본 기사에서는 [電気製鋼 (The Iron and Steel Institute of Japan)]에서 발행한 논문 ["다이캐스팅 및 용탕 침지 시험을 통한 표면 처리된 시편의 접합 평가"]를 소개합니다.
1. 개요:
- 제목: Evaluation of Soldering on Surface-Treated Specimens with both Actual Die Casting and Dipping Test into Molten Al Alloy (다이캐스팅 및 용탕 침지 시험을 통한 표면 처리된 시편의 접합 평가)
- 저자: Masamichi KAWANO
- 발행년도: 2021년
- 발행 학술지/학회: 電気製鋼, Vol.92, No.2, pp.87-92
- 키워드: 접합 거동, 표면 코팅, 다이캐스팅, 침지 시험, 코어 핀, 원형 봉 시편, 카보-질화, PVD 공정, 윤활제, 수용성 에멀젼 타입, 유성 타입, 염욕 질화
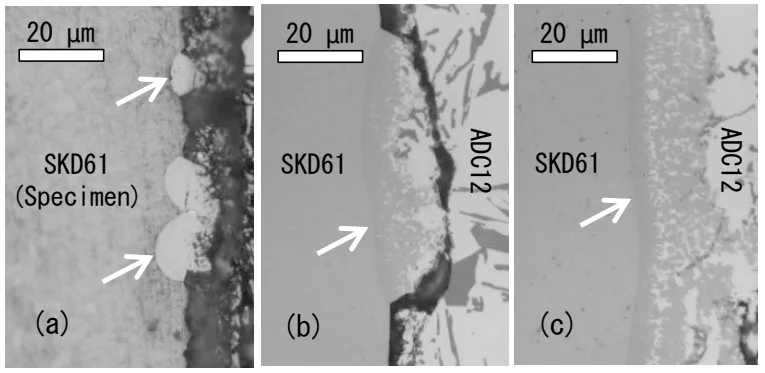
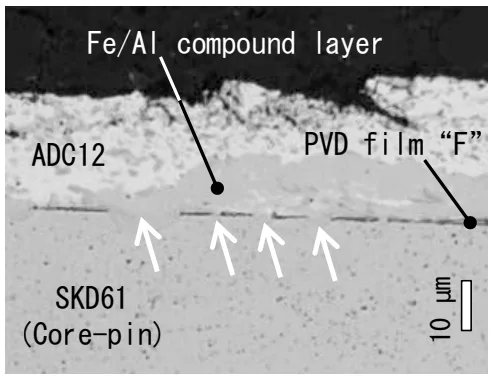
2. 초록 또는 서론
본 논문은 다이캐스팅 및 침지 시험에서 표면 코팅의 접합 거동을 조사합니다. 카보-질화 또는 PVD 공정으로 표면 처리된 코어 핀 및 원형 봉 시편을 평가했습니다. 다이캐스팅 실험에서 735°C의 용융 Al 합금을 54m/s의 속도로 코어 핀에 분사했습니다. 수용성 에멀젼 타입 및 유성 타입 윤활제를 사용했습니다. 코어 핀 표면 아래 1mm 지점의 최대 온도는 475°C에 도달했으며, 수용성 에멀젼 윤활제가 더 낮은 온도를 나타냈습니다. 18회의 다이캐스팅 샷 후 코어 핀의 접합은 표면 코팅 또는 윤활제와 관계없이 거의 동일했으며, 접합 계면에서 Fe/Al 화합물 층은 검출되지 않았습니다. 침지 시험에서 원형 봉 시편을 750°C의 용융 Al 합금에 30초 동안 담갔습니다. 염욕 질화는 PVD에 비해 우수한 내접합 성능을 보였습니다. 연구 결과, 다이캐스팅과 침지 시험에서의 접합 거동은 반드시 상관관계가 있는 것은 아닙니다.
본 논문의 서론에서는 다이캐스팅에서의 접합(소착)은 알루미늄 합금(Al 합금)이 금형에 부착되는 현상으로 정의하며, 이는 중요한 문제라고 강조합니다. 다이캐스트 제품의 접합은 표면 거칠기, 치수 부정확성과 같은 결함을 초래합니다. 심한 경우 광범위한 접합은 금형에서 제품을 꺼낼 수 없게 만듭니다. 따라서 접합 방지는 다이캐스트 제품의 품질 유지 및 안정적인 작동에 필수적입니다. 효과적인 대책으로는 (1) 금형 표면 온도 낮추기 및 (2) 금형 재료와 Al 합금 간의 직접적인 접촉 방지가 있습니다. 방법 (1)은 수질 관리를 통한 냉각수 유량 확보, 고압수 분사, 적층 제조를 이용한 복잡한 냉각 채널 설계 등 내부 냉각(内冷) 최적화를 포함합니다. 방법 (2)는 이형제 코팅(離型剤被膜) 및 산화물 또는 질화물로 구성된 경질 피막을 형성하는 표면 처리를 적용하는 것을 포함합니다. 용융 Al 합금(溶湯浸漬) 침지 시험은 일반적으로 접합 저항성을 평가하기 위해 사용되며, 시편에 부착된 Al 합금의 양을 육안으로 평가합니다. 이 비용 효율적인 방법은 다이캐스팅 응용 분야를 위한 표면 처리를 스크리닝하고 개발하는 데 매우 중요합니다. 본 논문은 다이캐스팅 및 침지 시험에서 다양한 표면 처리 간의 접합 저항성 순위를 비교하고, 용융 금속 흐름(湯流れ) 및 압력이 접합 거동에 미치는 영향과 함께 다양한 이형제 유형으로 인한 금형 온도 변화의 영향을 조사하는 것을 목표로 합니다.
3. 연구 배경:
연구 주제의 배경:
다이캐스팅에서의 접합은 알루미늄 합금(Al 합금)이 금형에 부착되는 현상으로 설명됩니다. 이 부착은 거친 표면 및 치수 부정확성을 포함하여 주조 제품에 결함을 초래합니다. 심한 경우 광범위한 접합으로 인해 금형에서 주물을 꺼낼 수 없게 됩니다. 따라서 접합 방지는 다이캐스트 제품의 품질을 유지하고 안정적인 다이캐스팅 작업을 보장하는 데 가장 중요합니다.
기존 연구 현황:
접합을 완화하기 위한 기존 전략은 크게 두 가지 접근 방식으로 분류됩니다. (1) 금형 표면 온도 낮추기 및 (2) 금형 재료와 용융 Al 합금 간의 직접적인 접촉 방지. 접근 방식 (1)은 수질 관리를 통해 적절한 냉각수 흐름을 보장하고, 고압수 분사를 사용하고, 적층 제조로 제작된 복잡한 냉각 회로를 활용하는 등 내부 냉각(内冷)을 최적화하는 것을 포함합니다. 접근 방식 (2)는 이형제 코팅(離型剤被膜) 및 산화물 또는 질화물로 구성된 경질 피막을 금형 표면에 생성하는 표면 처리를 적용하는 데 중점을 둡니다. 용융 Al 합금(溶湯浸漬) 침지 시험은 표면 처리의 접합 저항성을 평가하기 위해 널리 사용됩니다. 접합 저항성의 정도는 시험편에 부착된 Al 합금의 양을 육안으로 검사하여 쉽게 평가할 수 있습니다. 침지 시험은 다이캐스팅 응용 분야를 위한 표면 처리를 선택하기 위한 효율적이고 비용 효율적인 스크리닝 방법으로 사용됩니다.
연구의 필요성:
침지 시험은 표면 처리를 스크리닝하는 데 유용하지만, 침지 시험에서 관찰된 접합 거동과 실제 다이캐스팅 공정 간의 상관관계는 완전히 이해되지 않았습니다. 본 연구는 다이캐스팅 및 침지 시험 조건 모두에서 다양한 표면 처리의 접합 저항성 순위를 비교하여 이러한 격차를 해소하는 것을 목표로 합니다. 또한, 본 연구는 다이캐스팅 공정에 내재된 용융 금속 흐름(湯流れ) 및 압력이 접합 거동에 미치는 영향을 조사합니다. 또한 이형제 유형이 금형 온도에 미치는 영향과 그에 따른 접합 거동에 미치는 영향도 조사합니다.
4. 연구 목적 및 연구 질문:
연구 목적:
본 연구의 주요 목적은 다이캐스팅 및 침지 시험을 사용하여 평가할 때 다양한 표면 처리의 접합 저항성 순위를 비교하는 것입니다. 또한, 본 연구는 다이캐스팅 공정 내에서 용융 금속 흐름(湯流れ) 및 압력이 접합 현상에 미치는 영향을 규명하는 것을 목표로 합니다. 이형제 유형이 금형 온도에 미치는 영향과 그에 따른 접합 거동에 미치는 영향도 조사합니다.
핵심 연구 질문:
- 다이캐스팅과 침지 시험 간의 표면 처리의 접합 저항성 순위를 비교합니다.
- 다이캐스팅에서 용융 금속 흐름 및 압력이 접합에 미치는 영향을 조사합니다.
- 이형제 유형과 그에 따른 금형 온도 변화가 접합에 미치는 영향을 조사합니다.
5. 연구 방법론
연구 설계:
본 연구에서는 표면 처리된 시편의 접합 거동을 평가하기 위해 실제 다이캐스팅 및 침지 시험을 모두 활용하는 비교 실험 설계를 채택했습니다.
데이터 수집 방법:
- 다이캐스팅 시험: 시바우라 기계(주)에서 제조한 135톤 다이캐스팅 기계를 사용하여 다이캐스팅 실험을 수행했습니다. 주조 조건은 표 1에 자세히 설명되어 있습니다. 735°C의 용융 ADC12 합금을 게이트에서 20mm 떨어진 코어 핀에 직접 충돌하도록 분사했습니다. 이 코어 핀은 접합 평가를 위한 시편으로 사용되었습니다. 온도 측정은 일체형 코어 핀(一体ピン) 표면 아래 1mm 지점에 내장된 열전대를 사용하여 수행했습니다. 시판되는 두 가지 유형의 다이 이형제를 사용했습니다: 유성 타입 "R" 및 수용성 에멀젼 타입 "M".
- 침지 시험: 침지 시험의 경우 코어 핀과 동일한 표면 처리가 된 SKD61 강철로 만든 원형 봉 시편(Ø10 mm x 60 mm)을 사용했습니다. 시편을 이형제를 미리 도포하지 않고 750°C의 용융 ADC12 합금에 30초 동안 담갔습니다. 30초 후 시편을 꺼내어 상온까지 공랭했습니다.
분석 방법:
접합 거동은 주로 다이캐스팅 및 침지 시험 후 시편의 육안 검사 및 사진 기록을 통해 평가했습니다. 침지 시험에서 접합은 부착된 ADC12 합금이 문지르면 쉽게 제거되는지 또는 단단히 부착되어 있는지 여부에 따라 결정했습니다. 접합 계면 및 코팅 피막 상태를 분석하기 위해 접합된 부분의 단면을 현미경으로 관찰했습니다. 다이캐스팅 실험에서 얻은 온도 데이터를 분석하여 이형제 유형이 코어 핀 온도에 미치는 영향을 평가했습니다.
연구 대상 및 범위:
본 연구는 SKD61 다이강(46HRC)에 적용된 4가지 표면 처리, 즉 3가지 유형의 PVD(물리적 기상 증착) 코팅("A", "B", "C"로 식별)과 1가지 염욕 질화 처리("D")를 평가하는 데 중점을 두었습니다. 처리되지 않은 SKD61도 기준선으로 사용했습니다. 사용된 용융 합금은 ADC12였습니다. 다이캐스팅 실험에서는 유성 타입 "R" 및 수용성 에멀젼 타입 "M" 이형제를 모두 사용했습니다.
6. 주요 연구 결과:
핵심 연구 결과:
- 다이캐스팅 시험: 18회의 다이캐스팅 샷 후 표면 처리 또는 이형제 종류에 관계없이 코어 핀에서 접합이 발생했습니다. 육안 검사 및 단면 분석(그림 7, 그림 8) 결과, 접합 부위에서 표면 처리 피막이 사라지지 않았고, Fe/Al 화합물 층 형성도 관찰되지 않았습니다. ADC12 합금은 표면 처리 피막에 물리적으로 부착된 것으로 보입니다. 수용성 에멀젼 윤활제 "M"은 유성 타입 윤활제 "R"에 비해 코어 핀 온도를 낮추는 결과를 가져왔습니다(그림 4, 그림 5, 그림 6).
- 침지 시험: 침지 시험에서 염욕 질화("D")는 PVD 코팅에 비해 우수한 내접합 성능을 보였습니다(그림 10). 표면 처리 간의 접합 저항성 순위는 침지 시험과 다이캐스팅 시험 간에 상당한 차이를 보였습니다.
- 온도 측정: 다이캐스팅 중 코어 핀 온도 측정 결과, 수용성 이형제 "M"이 유성 타입 "R"보다 코어 핀 온도 감소에 더 효과적인 것으로 나타났습니다(그림 5, 그림 6).
제시된 데이터 분석:
- 그림 4: 비코팅 코어 핀 표면 아래 1mm 지점의 과도 온도 변화를 보여줍니다. 유성 타입 윤활제 "R"과 수용성 에멀젼 윤활제 "M"을 사용했을 때, 그리고 내부 냉각 유무에 따른 온도 차이를 보여줍니다.
- 그림 5 & 6: 용융 ADC12 온도 및 윤활제 유형과 관련된 비코팅 코어 핀의 최소 및 최대 온도를 나타냅니다. 이 그림들은 수용성 윤활제 "M"과 내부 냉각의 온도 감소 효과를 보여줍니다.
- 그림 7: 18회의 다이캐스팅 샷 후 코팅된 코어 핀의 외관을 보여줍니다. 모든 표면 처리 및 윤활 조건에서 접합이 발생했음을 시각적으로 보여줍니다.
- 그림 8: 18회의 다이캐스팅 샷 후 접합된 부분의 단면도를 보여줍니다. Fe/Al 화합물 층이 없음을 확인하고 ADC12가 표면 처리 피막에 물리적으로 부착되어 있음을 나타냅니다.
- 그림 9: 윤활제 "R"을 사용한 다이캐스팅 전후의 질화 "D" 및 PVD 코팅 "B"의 코팅 피막을 비교합니다. 18회 샷 후 질화층의 산화 피막 두께가 감소한 것을 보여주며, 이는 용융 금속 흐름으로 인한 침식을 시사합니다.
- 그림 10: 용융 ADC12에 침지 후 코팅된 원형 봉 시편의 외관을 보여줍니다. 표면 처리에 따라 접합량의 차이를 보여주며, 질화 "D"가 가장 적은 접합을 나타냅니다.
그림 목록:
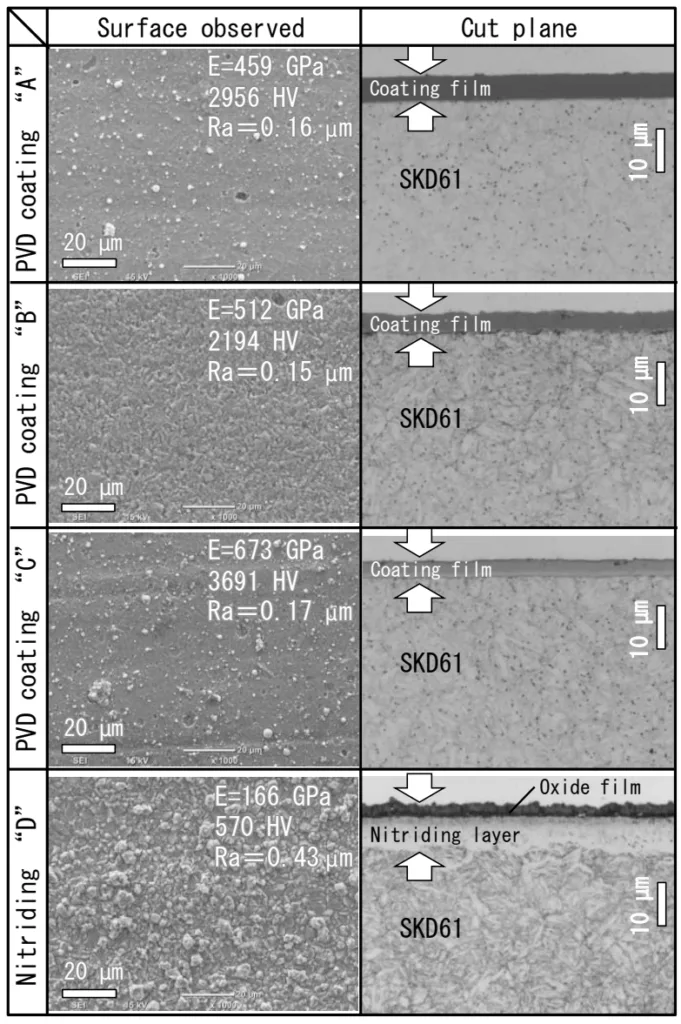
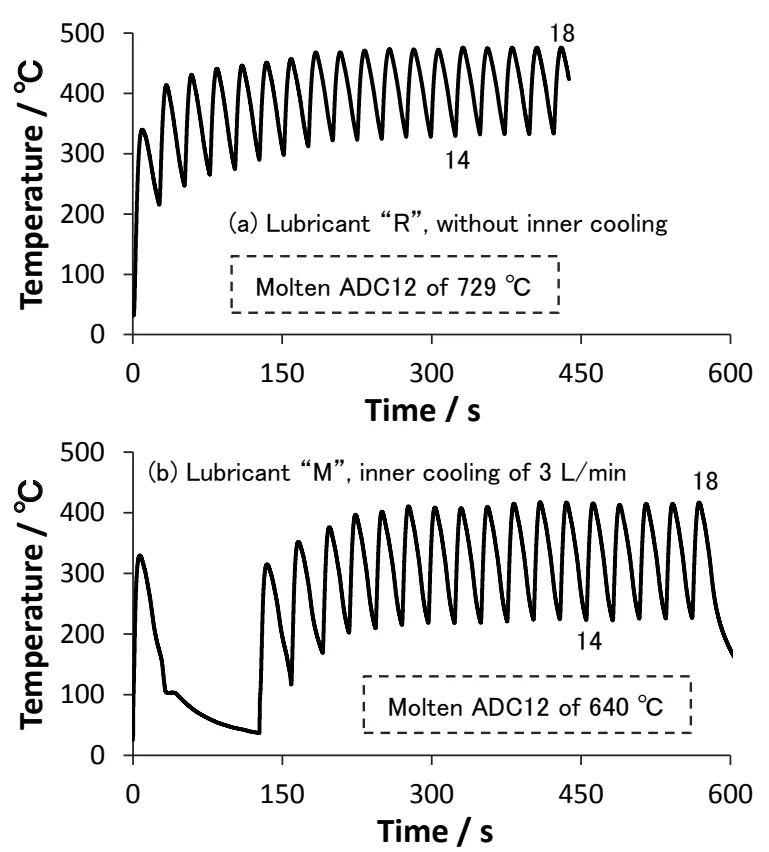
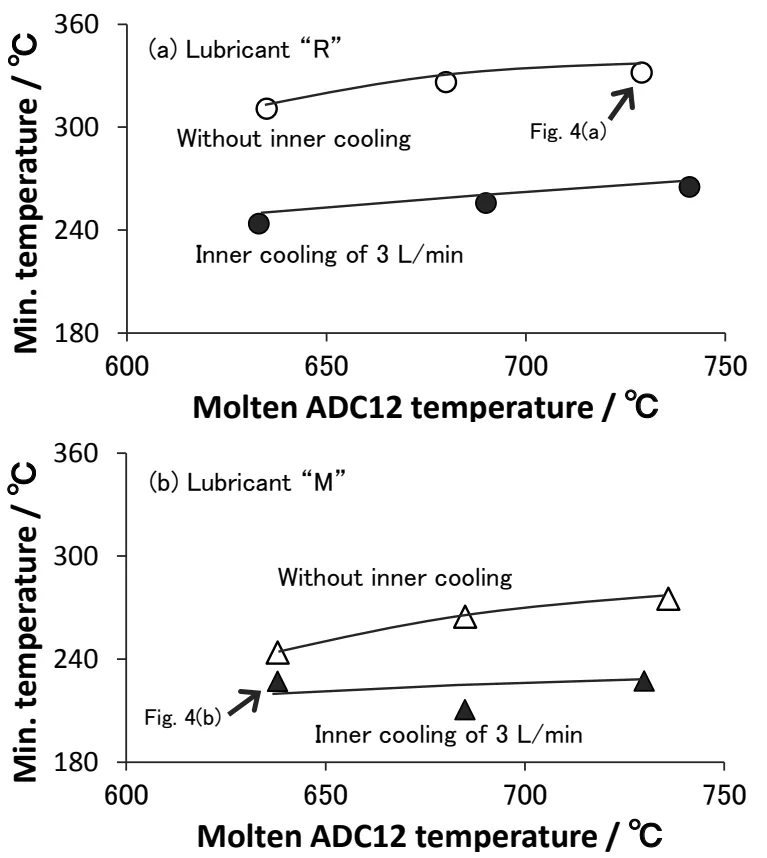
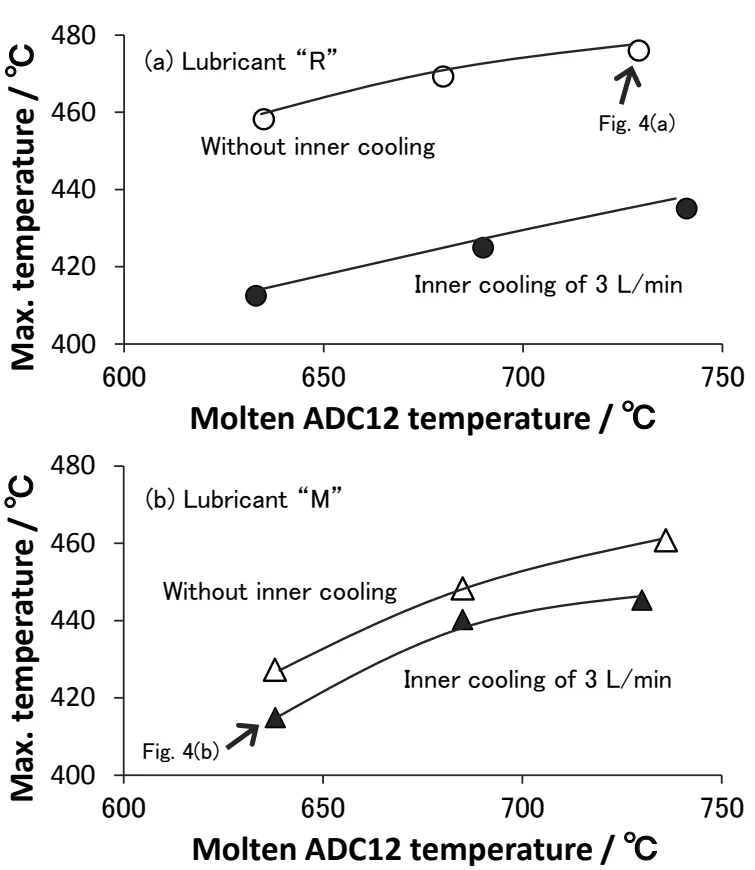
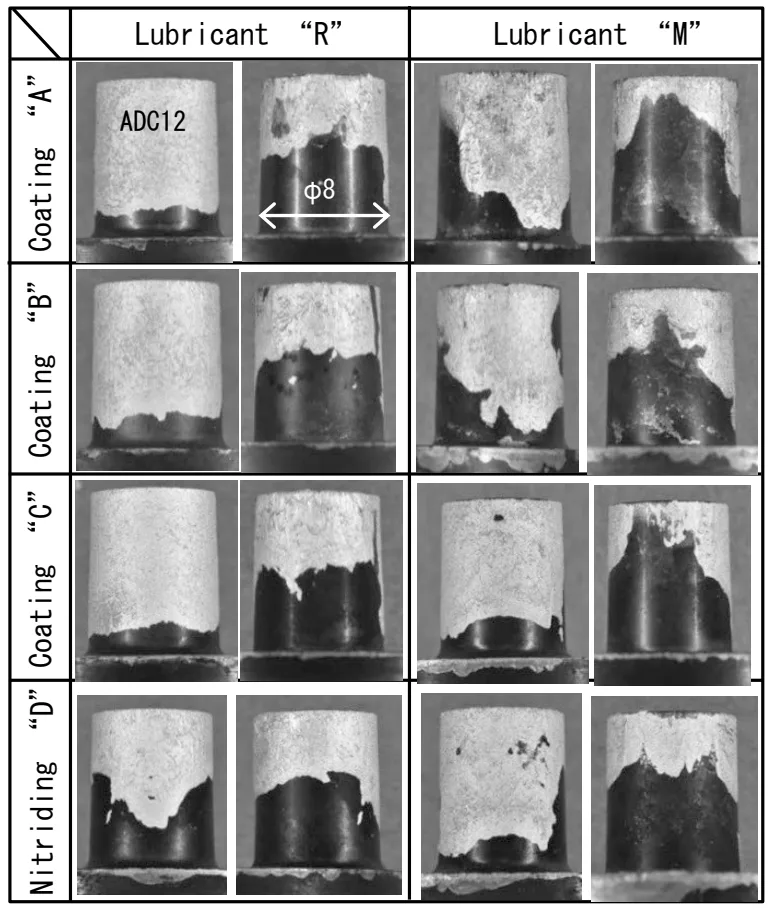
- Fig. 1. Initiation of soldering observed on dipping test into molten ADC12. (용융 ADC12에 침지 시험 시 관찰된 접합 시작)
- Fig. 2. Soldering observed on die-cast after 2000 shots. (2000회 샷 후 다이캐스트에서 관찰된 접합)
- Fig. 3. Four surface treatments for SKD61 of 46HRC. (46HRC SKD61에 대한 4가지 표면 처리)
- Fig. 4. Temperature transient at 1 mm below surface of non-coated core-pin. (비코팅 코어 핀 표면 아래 1mm 지점의 과도 온도 변화)
- Fig. 5. The minimum temperature of non-coated core-pin related to Fig. 4. (그림 4와 관련된 비코팅 코어 핀의 최소 온도)
- Fig. 6. The maximum temperature of non-coated core-pin related to Fig. 4. (그림 4와 관련된 비코팅 코어 핀의 최대 온도)
- Fig. 7. Appearance of coated core-pins after 18 shots. (18회 샷 후 코팅된 코어 핀의 외관)
- Fig. 8. Observation of cut plane at soldered part after 18 shots. (18회 샷 후 접합된 부분의 단면 관찰)
- Fig. 9. Comparison of coating film between before and after casting with lubricant "R". (윤활제 "R"을 사용한 다이캐스팅 전후의 코팅 피막 비교)
- Fig. 10. Appearance of coated round bar specimens after dipping into molten ADC12. (용융 ADC12에 침지 후 코팅된 원형 봉 시편의 외관)
7. 결론:
주요 연구 결과 요약:
본 연구 결과, 표면 처리의 접합 저항성 순위는 다이캐스팅과 침지 시험 간에 차이가 있는 것으로 나타났습니다. 다이캐스팅에서는 18회 샷 후 표면 처리 또는 이형제 종류에 관계없이 상당한 접합이 발생했습니다. 수용성 에멀젼 윤활제는 코어 핀 온도를 효과적으로 낮췄습니다. 반대로 침지 시험에서는 염욕 질화가 PVD 코팅에 비해 우수한 내접합 성능을 보였습니다. 두 시험 방법 간의 접합 거동 차이는 용융 금속 흐름 속도 및 압력의 차이로 인한 것으로 판단됩니다.
연구의 학문적 의의:
본 연구는 다이캐스팅과 침지 시험 간의 접합 평가의 차이점을 명확히 하고, 접합 현상에서 공정 조건, 특히 용융 금속 흐름 및 압력의 중요한 역할을 강조합니다. 침지 시험만으로는 실제 다이캐스팅 환경에서 발생하는 복잡한 접합 메커니즘을 완전히 나타내지 못할 수 있음을 시사합니다.
실용적 의미:
본 연구 결과는 실제 다이캐스팅 응용 분야에서 표면 처리의 접합 성능을 예측할 때 침지 시험 결과를 신중하게 해석해야 함을 시사합니다. 표면 처리 선택 시 용융 금속 흐름 및 압력과 같은 다이캐스팅 특유의 요소를 고려해야 합니다. 또한, 본 연구는 수용성 윤활제가 다이캐스팅 부품 온도를 낮추는 데 효과적이며, 이는 접합 완화에 도움이 될 수 있음을 확인합니다.
연구의 한계 및 향후 연구 분야:
본 연구는 제한된 표면 처리 세트와 특정 다이캐스팅 조건에 초점을 맞추었습니다. 더 넓은 범위의 표면 처리 및 다양한 사출 속도 및 압력을 포함한 다이캐스팅 매개변수를 조사하기 위한 추가 연구가 권장됩니다. 흐름 속도와 압력이 접합에 미치는 개별적인 기여도를 정량화하고, 확장된 다이캐스팅 사이클에 걸쳐 접합 거동을 탐색하는 것도 향후 연구 분야로 제안됩니다.
8. 참고 문헌:
- 1) 向川博, 樋口博, 小野英敏, 金子博志: 2004日本ダイカスト会議論文集,(2004), 25.
- 2) 古川雄一, 佐藤理通, 古倉冬彦, 植林秀悟: 2004日本ダイカスト会議論文集, (2004), 63.
- 3) 井戸信介: 型技術, 28(2013), 3, 30.
- 4) 野村康弘, 深見尚男, 小林竜之, 早藤哲典: 2016日本ダイカスト会議論文集,(2016), 35.
- 5) 木村有貴, 佐藤良輔, 鈴木将宏, 植田真広, 井川秀昭, 工藤英弘: 豊田自動織機技報, 70(2019), 83.
- 6) 前原一仁, 早藤哲典, 小林竜之: 2018日本ダイカスト会議論文集,(2018),75.
- 7) 河田一喜, 木立徹: 2016日本ダイカスト会議論文集, (2016), 7.
- 8) 石塚はる菜, 高村宏, 渡邊陽一: 2018日本ダイカスト会議論文集,(2018),11.
- 9) 横井直樹, 河野正道, 保母誠: 型技術者会議 2011 講演論文集,(2011), 202.
- 10) 河野正道, 宇野聡, 横井直樹: 2016日本ダイカスト会議論文集,(2016), 53.
- 11) 佐々木英人: 素形材, 51(2010), 10, 29.
- 12) (株)青木科学研究所「ダイカスト用原液塗布型油性離型 WFR series」(http://www.lubrolene.co.jp/industrials/wfr.html)
9. 저작권:
- 본 자료는 "Masamichi KAWANO"의 논문: "Evaluation of Soldering on Surface-Treated Specimens with both Actual Die Casting and Dipping Test into Molten Al Alloy"를 기반으로 작성되었습니다.
- 논문 출처: 電気製鋼, Vol.92, No.2, pp.87-92, 2021.
본 자료는 위 논문을 소개하기 위해 제작되었으며, 상업적 목적으로 무단 사용하는 것을 금지합니다.
Copyright © 2025 CASTMAN. All rights reserved.