本紹介記事は、[Teesside大学]により発表された論文["水系中子技術の軽合金への応用開発"]の研究内容をまとめたものです。
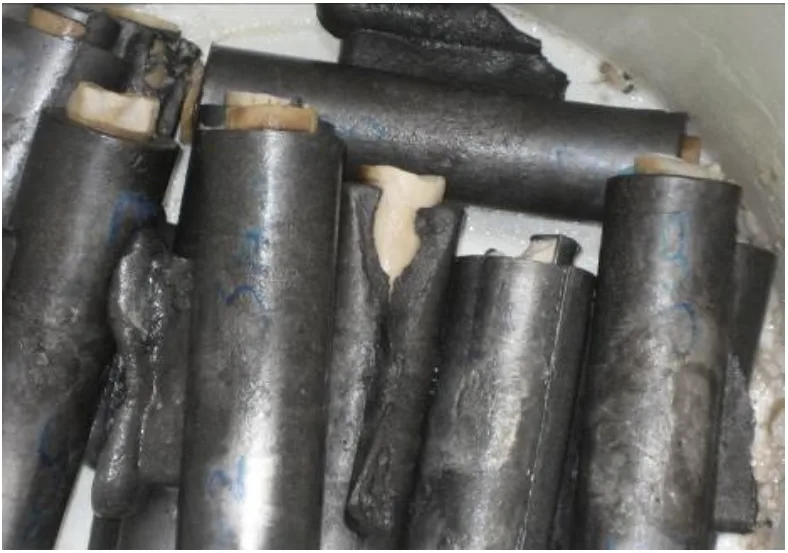
1. 概要:
- タイトル: 水系中子技術の軽合金への応用開発
- 著者: Manu Ramegowda
- 発行年: 2008年8月
- 発行ジャーナル/学会: 未発表博士論文. Teesside大学.
- キーワード: 水系中子技術, 軽合金, 溶融シリカ, 石膏, 酸化マグネシウム, 浸出
2. 概要 / はじめに
概要
本論文では、製造業の観点から、軽合金用の新しい水系中子技術の開発について述べている。
鋼鋳造に使用される中子は溶融シリカで作られており、還流下での熱水酸化ナトリウム(加圧熱酸)を使用して除去される。しかし、アルミニウムやその他の軽合金は水酸化ナトリウムによって腐食される。現在、アルミニウムやその他の軽合金に適した中子システムは存在しない。したがって、アルミニウムやその他の軽合金鋳造用の代替材料/浸出剤の組み合わせを見つけることが望ましい。
最近の研究レビューでは、セラミック中子は主に異なる添加剤を伴う溶融シリカで作られていることが示されている。先行研究では、充填材として溶融シリカ(異なるメッシュサイズ)を使用し、中子ミックスのスラリー作業寿命を制御するために酸化マグネシウムを使用することが提案されている。ケイ酸カルシウムは希酸での中子浸出を助ける。石膏(硫酸カルシウム)は、独自の石膏(Crystcal R、ファインキャスティングプラスター)の形で、結合を生成し、中子に強度を与えるために使用される。炭酸リチウムは促進剤として作用し、中子内の石膏の強化効果を向上させる。バインダー(Ludox® AM)と水は(添加材料として)組成物を結合させるために作用する。
中子組成物は、軽合金に適した強度と迅速な浸出特性を記録する中子を製造するために、異なる中子試験で作製された。中子試験は個別に混合され、木製の中子箱に注がれた。中子は24時間予備乾燥された。中子は異なる温度で2時間焼成され、その後2時間冷却された。中子は、破壊係数(MOR)を記録するために、コンピュータ化された三点曲げ試験に供された。平面ひずみ破壊靭性とワイブルパラメータが計算された。ワイブルパラメータは、Minitab解析ソフトウェアを使用してプロットされた。中子を使用して、重力ダイカストプロセスが実施された。後続の鋳物は、中子を浸出させるために希釈された硝酸、クエン酸、および酢酸に浸された。
異なる中子組成物を使用して、中子試験は混合、注型、乾燥、試験、および浸出された。中子試験における石膏の含有量が多いほど、中子が200°〜400°Cで焼成された場合に高いMORが記録され、600°〜800°Cで焼成された場合には逆の結果となった。異なるグレードの石膏(CRP、FCP)は強度に影響を与えない。1%の酸化マグネシウムは非常に短い作業寿命を与える。高含有量のバインダー(Ludox® AM)は、中子内で強力な中子を生成する。
手作業またはワックスがけプロセスを可能にする組成に応じて、実用的なMOR結果を得ることができる。破壊靭性は脆性材料の典型であり、ワイブルパラメータと一致する。鋳造プロセスは、新しい材料が十分に耐火性であることを示唆している。中子は、商業生産と両立可能な速度で希釈された硝酸、酢酸、およびクエン酸を使用して浸出される。
この方法論は、アルミニウムおよびおそらく軽合金用の溶融シリカと石膏および酸化マグネシウムを使用した中子を製造することに成功した。強度と金属を攻撃する酸による除去に関連する特定の産業用途に応じて、異なる中子試験を使用することができる。最適な浸出条件を微調整するためには、さらなる作業が必要である。
3. 研究背景:
研究トピックの背景:
中子は金属鋳造に不可欠な部品であり、鋳造品に内部形状を作成するために使用されます。従来、鋼鋳造用の中子は溶融シリカで作られ、熱水酸化ナトリウムを使用して除去されていました。しかし、この方法は、水酸化ナトリウムがこれらの合金を腐食させるため、アルミニウムや軽合金には適していません。したがって、軽合金用代替中子技術の開発が必要とされています。
既存研究の現状:
先行研究では、セラミック中子は主に添加剤を伴う溶融シリカで作られていることが示されています。異なるメッシュサイズの溶融シリカが充填材として使用され、酸化マグネシウムがスラリーの作業寿命を制御するために使用されています。ケイ酸カルシウムは希酸でのコア浸出を助けます。石膏(硫酸カルシウム)は、Crystcal Rやファインキャスティングプラスターなどの独自の石膏の形で、結合を生成し、強度を高めるために使用されます。炭酸リチウムは、コア内の石膏の強化効果を高めるために促進剤として使用されます。バインダー(Ludox® AM)と水もコア組成物に使用されています。
研究の必要性:
現在、アルミニウムやその他の軽合金に最適な中子システムは存在しません。既存の水酸化ナトリウムを使用する方法は、水酸化ナトリウムの腐食性のため、これらの合金には適用できません。アルミニウムや軽合金の鋳造を容易にするためには、代替材料と浸出剤の組み合わせが必要です。本研究は、希釈酢酸などの腐食性の低い浸出剤を使用し、環境上の利点を提供し、苛性ソーダに関連する廃棄物処理問題を解決する、軽合金に適した水系中子技術を開発することにより、このギャップに対処することを目的としています。
4. 研究目的と研究課題:
研究目的:
本プロジェクトの目的は、確立された水系中子技術を軽合金用中子形状の製造に応用し、苛性ソーダよりも腐食性の低い浸出剤、例えば希釈酢酸を使用してアルミニウム合金鋳物から中子を除去できるように組成を修正することである。本研究では、寸法安定性、強度、機械的特性、および環境に優しい試薬による容易な除去のために最適な中子組成を決定することを目的としています。最終的な目標は、開発された中子を鋳造用中子としての適合性を評価することです。
主要研究:
- 軽合金用の新しい水系中子技術の開発。
- アルミニウムやその他の軽合金鋳造用の代替材料/浸出剤の組み合わせの発見。
- 苛性ソーダよりも腐食性の低い浸出剤(希釈酢酸など)を使用してアルミニウム合金鋳物から中子を除去できるように中子組成を修正。
- 寸法安定性、強度、およびその他の機械的特性に最適な中子組成の決定。
- 開発された中子を鋳造用中子としての適合性を評価。
5. 研究方法
研究デザイン:
本研究では、初期の中子組成から開始し、機械的特性、鋳造性能、および中子除去を最適化するために成分を体系的に変化させる反復実験的アプローチを採用しました。さまざまな中子組成物が処方および試験され、石膏、バインダー、および酸化マグネシウムの割合の変化、ならびにケイ酸カルシウムおよび異なる石膏タイプの使用の影響を評価するように設計された試験が行われました。
データ収集方法:
- 中子準備: 中子組成物を混合し、木製の中子箱に注ぎ込み、予備乾燥し、異なる温度(200℃、400℃、600℃、800℃)で焼成しました。
- 機械的試験: コンピュータ化された三点曲げ試験を実施して、破壊係数(MOR)を測定しました。平面ひずみ破壊靭性とワイブルパラメータも計算されました。
- 中子除去試験: 中子を使用して重力ダイカストを行い、その後、さまざまな濃度と期間の希釈硝酸、クエン酸、および酢酸溶液で浸出しました。中子除去の容易さは、目視およびプロービングによって評価されました。
- 寸法測定: 収縮を評価するために、焼成前後のコア寸法(直径と長さ)を測定しました。
- 顕微鏡観察: 走査型電子顕微鏡(SEM)を使用して、選択された中子サンプルの表面形態を調べました。
分析方法:
- 破壊係数(MOR)分析: MOR値を三点曲げ試験データから計算して、中子強度を評価しました。
- ワイブル分析: ワイブルパラメータを計算し、Minitabソフトウェアを使用してプロットし、中子強度の信頼性と変動性を分析しました。
- 破壊靭性分析: 平面ひずみ破壊靭性(KIC)を計算して、材料の脆性破壊に対する抵抗性を評価しました。
- 統計分析: Minitabソフトウェアを統計分析に使用しました。
- 定性分析: 目視検査とプロービングを使用して、中子除去効果と中子欠陥を評価しました。
研究対象と範囲:
本研究は、軽合金、特にアルミニウム用の水系中子技術の開発に焦点を当てました。調査対象の中子材料には、溶融シリカ、石膏(各種)、酸化マグネシウム、炭酸リチウム、ケイ酸カルシウム、クエン酸三ナトリウム、およびLudox® AMバインダーが含まれていました。中子組成物は、機械的特性、重力ダイカストにおける鋳造性能、および希釈酸を使用した除去について試験されました。範囲は実験室規模の実験に限定されており、実規模の産業試験には拡大していません。
6. 主な研究結果:
主要な研究結果:
- 中子組成とMOR: 中子試験における石膏含有量が多いほど、200℃〜400℃で焼成した場合に高いMORが記録されましたが、600℃〜800℃で焼成した場合は逆の結果となりました。異なるグレードの石膏(CRP、FCP)は強度に大きな影響を与えませんでした。高バインダー含有量(Ludox® AM)は、強力な中子を生成しました。
- スラリー作業寿命: 1%の酸化マグネシウムは、非常に短いスラリー作業寿命をもたらしました。
- 浸出: 希釈された硝酸、クエン酸、および酢酸は、商業生産と両立可能な速度で中子を浸出させることに成功しました。高濃度の硝酸(1:1、1:2、1:5)は中子浸出に効果的でしたが、希釈された酢酸とクエン酸も、特に高濃度(酢酸で1:100、クエン酸で1:100)で有望な浸出能力を示しました。
- 寸法安定性: より細かいメッシュサイズの溶融シリカ(-200)は、より粗い溶融シリカと比較して、寸法安定性を向上させ、収縮を低減しました。
- ワイブル分析: ワイブル分析は、中子の脆性を示しており、ワイブル係数の値は強度のばらつきを示唆しています。
- 破壊靭性: 破壊靭性(KIC)値を計算し、材料の亀裂伝播に対する抵抗性の定量的な尺度を提供しました。
提示されたデータの分析:
- 温度によるMORの変化: MOR値は、特に石膏含有量が多い中子組成物の場合、焼成温度が高いほど(600℃〜800℃)一般的に低下しました。これは、高温での石膏の分解と結合の弱体化が原因であると考えられます。
- 酸化マグネシウムの影響: 酸化マグネシウムはスラリーの作業寿命を大幅に短縮し、硬化プロセスを促進する役割を強調しました。
- 浸出効果: 希釈硝酸は、一般的にクエン酸や酢酸よりも中子浸出に効果的でしたが、3つの酸すべてが、特に高濃度で浸出の可能性を示しました。有効性は、中子組成と焼成温度によって異なりました。
- 寸法変化: より細かい溶融シリカと特定の中子組成物(例:トライアルD)は、より優れた寸法安定性と収縮の低減を示しました。
- ワイブルと破壊靭性: ワイブル分析は中子の脆性を確認し、破壊靭性値は破壊に対する抵抗性の定量的な尺度を提供しました。
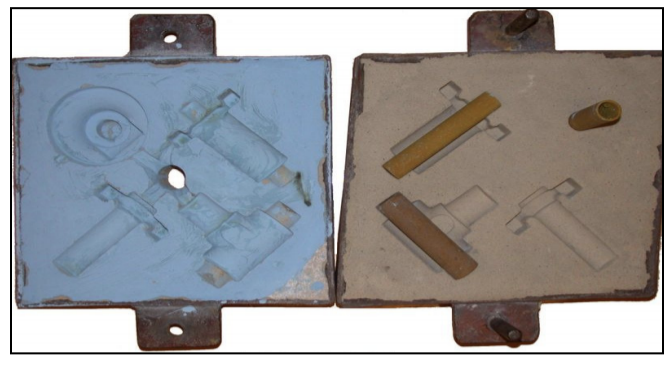
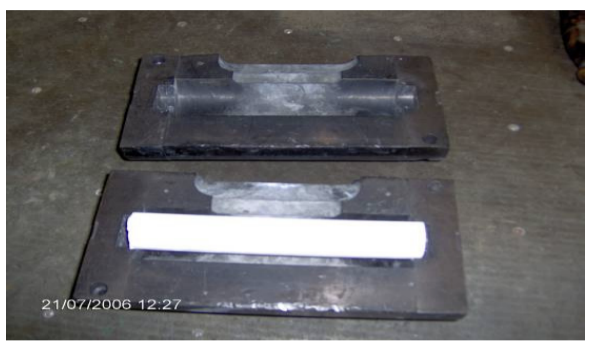
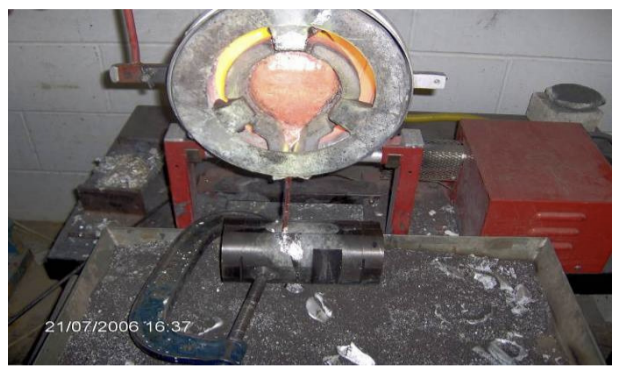
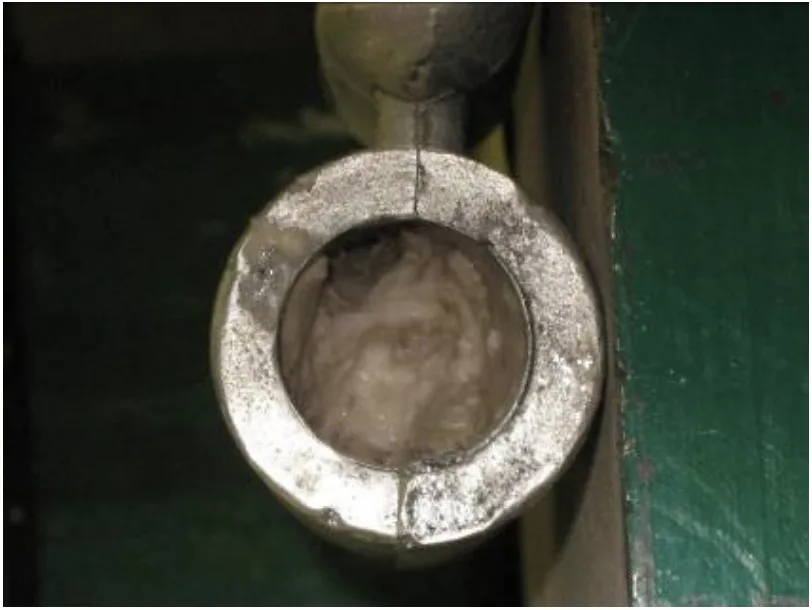

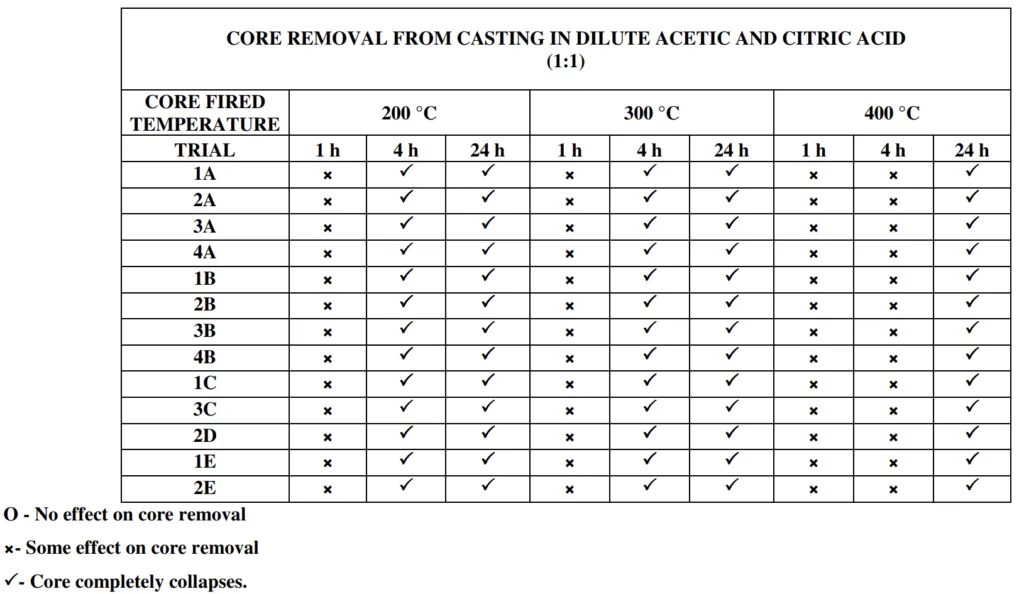
図の名前リスト:
- 図 1. 複雑な砂中子の例 (9)
- 図 2. さまざまなセラミック中子形状の例 (10)
- 図 3. レーシングカー排気部品用プリフォーム中子 (10)
- 図 4. 硬化後にドラッグに挿入される中子 (11)
- 図 5. コンベヤー式中子乾燥炉 (13)
- 図 6. 三点荷重方式 (35)
- 図 7. 砂中子による砂型鋳造 (59)
- 図 8. (a) 中子ブロー (b) 凝固前の中子からのガスによる欠陥 (54)
- 図 9. 中子付き中子金型箱
- 図 10. LLOYDユニバーサル試験機
- 図 11. 三点曲げ荷重による破壊サンプル
- 図 12. 中子付き鋳鉄分割金型
- 図 13. 組立金型への注湯工程
- 図 14. 鋳鉄金型の一般的な配置
- 図 15. マークされた鋳造部品
- 図 16. 乾燥させる中子
- 図 17. 中子試験における平均スラリー作業寿命
- 図 18. 中子試験における平均凝固時間
- 図 19. 200℃での中子試験における重量減少を伴う24時間焼成
- 図 20. 400℃での中子試験における重量減少を伴う24時間焼成
- 図 21. 異なる焼成温度におけるトライアルAの平均MOR
- 図 22. 異なる焼成温度におけるトライアルBの平均MOR
- 図 23. 異なる焼成温度におけるトライアルCの平均MOR
- 図 24. 異なる焼成温度におけるトライアルDの平均MOR
- 図 25. 異なる焼成温度におけるトライアルEの平均MOR
- 図 26. 4時間後の400℃で焼成されたトライアル1E中子に対する希釈硝酸の効果。
- 図 27. 異なる焼成温度におけるトライアルAの平均MOR
- 図 28. 断面Al-LM25の中子ブロー欠陥(中子除去済み)
- 図 29. 中子付き垂直立てかけ木製中子箱
- 図 30. 底部に沈降した30/50溶融シリカを備えた600℃で焼成された中子。
- 図 31. 中子試験の平均凝固時間
- 図 32. MgOの割合が異なるトライアル4Aにおける平均スラリー作業寿命
- 図 33. 異なる焼成温度におけるトライアルAの平均MOR
- 図 34. 異なる焼成温度におけるトライアルBの平均MOR
- 図 35. 異なる焼成温度におけるトライアルCの平均MOR
- 図 36. 異なる焼成温度におけるトライアルDの平均MOR
- 図 37. 異なる焼成温度におけるトライアルEの平均MOR
- 図 38. 1時間後の200℃で焼成されたトライアル1Bに対する希釈硝酸(1:1、1:2、1:5)の効果
- 図 39. 4時間後の200℃で焼成されたトライアル1Bに対する希釈硝酸(1:1、1:2、1:5)の効果
- 図 40. 異なる焼成温度におけるトライアルAの平均MOR
- 図 41. 金属を適切に供給していないため破損したAl-LM25
- 図 42. 中子試験の平均凝固時間
- 図 43. 異なる焼成温度におけるトライアルAの平均MOR
- 図 44. 異なる焼成温度におけるトライアルBの平均MOR
- 図 45. 異なる焼成温度におけるトライアルCの平均MOR
- 図 46. 異なる焼成温度におけるトライアルDの平均MOR
- 図 47. 異なる焼成温度におけるトライアルEの平均MOR
- 図 48. 200℃で焼成された溶融シリカメッシュサイズ(-200/-120)の中子表面トライアル4A。
- 図 49. 200℃で焼成された溶融シリカメッシュサイズ(-120/30-50)の中子表面トライアル4A。
- 図 50. 希釈水酸化カリウムによって腐食されたAl-LM25。
- 図 51. 200℃で希釈クエン酸(1:1)で浸出されたトライアル1B中子。
- 図 52. 中子試験の平均凝固時間
- 図 53. 異なる焼成温度におけるトライアルAの平均長さ収縮率
- 図 54. 異なる焼成温度におけるトライアルBの平均長さ収縮率
- 図 55. 異なる焼成温度におけるトライアルDの平均長さ収縮率
- 図 56. 異なる焼成温度におけるトライアルEの平均長さ収縮率
- 図 57. 異なる焼成温度におけるトライアルAの平均直径収縮率
- 図 58. 異なる焼成温度におけるトライアルBの平均直径収縮率
- 図 59. 異なる焼成温度におけるトライアルDの平均直径収縮率
- 図 60. 異なる焼成温度におけるトライアルEの平均直径収縮率
- 図 61. 異なる焼成温度におけるトライアルAの平均MOR
- 図 62. 異なる焼成温度におけるトライアルBの平均MOR
- 図 63. 異なる焼成温度におけるトライアルDの平均MOR
- 図 64. 異なる焼成温度におけるトライアルEの平均MOR
- 図 65. 中子試験の平均凝固時間
- 図 66. 異なる焼成温度におけるトライアルAの平均長さ収縮率
- 図 67. 異なる焼成温度におけるトライアル2Dの平均長さ収縮率
- 図 68. 異なる焼成温度におけるトライアルEの平均長さ収縮率
- 図 69. 異なる焼成温度におけるトライアルAの平均直径収縮率
- 図 70. 異なる焼成温度におけるトライアル2Dの平均直径収縮率
- 図 71. 異なる焼成温度におけるトライアルEの平均直径収縮率
- 図 72. 異なる焼成温度におけるトライアルAの平均MOR
- 図 73. 異なる焼成温度におけるトライアル2Dの平均MOR
- 図 74. 異なる焼成温度におけるトライアルEの平均MOR
- 図 75. 600℃でのトライアルAの分布概要プロット
- 図 76. 600℃でのトライアルEおよび2Dの分布概要プロット
- 図 77. 800℃でのトライアルAの分布概要プロット
- 図 78. 800℃でのトライアルEおよび2Dの分布概要プロット
- 図 79. (a) 800℃でのノッチ付き中子トライアル3Aの亀裂、(b) 600℃でのノッチ付き中子トライアル3Aの亀裂。
- 図 80. 中子試験の平均凝固時間
- 図 81. 異なる焼成温度における中子組成[6]の平均MOR
- 図 82. 異なる焼成温度における中子組成[7]の平均MOR
- 図 83. 中子組成[8]および[9]の平均凝固時間
- 図 84. 異なる焼成温度における中子組成[8]の平均MOR
- 図 85. 異なる焼成温度における中子組成[9]の平均MOR
7. 結論:
主な調査結果の概要:
本研究では、溶融シリカ、石膏、および酸化マグネシウムを使用して、軽合金用の水系中子技術の開発に成功しました。この研究では、苛性ソーダに代わる腐食性の低い代替手段として、希釈された硝酸、クエン酸、および酢酸を中子除去に使用できる可能性が実証されました。主な調査結果には、MOR、スラリー作業寿命、および浸出特性に対する中子組成の影響が含まれます。より細かい溶融シリカ粒子は、中子強度と表面仕上げを向上させました。最適な中子組成は、特定の用途の要件、強度、浸出効率、および寸法安定性のバランスによって異なります。
研究の学術的意義:
本研究は、軽合金用の水系中子技術の科学的理解に貢献しています。MOR、破壊靭性、浸出挙動など、さまざまな中子組成と焼成温度が中子特性に及ぼす影響に関する貴重なデータを提供します。この研究はまた、セラミック中子の信頼性を特徴付けるワイブル分析の応用を進めています。
実際的な意味合い:
開発された水系中子技術は、既存の中子システムの限界に対処し、アルミニウムおよび軽合金の鋳造に実用的なソリューションを提供します。希釈されたクエン酸と酢酸を浸出剤として使用することは、苛性ソーダに代わる環境に優しい代替手段となります。調査結果は、特定の鋳造要件と産業用途に基づいて適切な中子組成と浸出方法を選択する際に、鋳造所への指針を提供します。
研究の限界と今後の研究分野:
本研究は実験室規模で実施されたものであり、産業環境で技術を検証するにはさらなる研究が必要です。研究は、将来の研究のためのいくつかの分野を示唆しています。
- 気孔率と密度分析: 中子の気孔率と密度、および浸出速度への影響を調査する。
- 相変化分析: 焼成サイクルを最適化するために、高温での中子材料の相変化を分析する。
- 商業生産と試験: さまざまな低融点合金を使用した商業鋳造環境で、中子組成[4]および[5]の生産規模を拡大し、試験する。
- より細かい溶融シリカ粉: 中子の仕上げ、強度、および希釈酸からの浸出をさらに改善するために、より細かい粉末グレードの溶融シリカの使用を検討する。
- クリープ特性: 高温での応力変形と長期性能の理解を深めるために、クリープ挙動を調査する。
- バインダーグレードのバリエーション: さまざまなバインダーグレード(Ludox HSおよびSK)が中子特性に及ぼす影響を調べる。
- 混合スラリーの射出プロセス最適化: より高い粒子充填とMORを達成するために、混合スラリーの射出プロセスを検討する。
8. 参考文献:
- [1. CAD Casting: Direct Fabrication of Ceramic Shells and Cores by Three Dimensional Printing, Sachs E B, Curodeau A D, Manufacturing Review (USA). Volume 5, p117-126, June 1992.]
- [2. Ceramic slurry composition for ceramic core of a dental prosthesis, Kim J D, Lee M H, Korean Science Technology, US patent 5975905, November 1999.]
- [3. Moulded ceramic cores for the production of precision cast impellers by the unicast process, Greenwood R E, Precision casting supplements, Foundry trade journal, p178-182, March 1984.]
- [4. Elements of material science and engineering, Van Vlack L H, Third edition, Addison- Wesley Publishing Company, 1975.]
- [5. Ceramic cores in the sand foundry, Greenwood R E, Cast metal times, p11-12, April 2002.]
- [6. Casting solutions Ltd, Robson B, Ceramic core and mould expert, Sheffield, February 2004.]
- [7. Principles of foundry technology, Jain P L, Second edtion, Tata McGraw Hill, 1996.]
- [8. Ferrous foundry-man’s handbook, Brown J, Elsevier, p18-20, July 2000.]
- [9. www.eos-gmbh.de/030356_appl_cm06.htm, 18 September 2006.]
- [10. http://www.core-tech-inc.com/form_ground.html, 18 September 2006.]
- [11. Properties of ceramic cores, Mills D, The British investment casters technical association, Fifteenth annual conference, 1980.]
- [12. Principle of metal casting, Heine R W, Loper C R, Philip C, Second edition, Tata McGraw-Hill, New Delhi,p121-175, 1976.]
- [13. http://www.enercombustion.com/EnServices.htm,19 September 2006.]
- [14. Methods of firing core, Altoonian M A, Runions R D, US patent 6403020-B1, p1-7, June 2002.]
- [15. Ceramic core; Nucleus for precision internal section, Greenwood R E, Unicast development corporation, Modern technology, p29-31, 1985.]
- [16. Alumina-based ceramics for core materials, Greskovich C D, US patent 4156614, GE company, p1-4, October 1977.]
- [17. Low temperature co-fired ceramic with improved registration, Shepherd P N, US patent 6560860-B2, CTS Corporation, p 1-6, January 2001.]
- [18. Injection molding of ceramic components provides flexibility in metal casting and forming, Uram S, Industrial heating, p42-43, 1987.]
- [19. Multipiece core assembly for cast airfoil, Sikkenga W E, Grumm A W, Howmet research corporation, US patent 6347660, February 2002.]
- [20. The effect of cristobalite seed on the crystallization of fused silica based ceramic core- A kinetic study, Wang L Y, ceramic international, p187-193, 1995.]
- [21. Printed materials on manufacturing fused silica, Minco Company, Midway, TN, USA, 2004.]
- [22. Dimensional changes and creep of silica core ceramics used in investment casting of supper alloys, Wereszczak A A, Breder K, Journal of material science, p 4235-4245, April 2002.]
- [23. Alumina core having a high degree of porosity and crushability characteristics, Klung F J, US patent 4164424, GE company, p1-12, August 1979.]
- [24. Basic inorganic chemistry, Cotton A, Gaus P L, Third Edition, Wiley J &sons Inc, p307-208, 1995.]
- [25. Printed material for calcium silicate and Lithium carbonate, Material safety data sheet, Sigma Aldrich Company, Pool,Doorset, UK, 2002.]
- [26. A textbook of quantitative inorganic analysis, Vogel A I, Second edition, Longmans, s1939.]
- [27. BPB gypsum special plasters, Data sheets on plasters, BS EN 9002:1994.]
- [28. Printed material data sheet for tri-sodium citrate, University of Teesside Chemistry online database, 2005.]
- [29. CRC handbook of chemistry and physics, Forty fourth edition, p2292.]
- [30. Ludox AM®, Colloidal silica data sheet, Grace division , Grace W R & Co, Worms, Germany, 2006.]
- [31. Water Soluble cores and methods for manufacturing cast rotor, Aiga T, Toshiaki M, US patent 4438804, March1984.]
- [32. Basic inorganic chemistry, Cotton A, Gaus P L, Third edition, Wiley J &sons Inc, p231-232, 1995.]
- [33. Inorganic Chemistry , An Intermediate Text, Wood C W, Holliday A K, Third Edition, Butterworth’s, 1967,p165-166.]
- [34. Standard test method for flexural strength of advanced ceramics at ambient temperature, ASTM Standard C1161.]
- [35. Materials handbook, Brady G S, Clauser H R, Vaccari J A, fifteenth edition, McGraw-Hill, 2002.]
- [36. http://www.qualitydigest.com/jan99/html/body_weibull.html,19 September 2007.]
- [37. Interpret the shape, scale, and threshold on a Weibull probability plot, ID766, Minitab help handbook.]
- [38. Weibull Analysis, Weibull W, Journal of applied mechanics, p293-297, 1951.]
- [39. Engineering materials 2, Ashby M F, Jones D R H, Third edition, Elsevier Publications, p196-197, 2006.]
- [40. Strength, fracture toughness and microstructure of a selection of all ceramic materials, Ringer S P, Swain M V, Dental materials, p441-448, June2004.]
- [41. Fracture toughness comparison of three test methods with four dental porcelains, Wang H, Pallav P, Dental materials, p905-910, July2007.]
- [42. Engineering Materials 2 , Ashby M F, Jones D R H, Third edition, Elsevier Publications, p198-199, 2006.]
- [43. Aluminum alloys- structures and properties, Mondolfo L f, Butterworths London and Boston, p971, 1976.]
- [44. Aluminum LM25 data sheet, MRT casting limited, Foundries and machinist for non-ferrous cast parts, www.mrt-castings.co.uk., 20th September 2007.]
- [45. 一般的に使用されるマグネシウム合金は、アルミニウム、亜鉛、マンガン、銅、シリコン、鉄、ニッケルを含む化学組成を持っています。]
- [46. 銅とその合金は、溶融金属から作られた最も初期の金属物体の1つでした。銅は天然金属として発見されたため、人工物に加工されてきました。銅生産の大部分は鉱石から来ており、主に銅含有量のために採掘されています。主な合金元素には、ニッケル、亜鉛、および異なる金属の組み合わせが含まれます。金、錫、亜鉛を含む銅とその合金の融点は、木炭火や木炭火で到達できる温度範囲内にあるほど十分に低いです。]
- [47. 銅鋳造合金は、優れた耐食性、電気伝導性、良好な軸受面品質、およびその他の特別な特性が望まれるサービスに指定されています。不純物の許容誤差は、通常、鋳造品の方が鍛造銅よりも大きくなります。]
- [48. 表 17. さまざまなアルミニウム鋳造プロセスの比較 (48)]
- [49. 圧力ダイカストは、すべての鋳造プロセスの中で最速であり、大量の同一部品が必要なスタンピング、ダイ鍛造、プラスチック射出成形と競合します。溶融金属は、高圧下で金型キャビティに押し込まれます。ホットチャンバー(金属がチャンバーに流れ込む)とコールドチャンバーは、圧力ダイカストで使用される2つのタイプの機械原理です。金属は、高速ジェットでゲートを通ってダイに入り、その寸法と速度は、ゲートとランナーの寸法によって異なります。このジェットは、ダイキャビティの反対側の面を叩き、すべての方向に広がり、ダイキャビティを急速に満たし、キャビティが満たされるにつれて乱流に分解します。凝固は圧力下で行われます。ダイ自体は通常、鋼鍛造品から機械加工され、複雑なキャビティには放電加工法が使用されます。]
- [50. アルミニウム、マグネシウム、銅ベース、およびその他の高融点合金は、コールドチャンバー原理(金属はチャンバーに注入されます)を使用します。圧力ダイカストを使用すると、製品の製造に必要な時間(組み立て)と費用(ツーリング)が削減されます。]
- [51. 砂型鋳造は、砂で形成された金型を使用して粗い金属鋳物を製造する手段であり、砂が圧縮されたら除去される鋳造対象物のレプリカの周りに形成されます。中型の「グリーン」砂型は、上部(コープ)と下部(ドラッグ)の2つの部分で構成されるフラスコに囲まれています。目的の鋳物の形状は、成形砂が形成されるパターンによってシミュレートされます。パターンは木材または金属で作られており、一緒に取り付けることができる2つの部分にもなっています。グリーンサンドは、ドラッグに配置されたパターンの半分弱の周りに突き固められます。同じプロセスが、スパー(ランナー)とゲート(ライザー)を備えたコープで実行されます。]
- [52. アルミニウム合金の砂型鋳造では、ガス含有量と結晶粒微細化の2つの特別な点に注意する必要があります。ガス含有量は、ブローホールや気孔の形成を避けるために、合理的に低いレベルに制御する必要があります。脱ガス錠剤(ヘキサクロロエタン)は、ガス含有量を制御するために使用されます。ゆっくりと冷却された鋳物では、大きな結晶が形成され、機械的特性が低下する傾向がある場合があります。チタンとホウ素の添加は、アルミニウム合金砂型鋳造における結晶粒微細化を防ぐことができます。]
- [53. 鋳造品の欠陥の形状と位置は、サイズよりも重要であることがよくあります。鋳造品の低応力領域にある大きな気孔は、高い引張応力を受ける鋭い角にある小さな「バイフィルム」よりもはるかに有害ではない可能性があります。ダイが摩耗しているか、しっかりとクランプされていない場合、フィンまたはフラッシュが発生する可能性があります。また、ランアウトが発生する可能性もあります。鋳造部品]
- [54. 図 8. (a) 中子ブロー (b) 凝固前の中子からのガスによる欠陥 (54)]
- [55. 1974年、英国鋳鉄研究協会(BCIRA)は、重度に中子入れされた鋳物の内部通路でCO2中子砂を「破砕療法」を使用して緩めることを報告しました。金属中子箱は、中子が大量生産される場合、またはより耐久性のある封じ込めが必要な場合に推奨されます。]
- [56. 超音波振動を利用して中子を除去する他の試みも行われてきました。最初の試みは、超音波振動のみを使用してタービンブレードから中子を除去することでした。これは、鋳物が浸漬された熱い苛性アルカリを通して生成および伝播される超音波の使用に発展し、機械的および化学的中子除去技術を組み合わせました。]
- [57. 大容量コンデンサバンクから生成された電気エネルギーも、集束させることができます。水中の衝撃波から部品に伝達される圧力波の強度は、セラミック中子自体の音響インピーダンスに依存するため、セラミック中子に使用される材料の強度を知る必要があります。]
- [58. 水流は、大きな圧力下で中子に焦点を当てており、中子は徐々に洗い流されています。この手順は、専用の施設またはブラスト室で行われます。「セラバイト」は、典型的な商用プロセスの例です。]
- [59. 図 7. 砂中子による砂型鋳造 (59)]
- [60. より細かい溶融シリカ粒子を使用すると、ミックスが改善され、滑らかな流動性、注ぎやすいスラリーが生成され、許容可能な凝固と木製中子箱からの取り外しが可能になりました。これらのコアは注型コアであるため、全体的な平均強度は、混合スラリーを加圧下でコアボックスに注入することによって作られるプリフォームコアよりも低くなります。]
- [61. 水は通常、バインダーとは考えられていません。最適な割合の水が中子混合物中に存在しない限り、バインダーと添加剤は適切に機能しません。十分な水を使用しないと、「シリアル」からのグリーン強度と低い引っかき硬さ、焼成後の低い引張強さが得られません。この要因により、水分子は強力なプロトン受容体になります。]
- [62. 異なる温度で焼成された中子のMORの変動は予想されます。]
- [63. 高い割合のバインダーをセラミック原料に添加すると、スラリーの流れが非常に滑らかで遅くなります。]
- [64. 酸化マグネシウムを使用すると、混合スラリーが非常に速く凝固します。コロイダルシリカを使用すると、4〜10分以内に熱水中で容易に凝固するセラミックスラリーが形成されます。]
- [65. セラミック中子の導入により、砂型鋳造所は、競争力のあるコストと短縮された時間で、滑らかで精密な内部キャビティを備えた恩恵を受けています。研究者らは、他の場所で6つの異なるシリカコアを1530〜1600℃で焼成し、最高温度で10〜30分間保持した後、室温まで冷却することを調べました。]
- [66. そのような軽合金用のセラミック中子システム。1回の焼成サイクルを持つセラミック中子は、主に1300℃以上で焼成されます。高温は、セラミック材料のより小さな寸法変化と硬化を確認します。]
- [67. 長さが単一の中心またはエッジクラックである半無限幅のプレートの場合、Y(a / W)は1.1です。セラミック材料のKIC値は、金属のKIC値よりも小さく、通常は10 MN√mよりも小さくなっています。通常、セラミックは線膨張係数が低い。セラミック材料に見られる強力な原子間結合力は、0.5〜15×10-6(℃あたり)の範囲の熱膨張係数の値を与えます。]
- [68. 酸化マグネシウムとリン酸カルシウムの中子は、シリカベースの中子の使用を避けるために超合金を鋳造するために使用されました。]
- [69. 75%の酸化マグネシウムと25%の塩化マグネシウムの混合物を使用してスラリーを形成しました。]
- [70. 軽金属および超合金の場合、希釈硝酸および水酸化カリウムなどの塩基が使用されます。中子試験の平均凝固時間は、トライアルCを除いて、あらゆる商業用途に理想的でした。]
- [71. 浸出速度は約10 mm / hで、密度は20〜25%です。]
- [72. ケイ酸カルシウム、塩化ナトリウム、塩化カリウム、メタケイ酸ナトリウムを添加して中子を製造します。]
- [73. 「グリーンキャスト」プロセスは、水溶性中子を使用して熱可塑性樹脂および熱硬化性樹脂から中空部品を製造するための新しいロストコア技術です。]
- [74. 酸は、水素イオンを塩基(プロトン受容体)に示すことができる物質です。]
- [75. 0.05%のMgOを添加したシリカ材料で製造されたセラミック中子は、合成アモルファスシリカ(バインダー)で2%の収縮を示しました。中子収縮の量は、中子材料スラリー中の合成アモルファスシリカの割合に正比例して変化します。]
- [76. シリカ(17%)、ジルコン(30%)、およびバインダー(コロイダルシリカゲル)で製造されたセラミック中子は、寸法で0.5%の収縮を示します。]
- [77. 表 3. 溶融シリカの特性 (77)]
- [78. 高度なセラミックの平面ひずみ破壊靭性は、3 MN m-3/2と低く、12 MN m-3/2と高くなる可能性があります。]
- [79. 3点曲げで半円形のノッチを持つ円形断面の「Y」を計算するために、閉形式解が開発されました。]
- [80. 亀裂またはノッチが切れ刃(鋭利)を持っている場合、応力集中度は低くなり、偽の値を与える可能性があります。]
- [81. リン酸水素ナトリウムをバインダーとして使用しました。]
- [82. 炭酸リチウムは重要な工業用化学物質です。シリカやその他の材料との低融点フラックスを形成します。]
- [83. いくつかの添加剤または促進剤の添加は、中子の凝固時間と強度を高めると主張されています。]
- [84. 標準温度および圧力では、解離した酸は、完全に解離している強酸とは対照的に、水溶液中の非解離型と平衡状態にあるため、弱酸と見なされます。]
- [85. 表 9. 酢酸の特性 (85)]
- [86. 水酸化ナトリウムは、水に溶解すると、熱を放出して非常に溶けやすくなります。]
- [87. 濃縮された水酸化カリウム水溶液は、水酸化カリウム「ライ」と呼ばれています。]
- [88. 1つのオートクレーブ技術では、鋳物を水性苛性溶液(例:45%KOH)に、昇圧および昇温(例:1.72 MN / m2および177℃)で、中子を鋳物から溶解または浸出させる適切な時間浸漬します。]
- [89. 模範的なオープンケトル技術では、鋳物を同様の水性苛性物質に浸漬します]
- [90. 超合金翼形鋳物の内部通路からセラミック中子材料を除去する方法。これは、鋳物の外側ルート表面の通路の開口部でスプレーノズルから水を含む加圧流体を排出することを含む。これは、加圧流体の排出がコンピュータ数値制御(CNC)マシンによって制御される。]
- [91. セラミックの脆い性質のため、手動ノッチまたは亀裂は、平均「6 mm」で比較的大きいものの、半円形であると想定されています。]
- [92. 無機バインダーによって示される典型的な欠点は、ケイ酸塩が中子や金型などの成形形状に提案されている結果、崩壊性が低く、金属鋳物からの成形形状の除去が不十分であることです。]
- [93. 溶融シリカは浸出に時間がかかり、酸化マグネシウムは混合スラリーを急速に凝固させるため、両方の材料の代替案が検討されています。]
- [94. 本プロジェクトでは、確立された水系中子技術を使用して中子形状を製造することを目指しますが、苛性ソーダよりも腐食性の低い浸出剤、例えば希釈酢酸を使用してアルミニウム合金鋳物から中子を除去できるように組成を修正することを目指します。]
- [95. 亜麻仁油ベースの有機バインダーが広く使用されています。それらは、良好な濡れ性と加工性の特性を提供するために、樹脂とシンナーを含んでいます。]
- [96. 実験計画法(例:タグチ)が評価されましたが、最終的には採用されませんでした。]
9. 著作権:
- この資料は、"[Manu Ramegowda]"の論文:「"[Development of water-based core technology for light alloys]"」に基づいています。
- 論文出典: http://tees.openrepository.com/tees/handle/10149/112685
この資料は上記論文を紹介するために作成されたものであり、商業目的での無断使用を禁じます。
Copyright © 2025 CASTMAN. All rights reserved.