본 논문 요약은 ['수치 시뮬레이션 및 실험적 검증을 통한 자동차 발전기 상부 커버의 다이캐스팅 공정 설계'] 논문을 기반으로 작성되었으며, ['International Journal of Cast Metals Research']에 게재되었습니다.
1. 개요:
- 제목: 수치 시뮬레이션 및 실험적 검증을 통한 자동차 발전기 상부 커버의 다이캐스팅 공정 설계 (Design of die casting process of top cover of automobile generator through numerical simulations and its experimental validation)
- 저자: J.-H. Chen, W.-S. Hwang, C.-H. Wu, S.-S. Lu
- 발행 연도: 2011년
- 발행 저널/학회: International Journal of Cast Metals Research
- 키워드: 다이캐스팅 (Die casting), 수치 시뮬레이션 (Numerical simulation), 실험적 검증 (Experimental validation)
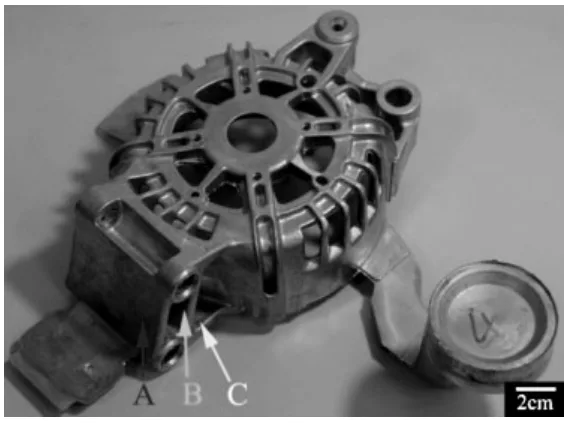
2. 연구 배경:
연구 주제 배경:
알루미늄 합금은 경량, 우수한 전기 및 열 전도성, 높은 열 및 광 반사율, 미려한 표면 조도, 뛰어난 내식성 등 다양한 장점으로 인해 운송 장비 및 정밀 가공을 포함한 다양한 산업 분야에서 활용이 증가하고 있습니다. 특히 경량 항공기 및 자동차에 적용하여 CO2 배출량을 획기적으로 줄일 수 있습니다. 다이캐스팅은 알루미늄 합금을 가공하는 주요 주조 방법 중 하나입니다. 그러나 기존의 다이캐스팅 금형 설계 및 공정 변수 설정은 경험과 반복적인 수정에 의존하여 시간과 비용이 많이 소모됩니다.
기존 연구 현황:
제품 불량률을 줄이기 위해 다이캐스팅 공정 조건 및 금형 설계를 최적화하는 데 컴퓨터 지원 엔지니어링(CAE) 분석 및 컴퓨터 지원 설계(CAD) 기술이 점점 더 많이 사용되고 있습니다. 수치 시뮬레이션은 금형 설계를 최적화하고 주조 품질을 향상시키는 강력한 도구로 부상했습니다. 수많은 연구에서 수치 시뮬레이션의 정확성이 입증되었지만, 주조 결함의 근본 원인을 심층적으로 연구하기보다는 시뮬레이션 정확성 입증에만 초점을 맞추는 경향이 있습니다.
연구의 필요성:
본 연구는 주조 결함을 줄이고 다이캐스팅 공정 설계의 효율성을 개선해야 하는 산업계의 지속적인 요구에 의해 필요성이 제기되었습니다. 수치 시뮬레이션의 단순 검증을 넘어 다이캐스팅 공정에서 결함의 근본 원인을 진단하고 해결하는 데 적극적으로 활용해야 할 필요성이 분명히 존재합니다.
3. 연구 목적 및 연구 질문:
연구 목적:
본 연구의 주요 목적은 수치 시뮬레이션을 활용하여 자동차 발전기 상부 커버의 기존 다이캐스팅 금형 설계에서 결함의 위치와 유형을 예측하는 것입니다. 또한, 연구는 다이캐스팅 금형 설계 개선을 용이하게 하기 위해 이러한 결함의 원인을 조사하는 것을 목표로 합니다.
핵심 연구:
본 연구는 다이캐스팅 공정에서 발생하는 유체 흐름 및 응고 열전달 현상을 분석하기 위해 수치 시뮬레이션을 사용하는 데 중점을 둡니다. 시뮬레이션 결과는 실험적 다이캐스팅을 통해 검증됩니다. 시뮬레이션에서 얻은 상세 정보를 바탕으로 개선된 다이캐스팅 설계를 제안하고 평가합니다.
연구 가설:
본 연구의 중심 가설은 다음과 같습니다.
- 수치 시뮬레이션은 다이캐스팅 공정에서 주조 결함의 발생 및 위치를 정확하게 예측할 수 있다.
- 수치 시뮬레이션 분석을 통해 얻은 정보를 바탕으로 개선된 다이캐스팅 설계는 식별된 주조 결함을 효과적으로 감소시키거나 제거할 수 있다.
4. 연구 방법론
연구 설계:
본 연구는 수치 시뮬레이션과 실험적 검증을 결합한 혼합 방법론적 접근 방식을 채택합니다. 연구 설계는 기존의 단일 러너 시스템 다이캐스팅 설계와 개선된 이중 러너 시스템 설계를 비교 분석하는 것을 포함합니다.
자료 수집 방법:
자료 수집은 두 가지 주요 방법을 통해 이루어집니다.
- 수치 시뮬레이션: ADSTEFAN 소프트웨어 패키지를 활용하여 다이캐스팅 공정 내 유체 흐름, 온도 분포 및 잔류 가스를 모델링하는 시뮬레이션을 수행했습니다.
- 실험적 다이캐스팅: 냉간 챔버 다이캐스팅을 사용하여 기존 및 개선된 금형 설계를 모두 사용하여 자동차 발전기 상부 커버를 제조했습니다. 주조품을 육안으로 검사하여 표면 결함을 식별하고 특성화했습니다.
분석 방법:
분석 방법은 다음을 포함합니다.
- 시뮬레이션 데이터 분석: ADSTEFAN 시뮬레이션에서 얻은 충전 시간, 온도 분포 및 잔류 가스 흐름 패턴 분석을 통해 결함 위치 및 유형을 예측합니다.
- 실험 데이터 분석: 실험 주조품의 육안 검사를 통해 표면 결함을 식별하고 분류하고, 이러한 결과를 수치 시뮬레이션의 결함 예측과 연관시킵니다.
연구 대상 및 범위:
연구 대상은 알루미늄 합금 ADC12를 사용하는 자동차 발전기 상부 커버의 다이캐스팅 공정입니다. 연구 범위는 이 특정 다이캐스팅 응용 분야에서 단일 러너 시스템과 이중 러너 시스템의 성능을 조사하고 비교하는 데 국한됩니다.
5. 주요 연구 결과:
핵심 연구 결과:
주요 연구 결과는 다음과 같이 요약됩니다.
- 단일 러너 시스템의 결함 식별: 기존의 단일 러너 시스템을 사용한 다이캐스팅은 그림 4에서 볼 수 있듯이 "콜드 모아레" 및 "미충진" 영역을 포함한 표면 결함을 발생시켰습니다.
- 수치 시뮬레이션 검증: ADSTEFAN을 사용한 수치 시뮬레이션은 실험 주조품에서 관찰된 결함의 위치와 유형을 성공적으로 예측했습니다. 시뮬레이션에서 얻은 충전 시간(그림 5), 온도 분포(그림 6-9) 및 잔류 가스 흐름(그림 10) 분석은 실험적으로 관찰된 결함과 상관 관계를 보였습니다.
- 이중 러너 시스템을 통한 개선된 설계: 시뮬레이션 통찰력을 기반으로 이중 러너 시스템(그림 12)을 통합한 개선된 다이캐스팅 설계를 제안했습니다. 이 설계는 향상된 유체 흐름 및 온도 분포 균일성을 보여주었습니다.
- 개선된 설계에서 결함 제거: 이중 러너 시스템 설계의 실험적 검증 결과 표면 결함이 관찰되지 않는 건전한 주조품을 얻었습니다(그림 16, 17). 이중 러너 시스템은 단일 러너 시스템에서 관찰된 결함을 효과적으로 완화했습니다.
데이터 해석:
단일 러너 시스템의 결함은 비대칭 캐비티 충전, 불균일한 온도 분포 및 다이캐스팅 공정 중 가스 포집으로 인한 것으로 해석됩니다. 특히 시뮬레이션 결과 단일 러너 시스템은 다음을 초래하는 것으로 나타났습니다.
- 두꺼운 부분이 마지막에 채워지는 비대칭 충전 패턴(그림 5).
- 불균일한 온도 분포로 인해 조기 응고 및 "콜드 모아레" 결함이 발생할 가능성(그림 9).
- 갇힌 공기 주머니로 인한 공기 주머니 결함(그림 10).
- 높은 게이트 속도(~128 m/s)로 인한 금형 침식 위험 증가(그림 11).
개선된 이중 러너 시스템은 다음을 통해 이러한 문제를 해결했습니다.
- 보다 대칭적인 캐비티 충전 촉진(그림 14).
- 보다 균일한 온도 분포 달성(그림 15).
- 게이트 속도를 ~62 m/s로 감소시켜 금형 침식 완화.
그림 목록:
- Fig. 1 ADSTEFAN 소프트웨어로 가져온 자동차 발전기 상부 커버의 파일 (STL)
- Fig. 2 유입 게이트의 메시 및 위치
- Fig. 3 단일 러너 시스템을 사용한 주조
- Fig. 4 단일 러너 시스템 다이캐스팅 표면의 결함
- Fig. 5 단일 러너 시스템을 사용한 자동차 발전기 상부 커버 다이캐스팅의 충전 시간 결과
- Fig. 6 0.0123초 충전 시간의 유체 흐름 결과 및 온도 분포
- Fig. 7 0.0346초 충전 시간의 유체 흐름 결과 및 온도 분포
- Fig. 8 0-0708초 충전 시간의 유체 흐름 결과 및 온도 분포
- Fig. 9 0.0746초 충전 시간의 유체 흐름 결과 및 온도 분포
- Fig. 10 단일 러너 시스템을 사용한 자동차 발전기 상부 커버 다이캐스팅 공정의 잔류 가스
- Fig. 11 단일 러너 시스템을 사용한 자동차 발전기 상부 커버 게이트의 유체 흐름 속도
- Fig. 12 이중 러너 시스템의 메시
- Fig. 13 이중 러너 시스템을 사용한 자동차 발전기 상부 커버 게이트의 유체 흐름 속도
- Fig. 14 이중 러너 시스템을 사용한 자동차 발전기 상부 커버 다이캐스팅의 충전 시간 결과
- Fig. 15 0.069초 충전 시간의 이중 러너 시스템을 사용한 자동차 발전기 상부 커버의 온도 분포
- Fig. 16 이중 러너 시스템 주조
- Fig. 17 이중 러너 시스템을 사용한 자동차 발전기 상부 커버 다이캐스팅의 개선된 표면 결함
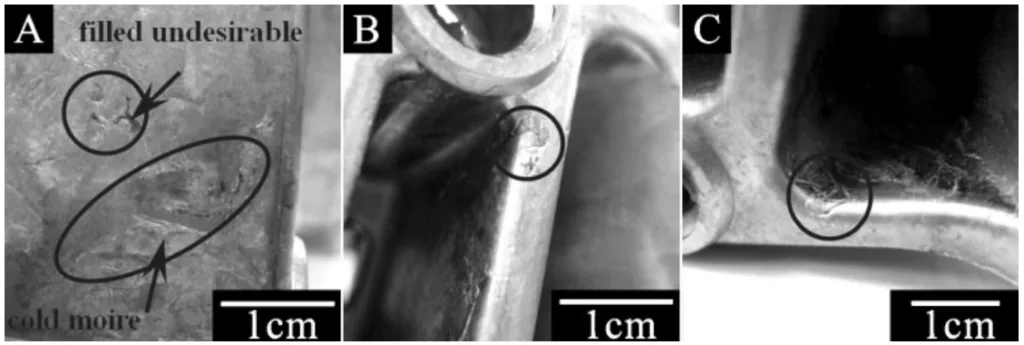
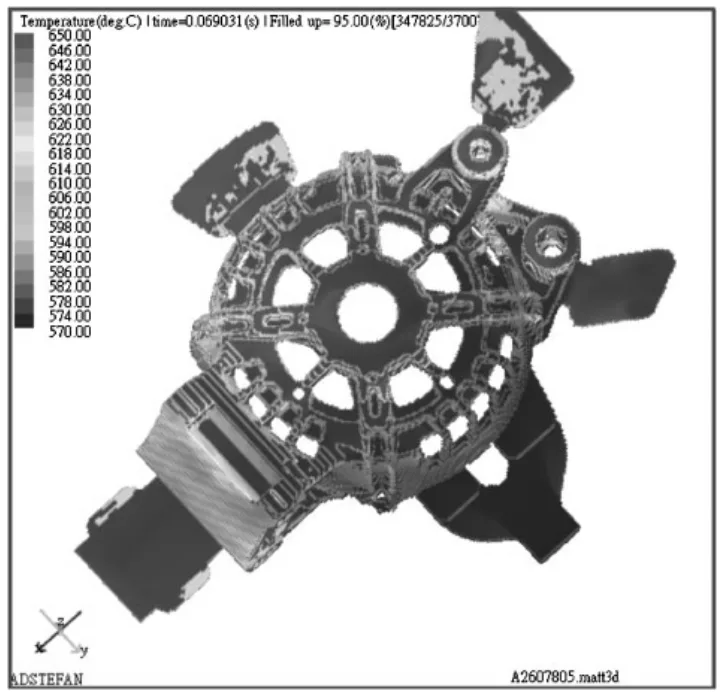
generator with double runner system at filling time of
0,069s
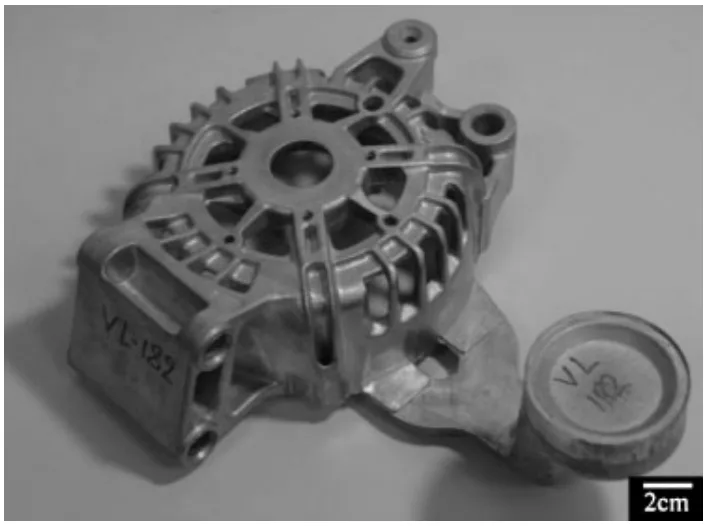
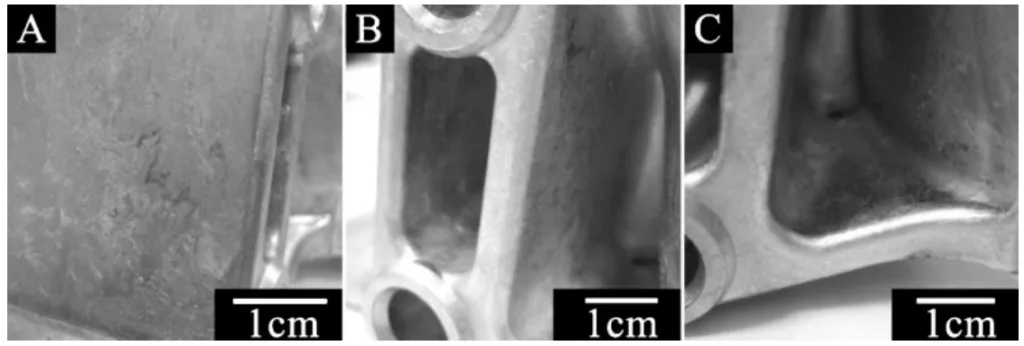
6. 결론:
주요 결과 요약:
본 연구는 다이캐스팅 공정에서 주조 결함을 예측하는 데 수치 시뮬레이션의 정확성과 신뢰성을 성공적으로 입증했습니다. ADSTEFAN 소프트웨어를 사용하여 연구팀은 자동차 발전기 상부 커버의 단일 러너 시스템 설계에서 결함을 정확하게 식별하고 예측했습니다. 또한 수치 시뮬레이션에서 얻은 통찰력을 활용하여 개선된 이중 러너 시스템 설계를 개발하고 실험적으로 검증했습니다. 이 개선된 설계는 표면 결함을 효과적으로 제거하고 다이캐스팅의 전반적인 품질을 향상시켰습니다.
연구의 학문적 의의:
본 연구는 다음을 통해 학문적 지식 체계에 기여합니다.
- 다이캐스팅 공정에서 결함을 예측하고 진단하는 강력한 도구로서 수치 시뮬레이션의 적용을 검증합니다.
- 다이캐스팅에서 유체 흐름, 온도 분포 및 결함 형성에 영향을 미치는 러너 시스템 설계의 중요한 역할을 강조합니다.
- 다이캐스팅에서 수치 시뮬레이션 기반 설계 최적화의 효과를 입증하는 상세한 사례 연구를 제공합니다.
실용적 의미:
본 연구의 실용적 의미는 다이캐스팅 산업에 매우 중요합니다.
- 다이캐스팅 설계를 최적화하고, 불량률을 줄이고, 주조 품질을 향상시키기 위해 수치 시뮬레이션을 활용하는 명확한 방법론을 제공합니다.
- 특히 균일한 충전 및 온도 분포를 달성하는 데 있어 복잡한 다이캐스팅 부품에 대해 단일 러너 시스템에서 이중 러너 시스템으로 전환하는 것의 실질적인 이점을 입증합니다.
- 연구 결과는 콜드 모아레, 미충진 영역 및 공기 주머니와 같은 결함을 최소화하기 위해 러너 시스템을 설계하는 데 다이캐스팅 엔지니어에게 귀중한 지침을 제공합니다.
연구의 한계점
본 연구의 한계점은 다음과 같습니다.
- 연구는 특정 부품인 자동차 발전기 상부 커버와 단일 알루미늄 합금인 ADC12에 초점을 맞추고 있습니다. 연구 결과의 다른 부품 형상 및 합금 시스템으로의 일반화 가능성은 추가 조사가 필요합니다.
- 연구는 주로 러너 시스템 설계를 조사했습니다. 주조 품질에 영향을 미칠 수 있는 다른 공정 변수 및 금형 설계 측면은 광범위하게 탐구되지 않았습니다.
7. 향후 후속 연구:
- 후속 연구 방향:
향후 연구에서는 수치 시뮬레이션 기반 최적화의 광범위한 적용 가능성을 검증하기 위해 이 방법론을 더 넓은 범위의 다이캐스팅 부품 및 알루미늄 합금으로 확장해야 합니다. 주입 속도, 압력 및 냉각 전략과 같은 다른 다이캐스팅 공정 변수가 주조 품질에 미치는 영향에 대한 추가 조사도 필요합니다. - 추가 탐구가 필요한 영역:
추가 탐구가 필요한 영역에는 다양한 주조 형상에 대한 최적의 러너 치수 및 구성을 결정하기 위한 이중 러너 시스템 설계의 파라메트릭 최적화가 포함됩니다. 또한 이중 러너 시스템에서 감소된 게이트 속도가 금형 수명 및 유지 보수 비용에 미치는 장기적인 영향도 평가해야 합니다.
8. 참고 문헌:
- 1. P. O. Lafsson, R. Sandstro and As. Karlsson: J. Mater. Sci., 1997, 32, (16), 4383-4390.
- 2. A. Kaye: 'Die casting metallurgy', 23-41; 1982, London, Butterworth Scientific.
- 3. M. C. Flemings: 'Solidification processing', 181-183; 1974, New York, McGraw-Hill.
- 4. N. A. El-Mahallawy, M. A. Taha, E. Pokora and F. Klein: J. Mater. Process. Technol., 1998, 73, (1-3), 125-138.
- 5. Y.-B. Jiao and Y.-H. Wei: Mech. Eng. Autom., 2008, 5, 97-100.
- 6. M. T. Rowley (ed.): 'International atlas of casting defects', 46-47; 1979, Des Plaines, IL, American Foundrymen Society.
9. 저작권:
- 본 자료는 "J.-H. Chen et al."의 논문: "수치 시뮬레이션 및 실험적 검증을 통한 자동차 발전기 상부 커버의 다이캐스팅 공정 설계"를 기반으로 작성되었습니다.
- 논문 출처: DOI 10.1179/136404611X13001912813906
본 자료는 위 논문을 기반으로 요약되었으며, 상업적 목적으로 무단 사용하는 것을 금지합니다.
Copyright © 2025 CASTMAN. All rights reserved.