本紹介資料は、「Journal of Magnesium and Alloys」に掲載された論文「Progress and prospects in Mg-alloy super-sized high pressure die casting for automotive structural components」に基づいています。
![Fig. 1. Mg-alloy super-sized die casting produced by Chongqing University, Millison Inc. and Boao Magnesium Aluminium Manufacturing Company Ltd. The geometry of the Mg-alloy super-sized castings has been withheld due to commercial confidentiality [5].](https://castman.co.kr/wp-content/uploads/image-2011-png.webp)
1. 概要:
- 論文タイトル: Progress and prospects in Mg-alloy super-sized high pressure die casting for automotive structural components (マグネシウム合金製超大型高圧ダイカスト自動車構造部品の進歩と展望)
- 著者: Tian Li, Jiangfeng Song, Ang Zhang, Guoqiang You, Yan Yang, Bin Jiang, XianYue Qin, Cheng Xu, Fushen Pan
- 発行年: 2023
- 掲載学術誌/学会: Journal of Magnesium and Alloys
- キーワード: Mg 合金 (Mg alloy); ギガキャスティング (Giga-casting); 高圧ダイカスト (HPDC); 超大型 (Super-sized).
2. 抄録:
Teslaのギガキャスティング(Giga-Casting)プロセスの導入以来、自動車産業では、電気自動車および内燃機関自動車の両方の軽量化を促進する大きな可能性から、超大型構造部品のコンセプトが広く受け入れられています。これらの超大型部品は、アルミニウム合金の3分の2、鋼鉄の4分の1の密度しかない優れた軽量特性を持つMg合金を使用することで、さらに軽量化できます。この卓越した特性は、構造的完全性を損なうことなく大幅な重量削減を達成するという魅力的な展望を提供します。本レビューは、Mg合金高圧ダイカスト(HPDC)プロセスに関する研究を検討し、Mg合金を超大型自動車HPDC部品に組み込む将来の展望についての洞察を提供します。
3. 緒言:
気候変動とその悪影響に対する懸念が高まる中、世界各国は温室効果ガス排出という重大な問題に対処するための取り組みを強化しています。政策立案者は、特に電気自動車(EV)の普及促進に焦点を当て、包括的なCO2排出政策の実施に注目しています。しかし、EVは、従来の燃焼エンジンと比較してEVバッテリーの重量が大幅に増加しているため、同様のサイズのICE車と比較して、数百から数千キログラムの大きな重量差を示すことがあります。その結果、車両の軽量化は、環境性能の向上と性能向上の両方を可能にするため、将来の自動車産業にとって極めて重要です。自動車の軽量化の分野で、最近の最も画期的な進歩の1つは、Teslaのギガキャスティング技術[1]です。この先進的な高圧ダイカスト(HPDC)技術により、EV構造用の超大型一体部品の製造が可能になります。この革新的なアプローチを採用することで、Teslaは171個の複雑な車両部品を、フロントとリアのアンダーボディというわずか2つの鋳造品に統合しました。これにより、30%の驚異的な重量削減と40%の印象的なコスト削減が実現し、EVの効率と性能を向上させるための競争力のあるソリューションとなっています[1]。ギガキャスティングの成功は世界的に大きな注目を集め、自動車産業が超大型構造部品を採用し、従来の車体およびシャシー要素の数を大幅に削減するきっかけとなりました。一方、現在の超大型自動車部品の代替材料の調査を通じて、より高度な軽量化技術の追求への関心が高まっており、特にMg合金に焦点が当てられています。地球上で最も軽い構造材料として知られるMg合金は、アルミニウム合金のわずか3分の2、鋼鉄の4分の1の密度しか示しません。この卓越した重量対強度比により、Mg合金は構造的完全性を損なうことなく大幅な重量削減を達成するための非常に有望な選択肢として位置づけられています。Mg合金の探求は、効果的で革新的な軽量化ソリューションを求める自動車産業の探求を推進する上で大きな可能性を秘めています。2023年6月に発表された革新的な成果[5]として、重慶大学の国家マグネシウム合金工学研究センター(CCMg)は、Chongqing Millison Technologies Inc.およびChongqing Boao Magnesium Aluminium Manufacturing Company Ltdと協力し、Millisonの8800Tギガプレスマシンを使用して、世界最大のMg合金自動車ダイカスト部品の試作に成功しました。図1に示すように、リアアンダーボディとバッテリーエンクロージャー用アッパーカバーという2つの超大型ボディインホワイト(BIW)部品が鋳造され、両部品の投影面積は2.2 m²を超え、現在入手可能な最大のMg合金自動車HPDC部品としての地位を確立しました。Al合金鋳造品と比較して32%の顕著な軽量化を実現したこれらのMg合金超大型鋳造品は、自動車産業における軽量化用途に大きな可能性を示しています。この可能性に基づき、本研究は、大型で薄肉の自動車構造部品向けのMg合金HPDCプロセスに関して行われた調査のレビューを提示することを目的としています。Mg合金、溶湯処理、酸化物関連欠陥、ホットティア、現在のMg合金超大型製品などのトピックをカバーし、超大型自動車HPDC部品の製造にMg合金を利用する際の重要な側面を探求し、超大型自動車部品の軽量特性を向上させる有望な手段としてのMg合金の実現可能性についての洞察を提供します。
4. 研究の概要:
研究テーマの背景:
自動車産業は、特に重量が増加するEVの普及に伴い、効率改善と環境性能向上のために車両重量を削減する必要に迫られています。Teslaのギガキャスティングに代表される超大型構造部品は、Al合金を用いて部品統合、コスト削減、軽量化を実現する道筋を示しています。Mg合金のようなより軽量な材料を探求することで、さらなる重量削減が可能です。
従来の研究状況:
Al合金を用いたギガキャスティングは自動車産業で確立されつつあります[1, 2, 3, 4]。自動車用途のMg合金に関する研究では、大型構造部品に適した非熱処理(NHT)形態で、鋳造性や延性などの望ましい特性を持つ適切な合金系(例:AM、AZ、AJ、AEシリーズ)が特定されています[6-11]。合金元素(Al、Si、Zn、Sr、Ca、RE)がMgの特性に及ぼす影響に関する研究が行われています[12-40]。溶湯処理技術(脱ガス、フラックス精錬、電磁・超音波・浮遊選鉱・濾過などの非フラックス精錬)は、Mg合金鋳造品の品質にとって重要であることが知られています[41-78]。Mg HPDCにおける一般的な欠陥、例えばダイソルダリング(Alよりは軽微)、酸化物介在物/バイフィルム、ホットティアなどが研究されています[79-132]。鋳造品の健全性を向上させるために、真空HPDC(VADC/SVDC)やVACURALなどの先進的な鋳造技術が使用されています[135-146]。大型Mg合金鋳造品の試作成功例も報告されています[5, 図8]。
研究の目的:
本レビューは、大型・薄肉の自動車構造部品に特化したMg合金高圧ダイカスト(HPDC)プロセスに関する既存の研究を検討することを目的としています。Mg合金を超大型自動車HPDC部品に組み込むことの実現可能性、利点、課題、および将来の展望についての洞察を提供することを目指しています。
研究の核心:
本論文は、Mg合金超大型HPDCに関連するいくつかの主要な領域をレビューします:
- 適切なMg合金: 大型・薄肉のNHT構造部品に関連する特性(鋳造性、流動性、延性、耐クリープ性など)に焦点を当て、様々なMg合金系(Mg-Al-Si、Mg-Al-Zn、Mg-Al-Sr、Ca含有、Mg-Al-RE)について議論します[12-40]。
- 溶湯処理: 脱ガス技術(不活性ガススパージング、活性ガス、真空)および介在物除去方法(フラックス精錬、電磁・超音波・気泡浮遊・濾過などの非フラックス精錬)を含む、鋳造前のMg合金溶湯処理の必要性と方法をカバーします[41-78]。
- 主要欠陥: Mg合金HPDCで遭遇する一般的な欠陥、すなわちダイソルダリング(Al合金との比較)、Mgの反応性と鋳造乱流による酸化物介在物およびバイフィルムの形成、ホットティア現象(合金組成と鋳造条件の影響)を分析します[79-132]。
- 鋳造装置/技術: 大型Mg部品用HPDCマシンの要件(Al部品と比較して低い型締力が必要となる可能性を含む)、および鋳造品質の向上を目的とした真空/超真空HPDC(VADC/SVDC)やVACURAL技術などの先進プロセスをレビューします[2, 133-146]。
- 現在の応用と可能性: 様々な自動車部品におけるMg合金HPDCの既存の応用例と、アンダーボディやバッテリーエンクロージャーなどの超大型Mg鋳造品の最近の開発状況を示し、実証された可能性を強調します[5, 17, 40, 133, 136, 147-152]。
5. 研究方法論
研究デザイン:
本研究は包括的な文献レビューです。科学論文、技術報告書、業界出版物から得られた既存の知識を統合し、評価します。
データ収集・分析方法:
著者は、Journal of Magnesium and Alloys、Materials Science and Engineering A、Metallurgical and Materials Transactionsなどの査読付きジャーナル、会議議事録、SAE Technical Papersなどの技術論文、特許、ハンドブックを含む広範な出版物から情報を収集しました。分析には、主要な発見の要約、傾向と相関関係の特定(例:合金組成 vs. 特性/欠陥)、異なるプロセスと材料の比較、課題の強調、収集された証拠に基づく技術の全体的な進歩と将来の可能性の評価が含まれます。
研究テーマと範囲:
本研究は、超大型自動車構造部品を製造するためのマグネシウム(Mg)合金への高圧ダイカスト(HPDC)技術の応用に特化しています。範囲は以下の通りです:
- 適切なMg合金の選択基準と特性(NHT、鋳造性、延性)。
- Mg合金に不可欠な溶湯準備技術(脱ガス、精錬)。
- Mg HPDCに関連する主要な鋳造欠陥(ダイソルダリング、酸化物/バイフィルム、ホットティア)の分析とその軽減策。
- 鋳造装置と先進的なHPDCプロセスバリエーション(大型プレス、真空アシスト、VACURAL)の評価。
- 自動車構造物、特に大規模なものにおけるMg合金HPDCの現在および新興の応用例のレビュー。
6. 主要な結果:
主要な結果:
- Mg合金は、はるかに低い密度により、Al合金と比較して超大型自動車部品の大幅な軽量化の可能性を提供します(例:32%の削減が報告されています[5])。
- Mg合金はHPDCにおいて優れた金型充填能力を示し、薄肉(最小1.8mm)で長い充填距離(最大1.2m)を持つ非常に大きな部品の製造を可能にします[図8, 150]。
- AE44のような合金は、流動性、強度、延性の良好なバランスにより、構造部品として有望です[39, 150, 図7]。非熱処理(NHT)合金は大型構造部品に好まれます。
- Mgの高い反応性と水素吸収感受性のため、高品質なMg鋳造品を製造するには効果的な溶湯処理(脱ガスおよび介在物除去)が不可欠です[41-78]。
- Mg合金は、HPDCにおいてAl合金と比較してダイソルダリングに対する感受性が著しく低く、より広いプロセスウィンドウを可能にし、より薄い断面の鋳造を容易にします[88, 89]。
- Mgの高い反応性は、HPDCの乱流充填中に溶湯を酸化およびバイフィルム欠陥形成に対して脆弱にします。真空HPDC(VADC/SVDC)やVACURALのような特殊技術はこれを軽減できますが、超大型部品に対するスケーラビリティの課題に直面します[90-105, 135-146]。
- ホットティアは、合金組成(凝固範囲、共晶相)および鋳造条件(金型温度、冷却速度、介在物、結晶粒構造)によって影響を受ける潜在的な欠陥です。AZ91のような一部の合金は比較的低い感受性を示します[表2, 106-132]。
- 密度が低いため、同等体積のMg部品を鋳造するには、Al部品と比較して低い型締力のHPDCマシンが必要となる可能性があり、潜在的に設備コストを削減できます[セクション5.1]。
- いくつかの例は、アンダーボディやバッテリーエンクロージャーなどの超大型部品に関する最近の試みを含め、様々な自動車部品に対するMg合金HPDCの成功した応用を示しています[図1, 図8, 40, 133, 147-152]。
![Fig. 2. Microstructure of AZ91D with and without degassing under different casting conditions [41].](https://castman.co.kr/wp-content/uploads/image-2012-png.webp)
![Fig. 3. the die soldering issue occurred during a 1.6 mm ultra-thin-walled HPDC test [86].](https://castman.co.kr/wp-content/uploads/image-2013-png.webp)
![Fig. 4. Sketch of a surface-film entrainment event in a light alloy casting [44,99].](https://castman.co.kr/wp-content/uploads/image-2014-png.webp)
![Fig. 5. Sketch of VACURAL Technology [145].](https://castman.co.kr/wp-content/uploads/image-2015-png.webp)
![Fig. 6. Sketch of the casting technique used by Gibbs Die Casting to cast Mg alloys [144].](https://castman.co.kr/wp-content/uploads/image-2016-png.webp)
![Fig. 7. A shock tower cast using AE44 alloy, dimensions 571 mm × 210 mm × 352 mm. (a) Appearance of the shock tower, with numbers denoting test bar sampling locations. (b) Tensile properties of the shock tower cast at different switchover positions of 560 mm, 580 mm, 600 mm [150].](https://castman.co.kr/wp-content/uploads/image-2017-png.webp)
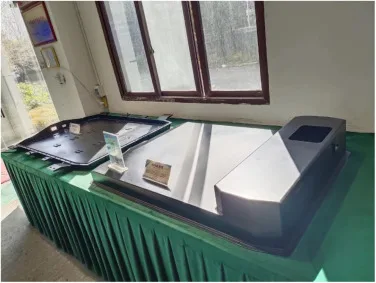
図表リスト:
- 図1. 重慶大学、Millison Inc.、Boao Magnesium Aluminium Manufacturing Company Ltdによって製造されたMg合金超大型ダイカスト。Mg合金超大型鋳物の形状は、商業上の機密保持のため伏せられています[5]。
- 図2. 異なる鋳造条件下での脱ガス処理あり/なしのAZ91Dの微細構造[41]。
- 表1. 様々な温度におけるマグネシウムの蒸気圧[49]。
- 図3. 1.6mm超薄肉HPDC試験中に発生したダイソルダリング問題[86]。
- 図4. 軽合金鋳造における表面フィルム巻き込み現象のスケッチ[44, 99]。
- 表2. 様々な商用Mg合金のホットティア評価。評価が高いほどHTS(ホットティア感受性)が高いことを示します[114]。
- 図5. VACURAL技術のスケッチ[145]。
- 図6. Gibbs Die CastingがMg合金を鋳造するために使用した鋳造技術のスケッチ[144]。
- 図7. AE44合金を使用して鋳造されたショックタワー、寸法571mm x 210mm x 352mm。(a) ショックタワーの外観、数字は試験片サンプリング位置を示す。(b) 560mm、580mm、600mmの異なる切り替え位置で鋳造されたショックタワーの引張特性[150]。
- 図8. Chongqing Qianhe Magnesium Tech Co.によって鋳造されたMg合金バッテリーエンクロージャー部品、厚さ1.8mm、サイズ1.2m * 0.8m。
7. 結論:
車両軽量化への需要増加は、Mg合金を自動車産業にとって非常に魅力的な材料として位置づけており、特にHPDCによって製造される超大型構造部品という新たなトレンドにおいて顕著です。本レビューは、この文脈におけるMg合金利用の重要な側面を強調しました。Mg合金は卓越した金型充填能力を持ち、長い充填距離(例:1.2m)にわたって薄肉(例:1.8mm)の極めて大きな部品の鋳造を可能にします。しかし、これらの超大型部品で一貫した品質を達成するには、潜在的な欠陥(酸化物、バイフィルム、ホットティアなど)と微細構造特徴の効果的な制御が必要であり、溶湯処理と鋳造プロセスパラメータの慎重な管理が求められます。全体として、Mg合金は超大型自動車部品の製造に大きな可能性を示し、実質的な軽量化の利点を提供しますが、この可能性を完全に実現し、関連する課題に対処するためには、さらなる研究開発が必要です。
8. 参考文献:
- [1] E. Musk, Tesla 2020 Annual Meeting of Stockholders and Battery Day, 2020.
- [2] T.A. Baser, E. Umay, V. Akıncı, in: International Conference on Technology, Engineering and Science, 2022, pp. 79-87.
- [3] H. Nakajima, Toyota Technical Workshop, Toyota Motor Corporation, Toyota City, Japan, 2023.
- [4] I. Dnistran, Toyota Showcases its Own Giga Casting in a Bid to Lower EV Costs, 2023 [cited 2023 3rd Aug] Available from: https://insideevs.com/news/671943/toyota-giga-casting/.
- [5] Z. Tong, South China Morning Post, South China Morning Post, Singapore, 2023.
- [6] Das, S.K., H.W. Hayden, and G.B. Barthold, Development of Non-Heat-Treatable Automotive Aluminum Sheet Alloys. 2000. p. 913-919.
- [7] A.W. Shah, et al., Int. J. Metalcast. (2023).
- [8] X.Z. Zhu, et al., J. Mater. Sci. 56 (18) (2021) 11083-11097.
- [9] RHEINFELDEN-ALLOYSHandbook Die Casting Aluminium Alloys, 2023 Alloys for Pressure Die Casting 2016 [citedAug 14]; Available from: https://rheinfelden-alloys.eu/wp-content/uploads/2017/01/Handbook-Die-Casting-Aluminium-Alloys_RHEINFELDEN-ALLOYS_2016_EN.pdf.
- [10] AlcoaAlcoa Specialty Alloys: C611 EZCastTM, 2022 [cited 2023 Aug 14]; Available from: https://www.alcoa.com/global/en/what-we-do/aluminum/cast-products/pdfs/ALC-C611-EzCast-SellSheet.pdf .
- [11] AlcoaAlcoa Specialty Alloys: C891F EZCastPlusTM, 2022 [cited 2023 Aug 14]; Available from: https://www.alcoa.com/global/en/what-we-do/aluminum/cast-products/pdfs/ALC-C891F-EzCastPlus-SellSheet.pdf.
- [12] A.L. Bowles, Q. Han, J.A. Horton, TMS (2005) 99-104.
- [13] Y.-Z. Lü, Q.-D. Wang, X.-Q. Zeng, W.-J. Ding, Y.-P. Zhu, Mater. Sci. Technol 17 (2) (2013) 207-214.
- [14] M. Pekguleryuz, M. Celikin, Int. Mater. Rev. 55 (4) (2013) 197-217.
- [15] S. Candan, E. Candan, Trans. Nonferrous Metals Soc. China 27 (8) (2017) 1725-1734.
- [16] A. LUO, M.O. Pekguleryuz, J. Mater. Sci. 29 (1994) 5259-5271.
- [17] J.P. Weiler, J. Magnes. Alloys 9 (1) (2021) 102-111.
- [18] Q.C. Jiang, et al., Mater. Sci. Eng.: A 392 (1-2) (2005) 130-135.
- [19] L.Y. Wei, G.L. Dunlop, H. Westengen, Mater. Sci. Technol. 12 (9) (1996) 741-750.
- [20] M. Easton, et al., Mater. Sci. Forum 828-829 (2015) 3-8.
- [21] M.O. Pekguleryuz, M.M. Avedesian, Inst. Magnes. Technol. 42 (12) (1992) 679-686.
- [22] V.E. Bazhenov, et al., J. Magnes. Alloys 9 (5) (2021) 1567-1577.
- [23] V.E. Bazhenov, et al., J. Magnes. Alloys 8 (1) (2020) 184-191.
- [24] G. Chen, et al., Trans. Nonferrous Metals Soc. China 21 (4) (2011) 725-731.
- [25] K. Hirai, et al., Mater. Sci. Eng.: A 403 (1-2) (2005) 276-280.
- [26] C. Jingyang, et al., Spec. Cast. Nonferrous Alloys 8 (2005) 454.
- [27] H.L. Zhao, S.K. Guan, F.Y. Zheng, J. Mater. Res. 22 (9) (2011) 2423-2428.
- [28] Y. Turen, Mater. Des. 49 (2013) 1009-1015.
- [29] E. Baril, P. Labelle, M.O. Pekguleryuz, Res. Summary 55 (2003) 34-39.
- [30] M.H. Kim, et al., Mater. Sci. Forum 419-422 (2003) 575-580.
- [31] S.-Y. Chang, J.-C. Choi, Met. Mater. 4 (2) (1998) 165-171.
- [32] C.D. Yim, et al., J. Mater. Sci. (8) (2006) 41.
- [33] Y. Nakaura, A. Watanabe, K. Ohori, Mater. Trans. 47 (4) (2006) 1031-1039.
- [34] Y. Fu, et al., J. Rare Earths 35 (5) (2017) 503-509.
- [35] Y. Cui, et al., Materials 13 (16) (2020).
- [36] Y. Lu, et al., Mater. Sci. Eng. A 278 (2000) 66-76.
- [37] W.Q. dong, et al., Trans. Nonferrous Metals Soc. China 02 (2000) 235-239.
- [38] Q. Hua, et al., Mater. Sci. Eng.: A 444 (1-2) (2007) 69-74.
- [39] T. Rzychoń, et al., Mater. Charact. 60 (10) (2009) 1107-1113.
- [40] B. Liu, et al., J. Magnes. Alloys 11 (1) (2023) 15-47.
- [41] E. Zhang, G.J. Wang, Z.C. Hu, Mater. Sci. Technol. 26 (10) (2010) 1253-1258.
- [42] Z.C. Hu, E.L. Zhang, S.Y. Zeng, Mater. Sci. Technol. 24 (11) (2008) 1304-1308.
- [43] A. Elsayed, et al., Trans. Am. Foundry Soc. 120 (2012) 423-429, Vol 120.
- [44] T. Li, J.M.T. Davies, D. Luo, Metall. Mater. Trans. B-Process Metall. Mater. Process. Sci. 52 (5) (2021) 3093-3106.
- [45] S.E. Housh, V. Petrovich, SAE Technical Paper, 920071, SAE international, Warrendale, Pa, USA, 1992.
- [46] S.E. Housh, V. Petrovich, Magnesium Refining: A Fluxless Alternative, 1992 SAE Technical Paper.
- [47] J. Thomson, et al., Transactions of the American Foundry Society and the One Hundred Eighth Annual Metalcasting Congress, 2004.
- [48] E.F. Emley, Metals Technol. 3 (1) (1976) 118-127.
- [49] S. Bell, et al., the Minerals and Metals Sector of Natural Resources Canada, 2006.
- [50] Y. Luo, Appl. Math. Model. 37 (9) (2013) 6177-6182.
- [51] T. Watanabe, et al., J. Jpn. Inst. Light Metals 26 (6) (1976) 266-272.
- [52] H.X. Cao, et al., J. Magnes. Alloys 7 (3) (2019) 370-380.
- [53] L.F. Zhang, T. Dupont, State of the Art in the Refining and Recycling of Magnesium, 2007 p. 25-+.
- [54] F. Pan, et al., J. Magnes. Alloys 4 (1) (2016) 8–14.
- [55] J. Wu, et al., Mater. Res. Express 9 (3) (2022) 032001.
- [56] Moon, B.G., B.S. You, and Koh. Kiho, in Magnesium Technology 2013, N. Hort, et al., Editors. 2013, John Wiley & Sons: New Jersey.
- [57] S.M. Patel, M.M. Patel, V.J. Rao, Mater. Res. Express 8 (11) (2021).
- [58] S.M. Patel, M.M. Patel, V.J. Rao, Mater. Res. Express 8 (11) (2021) 116503.
- [59] F.S. Pan, et al., J. Magnes. Alloys 4 (1) (2016) 8-14.
- [60] G.-h. Wu, et al., Trans. Nonferrous Metals Soc. China 20 (11) (2010) 2037-2045.
- [61] N. El-Kaddah, A.D. Patel, T.T. Natarajan, JOM 47 (5) (1995) 46-49.
- [62] N. Balasubramani, et al., J. Magnes. Alloys 9 (3) (2021) 829-839.
- [63] A. Kumar, P.M. Pandey, J. Magnes. Alloys 9 (6) (2021) 1989-2008.
- [64] Y. Chen, et al., J. Magnes. Alloys 10 (3) (2022) 614-626.
- [65] P. Emadi, B. Andilab, C. Ravindran, J. Magnes. Alloys 10 (12) (2022) 3397-3405.
- [66] H. Peng, et al., J. Magnes. Alloys 8 (2) (2020) 552-563.
- [67] A.R. Eivani, et al., J. Magnes. Alloys 9 (4) (2021) 1304-1328.
- [68] X. Ding, et al., J. Magnes. Alloys 11 (3) (2023) 903-915.
- [69] J.Y. Zhang, et al., J. Magnes. Alloys 9 (4) (2021) 1187-1200.
- [70] G.I. Eskin, Ultrason. Sonochem. 8 (3) (2001) 319-325.
- [71] Y.J. Chen, W.N. Hsu, J.R. Shih, Mater. Trans. 50 (2) (2009) 401-408.
- [72] Z.W. Shao, et al., Met. Mater. Int. 18 (2) (2012) 209-215.
- [73] Z.-W. Shao, et al., Trans. Nonferrous Metals Soc. China 20 (2010) s382-s387.
- [74] M. Khosro Aghayani, B. Niroumand, J. Alloys Compd. 509 (1) (2011) 114-122.
- [75] V. PETROVICH, W. MERCER E., W. GREEN, Patentscope, Espacenet, E.P. Office, Editor, U.S, 1993.
- [76] J. Zha, et al., in: Manufacturing Science and Technology, Pts 1-3, Р.С. Wang, 2011, pp. 2151-2154. Editors.
- [77] J. Wang, et al., Trans. Nonferrous Metals Soc. China 20 (7) (2010) 1235-1239.
- [78] J.L. Zha, et al., Adv. Mat. Res. 295-297 (2011) 2151-2154.
- [79] H. Huang, et al., Int. J. Cast Met. Res. 26 (4) (2013) 213-219.
- [80] Y.L. Li, et al., J. Mater. Sci. Technol. 33 (6) (2017) 558-566.
- [81] A. Juriani, Casting Defects Analysis in Foundry and Their Remedial Measures with Industrial Case Studies, 2015.
- [82] Akhyar, et al., Metalurgija 61 (2) (2022) 309-312.
- [83] Q.Y. Han, China Foundry 12 (2) (2015) 136-143.
- [84] S. Shankar, D. Apelian, Metall. Mater. Trans. B-Process Metall. Mater. Process. Sci. 33 (3) (2002) 465-476.
- [85] Z.W. Chen, Mater. Sci. Eng. a-Struct. Mater. Properties Microstruct. Process. 397 (1-2) (2005) 356-369.
- [86] Z.C. Niu, et al., J. Mater. Process. Technol. (2022) 303.
- [87] D. Schwam, A. Miller, Thin-Wall and High-Strength Die Casting Alloys, Defence Technical Information Center, 2017.
- [88] A.L. Bowles, Q. Han, J.A. Horton, et al., in: S.N. Mathaudhu, et al. (Eds.), Essential Readings in Magnesium Technology, Springer International Publishing, Cham, 2016, pp. 187-192. Editors.
- [89] C. Tang, M.Z. Jahedi, M. Brandt, the 6th International Tooling Conference, Karlstad Univ, Karlstad, Sweden, 2002.
- [90] M.M. Jalilvand, et al., J. Magnes. Alloys 8 (1) (2020) 219-230.
- [91] C.L. Cheng, et al., J. Magnes. Alloys 8 (4) (2020) 1281-1295.
- [92] S. Ma, et al., J. Magnes. Alloys 8 (3) (2020) 819-831.
- [93] M.M. Jalilvand, et al., J. Magnes. Alloys 10 (6) (2022) 1704-1717.
- [94] W.D. Griffiths, N.W. Lai, Metall. Mater. Trans. a-Phys. Metall. Mater. Sci. 38A (1) (2007) 190-196.
- [95] T. Li, W.D. Griffiths, J. Chen, Metall. Mater. Trans. a-Phys. Metall. Mater. Sci. 48A (11) (2017) 5516-5528.
- [96] T. Li, J.M.T. Davies, X. Zhu, J. Mater. Sci. 56 (29) (2021) 16671-16685.
- [97] T. Li, J.M.T. Davies, X.Z. Zhu, J. Magnes. Alloys 10 (1) (2022) 129-145.
- [98] C. Cingi, Mold-metal Reactions in Magnesium Investment Castings, Helsinki University of Technology, 2006.
- [99] J. Campbell, Castings, Butterworth-Heinemann, Oxford, 2004.
- [100] A.R. Mirak, et al., Int. J. Cast Met. Res. 20 (4) (2007) 215-220.
- [101] T. Li, J.M.T. Davies, Metall. Mater. Trans. A 51 (10) (2020) 5389-5400.
- [102] D. Dispinar, J. Campbell, Int. J. Cast Met. Res. 19 (1) (2006) 5–17.
- [103] I.H. Kalkan, et al., Shape Casting, Springer International Publishing, Cham, 2019.
- [104] J. Olofsson, A. Bjurenstedt, S. Seifeddine, Shape Casting, Springer International Publishing, Cham, 2019.
- [105] X. Li, S.M. Xiong, Z. Guo, J. Mater. Process. Technol. 231 (2016) 1-7.
- [106] G. Cao, I. Haygood, S. Kou, Metall. Mater. Trans. a-Phys. Metall. Mater. Sci. 41A (8) (2010) 2139-2150.
- [107] G. Cao, et al., Metall. Mater. Trans. a-Phys. Metall. Mater. Sci. 41A (3) (2010) 706-716.
- [108] Z.S. Zhen, et al., Int. J. Cast Met. Res. 22 (1-4) (2009) 331-334.
- [109] X.D. Du, et al., J. Magnes. Alloys 11 (2) (2023) 694-705.
- [110] Y. Zhou, et al., J. Magnes. Alloys 8 (4) (2020) 1176-1185.
- [111] G.J. Zhang, et al., J. Magnes. Alloys 7 (2) (2019) 272-282.
- [112] Z.Z. Yang, et al., J. Magnes. Alloys 6 (1) (2018) 44-51.
- [113] Q.S. Yang, et al., J. Magnes. Alloys 2 (1) (2014) 8-12.
- [114] J.F. Song, et al., J. Magnes. Alloys 4 (3) (2016) 151-172.
- [115] K. Strobel, et al., Int. J. Cast Met. Res. 23 (2) (2010) 81-91.
- [116] X. Su, et al., Int. J. Metalcast. 15 (2) (2021) 576-586.
- [117] G. Cao, S. Kou, Mater. Sci. Eng. a-Struct. Mater. Properties Microstruct. Process. 417 (1-2) (2006) 230-238.
- [118] Z.S. Zhen, et al., Light Metals Technol. 618-619 (2009) 533-540.
- [119] L. Zhou, et al., Int. J. Cast Met. Res. 24 (3-4) (2011) 170-176.
- [120] L. Zhou, et al., Magnes. Technol. 2011 (2011) 125-130.
- [121] J.F. Song, et al., Metall. Mater. Trans. a-Phys. Metall. Mater. Sci. 46A (12) (2015) 6003-6017.
- [122] A. Srinivasan, et al., Trans. Indian Inst. Met. 65 (6) (2012) 701-706.
- [123] M.A. Easton, et al., Metall. Mater. Trans. a-Phys. Metall. Mater. Sci. 45A (8) (2014) 3586-3595.
- [124] Z. Wang, et al., Metall. Mater. Trans. a-Phys. Metall. Mater. Sci. 46A (5) (2015) 2108-2118.
- [125] G. Cao, S. Kou, Metall. Mater. Trans. a-Phys. Metall. Mater. Sci. 37A (12) (2006) 3647-3663.
- [126] G. Zhang, et al., Materwiss Werksttech 50 (12) (2019) 1471-1483.
- [127] S.K. Rathi, A. Sharma, M. Di Sabatino, Eng. Fail. Anal. 79 (2017) 592-605.
- [128] L. Bichler, et al., Int. J. Metalcast. 2 (1) (2008) 43-56.
- [129] Z. Wang, et al., J. Mater. Sci. 49 (1) (2014) 353-362.
- [130] S. Li, D. Apelian, Int. J. Metalcast. 5 (1) (2011) 23-40.
- [131] J.M. Middleton, H.T. Protheroe, J. Iron Steel Institute 168 (4) (1951) 384-398.
- [132] G.H. Wu, et al., Acta Metall. Sinica 58 (4) (2022) 385-399.
- [133] Sophia, F., et al., in Magnesium Alloys, T. Tomasz Arkadiusz, C.-A. Katarzyna, and J. Ewa, Editors. 2023, IntechOpen: Rijeka. p. Ch. 2.
- [134] HPMMACHINERYHPM North America to Build 4500 Ton Die Cast Machine [cited 2023 Nov 19th]; Available from:, 2015. https://www.yizumi-hpm.com/hpm-north-america-to-build-4500-ton-die-cast-machine/.
- [135] H. Cao, et al., Vacuum 146 (2017) 278-281.
- [136] A.A. Luo, A.K. Sachdev, D. Apelian, J. Mater. Process. Technol. (2022) 306.
- [137] Cosma-International. Aluminum high pressure die casting. [cited 2023 18 Aug]; Available from: https://www.magna.com/docs/default-source/default-document-library/cosma_casting_brochure_english.pdf?sfvrsn=0.
- [138] T. Le, et al., Mater. Res. Express 7 (11) (2020) 116513.
- [139] X. Liu, et al., J. Mater. Res. Technol. 23 (2023) 4293-4306.
- [140] C. Ma, et al., J. Magnes. Alloys 11 (2) (2023) 753-761.
- [141] Z.-q. Wang, et al., Trans. Nonferrous Metals Soc. China 24 (12) (2014) 3762-3768.
- [142] X. Dong, X. Zhu, S. Ji, J. Mater. Process. Technol. 266 (2019) 105-113.
- [143] V. Nandakumar, Process and Tool Design for the High Integrity Die Casting of Aluminum and Magnesium Alloys, The Ohio State University, 2014.
- [144] A.A. Luo, J. Magnes. Alloys 1 (1) (2013) 2-22.
- [145] FRECH, Vacural Technol. (2023) [cited 2023 18th Aug]; Available from: https://www.frechusa.com/vacural-technology.
- [146] Foundry-Lexicon, Vacural Process (2023) [cited 2023 18 Aug]; Available from: https://www.giessereilexikon.com/en/foundry-lexicon/Encyclopedia/show/vacural-process-4629/?cHash=fa70abc99c24ba84803fb708ad2266a7.
- [147] J.P. Weiler, J. Magnes. Alloys 7 (2) (2019) 297-304.
- [148] M. Abate, M. Willman, Use of Cast Magnesium Back frames in Automotive Seating, 2005 SAE Technical Paper.
- [149] J.P. Weiler, Contemporary Magnesium Die-Casting Research and Technology: A Canadian Viewpoint, Springer International Publishing, Cham, 2021.
- [150] W. Xueyang, et al., Spec. Cast. Nonferrous Alloys 42 (04) (2022) 467-472.
- [151] X. Chen, et al., Cast Magnesium Subframe Development-Bolt Load Retention, 2021 SAE Technical Paper.
- [152] J. Aragones, et al., Development of the 2006 Corvette z06 Structural Cast Magnesium Crossmember, 2005 SAE Technical Paper.
9. 著作権:
- この資料は "Tian Li et al." による論文です。「Progress and prospects in Mg-alloy super-sized high pressure die casting for automotive structural components」に基づいています。
- 論文の出典: https://doi.org/10.1016/j.jma.2023.11.003
この資料は上記の論文に基づいて要約されたものであり、商業目的での無断使用は禁じられています。
Copyright © 2025 CASTMAN. All rights reserved.