본 기사에서는 [Faculty of Mechanical Engineering, Belgrade]에서 발행한 논문 ["고압 다이캐스팅 사출 서브세트의 사례 기반 제품 개발: 디자인 과학 연구 활용"]을 소개합니다.
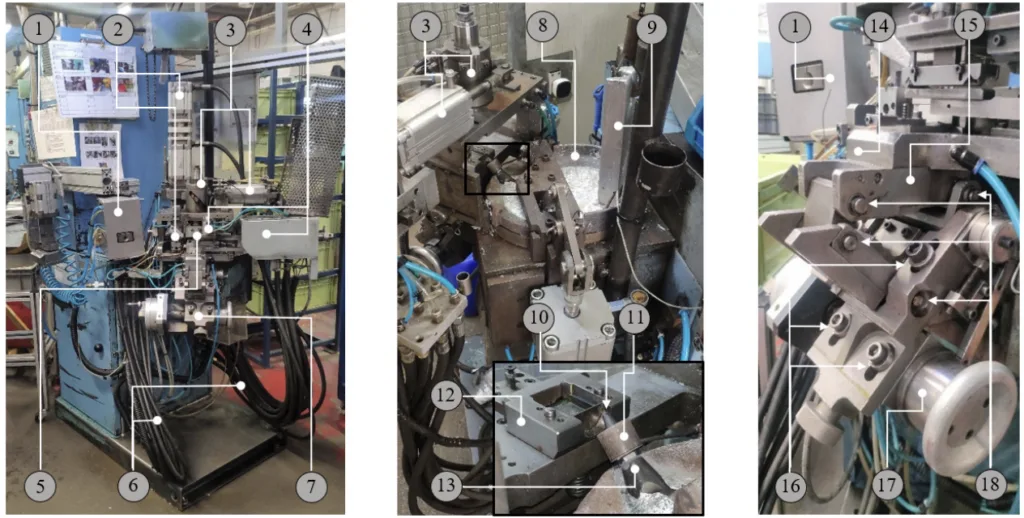
1. 개요:
- 제목: Case-Based Product Development of a High-Pressure Die Casting Injection Subset Using Design Science Research
- 저자: Matilde C. Tojal, F. J. G. Silva, R. D. S. G. Campilho, Arnaldo G. Pinto, Luís Pinto Ferreira
- 발행 연도: 2022년
- 발행 학술지/학회: FME Transactions
- 키워드: Product Development; DSR; Maintenance; Sustainability; Die Casting;Productivity; FMEA; Wear analysis.
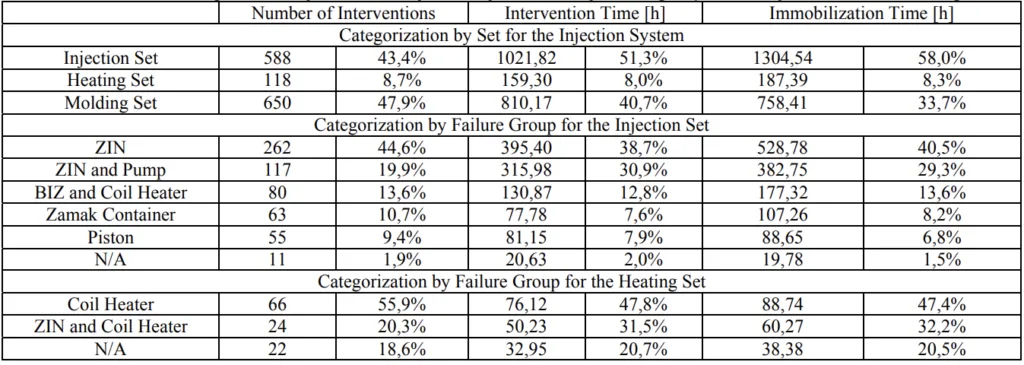
2. 초록 또는 서론
본 논문은 금속 가공 산업에서 널리 사용되는 고압 다이캐스팅에서 고온 부품과 직접 연결된 부품의 마모 문제를 다룹니다. 인적, 기계/공정 또는 공급업체 수준에서 중요한 문제 분석 및 완화에 자원을 집중하여 지속 가능한 유지보수 접근 방식을 제안합니다. 디자인 과학 연구(Design Science Research, DSR) 방법론은 새로운 사출 서브세트 개념 개발에 사용되었습니다. 이 개념의 구현은 소비 감소, 취득 비용 및 폐기물 감소, 유지보수 중 개입 시간 단축, 장비 가용 시간 증가와 같은 유익한 결과를 가져왔습니다. 본 연구는 자동차 산업에서 지속 가능한 제조의 중요성과 경제적, 환경적, 사회적 지속 가능성을 달성하는 데 있어 유지보수의 역할을 강조합니다. 또한, 사출 노즐과 같은 중요 부품의 효율성과 수명을 개선하는 데 초점을 맞춰 다이캐스팅 제품 개발에 DSR 방법론을 적용하는 것을 강조합니다.
3. 연구 배경:
연구 주제의 배경:
자동차 산업은 현대 사회의 경제 구조에서 중요한 역할을 하며 생산 시스템 기술 개발의 최전선에 영구적으로 위치하고 있습니다. 예비 부품 소비는 생산 시스템 내에서 경제적 및 인적 자원 소비의 주요 원인입니다. 지속 가능한 제조는 경제적, 환경적, 사회적 책임을 고려한 실행 가능한 생산을 창출하는 데 매우 중요합니다. 유지보수는 생산량, 비용, 시스템 가용성, 효율성 및 자원 활용에 상당한 영향을 미칩니다. 다이캐스팅, 특히 고압 다이캐스팅은 널리 사용되지만 사출 노즐과 같이 고온에 노출되는 부품에 심각한 마모를 유발합니다.
기존 연구 현황:
기존 연구에서는 모든 생산 시스템 내에서 중요한 예비 부품 선택 및 근본 원인 분석을 위한 데이터 수집의 중요성을 강조합니다 [15]. 제품 개발의 복잡성으로 인해 데이터 기반 의사 결정이 필수적입니다 [16]. 효과적인 유지보수 관리 시스템은 제품 수명 주기에서 상충되는 요소를 더 잘 이해하는 데 중요합니다 [17]. 혁신 및 제품 개발은 기업의 핵심 성공 요소이며 최적의 성능/비용 비율, 위험 관리 및 시스템 결함에 대한 무관용을 보장하는 것이 매우 중요합니다 [18-21]. 디자인 과학 연구(DSR)는 기존 제품에서 새로운 제품을 개발하는 데 일반적으로 사용되는 방법론이며 [26-27], 기술적 배경과 복잡한 문제 해결에 중점을 둡니다 [28]. Vaishnavi와 Kuechler [30] 및 Peffers et al. [32]과 같은 반복적인 DSR 프로세스는 설계 및 개발을 위한 구조화된 프레임워크를 제공합니다. Siedhoff [35]는 디자인 사고와 기존 DSR 단계를 통합하여 DSR을 더욱 발전시켰습니다.
연구의 필요성:
다이캐스팅 공정의 사출 노즐 영역은 지속적인 교체, 공정 중단 및 생산성 손실로 어려움을 겪고 있습니다 [25]. 이러한 중요한 영역에서 공정 효율성을 향상시키기 위해 노즐 및 연결 영역의 새로운 개념을 연구하는 것이 시급합니다. DSR은 확립되었지만, 특히 지속 가능한 유지보수 및 사출 서브세트의 마모 감소에 초점을 맞춰 특정 다이캐스팅 부품 개선에 적용하는 것은 추가 연구가 필요합니다. 본 연구는 DSR을 적용하여 고압 다이캐스팅 사출 서브세트에 대한 사례 기반 제품 개발을 수행함으로써 이러한 격차를 해소합니다.
4. 연구 목적 및 연구 질문:
연구 목적:
주요 목적은 디자인 과학 연구(DSR)를 적용하여 고압 다이캐스팅에서 지속 가능한 유지보수를 달성하는 방법을 입증하는 것입니다. 이는 인적, 기계/공정 또는 공급업체 수준에서 발생하는 중요한 문제 분석 및 완화에 자원 할당을 최적화하여 궁극적으로 장비 수명을 연장하고 폐기물을 줄이는 것을 목표로 합니다.
핵심 연구:
핵심 연구는 다음 사항에 중점을 둡니다.
- 고압 다이캐스팅 환경에서 제품 개발을 위한 디자인 과학 연구(DSR) 방법론 적용.
- Zamak Injection Nozzle (ZIN)과 같은 중요 부품의 수명과 성능을 향상시키기 위한 새로운 사출 서브세트 설계 개발.
- 개선 영역을 식별하기 위해 기존 사출 서브세트의 마모 메커니즘 및 고장 모드 분석.
- 지속 가능성, 유지보수, 생산성 및 비용 효율성에 미치는 영향을 평가하기 위해 새로운 사출 서브세트 개념 구현 및 검증.
연구 가설:
명시적으로 가설로 언급되지는 않았지만, 연구는 다음과 같은 암묵적 가정 하에 운영됩니다.
- 디자인 과학 연구 방법론은 고압 다이캐스팅에서 개선된 부품을 개발하는 효과적인 접근 방식입니다.
- DSR을 통해 개발된 재설계된 사출 서브세트는 ZIN과 같은 중요 부품의 마모를 크게 줄이고 수명을 연장할 수 있습니다.
- 새로운 사출 서브세트를 구현하면 예비 부품 소비 감소, 유지보수 비용 절감, 가동 중지 시간 감소 및 장비 가용성 증가를 포함하여 지속 가능한 유지보수의 측정 가능한 개선으로 이어질 것입니다.
5. 연구 방법론
연구 설계:
본 연구는 디자인 과학 연구(DSR) 방법론, 특히 디자인 사고와 기존 DSR 단계를 반복적 접근 방식으로 결합한 Siedhoff [35]가 개발한 프로세스를 사용합니다. 탐색적 연구로 시작하여 처방적 연구를 통해 솔루션 권장 사항을 생성합니다. DSR 사이클은 연구 대상 제품의 초기 설계로 시작하여 문제 식별, 제안, 개발, 평가 및 결론의 반복 단계를 거칩니다. 사례 기반 추론은 완전히 새로운 설계를 시작하는 대신 기존 제품을 수정하는 데 활용됩니다.
데이터 수집 방법:
데이터 수집 방법은 다음과 같습니다.
- 정량적 데이터: 회사 작업 지원 소프트웨어에서 수집한 다양한 예비 부품에 대한 예비 부품 소비 데이터, 취득 비용 및 총 비용. 이 데이터는 중요한 부품을 식별하기 위한 파레토 분석에 사용되었습니다.
- 정성적 데이터: 제조 공정의 관찰 및 모니터링을 통해 기술적 문제를 식별하고 소프트웨어 기반 데이터를 보완합니다.
- 기술 분석:
- SEM (주사 전자 현미경) 및 EDS (에너지 분산 X선) 분석: ZIN 마모 분석에 사용되었습니다.
- 금속 조직 및 경도 테스트: 완전한 마모 특성 분석 및 재료 특성 평가를 위해 수행되었습니다.
- Rockwell C 경도 테스트: ISO 6508-1:2016 표준에 따라 경도를 측정하기 위해 수행되었습니다.
분석 방법:
분석 방법은 다음과 같습니다.
- 파레토 분석: 취득 비용을 기준으로 연구할 예비 부품의 우선 순위를 정하는 데 사용되었으며, 가장 시급한 부품에 초점을 맞췄습니다.
- FMEA (고장 모드 및 영향 분석): 사출 시스템 부품의 고장 모드, 고장 빈도 및 개입 시간을 식별하는 데 사용되었습니다.
- Ishikawa 다이어그램 (피쉬본 다이어그램): 발견 사항을 요약하고 조기 ZIN 고장의 근본 원인을 식별하기 위해 개발되었으며, 솔루션 개발을 안내했습니다.
- 통계 분석: 개입 분류 및 고장 모드 빈도를 분석하기 위한 기술 통계.
연구 대상 및 범위:
본 연구는 Zamak 5를 강철 케이블 끝단에 다이캐스팅하는 데 사용되는 ZHPIM (Zamak High-Pressure Injection Machine)의 사출 시스템에 중점을 둡니다. 조사 대상의 주요 대상은 Zamak Injection Nozzle (ZIN)과 사출 서브세트 내 관련 부품입니다. 범위는 예비 부품 소비 분석, 고장 모드 및 성능, 수명 향상 및 지속 가능한 유지보수 관행에 기여하기 위한 DSR 방법론을 사용한 개선된 사출 서브세트 설계 개발을 포함합니다.
6. 주요 연구 결과:
주요 연구 결과:
- 파레토 분석: SP01, SP03 및 SP06이 가장 비싼 예비 부품으로 식별되어 사출 세트에 초점을 맞추도록 안내했습니다.
- 개입 분류: 사출 시스템 (개입의 85%) 및 몰딩 세트 (개입의 47.9%)가 주요 가동 중지 시간 원인임을 나타냅니다. 사출 세트 내에서 ZIN 개입이 중요했습니다 (44.6%).
- ZIN의 고장 모드 분석: 마모 및 파손이 ZIN의 주요 고장 모드였습니다. 손상된 히팅 세트는 ZIN 고장의 5.7%를 차지했습니다. 파손된 ZIN의 79.9%는 펌프 교체로 이어졌고, 마모 고장의 72.3%는 ZIN 교체만 필요했습니다.
- DSR 반복 및 모델 개발: 4개의 주요 DSR 반복 프로세스를 통해 새로운 ZIN 모델 (Model 01 ~ Model 07)을 개발했습니다. 수정 사항에는 ZIN 형상 변경 (ICZ 반경, 챔퍼 제거), 재료 경도 증가 (56-58 HRC) 및 밀봉 방법론 개선이 포함되었습니다.
- 마모 분석: SEM 분석 결과 ZIN의 ICZ에서 뚜렷한 마모 영역이 나타났습니다. 금속 조직 및 경도 테스트 결과 충격 영역에서 약간의 경도 감소가 나타났지만 중요한 미세 구조 변화는 없었습니다.
- 새로운 모델 (Model 07)의 구현 및 검증: 설계 변경 및 재료 사양 준수를 통합한 Model 07은 크게 향상된 성능을 입증했습니다. 의도된 거동인 소성 변형으로 인한 마모를 보였고, 이전 모델에 비해 크게 증가한 140일 이상의 작동 시간을 달성했습니다.
제시된 데이터 분석:
- 그림 1: 누적 취득 비용별 예비 부품 소비에 대한 파레토 분석으로, 다양한 예비 부품의 비용 기여도를 강조합니다.
- 표 1: 파레토 분석에 사용된 상위 10개 예비 부품에 대한 예비 부품 소비 데이터, 취득 비용 및 총 비용.
- 그림 2: ZHPIM 장비 구조로, 시스템, 세트 및 구성 요소의 계층적 분류를 보여줍니다.
- 그림 3: 워크스테이션, 사출 시스템 및 커플링 시스템 구성 요소로, 다양한 부품의 위치와 기능을 보여줍니다.
- 표 2: 시스템 및 고장 그룹별 개입 분류로, 다양한 구성 요소에 대한 개입 빈도 및 가동 중지 시간을 정량화합니다.
- 그림 4: ZIN 고장 모드에 대한 파레토 분석으로, 마모, 파손 및 기타 고장 유형의 빈도를 보여줍니다.
- 그림 5: 커플링 시스템 문제로 인한 사출 고장으로, 기술적 문제를 시각적으로 보여줍니다.
- 그림 6: 보호판의 위치로, 히팅 세트 및 ZIN에 대한 보호 조치를 보여줍니다.
- 그림 7: 커플링 시스템 튜닝 슬롯의 극심한 마모로, 마모 관련 문제를 보여줍니다.
- 그림 8: 다월 핀의 간극으로, 커플링 시스템의 피팅 문제를 강조합니다.
- 그림 9: 커플링 시스템 마모에 대한 개입 프로세스 영향으로, 유지보수로 인한 마모를 보여줍니다.
- 그림 10: 히팅 세트 밀봉의 기술적 문제로, 밀봉 문제를 보여줍니다.
- 그림 11: 히팅 세트 부식으로 인한 고장 모드로, 부식 관련 고장을 보여줍니다.
- 그림 12: ZIN과의 하단 프레임 플레이트 상호 작용으로, 기하학적 상호 작용을 보여줍니다.
- 그림 13: BFP와 ZIN ICZ 사이의 접촉점으로, 접촉 영역 세부 정보를 보여줍니다.
- 그림 14: 파손의 주요 원인으로 작용하는 기하학적 문제로, 설계 결함을 강조합니다.
- 그림 15: 필요한 작동 상태를 준수하는 BFP의 ICZ로, 준수 ICZ를 보여줍니다.
- 그림 16: 마모 및 충격으로 인한 BFP의 ICZ의 비준수로, 비준수 ICZ를 보여줍니다.
- 그림 17: ZIN 조기 고장에 대한 Ishikawa 다이어그램으로, 고장의 근본 원인을 요약합니다.
- 그림 18: ZIN에 대한 SEM 분석으로, 마모 영역의 SEM 이미지를 보여줍니다.
- 그림 19: 피팅에 의한 ZIN ICZ의 고장 모드로, 피팅 마모를 보여줍니다.
- 그림 20: 스폴링에 의한 ZIN ICZ의 고장 모드로, 스폴링 마모를 보여줍니다.
- 그림 21: 파손에 미치는 피드 마크 영향으로, 가공 마크를 보여줍니다.
그림 이름 목록:
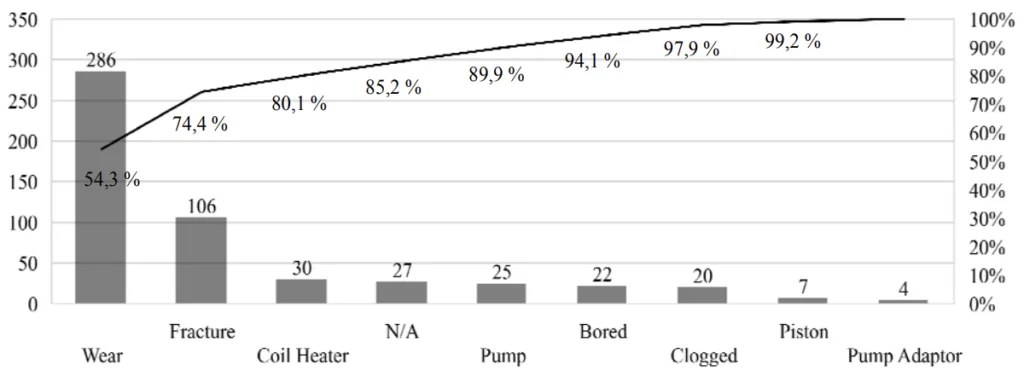
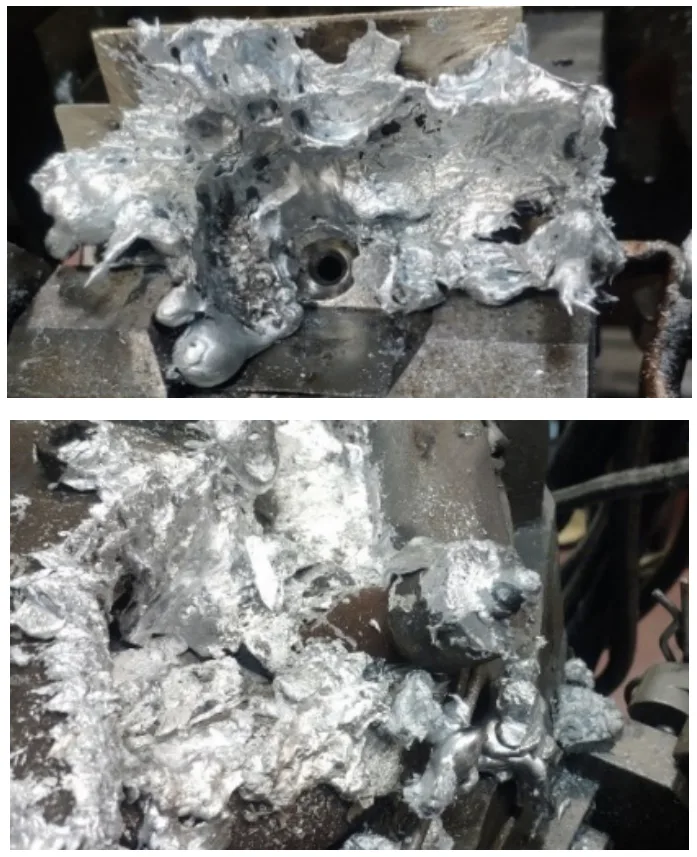
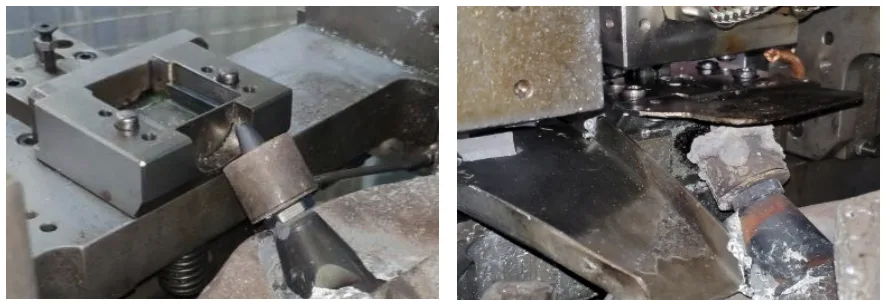
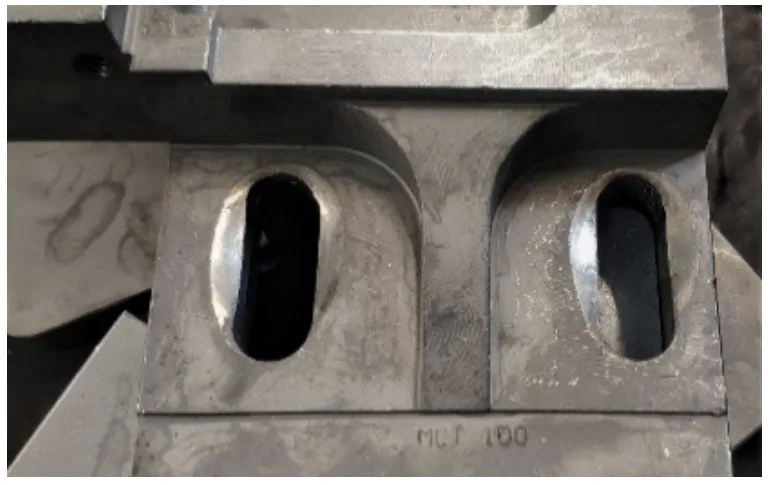
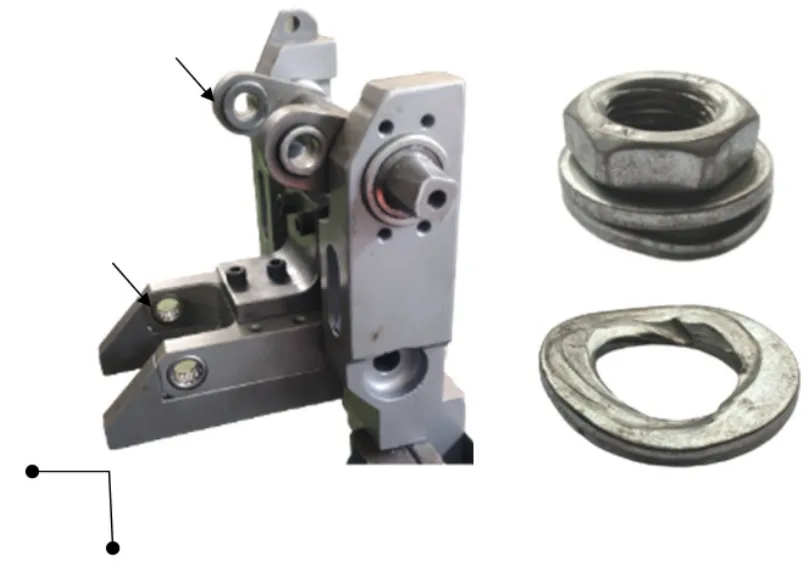
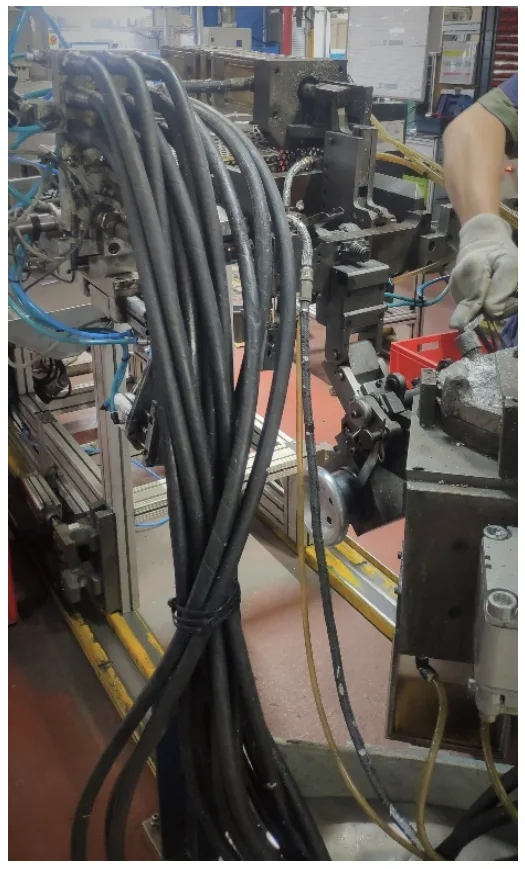
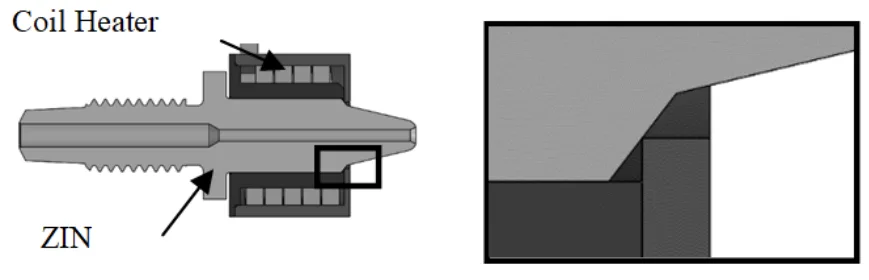
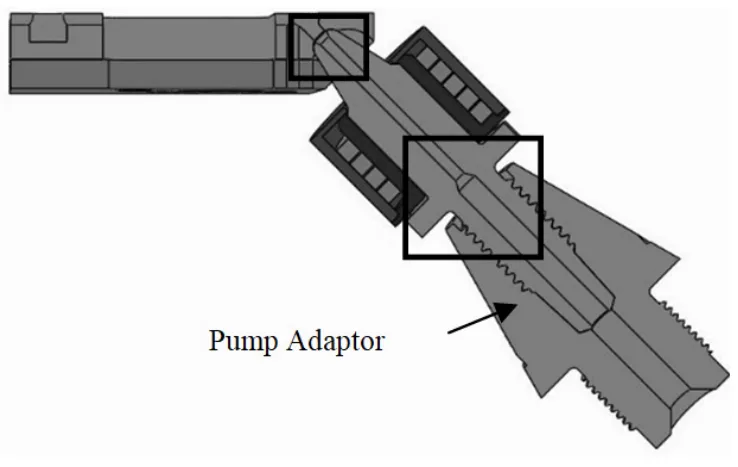
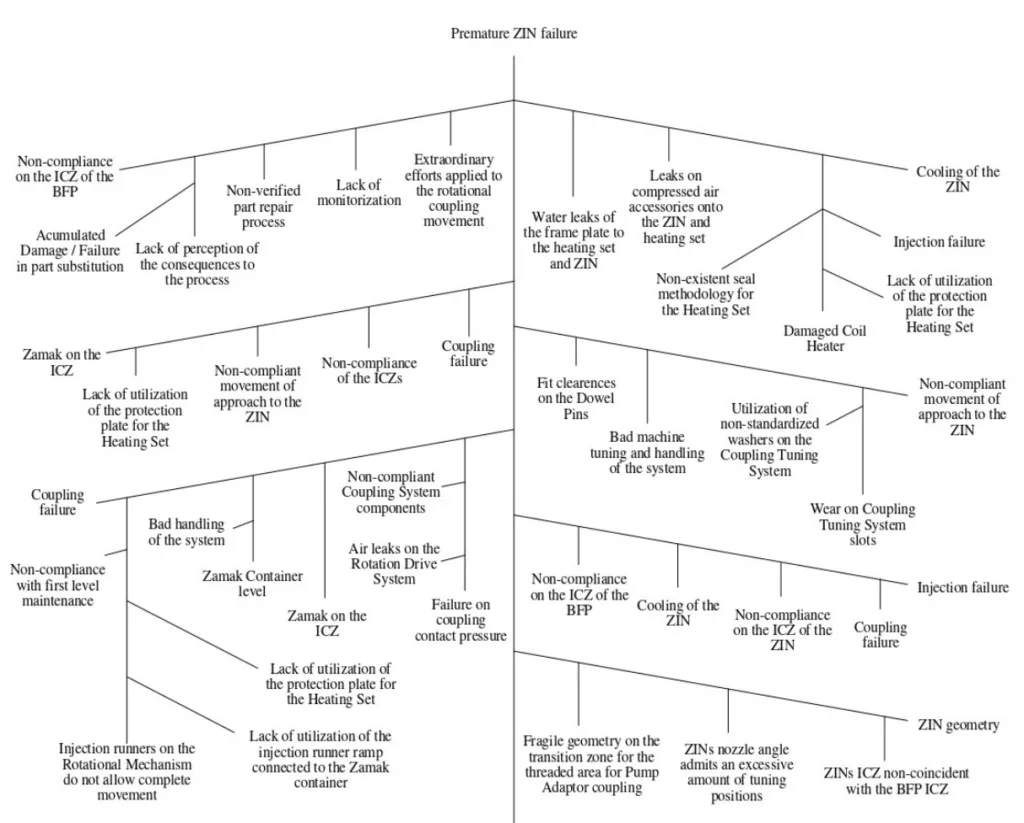
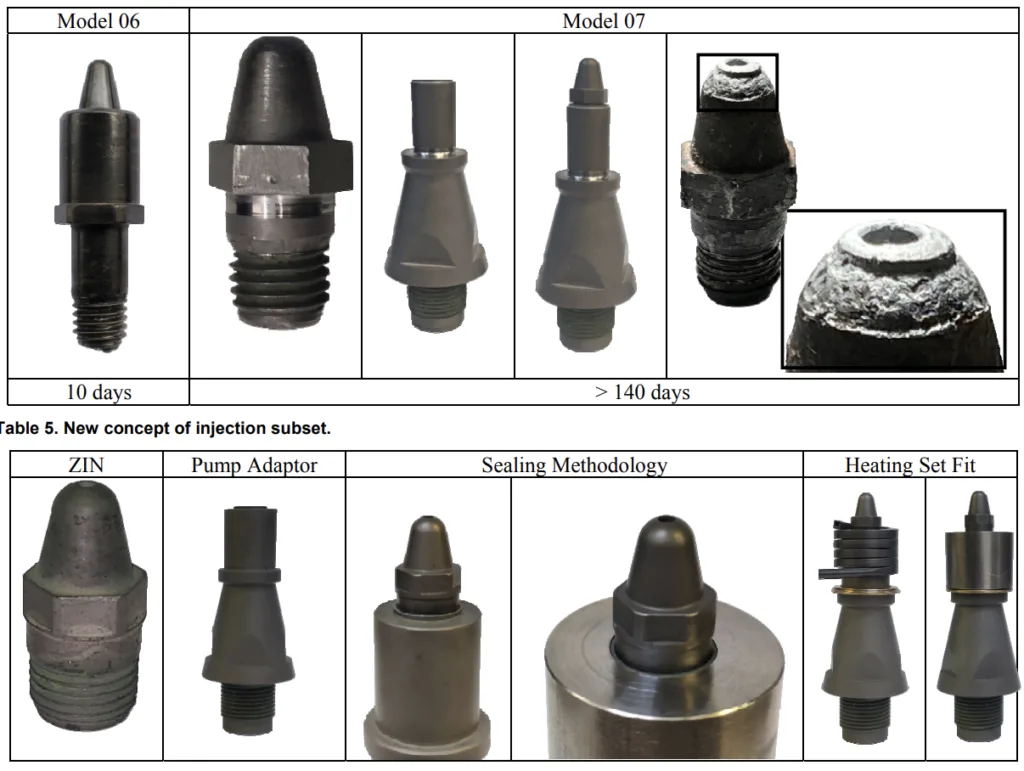
- Figure 1. Pareto's analysis on spare part consumption by accumulated acquisition cost (Overall expenses).
- Figure 2. ZHPIM equipment structure by main systems, sets and working groups.
- Figure 3. Workstation, Injection System and Coupling System and corresponding main components and location: (1) Cable trimming device; (2) Flower device and drive cylinder; (3) Mold closure system and drive cylinder; (4) Transfer and drive cylinder; (5) Mold and frame; (6) Air, water and oil hoses; (7) Coupling system; (8) Zamak container; (9) Zamak ingot; (10) Zamak injection nozzle; (11) Heating set; (12) Frame base; (13) Pump adaptor; (14) Support base; (15) Rotation mechanism; (16) Coupling tuning system; (17) Rotation drive system; (18) Dowel pins.
- Figure 4. Pareto's analysis for ZIN failure mode count for the period under study.
- Figure 5. Injection failure caused by technical problems on the coupling system elements.
- Figure 6. Location of the protection plates of the heating set and the internal parts of the moulding set
- Figure 7. Extreme wear on the coupling system tunning slots.
- Figure 8. Clearances on the dowel pins that connect to the coupling system and group of washers found on the ΖΗΡΙΜ.
- Figure 9. Intervention process impact on premature coup-ling and tunning system wear.
- Figure 10. Technical problems with the seal of the contact between the heating set and the ZIN.
- Figure 11. Failure mode by excessive corrosion of the heating set incapacitating the coil heater.
- Figure 12. Bottom frame plate interaction with the ZIN.
- Figure 13. Contact points between BFP and the ZIN inject-tion contact zones.
- Figure 14. Geometric issues function as a major contributor to failure mode by fracture.
- Figure 15. ICZ from BFP compliant with the required working state.
- Figure 16. Non-compliance of ICZs for the BFP due to abrasion and impact.
- Figure 17. Ishikawa diagram for ZINs premature failure
- Figure 18. SEM analysis to the ZIN.
- Figure 19. Failure mode of the ZIN injection contact zone by pitting.
- Figure 20. Failure mode of the ZIN injection contact zone by spalling.
- Figure 21. Feed marks impact on nucleation and propagation of premature failure.
7. 결론:
주요 연구 결과 요약:
본 연구는 디자인 과학 연구(DSR)를 성공적으로 적용하여 고압 다이캐스팅을 위한 새로운 사출 서브세트 개념을 개발하여 Zamak Injection Nozzle (ZIN)의 수명과 성능을 크게 향상시켰습니다. 새로운 Model 07은 작동 시간이 크게 증가 (140일 이상)했으며 소성 변형으로 인한 마모를 보여주어 마모 저항성이 향상되었음을 나타냅니다. 새로운 개념의 구현으로 예비 부품 소비, 취득 비용, 폐기물, 개입 시간 감소 및 장비 가용성이 증가했습니다.
연구의 학문적 의의:
본 연구는 다이캐스팅 제품 개발 환경에서 디자인 과학 연구 방법론의 효과적인 적용을 입증합니다. 실제 산업 문제를 해결하기 위해 DSR을 사용한 상세한 사례 연구를 제공하여 제조의 부품 설계 및 유지보수 관행을 개선하기 위한 구조화된 접근 방식을 제공합니다. 본 연구는 지속 가능한 제조에 대한 지식과 지속 가능성 목표 달성에 있어 유지보수 최적화의 역할에 기여합니다.
실용적 의미:
본 연구 결과는 특히 고압 다이캐스팅을 사용하는 작업에 대해 다이캐스팅 산업에 중요한 실용적 의미를 갖습니다. 개발된 사출 서브세트 개념은 가동 중지 시간, 유지보수 비용 및 예비 부품 소비를 줄이면서 장비 신뢰성과 생산성을 향상시키는 실질적인 솔루션을 제공합니다. 문제 분석 및 솔루션 개발에 대한 체계적인 접근 방식은 다른 제조업체에서 공정의 중요 부품 설계 및 유지보수를 개선하기 위해 채택할 수 있습니다.
연구의 한계 및 향후 연구 분야:
본 연구는 하나의 제조 환경 내의 특정 사례 연구로 제한됩니다. 향후 연구에서는 다른 다이캐스팅 응용 분야 및 다양한 유형의 사출 시스템으로 연구 결과를 일반화할 수 있는지 탐구할 수 있습니다. 특히 관찰된 약간의 경도 감소와 관련하여 다이캐스팅 조건에서 ZIN의 재료 거동에 대한 심층적인 조사를 통해 재료 선택 및 열처리 공정을 더욱 최적화할 수 있습니다. 향후 연구에서는 본 연구에서 확립된 DSR 프레임워크를 기반으로 다이캐스팅 공정에서 예측 유지보수를 위한 데이터 수집 및 분석 자동화에 집중할 수도 있습니다.
8. 참고 문헌:
- [1] R. J. S. Costa, F. J. G. Silva, R. D. S. G. Campilho, "A novel concept of agile assembly machine for sets applied in the automotive industry," Int. J. Adv. Manuf. Technol., Vol. 91, pp. 4043-4054, 2017. doi: 10.1007/s00170-017-0109-4
- [2] W. Araújo, F. J. G. Silva, R. Campilho, "Manufacturing cushions and suspension mats for vehicle seats: A novel cell concept," Int. J. Adv. Manuf. Tech., Vol. 90, pp. 1539-1545. 2017, doi: 10.1007/s00170-016-9475-6
- [3] A. Gritsenko, V. Shepelev, E. Zadorozhnaya, K. Shubenkova, "Test Diagnostics of Engine Systems in Passenger Cars," FME Trans., Vol. 48, pp. 46-52, 2020, doi: 10.5937/fmet2001046G.
- [4] F. J. G. Silva, R. M. Gouveia, Cleaner Production - Towards a Better Future. Cham, Switzerland: Springer International Publishing, 2020.
- [5] J. Malek and T. N. Desai, "A systematic literature review to map literature focus of sustainable manufacturing,” J. Clean. Prod., Vol. 256, p. 120345, 2020, doi: 10.1016/j.jclepro.2020.120345.
- [6] M. Siladić, B. Rašuo, "On-Condition Maintenance for Nonmodular Jet Engines: An Experience," J Eng Gas Turbine Power, Vol. 131(3), p. 032502, May 2009, doi: 10.1115/1.3019104.
- [7] B. Rašuo, G. Djuknić, "Optimization of the aircraft general overhaul process," Aircr. Eng. Aerosp. Technol., Vol. 85(5), pp. 343-354. 2013, doi: 10.1108/AEAT-02-2012-0017.
- [8] C. Franciosi, A. Voisin, S. Miranda, S. Riemma, and B. Iung, “Measuring maintenance impacts on sustainability of manufacturing industries: from a systematic literature review to a framework proposal," J. Clean. Prod., Vol. 260, p. 121065, 2020, doi: 10.1016/j.jclepro.2020.121065.
- [9] S. Ferreira, L. Martins, F. J. G. Silva, R. B. Casais, R. D. S. G. Campilho, and J. C. Sá, “A novel approach to improve maintenance operations," Procedia Manuf., Vol. 51, pp. 1531-1537, 2020, doi: 10.1016/j.promfg.2020.10.213.
- [10] L. Silvestri, A. Forcina, V. Introna, A. Santolamazza, and V. Cesarotti, “Maintenance transformation through Industry 4.0 technologies: A systematic literature review," Comput. Ind., Vol. 123, p. 103335, 2020, doi: 10.1016/j.compind.2020.103335.
- [11]L. Morgado, F. J. G. Silva, and L. M. Fonseca, "Mapping occupational health and safety management systems in Portugal: Outlook for ISO 45001:2018 adoption," Procedia Manuf., Vol. 38, pp. 755-764, 2019, doi: 10.1016/j.promfg.2020.01.103.
- [12] M. Jasiulewicz-Kaczmarek and P. Żywica, “The concept of maintenance sustainability performance assessment by integrating balanced scorecard with non-additive fuzzy integral," Eksploat. Niezawodn., Vol. 20(4), pp. 650–661, 2018, doi: 10.17531/ein.2018.4.16.
- [13] S. Ferreira, F. J. G. Silva, R. B. Casais, M. T. Pereira, and L. P. Ferreira, "KPI development and obsolescence management in industrial maintenance," Procedia Manuf., Vol. 38, pp. 1427–1435, 2019, doi: 10.1016/j.promfg.2020.01.145.
- [14] C. Franciosi, A. Lambiase, C. Franciosi, A. Lambiase, S. Alfredo, "Sustainable Maintenance: i a Maintenance: a Periodic Maintenance: Sustainable Maintenance: a Periodic Preventive Spare Parts Sustainable Spare Parts Management,” IFAC-PapersOnLine, Vol. 50(1), pp. 13692–13697, 2017, doi: 10.1016/j.ifacol.2017.08.2536.
- [15]T. Santos, F. J. G. Silva, S. F. Ramos, R. D. S. G. Campilho, and L. P. Ferreira, “Asset priority setting for maintenance management in the food industry," Procedia Manuf., Vol. 38, pp. 1623-1633, 2019, doi: 10.1016/j.promfg.2020.01.122.
- [16]T.G. Chondros, "The Development of Mechanics and Engineering Design and Machine Theory since the Rennaissance," FME Trans., Vol. 49, pp. 291-307, 2021, doi: 10.5937/fme2102291C.
- [17] F. Schönberg and M. Messer, "Decision data model in virtual product development,” Comput. Ind. Eng., Vol. 122, pp. 106-124, 2018, doi: 10.1016/j.cie.2018.05.047.
- [18]S. Altuntas, E. B. Özsoy, and Şi. Mor, “Innovative new product development: A case study," Procedia Comput. Sci., Vol. 158, pp. 214–221, 2019, doi: 10.1016/j.procs.2019.09.044.
- [19]M. Riesener, C. Doelle, M. Mendl-Heinisch, and N. Klumpen, "Identification of evaluation criteria for algorithms used within the context of product development," Procedia CIRP, Vol. 91, pp. 508-515, 2020, doi: 10.1016/j.procir.2020.02.207.
- [20] G. Bastchen, F. Silva, and M. Borsato, "Risk management analysis in the product development process," Procedia Manuf., Vol. 17, pp. 507-514, 2018, doi: 10.1016/j.promfg.2018.10.090.
- [21]J. G. Persson, “Current Trends in Product Development," Procedia CIRP, Vol. 50, pp. 378-383, 2016, doi: 10.1016/j.procir.2016.05.088.
- [22]R. G. Cooper, “The drivers of success in new-product development,” Ind. Mark. Manag., Vol. 76, pp. 36-47, 2019, doi: 10.1016/j.indmarman.2018.07.005.
- [23] V. Nunes, F. J. G. Silva, M. F. Andrade, R. Alexandre, A. P. M. Baptista, "Increasing the lifespan of high-pressure die cast molds subjected to severe wear," Surf Coat Tech, Vol. 332, pp. 319-331, 2017. doi: 10.1016/j.surfcoat.2017.05.098.
- [24]B.M.D.N. Moreira, R.M. Gouveia, F.J.G. Silva, R. D. S. G. Campilho, "A Novel Concept Of Production And Assembly Processes Integration," Procedia Manuf., Vol. 11, pp. 1385-1395. 2017, doi: 10.1016/j.promfg.2017.07.268.
- [25] V.F.C. Sousa, F.J.G. Silva, L.P. Ferreira, R.D.S.G. Campilho, T. Pereira, E. Braga, "Improving the Design of Nozzles Used in Zamak High-Pressure Die-Casting Process," FME Trans., Vol. 49, pp. 1005-1013, 2021. doi: 10.5937/fme2104005S.
- [26] O.I. Abdullah, W.T. Abbood, H.K. Hussein, "Development of Automated Liquid Filling System Based on the Interactive Design Approach," FME Trans., Vol. 48, pp. 938-945, 2020. doi: 10.5937/fme2004938A.
- [27] S. Tamada, M. Chandra, P. Patra, S. Mandol, D. Bhattacharjee, P.K. Dan, " Modeling for Design Simplification and Power-Flow Efficiency Improvement in an Automotive Planetary Gearbox: A Case Example," FME Trans., Vol. 48, pp. 707-715, 2020. doi: 10.5937/fme2003707T.
- [28] J. Grenha Teixeira, L. Patrício, K. H. Huang, R. P. Fisk, L. Nóbrega, and L. Constantine, “The MINDS Method: Integrating Management and Interaction Design Perspectives for Service Design," J. Serv. Res., Vol. 20(3), pp. 240-258, 2017, doi: 10.1177/1094670516680033.
- [29] Richard Baskerville & Vijay Vaishnavi, 2020. "A Novel Approach to Collectively Determine Cybersecurity Performance Benchmark Data," Progress in IS, in: Jan vom Brocke & Alan Hevner & Alexander Maedche (ed.), Design Science Research. Cases, pages 17-41, Springer.
- [30] V. K. Vaishnavi and W. K. Jr., “Introduction to Design Science Research in Information and Communication Technology," Des. Sci. Res. Methods Patterns Innov. Inf. Commun. Technol., 2nd edition, pp. 7-30, Boca Raton, FL, USA, CRC Press, 2015. ISBN: 9780429172205.
- [31]F. Devitt and P. Robbins, “Design, Thinking and Science," Commun. Comput. Inf. Sci., Vol. 388, pp-38-48, 2013, doi: 10.1007/978-3-319-04090-5.
- [32] K. Peffers, T. Tuunanen, M. A. RotUhenberger, and S. Chatterjee, "A design science research methodology for information systems research,” J. Manag. Inf. Syst., Vol. 24(3), pp. 45–77, 2007, doi: 10.2753/MIS0742-1222240302.
- [33]J. Q. Azasoo and K. O. Boateng, "A Retrofit Design Science Methodology for Smart Metering Design in Developing Countries," Proc. - 15th Int. Conf. Comput. Sci. Its Appl. ICCSA 2015, pp. 1–7, 2015, doi: 10.1109/ICCSA.2015.23.
- [34] Jan vom Brocke & Alan Hevner & Alexander Maedche, "Introduction to Design Science Research," Progress in IS, in: Jan vom Brocke & Alan Hevner & Alexander Maedche (ed.), Design Science Research. Cases, pages 1-13, 2020, Springer. doi: 10.1007/978-3-030-46781-4_1.
- [35] S. Siedhoff, "Design science research,” Seizing Bus. Model Patterns Disruptive Innov., pp. 29-43, Spinger, 2019. ISBN: 978-3658263355.
- [36] S. Gregor and A. R. Hevner, “Positioning and presenting design science research for maximum impact," MIS Q., Vol. 37(2), pp. 337–355, 2013, doi: 10.2753/MIS0742-1222240302.
- [37] K. Lepenioti, A. Bousdekis, D. Apostolou, and G. Mentzas, “Prescriptive analytics: Literature review and research challenges,” Int. J. Inf. Manage., Vol. 50, pp. 57–70, 2020, doi: 10.1016/j.ijinfomgt. 2019.04.003.
- [38] M. Relich and P. Pawlewski, “A case-based reasoning approach to cost estimation of new product development,” Neurocomputing, Vol. 272, pp. 40-45, 2018, doi: 10.1016/j.neucom.2017.05.092.
- [39] H. Saranga, et al. "Resource configurations, product development capability, and competitive advantage: An empirical analysis of their evolution," J. Bus. Res., Vol. 85, pp. 32-50, 2018, doi: 10.1016/j.jbusres.2017.11.045.
- [40] G. Pinto, F. J. G. Silva, A. Baptista, R. D. S. G. Campilho, and F. Viana, “Investigations on the Oxidation of Zn-coated Steel Cables," FME Trans., Vol. 49(3) pp. 587-597, 2021, doi: 10.5937/fme2103587P.
- [41]N. Martins, F. J. G. Silva, R. D. S. G. Campilho, and L. P. Ferreira, "A novel concept of Bowden cables flexible and full-automated manufacturing process improving quality and productivity,” Procedia Manuf., Vol. 51, pp. 438-445, 2020, doi: 10.1016/j.promfg.2020.10.062.
- [42] R. Ribeiro, F. J. G. Silva, A. G. Pinto, R. D. S. G. Campilho, and H. A. Pinto, “Designing a novel system for the introduction of lubricant in control cables for the automotive industry," Procedia Manuf., Vol. 38, pp. 715-725, 2019, doi: 10.1016/j.promfg.2020.01.096.
- [43]H. A. Pinto, F. J. G. Silva, R. P. Martinho, R. D. S. G. Campilho, and A. G. Pinto, “Improvement and validation of Zamak die casting moulds," Procedia Manuf., Vol. 38, pp. 1547–1557, 2019, doi: 10.1016/j.promfg.2020.01.131.
- [44] H. Pinto, F. J. G. Silva, “Optimisation of Die Cast-ing Process in Zamak Alloys," Procedia Manuf., Vol. 11, pp. 517–525, 2017, doi: 10.1016/j.prom fg.2017.07.145.
- [45]B. Arh, B. Podgornik, and J. Burja, "Electroslag remelting: A process overview,” Mater. Tehnol., Vol. 50(6), pp. 971-979, 2016, doi: 10.17222/mit.2016.108.
- [46] A. Pribulová, P. Futaš, M. Bartošová, “Cleanness and mechanical properties of steel after remelting under different slags by ESR," Key Eng. Mater., Vol. 635, pp. 112-117, 2015, doi: 10.4028 /www.scientific.net/KEM.635.112.
- [47]Y. Pan, C. Chen, S. Wang, “Properties Evaluation of a H13 ESR Hot Work Tool Steel Produced Using a Continuous Casting Electrode," China Steel Technical Report, Vol. 29, pp. 49-55, 2016.
9. 저작권:
- 본 자료는 "[Matilde C. Tojal, F. J. G. Silva, R. D. S. G. Campilho, Arnaldo G. Pinto, Luís Pinto Ferreira]"의 논문: "[Case-Based Product Development of a High-Pressure Die Casting Injection Subset Using Design Science Research]"을 기반으로 합니다.
- 논문 출처: https://doi.org/10.5937/fme2201032T
본 자료는 위 논문을 소개하기 위해 제작되었으며, 상업적 목적으로 무단 사용하는 것을 금지합니다.
Copyright © 2025 CASTMAN. All rights reserved.