バリューストリームマッピング(VSM)でダイカストの生産性を6%向上:学術論文から学ぶ、製造現場のムダ削減術
本技術概要は、Pradip Gunaki氏およびS.N. Teli氏によって執筆され、Journal of Emerging Technologies and Innovative Research (JETIR)に2015年に掲載された学術論文「Productivity Improvement by Value Stream Mapping in Die Casting Industry」に基づいています。ダイカスト専門家の皆様のために、株式会社CASTMANのエキスパートが要約・分析いたしました。
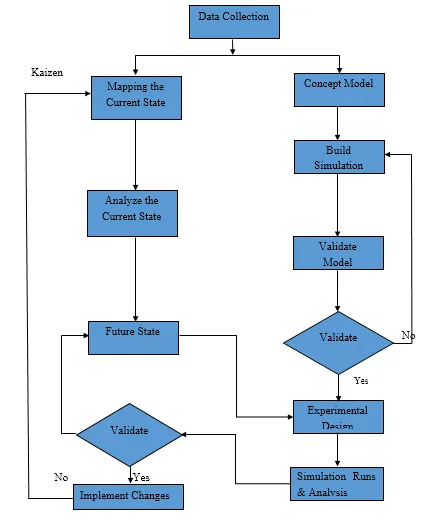
キーワード
- 主要キーワード: バリューストリームマッピング ダイカスト
- 副次キーワード: 生産性向上, 無駄の削減, サイクルタイム短縮, リーン生産方式, Arenaシミュレーション, カイゼン, 現状把握マップ
エグゼクティブサマリー
- 課題: ダイカスト製造において、非付加価値活動に起因するサイクルタイムの増大が、顧客要求への迅速な対応を困難にしていました。
- 手法: バリューストリームマッピング(VSM)を用いて現状の製造プロセスを可視化・分析し、Arenaシミュレーションソフトウェアで改善策の効果を定量的に検証しました。
- 重要なブレークスルー: VSMとカイゼン手法の導入により、生産時間全体に占める非付加価値活動の割合を39.96%から24.57%へと大幅に削減することに成功しました。
- 結論: 結果として、総サイクルタイムを6.146%短縮し、ダイカスト工場の生産性を著しく向上させることが実証されました。
課題:なぜこの研究がダイカスト専門家にとって重要なのか
グローバル市場での競争が激化する中、製造業はより高い柔軟性、競争力、高品質な製品を低コストで提供することが求められています。。特に、顧客の要求が多様化し、カスタマイズ品の受注が増加するダイカスト業界において、生産システムの効率化は喫緊の課題です。本研究で対象となった企業(論文内では「XYZ社」)では、価値を生まない「非付加価値活動」が原因でサイクルタイムが増加し、顧客の要求納期を満たすことが困難になるという問題に直面していました。これは、多くのダイカスト工場が共感するであろう、生産性と顧客満足度の間で板挟みになる典型的な状況と言えます。この研究は、こうした現場の切実な課題に対し、リーン生産方式の強力なツールを用いて解決策を提示するものです。
アプローチ:研究手法の解明
本研究では、生産性向上のための核心的なツールとしてバリューストリームマッピング(VSM)が採用されました。VSMは、トヨタ生産方式を源流とする可視化ツールであり、材料が顧客の手に渡るまでの全プロセス(付加価値活動と非付加価値活動の両方)をマップ化し、無駄を特定・削減することを目的とします。。
研究チームは、以下のステップでアプローチしました。(Figure 1参照)
- 現状分析: 現場視察、関係者への構造化面接(Figure 4参照)、データ収集を通じて、鋳造現場の現状のプロセスマップ(Current State Map)を作成しました。
- 問題点の特定: 作成したマップを基に、待機時間や不要な運搬といった非付加価値活動(ムダ)を洗い出しました。
- 改善策の立案と検証: カイゼンの哲学に基づき、作業環境の改善(5Sなど)やスキル訓練といった具体的な改善策を立案しました。さらに、Arenaシミュレーションソフトウェアを用いて、現状(Figure 7)と改善後の未来(Figure 12)のモデルを構築。これにより、実際のラインを変更する前に、改善策がサイクルタイムや生産性に与える影響を定量的に評価・検証しました。
このシミュレーションとの統合アプローチ(Figure 2参照)により、勘や経験だけに頼らない、データに基づいた確実な改善プロセスを実現しています。
ブレークスルー:主要な発見とデータ
本研究から得られた最も重要な結果は、VSMとシミュレーションを用いた体系的なアプローチが、生産性向上に直接的な効果をもたらすことをデータで証明した点です。
- 発見1:隠れた非付加価値活動の可視化: シミュレーション結果の分析から、現状の生産プロセスでは、全体の39.96%もの時間が待機や不要な運搬といった非付加価値活動に費やされていることが明らかになりました。
- 発見2:カイゼンによる大幅なムダ削減: カイゼン哲学に基づいた改善活動を実施した結果、非付加価値活動の割合を24.57%まで削減することに成功しました。これは約15%の改善に相当します。
- 発見3:サイクルタイムの確実な短縮: 非付加価値活動の削減により、製品1個あたりの総サイクルタイムは65.08分から61.08分へと、6.146%短縮されました。
- 発見4:生産性の向上: サイクルタイムの短縮と作業環境の改善は、労働生産性の向上に直結し、月間の生産可能個数が顧客需要(430個)を満たせるレベルへと改善される道筋を示しました。これらの改善効果は、現状と未来の比較グラフ(Figure 16)で明確に示されています。
貴社のHPDCオペレーションへの実践的な示唆
本研究の結果は、理論に留まらず、実際のダイカスト工場のオペレーション改善に直結する貴重な知見を提供します。
- プロセスエンジニアの方へ: 本研究の「CORRECTIVE ACTION FOR IMPROVEMENT」セクションで示されているように、VSMを用いて自社のプロセスを分析することで、これまで見過ごされていた待機時間や手待ちといった具体的な無駄(ムダ)を特定できます。本研究では、これによりサイクルタイムを6%以上削減できる可能性が示唆されています。
- 品質管理担当の方へ: 本研究ではカイゼンの一環として5S(整理・整頓・清掃・清潔・躾)の導入が挙げられています。これは作業エリアの秩序を保ち、安全性と人間工学を向上させるものであり、結果としてヒューマンエラーの削減や製品品質の安定化に間接的に貢献します。
- 生産管理者の方へ: 本研究で提示されたVSMとシミュレーションを組み合わせた手法(Figure 2参照)は、生産ライン全体のボトルネックを特定し、改善投資の効果を事前に予測するための強力なフレームワークとなります。これにより、「勘」に頼らないデータドリブンな意思決定が可能になり、工場全体の生産性向上を計画的に推進できます。
論文詳細
Productivity Improvement by Value Stream Mapping in Die Casting Industry
1. 概要:
- 論文名: Productivity Improvement by Value Stream Mapping in Die Casting Industry
- 著者: Pradip Gunaki, S.N. Teli
- 発表年: 2015
- 掲載誌/学会: Journal of Emerging Technologies and Innovative Research (JETIR)
- キーワード: Value Stream, Current Stream Mapping, Future State Mapping, Takt time, Cycle Time, Lean Manufacturing, Simulation.
2. 論文要旨:
バリューストリームマッピング(VSM)は、付加価値を生まないステップを特定し、除去または合理化することによって、製造、生産、ビジネスプロセスにおける無駄を明らかにする評価を得ています。プロセスの現状を反映するためにフロー図が描かれます。非付加価値活動は、各ステップ内およびステップ間で、時間とリソースの無駄によって特定されます。このプロセスは、シミュレーションソフトウェアの助けを借りて分析され、それを必要最小限の活動にまで劇的に削減・単純化する機会を探ります。無駄を減らすことで、プロセス全体における付加価値時間の割合が増加し、プロセスのスループット速度が向上します。これにより、再設計されたプロセスはより効果的(正しいことが行われる)かつ効率的(より少ないリソースで済む)になります。本稿では、Arenaシミュレーションソフトウェアを用いて、ダイカスト業界における非付加価値活動を排除するための是正手法について説明します。再設計されたプロセスは、プロセスのステップと情報の流れが再設計、単純化され、コストが削減され、生産性が向上した未来の状態でフローチャート化されます。
3. 序論:
バリューストリームマップは、顧客にとっての価値を創造するプロセス/活動のエンドツーエンドの集合体です。バリューストリームとは、製品を主要なフロー、すなわち(a)原材料から顧客の手に渡るまでの生産フロー、および(b)コンセプトから市場投入までの設計フロー、を通じて送り出すために現在必要とされるすべての活動(付加価値および非付加価値の両方)を指します。。グローバル市場における競争の激化は、メーカーに柔軟性、競争力、高品質な製品を提供し、生産コストの削減を確実にする生産システムとプロセスの開発を強いています。。VSMは、無駄を特定し排除することに焦点を当てた経営哲学を適用することにより、コスト削減に重点を置いています。。
4. 研究の概要:
研究トピックの背景:
顧客の要求を常に満たすことを目指す企業であること、そして市場の性質が製品実現プロセスに影響を与える可能性があります。これらの企業は、製品設計だけでなく、製品実現プロセスの生産性向上を必要としています。
従来の研究の状況:
多くの研究者がVSMの有効性を指摘しています。McManus氏とMillard氏は航空宇宙分野での製品開発(PD)への応用を探り、Al-Odeh氏らはVSMが価値向上、無駄の排除、フロー改善の機会を特定できることを示唆しました。Sheth1氏らは、VSMが非付加価値活動の観点から無駄を特定することを目的としていると述べています。
研究の目的:
本研究の主な目的は、ダイカスト業界において、VSMという可視化ツールとシミュレーションソフトウェアを用いて非付加価値活動を特定し、リーン技術によって是正措置を講じることで、生産性を低下させている要因を排除することです。
研究の核心:
研究の核心は、XYZアルミニウムダイカスト社の鋳造現場を対象としたケーススタディです。VSMを用いて現状(Current State)をマッピングし、ボトルネックと無駄を特定。その後、カイゼンに基づいた改善策を盛り込んだ未来(Future State)を設計し、その効果をArenaシミュレーションで定量的に比較・検証しました。
5. 研究手法
研究デザイン:
本研究は、Figure 1に示されるVSMの方法論に基づいています。クリティカルな工程として鋳造現場を選定し、情報フローと物資フローを収集、無駄を特定し、現状マップ(Current State Map)を作成。その後、問題点を分析し、改善戦略を立て、未来マップ(Future State Map)を描くという流れで進められました。
データ収集と分析手法:
データ収集は、現場視察(Site Visits, Figure 3参照)と、管理者、監督者、オペレーターへの構造化面接(Structured Interviews, Figure 4参照)によって行われました。収集されたサイクルタイムやプロセスロジックのデータは、Arenaシミュレーションソフトウェアに入力され、現状プロセスのモデル化(Figure 7)と、改善後のシミュレーション(Figure 12)による定量的分析に用いられました。
研究の対象と範囲:
研究対象は、自動車および非自動車向けの高品質アルミニウムダイカスト部品を製造するXYZ社です。特に、サイクルタイム、不適切な設備取り扱い、材料の無駄といった問題が指摘された鋳造現場(foundry shop floor)に焦点を当てています。
6. 主要な結果:
主要な結果:
シミュレーション分析から、以下の改善が観察されました。
- 生産の総サイクルタイムが6.146%削減されました。
- 非付加価値活動が39.96%から24.57%に削減されました(NVAの15%削減)。
- カイゼン哲学による労働生産性と作業環境の改善が確認されました。
- これらにより、サイクルタイムと非付加価値活動の削減を通じて生産性が向上しました。
図の名称リスト:
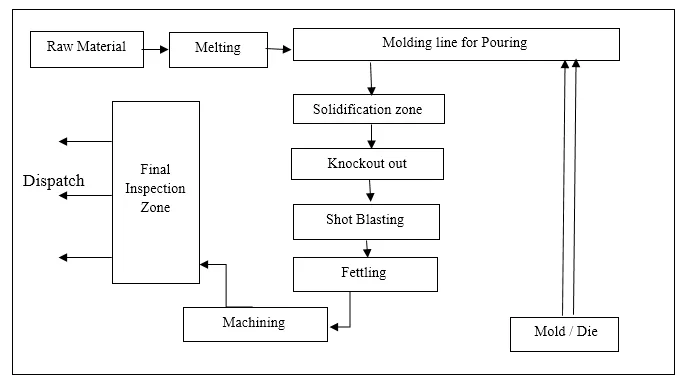
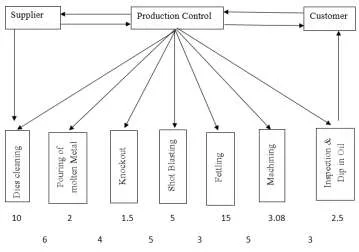
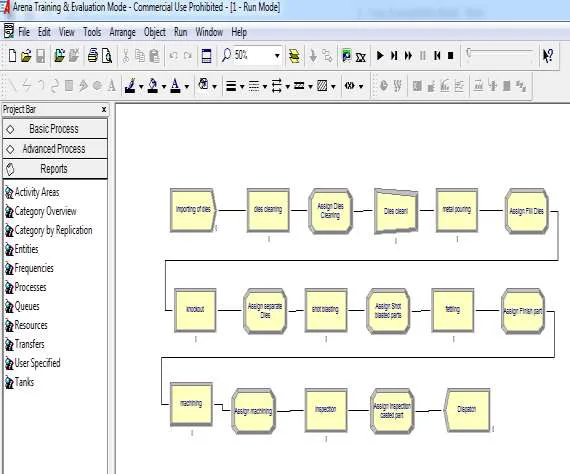
- Figure 1. Value Stream Mapping Methodology
- Figure 2. Integration of Value Stream Mapping with Simulation
- Figure 3 Site Visits
- 4. Structured Interviews
- Figure 5 Current Foundry Production Lay out
- Figure 6. Current State Map
- Figure 7. Arena Simulation Model for Current State Map
- Figure 8. Key Performance Indicator
- Figure 9 Category Overview of Queue
- Figure 10 Category Review of Time Entity
- Figure 11 Kaizen Umbrella
- Figure 12 Arena Simulation Model
- Figure 13. Category Review of non-value added activities
- Figure 14. Category Overview of Product Entity
- Figure 15 Future State Map
- Figure 16 Comparison between Current & Future State Map
7. 結論:
バリューストリームマッピングツールは、世界クラスの製造ツールとして、あらゆるセクターで効果的に使用できます。分析された研究は、ダイカスト業界のケーススタディです。主な目的は、バリューストリームにおける無駄の排除です。この研究では、バリューストリーム分析ツールを使用して非付加価値活動を特定します。現状を評価するために現状マップがプロットされます。無駄の排除技術が提示され、改善のために未来マップも推奨されます。研究の結果は、バリューストリームにおける非付加価値活動の15%の無駄削減を示し、その結果、総サイクルタイムが6.146%削減されます。VSMとシミュレーションソフトウェアの統合は、システムを適切に分析し、生産性を向上させる機会を見つけるのに役立ちます。バリューストリームマッピングは、生産性を向上させる機会を見つけるための可視化ツールです。
8. 参考文献:
- [List the references exactly as cited in the paper, Do not translate, Do not omit parts of sentences.]
- 1) R.M. Belokar, Sandeep Singh Kharb, Vikas Kumar “An Application of Value Stream Mapping In Automobile Industry: A Case Study", International Journal of Innovative Technology and Exploring Engineering (IJITEE) ISSN: 2278-3075, Vol.-1(2), pp.231-236, (2012).
- 2) Muhammad Abdus Samad et.Al, “Value Stream Mapping To Reduce Manufacturing Lead Time In A Semi-Automated Factory", Asian Transactions On Engineering, Vol.2 Issue 06, pp. 22-28, (2013).
- 3) Danijela Gracanina & BorutBuchmeister, BojanLalic “Using Cost-Time Profile for Value Stream Optimization”, Procedia Engineering 69 (2014), p. 1225 – 1231.
- 4) Rahani AR, Muhammad al-Ashraf “Production Flow Analysis through Value Stream Mapping: A Lean Manufacturing Process Case Study”, Procedia Engineering, Vol.41, pp.1727 – 1734, (2012).
- 5) Mahmoud Al-Odeh et.al, “Value Stream Mapping: Recreating an Industrial Environment in an Educational Setting", Proceedings of The (2014) IAJC/ISAM Joint International Conference ISBN, p.978-1-60643-379-9.
- 6) Palak P. Sheth1 et.Al, “Value Stream Mapping: A Case Study of Automotive Industry”, Ijret (2014), p.2321-7308.
- 7) Rehab M. Ali et.al “Dynamic Lean Assessment for Takt Time Implementation”, Procedia CRIP 17 (2014), p.577-581.
- 8) G. M. Gohane, A. S. Bonde & C.S. Sable," Improvement of Productivity Using Value Stream Mapping", IJSRD - International Jour nal for Scientifi c Research & Development| Vol. 2(8), ISSN (online): 2321-0613, pp.1-5, (2015).
- 9) G. Sahitya Reddy, Harsha Lingareddy & K.Jagadeeshwar, "Value Stream Mapping In A Manufacturing Industry", International Journal of Advanced Engineering Technology E-ISSN 0976-3945, Vol.4(2), pp.20-23,(2013).
- 10) Binu Bose V & K N Anilkumar, “Reducing rejection rate of castings using Simulation Model”, Proceedings of International Conference on Energy and Environment, International Journal of Innovative Research in Science, Engineering and Technology, Vol. 2(1), pp.589-597,(2013).
- 11) Petter Solding & Per Gullandar, “Concepts for Simulation Based Value Stream Mapping", Proceedings of the 2009 Winter Simulation Conference, pp.2231-2237, (2009).
- 12) Wei Xia & Jiwen Sun, “Simulation guided value stream mapping and lean improvement: A case study of a tubular machining facility", Journal of Industrial Engineering and Management, JIEM,pp.456-476, (2013).
- 13) Abu Md. Saifuddoha, Md. Ahasan Habib2, Sohana Yasmin Sumi, Md. Jennurine, Md. Saiful Islam, “Minimization Of Waste By Applying Value Stream Mapping In The Supply Chain Of Cement Industry”, IOSR Journal of Business and Management (IOSR-JBM), ISSN: 2319-7668, Volume 9, Issue 3,pp.79-84,(2013).
- 14) S. Santhosh kumar, M. Pradeep kumar, “Cycle Time Reduction of truck body assembly in an automobile industry by lean principles", Procedia Materials science, Vol.5, pp.1853-1862, (2014).
- 15) Schönemann, M. et.al “Integrating product characteristics into extended value stream modeling”, Procedia CIRP (2014) p.368 – 373.
専門家Q&A:あなたの疑問に答えます
Q1: この研究で生産性向上のために最も重要だと特定された要因は何ですか?
A1: この研究が結論付けた最も重要な要因は、バリューストリームにおける非付加価値活動(無駄)を体系的に特定し、排除することです。これは論文の「Conclusion」セクションで詳述されており、現状マップ(Figure 6)と未来マップ(Figure 15)を比較したデータによって裏付けられています。[Productivity Improvement by Value Stream Mapping in Die Casting Industry, Conclusion]
Q2: この研究は、生産性問題に対処する従来の方法とどう比較されますか?
A2: 論文の「Introduction」および「LITERATURE REVIEW」セクションでは、多くの改善アプローチが存在する中で、VSMは作業プロセスを合理化し、他の方法では見過ごされがちな無駄を特定し、変革プロセスを効果的に管理するためのユニークな可視化ツールを提供することを示唆しています。これは、単なる観察や個別改善を超えるアプローチです。[Productivity Improvement by Value Stream Mapping in Die Casting Industry, Introduction]
Q3: この発見は、すべての種類のダイカストに適用可能ですか、それとも特定のダイカストに限定されますか?
A3: 「IMPLEMENTATION OF VSM IN DIE CASTING INDUSTRY」セクションに記載されている通り、この研究は「自動車および非自動車向けの高品質アルミニウムダイカスト部品を製造するアルミニウムダイカスト会社」で実施されました。VSMと無駄削減の原則は一般的に適用可能ですが、得られた具体的な数値結果はこの特定の状況に関連するものです。[Productivity Improvement by Value Stream Mapping in Die Casting Industry, IMPLEMENTATION OF VSM IN DIE CASTING INDUSTRY]
Q4: 研究者たちは、この結論に達するためにどのような特定の測定またはシミュレーション技術を使用しましたか?
A4: 「ARENA SIMULATION MODELING」および「INTEGRATION OF VALUE STREAM MAPPING WITH SIMULATION」セクションで説明されているように、研究者たちはプロセスを可視化するためにバリューストリームマッピングを、提案された変更の影響を定量化するために「Arena Basic Edition software」によるシミュレーションモデリングを利用しました。[Productivity Improvement by Value Stream Mapping in Die Casting Industry, ARENA SIMULATION MODELING]
Q5: 論文によると、主な限界や今後の研究分野は何ですか?
A5: 論文の「Conclusion」セクションは、ケーススタディの肯定的な結果に焦点を当てており、研究の限界や将来の研究への具体的な方向性を明示的には述べていません。しかし、VSMが継続的改善のためのツールであることを強調しており、これはプロセスが繰り返し改善可能であることを示唆しています。[Productivity Improvement by Value Stream Mapping in Die Casting Industry, Conclusion]
Q6: この論文から、ダイカスト工場が得られる直接的で実践的な教訓は何ですか?
A6: 中核となる教訓は、構造化されたVSMアプローチを採用することで、隠れた無駄(このケースでは生産時間の約40%)を大量に特定し、サイクルタイムと生産性において測定可能な改善を達成できるということです。これは、論文「Productivity Improvement by Value Stream Mapping in Die Casting Industry」の全体的な結果によって強く裏付けられています。
結論と次のステップ
本研究は、HPDCにおける生産性向上プロセスのための貴重なロードマップを提供します。その発見は、品質を向上させ、欠陥を減らし、生産を最適化するための、明確でデータに基づいた道筋を示しています。
株式会社CASTMANでは、お客様が抱える最も困難なダイカストの問題を解決するために、最新の業界研究を応用することに専念しています。もし、この記事で議論された課題が貴社の事業目標と共鳴するものであれば、ぜひ当社の技術チームにご連絡ください。これらの先進的な原則を貴社のコンポーネントにどのように実装できるか、ご相談させていただきます。
著作権
- 本資料は、"Pradip Gunaki"氏および"S.N. Teli"氏による論文に基づいています。論文名: "Productivity Improvement by Value Stream Mapping in Die Casting Industry".
- 論文の出典: https://www.researchgate.net/publication/317427739
本資料は情報提供のみを目的としています。無断での商業利用は禁じられています。
Copyright © 2025 CASTMAN. All rights reserved.