본 기사에서는 ['전기 제강']에서 발행한 논문 ["수치 해석을 통한 다이캐스팅 금형 표면의 이젝팅 응력 분포 예측 및 평가"]를 소개합니다.
1. 개요:
- 제목: 수치 해석을 통한 다이캐스팅 금형 표면의 이젝팅 응력 분포 예측 및 평가 (Prediction and Evaluation of Ejecting Stress Distribution at Die Surface of Die-Casting through Numerical Analyses)
- 저자: Masamichi KAWANO, Satoshi UNO and Naoki YOKOI
- 발행 연도: 2017년
- 발행 학술지/학회: 전기 제강, Vol. 88, No. 1, pp. 33-38 (電気製鋼, Vol. 88, No. 1, pp. 33-38)
- 키워드: 다이캐스팅, 이젝팅 응력, 솔더링, 수치 해석, MAGMASOFT, Fe-Al 화합물 층, AMICOAT®-D (Die casting, Ejecting stress, Soldering, Numerical analysis, MAGMASOFT, Fe-Al compound layer, AMICOAT®-D)
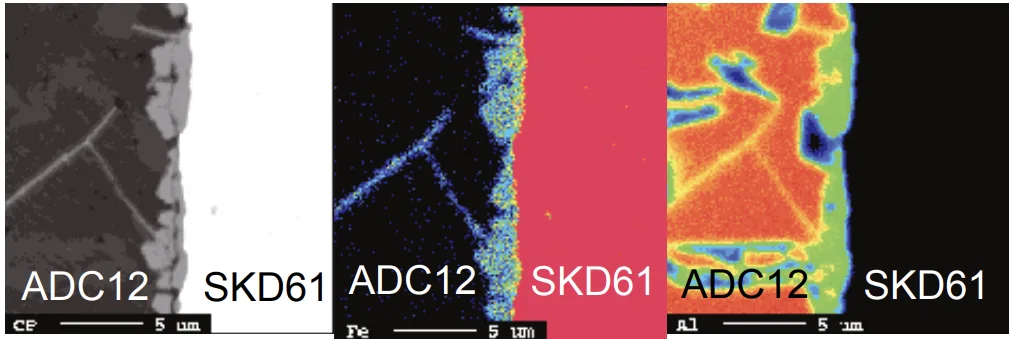
2. 초록/서론
다이캐스팅 주조법은 알루미늄 합금과 같은 용융 금속(이하, 용탕)을 금형 캐비티 내에 단시간에 압입하여 급속 응고시켜 치수 정밀도가 높은 복잡 형상 부품을 고효율로 제조하는 방법입니다. 그러나 다이캐스팅 금형의 캐비티 면은 600~700℃의 용탕과의 접촉으로 인해 450~550℃까지 가열될 수 있습니다. 이러한 고온 부위에서는 주조품 취출 시 알루미늄 합금이 금형에 용착되어 잔류하는 "소착(soldering)"이 발생하기 쉽습니다. 소착 부위에서는 주조품과 금형의 계면에 Fe/Al 반응층이 형성됩니다.
소착은 제품의 표면 품질 및 치수 정밀도를 저해합니다. 금형에 부착된 알루미늄 합금을 제거하기 위해서는 주조 일시 중단이 불가피하여 생산성이 크게 저하됩니다. 심각한 소착은 제거가 어려워 금형 교체가 필요할 수도 있으며, 이는 금형 비용 증가로 이어집니다. 따라서 소착 방지는 다이캐스팅의 중요한 과제입니다. 주조 계획 수립 시 소착 발생 가능성이 높은 부위를 파악하고 소착 방지 대책을 마련하는 것이 필수적입니다.
소착에 영향을 미치는 요인은 표면 처리 종류, 내부 냉각 채널 위치 및 유량, 용탕 온도, 사출 조건 등 다양합니다. 이러한 요인을 주조 시행착오를 통해 최적화하는 것은 비효율적이며 최적 해법을 얻기 어려울 수 있습니다. 따라서 조건 변화를 체계적이고 용이하게 할 수 있는 용탕 흐름 해석은 소착 방지 대책 연구에 적극적으로 활용됩니다.
용탕 흐름 해석 기반 소착 방지 대책 연구에서는 공정 설계 정확도를 높이기 위해 야금 현상, 특히 Fe/Al 반응층 형성에 기반한 지표가 필요합니다. 따라서 본 논문에서는 주조품을 금형에서 꺼낼 때의 "이젝팅 응력"에 초점을 맞추고 이를 반응층 형성과 연관시키고자 합니다. 본 논문에서는 실험적으로 도출된 이젝팅 응력 예측 공식을 용탕 흐름 해석 소프트웨어에 통합하여 소착 평가 지표로서의 유효성을 검증하고자 합니다.
3. 연구 배경:
연구 주제의 배경:
다이캐스팅에서 소착은 제품 품질과 치수 정밀도를 손상시키고, 금형에서 알루미늄 제거를 위한 생산 중단을 야기하며, 잠재적으로 비용이 많이 드는 금형 교체로 이어질 수 있기 때문에 중요한 문제입니다. 따라서 소착 방지는 다이캐스팅 작업에서 매우 중요한 목표입니다. 소착이 발생하기 쉬운 영역을 식별하고 효과적인 대책을 구현하는 것은 견고한 공정 설계를 위해 필수적입니다.
기존 연구 현황:
기존의 소착 완화 접근 방식은 종종 비효율적인 시행착오를 통한 주조 변수 조정에 의존합니다. 용탕 흐름 해석이 소착 방지 대책을 탐색하는 데 점점 더 많이 사용되고 있지만, 이러한 방법은 종종 소착의 야금학적 메커니즘에 근거한 정량적으로 견고한 지표가 부족합니다. 주조 시험을 통한 최적화는 비효율적이며 최적의 해결책으로 이어지지 않을 수 있습니다. 용탕 흐름 해석은 소착 방지 대책 검토를 위해 조건을 체계적이고 쉽게 변경하는 데 적극적으로 사용됩니다.
연구의 필요성:
소착 방지 대책을 위한 용탕 흐름 해석을 사용한 공정 설계의 정확성을 개선하려면 야금 현상, 특히 Fe/Al 반응층 형성에 부합하는 지표가 필요합니다. 다이캐스팅 인터페이스에서의 근본적인 야금 반응을 기반으로 소착 정도를 반영하는 신뢰할 수 있는 지표가 필요합니다.
4. 연구 목적 및 연구 질문:
연구 목적:
본 연구의 목적은 소착의 근본 원인인 Fe/Al 반응층 형성을 기반으로 다이캐스팅 금형 표면의 이젝팅 응력 분포를 예측하고 평가하는 방법을 개발하는 것입니다. 실험적으로 도출된 이젝팅 응력 공식을 용탕 흐름 해석 소프트웨어에 통합함으로써 이 연구는 이젝팅 응력을 소착 가능성 평가를 위한 효과적인 지표로 검증하는 것을 목표로 합니다.
핵심 연구 질문:
핵심 연구 질문은 이젝팅 응력을 다이캐스팅의 소착 위험을 평가하기 위한 정량적 지표로 확립하는 것입니다. 여기에는 다음이 포함됩니다.
- Fe/Al 반응층 형성을 기반으로 이젝팅 응력을 예측하는 공식 도출.
- 이 공식을 용탕 흐름 해석에 통합.
- 수치 해석 및 실험적 검증을 통해 이젝팅 응력을 소착에 대한 신뢰할 수 있는 지표로 검증.
5. 연구 방법론
연구 설계:
본 연구에서는 MAGMASOFT 소프트웨어를 사용한 수치 해석적 접근 방식을 채택하여 다이캐스팅 중 용탕 흐름 및 온도 분포를 시뮬레이션했습니다. Fe/Al 화합물 층 형성을 기반으로 도출된 이젝팅 응력 공식을 소프트웨어에 통합하여 금형 표면의 이젝팅 응력 분포를 예측했습니다.
데이터 수집 방법:
이젝팅 저항을 정량화하기 위해 135톤 Toshiba Machine DC-135JT 다이캐스팅 기계를 사용하여 실험을 수행했습니다. SKD61로 만든 코어 핀 모양의 시편을 사용하고 ADC12 알루미늄 합금을 주조했습니다. 열전쌍을 코어 핀 표면 근처에 삽입하여 온도를 측정했습니다. 이젝팅 하중은 이젝터 핀 뒷면의 로드 셀을 사용하여 측정했습니다.
분석 방법:
이젝팅 저항 F (MPa)는 이젝터 핀의 표면적으로 이젝팅 하중 PN (로드 셀로 측정)을 나누어 계산했습니다. 소착 파라미터 S는 Fe/Al 반응층 형성과 관련하여 시간 경과에 따른 exp(-Q/R/Ts)의 적분을 사용하여 계산했습니다. 소착 파라미터 S와 이젝팅 응력 F 사이의 상관 관계를 분석했습니다. FEM (유한 요소법) 분석을 사용하여 열전쌍 측정값과 열 분석 결과를 연관시켜 표면 온도 Ts를 추정했습니다.
연구 대상 및 범위:
본 연구는 다이캐스팅에 일반적으로 사용되는 SKD61 다이강과 ADC12 알루미늄 합금 사이의 계면에 초점을 맞추었습니다. 연구 범위는 용융 금속 온도, 금형 냉각 및 표면 처리와 같은 다양한 다이캐스팅 조건에서 금형 표면의 이젝팅 응력을 예측하고 평가하는 것이었습니다.
6. 주요 연구 결과:
핵심 연구 결과:
- 이젝팅 응력 공식 도출: SKD61과 ADC12 사이의 경계면에서 Fe-Al 화합물 층 형성을 고려하여 금형 표면의 이젝팅 응력에 대한 방정식을 도출했습니다. Fe-Al 반응에 대한 활성화 에너지 Q는 313 kJ/mol로 추정되었습니다.
- 주조 조건의 영향: 수치 해석 결과, 낮은 용융 ADC12 온도와 내부 수로를 사용한 금형 냉각이 이젝팅 응력을 효과적으로 감소시키는 것으로 나타났습니다.
- 표면 처리 효과: "AMICOAT®-D" 표면 처리의 경우 내부 수냉각이 없는 고온 용융 ADC12 조건에서도 이젝팅 응력이 현저히 감소하는 것으로 관찰되었습니다.
- S와 F의 상관 관계: 소착 파라미터 S (Fe/Al 반응층 두께와 관련)와 이젝팅 응력 F 사이의 명확한 양의 상관 관계가 F = C1⋅SC2 공식으로 표현되어 확립되었습니다.
제시된 데이터 분석:
- 그림 3: (a) 이젝팅 하중 P와 (b) 이젝팅 응력 F의 차이를 보여줍니다. 코어 핀 표면적으로 보정된 이젝팅 응력 F는 소착 심각도에 대한 크기 독립적인 척도를 제공합니다. 그림 3(b)는 소착에 대한 온도 민감 영역을 나타내며, 이젝팅 응력은 약 432°C 부근에서 14°C 온도 상승으로 5 MPa에서 10 MPa로 두 배 증가합니다.
- 그림 5: (a) 표면 온도 Ts와 (b) 소착 파라미터 S=∫(exp(-Q/R/Ts))dt의 전환 변화를 보여줍니다. Fe/Al 반응과 관련된 통합 열 이력을 나타내는 소착 파라미터 S는 이젝팅 응력과 상관 관계가 있는 것으로 나타났습니다.
- 그림 6: 소착 파라미터 S와 이젝팅 응력 F 사이의 관계를 보여줍니다. 염욕 질화 (PS) 및 PVD (AMICOAT®-D)와 같은 표면 처리는 비처리 대비 이젝팅 응력을 크게 감소시킵니다.
- 그림 9: 다양한 조건에서 주조 이젝팅 응력 F의 분포를 보여줍니다. 그림 9(a) (700°C 용융 금속, 냉각 없음)는 가장 높은 이젝팅 응력을 나타냅니다. 용융 금속 온도를 650°C로 낮추고 (그림 9(b)), 수냉각을 적용하고 (그림 9(c)), AMICOAT®-D 표면 처리를 사용하면 (그림 9(d)) 모두 이젝팅 응력이 효과적으로 감소합니다.
그림 목록:
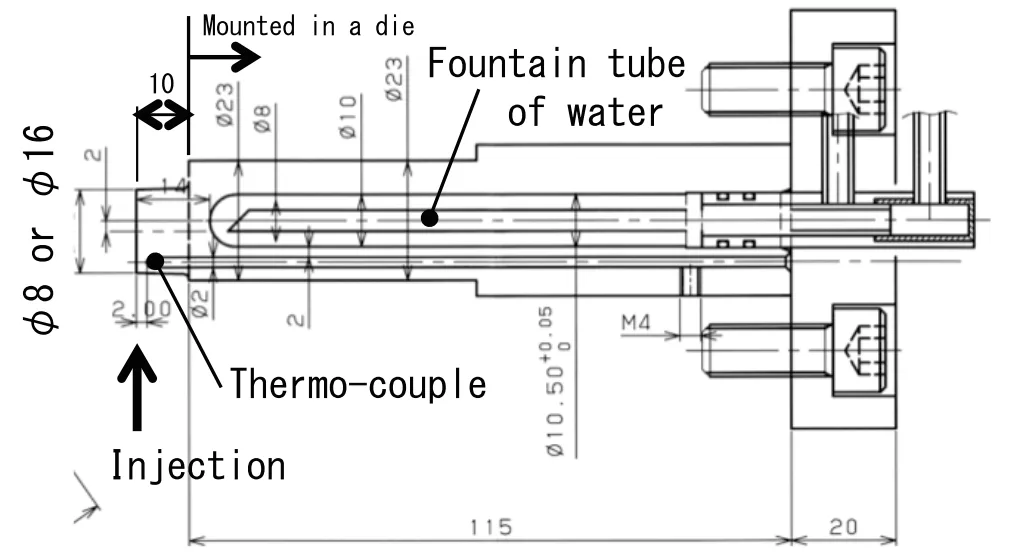
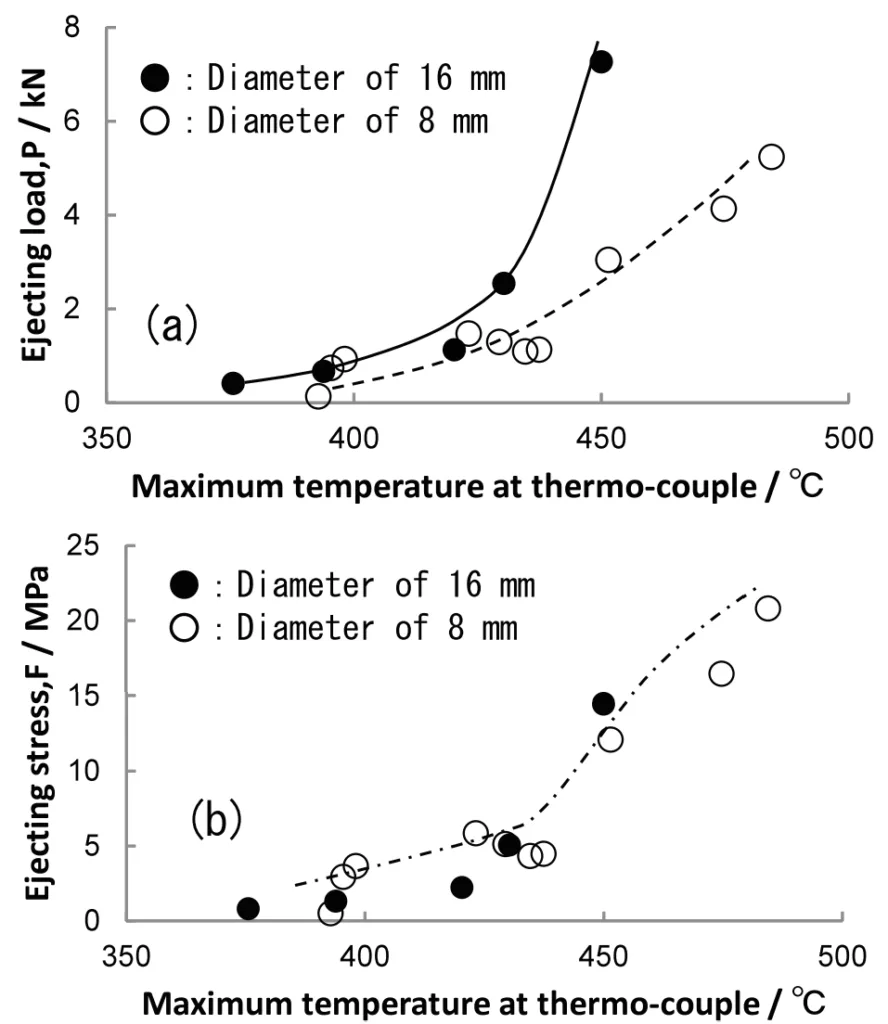

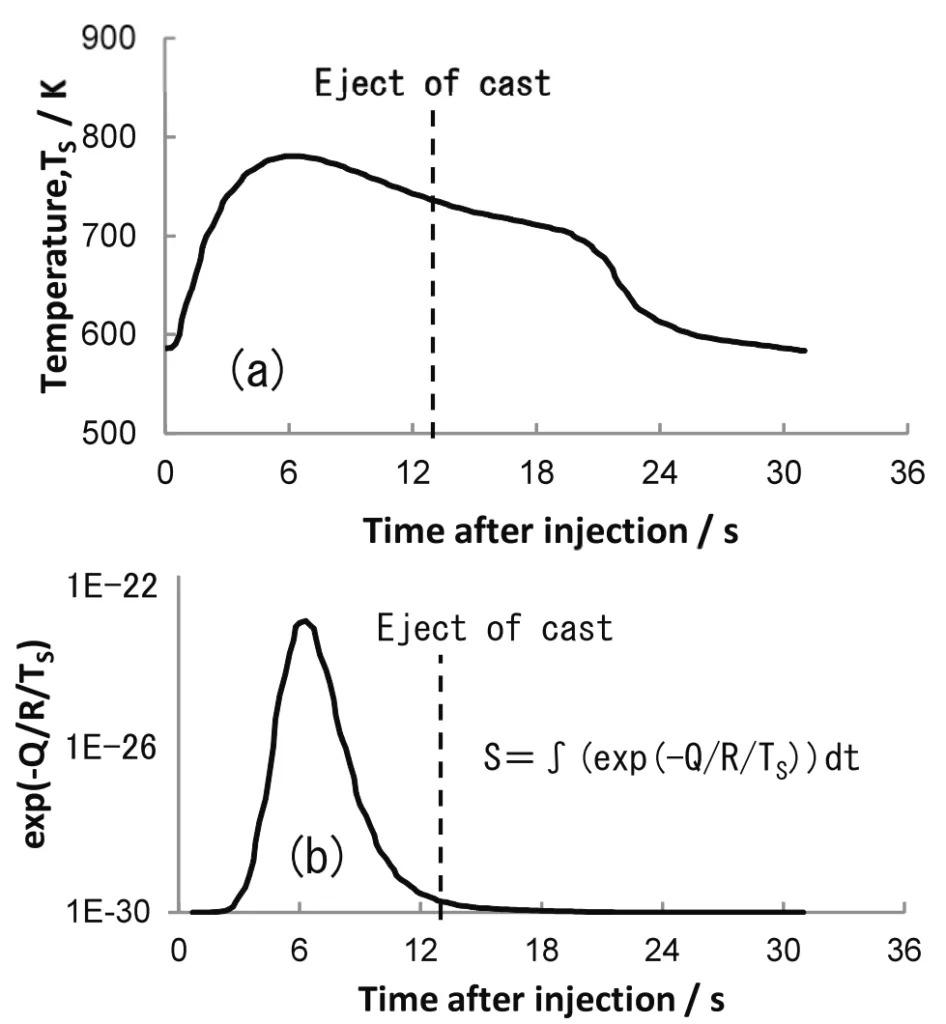
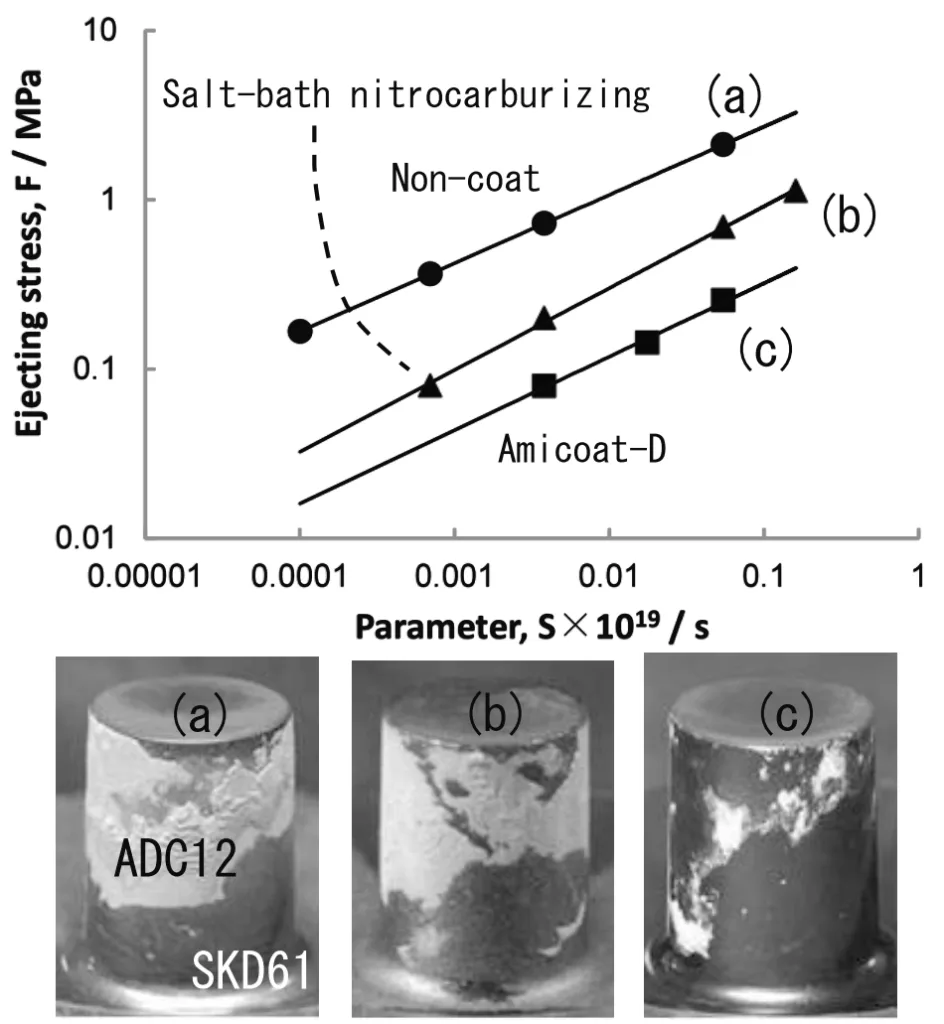
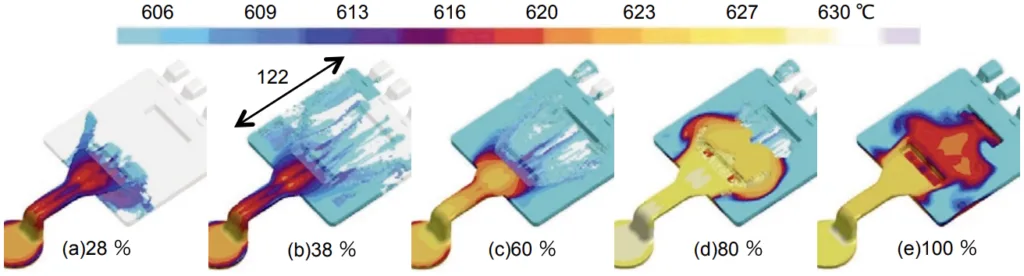
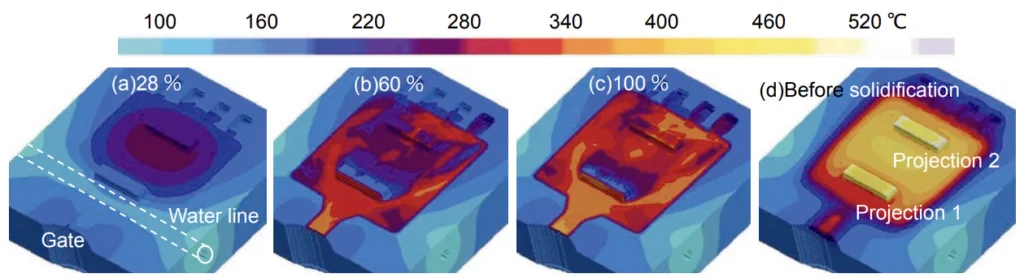
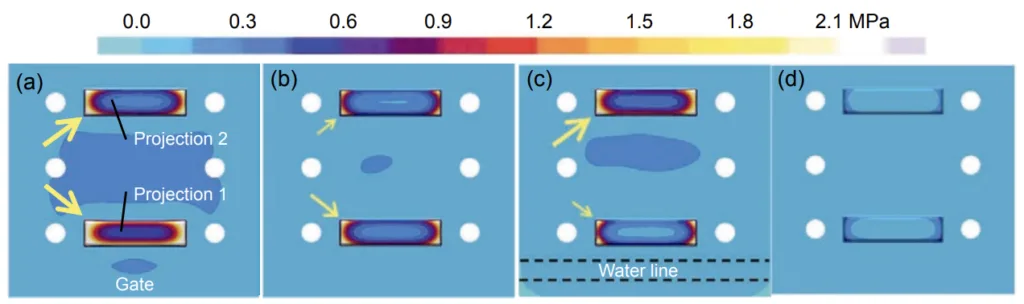
- Fig. 1. 소착 부위의 Fe 및 Al 분포. Fe/Al 화합물 층이 관찰됨. (Fig. 1. Distribution of Fe and Al at soldering part. Fe/Al compound layer is observed.)
- Fig. 2. 다이캐스팅 소착 실험용 코어 핀 모양 시편. 치수는 밀리미터 단위로 표시됨. 시편은 사출구에 가까운 금형에 장착됨. 열전쌍은 시편 표면 아래 1mm에 삽입됨. (Fig. 2. Core-pin like specimen of soldering experiment on die-casting. Dimension is given in millimeters. Specimen is mounted in a die located close to the injection gate. A thermo-couple is inserted at 1 mm below the surface of the specimen.)
- Fig. 3. (a) 이젝팅 하중 P와 (b) 이젝팅 응력 F의 차이. F는 코어 핀의 표면적을 고려하여 크기 효과를 보정함. (Fig. 3. Difference between (a) ejecting load P and (b) ejecting stress F. F is given by considering the surface area of core-pin then size effect is compensated.)
- Fig. 4. FE-해석을 통한 추정 온도 분포. 온도에 대한 표면의 (a) 시간 및 (b) 깊이의 현저한 영향이 관찰됨. (Fig. 4. Estimated temperature distribution through FE-analysis. Marked influence of (a) time and (b) depth from a surface on temperature can be seen.)
- Fig. 5. (a) 표면 온도 Ts 및 (b) 소착 파라미터 S=f(exp(-Q/R/Ts))dt의 전환 변화. (Fig. 5. Transition change of (a) surface temperature Ts and (b) soldering parameter S=f(exp(-Q/R/Ts))dt.)
- Fig. 6. 소착 파라미터 S와 이젝팅 응력 F의 관계. (Fig. 6. Relationship between soldering parameter S and ejecting stress F.)
- Fig. 7. 캐비티 내 용융 ADC12의 흐름 거동 및 온도. 충전율은 (a) 28%에서 (e) 100%까지의 체적 분율로 표시됨. (Fig. 7. Flow behavior and temperature of molten ADC12 in a cavity. Filling rate given by volume fraction represent from (a) 28 percent up to (e) 100 percent.)
- Fig. 8. 금형 온도 변화. 용융 ADC12의 충전율은 (a) 28%에서 (c) 100%까지로 표시됨. 충전 후 6초는 (d) 응고 완료 직전에 해당함. (Fig. 8. Transition of die temperature. Filling rate of molten ADC12 represent (a) 28 percent up to (c) 100 percent. At 6 seconds after filling corresponds to (d) just before finish of solidification.)
- Fig. 9. 주조 이젝팅 응력 F의 분포. (a), (b), (c) 및 (d)는 각각 700 °C 용융 ADC12, 650 °C 용융 ADC12, 700 °C 용융 ADC12 및 수냉 채널이 있는 금형, 700 °C 용융 ADC12 및 표면 처리 "AMICOAT®-D"를 나타내며, (d)는 내부 수냉각 조건이 없음. (Fig. 9. Distribution of cast ejecting stress F. (a), (b), (c) and (d) represent molten ADC12 of 700 °C, molten ADC12 of 650 °C, water cooling line in a die with molten ADC12 of 700 °C and surface treatment “AMICOAT®-D" with molten ADC12 of 700°C under the condition of no internal water cooling respectively.)
7. 결론:
주요 연구 결과 요약:
본 연구에서는 이젝팅 응력을 다이캐스팅의 소착 평가를 위한 정량적 지표로 성공적으로 공식화하고 검증했습니다. 주요 연구 결과는 다음과 같습니다.
- Fe/Al 반응층 형성을 기반으로 한 이젝팅 응력 공식 도출, 추정 활성화 에너지 Q = 313 kJ/mol.
- 낮은 용융 금속 온도, 금형 냉각 및 AMICOAT®-D 표면 처리가 이젝팅 응력을 효과적으로 감소시키는 것으로 확인.
- 용탕 흐름 해석을 통해 소착 가능성을 예측할 수 있도록 소착 파라미터 S와 이젝팅 응력 F 사이의 상관 관계 확립.
연구의 학문적 의의:
본 연구는 다이캐스팅의 소착 위험을 평가하기 위한 새롭고 객관적이며 온도에 민감한 지표인 이젝팅 응력 F를 소개합니다. 임계 온도에 의존하는 기존의 주관적인 방법과 달리 이젝팅 응력은 Fe/Al 반응층 형성이라는 야금 현상과 직접적으로 관련된 정량적 척도를 제공합니다.
실용적 의미:
이젝팅 응력 F는 다이캐스팅의 공정 설계 및 최적화를 위한 실용적인 지표로 활용될 수 있습니다. 용탕 흐름 해석을 통해 이젝팅 응력 분포를 예측함으로써 엔지니어는 주조 조건 조정, 냉각 시스템 최적화 및 적절한 표면 처리 선택과 같은 다양한 소착 방지 대책의 효과를 정량적으로 평가할 수 있습니다. 공정 설계의 지침은 이젝팅 응력 F가 주조품의 강도 또는 인장 강도를 초과하지 않도록 하는 것입니다.
연구의 한계 및 향후 연구 분야:
본 연구는 소착 평가를 위한 귀중한 프레임워크를 제공하지만, 향후 연구에서는 금형 표면 거칠기, 이젝팅 속도 및 다양한 합금 시스템과 같은 다른 요인이 이젝팅 응력 및 소착 거동에 미치는 영향을 탐구할 수 있습니다. 더 넓은 범위의 다이캐스팅 공정 및 형상에 대한 추가 검증은 이젝팅 응력 지표의 일반적인 적용 가능성을 강화할 것입니다.
8. 참고 문헌:
- 1) 青山俊三,下条浩:鋳造工学会 131回全国講演大会講演概要集(1997), 94.
- 2) 柴田浩二,諸住正太郎,幸田成康:日本金属学会誌, 30(1966), 382.
- 3) 伊吹基宏,尾崎公造:電気製鋼,76(2005), 241.
- 4) 西直美:鋳造工学,70(1998), 648.
- 5) 三中西信治,小川裕二,鈴木孝尚:鋳造工学会 130回全国講演大会講演概要集(1997), 54.
- 6) 特開2011-79053.
- 7) 西田公至:生産研究,28(1976), 464.
- 8) http://www.zerocut-watanabe.co.jp/pg321.html
9. 저작권:
- 본 자료는 "Masamichi KAWANO, Satoshi UNO and Naoki YOKOI"의 논문: "Prediction and Evaluation of Ejecting Stress Distribution at Die Surface of Die-Casting through Numerical Analyses"를 기반으로 작성되었습니다.
- 논문 출처: [DOI URL은 가능한 경우 추가 예정, 그렇지 않으면 논문 출처 정보 사용]
본 자료는 위 논문을 소개하기 위해 제작되었으며, 상업적 목적으로 무단 사용하는 것을 금지합니다.
Copyright © 2025 CASTMAN. All rights reserved.