이 기술 브리핑은 Ján Hašul과 Janette Brezinová가 저술하여 "INTERNATIONAL SCIENTIFIC JOURNAL 'MACHINES. TECHNOLOGIES. MATERIALS'" (2022)에 발표한 학술 논문 "Possibilities of reducing the degradation of molds for high-pressure of Al alloys"를 기반으로 합니다. HPDC 전문가를 위해 CASTMAN의 전문가들이 요약하고 분석했습니다.
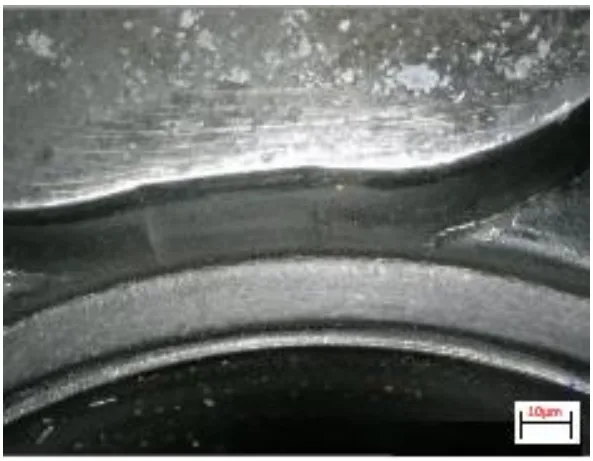
키워드
- 주요 키워드: HPDC 금형용 PVD 코팅
- 보조 키워드: 알루미늄 다이캐스팅, 금형 수명 연장, 열 피로 균열, nACRo³ 코팅, AlXN³ 코팅, 금형 표면 처리, Uddeholm Dievar
핵심 요약
- 과제: 고압 알루미늄 다이캐스팅에 사용되는 금형은 지속적으로 심각한 열적 및 기계적 응력에 노출되어 열 피로, 균열, 침식과 같은 열화 메커니즘을 유발하며, 이는 비용이 많이 드는 생산 중단 및 금형 교체로 이어집니다.
- 방법: 연구원들은 H13 공구강으로 제작된 금형 인서트의 일반적인 파손 모드를 분석했습니다. 그런 다음, 금형 내구성 향상 가능성을 평가하기 위해 기존의 AlXN³와 나노구조의 nACRo³라는 두 가지 다른 PVD 코팅을 적용하고 테스트했습니다.
- 핵심 돌파구: 나노구조 PVD 코팅인 nACRo³는 뛰어난 성능을 보여주었으며, 표면 미세경도를 최대 25%(810 HV)까지 크게 증가시키고 우수한 접착력을 보였습니다. 이는 용융 알루미늄과 주조 사이클의 응력에 대한 견고한 보호 장벽을 생성합니다.
- 결론: 이 연구는 고급 PVD 코팅, 특히 nACRo³와 같은 나노구조 코팅을 적용하는 것이 열화를 방지하고 HPDC 금형의 작동 수명을 연장하며 전반적인 제조 효율성을 개선하는 매우 효과적이고 데이터 기반의 전략임을 확인시켜 줍니다.
과제: 이 연구가 HPDC 전문가에게 중요한 이유
고압 다이캐스팅(HPDC)의 까다로운 세계에서 금형의 작동 수명은 중요한 경제적 요인입니다. 금형은 높은 압력(최대 100 MPa), 고온(약 700°C), 급격한 온도 변화의 혹독한 사이클을 견뎌야 합니다. 이러한 조건은 필연적으로 부식, 솔더링, 침식성 마모, 그리고 가장 두드러지게는 열 피로와 같은 주요 파손 메커니즘으로 이어져 다이의 수명을 제한합니다.
다이 표면의 지속적인 가열 및 냉각으로 인해 발생하는 열 피로는 상호 연결된 균열 네트워크를 형성합니다. 이러한 균열은 성장하여 재료 손실, 주조 부품의 치수 부정확성을 유발하고 결국 치명적인 금형 파손으로 이어질 수 있습니다. 수십 년 동안 엔지니어들은 이 문제와 씨름해 왔으며, 이러한 복잡한 공구를 교체하거나 수리하는 것은 생산 비용의 상당 부분을 차지합니다. 이 연구는 금형을 처음부터 보호하도록 설계된 표면 처리 솔루션을 조사함으로써 이 과제를 직접적으로 해결합니다.
접근법: 방법론 분석
해결책을 찾기 위해 연구원들은 2단계 접근법을 취했습니다. 첫째, 그들은 파손의 근본 원인을 이해하기 위해 Uddeholm Dievar(일반적인 H13 유형 열간 공구강)로 만들어진 마모된 금형 인서트를 분석했습니다. 광학 현미경, 주사 전자 현미경(SEM), 에너지 분산형 X선 분광법(EDX)을 사용하여 금형의 날카로운 모서리에 형성된 균열을 조사했습니다.
둘째, 예방적 해결책을 테스트했습니다. 연구팀은 Uddeholm Dievar 모재에 두 가지 다른 듀플렉스 PVD(물리적 기상 증착) 코팅을 적용했습니다.
- AlXN³: 기존의 나노 다층 코팅.
- nACRo³: 비정질 Si₃N₄ 매트릭스에 AlCrN 나노결정립으로 구성된 차세대 나노복합 코팅으로, 고온 내마모성을 위해 설계되었습니다.
그런 다음 이 코팅된 샘플들은 실제 현장에서의 실행 가능성을 측정하기 위해 엄격한 테스트를 거쳤으며, 여기에는 접착력을 위한 로크웰 C 압입 테스트와 표면 경도 향상을 정량화하기 위한 비커스 미세경도 테스트가 포함되었습니다.
돌파구: 주요 발견 및 데이터
이 연구는 PVD 코팅의 효과를 보여주는 명확하고 정량적인 결과를 산출했습니다.
- 발견 1: 균열 메커니즘 확인: 마모된 금형 분석 결과, 쐐기 모양의 분기된 균열이 주요 파손 모드임이 확인되었습니다. 이 균열은 주기적인 응력으로 인해 날카로운 모서리에서 시작되었으며, 주조 공정에서 나온 산화물과 이형제로 채워져 각 사이클마다 균열을 전파시키는 쐐기 역할을 했습니다. 이는 논문의 그림 5와 그림 6에 자세히 설명되어 있습니다.
- 발견 2: 우수한 코팅 접착력: AlXN³와 nACRo³ 코팅 모두 강철 기판에 "우수한 접착력"을 보였습니다. 로크웰 접착력 테스트(그림 7에 표시된 심각한 압입 테스트)에서 코팅은 HF 1-2 등급을 달성했으며, 이는 심각한 박리나 탈락 없이 미미하고 고립된 방사형 균열만 있음을 나타냅니다. 이는 코팅이 벗겨지지 않고 상당한 기계적 응력을 견딜 수 있음을 증명합니다.
- 발견 3: 표면 경도의 상당한 증가: PVD 코팅은 마모와 침식에 저항하는 핵심 요소인 표면 경도를 크게 향상시켰습니다. 모재와 비교할 때 AlXN³ 코팅은 경도를 최대 720 HV까지 증가시켰습니다. 고급 nACRo³ 코팅은 최대 810 HV에 도달하여 훨씬 더 나은 성능을 보였으며, 이는 약 18-25% 증가한 수치입니다. 결과는 그림 9의 경도 프로파일 그래프에 명확하게 시각화되어 있습니다.
귀사의 HPDC 제품에 대한 실질적 시사점
논문의 결과에 엄격히 근거하여, 이러한 발견은 제조 운영에 직접적이고 실질적인 영향을 미칩니다.
- 공정 엔지니어: 이 연구는 nACRo³와 같은 나노구조 PVD 코팅을 신규 또는 수리된 금형에 선제적으로 적용하면 더 내구성 있고 탄력적인 표면을 만들 수 있음을 시사합니다. 이는 열 피로 균열의 형성을 직접적으로 방지하여 필요한 유지보수 간격을 연장하고 예상치 못한 가동 중지 시간을 줄일 수 있습니다.
- 품질 관리: 그림 7과 그림 9에서 볼 수 있듯이 nACRo³ 코팅의 우수한 경도와 접착력은 안정적이고 내마모성이 있는 금형 표면을 제공합니다. 이는 금형 캐비티의 정밀한 형상을 더 오랜 기간 동안 유지하는 데 도움이 되어 연장된 금형 수명 전반에 걸쳐 보다 일관된 부품 품질과 치수 정확성을 보장합니다.
- 다이 설계: 이 연구는 중요한 설계 원칙을 강화합니다. 코팅은 강력한 보호층이지만, 연구 결과 파손은 "날카로운 전이 영역"(그림 5)에서 시작된다는 점을 확인했습니다. 이는 견고한 PVD 코팅과 날카로운 내부 모서리를 최소화하는 다이 설계를 결합하는 것이 금형 수명을 극대화하는 가장 효과적인 전략임을 시사합니다.
논문 세부 정보
Possibilities of reducing the degradation of molds for high-pressure of Al alloys
1. 개요:
- 제목: 고압 알루미늄 합금용 금형의 열화 감소 가능성
- 저자: Ján Hašul, Janette Brezinová
- 발행 연도: 2022
- 저널/학회: INTERNATIONAL SCIENTIFIC JOURNAL "MACHINES. TECHNOLOGIES. MATERIALS"
- 키워드: 알루미늄, 다이캐스팅, 열화, 코팅, 접착, 균열
2. 초록:
본 논문은 고압 알루미늄 및 그 합금 주조 기술에 사용되는 금형의 열화에 초점을 맞춥니다. 알루미늄 제품의 고압 주조 방법은 자동차 및 다양한 기계 부품 생산에서 정밀도와 생산성 요구 사항을 동시에 충족시키는 널리 사용되는 생산 방법 중 하나입니다. 고압 주조 공정에서 금형은 다양한 열적 및 기계적 하중에 노출되어 금형 및 그 형상 부품이 열화됩니다. 본 논문은 고압 알루미늄 및 그 합금 주조용 금형의 형상 부품 수명을 늘리기 위해 듀플렉스 PVD 코팅 사용에 초점을 맞춘 연구 결과를 제시합니다.
3. 서론:
고압 다이캐스팅 공정은 알루미늄, 마그네슘, 아연, 구리 합금으로 부품을 생산하는 데 사용됩니다. 금형은 20-60 m/s의 속도로 움직이는 용융 금속으로부터의 높은 압력, 급격한 온도 변화, 침식 등 혹독한 조건을 견뎌야 합니다. 이러한 조건은 침식, 부식, 마모, 열 피로와 같은 파손 메커니즘으로 이어져 다이의 수명을 제한합니다. 특히 열 피로는 균열 네트워크를 유발하여 비용이 많이 드는 다이 유지보수 및 교체로 이어집니다. 질화 및 PVD 코팅과 같은 표면 처리는 열 피로 저항성을 개선하고 마모를 줄이기 위해 개발되었으며, 연구에 따르면 PVD 코팅은 서비스 수명을 4배에서 17배까지 늘릴 수 있습니다.
4. 연구 요약:
연구 주제의 배경:
알루미늄 합금의 고압 다이캐스팅용 금형은 혹독한 작동 조건으로 인해 열화를 겪습니다. 이러한 열화는 금형의 수명을 제한하며, 이는 중요한 경제적 및 환경적 문제입니다.
이전 연구 현황:
이전 연구에서는 주요 파손 메커니즘(부식, 솔더링, 침식, 열 피로)을 확인하고 이를 완화하기 위한 다양한 표면 처리를 탐구했습니다. 질화물 및 탄화물 기반의 경질 PVD 코팅(예: TiN, CrN) 및 듀플렉스 처리는 서비스 수명을 크게 증가시키는 것으로 나타났습니다.
연구 목적:
본 연구는 금형 인서트의 열화 메커니즘을 상세히 분석하고, 기존(AlXN³) 및 차세대 나노구조(nACRo³) PVD 코팅을 적용하여 금형 기능 표면의 품질과 수명을 향상시키는 효과를 조사하는 것을 목표로 했습니다.
핵심 연구:
연구의 핵심은 두 부분으로 구성되었습니다: 1) 마모된 금형 인서트의 파손 분석을 통해 쐐기 모양 균열의 형성과 원인을 식별. 2) 금형 모재에 적용된 두 가지 PVD 코팅(AlXN³ 및 nACRo³)의 비교 분석을 통해 주요 성능 지표로서의 접착력과 미세경도를 평가.
5. 연구 방법론
연구 설계:
본 연구는 실험적 연구로 설계되었습니다. 기존의 마모된 금형 부품의 파손 분석으로 시작하여 표준화된 모재에 적용된 두 가지 다른 PVD 코팅의 비교 평가로 진행되었습니다.
데이터 수집 및 분석 방법:
모재는 Uddeholm Dievar 공구강이었습니다. 파손 분석은 광학 현미경과 EDX 장치가 장착된 Jeol JSM 7000F 주사 전자 현미경(SEM)을 사용하여 수행되었습니다. 코팅 접착력은 ISO 18265에 따라 로크웰 C 압입 테스트(메르세데스 테스트)를 사용하여 평가되었습니다. 미세경도는 ISO 6507-1에 따라 비커스 압입기(HV 0.025)가 장착된 Leco LM 700 테스터를 사용하여 측정되었습니다. 마찰 특성은 CSEM-Revertest 장치에서 스크래치 테스트로 평가되었습니다.
연구 주제 및 범위:
본 연구는 알루미늄 합금, 특히 Al-Si-Cu 기반 합금의 고압 주조용 금형에 초점을 맞췄습니다. 범위에는 마모된 금형의 균열 형성 분석과 AlXN³ 및 nACRo³ PVD 코팅이 제공하는 접착력 및 미세경도 향상 정량화가 포함되었습니다.
6. 주요 결과:
주요 결과:
연구 결과, 주기적인 응력으로 인해 금형의 날카로운 모서리에 쐐기 모양의 균열이 형성되는 것으로 나타났습니다. AlXN³ 및 nACRo³ PVD 코팅 모두 H13 강철 기판에 우수한 접착력을 가지고 있음을 확인했습니다. 결정적으로, 코팅은 표면 미세경도를 크게 증가시켰으며, nACRo³ 나노복합 코팅은 기존 AlXN³ 코팅(720 HV)보다 더 높은 최대 경도(810 HV)를 보였습니다.
그림 이름 목록 (원문 유지):
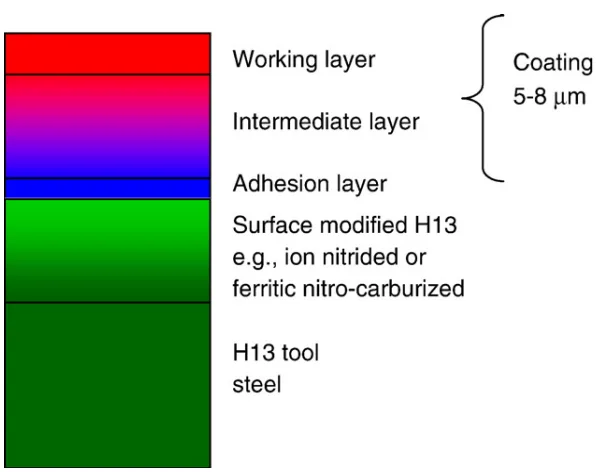

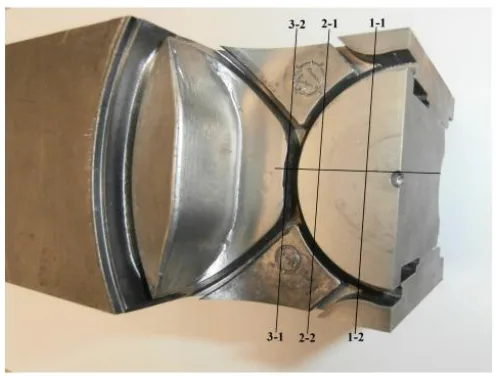
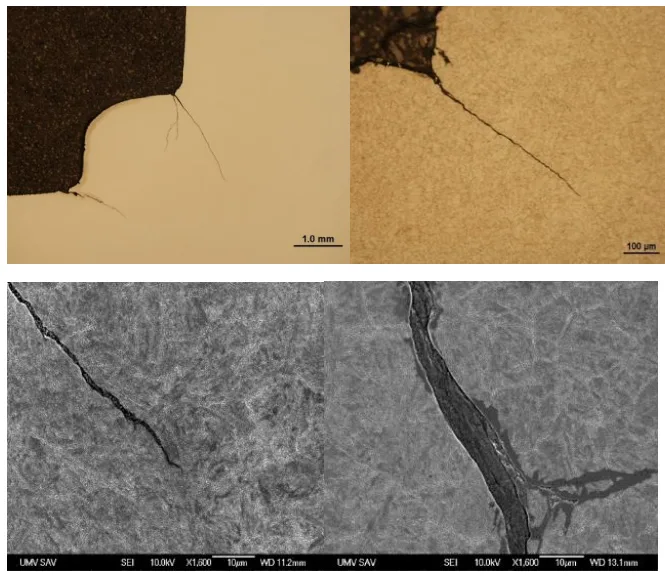
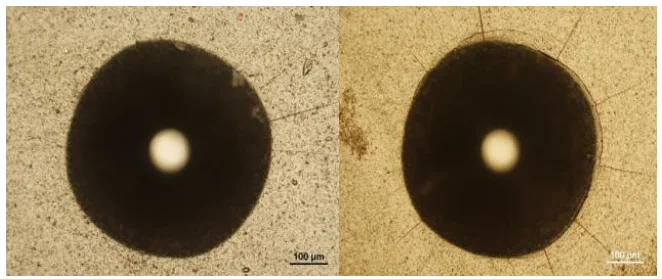
- Fig.1 Degradation of the mold part
- Fig.2 A diagram of an optimized coating architecture for die coatings used in aluminum high pressure die-casting.
- Fig.3 Sampling procedure from the mold part
- Fig.4 Worn solid half of the mold insert (left); appearance of cracks by capillary method (right)
- Fig.5 Cracks in the zones of sharp transitions of the surfaces of shaped parts of the mold (light and electron microscopy)
- Fig.6 Zone of sharp transitions of the surfaces of the shaped parts of the mold
- Fig.7 Indentation impression after Mercedes test; AIXN³ (left), nACRo³ (right)
- Fig.8 Dependence of acoustic emissions (AE) on the coefficient of friction (COF) of coatings
- Fig.9 Graph of measured microhardness values
7. 결론:
본 논문은 PVD 나노구조 코팅이 고압 알루미늄 다이캐스팅용 금형의 기능적 표면을 수정하는 효과적인 방법이라고 결론 내립니다. 탄성 변형으로 인한 분기된 균열의 열화 메커니즘이 분석되었습니다. 연구는 기존의 AlXN3 코팅과 차세대 나노구조 nACRo3 코팅을 성공적으로 적용하고 테스트했습니다. 테스트 결과 PVD 코팅의 높은 품질이 확인되었으며, 코팅이 조밀하고 온전하며 보호 장벽을 형성하고 우수한 접착력과 증가된 경도를 가짐을 보여주었습니다.
8. 참고 문헌 (원문 유지):
- D. Abid, A. Ktari, D. Mellouli, N. Gafsi, N. Haddar: Failure analysis of shot-sleeves used in brass high pressure die-casting process, In: Engineering Failure Analysis, 2019, Volume 104, pp. 177-188
- V. Nunes, F.J. Silva, M.F. Andrade, R. Alexandre, A.P.M. Baptista: Increasing the lifespan of high-pressure die cast molds subjected to severe wear, In: Surface & Coatings Technology, 2017, Volume 332, pp. 319-331
- S. H. Kang, J.J. Han, W.T. Hwang, S.M. Lee, H.K. Kim: Failure analysis of die casting pins for an aluminum engine block, In: Engineering Failure Analysis, 2019, Volume 104, pp. 690-703
- D. Mellouli, N. Haddar, A. Koster, H.F. Ayedi: Thermal fatigue failure of brass die - casting dies, In: Engineering Failure Analysis, 2012, Volume 20, pp. 137-146
- J. Wang et.al.: On the failure mechanism for high pressure die casting A390 hypereutectic alloy in low cycle and high cycle fatigue, In: Materials Science & Engineering A, 2018, Volume 723, pp. 48-55
- R. Ding et.al.: Failure analysis of H13 steel die for high pressure die casting Al alloy, In. Engineering Failure Analysis, 2021, Volume 124, pp. 105330
- J. Lin et.al.: Design methodology for optimized die coatings: The case for aluminum pressure die-casting, In: Surface & Coating Technology, 2006, Volume 201, pp. 2930-2941, Elsevier
- K. Bobzin, et. al: Analysis of CrN/AIN/Al2O3 and two industrially used coatings deposited on die castings cores after application in an aluminum die casting machine, In: Surface & Coating Technology, 2016, Volume 308, pp. 374-382, Elsevier
- B. Wang, et.al.: Method to evaluate the adhesion behaviour of aluminum-based alloys on various materials and coatings for lube-free die casting, In: Journal of Materials Processing Technology 2016, Volume 237, pp. 386-393, Elsevier
전문가 Q&A: 자주 묻는 질문에 대한 답변
Q1: 이 연구에서 금형 내구성 향상을 위해 확인된 가장 중요한 단일 요소는 무엇이었습니까?
A1: 이 연구는 nACRo3와 같은 고품질 나노구조 PVD 코팅을 적용하여 금형의 기능적 표면 품질을 수정하는 것이 가장 중요한 요소라고 결론지었습니다. 이는 "결론" 섹션에 자세히 설명되어 있으며, 높은 경도와 접착력을 가진 조밀하고 온전한 장벽을 형성하는 코팅의 능력을 강조합니다.
Q2: 이 연구는 금형 열화를 해결하기 위한 전통적인 방법과 어떻게 비교됩니까?
A2: 논문의 서론
에서는 표면 품질이 더 이상 충분하지 않을 때 연삭이나 용접과 같은 전통적인 사후 유지보수 방법을 언급합니다. 대조적으로, 여기서 조사된 PVD 코팅 접근법은 열화 발생을 예방하도록 설계된 선제적 표면 처리이며, 논문은 PVD 코팅이 코팅되지 않은 다이에 비해 서비스 수명을 "몇 배(4배에서 17배)" 늘릴 수 있다고 언급합니다.
Q3: 이 발견은 모든 종류의 합금에 적용됩니까, 아니면 특정 합금에만 적용됩니까?
A3: 초록
및 재료 및 방법
섹션에 설명된 바와 같이, 이 연구는 특히 Al 및 그 합금의 고압 주조에 사용되는 금형을 대상으로 수행되었으며, 테스트에는 Al-Si-Cu 기반 합금이 포함되었습니다. 금형 재료 자체는 열간 공구강인 Uddeholm Dievar였습니다. 다른 다이 재료나 주조 합금에 대한 적용 가능성은 추가 조사가 필요합니다.
Q4: 연구원들은 이 결론에 도달하기 위해 어떤 특정 측정 또는 시뮬레이션 기술을 사용했습니까?
A4: 연구원들은 코팅 접착력을 평가하기 위해 메르세데스 테스트라고도 알려진 로크웰 C 압입 테스트를 사용했으며, 표면 경도 증가를 정량화하기 위해 비커스 미세경도 시험기(HV 0.025)를 사용했습니다. 재료 및 방법
및 PVD 코팅의 접착력
섹션에 설명된 이러한 물리적 테스트는 결론을 뒷받침하는 정량적 데이터를 제공했습니다.
Q5: 논문에 따르면, 주요 한계점이나 향후 연구 분야는 무엇입니까?
A5: 이 논문은 코팅 자체의 재료 과학 및 특성에 초점을 맞추고 있으며, 제조 시설에서의 장기 생산 실행 동안의 성능을 자세히 설명하지 않습니다. 감사의 글
섹션에서는 "레이저 용접 오버레이"에 대한 관련 프로젝트를 언급하며, 복원 기술이 향후 연구의 또 다른 초점 영역임을 시사합니다.
Q6: 이 논문이 다이캐스팅 시설에 주는 직접적이고 실질적인 교훈은 무엇입니까?
A6: 핵심 교훈은 nACRo³와 같은 나노구조 PVD 코팅을 금형 인서트에 적용함으로써 표면 경도를 크게 높이고 우수한 접착력을 보장할 수 있으며, 이는 알루미늄 다이캐스팅의 주요 마모 및 균열 메커니즘에 직접적으로 대응한다는 것입니다. 이는 "고압 알루미늄 합금용 금형의 열화 감소 가능성"이라는 논문의 전반적인 결과에 의해 강력하게 뒷받침되는, 금형 수명을 연장하고 생산 안정성을 향상시키기 위한 실질적인 전략입니다.
결론 및 다음 단계
이 연구는 알루미늄 HPDC 운영에서 금형 내구성을 향상시키기 위한 귀중한 로드맵을 제공합니다. 이 발견은 품질을 개선하고 비용이 많이 드는 금형 열화의 영향을 줄이기 위한 명확하고 데이터 기반의 경로를 제공합니다. 나노구조 PVD 코팅의 우수한 경도와 접착력을 입증함으로써, 이 연구는 생산을 최적화하고 경쟁 우위를 확보하려는 모든 제조업체를 위한 강력한 도구를 강조합니다.
CASTMAN에서는 고객의 가장 어려운 다이캐스팅 문제를 해결하기 위해 최신 산업 연구를 적용하는 데 전념하고 있습니다. 이 논문에서 논의된 문제가 귀사의 운영 목표와 공감대를 형성한다면, 저희 엔지니어링 팀에 연락하여 이러한 고급 원칙을 귀사의 부품에 구현하는 방법을 논의하십시오.
저작권
- 이 자료는 "Ján Hašul, Janette Brezinová"의 논문입니다. "Possibilities of reducing the degradation of molds for high-pressure of Al alloys"를 기반으로 합니다.
- 논문 출처: 논문에는 특정 DOI URL이 기재되어 있지 않지만, INTERNATIONAL SCIENTIFIC JOURNAL "MACHINES. TECHNOLOGIES. MATERIALS", YEAR XVI, ISSUE 4, P.P. 123-126 (2022)에 발표되었습니다.
이 자료는 정보 제공 목적으로만 사용됩니다. 무단 상업적 사용을 금지합니다.
Copyright © 2025 CASTMAN. All rights reserved.