この論文概要は、['The Future of Structural Components in HPDC.']という論文に基づいて、['Bühler AG']で発表されたものです。
1. 概要:
- タイトル: The Future of Structural Components in HPDC.
- 著者: Hermann Jacob Roos, Martin Lagler, Luis Quintana
- 発表年: 論文中に明記されていません。
- 掲載ジャーナル/学会: Bühler AG
- キーワード: structural components, HPDC, die casting, automotive industry, weight reduction, thermal management, alloy selection, lightweight design, cost reduction.
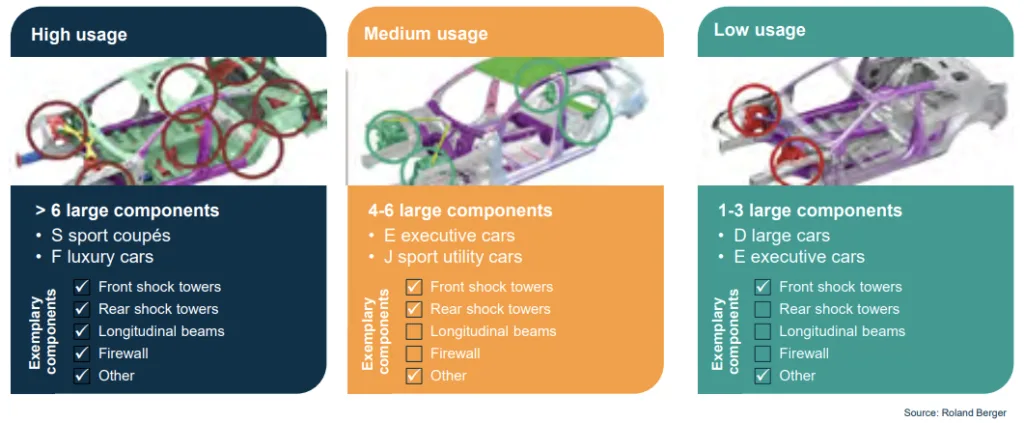
2. 概要 (Abstracts)
自動車産業における軽量化部品への継続的な探求は、ダイカストにとって有利な新たな市場、すなわち構造部品の出現をもたらしました。ショックタワーや縦梁のような大型で複雑な部品の需要は、2018年には600万台弱の自動車をカバーすると推定されており、その多くは複数の構造部品を搭載しています。現在の使用量は、2025年までに約900万台に増加すると予測されています。しかし、これらの構造部品は、自動車メーカーが求めるより剛性が高く軽量なソリューションを提供する一方で、長期間の生産ランにおけるコストが、スポーツカー、高級車、SUV、および少量生産が経済的に理にかなう品質Dセグメントのサルーンへの採用をこれまで制限してきました。しかし、ダイカストの経済性は変化しています。過去数年間で、構造部品のコストは最大20%も低下しました。本稿では、高度な熱管理、新しい合金の使用、および慎重な製品設計の組み合わせが、生産コストをさらに押し下げる可能性を示しています。これにより、ダイカスト構造部品は、大量自動車市場にとってより費用対効果の高いものになります。2023年には新車生産台数が1億1000万台に達すると予測されており¹、自動車1台あたり2〜6個の構造部品が搭載されることを考えると、これらの技術的進歩は、世界中のダイカストメーカーにとっての機会を大きく変える可能性があります。ダイカストマシンメーカーから鋳造所、そしてOEMまで、製造チェーン全体が協力すれば、それは可能になるでしょう。
3. 研究背景:
研究トピックの背景:
自動車産業は、燃費向上、バッテリー航続距離の延長、排出量削減のため、軽量化部品を継続的に追求しています。この傾向は、構造部品に対する大きな需要を生み出し、ダイカストにとって有利な市場を創出しました。電気自動車(EV)の普及は急速に進んでおり、世界の販売台数は2017年の約200万台から2018年には510万台へと2倍以上に増加しています。² すべての自動車メーカーは、より持続可能な自動車を、できれば低コストで生産することに注力しており、軽量化は重要な要素となっています。アルミニウム合金による大型構造部品のダイカストは、従来の鋼構造よりも優れた強度と成形性を持ちながら軽量であるため、自動車の軽量化を実現する実績のある方法として認識されています。
既存研究の現状:
ドイツの高級車市場で先駆的に採用されたダイカスト構造部品は、現在では幅広い車種で利用されています。図1は、自動車市場における構造部品の現在の使用状況を、車種(高使用量、中使用量、低使用量)と、フロントショックタワー、リアショックタワー、縦梁、ファイアウォールなどの代表的な部品別に分類して示しています。SスポーツクーペとF高級車は現在、最も高い使用量を示しており、衝突エネルギーを吸収するように設計された部品を組み込んでいます。EセグメントのエグゼクティブカーとJセグメントのスポーツユーティリティカーは、ショックタワーとロッカーレインフォースメントにダイカスト部品を使用しています。Dセグメントの大型車は、フロントショックタワーとトンネルレインフォースメントにダイカスト部品を使用しています。
研究の必要性:
ダイカスト構造部品の利点にもかかわらず、量産車市場への採用は、長期間の生産ランに関連するコストのために制限されてきました。ツーリングへの投資コストは比較的低いものの、工具の摩耗が増加するとメンテナンスコストが上昇し、Cセグメントの中型車市場や小型量産車市場では、全体的なユニットコストが法外に高くなります。しかし、ダイカストの経済性は進化しており、構造部品のコストは近年最大20%も低下しています。生産コストをさらに削減し、ダイカスト構造部品を量産車市場への採用においてより費用対効果の高いものにする技術的進歩を探求する必要があります。これにより、世界中のダイカストメーカーの可能性が開かれます。
4. 研究目的と研究課題:
研究目的:
本論文は、熱管理、合金選択、製品設計の進歩が、ダイカスト構造部品の生産コストをさらに削減し、量産自動車市場へのより広範な採用を可能にする方法を示すことを目的としています。最終的な目的は、ダイカストがコスト障壁を克服し、量産車における構造部品の実行可能なソリューションとなるための道筋を特定することです。
主要な研究課題:
主要な研究課題は、「現在の技術で、ダイカストが量産車市場へのコスト障壁を打ち破ることを可能にするために、どのような進歩と技術を導入できるか?」です。本論文では、以下の3つの技術分野について調査しています。
- 熱管理による生産性向上
- 新しい合金を利用した工程削減
- 製品設計による軽量構造
研究仮説:
中心となる仮説は、高度な熱管理を実施し、熱処理を最小限に抑えるか排除するために新しい合金を利用し、軽量製品設計を採用することで、ダイカスト構造部品の生産コストを大幅に削減でき、量産自動車用途において経済的に実現可能になるということです。具体的には、これらのアプローチの組み合わせにより、代表的なショックタワーの理論的なコスト削減プログラムで示されているように、23%を超えるコスト削減を達成できると仮説を立てています。
5. 研究方法
研究デザイン:
本論文では、ビューラー社のアプリケーションに関する知識と、ローランド・ベルガー社が実施した市場分析を活用した、分析的かつ実証的なアプローチを採用しています。実証的な実験ではなく、計算と業界のベストプラクティスに基づいて、理論的なコスト削減プログラムを提示しています。このデザインは、特定の技術的進歩がダイカスト構造部品の費用対効果に与える潜在的な影響を示すことに焦点を当てています。
データ収集方法:
分析は、ヨーロッパ、中国、北米で得られたビューラー社の業界経験とアプリケーションに関する知識に基づいています。市場データと予測は、ローランド・ベルガー社の調査(図2)から得られたもので、既存、既知、および予測される自動車アーキテクチャ、学会発表、および業界専門家へのインタビューを考慮しています。コスト削減の計算は、代表的なショックタワー部品を対象に、4,400トンマシンと2キャビティ3プレート金型構成を利用して提示されています。
分析方法:
本論文では、熱管理、新しい合金、および軽量設計がユニット生産コストに与える影響を評価するために、費用便益分析アプローチを採用しています。サイクルタイムの短縮、金型寿命の延長、およびスクラップ率の低減を定量化して、改善された熱管理によって達成されるコスト削減を示しています(図4および5)。熱処理を削減または排除する新しい合金の利用による潜在的なコスト削減も分析されています(図7)。最後に、軽量設計によるコスト削減を評価します(図8)。これらの3つの分野からの累積的なコスト削減を計算して、ダイカスト構造部品の競争力を高める全体的な可能性を示しています。
研究対象と範囲:
研究はダイカスト構造部品に焦点を当てており、特に代表的な自動車用ショックタワーをケーススタディとして使用しています。範囲は、高圧ダイカスト(HPDC)技術とその自動車産業への応用に限定されています。分析では、高級車から量産車まで、さまざまな車種セグメントを考慮し、コスト障壁に対処することで、これらのセグメント全体でダイカスト構造部品の使用を拡大する可能性を検討しています。
6. 主な研究成果:
主な研究成果:
本論文では、ダイカスト構造部品の生産コストを大幅に削減できる3つの主要な技術的進歩を特定しています。
- 熱管理の改善: 熱バランスを最適化し、ターゲットを絞ったマイクロ噴霧を組み込むことで、サイクルタイムを約33%短縮(代表的なショックタワーの場合、90秒から60秒)、金型寿命を50%以上延長(80,000サイクルから少なくとも120,000サイクル)、スクラップ率を5%から3%に低減できます。この組み合わせにより、ユニット生産コストを10%削減できます(図5)。
- 新しい合金システム: AlMg4Fe2やAlMg6Si2MnZrなどの新しい合金システムを利用することで、熱処理(HT)や矯正工程の必要性をなくし、生産コストをさらに削減できる可能性があります。新しい合金への切り替えにより、さらに10%のコスト削減が可能です(図7)。表1は、標準的な構造用合金システム(AlSi10MnMg)と、新しい合金(AlMg4Fe2)および高強度合金システム(AlMg6Si2MnZr)の特性を詳細に示しています。 図6: 構造部品用の異なる合金システムの可能性 合金システム AlSi10MnMg AlMg4Fe2 AlMg6Si2MnZr HT T7 F T5 UTM Rm[MPa] 200-240 240-260 350-380 耐力 Rp0,2% [MPa] 120-140 120-140 230-250 伸び A [%] 10-20 10-22 8-12
- 軽量製品設計: インテリジェントな製品設計(例えば、肉厚を2.5mmから1.8mmに削減するなど)により、最大20%の軽量化を達成できます。ショックタワーの例では、重量を4,000gから3,600g(10%削減)に軽量化することで、生産コストをさらに4%削減できます(図8)。
データ解釈:
図5、7、および8に示されているデータは、改善された熱管理、新しい合金の利用、および軽量設計を組み合わせることで、23%を超える累積的なコスト削減の可能性があることを示しています。図2は、構造部品市場の予測成長を示しており、需要の増加を強調しています。図3は、生産コスト削減による潜在的な市場成長を強調しており、2030年までに約600万ユニットから2500万ユニットへの大幅な拡大を示唆しています。図4は、熱管理の改善によって達成されたサイクルタイムの短縮を視覚的に表しています。
図表名リスト:
- Figure 1: Current usage for structural components in the automotive market (自動車市場における構造部品の現在の使用状況)
- Figure 2: Predicted growth in current structural components, 2015 to 2025 (現在の構造部品の予測成長、2015年から2025年)
- Figure 3: Potential structural component market growth with production cost savings (生産コスト削減による潜在的な構造部品市場の成長)
- Figure 4: How better thermal management can reduce cycle times by up to a third (熱管理の改善がサイクルタイムを最大3分の1まで短縮する方法)
- Figure 5: Cost reduction using improved thermal management (熱管理の改善によるコスト削減)
- Figure 6: Possibilities of different alloy systems for Structural components. (構造部品用の異なる合金システムの可能性)
- Figure 7: Potential cost savings from new alloys (新しい合金による潜在的なコスト削減)
- Figure 8: Cost saving potential by light weight design (軽量設計によるコスト削減の可能性)
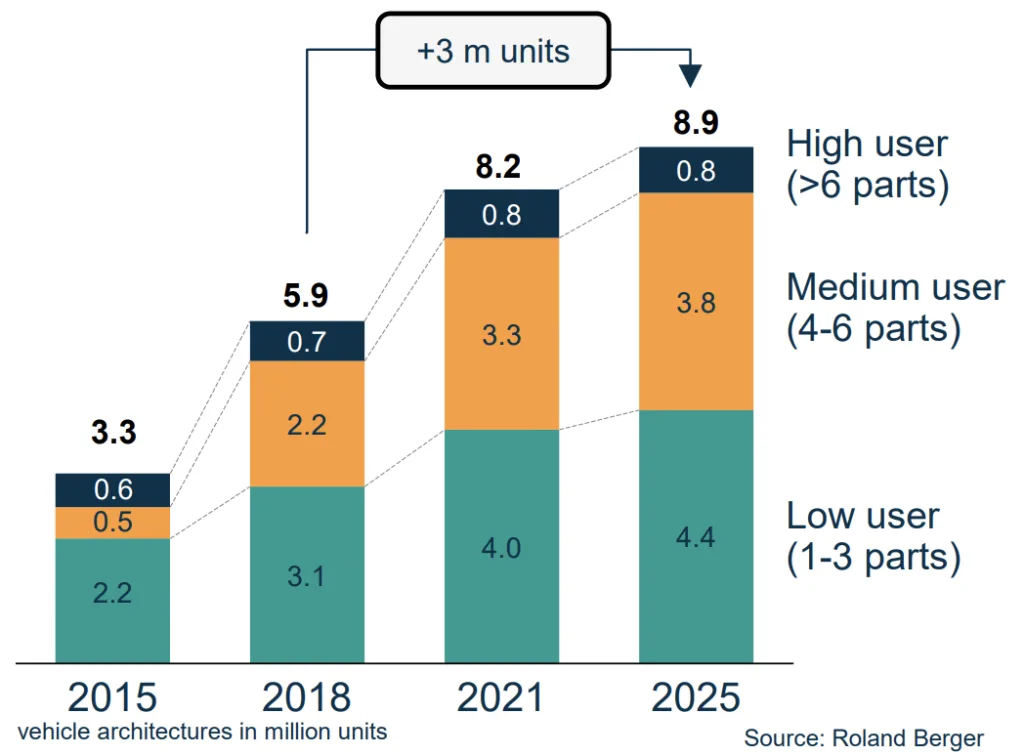
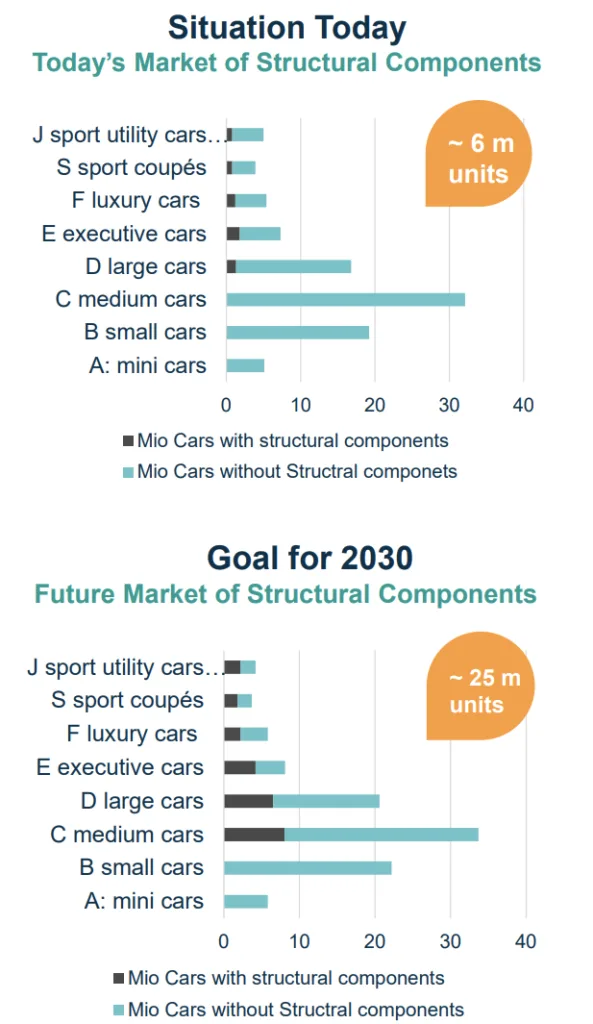
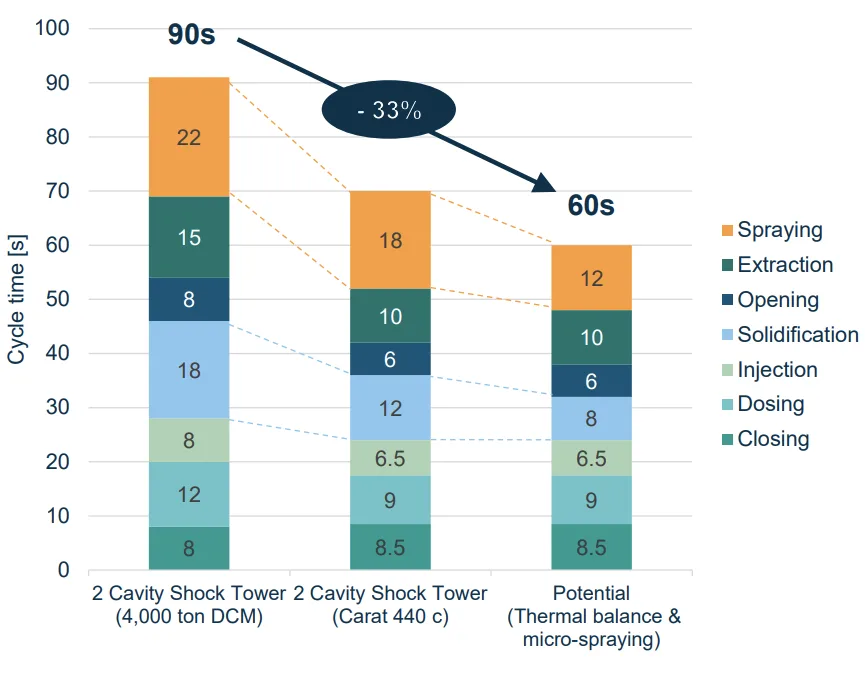
7. 結論:
主な調査結果の要約:
本論文は、ダイカスト構造部品がコスト障壁に対処することで、量産自動車市場への採用に大きな可能性があると結論付けています。高度な熱管理、新しい合金システム、および軽量製品設計の組み合わせにより、23%を超える大幅なコスト削減を達成できます。このコスト削減は、主にサイクルタイムの改善、金型寿命の延長、スクラップの削減、および熱処理や矯正などの鋳造後工程の排除によって推進されています。
研究の学術的意義:
本研究は、自動車産業の進化する需要に対応するために、ダイカスト技術における継続的なイノベーションの重要性を強調しています。特定の技術的進歩が、量産におけるダイカスト構造部品の経済的実現可能性にどのように貢献できるかを理解するためのフレームワークを提供します。この分析は、HPDCが自動車の軽量化と持続可能性の目標に貢献する可能性を強調しています。
実際的な意義:
調査結果は、ダイカスト鋳造所、自動車OEM、およびダイカストマシンメーカーにとって大きな実際的な意義があります。提案された技術的進歩を実施することで、ダイカストメーカーは量産市場に参入でき、OEMは費用対効果の高い軽量化ソリューションの恩恵を受けることができます。本論文では、これらの利点を実現するために、製造チェーン全体の協力が必要であることを強調しています。
研究の限界と今後の研究分野:
本論文は、計算と業界経験に基づいた理論的なコスト削減プログラムを提示しています。今後の研究では、パイロット生産研究と実際のケーススタディを通じて、これらの調査結果の実証的な検証を行うことができます。分析は代表的なショックタワーに焦点を当てています。今後の研究では、これらのコスト削減戦略の、より広範囲な構造部品や異なるダイカストプロセスへの適用可能性を調査できます。さらに、新しい合金と軽量設計で製造された構造部品の長期的な性能と耐久性を調査することは有益でしょう。
8. 参考文献:
- Wagner, Statistica, available at: https://www.statista.com/
statistics/266813/growth-of-the-global-vehicle-production-
since-2009/ - IEA (2019), "Global EV Outlook 2019", IEA, Paris, www.iea.
org/publications/reports/globalevoutlook2019/ - Roland Berger (2019), Independent research for Bühler
AG: Considers existing, known and projected architectures,
congress presentations and interviews with industry experts. - DGS award-winning casting: https://www.dgs-druckguss.
com/en/technology-and-innovation/awards
9. 著作権:
- この資料は、"Hermann Jacob Roos, Martin Lagler, Luis Quintana"氏の論文:"The Future of Structural Components in HPDC."に基づいています。
- 論文ソース: 論文中に明記されていません。
この資料は上記の論文に基づいて要約されたものであり、商業目的での無断使用は禁止されています。
Copyright © 2025 CASTMAN. All rights reserved.