この論文は、['AU J.T.'発行の「A Comparative Analysis of Grain Size and Mechanical Properties of Al-Si Alloy Components Produced by Different Casting Methods」に基づいて作成されました。
1. 概要:
- タイトル: 異なる鋳造方法で製造されたAl-Si合金部品の結晶粒径と機械的特性の比較分析 (A Comparative Analysis of Grain Size and Mechanical Properties of Al-Si Alloy Components Produced by Different Casting Methods)
- 著者: Abdulkabir Raji
- 発行年: 2010年1月
- 発行ジャーナル/学会: AU J.T. 13(3): 158-164
- キーワード: チル鋳造、微細組織、微細化、砂型鋳造、スクイズ鋳造
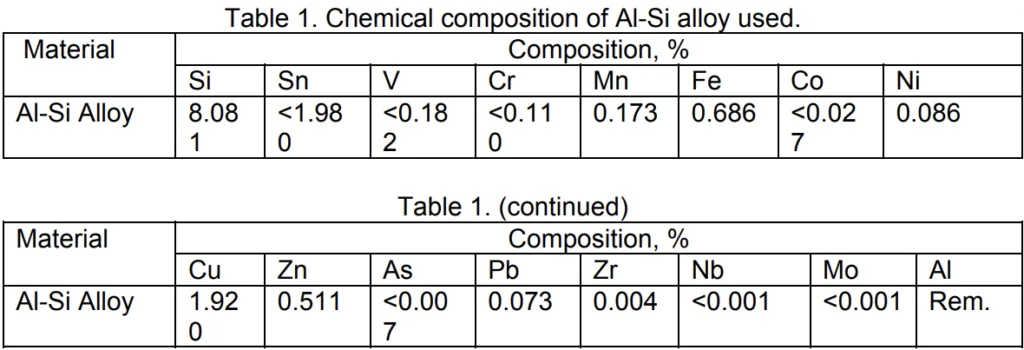
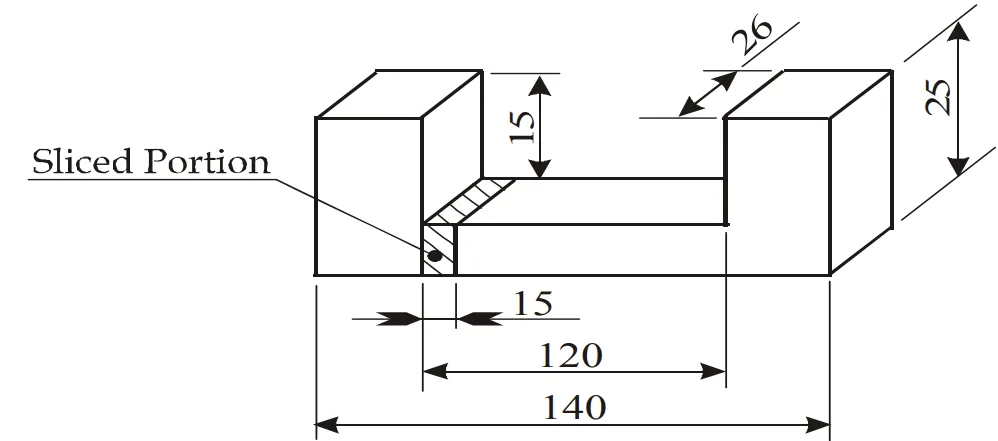
2. 抄録または序論
抄録
本研究は、様々な鋳造方法で製造されたアルミニウムシリコン合金部品の鋳造組織と機械的特性を比較するために実施されました。この目的のために、砂型鋳造、チル鋳造、およびスクイズ鋳造法を用いて、Al-8%Si合金から同じ形状とサイズの同様の製品を製造しました。鋳造品の微細組織の結晶粒径は、スクイズ鋳造、チル鋳造、砂型鋳造の順に大きくなることが観察されました。逆に、鋳造品の機械的特性は、砂型鋳造、チル鋳造、スクイズ鋳造の順に向上しました。したがって、スクイズ鋳造品は、高品質部品を必要とする工学用途において、鋳造肌のままの状態で使用でき、チル鋳造品および砂型鋳造品は、非工学用途またはより低い品質部品を必要とする工学用途において、鋳造肌のままの状態で使用できます。
序論
鋳造または金属鋳造は、紀元前2000年に遡る最も初期の金属成形法の一つであり、当時使用されていたプロセスは、今日使用されているものと原理的にほとんど変わりません(Amstead et al. 1979)。Wright (1990) と Rao (1992) は、金属鋳造はもっと早くから存在していたと考えています。Rao (1992) は紀元前3500年、Wright (1990) は鋳造の起源を約6000年前と見ています。彼はさらに、鋳造における多くの発展は東洋から来たものであり、紀元前1000年以前に中国人は鉄の鋳造方法を開発し、るつぼ鋼の鋳造方法は後にインドで発明されたと指摘しました。東洋の鋳造技術は中東とヨーロッパに輸出され、最初の鋳鉄製大砲は1500年頃にイングランドで製造されました。アメリカで作られた最初の既知の鉄鋳物は、1642年に作られた鋳鉄製調理鍋でした(Jain 1992)。この質素な始まりから、現代の鋳造産業は成長しました。今日、長年にわたって進化してきた数多くの鋳造プロセスが存在します。これらの鋳造プロセスは、一般的に砂型鋳造と特殊鋳造の2つの広範なクラスに分類できます。特殊鋳造には、ダイカスト、重力鋳造、インベストメント鋳造、遠心鋳造、加圧鋳造などが含まれ、それぞれに独自の特徴的な利点と欠点があります。砂型鋳造は、製造される鋳物の約80%を占めています(Mikhailov 1989)。1979年には、英国で製造される鋳物の80%がグリーンサンドモールド(Williams 1979)であり、連邦ドイツでは1986年の鋳造生産量の67%がグリーンサンドモールドであったと推定されています(Weiss and Kleinheyer 1987)。エンジニアリング製品や消費財は、砂型鋳造やダイカストなど、多くの技術によって製造されています。それぞれの代替技術は、独自の明確な能力と関連コストによって特徴付けられ、特定の用途分野を決定します。良好な比較のために、スクイズ鋳造、加圧ダイカスト、チル鋳造、砂型鋳造による製品の製造について検討します。砂型鋳造とスクイズ鋳造の比較を行う中で、Lynch et al. (1975) は、砂型鋳造部品は表面仕上げが粗いものの、砂型鋳造はアンダーカットやチャンネルを部品に鋳込むことができ、多くの小型部品を同時に同じ鋳型で鋳造できるため、生産性が向上するという安価な製造手段を提供すると指摘しました。一方、スクイズ鋳造は、収縮や微細孔のない完全密度の部品と、砂型鋳造よりも滑らかな表面仕上げとより近い公差を実現できます。さらに、高い生産速度と高い金属利用効率により、費用対効果の高い製造プロセスです。スクイズ鋳造で得られる最大重量は、アルミニウム基合金で19kgです(Clegg 1991; Yue and Chadwick 1996)。しかし、チル鋳造で得られる最大重量は、アルミニウム基合金、マグネシウム基合金、鋳鉄、銅基合金でそれぞれ70kg、25kg、13.6kg、9kgです(West and Gruback 1989; Clegg 1991)。Clegg (1991) はまた、スクイズ鋳造と他の類似技術を、表面仕上げ、寸法精度、最小肉厚、生産量の点で比較しました。スクイズ鋳造の表面仕上げは、圧力ダイカストで得られるものと同様で、0.4~3.2µmの範囲であり、チル鋳造で得られるもの(3.2~6.3µmの範囲)よりも優れています。チル鋳造で作られた鋳物の寸法公差または精度は、単一のダイハーフで±0.25mm以内です。重要な寸法が25mm未満の圧力ダイカストの場合、公差は亜鉛基合金で±0.08mm、アルミニウム基合金で±0.10mm、銅基合金で±0.18mmにすることができます。25~300mmの範囲の寸法の場合、上記の3つの合金クラスに対して、25mm増加するごとにそれぞれ±0.025mm、±0.038mm、±0.051mmの追加許容差を設ける必要があります。一方、スクイズ鋳造で作られたアルミニウム合金鋳物の寸法公差は0.2mm/100mmです(Clegg 1991)。チル鋳造の妥当な最小肉厚は5mmですが、亜鉛基合金では0.5mm、アルミニウム基合金では0.8mm、銅基合金では1.5mmの肉厚のセクションを圧力ダイカストで製造できます。スクイズ鋳造は、肉厚が6mmを超える鋳物に適していますが、0.3mmの薄肉セクションもスクイズ鋳造で製造されています(Clegg 1991)。スクイズ鋳造は、他の製造プロセスと比較して比較的新しい鋳造方法であり、多くの利点があります。その1つは、鋳物の微細組織をプロセス制御によって容易に操作して、必要な最適特性を達成できることです。さらに、造核剤も使用できますが、通常は必要ありません(Yue and Chadwick 1996)。Lynch et al. (1975) は、スクイズ鋳造は、微細な結晶粒、狭いデンドライトアーム間隔、および小さな構成粒子を備えた微細組織を持つと述べています。高圧と金属鋳型(ダイ)の複合効果は、高い熱伝達係数をもたらし、それが核生成速度とそれに続く核の成長速度の増加により、微細組織の変化をもたらします。この主張は、Yong and Clegg (2004) によって支持されています。鋳造プロセスを改善するために多くの研究が行われてきたという事実にもかかわらず、プロセスのより良い理解のためには、プロセスに関するさらなる研究が必要です。本研究は、砂型鋳造、チル鋳造、スクイズ鋳造法によって鋳造されたアルミニウムシリコン合金部品の結晶粒径と機械的特性を比較するために実施されました。
3. 研究背景:
研究トピックの背景:
金属鋳造、別名鋳造は、最も初期の金属成形法の一つです。紀元前2000年頃に起源を持つ鋳造の基本的な原理は、数千年以上にわたって一貫しています。現代の鋳造技術は、数多くの鋳造プロセスに拡大しており、大きく砂型鋳造と特殊鋳造に分類されます。特殊鋳造法には、ダイカスト、重力鋳造、インベストメント鋳造、遠心鋳造、加圧鋳造などがあり、それぞれに独自の利点と欠点があります。砂型鋳造は広く使用されている方法であり、総鋳造生産量の約80%を占めています。
既存研究の現状:
エンジニアリング製品や消費財は、砂型鋳造やダイカストなどの様々な技術を用いて製造されています。各技術は、明確な能力とコストプロファイルを持ち、特定の用途分野を決定します。先行研究では、砂型鋳造とスクイズ鋳造を比較しています。Lynch et al. (1975) は、砂型鋳造は表面仕上げが粗いものの、複雑な形状に適した費用対効果の高い製造方法を提供すると指摘しました。対照的に、スクイズ鋳造は、表面仕上げと寸法公差が向上した完全密度の部品を生成します。Clegg (1991) および Yue and Chadwick (1996) は、アルミニウム基合金のスクイズ鋳造で得られる最大重量を19kgと強調しています。
研究の必要性:
鋳造プロセスを改善するための広範な研究が行われてきたにもかかわらず、より包括的な理解のためには、さらなる調査が必要です。特に、異なる鋳造方法間の結晶粒径と機械的特性に焦点を当てた比較研究が必要です。本研究は、砂型鋳造、チル鋳造、およびスクイズ鋳造がアルミニウムシリコン合金部品の微細組織と機械的特性に及ぼす影響を比較するために設計されています。
4. 研究目的と研究課題:
研究目的:
主な研究目的は、砂型鋳造、チル鋳造、およびスクイズ鋳造法を用いて製造されたアルミニウムシリコン合金部品の微細組織の結晶粒径と機械的特性の比較分析を実施することです。
主な研究内容:
主な研究内容は、以下の評価と比較に焦点を当てています。
- 砂型鋳造、チル鋳造、およびスクイズ鋳造に起因するAl-Si合金微細組織における結晶粒径の変動。
- 3つの鋳造方法のそれぞれによって製造されたAl-Si合金部品の機械的特性、具体的には硬さ、引張強さ(UTS)、耐力、および伸び。
研究仮説:
本研究は、暗黙のうちに以下の仮説を立てています。
- スクイーズ鋳造は、Al-Si合金部品の微細組織において最も微細な結晶粒径をもたらし、次いでチル鋳造、そして最も粗い結晶粒径を示す砂型鋳造となる。
- 硬さ、UTS、耐力、および伸びを含む機械的特性は、スクイズ鋳造部品で最も優れており、次いでチル鋳造部品、砂型鋳造部品が最も低い機械的特性を示す。
5. 研究方法
研究デザイン:
本研究では、比較実験デザインを採用しました。アルミニウムシリコン合金部品は、砂型鋳造、チル鋳造、およびスクイズ鋳造の3つの異なる鋳造方法を用いて製造されました。次に、鋳造部品の得られた微細組織と機械的特性を比較しました。
データ収集方法:
- 材料準備: Al-Si合金スクラップを利用し、その組成をエネルギー分散型X線蛍光分析(EDXRF)および古典的な湿式分析を用いて検証しました。
- 鋳造プロセス: 砂型鋳造、チル鋳造、およびスクイズ鋳造は、指定された注湯温度で、スクイズ鋳造の場合は様々なスクイズ圧力(75MPa、100MPa、125MPa、150MPa)を用いて実施されました。Raji and Khan (2005; 2006) によって概説された方法に従って、鋳造パラメータを制御しました。
- 金属組織学的検査: 試料は、切断、研磨、研削、および0.24%フッ化水素酸(HF)によるエッチングによって調製されました。微細組織は、Pol Jenalab光学顕微鏡を用いて125倍の倍率で観察および撮影されました。
- 機械試験: 引張試験は、万能試験機を用いて実施し、硬さは、Raji and Khan (2006) によって概説された手順に従って、ロックウェル硬さ試験機を用いて測定しました。
分析方法:
- 定量的な結晶粒径分析: 結晶粒径は、米国試験材料協会(ASTM)結晶粒径番号(n)を用いて定量的に評価され、特定の倍率での結晶粒数に基づいて計算された式を用いて計算されました。
- 機械的特性の比較分析: 硬さ、UTS、耐力、および伸びについて得られたデータは、表にまとめられ、異なる鋳造方法およびプロセスパラメータ(注湯温度、スクイズ圧力)間で比較されました。統計分析は、傾向と差異を示すために表にデータを提示することによって暗黙的に使用されました。
研究対象と範囲:
- 材料: アルミニウムシリコン(Al-Si)合金、具体的にはAl-8%Si合金。
- 鋳造方法: 砂型鋳造、チル鋳造、およびスクイズ鋳造。
- プロセスパラメータ: 注湯温度(砂型鋳造の場合は650℃、700℃、750℃、800℃、チル鋳造およびスクイズ鋳造の場合は650℃、700℃、750℃)、スクイズ圧力(スクイズ鋳造の場合は75MPa、100MPa、125MPa、150MPa)。
- 範囲: 本研究は、これらの3つの鋳造方法を特定のAl-Si合金で比較し、結晶粒径と選択された機械的特性の評価に限定されています。
6. 主な研究結果:
主な研究結果:
- 結晶粒径: 微細組織分析により、結晶粒径はスクイズ鋳造 < チル鋳造 < 砂型鋳造の順に大きくなることが明らかになりました。スクイズ鋳造品は最も微細な結晶粒を示し、砂型鋳造品は最も粗い結晶粒を示しました。スクイズ鋳造におけるスクイズ圧力を上げると、結晶粒径が微細になりました。
- 硬さ: スクイーズ鋳造部品は、チル鋳造品よりも43〜47%高いHRF58.0までの最高の硬さ値を示しました。チル鋳造品は砂型鋳造品よりも硬度が高かった。砂型鋳造品は最も低い硬度を示し、HRF33.0からHRF35.5の範囲でした。
- 引張強さ(UTS): スクイーズ鋳造品は、温度と圧力に応じて146〜232 MPaの範囲で最高のUTSを示しました。チル鋳造品のUTSは約115 MPaでした。砂型鋳造品は最も低いUTSを示し、65〜102 MPaの範囲でした。
- 耐力: 耐力の傾向はUTSの傾向を反映しており、スクイーズ鋳造品が最も高く、次いでチル鋳造品、砂型鋳造品の順でした。
- 伸び: スクイーズ鋳造品は最も高い伸び率(3.4〜3.8%)を示し、次いでチル鋳造品(2.4〜2.7%)、砂型鋳造品(2.0〜2.3%)の順でした。
提示されたデータの分析:
表2は、様々な鋳造方法で製造されたアルミニウムシリコン合金の特性を示しています。砂型鋳造からチル鋳造、そしてスクイズ鋳造へと鋳造方法が変化するにつれて、ASTM結晶粒径番号(n*)が増加し、結晶粒径が微細になる明確な傾向を示しています。逆に、UTS、耐力、および硬さの値は同じ順序で増加し、スクイズ鋳造によって達成されたより微細な結晶粒組織で機械的特性が向上していることを示しています。伸びも同様の傾向を示していますが、それほど顕著ではありません。
データは、砂型鋳造(スクイズ圧力0 MPa)の場合、注湯温度を650℃から800℃に上げると、結晶粒の微細化(n*の低下)とUTS、耐力、および硬さの低下につながることを示しています。
スクイーズ鋳造の場合、スクイズ圧力を上げると、一般的に結晶粒径が微細になり(n*の増加)、機械的特性が向上します。ただし、注湯温度の範囲(650℃〜750℃)内での影響は、スクイズ圧力の大きな影響と比較して一貫性がありません。
図2〜5は、結晶粒径の違いを視覚的に確認しています。図2(砂型鋳造)、図3(チル鋳造)、図4および5(スクイズ鋳造)は、125倍の倍率での顕微鏡写真を示しています。顕微鏡写真は、砂型鋳造品は結晶粒が粗く(図2)、チル鋳造品は結晶粒が微細で(図3)、スクイーズ鋳造品は最も微細な結晶粒組織を示すことを示しています(図4および5)。白いパッチはアルミニウム(α)中の一次α固溶体を表し、黒いパッチは共晶(α+Si)を表します。
図のリスト:
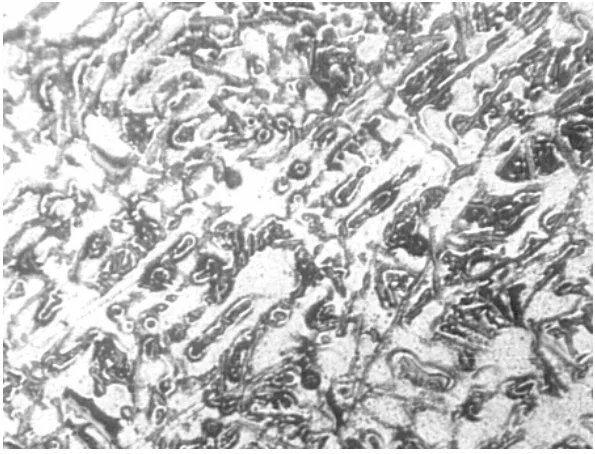
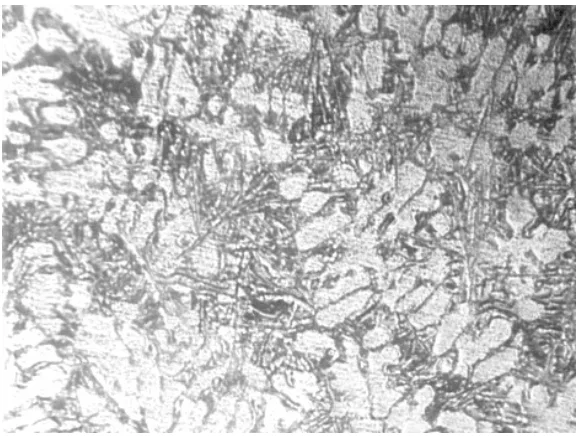
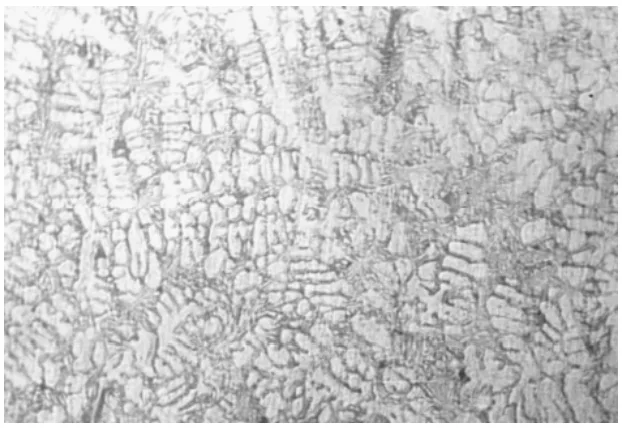
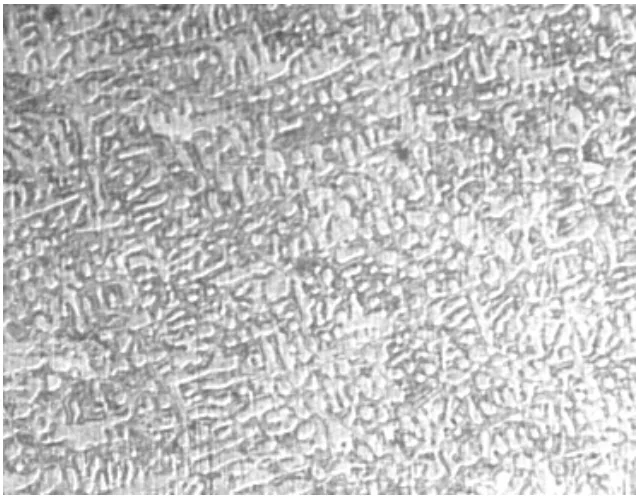
- 図 1. 金属組織試験用の鋳物のスライス部分。寸法はmm単位。
- 図 2. 注湯温度700℃(125倍)でのAl-8%Si合金砂型鋳造の顕微鏡写真。白いパッチは一次α、黒いパッチは共晶α+Si。
- 図 3. 注湯温度650℃(125倍)でのAl-8%Si合金チル鋳造の顕微鏡写真。白いパッチは一次α、黒いパッチは共晶α+Si。
- 図 4. 注湯温度650℃、スクイズ圧力100MPa(125倍)でのAl-8%Si合金スクイズ鋳造の顕微鏡写真。白いパッチは一次α、黒いパッチは共晶α+Si。
- 図 5. 注湯温度750℃、スクイズ圧力125MPa(125倍)でのAl-8%Si合金スクイズ鋳造の顕微鏡写真。白いパッチは一次α、黒いパッチは共晶α+Si。
7. 結論:
主な調査結果の要約:
本研究では、以下の結論が得られました。
- 鋳物の微細組織は、砂型鋳造、チル鋳造、スクイズ鋳造の順に微細度が増加します。
- 一般的に、スクイズ鋳造の機械的特性は、チル鋳造および砂型鋳造よりも高く、砂型鋳造の機械的特性が最も低くなります。
- スクイーズ鋳造は、チル鋳造および砂型鋳造と比較して、スクイーズ鋳造の機械的特性を大幅に向上させます。
- 砂型鋳造は、非工学用途および低い機械的特性が要求される工学用途において、鋳造肌のままの状態で使用できます。チル鋳造およびスクイズ鋳造は、中程度から高い機械的特性が要求される工学用途において、鋳造肌のままの状態で利用できます。
研究の学術的意義:
本研究は、異なる鋳造方法がAl-Si合金の微細組織と機械的特性にどのように影響するかについての基本的な理解に貢献します。砂型鋳造、チル鋳造、およびスクイズ鋳造の比較性能に関する定量的なデータを提供し、チル鋳造およびスクイズ鋳造に関連するより高い冷却速度が結晶粒の微細化と機械的特性の向上につながるという確立された知識を強化します。本研究は、Al-Si合金において優れた材料特性を達成するためのスクイズ鋳造の有効性を検証します。
実際的な意義:
調査結果は、エンジニアや製造業者がAl-Si合金部品の望ましい性能特性に基づいて適切な鋳造方法を選択するための実際的な指針を提供します。優れた機械的特性を備えた高品質部品を必要とする用途には、スクイズ鋳造が好ましい方法です。チル鋳造は、砂型鋳造よりも優れた特性のバランスを提供し、中程度の性能用途に適している場合があります。砂型鋳造は、低い機械的特性が許容されるコスト重視の用途にとって、依然として実行可能な選択肢です。
研究の限界と今後の研究分野:
本研究は、Al-8%Si合金と特定の範囲の鋳造パラメータに限定されています。今後の研究では、以下を検討できます。
- これらの鋳造方法の比較性能に対する、より広範囲の合金組成の影響。
- 特定のAl-Si合金の機械的特性を最大化するためのスクイズ鋳造パラメータ(圧力、温度、速度)の最適化。
- これらの鋳造方法で製造された部品の疲労強度や衝撃靭性などの他の機械的特性の調査。
- 包括的な方法選択ガイドを提供するための、各鋳造方法の経済分析(製造コストと達成可能な機械的特性を考慮)。
8. 参考文献:
- Amstead, B.H.; Ostwald, P.F.; and Begeman, M.L. 1979. Manufacturing processes. 7th ed., John Wiley and Sons, New York, NY, USA.
- Askeland, D.R. 1985. The science and engineering of materials. PWS Publishing Co., Boston, MA, USA.
- Clegg, A.J. 1991. Precision casting processes. Pergamon Press PLC, Oxford, UK.
- Jain, P.L. 1992. Principles of foundry technology. 3rd ed., Tata Mc Graw-Hill Publishing Co., Ltd., New Delhi, India.
- Lynch, R.F.; Olley, R.P., and Gallagher, P.C.J. 1975. Squeeze casting of brass and bronze. Paper No.75-90. AFS Trans. 83: 561-8.
- Mikhailov, A.M. 1989. Metal casting. Mir Publishers, Moscow, USSR.
- Raji, A.; and Khan, R.H. 2005. Effect of pouring temperature on the properties of Al-8%Si alloy sand cast components. Global J. Engin. Res. 4(1&2): 1-4.
- Raji, A.; and Khan, R.H. 2006. Effects of pouring temperature and squeeze pressure on the properties of Al-8%Si alloy squeeze cast components. AU J.T. 9(4): 229-37, April.
- Rao, P.N. 1992. Manufacturing technology: Foundry, forming and welding. Tata McGraw-Hill Publishing Co., Ltd., New Delhi, India.
- Weiss, R.; and Kleinheyer, U. 1987. Current trends in the use of moulding and core making processes. Casting Plant Technol. 3(4): 10-9.
- West, C.E.; and Gruback, T.E. 1989. Permanent mold casting. In: ASM. 1989. Metals handbook (Casting). vol. 15, pp. 275-85, ASM, Metal Park, OH, USA.
- Williams, R. 1997. The present status and future of green sand in the foundry industry. The British Foundryman 72(6, Special Supplement): 53-62.
- Wright, R.T. 1990. Manufacturing systems. The Goodheart-Willcox Co., Inc., Tinley Park, IL, USA.
- Yong, M.S.; and Clegg, A.J. 2004. Process optimisation for a squeeze cast magnesium alloy. J. Materials Process. Technol. 145(1): 134-41, January.
- Yue, T.M.; and Chadwick, G.A. 1996. Squeeze casting of light alloys and their composites. J. Materials Process. Technol. 58(2-3): 302-7, March.
9. 著作権:
- この資料は、"Abdulkabir Raji"氏の論文:「A Comparative Analysis of Grain Size and Mechanical Properties of Al-Si Alloy Components Produced by Different Casting Methods」に基づいています。
- 論文ソース: https://www.ajol.info/index.php/ajt/article/view/54637
この資料は上記の論文に基づいて要約されたものであり、商業目的での無断使用は禁止されています。
Copyright © 2025 CASTMAN. All rights reserved.