本記事では、リンショーピング大学が発行した論文 ["CAE modelling of cast aluminium in automotive structures"] をご紹介します。
1. 概要:
- タイトル: CAE modelling of cast aluminium in automotive structures
- 著者: Sreehari Veditherakal Shreedhara & Subrat Raman Singh
- 発行年: 2019年
- 発行ジャーナル/学会: リンショーピング大学、経営工学部、固体力学部門 (修士論文)
- キーワード: 鋳造アルミニウム、明示的FEA、LS-DYNA、落下塔、スプリングタワー、FEM、CrachFEM、MFGenYld
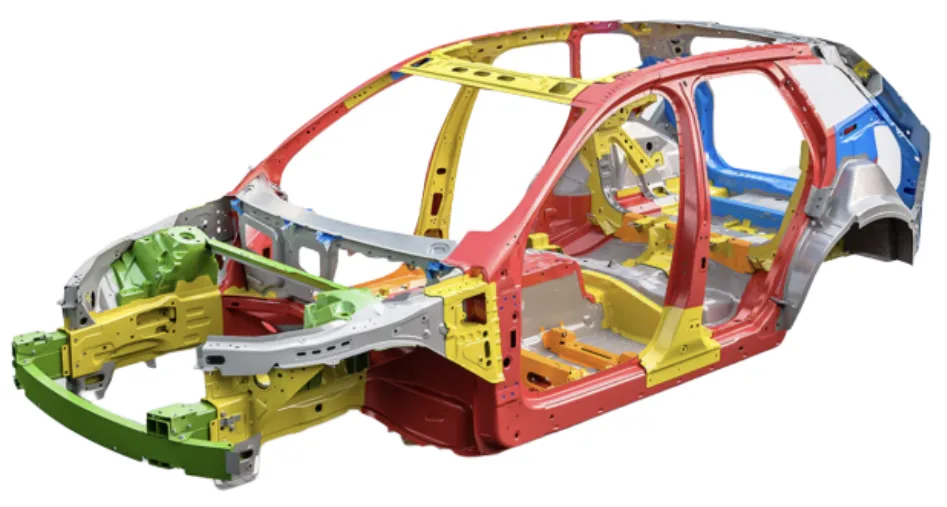
2. 概要または序論
自動車産業では、自動車メーカーがコンピュータ支援エンジニアリング(CAE)ソリューションの結果に基づいてエンジニアリング上の意思決定を行い、プロトタイピングとテストを、コストのかかる反復プロセスから最終的な検証および妥当性確認ステップへと変革することが強く推進されています。コンポーネントの材料特性と環境条件の変動性、および複雑なシステムの根底にある物理学に関する知識の欠如は、決定論的なCAEモデルのみに基づいて信頼性の高い予測を行うことを非現実的にすることがよくあります。そのような分野の1つが、鋳造アルミニウムコンポーネントのCAEモデリングです。これらの鋳造アルミニウムコンポーネントは、その称賛に値する機械的特性により、自動車産業で大きな関連性を獲得しています。鋳造アルミニウム合金の利点は、製造プロセスにおける確立された合金システム、その機能的完全性、および比較的軽量であることです。ただし、製造プロセス中に得られる気孔と微小空孔の存在は、特定の材料挙動を構成し、鋳造材料のモデリングにおける課題を確立します。さらに、材料の低い延性は、破壊を予測するための高度な数値モデルを要求します。
本修士論文の主な焦点は、鋳造アルミニウム合金コンポーネントであるスプリングタワーの、落下塔試験のモデリング手法を調査し、予測された挙動を物理試験結果で検証することです。ボルボ・カー・コーポレーションは現在、MATFEMが提供する鋳造アルミニウム部品の材料モデルを使用しており、この論文では、コンポーネントレベルの試験用の材料モデルを検証するために調査されています。
この目的を達成するために使用された方法論は、落下塔でコンポーネントレベルの試験を実行するための境界条件を開発し、明示的ソルバーLS-DYNAでさまざまなモデリング手法を使用して見つかった得られた結果とこれらを相関させることでした。したがって、シミュレーション結果は主要な設計変更によって影響を受ける可能性があるため、落下塔の正確で現実的なモデリングが重要です。スプリングタワーの詳細な有限要素モデルは、物理試験中に行われた観察から開発されました。洗練されたモデルは、スプリングタワーの既存のモデルと物理試験からの観察と良好な一致を示しました。
3. 研究背景:
研究トピックの背景:
自動車産業では、コンピュータ支援エンジニアリング(CAE)ソリューションの結果に基づいてエンジニアリング上の意思決定を行うことが大きく推進されています。この動きは、プロトタイピングとテストを、コストのかかる反復プロセスから最終的な検証および妥当性確認ステップへと変革することを目的としています。しかし、材料特性、環境条件の変動性、および複雑なシステム物理学に関する知識の不足は、決定論的なCAEモデルのみに基づいて信頼性の高い予測を行うことをしばしば困難にしています。重要な分野の1つは、鋳造アルミニウムコンポーネントのCAEモデリングです。鋳造アルミニウムコンポーネントは、その機械的特性、機能的完全性、および軽量性により、自動車産業でますます重要になっています。鋳造アルミニウム合金は有利である一方で、製造に起因する気孔や微小空孔のためにモデリング上の課題があり、特定の材料挙動や低い延性につながり、破壊予測には高度な数値モデルが必要となります。
既存研究の状況:
ボルボ・カー・コーポレーション(VCC)は、鋳造アルミニウム部品にMATFEMが提供する材料モデルを使用しています。このモデル、MFGenYld+CrachFEMは、FEソフトウェアに組み込まれており、多数のクーポン試験から導き出されたパラメータを持っています。しかし、これらの材料カードは、VCCの鋳造アルミニウムコンポーネントに対して排他的に検証されていません。2012年にVCCで同じ鋳造アルミニウムコンポーネントに対して行われた以前の落下試験は、最適でないセットアップのため、望ましい結果が得られませんでした。接着剤とバインドベルトを使用したこの以前のセットアップでは、衝撃時にスプリングタワーが水平方向に移動し、固定具の剛性問題を示し、荷重に耐えることができませんでした。試験結果は、予想される破壊がなく、延性のみを示しました。
研究の必要性:
MATFEM材料モデルの検証は、特にVCCでのコンポーネントレベルの試験において、FEシミュレーションにおける鋳造アルミニウムコンポーネントへの適用性を保証するために必要です。シミュレーション結果は設計変更によって大きく影響を受ける可能性があるため、落下塔試験の正確で現実的なモデリングが重要です。決定論的なCAEモデルが鋳造アルミニウムコンポーネントの挙動を予測する上で限界があることと、信頼性の高い破壊予測手法の必要性と相まって、改良されたCAEモデリング手法の研究が必要となります。以前の決定的な落下試験は、衝撃荷重下での鋳造アルミニウムコンポーネントの構造的完全性を正確に評価するために、より堅牢な試験セットアップとモデリングアプローチの必要性を強調しています。
4. 研究目的と研究課題:
研究目的:
本修士論文の主な目的は、自動車用途における鋳造アルミニウム構造物のCAEモデリング手法を研究、検証、および改善することです。これには、スウェーデンのヨーテボリにあるボルボ・カーズで使用されている現在のモデリングおよびシミュレーション技術を調査し、鋳造アルミニウム部品、特にスプリングタワーのコンポーネントレベルの試験用の材料モデル(MFGenYld+CrachFEM)を検証することが含まれます。
主要な研究:
主要な研究は、落下塔試験用の鋳造アルミニウム合金コンポーネントであるスプリングタワーのモデリング手法の調査に焦点を当てています。これには、落下塔でのコンポーネントレベルの試験のための境界条件を開発し、明示的ソルバーLS-DYNAでさまざまなモデリング手法を使用して得られた結果とこれらの試験を相関させることが含まれます。研究には、物理試験からの観察に基づいて、スプリングタワーの詳細な有限要素モデルを開発することも含まれます。
研究仮説:
- FEモデルと境界条件を改良して、物理的な落下塔試験をより正確に表現することにより、鋳造アルミニウムコンポーネントのシミュレーション結果と物理試験結果の間の相関関係を改善できると仮説を立てています。
- 本研究では、シェル要素とソリッド要素が、衝撃荷重下の比較的薄肉の鋳造アルミニウム構造物に対して正確な結果を提供するかどうかを判断することを目的としています。
- 本研究は、現在の計算能力に基づいて鋳造アルミニウムに最適な破壊予測手法を特定することを目的としており、特にMFGenYld+CrachFEM材料モデルを評価します。
5. 研究方法
研究デザイン:
本研究では、実験的検証とCAEシミュレーションを中心とした方法論を採用しています。これには、鋳造アルミニウム製スプリングタワーコンポーネントの物理的な落下塔試験と、LS-DYNAを使用した有限要素(FE)シミュレーションによる実験結果の相関関係が含まれます。この研究では、CAE予測の精度を向上させるために、FEモデルと試験セットアップを反復的に改良します。
データ収集方法:
データは、衝撃質量と試験リグに取り付けられた加速度計を使用した物理的な落下塔試験から収集されました。加速度計からのチャネルデータはMETApostにインポートされ、ノイズを除去するためにフィルタリングされ、力、速度、および変位データを取得するために処理されました。力と変位の曲線がプロットされ、分析と比較が行われました。
分析方法:
明示的なFEA(LS-DYNAを使用)をシミュレーションに採用しました。MFGenYld+CrachFEM材料モデルを使用しました。シミュレーションは、シェル要素モデルとソリッド要素モデルの両方で、要素定式化(ELFORM02、ELFORM13、ELFORM16)、メッシュサイズ、および摩擦係数を変更して実行されました。結果は、シミュレーションからの力-変位曲線、破壊位置、およびピーク力を実験データと比較することにより分析されました。METApostは、後処理、塑性ひずみの可視化、および破壊指標としての要素削除の識別に使用されました。
研究対象と範囲:
研究対象は、ボルボ自動車構造で使用されている鋳造アルミニウム合金製スプリングタワーコンポーネントです。範囲は、コンポーネントレベルでのこの単一コンポーネントのCAEモデリングの分析と検証に限定されています。衝撃速度と方向を変えて、2つの荷重ケースを調査しました。この研究は、自動車の耐衝撃性に関連する落下塔試験条件とCAEシミュレーションパラメータに焦点を当てています。
6. 主な研究結果:
主要な研究結果:
- 境界条件の改善: ローラーとガイドレールを含む落下塔セットアップを模倣するようにFEモデルを変更し、ソリッド要素を使用することで、初期の剛体インパクタセットアップと比較して、シミュレーション結果と物理試験結果の間の相関関係が改善されました。
- 要素定式化: ELFORM16(完全積分シェル定式化)は、破壊と力-変位曲線を予測するシェル要素モデルにおいて、ELFORM02と比較してより良い結果を提供しました。ELFORM13は、細かいメッシュであっても、ELFORM16よりも劣る結果を示しました。
- メッシュ感度: ソリッド要素モデルは、シェルモデルよりもメッシュ依存性が高くなりました。ソリッド要素の細かいメッシュ(2.5mmおよび1mm)は、粗いメッシュ(3.4mm)と比較して破壊予測精度を向上させましたが、シミュレーション時間を増加させました。
- 摩擦係数: インパクタとスプリングタワー間の摩擦は重要なパラメータでした。静摩擦係数(fs)を0.2から0.25および0.4に増加させると、力-変位曲線と実験データの相関関係が改善されました。
- シェル要素とソリッド要素: シェル要素モデルは、実験的な力-変位曲線とのより良い相関関係を示しました。ソリッド要素モデル、特に細かいメッシュを使用したモデルは、特にフランジ付近のスキニングなど、破壊位置をより正確に予測しましたが、ピーク力を過大評価する傾向がありました。
- 速度衝撃: より高い衝撃速度(6m/sおよび9m/s)では、最適化されたパラメータを持つシェルモデルとソリッドモデルの両方が、破壊位置を合理的に良好に予測しました。より低い速度(5m/sおよび4m/s)では、相関関係は良好なままでしたが、ソリッドモデルは依然として、物理試験と比較してシミュレーションでより大きな亀裂サイズを予測する傾向がありました。
提示されたデータの分析:
- 図5.3: 初期FEモデル(剛体インパクタとシェル要素(ELFORM02))が、6m/sでの物理試験と比較して、力-変位曲線を正確に予測できなかったことを示しています。FE結果のピーク力(61.68 kN)は、物理試験(75.46 kN)よりも低くなりました。
- 図5.4: 修正されたセットアップとさまざまなメッシュサイズおよび摩擦係数を使用したシェルモデル(ELFORM16)の、6m/sでの力-変位曲線の相関関係の改善を示しています。静摩擦(fs)を0.25に増加させると、結果が改善されました。
- 図5.6: 6m/sでのさまざまなメッシュサイズを持つソリッドモデル(ELFORM13およびELFORM16)の力-変位曲線を比較しています。ソリッドモデルは一般的に、シェルモデルおよび物理試験よりも高い力を示しました。
- 図5.9: 静摩擦(fs)を0.25に調整することにより、物理試験との良好な相関関係を示す、9m/sでのシェルモデルの力-変位曲線を示しています。
- 図5.10: ソリッドモデルも妥当な相関関係を提供しますが、より高い力値を示す、9m/sでのソリッドモデルの力-変位曲線を示しています。
- 図5.12および5.13: 4m/sでのシェルモデルとソリッドモデルの力-変位曲線を表示し、特に最適化された摩擦(シェルではfs=0.4)で、実験曲線との良好な相関関係を示しています。
- 図5.1、5.2、5.5、5.7、5.8、5.11、5.14、5.15、5.16、5.18、5.20、A.1、A.4、A.7、A.10: これらの図は、さまざまな衝撃速度で、さまざまな要素タイプ、メッシュサイズ、および境界条件を使用した物理試験とFEシミュレーションにおける破壊位置と亀裂開始を視覚的に比較しています。ソリッドモデルは一般的に破壊位置をより正確に予測しましたが、シェルモデルはより良い力-変位曲線の相関関係を提供しました。
図の名前リスト:
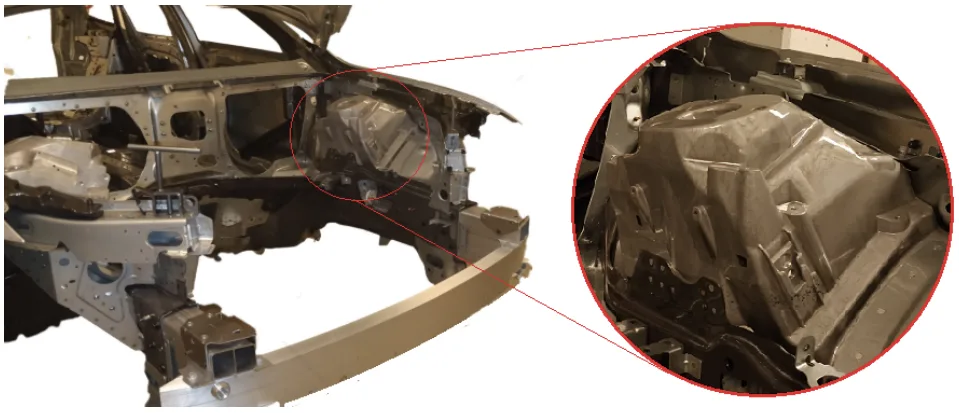
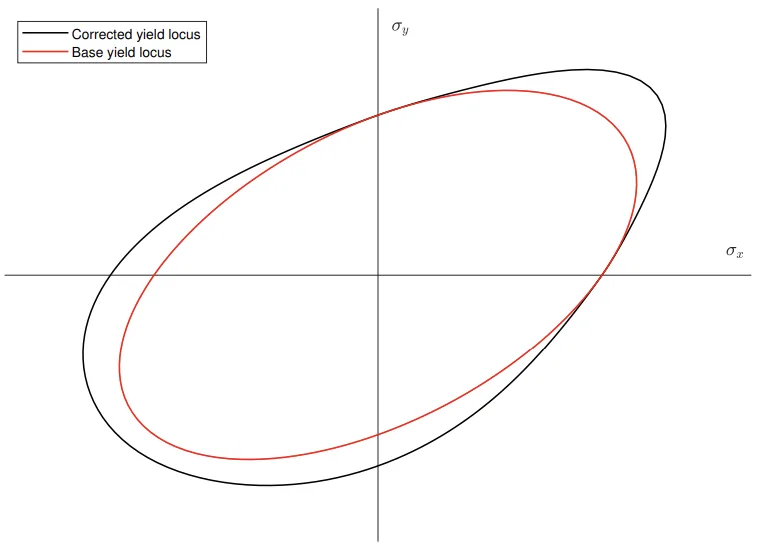
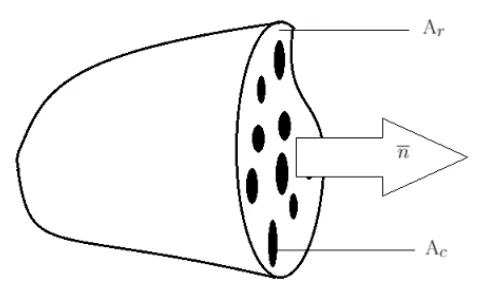
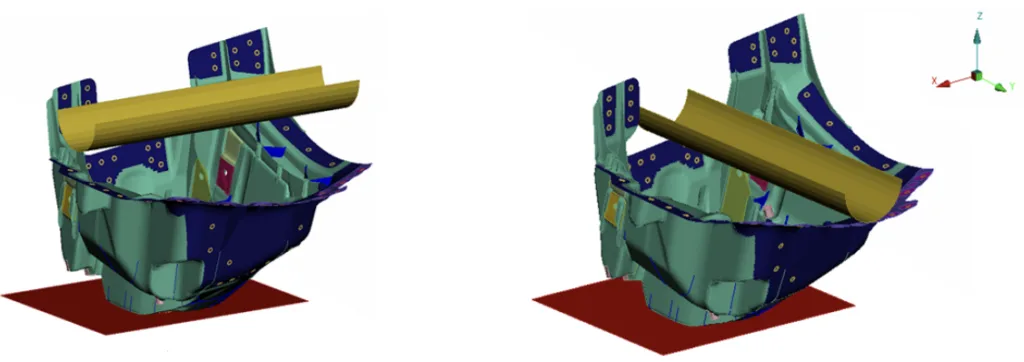
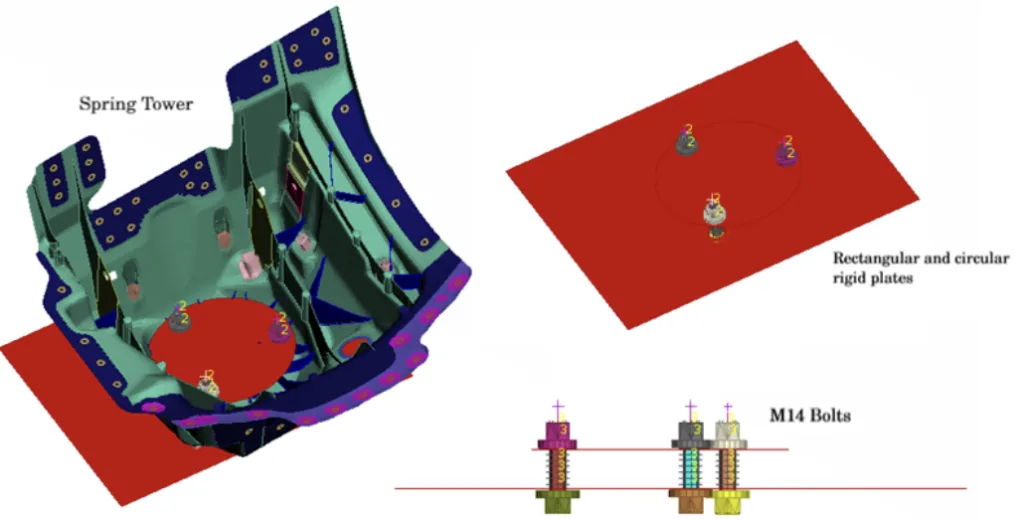
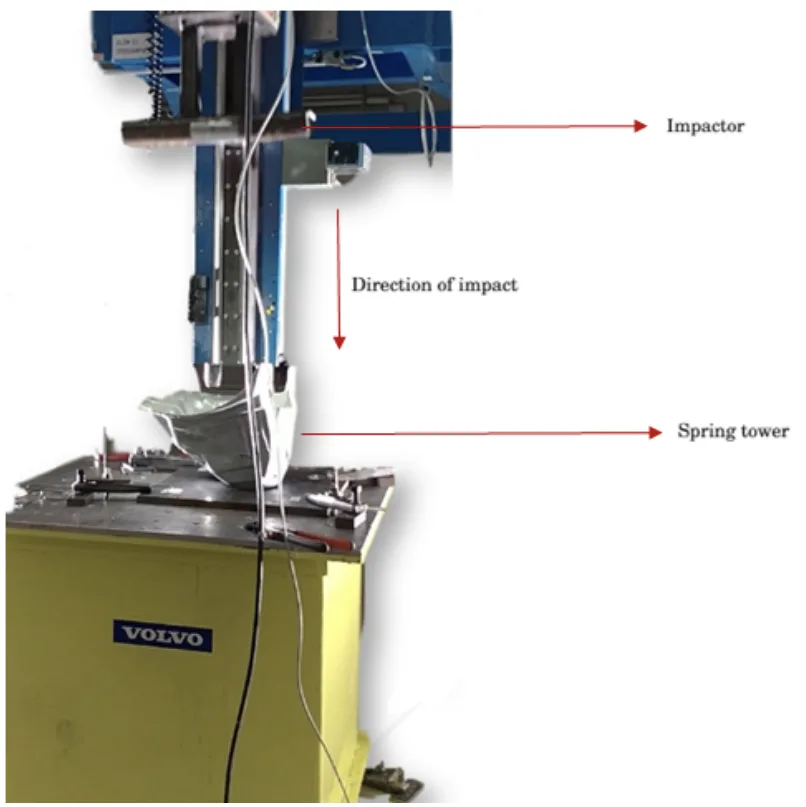
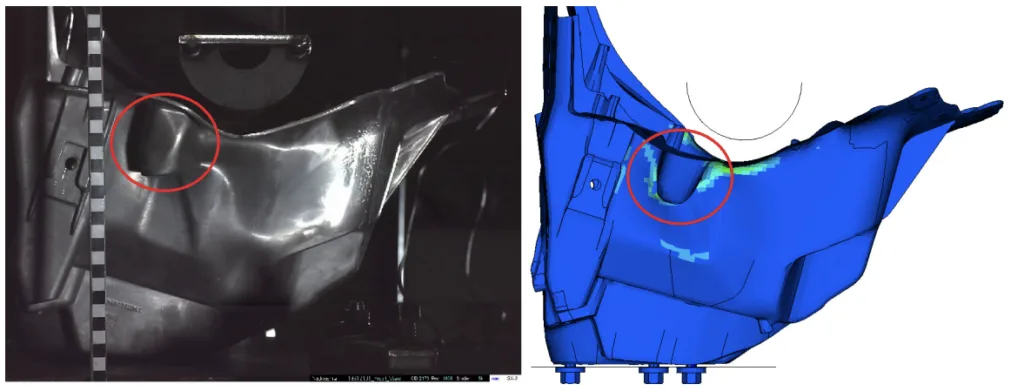
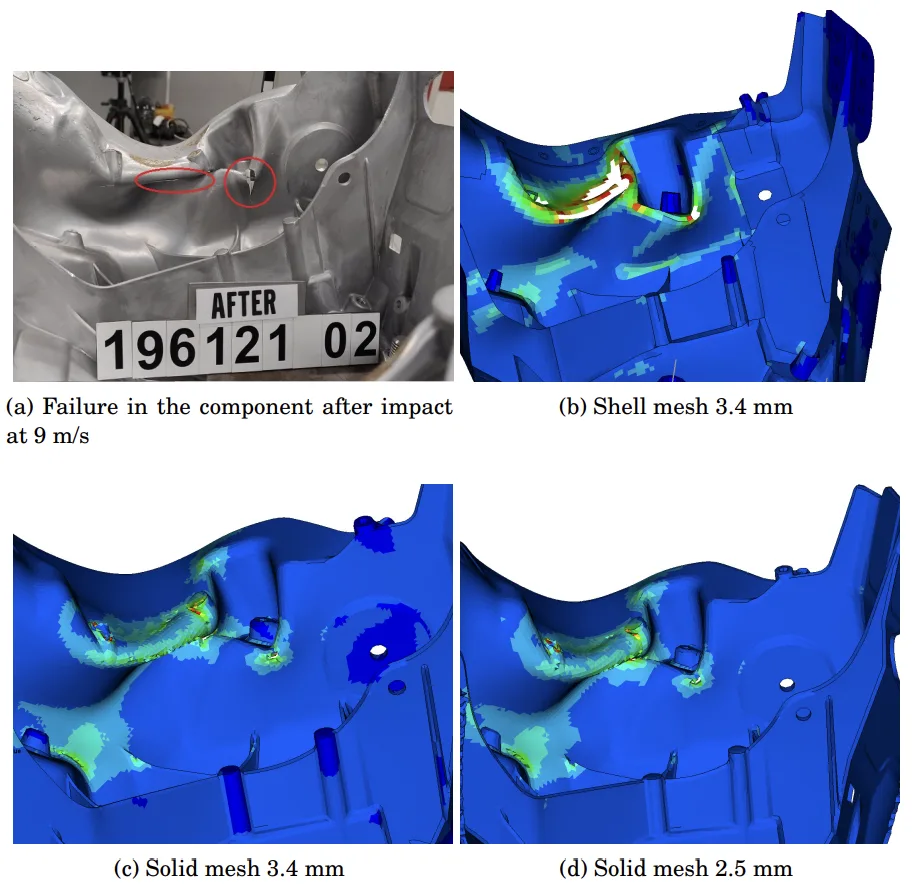
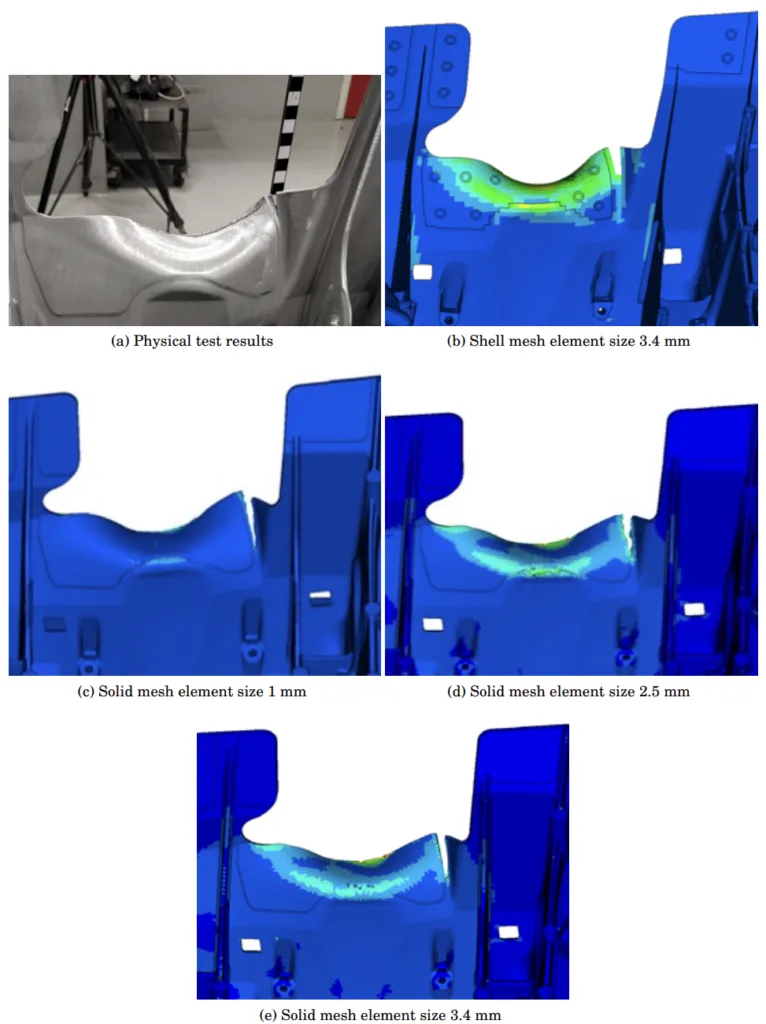
- 図 1.1: ボルボ XC60 のボディ材料
- 図 2.1: ボルボ XC60 のスプリングタワー
- 図 2.2: 以前のテストセットアップ
- 図 3.1: 降伏軌跡
- 図 3.2: 等方硬化 (左) と運動硬化 (右)
- 図 3.3: 無損傷領域 Ar、損傷領域 Ac、および表面 n の法線方向
- 図 3.4: さまざまな破壊モード 塑性不安定性 (左)、延性法線破壊 (中央)、および延性せん断破壊 (右)
- 図 4.1: 荷重ケース 1 と荷重ケース 2
- 図 4.2: FE モデル スプリングタワー、プレート、およびボルト
- 図 4.3: タイミング情報
- 図 4.4: 2 番目の荷重ケースの落下塔における物理試験セットアップ
- 図 4.5: ソリッドメッシュモデルのスプリングタワーとの相関関係のための修正されたセットアップ
- 図 5.1: 6m/s での剛体インパクタを備えた CAE モデルと比較した物理試験
- 図 5.2: 6m/s での物理試験と比較した剛体インパクタを備えた FE モデルにおける不正確な破壊予測
- 図 5.3: 6m/s での物理モデルと元の FE モデルの力対変位曲線
- 図 5.4: 6 m/s でのシェルモデルのシミュレーションを備えた物理試験の力対変位曲線
- 図 5.5: メッシュサイズが異なる 6 m/s での衝撃後の FE シェルモデルの破壊
- 図 5.6: 6m/s でのソリッドモデルのシミュレーションを備えた物理試験の力対変位曲線
- 図 5.7: ELFORM16 を使用したさまざまな要素サイズでの 6 m/s での FE モデルの破壊
- 図 5.8: ELFORM13 を使用したさまざまな要素サイズでの 6 m/s での FE モデルの破壊
- 図 5.9: 9 m/s でのシェルモデルの力対変位曲線
- 図 5.10: 9 m/s でのソリッドモデルの力対変位曲線
- 図 5.11: 9 m/s での物理モデルと FE モデルのさまざまな要素サイズでの破壊
- 図 5.12: 4 m/s でのシェルモデルの力対変位曲線
- 図 5.13: 4 m/s でのソリッドモデルの力対変位曲線
- 図 5.14: 4 m/s でのさまざまな要素サイズでの物理モデルと FE モデルの比較
- 図 5.15: 5 m/s での荷重ケース 2 の物理シミュレーションと FE シミュレーションの比較
- 図 5.16: 5 m/s での物理モデルと FE モデルの比較
- 図 5.17: 5 m/s でのシェルモデルの力対変位曲線
- 図 5.18: 5 m/s でのソリッド FE モデルの比較
- 図 5.19: 5 m/s でのソリッドモデルの力対変位曲線
- 図 A.1: 6 m/s での剛体インパクタによる破壊
- 図 A.2: 7.5m/s でのシェルモデルの力対変位曲線
- 図 A.3: 7.5 m/s でのソリッドモデルの力対変位曲線
- 図 A.4: 7.5 m/s での物理モデルと FE モデルのさまざまな要素サイズでの破壊
- 図 A.5: 5 m/s でのシェルモデルの力対変位曲線の比較
- 図 A.6: 5 m/s でのソリッドモデルの力対変位曲線の比較
- 図 A.7: 5 m/s でのさまざまな要素サイズでの物理モデルと FE モデルにおける亀裂開始
- 図 A.8: 4 m/s でのシェルモデルの力対変位曲線
- 図 A.9: 4 m/s でのソリッドモデルの力対変位曲線
- 図 A.10: 4 m/s でのさまざまな要素サイズでの物理モデルと FE モデルの比較
7. 結論:
主要な調査結果の要約:
本研究では、特に鋳造アルミニウムコンポーネントの場合、CAE結果と物理試験を相関させるために正確な試験セットアップを開発することの重要性を実証しました。MFGenYld+CrachFEM材料モデルは、適切なモデリング手法を適用した場合、物理結果とFE結果の間で良好な相関関係を示しました。荷重ケース1の試験セットアップは、荷重ケース2と比較してより良い選択肢でした。シェル要素モデルとソリッド要素モデルの両方が、妥当な精度の破壊予測を提供しました。ソリッド要素シミュレーションはより正確でしたが、メッシュ依存性が高く、計算コストが高くなりました。ソリッド四面体メッシュの改良は結果を改善しましたが、シミュレーション時間を増加させました。これは、選択的質量スケーリングを明示的な有限要素解析に適用することで部分的に相殺できます。完全積分シェル定式化(ELFORM16)は、計算コストが高いにもかかわらず、縮退積分要素よりも破壊予測に適していました。摩擦係数は、正確なシミュレーション結果を得るために慎重に検討する必要がある重要なパラメータでした。
研究の学術的意義:
本研究は、特に自動車の耐衝撃性シミュレーションにおける、鋳造アルミニウムコンポーネントのCAEモデリングに関する知識体系に貢献しています。シェル要素とソリッド要素のモデリングアプローチ、要素定式化、メッシュ感度、および境界条件と摩擦の影響の詳細な比較分析を提供します。調査結果は、衝撃荷重下での鋳造アルミニウムの構造挙動を予測するためのさまざまなモデリング手法の長所と短所を強調し、この分野の研究者やエンジニアに貴重な洞察を提供します。
実用的な意味合い:
本研究は、鋳造アルミニウム自動車構造物のCAE解析に関与するエンジニアに実用的なガイドラインを提供します。力-変位曲線の相関関係については、ELFORM16を備えたシェル要素モデルが効率的で正確であることが示唆されています。正確な破壊位置予測、特に複雑な形状やスキニングなどの局所的な効果については、計算コストは高くなりますが、細かいメッシュを備えたソリッド要素モデルが望ましいです。この研究では、信頼性と予測性のある鋳造アルミニウムコンポーネントの結果を得るために、材料モデルを実験的に検証し、CAEシミュレーションで試験セットアップと摩擦パラメータを慎重に検討する必要があることを強調しています。選択的質量スケーリングは、精度を大幅に損なうことなく、計算効率を最適化するために使用できます。
研究の限界と今後の研究分野:
本研究は、単一の鋳造アルミニウム製スプリングタワーコンポーネントと特定の落下塔試験条件に限定されています。使用された摩擦値は推定値であり、実験的に決定されたものではありません。今後の研究では、調査結果を一般化するために、より広範囲の鋳造アルミニウムコンポーネントと荷重条件を調査する必要があります。シミュレーション精度を向上させるには、摩擦係数を実験的に決定することが重要です。鋳造アルミニウムシミュレーションにおけるさまざまなひずみレベルに最適な要素定式化を決定的に結論付けるには、さらなる研究が必要です。鋳造アルミニウムの亀裂伝播予測のために、CrachFEMを超える高度な損傷および破壊モデルを調査することも有益です。
8. 参考文献:
- [1] Djukanovic G. Aluminium vs. steel in electric vehicles : the battle goes on. Aluminium insider; 2018. https://aluminiuminsider.com/aluminium-vs-steel-in-electric-vehicles-the-battle-goes-on/.
- [2] Lambert F. Volvo clarifies electrification plan, aims for 50 percent of sales to be fully electric by 2025. electrek; 2018. https://electrek.co/2018/04/25/volvo-electrification-plan-fully-electric/.
- [3] Dharwadkar N, Adivi KP. Modelling of Engine suspension components for crash simulation. Division of Vehicle safety, Department of Applied mechanics, Chalmers University of technology; 2014.
- [4] Dell H, Gese H, Oberhofer G. MF GenYID + CrachFEM User's theory Manual. 2014;.
- [5] Stouffer DC, Dame LT. Inelastic deformation of metals. 1st ed. John Wiley and Sons; 1996.
- [6] Björklund O. Ductile failure in High Strength Steel Sheets. Linköping University; 2014.
- [7] Xue L. Damage accumulation and fracture initiation in uncracked ductile solids subject to triaxial loading. 2006;.
- [8] Brenner F, Buckley M, Gese H, Oberhofer G. Influence of discretisation on stiffness and failure prediction in crashworthiness simulation of automotive high pressure die cast components. 9th European LS-DYNA Conference. 2013 Feb; Available from: https://www.dynalook.com/conferences/9th-european-ls-dyna-conference.
- [9] Hallquist J. LS-DYNA theory manual. Livermore Software Technology Corporation, California; 2006.
- [10] Olovsson L, Simonsson K, Unosson M. Selective mass scaling for explicit finite element analyses. 2005;.
- [11] Erhart T. Review of solid element formulations in LS-DYNA. LS-DYNA forum 2011; 2011.
- [12] Cook RD, Malkus DS, Plesha ME. Concepts and Applications of Finite Element Analysis, 3rd Edition. 3rd ed. Wiley Student Edition; 2004.
9. 著作権:
- この資料は、"SHREEHARI VEDITHERAKAL SHREEDHARA, SUBRAT RAMAN SINGH" の論文です: "CAE modelling of cast aluminium in automotive structures" に基づいています。
- 論文ソース: https://www.diva-portal.org/smash/record.jsf?pid=diva2%3A1291819&dswid=-4870
この資料は上記の論文を紹介するために作成されたものであり、商業目的での無断使用は禁止されています。
Copyright © 2025 CASTMAN. All rights reserved.