본 요약은 The International Journal of Advanced Manufacturing Technology에 게재된 논문 "A Study on Development of a Die Design System for Diecasting"을 기반으로 작성되었습니다.
1. 개요:
- 제목: 다이캐스팅 금형 설계 시스템 개발 연구 (A Study on Development of a Die Design System for Diecasting)
- 저자: J. C. Choi, T. H. Kwon, J. H. Park, J. H. Kim, C. H. Kim
- 발행 연도: 2002년
- 발행 학술지/학회: The International Journal of Advanced Manufacturing Technology
- 키워드: 다이캐스팅 (Diecasting); 금형 설계 시스템 (Die design system); 게이트 (Gate); 룰 기반 (Rule base); 러너 (Runner)
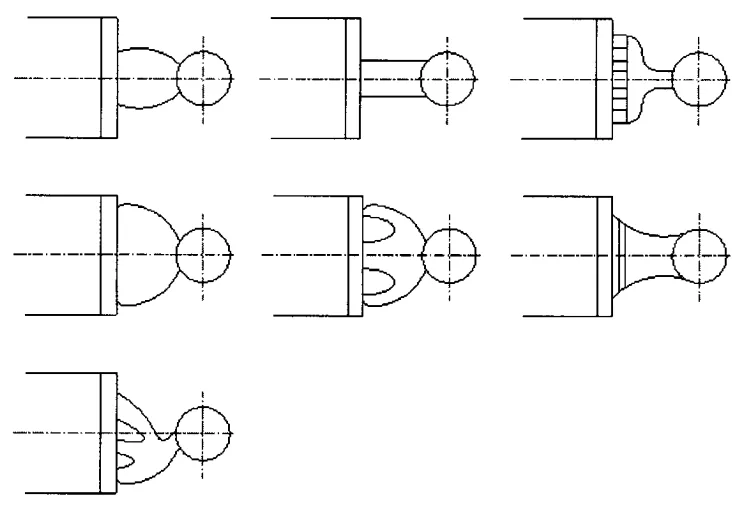
2. 연구 배경:
다이캐스팅은 짧은 리드 타임과 우수한 표면 조도를 요구하는 대량 생산 부품 제조에 있어 핵심적인 성형 방법입니다. 복잡한 형상과 박육 부품 생산 능력, 높은 생산성 및 치수 정확도 등의 장점으로 인해 자동차, 항공우주, 전자 산업 등에서 빠르게 발전하고 있습니다. 그러나 기존의 다이캐스팅 금형 설계는 경험 많은 설계자의 시행착오 방식에 의존해 왔습니다. 이러한 접근 방식은 숙련된 전문가의 노하우를 활용하지만, 경제적 비효율성과 개발 주기 지연을 야기합니다.
기존의 CAD (Computer-Aided Design) 및 CAM (Computer-Aided Manufacturing) 시스템은 사출 성형 및 기타 제조 분야에서는 널리 사용되지만, 다이캐스팅 금형 설계에는 적용이 제한적이었습니다. 더욱이, 현재의 생산 현장 관행은 금형 내 용융 금속 흐름 및 열 전달을 예측하는 강력한 분석 능력이 부족합니다. 이러한 결함으로 인해 특히 러너-게이트 시스템과 관련하여 반복적인 실험적 다이캐스팅 및 수정 작업이 필요하며, 이는 가공 시간과 비용 증가로 이어집니다. 러너, 게이트, 비스킷, 오버플로우, 에어 벤트 등 부품 시스템 요소를 포괄하는 복잡한 다이캐스팅 금형 설계는 상당한 전문 지식을 요구합니다. 설계 결함이 공정 후반에 발견될 경우 금형 수정에 많은 시간과 자원이 낭비될 수 있습니다.
3. 연구 목적 및 연구 질문:
본 연구는 기존 다이캐스팅 금형 설계의 한계를 극복하기 위해 CAD (Computer-Aided Design) 시스템 개발을 목표로 합니다. 주요 연구 목적은 특히 러너-게이트 시스템을 중심으로 다이캐스팅 금형 설계 프로세스를 자동화하는 것입니다. 본 연구는 다음과 같은 핵심 연구 질문을 다룹니다.
- 다이캐스팅, 특히 러너-게이트 시스템의 금형 설계 프로세스를 자동화하기 위한 CAD 시스템은 어떻게 개발될 수 있는가?
- 다이캐스팅 금형 설계에서 시행착오에 대한 의존도를 최소화하기 위해 특정 규칙과 방정식이 CAD 시스템에 어떻게 통합될 수 있는가?
- 3D 형상 처리 및 공정 계획 기술을 통합하여 금형 설계의 포괄적인 자동화를 어떻게 달성할 수 있는가?
기본적인 연구 가설은 확립된 다이캐스팅 원칙과 알고리즘을 통합한 룰 기반 CAD 시스템이 금형 설계의 효율성과 정확성을 크게 향상시켜 시행착오 반복으로 인한 개발 시간과 비용을 절감할 수 있다는 것입니다.
4. 연구 방법론:
본 연구는 다이캐스팅 금형 설계를 위한 CAD 시스템 개발에 초점을 맞춘 시스템 개발 접근 방식을 채택합니다. 연구 설계는 AutoLISP 언어를 사용하여 AutoCAD 환경 내에서 알고리즘 개발 및 시스템 구현을 중심으로 합니다. 특히 러너-게이트 시스템에 대한 금형 설계 자동화 프로세스를 설명하기 위해 플로우차트 기반 방법론이 제시됩니다.
본 연구의 데이터 수집은 러너 및 게이트 설계와 관련된 기존 다이캐스팅 지식, 경험적 규칙 및 확립된 방정식을 편집하는 것을 포함합니다. 이 지식 기반은 룰 기반 시스템의 기초를 형성합니다. 분석 방법은 주조 설계, 금형 레이아웃 설계 및 금형 생성을 위한 알고리즘 개발 및 구현을 포함합니다. 시스템의 기능은 캡 모양 제품 (모터 풀리) 및 모터 풀리 제품과 같은 예시 제품에 적용하여 자동 설계 프로세스 기능을 입증합니다. 연구 범위는 알루미늄 합금 다이캐스팅 금형 설계로 제한되며, 러너-게이트 시스템에 중점을 둡니다.
5. 주요 연구 결과:
본 연구의 핵심 결과는 다이캐스팅 금형 설계를 위한 기능적인 CAD 시스템 개발입니다. 주요 결과는 다음과 같습니다.
- 자동화된 금형 설계 알고리즘: 특히 러너-게이트 시스템에 대한 금형 설계를 자동화하는 알고리즘이 성공적으로 개발되었습니다. 이 알고리즘은 광범위한 수동 조정의 필요성을 줄여 효율적이고 효과적인 금형 설계를 용이하게 합니다.
- CAD 시스템 구현: 제안된 금형 설계 알고리즘 및 관련 데이터베이스가 AutoLISP를 사용하여 AutoCAD 내에 구현되었습니다. 이는 엔지니어가 다이캐스팅 금형 설계를 지원할 수 있는 실용적인 CAD 시스템을 만들었습니다.
- 플로우차트 기반 시스템 아키텍처: 본 연구에서는 주조 설계 (Fig. 2), 금형 레이아웃 설계 (Fig. 3) 및 금형 생성 (Fig. 4) 단계를 간략하게 설명하는 상세한 플로우차트를 제시했습니다. 이러한 플로우차트는 금형 설계 프로세스를 자동화하는 구조화된 접근 방식을 제공합니다.
- 데이터베이스 통합: 시스템은 다음과 같은 필수 데이터베이스를 통합합니다.
- 재료 및 수축 데이터베이스: 알루미늄 다이캐스팅 합금의 물리적 및 기계적 특성 (Table 1) 및 수축 데이터를 포함합니다.
- 게이트 및 러너 데이터베이스: 충전 속도 및 최소 주조 두께 (Table 2) 및 러너 설계 매개변수를 기반으로 게이트 면적 계산을 위한 데이터를 제공합니다.
- 오버플로우, 에어 벤트 및 캐비티 블록 데이터베이스: 오버플로우, 에어 벤트 및 캐비티 블록 구성에 대한 설계 지침을 포함합니다.
- 시스템 적용 예시: 개발된 시스템은 캡 모양 제품 (Fig. 9) 및 모터 풀리 제품 (Fig. 10)의 금형 설계를 성공적으로 적용하여 실용적인 적용 가능성을 입증했습니다.
그림 목록:
- Fig. 1. 다이캐스팅 금형 설계 시스템의 플로우차트 (Flowchart of the die design system for diecasting).
- Fig. 2. 주조 설계 플로우차트 (Flowchart for cast design).
- Fig. 3. 금형 레이아웃 설계 플로우차트 (Flowchart for die layout design).
- Fig. 4. 금형 생성 플로우차트 (Flowchart for die generation).
- Fig. 5. 러너의 일반적인 단면 형상 개략도 (Schematic drawing of general section shape for runner).
- Fig. 6. 러너 유형 개략도 (Schematic drawing of runner type).
- Fig. 7. 오버플로우의 일반적인 형상 개략도 (Schematic drawing of general shape for overflow).
- Fig. 8. 캐비티 블록의 일반적인 형상 개략도 (Schematic drawing of general shape for cavity block).
- Fig. 9. 캡 모양 제품에 개발된 시스템 적용 (Application of the developed system for a cap-shaped product). (a), (b), (c)
- Fig. 10. 모터 풀리 제품에 개발된 시스템 적용 (Application of the developed system for a motor pulley product). (a), (b), (c)
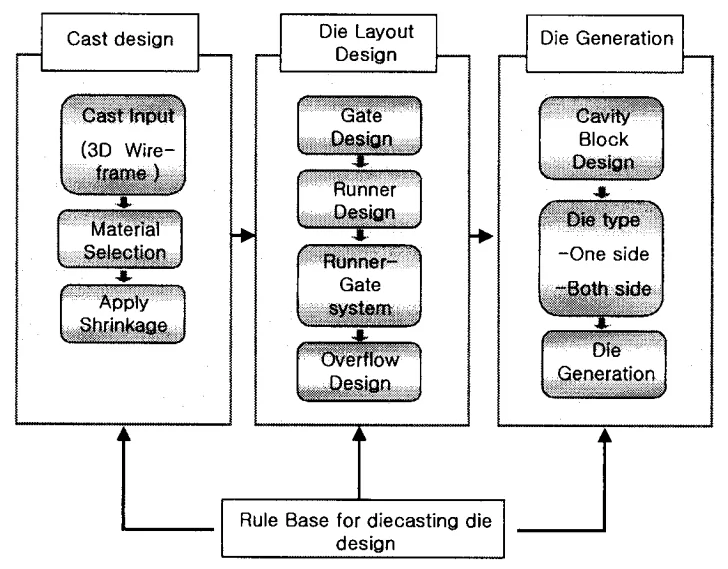
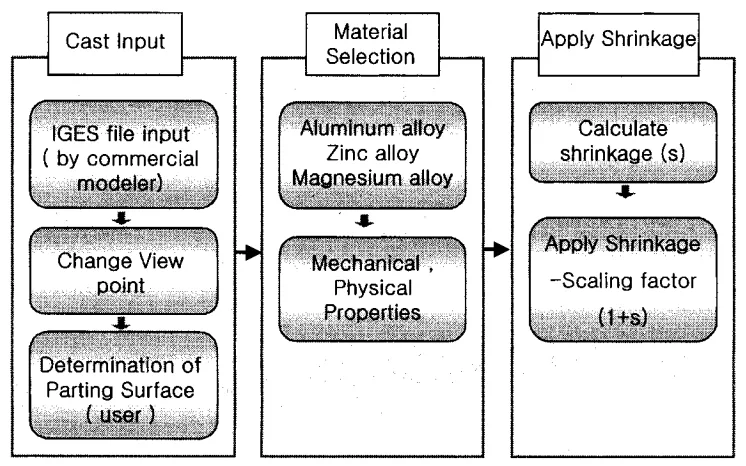
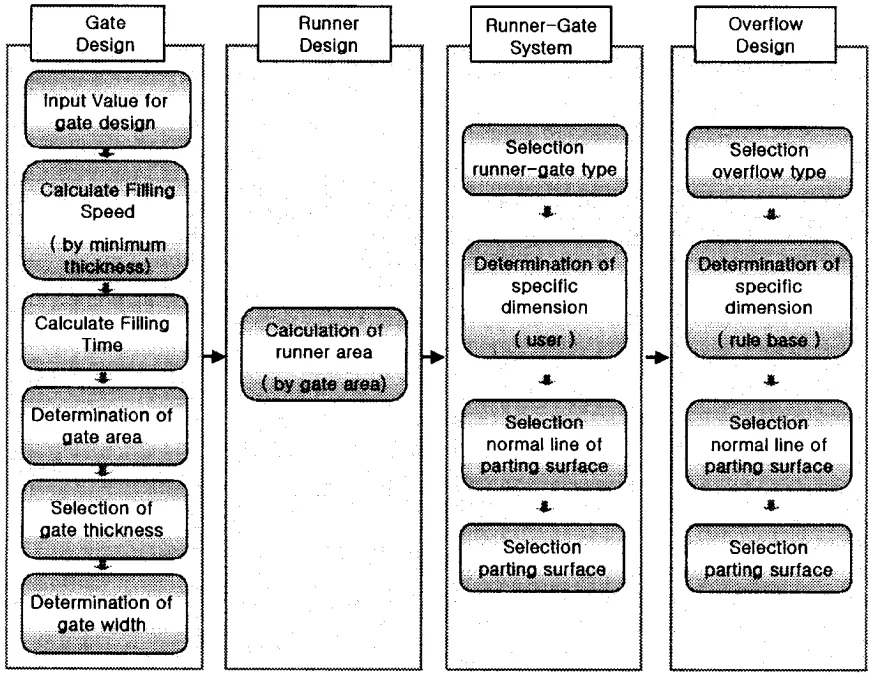
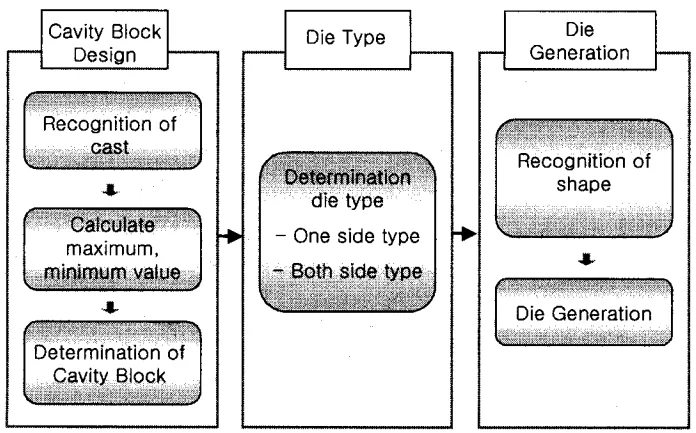
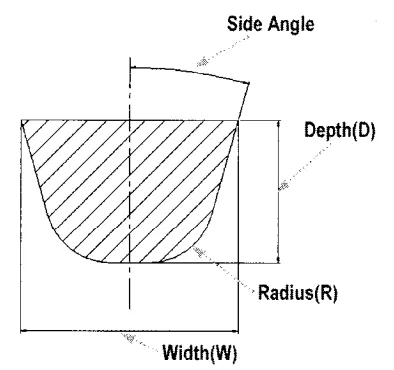
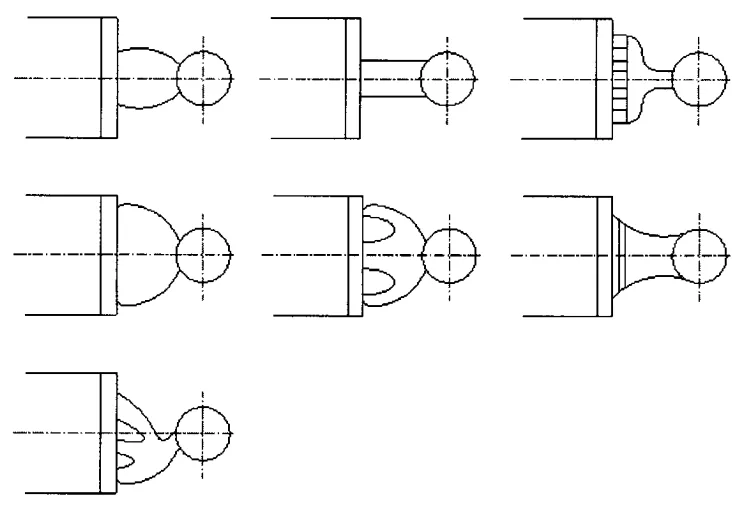
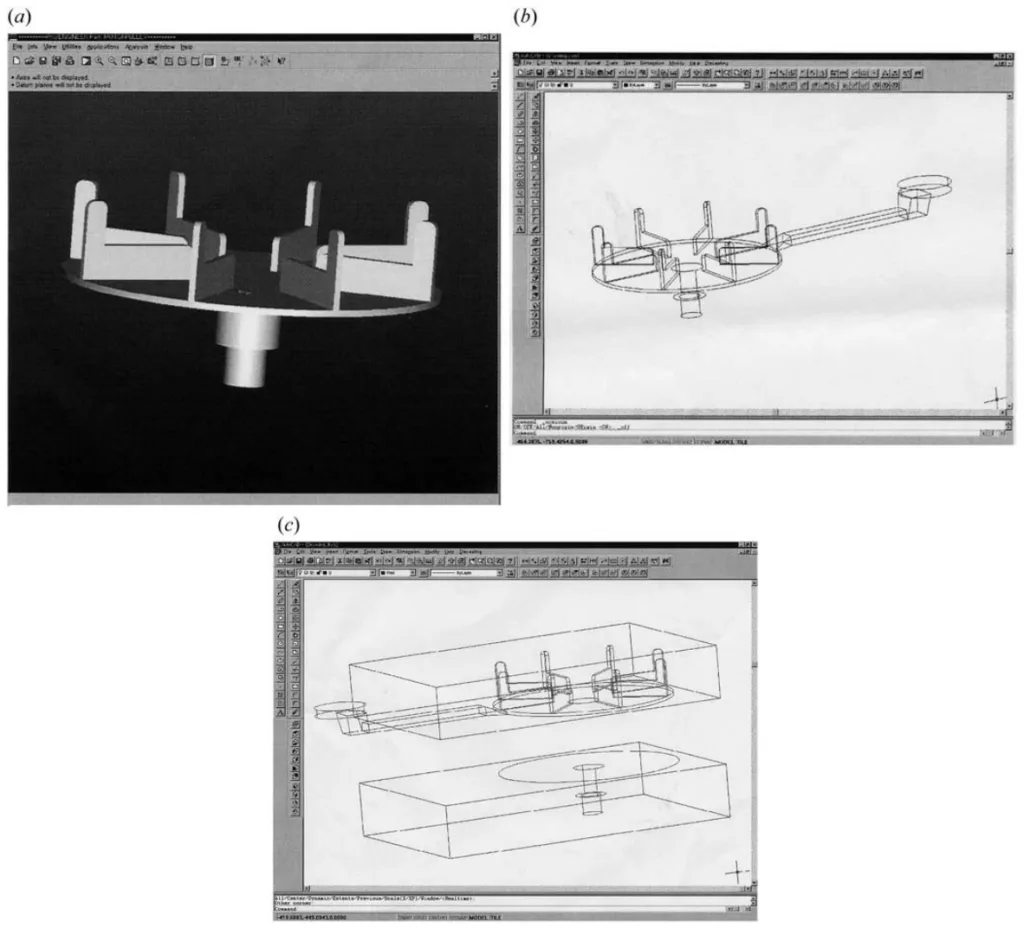
6. 결론 및 논의:
본 연구는 특히 러너-게이트 시스템 자동화에 중점을 두고 다이캐스팅 금형 설계를 위한 자동화된 CAD 시스템을 성공적으로 개발했습니다. 본 연구는 CAD 환경 내에 통합된 룰 기반 접근 방식을 사용하여 금형 설계 프로세스를 간소화하고 향상시키는 타당성을 입증합니다.
학문적 의의: 본 연구는 쉽고 효과적인 금형 설계 시스템을 만들기 위한 알고리즘을 제공합니다. 금형 설계의 실질적인 지식과 경험적 측면을 구조화되고 절차적인 프레임워크로 공식화하고 정량화합니다. 이는 금형 설계를 경험 기반 예술에서 보다 체계적이고 엔지니어링 중심적인 프로세스로 전환한다는 점에서 중요합니다.
실용적 의의: 개발된 시스템은 다이캐스팅 산업에 상당한 실용적 의미를 갖습니다. 특히 러너-게이트 시스템과 같은 금형 설계의 핵심 측면을 자동화함으로써 다이캐스팅 전문 지식이 부족한 엔지니어조차도 금형 설계 작업을 보다 효율적으로 수행할 수 있습니다. 이는 설계 주기 시간 단축, 개발 비용 절감, 최적화된 러너 및 게이트 구성을 통한 금형 성능 향상으로 이어질 수 있습니다. 시스템의 시행착오 최소화 능력은 재료 낭비 및 생산 지연을 줄입니다.
연구의 한계: 저자들은 현재 시스템에 한계가 있음을 인정합니다. 언더컷이 있는 제품의 금형 설계는 아직 다루지 않습니다. 또한, 파팅 표면 결정은 여전히 사용자 입력에 의존하며, 시스템의 적용 가능성은 주로 단일 인상 금형에 대해 입증됩니다.
7. 향후 후속 연구:
개발된 CAD 시스템의 기능과 범위를 향상시키기 위해 향후 연구 방향이 제시됩니다.
- 언더컷 처리: 언더컷이 있는 다이캐스팅 부품 처리를 위한 설계 규칙 및 알고리즘을 통합하도록 시스템을 확장합니다.
- 자동 파팅 표면 결정: 최적의 파팅 표면 결정을 자동화하는 알고리즘을 개발하여 현재 사용자 선택에 대한 의존성을 제거합니다.
- 다중 인상 금형: 다중 인상 금형 설계에 대한 시스템의 적용 가능성을 확장하여 대량 생산 시나리오에서 실용적인 유용성을 더욱 높입니다.
- 고급 시뮬레이션 통합: 예측된 금속 흐름 및 열 전달 특성을 기반으로 러너 및 게이트 설계를 더욱 최적화하기 위해 다이캐스팅 공정 시뮬레이션 도구를 통합합니다.
8. 참고 문헌:
- H. H. Doehler, Diecasting, McGraw-Hill, 1951.
- C. C. Tai and J. C. Lin, "A runner-optimization design study of a die-casting die", Journal of Materials Processing Technology, 84, pp. 1-12, 1998.
- C. C. Tai and J. C. Lin, "The optimal position for the injection gate of a die-casting die", Journal of Materials Processing Technology, 86, pp. 87-100, 1998.
- S. Sulaiman and T. C. Keen, "Flow analysis along and gating system of a casting process", Journal of Materials Processing Technology, 63, pp. 690-695, 1997.
- W. Zhang, S. Xiong and B. Liu, "Study on a CAD/CAM system of diecasting", Journal of Materials Processing Technology, 63, pp. 707-711, 1997.
- J. P. Kruth, "Steps toward an integrated CAD/CAM system for mold design and manufacture: anisotropic shrinkage, component library and link to NC machining and EDM", Annals CIRP, 35, 1986.
- Y.-M. Chen and C.-L. Wei, "Computer-aided feature-based design for net shape manufacturing", Computer Integrated Manufacturing System, 10(2), pp. 147-164, 1997.
- T. Kishinami et al., "Development of interactive mold cavity CAD/CAM system", Annals CIRP, 32(1), pp. 345-349, 1983.
- P. A. Walsham et al., "Further developments of a geometric modeling system for the computer aided manufacture of dies and molds", CIRP Annals, 32(1), pp. 339-342, 1983.
- J. Worbye, "New information points the way to longer die-casting die life", Diecasting Engineer, pp. 42-54, 1998.
9. 저작권:
본 자료는 "J. C. Choi, T. H. Kwon, J. H. Park, J. H. Kim, C. H. Kim"의 논문: "A Study on Development of a Die Design System for Diecasting"을 기반으로 합니다.
본 자료는 상기 논문을 기반으로 요약되었으며, 상업적 목적으로 무단 사용하는 것을 금지합니다.
Copyright © 2025 CASTMAN. All rights reserved.