本稿は、「Technische Universität Darmstadt」より発行された論文「Influence of Zr, Cr and Sc alloying on the microstructure and mechanical properties of a Al-Mg-Si casting alloy」に基づいています。
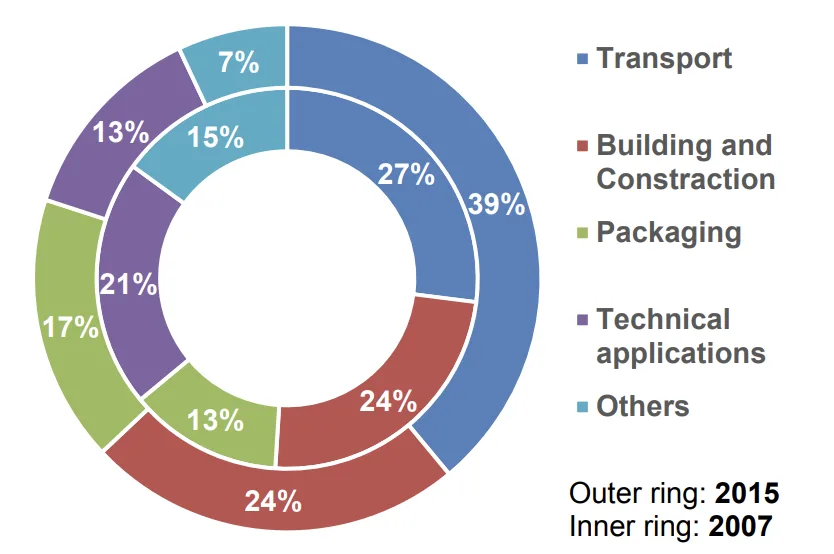
1. 概要:
- 論文名: Influence of Zr, Cr and Sc alloying on the microstructure and mechanical properties of a Al-Mg-Si casting alloy
- 著者: Prach Olena, M.Sc.
- 発行年: 2021
- 発行学術誌/学会名: Technische Universität Darmstadt
- キーワード: Al-Mg-Si鋳造合金, ジルコニウム, クロム, スカンジウム, 微細組織, 機械的特性, 高圧ダイカスト (HPDC)
2. 抄録:
本研究では、Sc、Cr、Zrを添加した新しいAl-Mg-Si-Mn鋳造合金を開発し、その微細組織と機械的特性を調査した。Al-Mg-Si-Mn合金の示差走査熱量測定(DSC)により、共晶溶融温度が595℃であることが確認され、Cr、Zr、Scの添加は合金の凝固挙動を変化させなかった。Cr、Zr、Scの微量添加は、主にα-Al相とα-Al15(Mn,Fe)3Si2相から成る微細組織を本質的に変化させなかったが、層間間隔をわずかに変化させた。Scを含まない合金ではAl3ZrおよびAl7Cr金属間化合物が観察され、Scを含む合金ではAl3ScおよびAl3Zr相が観察された。Zr、Cr、Scは主に固溶体を強化した。微小硬度およびナノ硬度測定では、合金グループ内で一貫した傾向が示された。ZrまたはZr+Crの添加は、母材合金と比較して降伏強度および引張強度を大幅に増加させなかったが、Scの添加は引張特性を著しく向上させた。SZ11合金(Sc+Zr)は、S2(Scのみ)合金と同様の結果を示した。鋳造まま状態からの人工時効(T5)処理は、母材合金において析出硬化をもたらさなかった。Scを含まない合金は225℃でのT5処理に最もよく反応し、Scを含む合金は325℃でナノ分散したAl3Sc析出物により最大の効果を得た。高温溶体化処理(T6)は繊維状共晶の球状化を引き起こし、強度を低下させたが延性を向上させた。予想外に、HPDC合金はT6処理に対して延性の面で肯定的な反応を示した。
3. 緒言:
軽量Al合金は、輸送部門における省エネルギーと燃費向上のためにますます重要になっている。Al-Mg-Si系展伸材(6xxx系)は、時効硬化による優れた強度ポテンシャルにより広く使用されている。Al-Si系鋳造合金がアルミニウム鋳物の90%以上を占める一方で、Al-Mg-Si系鋳造合金はそれほど一般的ではないが、良好な鋳造性、耐食性、および鋳放し状態での機械的特性により、自動車および航空宇宙分野での利用が増加している。
本論文の目的は、市販のMagsimal®59合金の機械的特性を、Sc、Cr、Zrの合金化によって改善することである。スカンジウム添加は、Al3Sc析出物の形成と結晶粒微細化により強度を大幅に向上させることが知られているが、その高コストが使用を制限している。ジルコニウムは加工性を向上させ、より安価であり、クロムは結晶粒構造制御と靭性向上のために使用される。
主な目的は、Sc、Zr、Crを含むAl-Mg-Si合金に関する知識を深め、ScおよびZrの単独添加がAl-Mg-Si合金の微細組織と特性に及ぼす影響を調査し、Zrおよび/またはCrによるScの完全または部分的置換によって同様の機械的特性と析出挙動を得る可能性を探ることである。
4. 研究概要:
研究テーマの背景:
アルミニウム合金は、特に輸送分野において、様々な産業で軽量化を実現し、燃料消費と排出物を削減するために不可欠である。熱処理性と良好な特性バランスで知られるAl-Mg-Si合金は、主に展伸材として使用されている。しかし、複雑な形状の製造能力と良好な機械的性能を組み合わせるために、高性能Al-Mg-Si鋳造合金、特に高圧ダイカスト(HPDC)用の合金開発への関心が高まっている。Zr、Cr、Scなどの元素による微量合金化によってこれらの合金を最適化することで、その微細組織と機械的特性を向上させることができる。
従来の研究状況:
これまでの研究では、鋳放し状態で良好な機械的特性を示すMagsimal®59、Hydronalium 511、Aural11などの市販鋳造合金を含む、Al-Mg-Si系の利点が確立されている。Sc(大幅な強化、結晶粒微細化)、Zr(加工性向上、Al3Zr析出物)、Cr(結晶粒構造制御、靭性)のアルミニウム合金への個別添加の効果は、主に展伸材や他のAl合金系に関する研究から知られている。しかし、これらの元素を組み合わせた添加、特にSc置換に焦点を当てたAl-Mg-Si 鋳造 合金、とりわけHPDC材に関する包括的な研究は限られている。これらの複雑な多成分合金における相形成を理解するためには、熱力学的モデリングと相図計算が不可欠である。
研究目的:
本研究の主な目的は、スカンジウム(Sc)、ジルコニウム(Zr)、クロム(Cr)の系統的な合金化を通じて、市販のAl-Mg-Si鋳造合金(Magsimal®59)の機械的特性を改善することである。具体的な目的は以下の通りである。
- Sc、Zr、Crの個別および複合添加がAl-Mg-Si母合金の微細組織と機械的特性に及ぼす影響を調査する。
- 機械的性能を維持または向上させつつ、高価なスカンジウムをより経済的なジルコニウムおよび/またはクロムで部分的または完全に置換する可能性を探る。
- 鋳放し状態と熱処理状態の両方で、これらの新開発合金における析出挙動と強化機構を理解する。
核心研究:
本研究の核心は、Magsimal®59組成をベースに、Zr、Cr、Scを個別および組み合わせて系統的に添加した新しいAl-Mg-Si-Mn鋳造合金の開発と調査であった。これらの合金は高圧ダイカスト(HPDC)によって製造された。研究は以下に焦点を当てた。
- 微細組織評価: 示差走査熱量測定(DSC)、光学顕微鏡、エネルギー分散型X線分光法(EDS)を備えた走査型電子顕微鏡(SEM)、および透過型電子顕微鏡(TEM)を用いた、鋳放し状態および熱処理状態の微細組織の包括的な分析。これには、構成相、金属間化合物(例:Al15(Mn,Fe)3Si2、Al3Zr、Al7Cr、Al3Sc)、共晶組織(Mg2Si)形態、デンドライトアーム間隔(DAS)、およびラメラ間隔(ILS)の同定が含まれた。
- 機械的特性評価: 鋳放し状態および様々な熱処理状態(T5およびT6処理)における、微小硬さ、マクロ硬さ(ブリネル)、ナノ硬さ(α-Alマトリックスおよび共晶領域、金属間化合物の)、および引張特性(降伏強度、引張強さ、伸び)の評価。
- 熱処理応答: 種々の人工時効(鋳放し状態から125-325℃でのT5)および溶体化処理後人工時効(T6処理、脱ガス現象の研究を含む)熱処理に対する合金の応答の調査。
- 熱力学計算: Thermo-Calcソフトウェアを用いた相図の計算と、開発された多成分合金における相形成の予測。
5. 研究方法論
研究設計:
本研究は、合金元素Zr、Cr、ScがAl-Mg-Si-Mn母合金(市販のMagsimal®59)に及ぼす影響を系統的に調査するように設計された。これらの元素の濃度を個別に、または組み合わせて変化させた一連の実験合金が開発された(詳細はTable 3.6参照)。すべての合金は、工業的応用に適した条件を確保するために高圧ダイカスト(HPDC)を用いて製造された。本研究では、開発された合金を、鋳放し状態および様々な熱処理条件(T5およびT6)において母合金と比較した。
データ収集・分析方法:
- 鋳造: 合金はFrech DAK 450-54コールドチャンバーHPDC機を用いて作製された。添加にはマスターアロイ(AlCr20、AlZr15、AlSc2)が使用された。
- 化学分析: 組成制御のためのスパーク発光分光分析(Ametek Spectromaxx)。
- 示差走査熱量測定(DSC): NETZSCH社製装置を用いて相変態温度(例:溶融、凝固)を決定した。
- 微細組織評価:
- 光学顕微鏡および走査型電子顕微鏡(SEM - TESCAN Mira3)とエネルギー分散型X線分光法(EDS)を用いて、ImageJソフトウェアにより相の同定、形態、分布、デンドライトアーム間隔(DAS)、ラメラ間隔(ILS)を評価した。
- 電子プローブマイクロアナライザ(EPMA - JEOL JXA-8100)を用いて詳細な元素マッピングを行った。
- 透過型電子顕微鏡(TEM - Philips CM20)を用いて微細な析出物や分散粒子を観察した。
- 機械的試験:
- 硬さ: ブリネル硬さ、ビッカース微小硬さ(Zwick Roell)、およびナノインデンテーション(iNano、G200、バーコビッチ圧子使用)をLCおよびCSMモードで測定した。
- 引張試験: ASTM E8_E8M_13aに準拠し、Instron 5967試験機で室温単軸引張試験を実施した。
- 熱処理: T5(鋳放し状態からの人工時効、125℃、175℃、220℃、325℃)およびT6(溶体化処理480-570℃、水焼入れ後、175℃、225℃、325℃で人工時効)。溶体化処理中の脱ガス効果も調査した。
- 熱力学計算: Thermo-Calcソフトウェア(TCAl2: Al-alloys v2.1データベース)を用いて相図を計算し、相形成を予測した。
研究テーマ・範囲:
本研究は、Al-Mg-Si-Mn鋳造合金、具体的にはMagsimal®59母材組成に、ジルコニウム(0.1-0.2 wt.%)、クロム(0.1-0.3 wt.%)、スカンジウム(0.1-0.2 wt.%)およびそれらの組み合わせ(例:Cr+Zr、Sc+Zr)を添加したものを対象とした。範囲は以下を含む。
- DSCを用いた相変態および凝固挙動の調査。
- 鋳放し状態における詳細な微細組織分析(存在する相、その形態、サイズ、分布、元素偏析)。同定された相には、α-Al、Mg2Si共晶、α-Al15(Mn,Fe)3Si2、Al3Zr、Al7Cr、Al3Scが含まれる。
- DAS、ILS、相の体積分率などの微細組織特徴の定量化。
- 鋳放し状態における機械的特性(様々な硬さスケール、引張強さ、降伏強度、伸び)の評価。
- 熱処理への応答の研究:
- T5時効:時効硬化曲線と硬さおよび引張特性への影響。
- T6処理:溶体化処理温度が脱ガス、微細組織、およびその後の時効応答が硬さおよび引張特性に及ぼす影響。
- 微細組織と機械的特性の相関。
- Zrおよび/またはCrによるSc置換の可能性の評価。
6. 主な結果:
主な結果:
鋳造まま状態:
- DSC: Al-Mg-Si-Mn合金の共晶溶融温度は約595℃と決定された。Cr、Zr、Scの添加(単独または複合)は、合金の凝固挙動を著しく変化させなかった。
- 微細組織: 主な相はα-Al(等軸晶、球状ロゼット形態、DAS 約10-12 µm)およびα-Al15(Mn,Fe)3Si2であった。Cr、Zr、Scの添加は、Mg2Si共晶のラメラ間隔(ILS)をわずかに変化させた。
- Scフリー合金: Al3Zr(Z2合金で直方体状、約13 µm)およびAl7Cr金属間化合物がZr/Cr含有量に応じて観察された。
- Sc含有合金: Al3Sc(不規則形状、α-Al15(Mn,Fe)3Si2近傍)が特にS2合金(0.2 wt.% Sc)で観察された。Zr添加により、Al3Zr相も存在した(例:SZ11、SZ21、SZ21ではより大きなAl3Zr)。
- Zr、Cr、Scは主に固溶強化に寄与した。MnおよびCrは一部が初晶粒子として、一部が固溶体として存在した。
- 硬さ: 同じ主要合金元素を持つ合金内(例:Z1-Z2、S1-S2)では、平均微小硬さおよびナノ硬さは同様であった。Sc含有合金は一般的に高い硬さを示した。ZrまたはZr+Crの添加は、M59母材と比較してマクロ/ミクロ硬さを大幅に増加させなかった。ScおよびSc+Zr添加は最も高いマクロ硬さをもたらした(例:SZ21およびSCZはM59より約15%硬い)。α-Alおよび共晶領域のナノ硬さは合金化により増加し、ScおよびSc+Zr添加が最も高い共晶硬さを示した。
- 引張特性: ZrまたはZr+Crの添加は、降伏強度を大幅に増加させなかった。Scによる合金化は、引張特性(YS、UTS、伸び)を著しく向上させた。0.1 wt.%のScは固溶強化に十分であり、さらなるSc添加は強度向上にはつながらなかった。SZ11合金(Sc+Zr)は、S2合金(Scのみ)と同等の引張特性を示した。
熱処理状態:
- T5時効(鋳造ままから):
- 母材合金(M59)は顕著な析出硬化を示さなかった。
- Scフリー合金は225℃で良好な応答を示した。
- Sc含有合金は325℃で最大の効果を示し、ナノサイズのAl3Sc析出物が観察された(例:225℃/325℃で時効処理したS1、S2合金)。
- S2合金(0.2 wt.% Sc)は325℃で最高のYSおよびUTSを達成した。
- T6処理(溶体化処理+時効):
- 高温溶体化処理(ST > 520℃)は、繊維状Mg2Si共晶の球状化を引き起こし、引張/降伏強度を大幅に低下させたが、延性は向上した。
- 母材合金では、ST温度 ≥ 520℃で脱ガス(ブリスター)が観察された。
- ST後の硬さは鋳造ままより低かったが、時効後に上昇した。
- 母材合金の場合、T6処理(ST 570℃ + AA 175℃)はT5処理と同等の硬さをもたらし、YSは164 MPa(鋳造まま)から200 MPaに上昇した。S2合金の場合、YSは194 MPa(鋳造まま)から220 MPaに上昇した。高温STでのブリスターのため、T6処理後の伸びは一般的に鋳造ままより低かった。
- 低温ST(例:480℃)ではMg2Siが効果的に溶解せず、時効応答は劣っていた。
- Al3Zr、Al3Sc、Al7Crの初晶金属間化合物は、520℃のSTでは大きな影響を受けなかった。
- 比較: HPDC合金は、ブリスターを制御できれば、T6処理に対して延性の点で予想外の良好な応答を示した。T5処理、特にSc含有合金の325℃での処理は、大幅な強度向上をもたらした。Al3ScとMg2Siの析出硬化の組み合わせは、熱処理を最適化する上で複雑なシナリオを提示する。
![Figure 2.5 Graphical illustration of a) hot-chamber, b) cold-chamber die casting
machine[32]](https://castman.co.kr/wp-content/uploads/image-2222-1024x447.webp)
![Figure 2.6 a) Structural zone formation in castings [36], b) dendritic arms [36], c) SEM image of dendrites in Al-Mg-Si alloys (present work), d) SEM image of aluminum dendrites in the fractured surface of a tensile test bar of the Al-MgSi alloy (present work).](https://castman.co.kr/wp-content/uploads/image-2223-1024x880.webp)
![Figure 6.17 Microstructure of the AlMg5Si2Mn HPDC alloy and 3D modelling of theMg2Si eutectic in the a)as-cast and b,c) heat-treated state. From [171]](https://castman.co.kr/wp-content/uploads/image-2224-1024x540.webp)
図の名称リスト:
- Figure 2.1 2007年と2015年のAl合金の適用分野の比較、[22]より引用・改変。
- Figure 2.2 世界のアルミニウム生産量、[18]より引用。
- Figure 2.3 アルミニウム合金の半製品、[22]より引用・改変。
- Figure 2.4 鋳造技術の分類。[31]より引用。
- Figure 2.5 a) ホットチャンバー式、b) コールドチャンバー式ダイカストマシンの図解、[32]より引用。
- Figure 2.6 a) 鋳物における凝固組織帯の形成[36]、b) デンドライトアーム[36]、c) Al-Mg-Si合金のデンドライトのSEM像(本研究)、d) Al-Mg-Si合金の引張試験片破断面におけるアルミニウムデンドライトのSEM像(本研究)。
- Figure 2.7 Al-Mg-Si-Sc-Zr合金のSEM像とMg、Si、Sc、ZrのEDXマップ、および測定線に沿った組成変化[45]。
- Figure 2.8 a) 鋳放しAl-Mg2Si合金におけるMg2Si共晶の形態、b) 575℃で溶体化処理後[49]。
- Figure 2.9 Alにおける強化機構の模式図。[50]より引用。
- Figure 2.10 固溶体の種類 a) 置換型固溶体、b) 格子間型固溶体。[55]より引用・改変。
- Figure 2.11 母相と第二相の間の結晶学的関係。a) 歪んでいるが連続的な格子面を持つ整合性、b) 半整合性、c) 不整合な平衡析出物。[54,66]より引用・改変。
- Figure 2.12 転位と析出物の相互作用機構の模式図:粒子ループと粒子切断。[71]より引用・改変。
- Figure 2.13 粒子の大きさと強度の関係、[50,51]より引用。
- Figure 3.1 a) 擬二元系線(赤線)と実験的に確立されたL → (Al) + Mg2Si(黒曲線)の不変線を持つ三元Al-Mg-Si状態図、b) 過剰Mgの影響を示す二元Al-Mg2Si状態図[94]、c) Al-Mg-Si液相面[88]。
- Figure 3.2 二元状態図 a) Al-Mg2Si、調査合金は矢印で示す、[87]より引用・改変、b) 計算されたAl-5Mg-2Si-(0…2.0)Mn状態図。
- Figure 3.3 a) Al-Sc状態図[120]、b) Thermo-Calcにより計算されたAl-Sc状態図のAlリッチ側。
- Figure 3.4 Al3Sc析出物のL12型構造の模式図。
- Figure 3.5 a) Al-2Scマスターアロイ中のAl3Sc粒子のSEM像[123]、b) Al-0.7Sc合金中のAl3Sc粒子のTEM明視野像[116]、c) Al3Sc析出物のTEM明視野像[111]。
- Figure 3.6 a) Al-Zr状態図のAlリッチ側、b) 様々な結晶構造[130]。
- Figure 3.7 焼鈍後のAl-Mg-Si-Zr展伸材のTEM像 a) 明視野像、b) 暗視野像[111]。
- Figure 3.8 Al3(Sc,Zr)ナノ粒子のTEM明視野像、a) [114]、b) [135]、c) [128]。
- Figure 3.9 調査合金AlMg5Si2Mnにa)Zr、b)CrおよびZrを添加した計算状態図。
- Figure 3.10 調査合金AlMg5Si2Mnにa)Sc、b)ScおよびZr、c)Sc、CrおよびZrを添加した状態図。
- Figure 3.11 a) 溶体化処理および析出硬化の代表的な温度域[13]、b) 調査合金の析出シーケンス、[50]より引用・改変。
- Figure 4.1 a) HPDC機から取り出した直後のゲートシステムおよびオーバーフロー付き鋳造プレート、b) 鋳造システム除去後。
- Figure 4.2 a) 圧痕とその対角線測定の模式図、b) 研磨面上の微小硬さ圧痕の像。
- Figure 4.3 荷重-変位曲線の模式図。
- Figure 4.4 引張試験片の模式図。
- Figure 5.1 鋳放し状態の母材合金のDSC曲線。
- Figure 5.2 a) Scフリー合金のDSC加熱・冷却曲線、b) 590-600℃範囲におけるこれらの合金の拡大DSCトレース。
- Figure 5.3 Sc含有合金のDSC加熱・冷却曲線。
- Figure 5.4 対応する微細組織を持つプレートの断面。
- Figure 5.5 母材合金のSEM像:a) 微細組織の概観、b) Mn含有金属間化合物。
- Figure 5.6 母材合金のSEM像とデンドライト領域のEMPAマップ。
- Figure 5.7 Scフリー合金のSEM像。
- Figure 5.8 a)Z1合金およびb)Z2合金におけるZrの分布のEMPAマップ。
- Figure 5.9 a)CZ11合金およびb)CZ12合金におけるZrおよびCrの分布のEMPAマップ。
- Figure 5.10 Sc含有合金のSEM像。
- Figure 5.11 鋳放し状態のa)S1、b)S2合金のデンドライト領域のSEM像とEMPAマップ。
- Figure 5.12 鋳放し状態のa)SZ11、b)SZ21合金のデンドライト領域のSEM像とEMPAマップ。
- Figure 5.13 母材合金中のMn含有相のSEM像。a) 研磨試料、b) 破断面、c) Sc含有合金中のMn含有相。
- Figure 5.14 粗大なCr、Zr含有相を持つ合金のSEM像[159]。
- Figure 5.15 CZ33合金におけるAl7CrおよびAl3Zr金属間化合物のSEM像とEDS元素マッピング[159]。
- Figure 5.16 母材合金のTEM明視野像 a-c) βおよびβ'析出物を含む。
- Figure 5.17 母材合金中のMn含有分散粒子 a-b) および b)S1、c)S2合金で観察されたAl3Sc析出物のTEM明視野像。
- Figure 5.18 a) プレート断面、b) プレート端部近傍および中央部におけるα-Alと共晶の体積分率、M59、Z2、S2合金の中央領域のILS。
- Figure 5.19 鋳放し状態におけるScフリー合金およびSc含有合金の a) マクロ硬さおよび b) ミクロ硬さ。
- Figure 5.20 a) α-Alマトリックスおよびb) 共晶に圧痕を入れた調査合金の微細組織、c) α-Alマトリックスおよび共晶のナノ硬さ測定。
- Figure 5.21 α-Al15(Mn,Fe)3Si2金属間化合物相の像と対応する荷重-変位および硬さ-変位曲線。
- Figure 5.22 a) Al7Crおよびb) Al3Zr金属間化合物相の像と対応する硬さ-変位曲線。
- Figure 5.23 α-Al15(Mn,Fe)3Si2、Al3ZrおよびAl7Cr初晶相の荷重-変位および硬さ-変位曲線。
- Figure 5.24 調査合金の引張特性 a) 降伏強度、b) 引張強さ、c) 鋳放し状態での破断伸び。
- Figure 5.25 HPDCで処理された鋳放し合金の破断面の代表的なSEM形態。a) 母材合金の引張試験片のマクロ破断面、b) 母材合金の破断面の気孔、c) Scフリー合金Al3ZrおよびAl7Cr金属間化合物の拡大破断面 d) CZ22およびe) SZ12合金。
- Figure 5.26 層間間隔の変化が a) 降伏強度および b) 伸びに及ぼす影響。
- Figure 6.1 a)125℃、b)175℃、c)225℃、d)325℃における時間関数としての微小硬さ。
- Figure 6.2 a)母材合金(黒線)およびZ2(青線)、b)S2(緑線)の3時間時効温度関数としての引張特性。
- Figure 6.3 325℃でのAA後の時効時間の関数としての引張特性。
- Figure 6.4 3時間のAA後の化学組成の関数としての引張特性 a)225℃、b)325℃。
- Figure 6.5 225℃および325℃で3時間人工時効後の引張特性 a-b)降伏応力、c-d)引張強さ、e-f)破断伸び。
- Figure 6.6 M59合金の人工時効後 a-b)175℃、c-d)325℃でのTEM明視野像。
- Figure 6.7 人工時効後のSc含有合金のTEM明視野像:a)S1 225℃後、b)S1 325℃、c)S2 225℃、d)S2 325℃。
- Figure 6.8 a)熱処理および鋳放し状態後のプレート全体の硬さ。175℃(24時間)でのAA、b)母材合金の表面引張試料と異なる溶体化処理スケジュール後。
- Figure 6.9 1時間の異なる温度での溶体化処理後の組織[172]。
- Figure 6.10 570℃および480℃での溶体化処理後175℃で時効処理した母材合金の硬さ-時間曲線。黒線は鋳放し状態から直接AA処理した結果を示す。
- Figure 6.11 M59合金の微細組織 a)鋳放し状態、および b)480℃、c)520℃、d)570℃での溶体化処理後。
- Figure 6.12 a)Z2、b)S2、c)CZ33合金の520℃で3時間ST処理後のSEM像[172]。
- Figure 6.13 高温T6処理(ST570℃+AA175℃)後の母材およびS2合金の応力-ひずみ曲線。
- Figure 6.14 ST520+AA225およびST520+AA325(赤記号で示す)後の化学組成の関数としての引張特性。
- Figure 6.15 M59合金の溶体化処理後(時効なし)のTEM明視野像(<001>Al軸に沿って撮影) a-b)520℃、c-d)570℃*。
- Figure 6.16 Z2合金(0.2 wt.% Zr)をHPDCで処理し、520℃で1.5時間ST処理した後のAl3Zr分散粒子を示すTEM明視野像(<001>Al軸に沿って撮影)。
- Figure 6.17 AlMg5Si2Mn HPDC合金の微細組織と a)鋳放し状態およびb,c)熱処理状態におけるMg2Si共晶の3Dモデリング。[171]より。
- Figure 6.18 T6処理後および鋳放し状態(破線)における母材合金およびS2合金の比較応力ひずみ曲線。
- Figure 6.19 M59、Z2、S2合金の異なる熱処理レジーム後の引張特性。
- Appendix A.1 コールドチャンバーダイカストの鋳造サイクル[32](付録図)
- Appendix A.5 a)175℃およびb)325℃での人工時効後の母材合金のSEM像[SC31]。(付録図)
- Appendix A.6 a)単一添加合金およびb-c)複合添加合金の鋳放し状態での比較応力ひずみ曲線。(付録図)
7. 結論:
本研究は、Sc、Cr、Zrを添加した新しいAl-Mg-Si-Mn鋳造合金を成功裏に開発し、その微細組織と機械的特性を明らかにした。
鋳造まま状態:
- 共晶溶融温度は、微量合金元素の添加に影響されず、一貫して約595℃であった。
- 微細組織は、α-Al、Mg2Si共晶、およびα-Al15(Mn,Fe)3Si2相から構成されていた。Scフリー合金はAl3ZrおよびAl7Crを形成し、Sc含有合金はAl3ScおよびAl3Zrを形成した。これらの添加は層間間隔をわずかに変化させた。
- Zr、Cr、Scの添加は主に固溶強化に寄与した。
- 硬さ(ミクロ、ナノ)は合金グループ内で一貫しており、Sc含有合金は一般的に硬かった。
- ZrまたはZr+Crの添加は、母材合金と比較して降伏強度/引張強度を大幅に向上させなかった。しかし、Scの添加は引張特性を著しく向上させた。SZ11(Sc+Zr)合金は、S2(Scのみ)合金と同等の性能を示し、Sc置換の可能性を示唆した。
熱処理状態:
- 鋳造ままからの母材合金の人工時効(T5)は、析出硬化をもたらさなかった。
- Scフリー合金は225℃でのT5によく反応し、Sc含有合金は325℃でのT5から最大の効果を得て、ナノ分散Al3Sc析出物を形成した。
- T6の初期段階(高温溶体化処理)は、繊維状共晶の球状化を引き起こし、強度を低下させたが延性を向上させた。母材合金の完全なT6処理は、機械的特性に大きな改善をもたらさなかった。
- HPDC合金は、予想外に、T6処理に対して延性の点で肯定的な反応を示した。
全体として、Sc、またはScとZrの組み合わせによる合金化は、Al-Mg-Si HPDC合金の機械的特性を大幅に向上させる。特定の熱処理(T5対T6)は、望ましい強度と延性のバランスに基づいて選択する必要があり、高温(例:Sc合金の場合は325℃)でのT5は強度に、T6は潜在的に延性に有望である。
8. 参考文献:
9. 著作権:
- 本資料は「Prach Olena, M.Sc.」の論文です。「Influence of Zr, Cr and Sc alloying on the microstructure and mechanical properties of a Al-Mg-Si casting alloy」に基づいています。
- 論文出典: urn:nbn:de:tuda-tuprints-172138
本資料は上記論文に基づいて要約されており、商業目的での無断使用を禁じます。
Copyright © 2025 CASTMAN. All rights reserved.