AIで自動車部品の破壊を未然に防ぐ:オルタネーターヒートシンクの振動疲労問題への新アプローチ
このテクニカルブリーフは、Dinçer Kökden氏らによる学術論文「Prevention of the Fracture Problem Occurring in Automotive Alternator Heatsink Blocks Using Artificial Intelligence」に基づいています。この論文は、2024年にApplied Sciences誌に掲載されたものです。高圧ダイカスト(HPDC)の専門家であるCASTMANが、業界のプロフェッショナルのためにその内容を要約・分析しました。
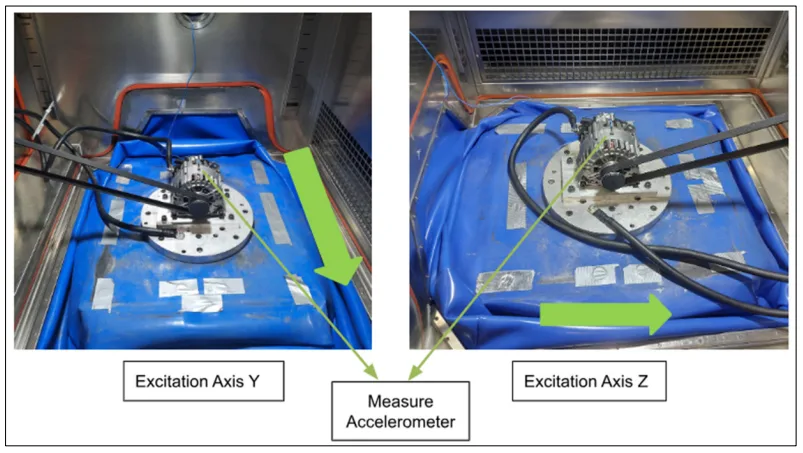
キーワード
- 主要キーワード: 自動車用ヒートシンク 破壊防止
- 副次キーワード: 人工ニューラルネットワーク, 振動疲労, 共振周波数, 設計最適化, 有限要素解析, 自動車部品, AI予測モデル
エグゼクティブサマリー
- 課題: 自動車用オルタネーターのヒートシンクは、薄肉で複雑な形状を持つため、エンジンの振動によって共振し、疲労破壊を起こしやすいという問題がありました。従来の開発プロセスでは、物理的な振動試験で破壊が起きてから再設計を行うため、時間とコストが大幅にかかっていました。
- 手法: 研究チームは、人工ニューラルネットワーク(ANN)と最適化アルゴリズムを用いて、ヒートシンクの設計パラメータ(ボルト穴の厚み、B+領域の断面積、ケーブル重量)と共振周波数の関係をモデル化しました。
- 重要なブレークスルー: 開発されたAIモデルは、ヒートシンクの共振周波数を極めて高い精度(R値 > 0.999)で予測することに成功しました。これにより、物理的な試作や試験を行う前に、設計段階で破壊のリスクを回避する最適な設計を見つけ出すことが可能になりました。
- 結論: AIとシミュレーションを統合することで、設計と検証にかかる時間を大幅に短縮し、振動による部品の破壊問題を効果的に防止できることが実証されました。これは、製品の信頼性向上と開発コスト削減に直結する画期的なアプローチです。
課題:なぜこの研究がHPDCの専門家にとって重要なのか
自動車のオルタネーターは、エンジンの機械的エネルギーを電気エネルギーに変換する際に大量の熱を発生させます。この熱を効率的に放散するために、表面積を最大化した薄肉のヒートシンクが不可欠です(Ref. [1-3])。これらのヒートシンクは、多くの場合、複雑な形状を持つ鋳造品であり、その性能は車両の信頼性に直結します。
しかし、これらの部品は車両の寿命を通じて常に激しい振動にさらされます。特に、部品の固有振動数(共振周波数)がエンジンの振動数と一致すると、振幅が急激に増大し、疲労亀裂が発生・進展し、最終的には部品の破壊に至ります(Ref. [5])。本研究で取り上げられたオルタネーターヒートシンクでは、振動試験中にボルト締結部で破壊が発生しました。
この問題は、開発プロセスの後期段階で発覚することが多く、手戻りによる設計変更や金型修正は、開発期間の延長とコスト増大の大きな原因となります。この「試験しては壊れ、設計し直す」という従来型のサイクルから脱却し、設計の初期段階で動的な性能を予測・最適化する手法が強く求められていました。
アプローチ:研究手法の解明
この課題を解決するため、研究チームはFigure 1に示される体系的なアプローチを取りました。
- データ収集と問題の特定: 実際の振動試験ベンチでオルタネーターの特性評価試験を行い、破壊の原因となった共振周波数(496.17 Hz)を特定しました。
- シミュレーションによる検証: 有限要素法(FEM)を用いたモーダル解析シミュレーションを行い、試験で観測された破壊モードが、ヒートシンクのB+ゾーンにおける局所的な共振モード(シミュレーションでは460.21 Hz)と一致することを確認しました(Figure 5)。
- 実験計画法(DOE): 破壊を回避するため、共振周波数を安全な領域(700 Hz以上)にシフトさせることを目標としました。そのために、設計変更が可能な3つのパラメータ(B+領域の断面積、ボルト穴の厚み、B+ケーブルの重量)を設計変数として設定。ラテン超方格法を用いて60通りの設計案を作成し、それぞれについてモーダル解析シミュレーションを実施しました(Table 2)。
- AIモデルの構築と最適化: 60個の設計データセットを用いて、設計変数から共振周波数を予測する人工ニューラルネットワーク(ANN)モデルを構築しました。このモデルは、極めて高い予測精度を達成しました(Table 3)。その後、遺伝的アルゴリズム(GA)や粒子群最適化(PSO)など6種類の最適化アルゴリズムを用いて、共振周波数を最大化する最適な設計パラメータの組み合わせを探索しました。
ブレークスルー:主要な発見とデータ
本研究により、AIを活用して設計を最適化するアプローチの有効性が明確に示されました。
発見1:破壊原因の正確な特定
振動試験とシミュレーションを組み合わせることで、破壊が496.17 Hzで発生する5次モードの局所共振に起因することを突き止めました(Table 1, Figure 4)。このモードは、ヒートシンクのB+ゾーンに高い応力を発生させていました(Figure 6)。発見2:高精度なAI予測モデルの構築
Levenberg-Marquardtアルゴリズムを用いたANNモデルは、学習データとテストデータの両方で0.999を超える非常に高いR値(決定係数)を示しました(Figure 9)。これは、モデルが未知の設計に対しても共振周波数を正確に予測できることを意味します。発見3:効果的な最適化アルゴリズムの特定
6つの最適化アルゴリズムを比較した結果、AOA、AVOA、EO、GAの4つが、計算速度と精度の両面でこの問題に最も適していることがわかりました(Figure 11, Table 4)。これらのアルゴリズムは、共振周波数を728.9 Hz以上に高める最適な設計案を迅速に見つけ出しました。発見4:最適化結果の妥当性
AIによる最適化で得られた設計値(例:TD1=3.275, TD2=4, TD3=40)を、再度FEM解析で検証したところ、予測値と解析値の誤差は最大でも1.64%と非常に小さく、AIモデルの信頼性が証明されました(Table 5)。
HPDC製品への実践的な示唆
この研究成果は、学術的な興味にとどまらず、実際のHPDC製品の設計・製造現場に直接的な価値をもたらします。
設計エンジニア向け: 本研究で示されたフレームワークは、振動や疲労が懸念されるあらゆる鋳造部品に応用可能です。開発の初期段階でAI予測モデルを用いることで、コストのかかる物理的な試作・試験の回数を大幅に削減し、「テストして壊れる」という手戻りのサイクルを断ち切ることができます。これにより、開発期間の短縮とコスト削減が期待できます。
品質管理向け: Figure 9で示されたAIモデルの予測精度は、設計が品質要件(この場合は動的耐久性)を満たしているかを、金型製作前にデジタル上で検証できることを意味します。これは、品質保証のフロントローディング(前倒し)を実現し、量産段階での不具合リスクを低減します。
金型設計・部品設計向け: この研究は、ボルト穴周りの肉厚やリブの形状といった微細な設計変更が、部品全体の動的性能にどれほど大きな影響を与えるかを定量的に示しています。AIと最適化アルゴリズムを組み合わせることで、経験や勘に頼るのではなく、データに基づいて強度と軽量化を両立する最適な設計を効率的に見つけ出すことが可能になります。
論文詳細
Prevention of the Fracture Problem Occurring in Automotive Alternator Heatsink Blocks Using Artificial Intelligence
1. 概要:
- Title: Prevention of the Fracture Problem Occurring in Automotive Alternator Heatsink Blocks Using Artificial Intelligence
- Author: Dinçer Kökden, Adem Egi, Emre Bulut, Emre İsa Albak, İbrahim Korkmaz and Ferruh Öztürk
- Year of publication: 2024
- Journal/academic society of publication: Applied Sciences
- Keywords: vibration; neural network; heatsink; fracture; fatigue; automotive; crack; regression; optimization
2. Abstract:
本研究では、人工ニューラルネットワークを用いて、自動車用オルタネーターヒートシンクの振動疲労試験における破壊防止について調査した。オルタネーターヒートシンクのような自動車部品は、その寿命を通じて高い周期の振動疲労荷重にさらされ、疲労亀裂の形成と伝播、そして最終的な部品の故障につながる可能性がある。本研究では、形状や荷重条件を含むヒートシンクの共振周波数に影響を与える基本パラメータを特定した。データ駆動型の意思決定は、人工知能アプローチを用いて予測と決定のためのデータを分析する高度な予測的洞察を提供する。振動疲労試験における共振周波数を予測するために、効率的な人工ニューラルネットワークモデルが定義された。人工ニューラルネットワークがパラメータと共振周波数の間の関数関係を確立するために訓練された一方で、回帰分析を用いてヒートシンクの共振周波数を検出する予測モデルが開発された。提案されたアプローチは、自動車用オルタネーターヒートシンクの振動疲労試験における破壊問題を防止するための包括的なフレームワークを提供し、最終的にこれらの重要部品の信頼性の高い設計と性能に貢献することを目指す。人工ニューラルネットワークアプローチは、新しい固有振動数の予測において高い分類精度を達成し、回帰モデルも正確な予測を行うことができた。本研究の結果は、オルタネーター部品の振動試験のような動的試験の前に発生する可能性のある破損問題を防止する上で、設計とシミュレーションに費やす時間を大幅に短縮できることを示した。
3. Introduction:
車両におけるオルタネーターの性能と信頼性は、効果的な熱管理戦略に大きく依存している(Ref. [1-3])。エンジンからの機械的エネルギーを電気エネルギーに変換するオルタネーターは、作動中にかなりの熱を発生させ、適切に対処されないと熱暴走やシステム故障の可能性につながる。熱管理は、オルタネーターから発生する熱を効率的に放散させ、最適な動作温度を維持し、寿命を延ばすため、オルタネーター設計の重要な側面である。オルタネーターヒートシンク設計の基本原則は、熱伝達に利用できる表面積を最大化し、それによって放熱率を高めることである。これは、フィンなどの拡張表面を組み込むことで達成でき、ヒートシンクと周囲の空気との接触面積を増加させる。ヒートシンクの設計を最適化し、熱性能を向上させ、冷却システムの全体的なサイズと重量を削減することに焦点を当てた広範な研究が行われてきた。より良い冷却のために広い表面積で製造されたオルタネーターヒートシンクは、薄い構造で製造されており、そのため、動的荷重を受けると、固有振動数が励振周波数と一致する場合、特定の領域で破損する可能性がある。
4. 研究の要約:
研究トピックの背景:
自動車のオルタネーターヒートシンクは、冷却性能を高めるために薄肉で複雑な形状を持つが、そのためにエンジンの振動に対して脆弱である。特に、部品の共振周波数が車両の動作周波数帯域内にある場合、振動が増幅され、ボルト締結部などの応力集中箇所で疲労破壊が発生する。この問題は、製品開発における手戻りの原因となり、時間とコストを増大させる。
従来の研究の状況:
従来、この種の問題への対処は、物理的な試作品を作成し、振動耐久試験を実施し、破壊が確認された場合に設計を修正するという、反復的なプロセスに依存していた。計算機援用工学(CAE)も利用されてきたが、AI、特に人工ニューラルネットワーク(ANN)を設計最適化プロセスに統合し、破壊を未然に防ぐための予測モデルを構築するアプローチは新しい。
研究の目的:
本研究の目的は、人工知能(AI)と最適化手法を用いて、自動車用オルタネーターヒートシンクの振動疲労による破壊問題を未然に防ぐための包括的なフレームワークを開発することである。具体的には、設計パラメータから共振周波数を高精度で予測するAIモデルを構築し、物理試験の前に設計を最適化することで、開発の時間とコストを大幅に削減することを目指す。
研究の核心:
研究の核心は、(1) 実際の振動試験とFEMシミュレーションによる破壊現象の正確な特定、(2) 設計パラメータ(B+断面積、ボルト穴厚み、ケーブル重量)と共振周波数の関係を学習する高精度な人工ニューラルネットワーク(ANN)モデルの構築、(3) 複数の最適化アルゴリズム(AOA, Aquila, AVOA, EO, GA, PSO)を用いて共振周波数を最大化する最適設計案の探索、という3つのステップにある。このプロセス全体を通じて、物理的な試作を介さずに、デジタル空間で設計の妥当性評価と最適化を完結させることを試みた。
5. 研究方法
研究設計:
本研究は、Figure 1に示される6段階のプロセスで設計されている。
1. データ収集: 振動試験ベンチでオルタネーターの共振周波数を測定。
2. 検証: 試験結果をFEMシミュレーションで再現し、破壊モードを特定。
3. 実験計画(DOE): 設計パラメータを変更した60通りの仮想モデルを作成し、シミュレーションで各々の共振周波数を算出。
4. ANNモデル構築: DOEで得られたデータセットを使い、共振周波数を予測するANNモデルを作成。
5. 最適化: 構築したANNモデルを目的関数として、6種類の最適化アルゴリズムで共振周波数が最大となる設計パラメータを探索。
6. 結果の検証: 最適化された設計を再度FEMシミュレーションで検証し、AIモデルの予測精度を確認。
データ収集と分析方法:
データ収集は、40kNの動電式シェーカーと恒温槽を用いた振動試験によって行われた。100-1000Hzのサインスイープ試験で共振周波数を特定し、100-500Hz、10gの条件で72時間の耐久試験を実施した。データ分析には、FEMソフトウェア(ANSYS 2019 R2)によるモーダル解析と、MATLAB R2024aを用いたANNモデルの構築および最適化計算が用いられた。ANNモデルの性能はR値(決定係数)で評価された。
研究対象と範囲:
研究対象は、自動車用オルタネーターのヒートシンク部品である。特に、振動試験中に破壊が確認されたB+端子周辺のボルト締結部に焦点を当てている。研究の範囲は、ヒートシンクの3つの設計パラメータ(B+領域の断面積、ボルト穴の厚み、B+ケーブルの重量)を変更した場合の、局所的な共振周波数の変化を予測し、最適化することに限定される。
6. 主要な結果
主要な結果:
- 初期の振動試験により、5つの主要な共振モードが特定され、そのうち5番目のモード(496.17 Hz)がB+ゾーンの局所モードであり、耐久試験後の破壊の原因であることが確認された(Table 1, Figure 4)。
- FEMシミュレーションにより、この破壊がB+ゾーンのボルト穴周辺での高い応力に起因することが裏付けられた(Figure 5, Figure 6)。
- 3つの設計パラメータを変更した60通りの設計案についてシミュレーションを行い、共振周波数が515 Hzから720 Hzの範囲で変動するデータセットを作成した(Table 2)。
- このデータセットを用いて構築されたANNモデルは、k-fold交差検証において、すべての分割でR値が0.997以上という非常に高い精度を示した(Table 3, Figure 9)。
- 6種類の最適化アルゴリズム(AOA, Aquila, AVOA, EO, GA, PSO)を実行した結果、PSOを除く5つのアルゴリズムがほぼ同じ最適解(約728.9 Hz)に到達した。特にAOA, AVOA, EO, GAは計算速度と精度のバランスに優れていた(Table 4)。
- 最適化によって得られた設計値は、FEM解析による検証結果との誤差が最大でも1.64%であり、ANNメタモデルの有効性が確認された(Table 5)。
Figure Name List:
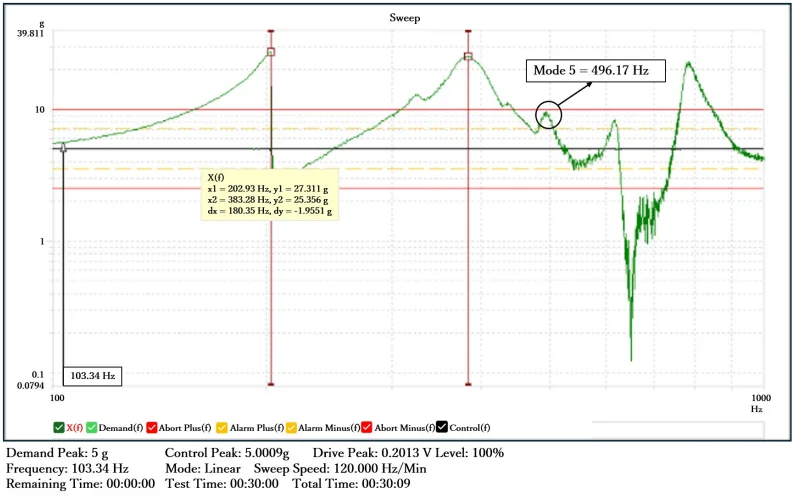
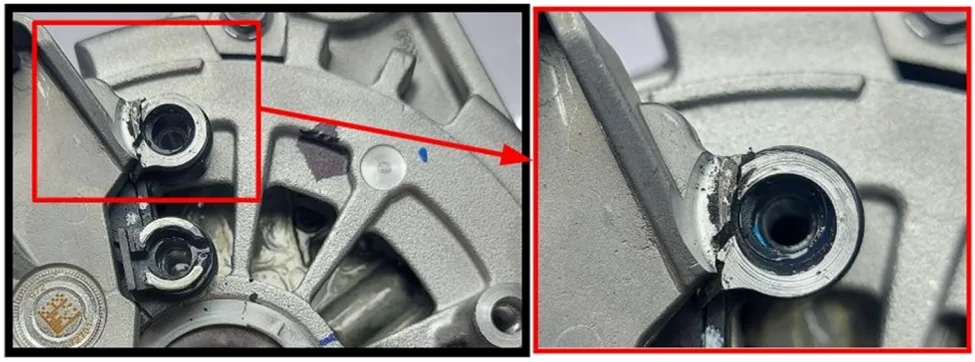
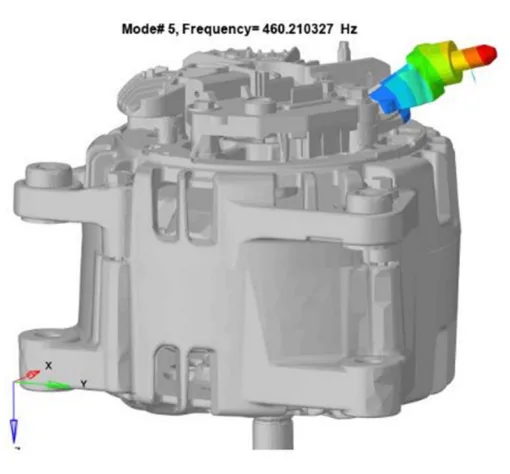
- Figure 1. Flowchart of proposed study.
- Figure 2. Alternator resonance frequency characterization test setup.
- Figure 3. Resonance frequency characterization test results of alternator at Z-axis.
- Figure 4. Heatsink fracture after durability test.
- Figure 5. Alternator heatsink B+ zone local resonance modal shape.
- Figure 6. Alternator heatsink analysis with ANSYS 2019 R2.
- Figure 7. Heatsink modal analysis with ANSYS 2019 R2.
- Figure 8. NN architecture.
- Figure 9. MATLAB R-values.
- Figure 10. MATLAB Simulink prediction model.
- Figure 11. Convergence curves of each optimization algorithm.
- Figure 12. Best convergence curve of each optimization.
7. Conclusion:
本研究は、自動車用オルタネーターヒートシンクの振動疲労による破壊問題を防止するために、人工ニューラルネットワーク(ANN)と最適化手法を統合した効果的なフレームワークを実証した。
1. AIモデルは、部品の共振周波数を高精度で予測でき、これにより、コストと時間のかかる物理的な試作・試験の前に、設計段階で破壊リスクを回避することが可能になる。
2. ANNとMATLAB Simulinkによる回帰モデルは、有限要素解析と比較して計算時間と労力を大幅に削減しつつ、正確な近似値を提供した。
3. 比較した6つの最適化手法のうち、PSOを除く5つが同様の優れた最適解を導き出し、特にAOA, AVOA, EO, GAが本問題に対して適していることが示された。
このアプローチは、設計とシミュレーションに費やす時間を大幅に短縮し、自動車部品開発における繰り返しの破壊問題に対処するための、時間とコストを節約する重要な手法となりうる。
8. References:
- [List the references exactly as cited in the paper, Do not translate and omit.]
専門家Q&A:あなたの疑問にお答えします
Q1: この研究で特定された、ヒートシンクの共振周波数を改善するための最も重要な要因は何でしたか?
A1: この研究では、共振周波数に影響を与える3つの設計変数、すなわち「オルタネーターB+領域の断面積(Td1)」「ボルト穴の厚み(Td2)」「オルタネーターB+ケーブルの重量(Td3)」が重要な要因として特定され、最適化されました。この詳細は論文の「3.1. Design of the Experiment」セクションで述べられており、Table 2のデータで裏付けられています。
Q2: この研究のアプローチは、振動疲労問題に対処する従来の方法とどう違うのですか?
A2: 論文の「1. Introduction」で示唆されているように、従来の方法は物理的な試作品の試験と、破壊後の再設計という反復的なプロセスに依存していました。対照的に、本研究では人工知能(AI)を用いて設計段階で共振周波数を予測・最適化するという新しいアプローチを導入し、物理試験の前に問題を解決することで、開発の時間とコストを大幅に削減できる可能性を示しました。
Q3: この発見は、あらゆる種類の合金に適用可能ですか、それとも特定の合金に限定されますか?
A3: 本研究は、特定の自動車用オルタネーターヒートシンクを対象として行われましたが、使用された材料(合金)については論文中に明記されていません。したがって、この研究で確立された手法(AIと最適化のフレームワーク)は他の部品や材料にも応用可能であると考えられますが、具体的な最適設計値は部品の材料や形状に依存するため、個別のケースでさらなる調査が必要です。
Q4: 研究者たちは、この結論に達するためにどのような特定の測定またはシミュレーション技術を使用しましたか?
A4: 研究者たちは、「2. The Proposed Approach」セクションで説明されているように、物理的な測定には動電式シェーカーを用いた振動試験を、シミュレーションにはANSYSソフトウェアを用いた有限要素法(FEM)によるモーダル解析を利用しました。さらに、予測モデルの構築と最適化にはMATLABの人工ニューラルネットワークツールボックスを使用しました。
Q5: 論文によると、この研究の主な限界や今後の研究課題は何ですか?
A5: 論文の「4. Conclusions」では、直接的な限界については言及されていませんが、このアプローチが「同様の部品の固有振動数を予測できる」と述べており、その汎用性の検証が今後の課題となりうることが示唆されています。また、この研究は特定の部品に焦点を当てているため、異なる形状や材料、荷重条件を持つ他の部品への適用可能性を探ることが今後の研究テーマとなり得ます。
Q6: この論文から、ダイカスト工場が直接得られる実践的な教訓は何ですか?
A6: 最も重要な教訓は、AIとシミュレーションを組み合わせることで、製品の設計段階で動的性能(この場合は耐振動性)を予測し、最適化できるということです。これにより、金型を製作し、物理的なサンプルを鋳造する前に、破壊のリスクを大幅に低減できます。これは、開発サイクルの短縮、コスト削減、そして最終製品の信頼性向上に直結します。この結論は、論文「Prevention of the Fracture Problem Occurring in Automotive Alternator Heatsink Blocks Using Artificial Intelligence」の全体的な結果によって強く裏付けられています。
結論と次のステップ
この研究は、HPDC製品の動的性能を向上させるための貴重なロードマップを提供します。その発見は、品質を向上させ、欠陥を減らし、生産を最適化するための、明確でデータ駆動型の道筋を示しています。
CASTMANでは、最新の業界研究を応用して、お客様の最も困難なダイカストの問題を解決することに専念しています。この論文で議論された課題が貴社の事業目標と共鳴するものであれば、ぜひ当社のエンジニアリングチームにご連絡ください。これらの先進的な原則を貴社の部品にどのように実装できるか、ご相談させていただきます。
著作権
- This material is a paper by "Dinçer Kökden, Adem Egi, Emre Bulut, Emre İsa Albak, İbrahim Korkmaz and Ferruh Öztürk". Based on "Prevention of the Fracture Problem Occurring in Automotive Alternator Heatsink Blocks Using Artificial Intelligence".
- Source of the paper: https://doi.org/10.3390/app142411758
この資料は情報提供のみを目的としています。無断での商業利用は禁じられています。
Copyright © 2025 CASTMAN. All rights reserved.