この論文の紹介は、[「Manufacturing Processes of Car Alloy Wheels」]([「HAL open science」]発行)に基づいて作成されました。
1. 概要:
- タイトル: Manufacturing Processes of Car Alloy Wheels
- 著者: Mohsen Soori
- 発行年: 2022年
- 発行ジャーナル/学会: HAL open science (プレプリント)
- キーワード: Alloy wheels, Casting, CNC machining operations, Finite Element Method, Optimization
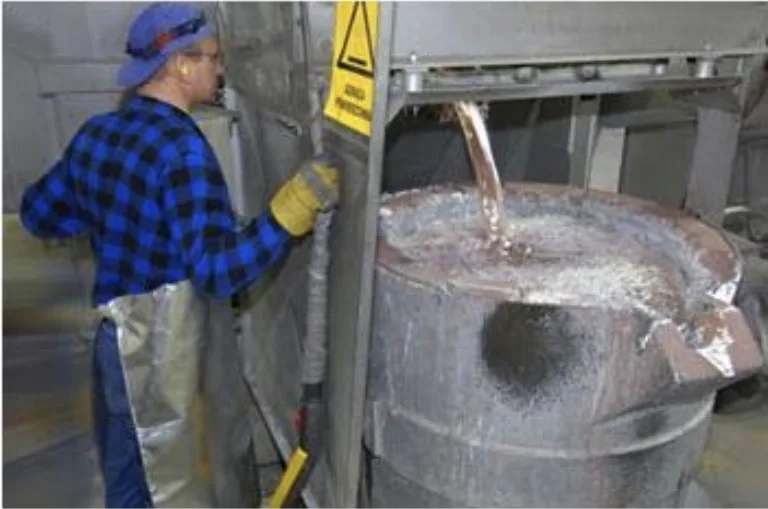
2. 概要
乗用車は、燃料消費量を削減するために、より軽量なホイールである合金ホイールを使用しています。合金ホイールは通常、アルミニウムやマグネシウムなどの軽量で強力な合金で作られており、運転の安全性を高めるためにブレーキシステムの性能を向上させることができます。合金ホイールは、鋳造、機械加工、鍛造の各工程を経て製造されます。製造プロセスを分析・修正することで、部品生産の効率を高めることができます。有限要素解析(Finite Element Analysis)は、実際の作業条件下でのホイールの静的および動的応力を特定するために使用できます。旋盤などの工作機械を使用した機械加工プロセスも、分析・修正することができます。最適化プロセスは、製造された合金ホイールの剛性を高めるために使用できます。新しい合金特性は、合金ホイールの性能を向上させるために、仮想シミュレーションを使用してテストできます。製造部品の品質を向上させるために、低圧ダイカストによる合金ホイールの製造プロセスにおける熱モデルが分析されます。これにより、合金ホイールの製造プロセスにおける付加価値を高めることができます。
キーワード: Alloy wheels, Casting, CNC machining operations, Finite Element Method, Optimization
3. 研究背景:
研究トピックの背景:
自動車産業における燃費向上の追求は、乗用車への合金ホイールの採用を推進してきました。これは主に、鋼製ホイールと比較して軽量であることが理由です。これらの合金ホイールは、通常、アルミニウムやマグネシウムなどの軽量で堅牢な材料で構成されており、燃費の向上に貢献するだけでなく、ブレーキシステムの性能も向上させ、運転の安全性を高めます。合金ホイールの製造には、鋳造、機械加工、鍛造などの主要な工程が含まれます。
既存研究の現状:
合金ホイール製造における現在の研究は、部品生産の効率を最大化するために、生産プロセスを分析および改良することに重点を置いています。有限要素解析(FEA)は、運転条件下でのホイール内の静的および動的応力を評価するために使用されています。旋盤工作機械を利用した機械加工工程は、最適化のために分析および修正の対象となります。さらに、最適化手法は、製造された合金ホイールの剛性を高めるために適用されています。仮想シミュレーションは、新しい合金特性を評価し、ホイール全体の性能を向上させるために利用されています。低圧ダイカストプロセスの熱モデリングも、製造部品の品質を向上させるために調査されています。
研究の必要性:
この研究は、合金ホイール製造における効率と品質の向上に対する継続的な要求によって必要とされています。既存の製造方法論を分析および修正することにより、性能、安全性、構造的完全性などの重要な側面に対処し、合金ホイールの製造プロセスにおける付加価値を高めることを目的としています。
4. 研究目的と研究課題:
研究目的:
本研究の主な目的は、合金ホイールの製造プロセスに関する包括的な概要を示し、これらの製造技術の進歩と最適化を目的とした最近の研究努力を分析することです。
主な研究:
本稿では、合金ホイールの製造開発に関する最近の学術研究をレビューし、以下の主要分野に焦点を当てています。
- Computer Simulation of Casting Process of Aluminum Wheels
- Casting defects in low-pressure die-cast aluminum alloy wheel
- Process capability improvement for aluminum alloy wheel machining
- Analysis of Static Stress in an Alloy Wheel of the Passenger car
- Optimization of Rigidity of Aluminum Alloy Wheels
- Analysis of Alloy properties for the Manufacture of Automotive Wheels
- Simulation of Inner Rim Compression Test of Aluminum Alloy Wheels
- Analysis of the forging processes for 6061 aluminum-alloy wheels
- Development of a 3-D thermal model of the low-pressure die-cast (LPDC) process of A356 aluminum alloy wheels
- Precision forging technology for aluminum alloy
- Finite element simulation and experimental validation of the cracking phenomenon in aluminum alloy wheels
- Effect of Cooling Process on Porosity in the Aluminum Alloy Automotive Wheel During Low-Pressure Die Casting
研究仮説:
明示的に正式な仮説として述べられていませんが、レビューされた研究は、FEA、熱モデリング、最適化アルゴリズムなどの高度な分析およびシミュレーション技術の適用が、鋳造や機械加工から鍛造や品質管理まで、さまざまな段階にわたる合金ホイールの製造プロセスの改善に大きく貢献できるという前提を暗黙のうちに調査しています。
5. 研究方法
研究デザイン:
本研究では、文献レビューデザインを採用し、自動車用合金ホイールの製造プロセスに関連する既存の研究論文を体系的に調査および統合します。
データ収集方法:
このレビューのデータは、合金ホイール製造技術に焦点を当てた査読付きジャーナル記事、会議議事録、および学術出版物の包括的な検索と分析を通じて収集されました。
分析方法:
採用された分析方法は、記述的要約です。選択された各研究論文を分析および要約して、主要な調査結果、方法論、および結論を抽出します。次に、要約を統合して、この分野における最近の進歩と傾向の概要を提供します。
研究対象と範囲:
研究対象は、鋳造、機械加工、鍛造、材料特性、プロセス最適化、欠陥分析など、合金ホイール製造のさまざまな側面を網羅しています。範囲は、合金ホイールの生産プロセスを強化することを目的とした研究開発活動に限定されており、主にアルミニウム合金および関連する製造技術に焦点を当てています。
6. 主な研究結果:
主な研究結果:
本稿では、合金ホイール製造のいくつかの重要な分野における最近の研究の知見を要約および統合しています。
- Computer Simulation of Casting Process: HsuとYu [22]は、鋳造シミュレーションソフトウェアを利用して、金型温度が安定するまでアルミニウムホイールの鋳造プロセスを反復的にモデル化しました。「収縮指数」(SI)を導入して鋳造品質を定量化し、漏れ試験結果と良好な相関関係を示し、鋳造パラメータの最適化を可能にしました。
- Casting Defects in Low-Pressure Die-Cast Aluminum Alloy Wheel: Zhangら [23]は、低圧ダイカストアルミニウムホイールの鋳造関連欠陥を調査し、ホイールの美観、気密性、および機械的性能に影響を与える主要な課題として、マクロおよびミクロの気孔率、巻き込まれた酸化膜、および外因性酸化物介在物を特定しました。
- Process Capability Improvement for Aluminum Alloy Wheel Machining: Sharmaら [24]は、A356アルミニウム合金ホイールの機械加工の工程能力を向上させるために、DMAIC(Define-Measure-Analyze-Improve-Control)アプローチを適用しました。石川ダイアグラムとプロセス故障モード分析を利用して、工程能力指数(Cp、Cpk、Cpm)の大幅な改善を達成しました。
- Analysis of Static Stress in an Alloy Wheel of the Passenger car: Nallusamyら [25]は、静的応力解析を使用して、合金ホイールの品質と安全性を向上させ、A356合金とT6熱処理を使用しました。彼らの研究は、試験生産性を向上させるために動的コーナリング疲労試験を最適化することに焦点を当てました。
- Optimization of Rigidity of Aluminum Alloy Wheels: Kocaturkら [26]は、アルミニウム合金ホイールの剛性パラメータの最適化手順を示し、有限要素シミュレーションにはANSYS Workbenchを、統計分析にはMinitabを利用しました。彼らの研究は、質量増加を最小限に抑えながら剛性を最大化することを目的としていました。
- Analysis of Alloy properties for the Manufacture of Automotive Wheels: Kabaら [27]は、合金特性を分析し、AlSi7Mg0.3合金とAlSi5Mg0.3合金を比較しました。AlSi5Mg0.3はより小さな結晶粒を示しますが、AlSi7Mg0.3は優れた機械的特性と流動性を提供し、産業用途に適していることがわかりました。
- Simulation of Inner Rim Compression Test of Aluminum Alloy Wheels: KaraとDaysal [28]は、ABAQUSを使用してインナーリム圧縮試験のシミュレーションを開発し、シミュレーション結果と実験データを比較して、ホイールの安全性を確保するために重要な破壊および破壊挙動を評価しました。
- Analysis of the forging processes for 6061 aluminum-alloy wheels: Kimら [29]は、有限要素法を使用して6061アルミニウム合金ホイールの鍛造プロセスを分析し、熱機械モデルと剛性粘塑性を取り入れて、高温での金属成形をシミュレーションし、プロセス条件を最適化しました。
- Development of a 3-D thermal model of the low-pressure die-cast (LPDC) process of A356 aluminum alloy wheels: Zhangら [30]は、ABAQUSを使用してLPDCプロセスの3D熱モデルを開発し、広範な温度測定で検証しました。このモデルは、複雑な熱流路とホットスポットを特定し、生産能力向上のためのプロセス最適化を支援しました。
- Precision forging technology for aluminum alloy: Dengら [31]は、アルミニウム合金の精密鍛造技術をレビューし、変形特性に関連する課題を克服し、精密形状を実現するためのクローズドダイ鍛造や等温ダイ鍛造などの高度な技術を強調しました。
- Finite element simulation and experimental validation of the cracking phenomenon in aluminum alloy wheels: Otarawannaら [32]は、ホイール衝撃試験中の亀裂現象を予測するために有限要素解析を使用し、FEAモデルを実験結果に対して検証して、設計時間とコストを削減しました。
- Effect of Cooling Process on Porosity in the Aluminum Alloy Automotive Wheel During Low-Pressure Die Casting: Suiら [33]は、低圧ダイカストにおける気孔率に対する冷却プロセスの影響を調査しました。数値シミュレーションと実験により、戦略的な冷却と断熱が、重要な領域の微細孔欠陥を低減できることが実証されました。
提示されたデータの分析:
レビューされた研究は、合金ホイールの製造プロセスを最適化および強化するために、計算シミュレーションおよび分析ツールへの依存度が高まっていることをまとめて強調しています。鋳造や鍛造から機械加工や材料選択まで、有限要素解析、熱モデリング、プロセスシミュレーションは、欠陥の特定と軽減、プロセス効率の向上、製品の品質と安全性の確保に役立っています。提示されたデータは、研究者が合金ホイールの製造における課題に対処するために、数値方法論と実験方法論の両方を活用して、多面的なアプローチを取っていることを示しています。
図のリスト:
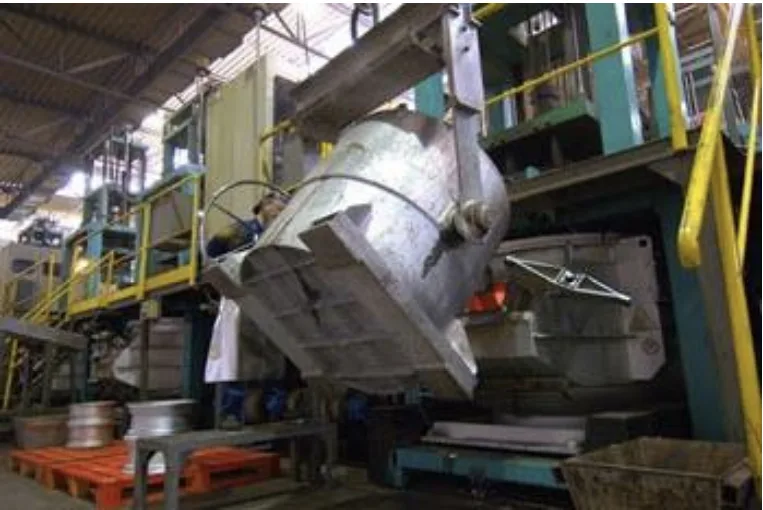
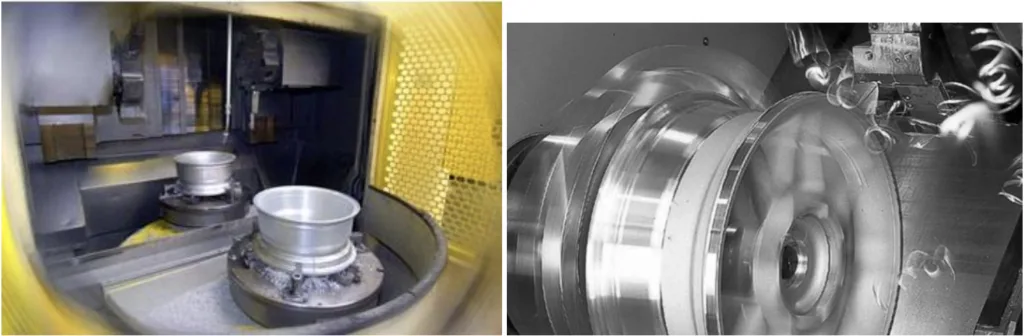
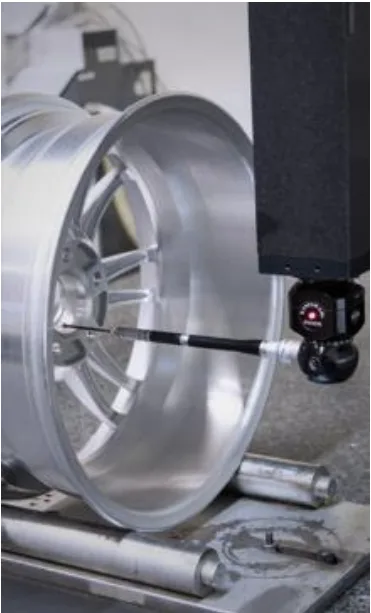
![Fig. 5. CAD models of casting molds for an aluminum disc wheel [22]](https://castman.co.kr/wp-content/uploads/image-655-png.webp)
![Fig. 6. The finite element model of an aluminum wheel and its molds [22].
Temperature distributions of mold during the casting process is shown in the figure 5.](https://castman.co.kr/wp-content/uploads/image-656-1024x377.webp)
![Fig. 7. Temperature distributions of mold during the casting process [22].](https://castman.co.kr/wp-content/uploads/image-657-png.webp)
![Fig. 8. Alloy wheel machining drawing with center hole diameter of ø50.000 (±0.050) [24].](https://castman.co.kr/wp-content/uploads/image-658-1024x551.webp)
![Fig. 12. Contour of the von Mises stress obtained from the simulation without the tire at 850 kg. Arrows mark the location where the von Mises stress is maximum (ignoring the direct impact region) [32].](https://castman.co.kr/wp-content/uploads/image-659-1024x545.webp)
![Fig. 13. Effect of the cooling and insulation process in removing the macroporosity defects in the junctions of prodcuced alloy wheels [33].](https://castman.co.kr/wp-content/uploads/image-660-1024x295.webp)
- Fig. 1. Providing the molten alloys for the casting operation.
- Fig. 2. Casting operation of wheel alloys.
- Fig. 3. Machining operations of wheel alloys.
- Fig. 4. Quality control of produced alloy wheels using the CMM.
- Fig. 5. CAD models of casting molds for an aluminum disc wheel [22].
- Fig. 6. The finite element model of an aluminum wheel and its molds [22].
- Fig. 7. Temperature distributions of mold during the casting process [22].
- Fig. 8. Alloy wheel machining drawing with center hole diameter of ø50.000 (±0.050) [24].
- Fig. 9. Wheel configuration just after forging [29].
- Fig. 10. 30° section mesh of a wheel and die (wheel differentiated by fine mesh size compared to die) [30].
- Fig. 11. Contour plot of temperatures in the (a) wheel and (b) die prior to die-open [30].
- Fig. 12. Contour of the von Mises stress obtained from the simulation without the tire at 850 kg. Arrows mark the location where the von Mises stress is maximum (ignoring the direct impact region) [32].
- Fig. 13. Effect of the cooling and insulation process in removing the macroporosity defects in the junctions of prodcuced alloy wheels [33].
7. 結論:
主な調査結果の要約:
本研究では、合金ホイールの製造プロセスを包括的にレビューし、プロセスの最適化と強化を目的とした最近の研究を強調しました。調査結果は、合金ホイールの製造を進歩させる上で、コンピュータシミュレーションと分析が極めて重要な役割を果たしていることを一貫して強調しています。研究努力は、自動車用アルミニウム合金鋳造における欠陥の軽減、機械加工効率の向上、静的応力解析による構造的完全性の確保、ホイール剛性の最適化、および高度な合金材料の探求に大きく向けられています。低圧ダイカストの熱モデリングと鍛造技術の進歩も、重要な焦点分野です。低圧ダイカストにおける冷却方法は、製造部品の品質を向上させるために重要であることが特定されています。
研究の学術的意義:
このレビューは、合金ホイール製造における現在の学術研究の動向に関する貴重な統合を提供します。製造上の課題に対処し、プロセスの理解を深めるために、学術界が仮想シミュレーションと分析技術を活用することに焦点を当てていることを強調しています。この研究は、最先端技術を理解し、この分野における将来の研究の方向性を特定しようとしている研究者にとって、統合されたリソースとして役立ちます。
実際的な意義:
レビューされた研究の実際的な意義は、合金ホイール製造業界にとって非常に重要です。これらの研究は、製造業者が生産プロセスを改良し、製品品質を向上させ、運用効率を向上させるための実用的な洞察と方法論を提供します。仮想シミュレーションと最適化技術の重視は、プロセスの開発と品質管理のための費用対効果が高く、時間節約になるアプローチを提供し、製造成果の大幅な改善につながる可能性があります。
研究の限界と今後の研究分野:
レビュー論文として、本研究は本質的に既存の公開された研究に依存しており、オリジナルの実験的検証は含まれていません。今後の研究では、要約された技術の産業実装と、実際の製造環境での検証に焦点を当てる必要があります。合金ホイール製造における新しい最適化アルゴリズム、高度なシミュレーション方法論、およびインダストリー4.0技術の統合のさらなる探求も、今後の調査が推奨される分野です。
8. 参考文献:
- 1. Soori M, Arezoo B, Habibi M (2017) Accuracy analysis of tool deflection error modelling in prediction of milled surfaces by a virtual machining system. International Journal of Computer Applications in Technology 55 (4):308-321
- 2. Soori M, Arezoo B, Habibi M (2014) Virtual machining considering dimensional, geometrical and tool deflection errors in three-axis CNC milling machines. Journal of Manufacturing Systems 33 (4):498-507
- 3. Soori M, Arezoo B, Habibi M (2013) Dimensional and geometrical errors of three-axis CNC milling machines in a virtual machining system. Computer-Aided Design 45 (11):1306-1313
- 4. Soori M, Arezoo B, Habibi M (2016) Tool deflection error of three-axis computer numerical control milling machines, monitoring and minimizing by a virtual machining system. Journal of Manufacturing Science and Engineering 138 (8)
- 5. Soori M, Arezoo B (2020) Virtual Machining Systems for CNC Milling and Turning Machine Tools: A Review. International Journal of Engineering and Future Technology 18 (1):56-104
- 6. Soori M, Arezoo B A Review in Machining-Induced Residual Stress.
- 7. Soori M, Arezoo B (2022) NURBS Interpolation Algorithm to Minimize Chord Error in 5-Axis CNC Milling Operations of Turbine Blades.
- 8. Soori M (2019) Virtual product development. GRIN Verlag,
- 9. Dastres R, Soori M (2021) Advances in Web-Based Decision Support Systems. International Journal of Engineering and Future Technology
- Dastres R, Soori M (2021) A Review in Recent Development of Network Threats and Security Measures. International Journal of Computer and Information Engineering 15 (1):75-81
- Dastres R, Soori M (2021) Artificial Neural Network Systems. International Journal of Imaging and Robotics (IJIR) 21 (2):13-25
- Dastres R, Soori M (2021) A Review in Advanced Digital Signal Processing Systems. International Journal of Electrical and Computer Engineering 15 (3):122-127
- Soori M, Asmael M, Solyalı D (2020) Recent Development in Friction Stir Welding Process: A Review. SAE International Journal of Materials and Manufacturing (5):18
- Soori M, Asmael M (2021) Virtual Minimization of Residual Stress and Deflection Error in Five-Axis Milling of Turbine Blades. Strojniski Vestnik/Journal of Mechanical Engineering 67 (5):235-244
- Soori M, Asmael M (2021) Cutting temperatures in milling operations of difficult-to-cut materials. Journal of New Technology and Materials 11 (1):47-56
- Soori M, Asmael M, Khan A, Farouk N (2021) Minimization of surface roughness in 5-axis milling of turbine blades. Mechanics Based Design of Structures and Machines:1-18. doi:10.1080/15397734.2021.1992779
- Soori M, Asmael M (2021) MINIMIZATION OF DEFLECTION ERROR IN FIVE AXIS MILLING OF IMPELLER BLADES. Facta Universitatis, series: Mechanical Engineering. doi:10.22190/FUME2108220695
- Soori M, Asmael M (2022) A Review of the Recent Development in Machining Parameter Optimization. Jordan Journal of Mechanical & Industrial Engineering 16 (2):205-223
- Dastres R, Soori M, Asmael M (2022) RADIO FREQUENCY IDENTIFICATION (RFID) BASED WIRELESS MANUFACTURING SYSTEMS, A REVIEW. Independent Journal of Management & Production 13 (1):258-290
- Dastres R, Soori M (2021) Advances in Web-Based Decision Support Systems. International Journal of Engineering and Future Technology 19 (1):1-15
- Dastres R, Soori M (2021) The Role of Information and Communication Technology (ICT) in Environmental Protection. International Journal of Tomography and Simulation 35 (1):24-37
- Hsu Y-L, Yu C-C (2006) Computer simulation of casting process of aluminium wheels-a case study. Proceedings of the Institution of Mechanical Engineers, Part B: Journal of Engineering Manufacture 220 (2):203-211
- Zhang B, Cockcroft S, Maijer D, Zhu J, Phillion A (2005) Casting defects in low-pressure die-cast aluminum alloy wheels. Jom 57 (11):36-43
- Sharma G, Rao PS, Babu BS (2018) Process capability improvement through DMAIC for aluminum alloy wheel machining. Journal of Industrial Engineering International 14 (2):213-226
- Nallusamy S, Prabu NM, Balakannan K, Majumdar G Analysis of Static Stress in an Alloy Wheel of the Passengercar. In: International Journal of Engineering Research in Africa, 2015. Trans Tech Publ, pp 17-25
- Kocaturk O, Elagoz FY, Kara A Optimization of Rigidity of Aluminum Alloy Wheels. In: Fracture, Fatigue and Wear, 2018. Springer, pp 814-819
- Kaba M, Donmez A, Cukur A, Kurban A, Cubuklusu H, Birol Y (2018) AlSi5Mg0. 3 Alloy for the manufacture of automotive wheels. International Journal of Metalcasting 12 (3):614-624
- Kara A, Daysal O Simulation of Inner Rim Compression Test of Aluminum Alloy Wheels. In: Key Engineering Materials, 2018. Trans Tech Publ, pp 379-384
- Kim Y, Ryou T, Choi H, Hwang B (2002) An analysis of the forging processes for 6061 aluminum-alloy wheels. Journal of Materials Processing Technology 123 (2):270-276
- Zhang B, Maijer D, Cockcroft S (2007) Development of a 3-D thermal model of the low-pressure die-cast (LPDC) process of A356 aluminum alloy wheels. Materials Science and Engineering: A 464 (1-2):295-305
- Deng L, Wang X, Jin J, Xia J (2018) Precision forging technology for aluminum alloy. Frontiers of Mechanical Engineering 13 (1):25-36
- Otarawanna S, Uttamung P, Malatip A Finite element simulation and experimental validation of the cracking phenomenon in aluminium alloy wheels during the impact test. In: AIP Conference Proceedings, 2018. vol 1. AIP Publishing LLC, p 020303
- Sui D, Cui Z, Wang R, Hao S, Han Q (2016) Effect of cooling process on porosity in the aluminum alloy automotive wheel during low-pressure die casting. International Journal of Metalcasting 10 (1):32-42
9. 著作権:
- この資料は、"Mohsen Soori"氏の論文:"Manufacturing Processes of Car Alloy Wheels"に基づいています。
- 論文ソース: https://hal.science/hal-03740879v1
この資料は上記の論文に基づいて要約されたものであり、商業目的での無断使用は禁止されています。
Copyright © 2025 CASTMAN. All rights reserved.