. 고정 측의 경우 가장 큰 기여 요인은 플래튼 영역에 대한 금형의 길이와 너비입니다. (출처: "컴퓨터 모델링 및 차원 해석을 이용한 다이캐스팅에서의 파팅 평면 분리 및 타이바 하중 예측", 섹션 6.1 파팅 평면 분리 예측을 위한 멱법칙의 결론).
Q2: 이 연구는 타이바 하중 불균형을 해결하기 위한 전통적인 방법과 어떻게 비교됩니까?
A2: 논문의 서론
및 문제 제기
섹션에서는 Herman의 방법과 같은 전통적인 방법들이 금형과 기계를 완벽한 강체로 가정하고 플래튼 위 금형 위치의 영향을 완전히 무시한다고 지적합니다. 이 연구는 금형과 기계의 강성을 고려하고 특히 금형 및 캐비티 위치를 포함하는 더 진보된 멱법칙 모델을 도입하여 더 정확한 예측을 가능하게 합니다. (출처: "컴퓨터 모델링 및 차원 해석을 이용한 다이캐스팅에서의 파팅 평면 분리 및 타이바 하중 예측", 섹션 1.5 문제 제기).
Q3: 이 발견은 모든 종류의 합금에 적용됩니까, 아니면 특정 합금에만 적용됩니까?
A3: 이 연구는 주조 합금의 야금학이 아닌 금형과 기계의 구조 역학에 초점을 맞추고 있습니다. 연구 방법론
섹션에 설명된 시뮬레이션은 금형 및 기계 부품이 ST4140 강철로 만들어졌다고 가정하고 수행되었습니다. 특정 모델 계수는 이를 기반으로 하지만, 차원 해석 접근 방식 자체는 주조 합금에 관계없이 구조적 거동을 이해하는 데 일반적으로 적용할 수 있습니다. (출처: "컴퓨터 모델링 및 차원 해석을 이용한 다이캐스팅에서의 파팅 평면 분리 및 타이바 하중 예측", 섹션 3.2.3 재료 특성, 표 3.2).
Q4: 연구자들이 이 결론에 도달하기 위해 사용한 구체적인 측정 또는 시뮬레이션 기술은 무엇이었습니까?
A4: 연구자들은 컴퓨터 실험을 수행하기 위한 유한 요소 해석(FEA), 시뮬레이션을 구조화하기 위한 실험 계획법(DOE) 프레임워크, 그리고 최종 멱법칙 모델을 개발하기 위한 버킹엄 파이 정리에 기반한 차원 해석의 조합을 활용했습니다. (출처: "컴퓨터 모델링 및 차원 해석을 이용한 다이캐스팅에서의 파팅 평면 분리 및 타이바 하중 예측", 섹션 4.3 차원 해석 및 경험적 상관관계).
Q5: 논문에 따르면, 주요 한계점이나 향후 연구 분야는 무엇입니까?
A5: 저자들은 향후 연구
섹션에서 현재 모델이 단일 캐비티, 개폐형 금형에 특정되어 있다고 말합니다. 그들은 향후 연구가 다중 캐비티 금형 및 비개폐형 금형(슬라이드 잠금 메커니즘 포함)으로 모델을 확장하고 플런저의 동적 충격 하중을 통합하는 데 초점을 맞춰야 한다고 제안합니다. (출처: "컴퓨터 모델링 및 차원 해석을 이용한 다이캐스팅에서의 파팅 평면 분리 및 타이바 하중 예측", 섹션 6.4 향후 연구).
Q6: 이 논문이 다이캐스팅 시설에 주는 직접적이고 실용적인 교훈은 무엇입니까?
A6: 핵심 교훈은 제시된 멱법칙 모델을 사용하여 시설이 주요 설계 매개변수(금형 크기, 서포트 필러 레이아웃, 플래튼 선택 등)가 파팅 평면 분리 및 타이바 하중에 미치는 영향을 빠르고 정확하게 예측할 수 있다는 것입니다. 이를 통해 강철을 가공하기 전에 금형 및 기계 설정을 최적화하여 결함을 줄이고 부품 품질을 개선하며 공구 수명을 연장할 수 있습니다. 이는 "컴퓨터 모델링 및 차원 해석을 이용한 다이캐스팅에서의 파팅 평면 분리 및 타이바 하중 예측" 논문의 전반적인 결과에 의해 강력하게 뒷받침되는 결론입니다.
결론 및 다음 단계
이 연구는 HPDC 운영에서 구조적 무결성을 향상시키기 위한 귀중한 로드맵을 제공합니다. 시행착오와 초기 설계를 위한 시간 소모적인 FEA의 한계를 넘어, 이 연구 결과는 품질을 개선하고 플래시와 같은 결함을 줄이며 생산을 최적화하기 위한 명확하고 데이터 기반의 경로를 제공합니다.
CASTMAN에서는 고객의 가장 어려운 다이캐스팅 문제를 해결하기 위해 최신 산업 연구를 적용하는 데 전념하고 있습니다. 이 논문에서 논의된 문제가 귀사의 운영 목표와 관련이 있다면, 저희 엔지니어링 팀에 연락하여 이러한 고급 원칙을 귀사의 부품에 구현하는 방법을 논의하십시오.
저작권
- 이 자료는 "Karthik S Murugesan"의 논문 "컴퓨터 모델링 및 차원 해석을 이용한 다이캐스팅에서의 파팅 평면 분리 및 타이바 하중 예측"을 기반으로 합니다.
- 논문 출처: https://etd.ohiolink.edu/acprod/odb_etd/ws/send_pdf/Murugesan%20Karthik%20S.pdf?acc_num=osu1218479383
이 자료는 정보 제공 목적으로만 사용됩니다. 무단 상업적 사용은 금지됩니다.
Copyright © 2025 CASTMAN. All rights reserved.