본 소개 자료는 "[International Journal of Mechanical Engineering]"에 게재된 "[Minimise the Nonfilling defect in the high pressure casting process component for an automotive application with metal flow simulation analysis]" 논문을 기반으로 합니다.
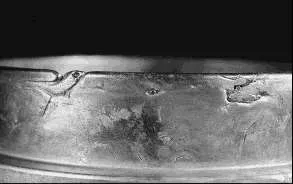
1. 개요:
- 제목: Minimise the Nonfilling defect in the high pressure casting process component for an automotive application with metal flow simulation analysis
- 저자: R.Govindarao, Dr.K.Eshwara Prasad (Rted)
- 발행 연도: 2022
- 게재 학술지/학회: International Journal of Mechanical Engineering
- 키워드: Nonfilling, Machine parameters, Simulation flow analysis.
2. 초록:
고압 다이캐스팅 공정은 모든 엔지니어링 응용 분야를 해결하는 세계적으로 중요한 주조 공정 중 하나입니다. 고압 다이캐스팅 제품은 항공 우주, 자동차, 가정용품, 농업 및 기타 엔지니어링 응용 분야 등 매우 다양한 분야에서 사용됩니다. 고압 다이캐스팅 공정에서 불량률은 약 7%에서 10%에 달합니다. 이 불량률에는 표면 결함 및 내부 결함으로 인한 불량이 포함됩니다. 표면 결함은 눈에 보이며 공정 가동 중에 최대한 해결할 수 있습니다. 모든 표면 결함 중에서 미충진(non-filling)은 모든 주물 형상에서 가장 반복적으로 발생하는 결함 중 하나입니다. 콜드샷(coldshot), 치핑(chipp off), 균열(crack), 주물 파손(casting broken) 등 일부 표면 결함은 공정 자체에서 제거될 수 있습니다. 그러나 미충진과 같은 표면 결함은 즉시 해결할 수 없습니다. 이는 기계 매개변수 최적화 및 금형 설계 개념과 같은 분석이 필요합니다.
3. 서론:
고압 다이캐스팅 공정은 고온의 용융 금속을 닫힌 강철 금형에 주입하는 과정을 포함합니다. 주물의 두께에 따라 주물의 응고를 위해 일정 시간(최소 6초 - 최대 15초) 동안 유지해야 합니다. 주물은 금형이 열린 후 취출되며 추출기가 주물을 수거합니다. 다음 작업을 수행하기 전에 금형을 원하는 온도 값(240°C)으로 냉각해야 합니다. 그렇지 않으면 주물이 금형에 달라붙을 수 있습니다. 이를 위해 금형은 RO 물과 혼합된 특수 화학 냉각제를 사용하여 냉각됩니다. 금형은 주물 면적에 따라 스프레이를 통해 몇 초(최소 4초 - 최대 10초) 동안 화학 냉각제로 냉각됩니다. 그 후 다음 사이클이 반복됩니다. 주물은 버(burr) 및 여분의 돌출된 재료를 제거하기 위한 추가 작업으로 넘어갑니다.
4. 연구 요약:
연구 주제 배경:
현재 고압 다이캐스팅 공정에서 불량은 매우 높은 비용을 발생시키고 있습니다. 불량률은 최대 9%에 달하며 이는 조직에 매우 큰 손실입니다. 이러한 불량은 미충진 5%, 바디 누수(body leak) 3% 및 나머지 표면 결함으로 인해 발생합니다. 표면 결함은 단 1%까지만 기여합니다. 미충진 결함은 표면 결함 중 하나로도 알려져 있습니다. 일부 표면 결함은 금속 온도, 압력 및 속도와 같은 공정 매개변수를 수정하여 공정 자체에서 줄일 수 있습니다. 한 배치 수량(500개)의 불량 세부 정보 기여도는 파레토 분석에 나와 있습니다. 제시된 파레토 분석에 따르면 미충진 결함이 전체 주조 불량의 약 47%를 차지하여 가장 중요한 결함입니다.
기존 연구 현황:
논문에 따르면, 전통적인 방법은 다이캐스터가 기계와 금형에서 새로운 결함 없는 주물을 얻을 때까지 공정 매개변수를 미세 조정하는 것을 포함합니다. 이 수동 접근 방식은 시간이 많이 소요되는 것으로 설명됩니다. MAGMASOFT와 같은 시뮬레이션 방법이 존재하며, 압력 다이캐스팅을 포함한 다양한 주조 공정에 널리 사용되어 난류 충진 및 금속 온도를 분석하는 기능을 제공합니다.
연구 목적:
본 연구는 금속 유동 시뮬레이션 분석을 적용하여 자동차 부품용 고압 다이캐스팅 공정에서 미충진 결함을 최소화하는 것을 목표로 합니다. 시뮬레이션을 사용하여 금속 유동 경로를 확인하고, 다른 위치에서의 온도를 분석하며, 주물 내 결함 위치를 식별하고, 러너 설계 및 기계 매개변수를 최적화하여 불량률을 줄이고 공정을 개선하는 것이 목적입니다.
핵심 연구:
연구의 핵심은 MAGMASOFT 유동 시뮬레이션 소프트웨어를 사용하여 자동차 부품의 고압 다이캐스팅 공정을 분석하는 것이었습니다. 주로 금속 주입 위치와 러너 단면을 변경한 네 가지 다른 러너 설계 모델이 생성되었습니다. 시뮬레이션은 사출의 세 단계(S1: 저속 접근, S2: 고속 충진, S3: 증압)에 걸쳐 용융 금속이 금형으로 난류 충진되는 것을 분석했습니다. 금속 온도, 압력, 속도, 충진 시간, 충진율과 같은 주요 매개변수를 다양한 위치와 단계(모델당 18단계 분석)에서 평가하여 네 가지 러너 설계의 성능을 비교했습니다. 목표는 미충진 결함의 위험을 가장 잘 완화하는 설계를 식별하는 것이었습니다. 시뮬레이션 결과는 최적의 설계(Model-4)를 기반으로 금형을 제조하는 데 사용되었으며, 이후 실험적 시험을 통해 결과를 검증했습니다.
5. 연구 방법론
연구 설계:
본 연구는 시뮬레이션 기반 비교 연구 후 실험적 검증을 수행하는 방식을 사용했습니다. 고압 다이캐스팅 금형에 대한 네 가지 고유한 러너 설계를 MAGMASOFT를 사용하여 시뮬레이션했습니다. 시뮬레이션 결과(충진 시간, 충진율, 온도 분포)를 비교하여 미충진 결함을 최소화하기 위한 최적의 설계를 식별했습니다. 그런 다음 선택된 설계(Model-4)를 기반으로 금형을 제조하고, 실제 불량률을 측정하여 시뮬레이션 예측을 검증하기 위한 생산 시험을 수행했습니다.
데이터 수집 및 분석 방법:
데이터 수집에는 다음이 포함되었습니다:
- 부품 도면을 기반으로 금형 세그먼트(코어, 캐비티, 러너, 게이트, 오버플로우, 채널, 냉각/가열 라인)의 완전한 3D 모델 생성.
- 주물 형상 및 면적을 기반으로 한 기계 용량 계산(예: 800T, 900T).
- 플런저 팁 및 챔버 치수를 포함한 수학적 계산을 위한 3D 모델 치수 동기화.
- 시뮬레이션 소프트웨어(MAGMASOFT)에 공정 매개변수 입력, 시뮬레이션 반복 실행(낮음, 중간, 높음 매개변수 범위).
- 정확도를 위한 형상 메싱 및 사출의 세 단계 분석을 포함한 시뮬레이션 실행.
- 18개 단계에 걸쳐 네 가지 모델 각각에 대한 시뮬레이션 출력 데이터 수집(금속 온도, 압력, 속도, 플런저 이동 거리, 용융 금속 유동 방향, 총 충진 시간, 충진율(단위 시간당 채워진 금속 부피)).
- 네 가지 모델 간의 충진 시간 및 온도 분포(특히 오버플로우 및 칠 벤트와 같은 충진 종료 위치) 비교에 중점을 둔 시뮬레이션 결과 분석.
- 선택된 시뮬레이션 모델(Model-4)에 따라 제작된 금형을 사용한 실험적 시험(500개 배치) 수행.
- 파레토 분석을 사용하여 실험적 시험에서 얻은 불량 데이터(특히 미충진 결함) 수집 및 분석.
연구 주제 및 범위:
본 연구는 자동차 부품의 고압 다이캐스팅(HPDC) 공정에 초점을 맞췄습니다. 주요 범위는 금속 유동 시뮬레이션 분석(특히 MAGMASOFT) 적용을 통한 미충진 결함 감소였습니다. 연구는 다음을 포함했습니다:
- 용융 금속 충진 공정 시뮬레이션.
- 네 가지 다른 러너 설계 비교.
- 세 가지 사출 단계(S1 - 저속 사출, S2 - 고속 사출/충진, S3 - 증압) 분석.
- 주요 공정 지표 평가: 충진 시간, 충진율, 금속 온도 분포, 압력 및 속도.
- 시뮬레이션 결과를 기반으로 한 최적의 러너 설계 식별.
- 생산 배치에서 결함률 측정을 통한 선택된 설계의 실험적 검증.
6. 주요 결과:
주요 결과:
- 초기 파레토 분석(Graph 1.0) 결과, 연구된 사례에서 미충진 결함이 주조 불량의 47%를 차지하여 가장 중요한 결함으로 나타났습니다.
- 유동 시뮬레이션 분석은 네 가지 러너 설계(Model 1-4)를 비교했습니다. Model 1과 2는 높은 충진 시간과 낮은 충진율로 인해 부적합한 것으로 간주되었습니다.
- Model 3은 네 모델 중 가장 낮은 충진 시간을 보였습니다(Graph 2.0). 그러나 Model 4에 비해 오버플로우 및 칠 벤트 영역에서 더 낮은 금속 온도(592°C - 615°C)를 나타냈습니다.
- Model 4는 Model 3과 거의 동일한 충진 시간을 가졌지만 칠 벤트 및 오버플로우 영역에서 더 높은 금속 온도를 유지했습니다. 이러한 영역의 높은 온도는 숨겨진 가스의 배출을 용이하게 하고 블로우 홀 및 수축 기공과 같은 결함 가능성을 줄이는 데 유리합니다. Model 4는 또한 다른 모델에 비해 더 높은 충진율을 보였습니다(Graph 3.0).
- 시뮬레이션 결과를 바탕으로 Model 4가 금형 제조에 가장 적합한 것으로 선정되었습니다.
- Model 4에 따라 설계된 금형을 사용하여 수행된 실험적 시험 결과, 미충진 결함률이 초기 6.0%에서 1.60%로 크게 감소한 것으로 나타났습니다(Graph 5.0). 검증 배치의 불량 데이터는 Graph 4.0에 표시됩니다.
- 본 연구는 시뮬레이션이 러너 설계 및 공정 매개변수를 최적화하고, 미충진 결함을 효과적으로 줄이며, 시간이 많이 걸리는 수동 시행착오 방법에 대한 의존도를 낮추는 데 유용한 도구라고 결론지었습니다.
그림 이름 목록:
- Graph 1.0 Diecasting defects Pareto analysis
- Fig: 1.0 Nonfilling defect
- Fig: 2.0 The runner design models in four types for the simulation model
- Fig:3.0 Metal flow during Firsr phase
- Fig 4.0 Metal flow during second phase
- Fig 5.0 Metal flow during third phase
- Graph 2.0 The filling time in each model for each cycle in Second phase condition
- Graph 3.0 Fill ratios of the all simulation models
- Graph:4.0 Non filling rejection data
- Graph 5.0 Initial nonfilling and final nonfilling
7. 결론:
시뮬레이션 모델은 모든 다이캐스팅 산업에 적용 가능하며 상당한 비용 절감 효과를 제공할 수 있습니다. 불량으로 인한 낭비 감소가 시뮬레이션 패키지 비용을 상쇄할 수 있기 때문입니다. 고압 다이캐스팅 설계에서의 시뮬레이션은 매우 효과적이며, 강철 주조 시뮬레이션보다 더 효과적일 수 있어 고품질 주물 생산을 가능하게 합니다. 시뮬레이션 소프트웨어가 100% 완벽한 결과를 제공하지는 않지만, 금형 제작자에게 중요한 정보를 제공하여 주요 실수를 피하는 데 도움을 줍니다. 시간, 비용 및 품질 개선을 달성하기 위해 모든 신규 프로젝트에서 금형 유동 시뮬레이션을 필수 활동으로 고려하는 것이 좋습니다. 신규 프로젝트에 시뮬레이션 모델을 활용하면 시간과 비용을 절약하고, 불량 및 기계 고장으로 인한 낭비를 제거하며, 궁극적으로 고객 만족도를 향상시킬 수 있습니다.
8. 참고 문헌:
- [1] Proceedings of the NADCA, “Diecasting defects and design of experiments”, WG. Cleveland, USA Year -1993, Chapter-2 Page: 13-14
- [2] Edward J,Vinarcik, “High Integrity Die-casting processes", Year- 2003.Page: 134-136.
- [3] Genick, Bar-Meir,Minneapolis, “Fundamentals of Die Casting Design", Version: 0.1.2 April 1, 2009, Chapter-1, Page 8-9.
- [4] Hyuk-jae kwon, Hong-kyu Kown, “Computer aided engineering (CAE) simulation for the design optimisation of gate system on high pressure diecasting process (HPDC)”, Elsevier 2018 Page: 149-152
- [5] A J Norwood, P M Dickens*, "Surface temperature of tools during the high-pressure die casting of aluminium", Wolfsan School of Mechanical and Manufacturing Engineering, Loughborough University,UK DOI: 10.1243/09544054JEM745. Year-Aug-2007, Page-1659
- [6] Emil Ragan, Marta Kollarova, "Calculation of Transient Haracterostics in Mould cavity, International journal of Engineering", Tome IX (Year 2011). Fascicule 3. ISSN 1584 – 2673 Page: 1-2.
- [7] Hanxue,chaos shen, chengwang,Hui xui, Direct “Observation of filling Process and Porosity Prediction in High Pressure" Diecasting, Journal name: Materials MPDI 2nd April-2009. Page: 2-9
- [8] M. T. Alonso Rasgado, K. Davey, L. D. Clark and S. Hinduja “Simplified Thermal Stress Analysis "- Department of Mechanical, Aerospace and Manufacturing Engineering UMIST, Manchester, 12TH INTERNATIONAL SCINETIFIC CONFERENCE. Year-2003, Page: 1-2.
- [9] G-Bar Meir, Minnesota The mathematical “Theory of PQ² Diagram", Supercomputing Institute. University of MINNESOTA USA, USMI 99/40 MARCH-1999. Page- 5-6
- [10] John wronowicz, Mike Cox, RexFish,” PQ²- EC-700", July 1998. Page 1-29
9. 저작권:
- 본 자료는 "R.Govindarao and Dr.K.Eshwara Prasad (Rted)"의 논문입니다. "Minimise the Nonfilling defect in the high pressure casting process component for an automotive application with metal flow simulation analysis"를 기반으로 합니다.
- 논문 출처: [논문에 DOI URL이 제공되지 않음]
본 자료는 상기 논문을 바탕으로 요약되었으며, 상업적 목적의 무단 사용을 금지합니다.
Copyright © 2025 CASTMAN. All rights reserved.