1. 概要:
- タイトル: Taguchi法による新規部分凝固高圧アルミニウムダイカストの最適化 (Optimization in Novel Partial-Solid High Pressure Aluminum Die Casting by Taguchi Method)
- 著者: Yekta Berk Suslu, Mehmet Sirac Acar, Mithat Senol, Muammer Mutlu, Ozgul Keles
- 発表年: 2018年
- 掲載ジャーナル/学会: The Minerals, Metals & Materials Society (TMS) - Light Metals 2018 Conference Proceedings
- キーワード: 高圧ダイカスト, 部分凝固加工, アルミニウム, Taguchi法, 最適化
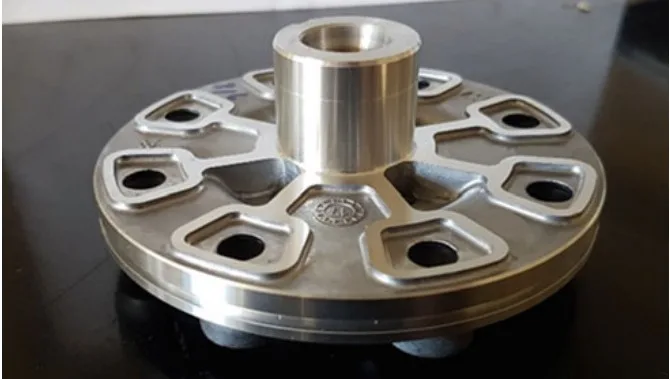
2. 研究背景:
- 研究トピックの社会的/学術的背景:
- 高圧ダイカスト (HPDC) は、自動車、航空宇宙、家電産業に不可欠な部品製造に不可欠な方法です。
- HPDCの利点は、高速凝固によるサイクル時間の短縮であり、大量生産を可能にします。
- しかし、HPDCにおける主な欠陥は、効率を低下させる多孔性と引け巣です。
- 既存研究の限界:
- 従来のHPDC法では、多孔性や引け巣の欠陥を最小限に抑えることが難しい場合があります。
- 真空引き、冷却ベント、射出速度の調整などの技術は役立つ場合がありますが、これらの問題を完全には解消できない可能性があります。
- 従来の鋳造法、HPDCを含め、多孔性、引け巣、コールドスラグ欠陥などの欠陥が発生しやすいです。
- 研究の必要性:
- 従来のHPDCの限界を克服し、部品品質を向上させるために、部分凝固鋳造が解決策として検討されています。
- 部分凝固鋳造、特にガス誘導半凝固 (GISS) 技術を使用することで、微細構造を変化させ、機械的特性を向上させることができます。
- GISS-HPDCプロセスを最適化することは、高品質部品を欠陥を減らして製造する可能性を最大限に引き出すために必要です。
- 実験計画法の一つであるTaguchi法は、GISS-HPDCに関わる複雑なパラメータを最適化するための有用なツールとして特定されています。
3. 研究目的と研究課題:
- 研究目的:
- ガス誘導半凝固 (GISS) 技術を高圧ダイカスト (HPDC) に統合し、「A」クラス品質の部分凝固アルミニウム自動車部品を製造するためのパラメータを最適化すること。
- GISS-HPDCにおける多孔性レベルと微細構造特性に対する主要なプロセスパラメータの影響を明らかにすること。
- 主な研究課題:
- 部分凝固HPDCにおける多孔率に、溶融温度、ガス吹込み時間、二次射出速度、ゲート厚さはどのように影響するか? (GISS技術を使用)
- GISS-HPDCで製造されたアルミニウム自動車部品において、多孔性を最小限に抑え、「A」クラス品質を達成するための溶融温度、ガス吹込み時間、二次射出速度、ゲート厚さの最適レベルは何か?
- GISS技術は、HPDCアルミニウム部品の微細構造、特に球状構造の形成と金属間化合物の分布にどのように影響するか?
- 研究仮説: (研究デザインに暗黙的に含まれる)
- Taguchi法を適用することで、GISS-HPDCアルミニウム自動車部品の多孔性を最小限に抑えるための溶融温度、ガス吹込み時間、二次射出速度、ゲート厚さの最適な組み合わせを特定できる。
- GISS技術は、HPDCアルミニウム部品において球状微細構造の形成を促進し、従来のHPDCと比較して機械的特性の向上と多孔性の低減につながる。
- ゲート厚さ、溶融温度、二次射出速度、ガス吹込み時間は、GISS-HPDCの多孔性レベルにさまざまな程度の影響を与え、それらの相対的な重要性はTaguchi分析を通じて決定できる。
4. 研究方法:
- 研究デザイン:
- Taguchi L9直交配列を用いた実験計画法 (DOE) アプローチ。
- GISS-HPDCプロセスを最適化するために、4つのパラメータをそれぞれ3つのレベルで調査しました。
- L9直交配列により、4つのパラメータをわずか9回の実験で調査でき、総当たり法と比較して実験回数を大幅に削減できました。
- データ収集方法:
- 実験鋳造: L9直交配列に基づいて9回の鋳造試験を実施。EN AC 48000 (AlSi12CuNiMg) アルミニウム合金を使用。各実験で15個の試験片を7700 kNの締付力を持つコールドチャンバーHPDCマシンを使用して製造。鋳造後に部品を機械加工。
- 透過X線検査 (非破壊): Bosello Industrial X線スキャナー (115 kV, 1.5 mA) を使用して、各実験の5番目、10番目、15番目の試験片の多孔性レベルを評価。多孔性は4 (最良 - Aクラス) から 1 (最悪 - Dクラス) までで評価。
- 微細構造評価 (破壊): 各実験の15番目の試験片を微細構造評価に使用。
- 光学顕微鏡: Nikon Eclipse LV100ND 光学顕微鏡を使用して、金属組織学的準備 (研磨、研削、ケラー試薬で10秒間エッチング) 後に微細構造を観察。
- 走査型電子顕微鏡 (SEM) およびエネルギー分散型分光法 (EDS): FESEM, JSM 7000 F を形態学的分析および金属間化合物の特定に利用。
- 分析方法:
- 透過X線品質スコア: 各実験の5番目、10番目、15番目の試験片の透過X線グレードから平均品質スコアを算出。
- S/N比 (信号対雑音比) 分析: S/N比は、「大きいほど良い」品質特性に基づいて計算され、以下の式を使用。
-10 log₁₀ (Σ(1/Yᵢ²)/n)
ここで、Yᵢ は実験における各試験片の品質スコア、n は試験片数 (この場合 n=3、各実験で3つの試験片を評価)。Minitab 18 ソフトウェアをS/N比分析に使用。- S/N比の主効果プロット: 各パラメータレベルがS/N比に与える影響を視覚化し、最適なレベルを特定するために作成。
- 確認実験: Taguchi分析で特定された最適なパラメータの組み合わせを使用して確認鋳造実験を実施し、結果を検証。
- 研究対象と範囲:
- 材料: 市販のEN AC 48000 (AlSi12CuNiMg) アルミニウム鋳造合金。化学組成は表2に記載:Si (12%)、Fe (0.21%)、Mn (1.2%)、Cu (0.9%)、Ni (0.81%)、Mg (0.74%)、Al (残部)。
- 部品タイプ: 自動車部品 (特定の形状は図1に示されており、「製造部品、鋳造および機械加工」と説明)。
- プロセス: 部分凝固高圧ダイカスト (GISS-HPDC)。
- 調査パラメータ:
- A: 溶融温度 (°C): レベル: 1 (650±5), 2 (670±5), 3 (690±5)
- B: ガス吹込み時間 (秒): レベル: 1 (0), 2 (5), 3 (10)
- C: 二次射出速度 (m/s): レベル: 1 (4), 2 (4.5), 3 (5)
- D: ゲート厚さ (mm): レベル: 1 (1.8), 2 (2.4), 3 (3.5)
- 品質特性: 多孔性レベル (最小化)。
5. 主な研究成果:
- 主な研究成果:
- 最適パラメータの組み合わせ: S/N比分析に基づき、最適パラメータの組み合わせはA3B3C2D1と決定。これは以下に対応します。
- 溶融温度: レベル 3 (690 ± 5 °C)
- ガス吹込み時間: レベル 3 (10 秒)
- 二次射出速度: レベル 2 (4.5 m/s)
- ゲート厚さ: レベル 1 (1.8 mm)
- パラメータの重要度: ゲート厚さが多孔性を低減する最も効果的なパラメータであり、次いで溶融温度、二次射出速度、ガス吹込み時間の順に影響力が減少 (図4のS/N値の最小値と最大値の差に基づいて)。
- 多孔性低減と「A」クラス品質: 最適パラメータ (A3B3C2D1) を使用した確認実験では、5番目、10番目、15番目の試験片の透過X線スコアがそれぞれ4、4、4となり、「A」クラス品質の部品が得られました。これはTaguchi最適化を検証し、高品質部品の製造に成功したことを示しています。
- 微細構造の変化: GISS適用試験片は、従来のHPDCと比較して、より微細で球状の初晶α-Al相分布を示しました。非樹枝状晶の微細構造が達成されました。
- 金属間化合物の特定: SEM-EDS分析により、金属間化合物はα-Alマトリックス、Al-Cu-Ni混合物、Al₃FeSi、Al₁₅Si₂(FeMn)₃、Al₂Cu、Al₅(FeMn)Si₁.₅として特定されました。
- 最適パラメータの組み合わせ: S/N比分析に基づき、最適パラメータの組み合わせはA3B3C2D1と決定。これは以下に対応します。
- 統計的/定性的分析結果:
- 表4: 9つの実験それぞれについて、5番目、10番目、15番目の試験片の透過X線グレード (Y₁、Y₂、Y₃)、平均品質スコア (Ỹ)、および計算されたS/N比を示しています。最高の平均品質スコア (4.00) とS/N比 (12.04) を持つ実験9は、L9実験の中で最良の結果を表しています。
- 図3: 「A」クラス (最良) と「D」クラス (最悪) 品質部品の透過X線画像を示し、多孔性レベルの違いを視覚的に示しています。図3aは多孔性がほとんどない (「A」クラス) のに対し、図3bは多孔性が白い円形の点として見られる (「D」クラス) ことを示しています。
- 図4: S/N比の主効果プロット。各パラメータとレベルがS/N比に与える影響を示しています。ゲート厚さが最も影響力のあるパラメータであることを視覚的に確認できます。
- 図5: 確認実験試験片 (5番目、10番目、15番目) の透過X線試験結果。一貫して高品質 (すべて透過X線スコア4) であることを示しています。
- 図6: 9つの実験すべてからの15番目の試験片の光学顕微鏡画像。異なるパラメータの組み合わせによる微細構造の変化を示しています。GISS適用試験片では球状微細構造が明らかです。
- 図7: Taguchi確認実験試験片の微細構造。破断した樹枝状晶と球状α-Al粒子を示しています。
- 図8: Taguchi信頼性試験片のSEM分析BSE画像。異なる金属間化合物相 (中国文字状、針状) とEDS分析領域を示しています。
- 表5: 図8dの異なる領域のEDS分析結果 (wt%)。元素組成と文献比較に基づいて、考えられる金属間化合物を特定しています。
- データ解釈:
- S/N比分析は、GISS-HPDCにおける多孔性を最小限に抑えるための最適なパラメータ設定を効果的に特定しました。
- 確認実験は、Taguchi法がプロセス最適化に有効であることを検証しました。
- GISS技術は、機械的特性を向上させることが知られている球状微細構造を促進することに成功しました。
- ゲート厚さが、この特定のGISS-HPDCアプリケーションにおける多孔性低減のための最も重要なパラメータとして浮上しました。
- ガス吹込み時間は重要ですが、過度の吹込み時間は溶融物の特性に悪影響を及ぼし、潜在的に欠陥を引き起こす可能性があるため、最適化する必要があります。選択された10秒の吹込み時間は、悪影響を与えることなく生産サイクル時間を安定させるのに理想的であると見なされました。
- 図のリスト:
- 図 1 製造部品、鋳造および機械加工
- 図 2 ガス吹込みプロセス
- 図 3 「A」クラス (最良) と「D」クラス (最悪) 品質
- 図 4 主効果プロット
- 図 5 確認実験における5番目、10番目、15番目の試験片の透過X線試験結果
- 図 6 15番目の試験片の光学顕微鏡画像
- 図 7 Taguchi確認実験試験片の微細構造
- 図 8 Taguchi信頼性試験片のSEM分析BSE画像; a 全体像, b 中国文字状金属間化合物, c 針状金属間化合物, d 異なる種類の金属間化合物を含む領域

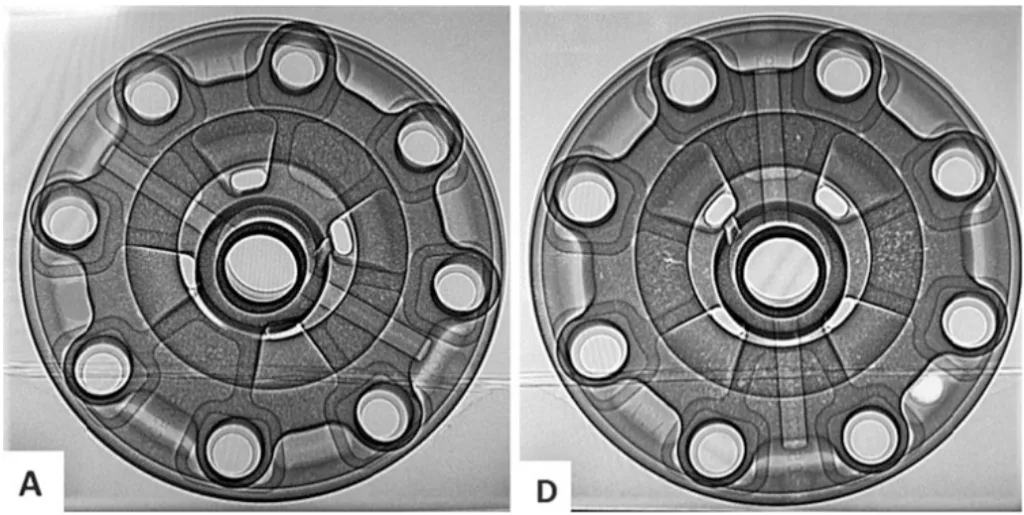
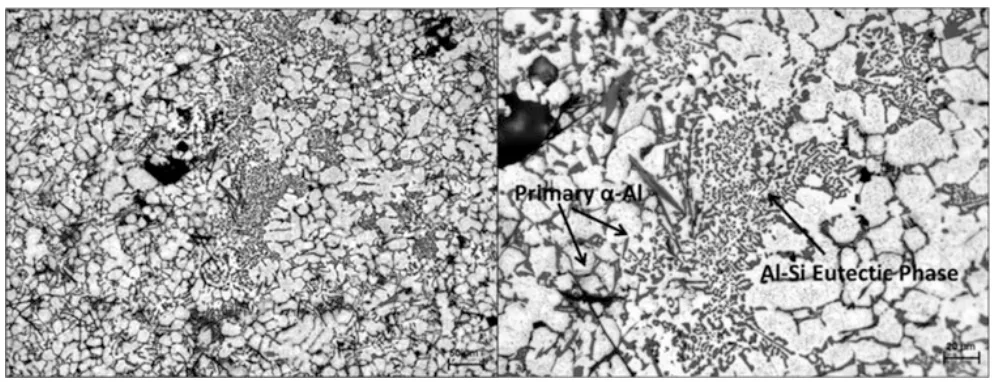
6. 結論と考察:
- 主な結果の要約:
- Taguchi L9直交配列法は、アルミニウム自動車部品製造のためのGISS-HPDCプロセスの最適化に成功裏に適用されました。
- 多孔性を最小限に抑え、「A」クラス品質を達成するための最適プロセスパラメータ (A3B3C2D1: 溶融温度 690 ± 5 °C、ガス吹込み時間 10 秒、二次射出速度 4.5 m/s、ゲート厚さ 1.8 mm) が特定されました。
- ゲート厚さが多孔性に最も影響を与えるパラメータであることが判明しました。
- GISS技術により、非樹枝状晶の球状微細構造が得られました。
- 金属間化合物 (α-Al、Al-Cu-Ni、Al₃FeSi、Al₁₅Si₂(FeMn)₃、Al₂Cu、Al₅(FeMn)Si₁.₅) が特定されました。
- 確認実験により、最適化結果が検証されました。
- 研究の学術的意義:
- 本研究は、GISS-HPDCのような新規製造プロセスの最適化にTaguchi法が効果的に適用できることを示しています。
- 部分凝固アルミニウム合金のダイカストにおける多孔性と微細構造に対する主要なプロセスパラメータの影響に関する貴重な洞察を提供します。
- 本研究は、GISS技術とそのHPDC部品品質向上の可能性の理解に貢献します。
- 実用的な意義:
- 最適化されたGISS-HPDCプロセスは、多孔性を低減し、性能を向上させた高品質のアルミニウム自動車部品を製造するために、産業現場に直接導入できます。
- 特定された最適なパラメータ設定は、EN AC 48000合金および同様の部品形状でGISS-HPDCを使用する製造業者にとって貴重なガイドラインとなります。
- 本研究は、GISS-HPDCにおける多孔性制御におけるゲート厚さの重要性を強調し、金型設計に関する実用的なガイダンスを提供します。
- 研究の限界:
- 最適化は、特定のアルミニウム合金 (EN AC 48000) と特定の自動車部品形状に対して実施されました。最適なパラメータは、異なる合金または部品設計に対して再評価する必要がある場合があります。
- 本研究では、多孔性を主要な品質特性として焦点を当てました。機械的特性や表面仕上げなど、部品品質の他の側面をさらに調査することができます。
- 調査されたパラメータとレベルの範囲は、表3で定義されたものに限定されました。より広い範囲またはより細かいレベルを調査することで、さらなる最適化の可能性が明らかになる可能性があります。
7. 今後のフォローアップ研究:
- フォローアップ研究の方向性:
- 最適化されたGISS-HPDCパラメータが、製造された部品の機械的特性 (引張強度、降伏強度、伸び、硬度、耐疲労性) に与える影響を調査する。
- 最適化されたGISS-HPDCプロセスの他のアルミニウム合金および異なる部品形状への適用可能性を探る。
- 金型温度、射出圧力プロファイル、冷却速度などの追加要因を考慮して、GISSプロセスパラメータをさらに最適化する。
- 異なる不活性ガス (例: アルゴン、窒素) およびガス射出方法がGISSプロセスと部品品質に与える影響を調査する。
- GISS-HPDCにおける金属間化合物の形成メカニズムと、それらが機械的特性に与える影響の詳細な分析を実施する。
- 高度なシミュレーションツールを使用して、GISS-HPDCプロセスをさらに最適化し、部品品質を予測する。
- さらなる探求が必要な分野:
- 最適化されたGISS-HPDCで製造された部品の、実際の自動車用途における長期的な性能と信頼性。
- 大量生産のためのGISS-HPDCプロセスの費用対効果と拡張性。
- 従来のHPDCと比較したGISS-HPDCプロセスの環境影響評価。
8. 参考文献:
- http://www.aluminum.org/product-markets (2017年8月)
- Bonollo F, Gramegna N, Timelli G (2015) High-pressure die-casting: Contradictions and challenges. JOM, 67(5), 901–908.
- Atkinson H (2010) Semisolid processing of metallic materials. Materials Science and Technology, 26(12): 1401-1413.
- Czerwinski F (2006) The basics of modern semi-solid metal processing. JOM, 58(6): 17.
- Nafisi S, Gomashchi R (2016) Semi-solid processing of aluminum alloys, Springer, Switzerland, 9.
- Rice CS, Mendez PF (2001) Slurry-Based Semi-Solid DIE CASTING. Advanced materials & processes, 159(10): 49-52.
- Wannasin J et al. (2008) Development of the Gas Induced Semi-Solid metal process for aluminum die casting applications. In Solid State Phenomena, 141: 97-102.
- Flemings MC, Yurko JA, Martinez RA (2004) Solidification processes and microstructures. Proceedings of the TMS Annual Meeting, 3-14.
- Wannasin J, Janudom S, Rattanochaikul T, Canyook R, Burapa R, Chucheep T, Thanabumrungkul S (2010) Research and development of gas induced semi-solid process for industrial applications. Transactions of Nonferrous Metals Society of China 20: 1010-1015.
- Curle UA (2010) Semi-solid near-net shape rheocasting of heat treatable wrought aluminum alloys. Transactions of Nonferrous Metals Society of China (20)9: 1719-1724.
- Mahathaninwong N, Plookphol T, Wannasin J, Wisutmethangoon S (2012) T6 heat treatment of rheocasting 7075 Al alloy. Materials Science and Engineering: A, 532: 91-99.
- Verran GO, Mendes RPK, Dalla Valentina LVO (2008) DOE applied to optimization of aluminum alloy die castings. Journal of materials processing technology, 200.1: 120-125.
- Syrcos GP (2003) Die casting process optimization using Taguchi methods. Journal of materials processing technology, 135.1: 68-74.
- Thanabumrungkul S, et al. (2010) Industrial development of gas induced semi-solid process. Transactions of Nonferrous Metals Society of China 20: 1016-1021.
- Jumpol W, Wannasin J, Janudom S, Canyook R, Plookphol T, Wisutmethangoon S (2015) Effects of Solid Fractions in a Slurry Die Casting Process on Defects of 7075 Aluminum Alloy. In Applied Mechanics and Materials, 752: 7–10.
- Wannasin J, Martinez RA, Flemings MC (2006) Grain refinement of an aluminum alloy by introducing gas bubbles during solidification. Scripta Materialia, 55.2: 115-118.
- Canyook R, et al. (2012) Characterization of the microstructure evolution of semi-solid metal slurry during the early stages. Acta Materialia, 60.8: 3501-3510.
- Shabestari SG, Honarmand M, Saghafian H. (2015) Microstructural evolution of A380 aluminum alloy produced by gas-induced semi-solid technique (GISS). Advances in Materials and Processing Technologies, 1(1-2), 155-163.
- Janudom S, Rattanochaikul T, Burapa R, et al. (2010) Feasibility of semi-solid die casting of ADC12 aluminum alloy. Transactions of Nonferrous Metals Society of China 20(9);1756–1762.
- Krendelsberger N, Weitzer F, Schuster JC. (2007) On the Reaction Scheme and Liquidus Surface in the Ternary System Al-Fe-Si. Metallic Materials Transactions, 38A: 1681-1691.
- Bosselet F et al. (2004) Affinement expérimental de l'isotherme Al-Fe-Si à 1000 K. Journal de Physique IV (Proceedings), 122: 41-46.
- Dinnis CM, Taylor JA, Dahle AK (2005) As-cast morphology of iron-intermetallics in Al-Si foundry alloys. Scripta Materialia, 53 (8): 955-958.
- Irizalp SG, Saklakoglu N, (2014) Effect of Fe-rich intermetallics on the microstructure and mechanical properties of thixoformed A380 aluminum alloy. Engineering Science and Technology, an International Journal, 17(2): 58-62.
- Mohamed AMA, Samuel AM, Samuel FH, Doty HW (2009) Influence of additives on the microstructure and tensile properties of near-eutectic Al-10.8% Si cast alloy. Materials & Design, 30 (10): 3943-3957.
9. 著作権:
- この資料は、Yekta Berk Suslu, Mehmet Sirac Acar, Mithat Senol, Muammer Mutlu, Ozgul Keles氏らの論文「Optimization in Novel Partial-Solid High Pressure Aluminum Die Casting by Taguchi Method」に基づいています。
- 論文ソース: https://doi.org/10.1007/978-3-319-72284-9_40
この資料は上記の論文に基づいて要約されたものであり、商業目的での無断使用は禁止されています。
Copyright © 2025 CASTMAN. All rights reserved.