본 소개 문서는 "[MDPI]"에서 출판한 논문 "[Automated Defect Detection through Flaw Grading in Non-Destructive Testing Digital X-ray Radiography]"를 기반으로 합니다.
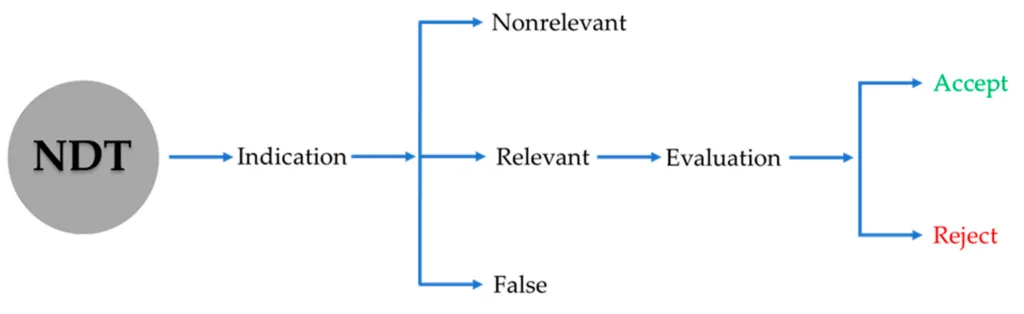
1. 개요:
- 논문 제목: Automated Defect Detection through Flaw Grading in Non-Destructive Testing Digital X-ray Radiography (비파괴 검사 디지털 X선 방사선 촬영에서 결함 등급화를 통한 자동 결함 검출)
- 저자: Bata Hena, Gabriel Ramos, Clemente Ibarra-Castanedo, Xavier Maldague
- 발행 연도: 2024
- 발행 학술지/학회: NDT
- 키워드: 비파괴 검사; 디지털 X선 방사선 촬영; 머신러닝; 자동 결함 인식; 결함 등급화; K-D 트리 (non-destructive testing; digital X-ray radiography; machine learning; automated defect recognition; defect grading; K-D tree)
2. 초록:
공정 자동화는 특화된 기술과 장비를 활용하여 생산 공정을 자동화하고 개선하며, 이를 통해 더 높은 제조 효율성, 생산성 향상 및 비용 절감을 이<0xEB><0x81><0x8A>냅니다. 알루미늄 다이캐스팅 산업은 제조 분야에서 공정 자동화 솔루션 구현을 통해 자동차 및 항공우주 산업과 같은 안전 필수 분야에 부품을 공급하며 상당한 이점을 얻었습니다. 그러나 이 부품 제조 방식은 제조상의 흠(flaw) 발생에 매우 취약하여, 해당 부품의 사용 적합성을 확인하기 위한 적절한 비파괴 검사(NDT)가 필요합니다. 최근 몇 년간 머신러닝은 디지털 X선 방사선 촬영에서 흠을 검출하고 분류하기 위한 자동화 솔루션 개발 도구로서 중심적인 역할을 해왔습니다. 이러한 머신러닝 기반 솔루션은 제조 산업의 높은 생산 처리량을 따라잡기 위해 부품 검사에 점점 더 많이 개발되고 배치되고 있습니다. 본 연구는 검출된 흠이 부품을 사용 부적합하게 만들 수 있는 결함(defect)에 해당하는지를 평가하는 결함 등급화 알고리즘 개발에 중점을 둡니다. ASTM 2973-15 (알루미늄 및 마그네슘 다이캐스팅 검사를 위한 표준 디지털 참조 영상)의 지침에 따라, K-D(k-차원) 트리를 활용한 등급화 파이프라인이 개발되어 검출된 흠을 효과적으로 구조화하고, 시스템이 허용 가능한 등급화 기준에 따라 결정을 내릴 수 있도록 합니다. 이 솔루션은 다양한 등급화 기준에 대한 적합성 측면에서 동적이며, 디지털 X선 방사선 촬영 응용 분야에서 자동화된 의사 결정(합격/불합격) 달성 가능성을 제공합니다.
3. 서론:
공정 자동화는 특화된 기술과 장비를 활용하여 생산 공정을 개선하며, 하드웨어, 소프트웨어, 정보 기술을 결합하여 제조 운영을 관리하고 제어함으로써 더 높은 제조 효율성, 생산성 향상 및 비용 절감을 이<0xEB><0x81><0x8A>냅니다 [1]. 알루미늄 다이캐스팅(ADC) 산업은 제조 분야에서 공정 자동화 솔루션 구현을 통해 상당한 이점을 얻었으며, 자동차 및 항공우주 산업과 같은 분야에 서비스를 제공하는 알루미늄 다이캐스팅 부품의 놀라운 생산 처리량을 달성했습니다 [2]. 이 제조 기술은 용융된 알루미늄 합금을 금형에 주입하고, 금형을 냉각시킨 후 부품을 추출하는 과정을 포함합니다. 이 생산 방식은 관련된 공정 때문에 제조상의 흠 발생에 매우 취약하며, 적절한 모니터링이 필요합니다 [3]. 그럼에도 불구하고, 알루미늄 다이캐스팅(ADC)은 제품의 가벼운 무게, 대량 생산 요구사항에 대한 경쟁력 있는 비용, 높은 생산 처리량, 더 높은 공정 자동화 가능성, 더 나은 제품 일관성 등 다른 제조 공정에 비해 여러 장점을 제공합니다 [4].
제조된 알루미늄 다이캐스팅의 결함이 감지되지 않은 채 방치될 경우 얼마나 위험할 수 있는지를 고려할 때, 요구되는 제조 부품에 대한 적절한 NDT 검사를 수행하는 것이 필수적입니다 [5]. NDT는 다양한 산업에서 중요한 역할을 하며, 부품에 손상을 주거나 기능을 저해하지 않으면서 흠을 검출할 수 있는 다양한 기술을 제공합니다. 일반적인 NDT 기술에는 방사선 촬영, 초음파 검사, 육안 검사, 적외선 열화상 검사, 액체 침투 탐상 검사, 와전류 검사 등이 있습니다 [6]. 연구에 따르면, 방사선 촬영은 알루미늄 다이캐스팅 부품의 품질을 평가하는 데 사용되는 여러 NDT 방법 중 가장 선호되는 방법으로 나타났습니다 [7]. 수 세기 동안 사용된 방사선 촬영 절차는 재료를 투과할 만큼 충분히 높은 강도의 X선 또는 감마선을 사용하여 검사 대상 부품의 전체 부피를 철저히 검사할 수 있게 합니다 [8]. X선은 자연적인 인간 시각으로는 보이지 않으므로, 영상 획득 중 X선 신호에 포함된 잠재 정보를 드러내기 위해 디지털 검출기 어레이(DDA), 광자 계수 검출기, X선 필름 등과 같은 센서를 사용해야 합니다.
디지털 방사선 촬영(DR)은 기존의 필름 방사선 촬영 사용을 점차 대체하고 있습니다. 이 영상 방식에서는 검출기의 민감한 단위(픽셀)에 의해 포착된 X선 광자가 수치 값으로 변환됩니다. 더 나아가, 쉬운 시각적 매력과 인간의 이해를 위해 픽셀 값의 2D 매트릭스가 회색조 분포로 변환되어 디지털 방사선 사진이 형성됩니다. 디지털 방사선 영상은 계산 처리에 유용합니다 [9-12]. 따라서 영상 속성의 다양한 후처리 조정(예: 인지 가능한 대비, 선명도, 밝기)뿐만 아니라 다른 영상 필터링 프로세스가 디지털 방사선 영상으로 가능합니다. DR 시스템의 적절한 성능을 보장하고 NDT에서 디지털 영상의 완전한 통합을 보장하기 위해 관련 표준이 제정되었습니다. NDT 표준을 방사선 검사에 통합하는 것은 다양한 산업 전반에 걸쳐 정확하고 신뢰할 수 있는 검사를 보장하는 데 중요합니다. NDT 표준은 방사선 기법, 노출 매개변수, 영상 품질 및 결과 해석에 대한 필수 지침을 제공합니다. 이러한 표준은 균열이나 개재물과 같은 흠을 탐지하는 것이 안전 및 품질 보증에 중요한 항공우주 및 자동차와 같은 산업에서 널리 적용됩니다. 이러한 표준을 이해하고 준수하는 것은 방사선 검사의 일관성과 신뢰성을 향상시켜 NDT 프로세스의 필수적인 부분을 만듭니다. 미국 기계 학회(ASME), 미국 재료 시험 학회(ASTM), 국제 표준화 기구(ISO)와 같은 기관은 NDT 산업 내 실무 표준화에 대한 규제 감독을 제공합니다. 산업 내 NDT 실무의 이상적인 경우는 NDT 검사관 자격에 대한 운영 NDT 표준(예: ISO 9712)의 요구사항을 만족하는 자격을 갖춘 NDT 검사관에 의해 수행되는 것입니다. 이러한 훈련된 검사관은 관련 운영 NDT 표준에 따라 방사선 영상을 획득하고 해석합니다 [13]. 영상 품질이 허용 가능한 것으로 간주된 후, 검사관은 관련 검출된 지시에 초점을 맞춰 부품의 합격 또는 불합격 여부를 평가하고 결정합니다 (그림 1 참조). NDT 실무에서 잠재적 오류를 방지하기 위한 규정에도 불구하고, NDT 검사관이 인간이기 때문에 오류를 범할 가능성을 배제하는 것은 잘못된 것입니다 [14, 15]. NDT 검사관에 의한 방사선 영상 해석은 피로, 검사 경험, 마음 상태와 같은 요인에 의해 영향을 받을 수 있습니다. 따라서 구조화된 규제 지침 세트를 구현한 후에도 한 연구에서는 시각적 인간 해석의 효과가 약 80%라고 밝혔습니다 [16].
최근 몇 년간 증가하는 계산 능력으로 인해, 비파괴 검사(NDT) 공정을 자동화하려는 아이디어가 구상되고 개발되어, 제조된 부품의 100% 검사를 달성할 수 있는 실행 가능한 경로를 제공합니다. NDT 데이터로부터 흠의 인식 및 평가를 자동화하기 위한 인공 지능(AI) 솔루션 사용은 재료의 방사선 영상에서 흠 식별을 위해 NDT 분야의 많은 연구자들에 의해 널리 탐구된 접근 방식이었습니다 [17]. 이러한 AI 기반 솔루션은 전통적으로 인간 작업자에 의해 수행되었던 작업을 자동화해야 하는 필요성 증가로 인해 요구됩니다 [18]. 공정 자동화 기반 제조 산업에서 NDT에 대한 수요 증가와 이러한 증가하는 검사 요구를 충족시킬 자격을 갖춘 NDT 검사관 수 감소를 고려할 때, 비파괴 검사에서 AI 사용의 필요성은 더욱 명백해집니다 [19]. 컴퓨터 비전 기반 솔루션이 유익할 수 있지만, 안전 필수 분야에서의 수용을 촉진하기 위해 관련 운영 NDT 표준에 따라 개발되고 적용되어야 합니다.
4. 연구 요약:
연구 주제의 배경:
알루미늄 다이캐스팅(ADC) 부품은 제조상의 흠을 가질 가능성이 있으며 [20], 그 대부분은 주조 부품 표면에서는 보이지 않지만 주조 부피 내에 존재할 수 있습니다 [21]. 다이캐스팅 생산 자동화의 기존 능력으로 인해, 산업계는 현재 상당한 생산 처리량을 가지고 있어 시간, 비용 및 검사 작업을 수행할 자격을 갖춘 NDT 인력 부족과 같은 교란 요인의 영향으로 인해 모든 제조된 부품을 테스트하기 어렵습니다. 여러 산업에서는 통계적 접근 방식을 채택하여 제조된 부품의 특정 수량만 검사하지만, 이러한 접근 방식은 모든 제조 부품의 100% 검사보다 열등합니다. 따라서 모든 제조 부품의 100% 검사를 달성하기 위해 컴퓨터 기반 대안을 활용하는 아이디어가 다른 응용 분야에서의 성공 사례로 인해 널리 퍼지게 되었습니다. 다양한 산업에서 알루미늄 다이캐스팅(ADC)을 사용하여 부품을 제조하며, 이는 거의 최종 형상에 가까운 우수한 치수 정밀도를 제공하고 광범위한 2차 가공의 필요성을 최소화합니다 [22]. 특정 알루미늄 다이캐스팅 부품이 사용 중 의도된 기능으로 인해, 이들의 고장은 산업 및 고객에게 상당한 경제적 손실을 야기할 수 있으며 소송 가능성이 있는 영향을 미칠 수 있습니다.
기존 연구 현황:
디지털 X선 방사선 촬영을 이용한 비파괴 검사(NDT)에서의 자동 결함 인식(ADR)은 알루미늄 다이캐스팅의 품질 관리에서 필수적인 구성 요소가 되고 있습니다. 최근 간행물들은 ADR 기술의 중요성을 강조하며, 진화하는 품질 보증 환경에서의 중요성을 강조합니다. 흠 등급화에 초점을 맞춘 우리의 연구는 전략적으로 위치합니다. 단순히 흠을 탐지하고 특성화하는 것에서부터 표준 충족 여부를 결정하기 위해 체계적으로 등급을 매기는 것으로의 전환은 기술 발전과 산업 수용 증대에 중요합니다. 최근 몇 년간 ADR 알고리즘의 발전이 문헌에서 나타났으며, 특히 알루미늄 다이캐스팅과 관련된 산업의 NDT 검사 요구를 계산적으로 해결할 수 있는 솔루션 개발 가능성을 강조합니다. 한 연구[23]에서는 객체 검출 방법(YOLO, RetinaNet, EfficientDet 기반)을 사용하여 알루미늄 주조 결함을 탐지했습니다. 이 연구는 테스트 데이터셋에서 평균 정밀도 0.90과 F1 점수 0.91을 달성한 훈련된 모델로 높은 성능 결과를 보여주었으며, 알루미늄 주물에서 결함을 식별하는 데 있어 인간 작업자를 지원하는 모델의 능력을 입증했습니다. 유사하게, 다른 연구[24]에서는 YOLOv3_darknet53의 백본을 EfficientNet으로 대체한 YOLOv3_EfficientNet 객체 검출 방법을 활용하여 결함 식별에 딥러닝 사용을 조사했습니다. 그들의 연구는 좋은 모델 성능을 보여주었습니다. 컴퓨터 비전과 딥러닝을 사용하여 흠 검출을 간소화하는 데 유사한 성공이 기록되었습니다[25]. 컨볼루션 신경망(CNN)은 이 영역에서 특히 중요한 기능을 수행합니다. 참고문헌 [26]은 방사선 영상에서 결함을 탐지하도록 설계된 매우 효율적인 CNN 모델을 소개했습니다. 그들은 탐지 정밀도를 향상시키기 위한 신경망 아키텍처의 지속적인 개선의 중요성을 입증했습니다. 종합적으로, 이러한 연구들은 ADR 시스템의 성능을 향상시키기 위해 정교한 계산 방법과 딥러닝 활용을 향한 상당한 추세를 보여줍니다.
그럼에도 불구하고, 이러한 발전에도 불구하고 여러 장애물과 제약이 계속 존재합니다. 복잡한 결함 형상과 다양한 방사선 조건은 종종 기존 알고리즘에 대한 도전 과제이며, 이는 [26]에서 논의되었습니다. 이는 딥러닝 모델이 다양한 흠 유형과 주조 조건에 걸쳐 효과적으로 일반화하는 데 필요한 광범위한 훈련 데이터에 의해 더욱 악화되며, 이 점은 [23]에서 제기되었습니다. 또한, [25]의 저자들은 고급 CNN의 높은 계산 요구 사항이 실시간 산업 응용에 상당한 장애물을 제시한다고 관찰했습니다. 따라서 그들은 이미지 수준 레이블을 사용하여 작은 주조 흠을 탐지하기 위한 효율적인 CNN 모델을 제안했습니다. 그들의 연구는 결함 탐지 능력을 향상시키기 위해 이중 선형 풀링(bilinear pooling)과 함께 객체 수준 주의 메커니즘을 활용했습니다.
흠 식별 및 특성화에서 상당한 진전이 이루어졌지만, 결함 등급화는 덜 연구되었지만 중요한 분야로 남아 있습니다. 정확한 등급화는 검출된 흠의 심각성과 영향을 결정하는 데 중요하며, 이는 결국 테스트 중인 주물의 사용 적합성을 결정합니다. 흠을 정밀하게 등급화하는 능력은 생산자가 심각성과 제품 성능에 대한 잠재적 영향에 따라 이를 분류할 수 있게 하여, 자동차 및 항공우주 부품과 같은 필수 응용 분야에 사용되는 알루미늄 주물의 신뢰성과 안전성을 향상시킵니다. 기존 ADR 시스템에 결함 등급화를 통합하면 품질 보증에 대한 보다 완전한 접근 방식이 가능합니다. 제조업체는 탐지, 특성화 및 등급화를 결합하여 제조 공정에 대한 포괄적인 이해를 얻을 수 있으며, 이는 더 높은 제품 품질과 폐기물 감소로 이어집니다. 이러한 포괄적인 접근 방식은 현재 문헌에서 발견되는 연구 격차를 고려할 때 특히 중요합니다. 우리의 연구는 기존 흠 인식 솔루션의 탐지 및 특성화 능력을 계승하는 새로운 흠 등급화 방법론을 제시함으로써 이 격차를 메우고자 합니다. 이 돌파구는 오류 발견과 그 실제적 영향 이해 사이의 간극을 좁혀 알루미늄 다이캐스팅의 품질 관리를 위한 강력한 프레임워크를 제공할 것으로 예상됩니다.
이 격차를 메움으로써, 우리의 논문은 ADR 기술의 발전에 기여하여 알루미늄 주물이 최고의 품질 및 신뢰성 기준을 만족하도록 보장하는 것을 목표로 합니다. 이 연구는 ADR 시스템의 지속적인 혁신 필요성과 이러한 시스템에 결함 등급화를 통합하는 것의 잠재적 영향을 강조합니다.
연구 목적:
본 연구는 ADR의 격차를 메우기 위해 포괄적인 흠 등급화 알고리즘 개발을 목표로 합니다. 목적은 다음과 같습니다:
- 탐지된 흠을 참조 표준(예: ASTM E2973-15) 또는 고객 사양에 맞춰 여러 심각도 수준으로 분류하는 등급화 알고리즘 개발.
- 단순 탐지를 넘어 자격 있는 등급화로 나아가는 방법을 제안함으로써 안전 필수 분야에서 ADR 솔루션 통합 강화.
- 등급화 과정에서 결정론적 결과를 산출하여 정확성과 해석 가능성을 향상시키는 컴퓨터 비전 기술 구현.
동기는 NDT 표준(특히 ASTM E2973-15 및 ASTM E1316의 용어)에 기반한 체계적인 접근 방식을 제공하여 탐지된 흠(결점)을 평가하고 그것이 거부 가능한 결함(defect)을 구성하는지 결정함으로써 알루미늄 다이캐스팅의 품질 관리를 개선하는 것입니다.
핵심 연구:
이 연구의 핵심은 알루미늄 및 마그네슘 다이캐스팅의 디지털 X선 방사선 촬영 영상에 대한 새로운 흠 등급화 방법론의 개발 및 적용입니다. 이 방법론은 다른 알고리즘에 의해 수행되는 초기 탐지 및 특성화 단계를 따릅니다. 이는 특히 ASTM E2973-15 표준(기공, 콜드 필, 수축 및 이물질과 같은 불연속성의 다양한 심각도 수준에 대한 디지털 참조 영상 제공 [27])에 의해 주로 안내되는 확립된 기준에 따라 탐지된 흠을 등급화하는 데 중점을 둡니다.
이 연구는 ASTM E1316에 정의된 중요한 구분을 강조합니다:
- 불연속성(Discontinuity): 재료 구조의 중단.
- 흠(Flaw): 탐지 가능하지만 반드시 거부 가능하지는 않은 결점 또는 불연속성.
- 결함(Defect): 그 특성(크기, 모양, 위치 등)이 지정된 허용 기준을 위반하여 부품을 거부 가능하게 만드는 하나 이상의 흠.
개발된 알고리즘은 탐지되고 특성화된 흠(일반적으로 분할 마스크 형태의 입력으로 제공됨)을 받아 표준(또는 사용자 정의 기준)에서 파생된 등급화 규칙에 따라 평가하여 결함에 해당하는지 판단하고, 궁극적으로 합격/불합격 결정을 내립니다. 등급화 프로세스는 정의된 평가 영역(ASTM E2973에 따라 700mm²) 내에서 흠 면적 및 수량과 같은 흠 속성을 고려합니다. 방법론의 핵심 구성 요소는 탐지된 흠의 효율적인 공간 구성 및 질의를 위한 K-D 트리 데이터 구조의 사용입니다.
5. 연구 방법론
연구 설계:
본 연구는 흠 탐지, 분할 및 특성화 단계를 따르는 독립적인 파이프라인으로 의도된 흠 등급화 알고리즘을 설계합니다. 입력은 고유한 흠과 그 클래스를 식별하는 분할 마스크로 가정합니다. 출력은 등급화에 기반한 합격/불합격 결정입니다. 등급화 로직은 ASTM E2973-15 표준에서 파생된 규칙에 기반하며, 네 가지 흠 범주(기공, 수축, 콜드 필, 이물질)에 중점을 둡니다.
주요 방법론 단계는 다음과 같습니다:
- 입력 처리: 입력 영상에서 다른 흠 클래스를 식별할 수 있는 분할된 영상 수신 (예: 연구의 합성 데이터 생성에서 수행된 색상 코딩 - 그림 3, 표 1 참조).
- 클래스 분리: 입력 영상에 존재하는 각 흠 클래스에 대한 이진 마스크 생성.
- 흠 속성 추출: 각 클래스별 이진 마스크에 대해 영상 분석 라이브러리(
skimage.measure.regionprops
)를 사용하여 개별 흠의 속성(예: 면적) 추출. - 공간 인덱싱: 효율적인 공간 질의를 위해 탐지된 흠의 중심점을 사용하여 K-D(k-차원) 트리 구축 [32, 33]. 이는 특정 관심 영역(ROI) 내의 흠을 신속하게 검색하는 것을 용이하게 합니다.
- ROI 관리 및 반복: ROI(700mm² 평가 영역) 정의를 위해 슬라이딩 윈도우 접근 방식 사용. K-D 트리와 함께 "스트라이드 함수"를 사용하여 영상을 효율적으로 탐색하고, ROI를 흠이 포함된 다음 영역으로 동적으로 이동시켜 빈 영역 처리를 피합니다.
- 등급화 로직 적용: 각 ROI 내에서, ROI 내의 흠을 검색하기 위해 K-D 트리를 질의하고, 정의된 심각도 수준 기준에 대해 크기(면적)와 수량을 평가하여 등급화 규칙(ASTM E2973 용어에서 파생된 표 2 기반) 적용.
- 결정 집계 및 보고: 모든 ROI에 걸쳐 등급화 결과를 집계하고, 잠재적으로 시각화(예: 등급화 맵)와 함께 최종 보고서 생성. 전체 방법론은 그림 5에 개략적으로 설명되어 있습니다. K-D 트리는 이 응용 프로그램의 2D 공간 컨텍스트에서 효율성과 복잡성의 균형 때문에 R-트리[34]와 같은 대안보다 선택되었습니다.
데이터 수집 및 분석 방법:
등급화 파이프라인을 테스트하고 검증하기 위해 테스트 이미지를 합성적으로 생성했습니다. 네 가지 클래스(기공, 수축, 콜드 필, 이물질)에 대해 다양한 크기와 형태를 가진 실제 흠(알루미늄 다이캐스팅 부품의 실제 주석에서 추출)을 추출하여 흠 저장소를 형성했습니다. 그런 다음 이 추출된 흠들을 배경 이미지 위에 무작위로 배치했습니다. 각 흠 클래스에는 후속 처리 단계에서 식별을 위해 고유한 색상 코드가 할당되었습니다(표 1). (그림 4a는 생성된 흠을 보여주고, 4b는 색상 코딩된 분류를 보여줍니다). 이 합성 접근 방식을 통해 다양한 흠 분포를 가진 다양한 데이터셋을 생성할 수 있었습니다.
ASTM E2973-15 표준은 참조 이미지를 사용합니다(예: 기공의 경우 그림 2). 계산 적용을 위해 이러한 시각적 참조는 700mm² 검사 영역 내의 흠 면적과 수량을 기반으로 한 정량적 디지털 메트릭(등급화 규칙)으로 변환되었습니다. 흠 면적 범위와 700mm²당 최대 수량을 기반으로 심각도 등급(1~4)을 정의하는 사용자 정의 참조 표(표 2)가 연구에 사용되었습니다. skimage.measure.regionprops
라이브러리는 이진 마스크에서 탐지된 흠(블롭)의 기하학적 속성(예: 면적)을 추출하는 데 사용되었습니다. K-D 트리는 흠 중심점을 공간적으로 구성하여 효율적인 분석을 가능하게 했습니다.
연구 주제 및 범위:
이 연구는 알루미늄 및 마그네슘 다이캐스팅의 디지털 X선 방사선 촬영 영상에서 탐지된 흠의 자동 등급화에 중점을 둡니다. 범위는 ASTM E2973-15에 정의된 네 가지 불연속성 범주(기공, 수축, 콜드 필, 이물질)로 제한됩니다. 핵심 작업은 이 표준(또는 사용자 정의 가능한 고객 기준)에서 파생된 기준에 따라 탐지된 흠을 평가하여 거부 가능한 결함에 해당하는지 여부를 결정하는 것입니다. 방법론은 2D 방사선 영상을 처리하고, 흠 특성을 추출하고, 정의된 평가 영역(700mm²) 내에서 효율적인 공간 분석을 위해 K-D 트리를 활용하고, 흠 크기와 수량에 기반한 특정 등급화 규칙을 적용하는 것을 포함합니다. 이 연구는 흠의 사전 탐지 및 분류를 가정하고 등급화 알고리즘 자체를 개발합니다.
6. 주요 결과:
주요 결과:
개발된 등급화 파이프라인의 주요 출력은 처리된 입력 영상 위에 활성화된 관심 영역(ROI)의 오버레이로 표시되며, 이는 이 연구에서 활용된 참조 조건을 충족하는 흠 분포를 가진 영상에 등급화 규칙이 적용된 위치를 보여줍니다 (그림 6). 결과는 더 나은 시각화와 쉬운 인간 검증을 위해 흠 클래스별로 별도로 표시됩니다 (기공 - 행 a, 수축 - 행 b, 콜드 필 - 행 c, 이물질 - 행 d).
네 가지 심각도 수준(등급 1~4)이 고려되며, 각 수준에는 식별을 위해 고유한 ROI 색상이 할당됩니다:
- 등급 1: 파란색
- 등급 2: 녹색
- 등급 3: 주황색
- 등급 4: 갈색
등급화는 사용자 정의 참조(표 2)에 정의된 기준에 따라 수행되며, 참조 문서에 문서화된 대로 입력 영상의 700mm² 단위 면적당 적용됩니다. 다른 심각도 수준에 해당하는 여러 활성화된 ROI가 겹칠 경우, 더 높은 심각도 수준과 관련된 ROI가 시각화에서 우선권을 갖습니다. 사용된 참조 조건(표 2)에 따라, 이물질 클래스가 탐지되면 자동으로 등급 4(갈색 ROI) 분류로 이어집니다. 그림 6의 열은 흠 클래스에 기반한 격리된 흠 클래스(i), 분석 중 생성된 경계 상자(ii), 평가된 영역 전반에 걸쳐 심각도 수준을 나타내는 최종 강조 표시된 등급화 맵(iii)을 보여줍니다.
그림 이름 목록:
- Figure 1. ASTM E1316-22a에 따른 NDT의 공정 흐름.
- Figure 2. 기공 흠의 시각화를 향상시킨 ASTM 2973의 등급화 참조; 심각도 증가 순서(1에서 4)로 배열됨.
- Figure 3. 실제 흠을 사용하여 입력 이미지를 생성하는 워크플로우, 각 흠은 네 가지 고유 클래스를 구별하기 위해 색상 코딩됨.
- Figure 4. (a) 생성된 흠의 무작위 분포를 가진 이미지; (b) 흠을 4개의 고유 색상 코드로 무작위 분류한 것을 보여줌. 원본 이미지 크기는 3098 × 3097 픽셀.
- Figure 5. 제안된 결함 등급화 방법론의 개략도.
- Figure 6. 행 (a-d)는 각각 기공, 수축, 콜드 필, 이물질을 나타냄; 열 (i-iii)은 흠 클래스 기반의 격리된 흠 클래스, 경계 상자 및 강조 표시된 경계 상자를 보여줌. 경계 상자 색상은 등급을 나타냄: 등급 1 (파란색), 등급 2 (녹색), 등급 3 (주황색), 등급 4 (갈색).
7. 결론:
본 연구는 흠과 결함 간의 중요한 구분을 강조하여 결함 검출을 재검토합니다. 흠 검출 알고리즘에 견고한 등급화 시스템을 통합함으로써, 다이캐스팅의 디지털 방사선 영상에서 탐지된 흠으로부터 진정한 결함을 식별하기 위한 상세하고 신뢰할 수 있으며 적응 가능한 접근 방식을 제공합니다. 제안된 방법은 ASTM E1316에 요약된 평가 프로세스를 분리하여, 업계에서 사용되는 확립된 비파괴 검사(NDT) 표준에 따라 관련 흠을 등급화하여 결함의 존재 또는 부재에 대한 정보에 입각한 결정을 내리는 데 중점을 둡니다.
이 연구에서 제안된 등급화 파이프라인은 검사 프로세스의 효율성과 정확성을 향상시킬 뿐만 아니라, 제조된 부품의 방사선 평가에서 의사 결정 및 품질 관리를 완전히 자동화하기 위한 경로를 제공합니다. 이 방법을 기존 NDT 워크플로우에 원활하게 통합함으로써, 산업계는 결함 등급화의 정확성과 신뢰성을 유지하거나 향상시키면서 검사 시간과 비용을 크게 절감할 수 있습니다. 이 전략은 결함 등급화에서 운영 NDT 표준 준수의 중요성을 강조하여, 부품의 사용 적합성을 손상시킬 가능성이 있는 흠(또는 흠 그룹)만이 합의된 표준에 따라 결함으로 분류되도록 보장합니다. 이 솔루션은 이 분야에서 상당한 진전을 나타내며, 다양한 산업에 적용 가능한 다목적의 적응형 도구를 제공합니다.
향후 연구에서는 제안된 등급화 알고리즘을 컴퓨터 단층 촬영 영상과 같은 체적 영상의 3D 응용 프로그램에 통합하도록 업그레이드하는 것을 탐색할 수 있습니다. 또한, 머신러닝 기반 기술을 통합하여 등급화 기준을 더욱 정교화하면 제안된 접근 방식의 적용 가능성을 다양화하여 더 높은 정확성을 가능하게 할 수 있습니다. 이러한 방향은 제안된 접근 방식의 범위를 넓혀 차세대 자동화 NDT 디지털 방사선 촬영 솔루션에서의 역할을 공고히 할 수 있습니다.
8. 참고 문헌:
- [References] (참고 문헌 목록은 원문 영어 그대로 유지됩니다.)
- [1] Hahn, J.; Bequette, B.W. Process Automation. In Springer Handbook of Automation; Nof, S.Y., Ed.; Springer International Publishing: Cham, Switzerland, 2023; pp. 585–600. ISBN 978-3-030-96729-1.
- [2] Perzyk, M.; Dybowski, B.; Kozłowski, J. Introducing Advanced Data Analytics in Perspective of Industry 4.0 in a Die Casting Foundry. Arch. Foundry Eng. 2019, 19, 53-57. [CrossRef]
- [3] Fiorese, E.; Bonollo, F.; Timelli, G.; Arnberg, L.; Gariboldi, E. New Classification of Defects and Imperfections for Aluminum Alloy Castings. Int. J. Met. 2015, 9, 55-66. [CrossRef]
- [4] Sigworth, G. Aluminum Casting Alloys and Casting Processes. In Aluminum Science and Technology; ASM International: Almere, The Netherlands, 2018; ISBN 978-1-62708-207-5.
- [5] Ferguson, M.; Ak, R.; Lee, Y.-T.T.; Law, K.H. Detection and Segmentation of Manufacturing Defects with Convolutional Neural Networks and Transfer Learning. arXiv 2018, arXiv:1808.02518. [CrossRef] [PubMed]
- [6] Silva, M.I.; Malitckii, E.; Santos, T.G.; Vilaça, P. Review of Conventional and Advanced Non-Destructive Testing Techniques for Detection and Characterization of Small-Scale Defects. Prog. Mater. Sci. 2023, 138, 101155. [CrossRef]
- [7] Wilczek, A.; Długosz, P.; Hebda, M. Porosity Characterization of Aluminium Castings by Using Particular Non-Destructive Techniques. J. Nondestruct. Eval. 2015, 34, 26. [CrossRef]
- [8] Dwivedi, S.K.; Vishwakarma, M.; Soni, P.A. Advances and Researches on Non Destructive Testing: A Review. Mater. Today Proc. 2018, 5, 3690-3698. [CrossRef]
- [9] Körner, M.; Weber, C.H.; Wirth, S.; Pfeifer, K.-J.; Reiser, M.F.; Treitl, M. Advances in Digital Radiography: Physical Principles and System Overview. Radiographics 2007, 27, 675-686. [CrossRef]
- [10] de Carvalho, A.A.; Suita, R.C.d.S.B.; Silva, R.R.d.; Rebello, J.M.A. Evaluation of the Relevant Features of Welding Defects in Radiographic Inspection. Mat. Res. 2003, 6, 427-432. [CrossRef]
- [11] Aryan, P.; Sampath, S.; Sohn, H. An Overview of Non-Destructive Testing Methods for Integrated Circuit Packaging Inspection. Sensors 2018, 18, 1981. [CrossRef]
- [12] Wang, B.; Zhong, S.; Lee, T.-L.; Fancey, K.S.; Mi, J. Non-Destructive Testing and Evaluation of Composite Materials/Structures: A State-of-the-Art Review. Adv. Mech. Eng. 2020, 12, 168781402091376. [CrossRef]
- [13] Ulus, Ö.; Davarcı, F.E.; Gültekin, E.E. Non-Destructive Testing Methods Commonly Used in Aviation. Int. J. Aeronaut. Astronaut. 2024, 5, 10-22. [CrossRef]
- [14] Dobrzański, L.A.; Krupinski, M.; Sokolowski, J.H. Computer Aided Classification of Flaws Occurred during Casting of Aluminum. J. Mater. Process. Technol. 2005, 167, 456–462. [CrossRef]
- [15] Wu, B.; Zhou, J.; Ji, X.; Yin, Y.; Shen, X. Research on Approaches for Computer Aided Detection of Casting Defects in X-Ray Images with Feature Engineering and Machine Learning. Procedia Manuf. 2019, 37, 394-401. [CrossRef]
- [16] Hou, W.; Zhang, D.; Wei, Y.; Guo, J.; Zhang, X. Review on Computer Aided Weld Defect Detection from Radiography Images. Appl. Sci. 2020, 10, 1878. [CrossRef]
- [17] Yu, H.; Li, X.; Song, K.; Shang, E.; Liu, H.; Yan, Y. Adaptive Depth and Receptive Field Selection Network for Defect Semantic Segmentation on Castings X-Rays. NDT E Int. 2020, 116, 102345. [CrossRef]
- [18] Vrana, J.; Singh, R. NDE 4.0—A Design Thinking Perspective. J. Nondestruct. Eval. 2021, 40, 8. [CrossRef]
- [19] Dobmann, G. Quo Vadis NDT?-A Forecast of the Future. BNiD 2020, 5, 6-17. [CrossRef]
- [20] Min, C.; Yi, W.; Jigui, Z.; Jiang, F.; Jianjun, M. Simulation and Optimization of Casting Process for Aluminum Alloy Special-Shaped Parts. J. Phys. Conf. Ser. 2021, 1986, 012018. [CrossRef]
- [21] Samuel, A.M.; Samuel, E.; Songmene, V.; Samuel, F.H. A Review on Porosity Formation in Aluminum-Based Alloys. Materials 2023, 16, 2047. [CrossRef]
- [22] Itamura, M.; Anzai, K.; Hirata, N.; Akahoshi, N.; Maeda, T.; Tanazawa, H.; Furuya, Y.; Fukuoka, S.; Yamamoto, N. Development of Aluminum Die Casting Products with High Accuracy as Well as Superior Die-to-Casting Transcriptional Capability by Using Semi-Solid Method. In Proceedings of the Semi-Solid Processing of Alloys and Composites XII; Trans Tech Publications Ltd.: Stafa-Zurich, Switzerland, 2013; Volume 192, pp. 447-453.
- [23] Mery, D. Aluminum Casting Inspection Using Deep Object Detection Methods and Simulated Ellipsoidal Defects. Mach. Vis. Appl. 2021, 32, 72. [CrossRef]
- [24] Xue, L.; Hei, J.; Wang, Y.; Li, Q.; Lu, Y.; Liu, W. A High Efficiency Deep Learning Method for the X-Ray Image Defect Detection of Casting Parts. Meas. Sci. Technol. 2022, 33, 095015. [CrossRef]
- [25] Hu, C.; Wang, Y. An Efficient Convolutional Neural Network Model Based on Object-Level Attention Mechanism for Casting Defect Detection on Radiography Images. IEEE Trans. Ind. Electron. 2020, 67, 10922–10930. [CrossRef]
- [26] Tang, J.; Liu, S.; Zhao, D.; Tang, L.; Zou, W.; Zheng, B. An Algorithm for Real-Time Aluminum Profile Surface Defects Detection Based on Lightweight Network Structure. Metals 2023, 13, 507. [CrossRef]
- [27] Mizgan, H.; Ganea, M. Optimization of Aluminium Die-Casting Process through Predictive Maintenance and Parameter Traceability Systems. IOP Conf. Ser. Mater. Sci. Eng. 2022, 1256, 012028. [CrossRef]
- [28] Zhang, J.; Guo, Z.; Jiao, T.; Wang, M. Defect Detection of Aluminum Alloy Wheels in Radiography Images Using Adaptive Threshold and Morphological Reconstruction. Appl. Sci. 2018, 8, 2365. [CrossRef]
- [29] Mery, D.; Filbert, D. Automated Flaw Detection in Aluminum Castings Based on the Tracking of Potential Defects in a Radioscopic Image Sequence. IEEE Trans. Robot. Automat. 2002, 18, 890–901. [CrossRef]
- [30] Koshti, A.M. Using Requirements on Merit Ratios for Assessing Reliability of NDE Flaw Detection in Multi-Hit Detection in Digital Radiography. In Proceedings of the Health Monitoring of Structural and Biological Systems XV; Fromme, P., Su, Z., Eds.; SPIE: St Bellingham, WA, USA, 2021; Volume 11593, p. 115932K.
- [31] Yahaghi, E.; Mirzapour, M.; Movafeghi, A.; Rokrok, B. Interlaced Bilateral Filtering and Wavelet Thresholding for Flaw Detection in the Radiography of Weldments. Eur. Phys. J. Plus 2020, 135, 42. [CrossRef]
- [32] Friedman, J.H.; Bentley, J.L.; Finkel, R.A. An Algorithm for Finding Best Matches in Logarithmic Expected Time. ACM Trans. Math. Softw. 1977, 3, 209-226. [CrossRef]
- [33] Bentley, J.L. Multidimensional Binary Search Trees Used for Associative Searching. Commun. ACM 1975, 18, 509-517. [CrossRef]
- [34] Guttman, A. R-Trees: A Dynamic Index Structure for Spatial Searching. In Proceedings of the ACM SIGMOD Conference, Boston, MA, USA, 18-21 June 1984.
9. 저작권:
- 이 자료는 "[Bata Hena, Gabriel Ramos, Clemente Ibarra-Castanedo, Xavier Maldague]"의 논문입니다. "[Automated Defect Detection through Flaw Grading in Non-Destructive Testing Digital X-ray Radiography]"를 기반으로 합니다.
- 논문 출처: [https://doi.org/10.3390/ndt2040023]
이 자료는 상기 논문을 바탕으로 요약되었으며, 상업적 목적의 무단 사용을 금지합니다.
Copyright © 2025 CASTMAN. All rights reserved.