本紹介資料は、「Scientia Iranica, Transactions B: Mechanical Engineering」に掲載された論文「Minimizing the casting defects in high-pressure die casting using Taguchi analysis」に基づいています。
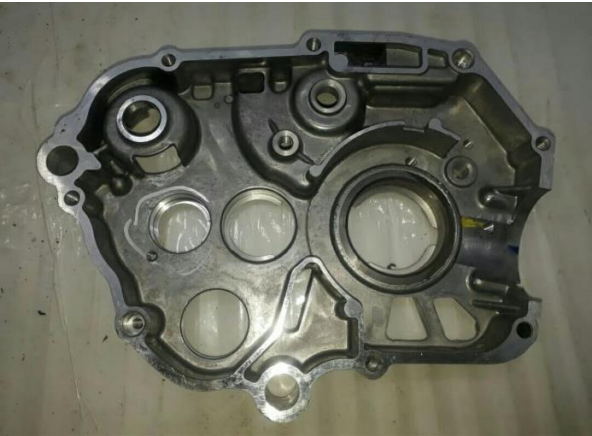
1. 概要:
- 論文タイトル: Minimizing the casting defects in high-pressure die casting using Taguchi analysis
- 著者: S. Tariq, A. Tariq, M. Masud, and Z. Rehman
- 発行年: 2022 (オンライン公開 2021年5月, 冊子発行 2022年)
- 掲載学術誌/学会: Scientia Iranica, Transactions B: Mechanical Engineering (Sharif University of Technology 発行)
- キーワード: High pressure die casting; Porosity; Design of experiment; Optimization; Casting defects.
2. 抄録 (Abstract):
高圧ダイカスト(HPDC)は自動車産業における主要な生産プロセスの一つであり、幾何学的に複雑な非鉄鋳物を製造するために広く用いられています。HPDCで製造された製品の機械的強度と微細構造は、射出圧力、溶湯温度、1次および2次プランジャー速度、冷却温度などのいくつかのプロセスパラメータの変動によって変化します。これらのプロセスパラメータは鋳造品質に直接影響するため、プロセスの生産性を最大化し、ポロシティ(気孔)、ピンホール、ブローホールなどの鋳造欠陥を最小化するためには、それらの最適な組み合わせが必要です。そこで、この問題に取り組むため、本論文では実験計画法(DOE)とタグチ分析を組み合わせてパラメータを最適化することにより、HPDCプロセスにおける主要な鋳造欠陥であるポロシティを最小化するアプローチを提示します。得られた結果は、冷却時間、射出圧力、および2次プランジャー速度が応答因子(鋳造部品の密度)に大きな影響を与えることを示しました。さらに、178 barの射出圧力、665°Cの溶湯温度、5秒の冷却時間、210°Cの金型温度、0.20 m.s⁻¹の1次プランジャー速度、および6.0 m.s⁻¹の2次プランジャー速度を使用することにより、選択された部品のポロシティによる不良率が61%削減されたと結論付けられました。
3. はじめに (Introduction):
高圧ダイカスト(HPDC)は、自動車、通信、農業などの産業向けに、経済的で複雑な形状かつ寸法精度の高い非鉄金属部品(アルミニウムなど)を製造するために、最も重要かつ広く使用されている製造プロセスの一つです[1, 2]。自動車産業では、クラッチ、ギアボックス、サスペンション、ブレーキ部品、コネクティングロッドなど、幅広い部品の製造に使用されています[3]。一般的にHPDCでは、溶融金属が準備され、高圧下でスリーブを通って金型キャビティに強制的に注入され、凝固が起こるまで高圧下に保持されます。金属の凝固後、金型が解放され、鋳造品が取り出されます[6]。HPDCプロセスは、優れた部品生産、高い寸法精度、部品あたりの製造コスト削減をもたらします[4]。プロセスには多くの利点がありますが、最終的な鋳造品には依然としてポロシティ、ピンホール、ブローホール、収縮、介在物、リングクラックなどの欠陥が存在します[4, 5, 7]。これらの欠陥は、引張強度や疲労強度に直接影響を与えるだけでなく、鋳造部品の被削性や表面仕上げにも悪影響を及ぼします[5, 8-10]。HPDCによって製造される部品の品質は、射出圧力、溶湯温度、1次および2次プランジャー速度、鋳造圧力、冷却温度、金型冷却時間など、様々な制御パラメータに依存します[5, 11-13]。これらのパラメータはそれぞれ、完璧な凝固と鋳造欠陥のない部品を得るために最適値に設定する必要があります。これらの制御パラメータの中で、射出圧力はポロシティの主要な寄与因子であり、ポロシティの変化は金型キャビティ内の負圧と線形関係にあります[14-16]。さらに、不均一な冷却温度は収縮欠陥の形成を引き起こします[17]。注入温度、鋳造圧力、1次および2次プランジャー速度の変動は、鋳造部品の冶金学的特性と機械的強度を変化させます[18]。プランジャー速度とその動きは、ダイカストの最終品質において重要な役割を果たします。1次プランジャー速度は機械内のダイカストチャンバーの充填に関連し、2次プランジャー速度は金型キャビティの充填と相関しています[19]。A380合金を扱う際の冷却温度の変動により、熱処理プロセス中に通常、空気巻き込み欠陥が発生します[20]。充填中の凝固挙動は表面欠陥に非常に大きな影響を与えます。金型内の溶湯温度の低下率は表面欠陥の確率に影響し、固体表面層の厚さが増加するにつれて増加します[21]。同様に、金型温度はHPDCにおける製品の品質に影響を与え、最適範囲からの逸脱は鋳造欠陥を引き起こします[22, 23]。1次および2次プランジャープロファイルと速度は、アルミニウム合金の場合、鋳物の強度特性を低下させる上で重要な役割を果たします[19]。これらの理由から、最小限の欠陥で高品質の鋳物を生産するためには、異なるHPDCプロセス制御パラメータ(射出圧力、溶湯温度、1次および2次プランジャー速度、鋳造圧力、冷却温度、金型冷却時間)の組み合わせを最適化する必要があります。
4. 研究概要:
研究テーマの背景:
HPDCは複雑な非鉄部品を大量生産するための重要なプロセスですが、製品の品質と性能を損なうポロシティなどの様々な鋳造欠陥が発生しやすいという課題があります。多数の相互作用するプロセスパラメータを制御することは不可欠ですが困難です。
先行研究の状況:
先行研究では、シミュレーションや実験を通じて個々のHPDCパラメータの影響が調査されてきました。ファジィシステム、ニューラルネットワーク、および「Anycasting」などのソフトウェアシミュレーションを用いた手法が、ポロシティなどの欠陥を予測または最小化するために使用されてきました[25-28]。実験計画法(DOE)と組み合わせたタグチメソッドは、スクイズキャスティングや砂型鋳造など、様々な製造プロセスの最適化に適用されています[35-39]。しかし、実際の産業アプリケーションにおいて、複数の主要なHPDCパラメータを同時に最適化してポロシティ欠陥を最小化することに特化した、DOEとタグチ分析を用いた包括的な実験的アプローチは、あまり検討されていないことが確認されました。鋳造現場で用いられる従来の試行錯誤法は、しばしば非効率的でコストがかかります[29]。
研究目的:
本研究は、特定の自動車部品(バイク用クランクケースLH)の工業的HPDCプロセスにおいて、主要な鋳造欠陥であるポロシティを最小化することを目的としました。これは、実験計画法(DOE)とタグチ分析を組み合わせて、6つの主要な制御可能なプロセスパラメータ(射出圧力、溶湯温度、金型冷却時間、金型温度、1次プランジャー速度、2次プランジャー速度)を最適化することによって達成されました。目標は、鋳造部品の密度を最大化することによりポロシティを低減し、全体的な製品品質と生産歩留まりを向上させる最適なパラメータの組み合わせを見つけることでした。
研究の核心:
研究はバイク製造会社で実施されました。高い生産量と不良率のため、アルミニウムADC 12合金製のクランクケース左側(LH)部品が選定されました(Figure 1, Table 1, Table 2)。生産データ分析とパレート図(Table 3, Figure 3)により、ポロシティ/ピンホールが不良の主な原因として特定されました(Figure 2)。ポロシティの原因となる要因を特定するために特性要因図(Figure 4)が用いられ、鋳造現場で制御可能な6つのHPDCプロセスパラメータが因子として選択されました。各因子について3つの水準を持つタグチL27直交表(Table 5)が実験計画に使用されました。実験は800トンのHPDCマシンで行われました。得られた鋳物の密度が応答因子として測定され(アルキメデスの原理を使用、Table 6)、密度が高いほどポロシティが少ないことを示します(S/N比「望大特性」)。Minitabソフトウェアを使用して、各パラメータの影響を特定し、最適設定を予測するためにタグチ分析(平均応答とS/N比)が実行されました(Table 7, Table 8, Figure 5, Figure 6)。最適な組み合わせを確認するために、提案された最適レベル周辺で個々のパラメータを変更するさらなる検証実験が行われました(Table 10-15)。最後に、最適化されたパラメータを1週間実施し、ポロシティによる不良率の削減を確認するために生産データが収集されました(Table 16, Table 17, Figure 7)。
5. 研究方法論
研究デザイン:
本研究では、DOEおよびタグチロバスト実験の原則に基づいた構造化された実験計画を採用しました。方法論には以下が含まれます:
- 既存のダイカスト手順を分析し、最も頻繁に鋳造される部品とその主要な欠陥を特定する。
- 入力変数(因子)と応答因子(密度)を選択する。
- 初期試行と鋳造現場の実践に基づいてパラメータの範囲とレベルを設定する。
- 自由度(DOF)に基づいて適切な直交表(L27)を選択する。
- OA設計に従って実験を実施する。
- 応答因子データを取得し、タグチ法(平均およびS/N比分析)を用いて分析する。
- 最適なパラメータ設定を洗練し確認するために検証実験を実施する。
- 最適化されたパラメータの実施前後の生産欠陥データを比較する。
データ収集・分析方法:
- 部品/欠陥特定: 1ヶ月間の生産データ(Table 1)と欠陥記録(Table 3)を収集しました。パレート分析(Figure 3)を用いて、ポロシティ/ピンホールを主要な欠陥として特定しました。
- 材料分析: ADC 12アルミニウム合金の材料組成は、Spectromax金属分析装置を用いて決定されました(Table 2)。
- パラメータ選択: 特性要因図(フィッシュボーンダイアグラム)(Figure 4)が、ポロシティに影響を与える可能性のある因子を特定するのに役立ちました。6つの制御可能な因子が選択されました。
- 実験設定: 補助装置を備えた800トンのYizumi SM-800T HPDCマシンが使用されました。因子レベルが設定されました(Table 4)。L27 OAに基づいた27回の実験ラン(Table 5)が実施され、各ランごとに3つのサンプル(「ショット」)が採取されました。
- 応答測定: 各鋳造部品の質量は、最小表示1gの電子計量スケールを用いて測定されました。密度はアルキメデスの原理を用いて計算されました(Table 6)。
- データ分析: Minitab 18ソフトウェアを用いてタグチ分析が実施されました。分析には、密度の「望大特性」基準を用いた平均応答(Table 7, Figure 5)および信号対雑音(S/N)比(Table 8, Figure 6)の計算が含まれました。
- 検証: 最終的な最適化設定を見つけるために、予測された最適値の周りで一度に1つの因子を変更するターゲット実験が実施されました(Tables 10-15)。最適化後の生産データが収集され(Table 17)、分析されました(Figure 7)。
研究対象と範囲:
本研究は、アルミニウムADC 12合金から作られた特定のコンポーネント、クランクケース左側(LH)部品の 高圧ダイカスト(HPDC)プロセスの最適化に焦点を当てました。範囲は、以下の6つの特定のプロセスパラメータを最適化することにより、ポロシティ欠陥を最小化することに限定されました:
- 射出圧力 (bar)
- 溶湯温度 (°C)
- 金型冷却時間 (s)
- 金型温度 (°C)
- 1次プランジャー速度 (m.s⁻¹)
- 2次プランジャー速度 (m.s⁻¹)
研究では、密度を主要な測定可能な応答変数として使用し、密度が高いほどポロシティが低いと仮定しました。実験は、バイク製造施設の産業環境内で行われました。
6. 主な結果:
主な結果:
- 生産データの分析により、クランクケースLH部品の最も重大な欠陥は「ピンホール/ブローホール」(ポロシティ)であり、全不良の32.17%を占めていることが明らかになりました(1ヶ月間で不良1352個中435個)。
- タグチ分析(平均およびS/N比)により、密度(ひいてはポロシティ)に影響を与える最も重要なパラメータは、影響度の高い順に、金型冷却時間(Rank 1)、射出圧力(Rank 2)、2次プランジャー速度(Rank 3)であることが特定されました。溶湯温度(Rank 4)、金型温度(Rank 5)、1次プランジャー速度(Rank 6)の影響は比較的小さいものでした。
- タグチ分析とその後の検証実験を通じて、密度を最大化(ポロシティを最小化)するための最適なパラメータの組み合わせは次のように決定されました:
- 射出圧力: 178 bar
- 溶湯温度: 665°C
- 金型冷却時間: 5 s
- 金型温度: 210°C
- 1次プランジャー速度: 0.20 m.s⁻¹
- 2次プランジャー速度: 6.0 m.s⁻¹
- これらの最適化されたパラメータを1週間生産に適用した結果、ポロシティ/ピンホールによる不良率が大幅に削減されました。不良数量は435個(全生産の0.9%、全不良の32.17%)から140個(全生産の0.29%、全不良の11.47%)に減少し、これはポロシティ関連の不良率が約61%削減されたことを示しています。
- 最適化されたパラメータの適用後、クラック(約16%)および介在物(約10%)による不良率の削減も観察されました。収縮、へこみ、リングクラック/ミスマッチ、シェードなどの他の欠陥には大きな変化は見られませんでした。
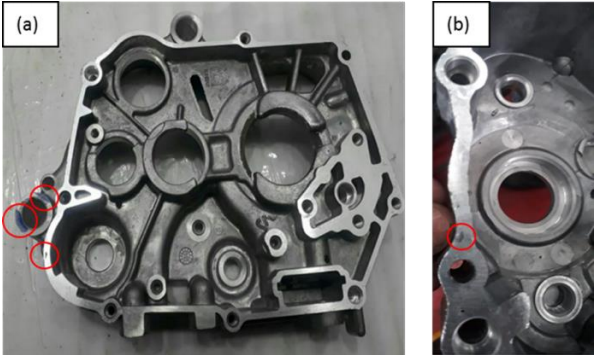
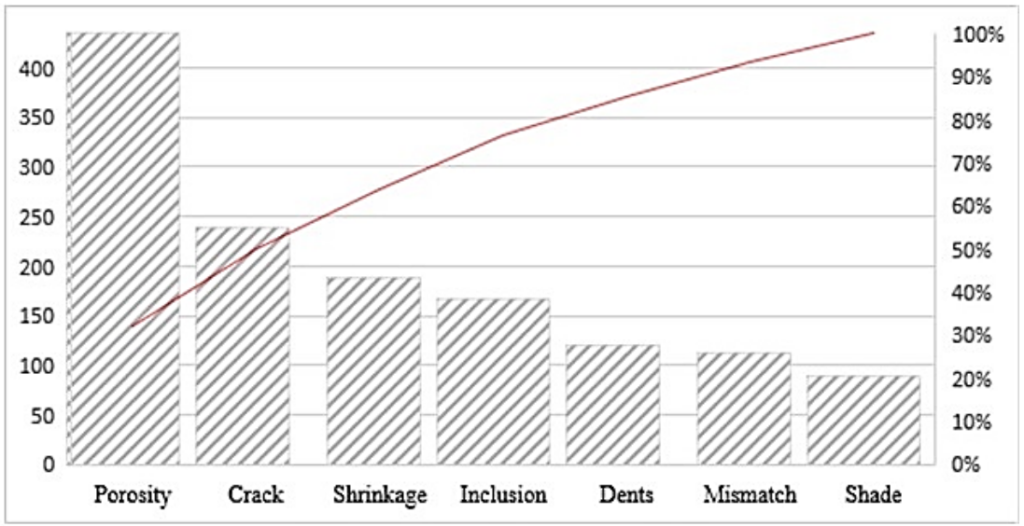
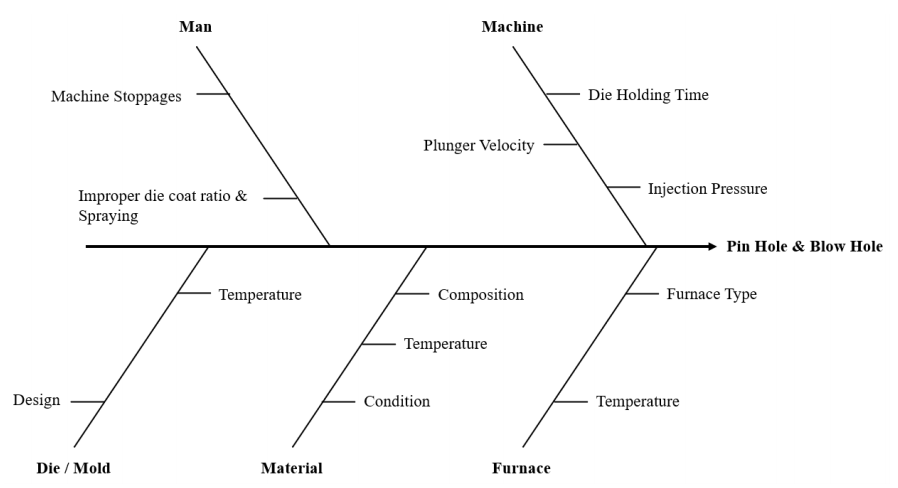
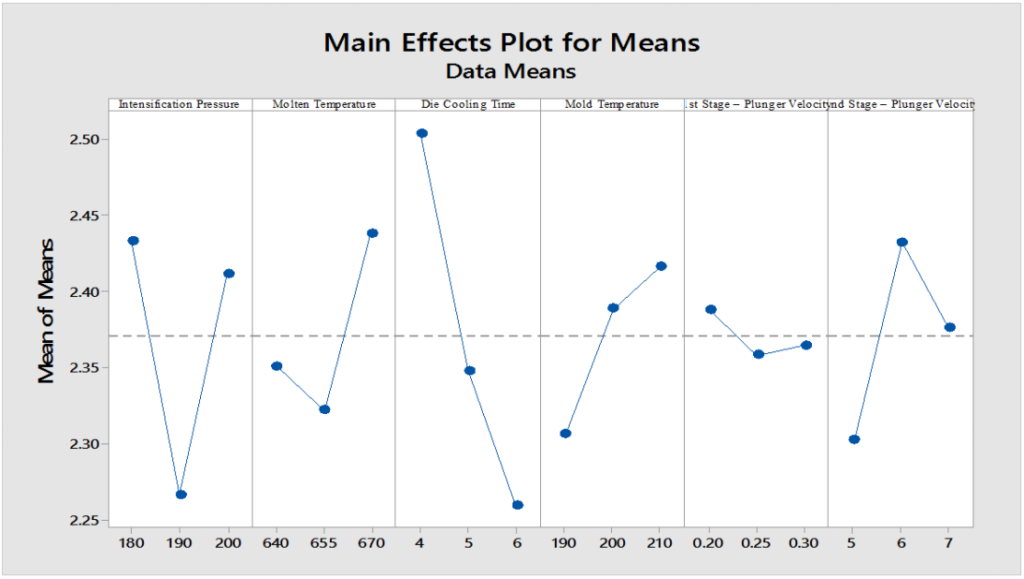
図のリスト (Figure Name List):
- Figure 1. Crankcase specimen produced with the High-Pressure Die Casting (HPDC) process.
- Figure 2. Casting defects found in the Crankcase: (a) pinhole and (b) porosity.
- Figure 3. Pareto chart of the defects.
- Figure 4. Cause and effect diagram.
- Figure 5. Response graph of means against the selected input parameters.
- Figure 6. Response graph of the S/N ratio against the selected input parameters.
- Figure 7. Pareto chart of the defects after optimization.
7. 結論:
高圧ダイカスト(HPDC)は、大量の複雑な部品をコスト効率よく生産するための重要な製造プロセスですが、ポロシティ、ピンホール、ブローホール、スティッキング、クラック、介在物などの様々な欠陥が発生しやすいという性質があります。これらの欠陥の発生は、射出圧力、溶湯温度、金型冷却時間、金型温度、1次プランジャー速度、2次プランジャー速度など、様々なプロセスパラメータの値を最適に組み合わせることで制御できます。本研究では、実験計画法(DOE)とタグチ分析を組み合わせたアプローチを開発し、ラホール(パキスタン)のバイク製造会社におけるHPDCプロセスを対象として、これらのプロセスパラメータを最適化し、鋳造欠陥を最小化しました。実験と比較のために、頻繁に発生していた主要な欠陥(ポロシティ)を最小化し、HPDCで製造された部品(クランクケースLH)の応答因子(密度)を最大化することを選択しました。タグチ分析とそれに続く実験計画から、冷却時間、射出圧力、および2次プランジャー速度が応答因子(密度)に最も大きな影響を与えることがわかりました。178 barの射出圧力、665°Cの溶湯温度、5秒の冷却時間、210°Cの金型温度、0.20 m.s⁻¹の1次プランジャー速度、および6.0 m/sの2次プランジャー速度を使用することで、欠陥率の削減が達成されました。これらの最適化されたパラメータにより、選択された部品のポロシティによる全体的な不良率が約61%減少しました。
8. 参考文献 (References):
- [1] Teng, X., Mae, H., Bai, Y., et al. "Pore size and fracture ductility of aluminum low pressure die casting", Eng. Fract. Mech., 76(8), pp. 983-996 (2009).
- [2] Fracchia, E., Lombardo, S., and Rosso, M. "Case study of a functionally graded aluminum part", Appl. Sci., 8(7), p. 1113 (2018).
- [3] Makhlouf, M.M., Apelian, D., and Wang, L., Microstructures and Properties of Aluminum Die Casting Alloys, USDOE Idaho Operations Office, Idaho Falls, ID (US); North American Die … (1998).
- [4] Dargusch, M.S., Dour, G., Schauer, N., et al. "The influence of pressure during solidification of high pressure die cast aluminium telecommunications components", J. Mater. Process. Technol., 180(1-3), pp. 37-43 (2006).
- [5] Bonollo, F., Gramegna, N., and Timelli, G. "High-pressure die-casting: contradictions and challenges", Jom, 67(5), pp. 901-908 (2015).
- [6] Hamasaiid, A., Dargusch, M.S., Davidson, C., et al. "Effect of mold coating materials and thickness on heat transfer in permanent mold casting of aluminum alloys", Metall. Mater. Trans. A, 38, pp. 1303-1316 (2007).
- [7] Adamane, A.R., Arnberg, L., Fiorese, E., et al. "Influence of injection parameters on the poorosity and tensile properties of high-pressure die cast Al-Si alloys: A review", Int. J. Met., 9(1), pp. 43-53 (2015).
- [8] Hidalgo, R., Esnaola, J., Larrañaga, M., et al. “Influence of surface finish and porosity on the fatigue behaviour of A356 Aluminium casting alloy", MATEC Web Conf., 165, p. 14007 (2018).
- [9] Anilchandra, A.R., Arnberg, L., Bonollo, F., et al. "Evaluating the tensile properties of aluminum foundry alloys through reference castings-A review", Materials (Basel)., 10(9), p. 1011 (2017).
- [10] Yang, H., Yu, W., LI, X., et al. "Effect of different processing parameters on interfacial heat-transfer behavior in high-pressure die-casting process", Trans. Nonferrous Met. Soc. China, 28, pp. 2599-2606 (2018).
- [11] Kong, L.X., She, F.H., Nahavandi, S., et al. "Die temperature monitoring of high pressure die casting", Smc 2000 Conference Proceedings, 2000 Ieee International Conference on Systems, Man and Cybernetics, Cybernetics Evolving to Systems, Humans, Organizations, and Their Complex Interactions, 3, pp. 1756-1761 (2000).
- [12] Syrkos, G. "Die casting process optimization using Taguchi methods", J. Mater. Process. Technol., 135, pp. 68-74 (2003).
- [13] Ingle, V. and Sorte, M.B. "Defects, root causes in casting process and their remedies: Review", Int. J. Eng. Res. Appl., 07, pp. 47-54 (2017).
- [14] Zyska, A., Konopka, Z., Lagiewka, M., et al. "Porosity of castings produced by the vacuum assisted pressure die casting method", Archives of Foundry Engineering, 15(1), pp. 125-130 (2015).
- [15] Apparao, K.C. and Birru, A.K. "QFD-Taguchi based hybrid approach in die casting process optimization", Trans. Nonferrous Met. Soc. China, 27(11), pp. 2345-2356 (2017).
- [16] Wang, Y., Shiping, W., Lianjie, N., et al. "Optimization of low-pressure die casting process parameters for reduction of shrinkage porosity in ZL205 A alloy casting using Taguchi method", Proc. Inst. Mech. Eng. Part B J. Eng. Manuf., 228, pp. 1508-1514 (2014).
- [17] Kwon, H.-J. and Kwon, H.-K. "Computer aided engineering (CAE) simulation for the design optimization of gate system on high pressure die casting (HPDC) process", Robot. Comput. Integr. Manuf., 55, pp. 147-153 (2019).
- [18] Yalçın, B., Koru, M., Ipek, O., et al. "Effect of injection parameters and vacuum on the strength and porosity amount of die-casted A380 alloy", International Journal of Metalcasting, 11(2), pp. 195-206 (2017).
- [19] Fiorese, E., Bonollo, F., and Battaglia, E. "A tool for predicting the effect of the plunger motion profile on the static properties of aluminium high pressure die cast components", Metals (Basel)., 8(10), p. 798 (2018).
- [20] Cao, H., Wang, C., Che, J., et al. "Effect of flow state of pure aluminum and A380 alloy on porosity of high pressure die castings", Materials (Basel), 12(24), p. 4219 (2019).
- [21] Iwata, Y., Dong, S., Sugiyama, Y., et al. "Effects of solidification behavior during filling on surface defects of aluminum alloy die casting", Mater. Trans., 54, pp. 1944-1950 (2013).
- [22] Sadeghi, M. and Mahmoudi, J. "Experimental and theoretical studies on the effect of die temperature on the quality of the products in high-pressure die-casting process", Adv. Mater. Sci. Eng., 2012, p. 434605 (2012).
- [23] Liu, C., Jiao, X., Nishat, H., et al. "Characteristics of Fe-rich intermetallics compounds and their influence on the cracking behavior of a newly developed high-pressure die cast Al-4Mg-2Fe alloy", J. Alloys Compd., 854, p. 157121 (2021).
- [24] Kumar, S., Satsangi, P., and Prajapati, D.R. "Optimization of green sand casting process parameters of a foundry by using Taguchi's method", The International Journal of Advanced Manufacturing Technology, 55, pp. 23-34 (2010).
- [25] Fajkiel, A., Dudek, P., Walczak, W., et al. "Improvement of quality of a gravity die casting made from aluminum bronze be application of numerical simulation", Arch. Foundry Eng., 7, pp. 11-14 (2007).
- [26] Świłło, S. and Myszka, D. “Archives of 39/3 advanced metrology of surface defects measurement for aluminum die casting", Archives of Foundry Engineering, 11(3), pp. 227-230 (2011).
- [27] Cica, D. and Kramar, D. "Intelligent process modeling and optimization of porosity formation in high-pressure die casting", International Journal of Metalcasting, 12, pp. 814-824 (2018).
- [28] Cao, H., Shen, C., Wang, C., et al. "Direct observation of filling process and porosity prediction in high pressure die casting", Mater. (Basel, Switzerland), 12(7), p. 1099 (2019).
- [29] Aamir, M., Tu, S., Tolouei-Rad, M., et al. "Optimization and modeling of process parameters in multi-hole simultaneous drilling using Taguchi method and fuzzy logic approach", Materials (Basel), 13(3), p. 680 (2020).
- [30] Do, T.-V. and Hsu, Q.-C. "Optimization of minimum quantity lubricant conditions and cutting parameters in hard milling of AISI H13 steel", Appl. Sci., 6(3), p. 83 (2016).
- [31] Vu, N.-P., Nguyen, Q.-T., Tran, T.-H., et al. "Optimization of grinding parameters for minimum grinding time when grinding tablet punches by CBN wheel on CNC milling machine", Applied Sciences, 9(5) (2019).
- [32] Lan, T.-S., Chuang, K.-C., and Chen, Y.-M. "Optimization of machining parameters using fuzzy Taguchi method for reducing tool wear", Appl. Sci., 8(7), p. 1011 (2018).
- [33] Kolahan, F. and Azadi Moghaddam, M. "The use of Taguchi method with grey relational analysis to optimize the EDM process parameters with multiple quality characteristics", Sci. Iran., 22(2), pp. 530-538 (2015).
- [34] Azadi Moghaddam, M. and Kolahan, F. "Modeling and optimization of the electrical discharge machining process based on a combined artificial neural network and particle swarm optimization algorithm", Sci. Iran., 27(3), pp. 1206-1217 (2020).
- [35] Karthik, A., Karunanithi, R., Srinivasan, S.A., et al. "The optimization of squeeze casting process parameter for AA2219 alloy by using the Taguchi method", Materials Today: Proceedings, 27, pp. 2556-2561 (2020).
- [36] Hassasi, S.A., Abbasi, M., and Hosseinipour, S.J. "Parametric investigation of squeeze casting process on the microstructure characteristics and mechanical properties of A390 aluminum alloy", Int. J. Met., 14(1), pp. 69-83 (2020).
- [37] Souissi, N., Souissi, S., Niniven, C., et al. "Optimization of squeeze casting parameters for 2017 a wrought Al alloy using Taguchi method", Metals (Basel), 4(2), pp. 141-154 (2014).
- [38] Prabhakar, A., Papanikolaou, M., Salonitis, K., et al. "Minimising defect formation in sand casting of sheet lead: A DoE approach", Metals (Basel), 10(2), p. 252 (2020).
- [39] Mohsin, I., He, K., Li, Z., et al. "Optimization of the polishing efficiency and torque by using Taguchi method and ANOVA in robotic polishing", Appl. Sci., 10(3), p. 824 (2020).
- [40] Balikai, V.G., Siddlingeshwar, I.G., and Gorwar, M. "Optimization of process parameters of High Pressure Die Casting process for ADC12 Aluminium alloy using Taguchi method", Int. J. Pure Appl. Math., 120(6), pp. 959-969 (2018).
- [41] Sarin, S. "Teaching Taguchi's approach to parameter design", Quality Progress, 30(5), p. 102 (1997). 30 (1997).
- [42] Wu, C.C. and Su, T.S. "Application of the Taguchi method for the optimization of visual inspection parameters for multi-layer ceramic capacitors", Sci. Iran., 21(6), pp. 2379-2386 (2014).
- [43] Chang, M.S. "Use of Taguchi method to develop a robust design for the magnesium alloy die casting process", Mater. Sci. Eng. A, 379(1-2), pp. 366-371 (2004).
- [44] Kamaruddin, S., Khan, Z., and Foong, S. "Application of Taguchi method in the optimization of injection moulding parameters for manufacturing products from plastic blend", Int. J. Web Eng. Technol., 2, pp. 574-580 (2010).
- [45] Asim, M., Khan, M., Khan, L., and Umer, M. "An integrated approach of quality for polymer composite manufacturing validated and optimized through Taguchi method", Sci. Iran., 24, pp. 1985-1995 (2017).
- [46] Banik, K. "Effect of mold temperature on short and long-term mechanical properties of PBT", Express Polym. Lett.-Express Polym Lett., 2, pp. 111-117 (2008).
9. 著作権 (Copyright):
- 本資料は、「S. Tariq, A. Tariq, M. Masud, and Z. Rehman」による論文です。「Minimizing the casting defects in high-pressure die casting using Taguchi analysis」に基づいています。
- 論文の出典: https://doi.org/10.24200/sci.2021.56545.4779
本資料は上記の論文に基づいて要約されており、商業目的での無断使用は禁じられています。
Copyright © 2025 CASTMAN. All rights reserved.