本紹介は、『International Journal of Engineering Research & Technology (IJERT)』に掲載された論文「Optimization of Runner Design in Pressure Die Casting」を基に作成されています。
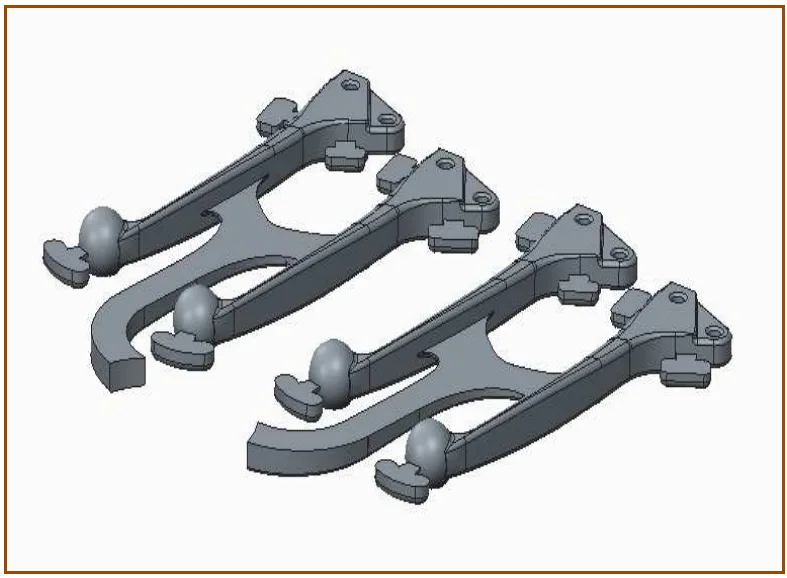
1. 概要
- 論文名: Optimization of Runner Design in Pressure Die Casting (圧力ダイカストにおけるランナー設計の最適化)
- 著者: Nair Akhil K. Raveendran, Prof. Amol N. Patil
- 発行年: 2017年
- 発行学術誌/学会: International Journal of Engineering Research & Technology (IJERT)
- キーワード: Runner (ランナー), Gate (ゲート), High pressure die casting (高圧ダイカスト), Fill time (充填時間)
2. 要旨
高圧ダイカストで高品質な部品を製造するため、コンピュータ支援シミュレーションが金型設計の最適化に用いられてきました。有限差分法、有限体積法、有限要素法が充填プロセスシミュレーションで使用され、一般的な問題に対して大きな進展が見られました。しかし、特定の課題に対処するための金型設計の最適化については、さらなる研究が望まれています。ダイカストでは、金型が同一または異なる部品を製造するための複数のキャビティを持つことがよくあります。複数のキャビティには、主ランナーに接続する分岐ランナーの適用が必要です。複数のキャビティが同時に充填を開始し、同じ充填時間を確保することが設計者にとって重要であるため、ランナーシステムの設計は常にダイカストの重要課題でした。設計における重要な要素は、キャビティの体積に応じて各分岐ランナーの断面積を調整することですが、これだけではキャビティを同時に充填するには不十分な場合があります。分岐ランナーと主ランナーの間の角度が充填圧力、充填時間、残留応力に影響を与えることが観察されていますが、これらの観察は実用的な鋳造品ではなく、非常に単純な実験室レベルの金型設計に限定されていました。
3. 緒言
ダイカストは、ダイカストマシンの射出システムからの油圧エネルギーを溶湯に加えて運動エネルギーを伝え、金型キャビティを高速で充填するプロセスです。本論文は、コールドチャンバー高圧ダイカストのランナーにおける問題、特に不正確に設計された湯口システムが製品にジェットマークを引き起こす問題を取り扱います。溶湯のジェッティングはランナー壁の溶損につながり、長期間の生産稼働後には、この摩耗が局部的な窪みを形成し、さらに湯の流れ方向を変化させます。この問題には、ランナー側壁の摩耗を最小限に抑えるため、ランナー側壁でのジェッティングがほとんど、あるいはまったくない溶湯の流れを作り出すようにランナーを設計する解決策が必要です。本論文では、ダイカスト設計プロセスにおける重要なツールであるP-Q²線図を利用して、プロセスパラメータの操作ウィンドウを決定します。
4. 研究の概要
研究テーマの背景
高圧ダイカストにおける高品質な部品は、最適な金型設計に大きく依存します。複数のキャビティを持つ金型の場合、すべてのキャビティが同時に均一に充填されるように、ランナーシステムが非常に重要です。不適切に設計されたランナーは、欠陥、生産コストの増加、金型の摩耗を引き起こす可能性があります。
先行研究の状況
コンピュータ支援シミュレーションは、金型設計を最適化するために広く使用されてきました。先行研究では、分岐ランナーと主ランナーの間の角度のような要因が充填圧力と時間に影響を与えることが示されています。しかし、これらの観察は、しばしば単純な実験室レベルの設計に限定されていました。本研究は、実用的で多キャビティの工業部品に数値流体力学(CFD)法を適用することにより、既存の知識を基に構築されています。また、ゲーティングシステムに関するHermanの設計手法や、Ref.で述べられているようなプロセスパラメータ最適化のためのP-Q²線図の使用など、確立された設計手法を参照しています。
研究の目的
本研究の主な目的は、高圧ダイカスト金型のランナー設計を最適化し、ジェットマークなどの製品欠陥をなくすことでした。この研究は、ランナー側壁でのジェッティングを最小限に抑え、溶損を防ぎ、金型キャビティの完全な充填を保証し、最終的に鋳造部品の不良率を低減するランナーを設計することを目的としました。
研究の核心
研究の核心は、欠陥部品を生産していた既存のクラッチレバー用金型を分析するためにCFDシミュレーションを使用したことです。この分析により、不均一な充填が凝固欠陥やジェットマークを引き起こす充填パターンの問題が特定されました。この分析に基づき、ランナー設計はファンタイプからタンジェンシャルタイプに変更されました。その後、この新しい設計をシミュレーションおよび分析し、スムーズな充填の実現、ポロシティの低減、欠陥の除去における有効性を検証しました。
5. 研究方法
研究設計
本研究は比較分析手法に従いました。まず、4キャビティのクラッチレバー用の既存の金型設計を分析し、その欠陥を理解しました。続いて、修正されたランナー設計が開発され、シミュレーションが行われました。そして、修正された設計の性能を、主要な鋳造パラメータを評価することによって元々の設計と比較し、改善点を検証しました。
データ収集・分析方法
本研究では、主に数値流体力学(CFD)シミュレーションを用いて鋳造プロセスを分析しました。充填時間、凝固、インゲート速度、金型溶損、エア巻き込み、コールドシャットなどのパラメータが考慮されました。分析では、ファンタイプやタンジェンシャルタイプを含むさまざまなランナーの繰り返し計算結果を解析ソフトウェアを使用して比較し、最も適した設計を決定しました。
研究の対象と範囲
本研究は、クラッチレバーを生産する4キャビティの高圧ダイカスト(HPDC)金型のランナーシステムの最適化に焦点を当てています。研究範囲には、キャビティのスムーズな充填を実現し、製品欠陥を減らし、全体的な鋳造品質を向上させるためのランナーの軌道と方向変化の分析が含まれます。
6. 主な結果
主な結果
CFD解析により、ランナーをファンタイプからタンジェンシャルタイプに変更することで、溶湯の流れが金型と製品に与える悪影響をうまく低減できることが実証されました。この変更により、鋳造品のジェットマークが大幅に減少しました。その結果、溶湯が早期に凝固することなく金型を完全に充填するため、不良率が低下しました。また、解析により、新しい設計では前の繰り返し計算と比較してポロシティが減少したことも確認されました。ジェットマークがなくなったため、研磨などの後処理作業の必要性もなくなりました。
図のリスト
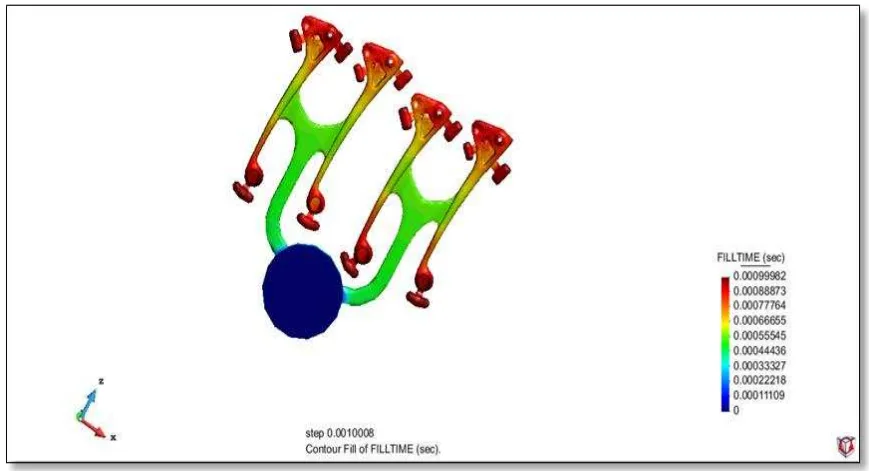
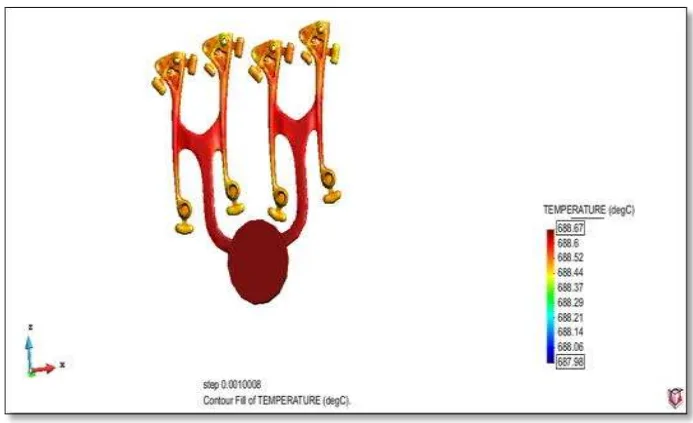
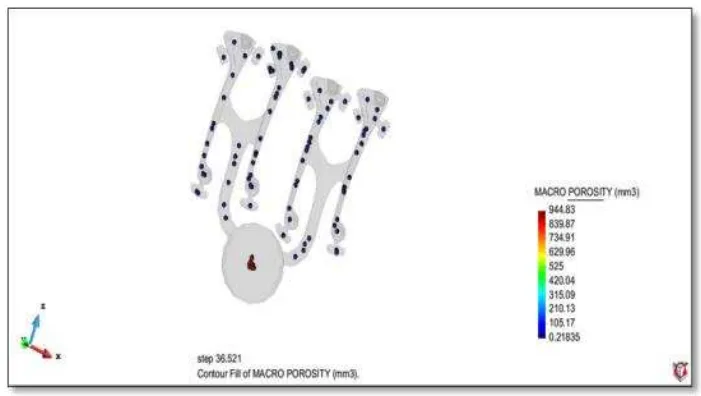
- Fig. 1. Runner System of the Modified Design
- Fig. 2. Filling Time of the Modified Design
- Fig. 3. Temperature of molten metal in Modified Design
- Fig. 4. Porosity in runner system of Modified Design
7. 結論
CFD解析により、ランナーをファンランナーからタンジェンシャルランナーに変更することで、金型と製品への流れの影響が低減されることがわかりました。金型と製品にジェットマークが発生する可能性が低くなりました。溶湯が金型を完全に充填するようになり、不良率が減少しました。また、最初の繰り返し計算と比較してポロシティも減少しました。ジェットマークが減少したため、研磨のような製品の後処理は不要となりました。
8. 参考文献
- B. Vijaya Ramnath et al. (2014), Analysis and Optimization of Gating System for Commutator End Bracket, Procedia Materials Science 6 (2014) 1312–1328
- Marco Antonio Pego Guerr, Die Casting Design – A Parametric Approach, Thesis submitted to Ottawa-Carleton Institute for Mechanical and Aerospace Engineering (1997)
- P.R.Vispute, D.S.Chaudhari, Swapnil Kulkarni, Utilizing Flow Simulation In The Design Phase Of A Die Casting Die To Optimize Design Parameters While Validating Through Experimentation During Trials, International Journal of Scientific Research and Management Studies (IJSRMS) ISSN: 23493771 Volume 1 Issue 8, pg: 263-269
- Shaik Riyaz Ahmed, K.Devaki Devi and S.V.S. Himathejeswini, Design & Analysis of Heat Sink High-Pressure Die Casting Component, International Journal of Current Engineering and Technology, Vol.6, No.5 (Oct 2016)
- Tuula Höök, Tampere University of Technology, HPDC runner and gating system design, CAE Mould Design.
9. 著作権
- 本資料は、Nair Akhil K. Raveendran, Prof. Amol N. Patilによる論文です。「Optimization of Runner Design in Pressure Die Casting」に基づいています。
- 論文の出典: http://www.ijert.org
本資料は上記の論文を基に要約したものであり、商業目的での無断使用を禁じます。
Copyright © 2025 CASTMAN. All rights reserved.
論文要約
研究に関する主な質疑応答
本研究は、ランナーシステムを最適化することにより、高圧ダイカストにおけるジェットマークや高い不良率といった欠陥を解決することを目的としました。CFD解析を用いて、クラッチレバー部品のランナー設計をファンタイプからタンジェンシャルタイプに変更することで、溶湯の流れが改善されることを実証しました。この新しい設計は、完全かつ均一な金型充填を保証することで、ジェットマークをなくし、ポロシティを低減し、部品の不良率を減少させることに成功しました。
Q1. 本論文で議論されている既存のダイカストプロセスの主な問題点は何でしたか?
A1. 主な問題点は、コールドチャンバー高圧ダイカスト金型の不正確に設計された湯口システムであり、これがジェッティング、ランナー壁の溶損、金型の不完全充填、そして最終製品のジェットマークを引き起こし、高い不良率につながっていました。(出典:「Optimization of Runner Design in Pressure Die Casting」、緒言および設計と解析のセクション)。
Q2. この問題を解決するために、どのような具体的な設計変更が実施されましたか?
A2. 溶湯の流れが金型と製品に与える乱流の影響を低減するため、ランナーの設計がファンランナーからタンジェンシャルランナーに変更されました。(出典:「Optimization of Runner Design in Pressure Die Casting」、結論)。
Q3. 新しい設計を評価するために、どのような方法論が用いられましたか?
A3. 数値流体力学(CFD)シミュレーションを用いて、既存のランナー設計と修正されたランナー設計の性能を比較分析し、充填時間、ポロシティ、温度分布といったパラメータに焦点を当てました。(出典:「Optimization of Runner Design in Pressure Die Casting」、設計と解析のセクション)。
Q4. 新しいランナー設計は充填時間に影響を与えましたか?
A4. はい、修正されたタンジェンシャルランナーでの充填時間は0.00099982秒であり、以前のファンゲートランナーと比較してわずかに増加しましたが、大幅な変化ではなく、プロセスに悪影響は与えませんでした。(出典:「Optimization of Runner Design in Pressure Die Casting」、Figure 2とその周辺のテキスト)。
Q5. 修正された設計は、欠陥の観点から製品品質にどのような影響を与えましたか?
A5. 修正された設計により、ポロシティが減少し、製品上の目に見えるジェットマークがなくなり、溶湯が金型を完全かつ均一に充填することが保証され、部品の不良率が大幅に減少しました。(出典:「Optimization of Runner Design in Pressure Die Casting」、結論および3ページのテキスト)。
Q6. 最適化された設計で作られた製品には、後処理が必要でしたか?
A6. いいえ、改善されたランナー設計によってジェットマークがなくなったため、研磨のような後処理工程はもはや不要となりました。(出典:「Optimization of Runner Design in Pressure Die Casting」、結論)。