この文書は、研究論文「Defect reduction using Lean Six Sigma and DMAIC」を要約したもので、その方法論、調査結果、およびダイカスト業界への影響に関する詳細な概要を提供します。
1. 概要:概要
- タイトル: Defect reduction using Lean Six Sigma and DMAIC
- 著者: Condé, G.C.P., Oprime, P.C., Pimenta, M.L., Sordan, J.L., Bueno, C.R.
- 発行年: 2022年8月
- 発行学術誌/学会: 第5回ICQEM会議議事録、ミーニョ大学、ポルトガル、2022年
- キーワード:
- 欠陥削減
- Lean Six Sigma
- DMAIC
2. 研究背景:研究背景
- 研究テーマの社会的/学術的背景:
- 競争圧力により、企業は無駄を排除し、製品品質を向上させるソリューションを模索せざるを得なくなっています。
- Lean Six Sigma(LSS)は、ビジネス変革のための最も効果的なアプローチの1つと考えられています。
- 自動車部品セクターは、高い廃棄率と不必要なオペレーションによって引き起こされる深刻な効率性の問題を抱えています。
- 自動車セクターにおけるLSSとDMAICの適用事例はいくつかあるものの、文献によると、これらの方法論は自動車部品メーカーでは依然として十分に適用されていません。
- 既存研究の限界:
- LSSとDMAICの文献には、実用的な応用の記述が多数ありますが、自動車部品製造の文脈における構造化された改善活動で使用されるプロセス全体の詳細な記述が必要です。
- 研究の必要性:
- 自動車部品メーカーにおける欠陥を削減するためにLean Six SigmaとDMAICの方法論が適用される実証的なケーススタディを提示すること。
- 自動車部品製造における欠陥削減のために同様の改善方法論を使用しようとする人々に参考資料を提供すること。
3. 研究目的と研究課題:研究目的と研究課題
- 研究目的:
- Lean Six SigmaとDMAICの方法論を用いた自動車部品メーカーにおける欠陥削減の実証的なケーススタディを提示すること。
- 構造化された改善活動で使用されるプロセス全体を詳細に記述すること。
- 核心的な研究課題:
- 自動車部品製造会社内のダイカストおよび機械加工プロセスにおける欠陥を削減するために、Lean Six SigmaとDMAICの方法論をどのように効果的に適用できるか?
- これらのプロセスにおける欠陥率に影響を与える主要な変数は何か?
- 欠陥発生率を持続的に削減し、シグマレベルを向上させるために、どのようなソリューションを実装できるか?
- 研究仮説:
- Lean Six Sigmaフレームワーク内のDMAIC方法論の適用は、自動車部品製造のダイカストおよび機械加工プロセスにおける欠陥の有意かつ持続的な削減につながる可能性がある。
4. 研究方法論:研究方法論
- 研究デザイン:
- 実証的単一縦断的ケーススタディ。
- DMAIC方法論(定義、測定、分析、改善、管理)に従いました。
- データ収集方法:
- DMAICステップシーケンスで実施された半構造化面接。
- 文書分析。
- 直接的な現場観察。
- 分析方法:
- Minitabを用いた統計分析。
- 実験計画法(要因実験)。
- 仮説検定。
- 原因と結果のマトリックス。
- 測定システム分析(MSA)。
- プロセス能力分析。
- 研究対象と範囲:
- ブラジルに所在し、主要な自動車メーカー向けにダイカストおよび機械加工されたアルミニウム自動車部品を製造する製造会社。
- この研究は、特定の自動車部品であるリアビューハウジングサポート(RHS)のダイカストおよび機械加工プロセスにおける欠陥削減に焦点を当てました。
5. 主要な研究結果:主要な研究結果
- 核心的な研究結果:
- 分析により、ダイカストおよび機械加工段階における主な欠陥が指摘されました。
- ダイカスト: 「金型温度、金属温度、および二次射出速度が、不良ダイカスト部品の量に影響を与えた。」
- 機械加工: 「一方、機械加工プロセスにおける欠陥の発生率は、固定方法の影響を受けた。」
- 「実装されたソリューションは、慢性的に高いレベルから許容可能なレベルまで欠陥発生率を低下させた。」
- 「シグマレベルは、3.4σから4σに持続的に上昇した。」
- 統計的/定性的な分析結果:
- 定義段階: 「2つの管理図が作成された。ダイカスト部品の不良率のp管理図(図1)と、機械加工部品の不良率のp管理図(図2)。」これらの管理図は、特殊原因と高い欠陥率を示すプロセスを示しました。ベースラインのシグマレベルは「3.4σ」と計算されました。
- 測定段階: 「プロジェクトチームは、SIPOC(サプライヤー、インプット、プロセス、アウトプット、顧客)マトリックス(図3)を作成した。」詳細な変数分析により、欠陥率に影響を与える可能性のある30の変数が特定されました(表3)。「原因と結果のマトリックス」は、7つの主要な変数を優先順位付けしました(表4および5)。「測定システム分析(MSA)」は、許容可能な測定システムを確認しました(表7の「すべてのカッパは0.7を超えている」)。
- 分析段階: 「石川図」(図7および図8)を根本原因分析に使用しました。「一連の要因実験」(図9、10、13、14)により、有意な変数が特定されました。
- ダイカスト: 金型温度(x1)、金属温度(x2)、および二次射出速度(x3)。図12に見られる最適な組み合わせ:「金型温度レベル= 220°C、金属温度レベル= 700°C、射出速度(第2段階)レベル= 3メートル/秒」。
- 機械加工: 固定方法(x5)。図16に見られる最適な方法:「タイプII(代替)固定方法-x5、別名「トーレス」」。
- 改善段階: 「意思決定マトリックス」(表10)は、実装のための4つのソリューションをランク付けして選択しました:「熱油の使用、新しい機械加工固定方法、鋳造部品のメンテナンスの改善、代替工具ホルダータイプ。」
- 管理段階: 「仮説検定」(図18および図19)は、ダイカストおよび機械加工プロセスの両方で欠陥率の有意な低下を確認しました(P値= 0.000)。「プロセス能力分析」(図21および図22)は、改善され持続的なプロセスパフォーマンスを示し、「4σ」シグマレベルに達しました(図20)。
- データ解釈:
- 統計分析と実験結果は、DMAIC方法論が欠陥の根本原因を特定し、対処する上で効果的であることを示しました。
- 最適化されたパラメータと実装されたソリューションは、欠陥率の有意かつ持続的な削減と、プロセスシグマレベルの向上につながりました。
- 図の名前リスト:
- 図1 - ダイカスト部品の不良率のp管理図。
- 図2 - 機械加工部品の不良率のp管理図。
- 図3 - SIPOC / ダイカストおよび機械加工ハウジングサポート製造プロセス。
- 図4 - 部品領域。
- 図5 - 改善前の最終プロセス歩留まり計算。
- 図6 - パレート図 - 部品不良の主な理由。
- 図7 - 選択された変数x1(金型温度)の根本原因分析。
- 図8 - 選択された変数x7(切削工具タイプ-ねじ)の根本原因分析。
- 図9 - 最初の実験実行の効果のパレート図 - ダイカスト。
- 図10 - 2回目の実験実行の効果のパレート図 - ダイカスト。
- 図11 - 2回目の実験実行における相互作用 - ダイカスト。
- 図12 - 2回目の実験実行中に見つかった変数の最適な組み合わせ - ダイカスト。
- 図13 - 最初の実験実行の効果のパレート図 - 機械加工。
- 図14 - 2回目の実験実行の効果のパレート図 - 機械加工。
- 図15 - 2回目の実験実行における相互作用 - 機械加工。
- 図16 - 2回目の実験実行中に見つかった変数の最適な組み合わせ - ダイカスト。
- 図17 - プロジェクトチーム会議。
- 図18 - ダイカスト改善の仮説検定。
- 図19 - 機械加工改善の仮説検定。
- 図20 - 改善されたプロセスの最終プロセス歩留まり計算。
- 図21 - 定期的なプロセス能力分析 - ダイカストプロセス。
- 図22 - 定期的なプロセス能力分析 - 機械加工。
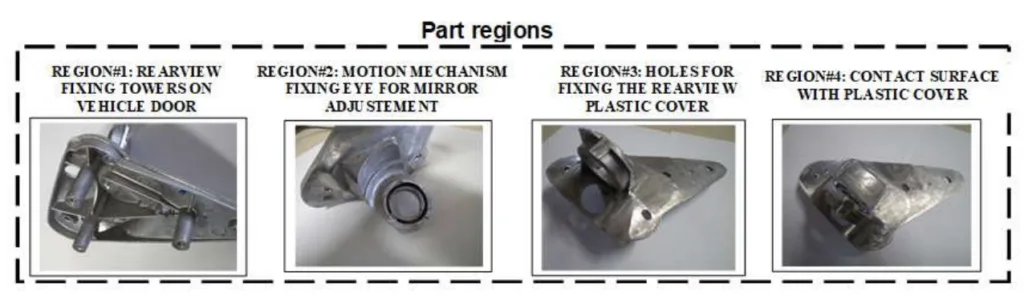
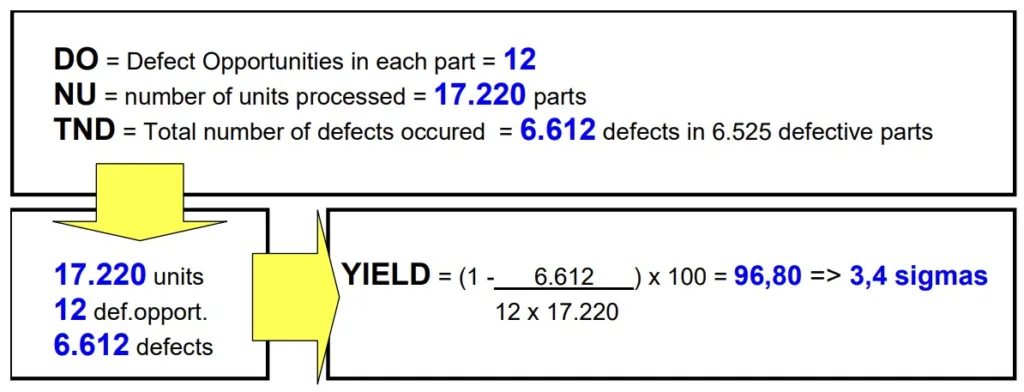
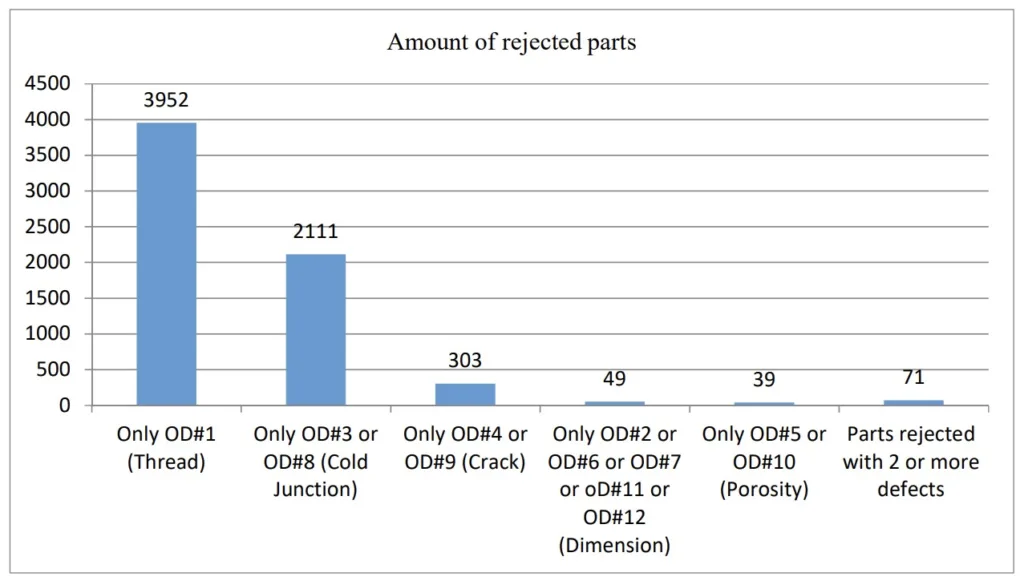
6. 結論と考察:結論と考察
- 主な結果の要約:
- プロジェクトは、DMAIC方法論をダイカストおよび機械加工プロセスの欠陥削減に効果的に適用しました。
- 欠陥に影響を与える主要な変数が特定され、最適化されました。
- 実装されたソリューションは、「3.4σから4σ」へのシグマレベルの持続的な向上につながりました。
- ダイカストプロセスで「7%未満」、機械加工プロセスで「1%未満」に不良率を削減するというプロジェクト目標が達成されました。
- 研究の学術的意義:
- 自動車部品製造におけるLean Six SigmaとDMAICの効果的な適用を示す詳細な実証的ケーススタディを提供します。
- 特定のツールと手法の使用を含む、DMAIC実装のステップバイステッププロセスを示すことで、文献に貢献します。
- 実務上の示唆:
- この論文は、同じタイプの改善方法論を使用しようとする人々に使用できます。
- この研究は、欠陥削減のためにLean Six Sigmaプロジェクトを実装しようとしている自動車部品業界の管理者およびエンジニアにとって参考資料として使用できます。
- 詳細な方法論と特定された主要な変数は、同様の改善イニシアチブのための実用的なガイダンスを提供します。
- 成功したケーススタディは、DMAICが製造プロセスにおいて有意かつ持続的な改善を達成する可能性を示しています。
- 研究の限界:
- 「この研究は単一のケーススタディに限定されており、他のタイプの業界に結果を一般化する意図はありません。」
7. 今後の研究:今後の研究
- 今後の研究の方向性:
- 今後の研究では、これらの調査結果の他のタイプの業界および製造プロセスへの一般化可能性を調査できます。
- 欠陥削減を超えた自動車部品製造の他の分野におけるLSSとDMAICの適用を調査することは有益である可能性があります。
- さらなる探求が必要な領域:
- 達成された改善の長期的な持続可能性と、それに影響を与える要因を調査すること。
- 自動車部品製造におけるLSSとDMAICの実装の成功に対する組織文化と従業員のエンゲージメントの影響を調査すること。
8. 参考文献:参考文献
- Antony, J. (2015), “Challenges in the deployment of LSS in the higher education sector: Viewpoints from leading academics and practitioners”, International Journal of Productivity and Performance Management.
- Antony, J., Antony, F. J., Kumar, M. and Cho, B. R. (2007). “Six sigma in service organisations: Benefits, challenges and difficulties, common myths, empirical observations and success factors", International journal of quality & reliability management, Vol. 24 No. 3, pp. 294-311.
- Bass, I., and Lawton, B. (2009). Lean six sigma using SigmaXL and Minitab. McGraw Hill Professional.
- Bayou, M. E. and De Korvin, A. (2008). “Measuring the leanness of manufacturing systems—a case study of Ford Motor Company and General Motors”, Journal of Engineering and Technology Management, Vol. 25 No 4, pp. 287-304.
- Chaurasia, B., Garg, D., & Agarwal, A. (2019), “Lean Six Sigma approach: a strategy to enhance performance of first through time and scrap reduction in an automotive industry”, International Journal of Business Excellence, Vol. 17, No. 1, pp. 42-57.
- Costa, L. B. M., Godinho Filho, M., Fredendall, L. D. and Ganga, G. M. D. (2021), “Lean six sigma in the food industry: Construct development and measurement validation”, International Journal of Production Economics, Vol. 231, pp. 107843.
- Chua, R. C. H. and DeFeo, J. A. (2006), Juran's quality planning and analysis: For enterprise quality. Tata McGraw-Hill Education.
- Daniyan, I., Adeodu, A., Mpofu, K., Maladzhi, R. and Katumba, M. G. K. Κ. (2022), “Application of lean Six Sigma methodology using DMAIC approach for the improvement of bogie assembly process in the railcar industry”, Heliyon, e09043.
- Doolen, T. L. and Hacker, M. E. (2005), “A review of lean assessment in organizations: an exploratory study of lean practices by electronics manufacturers”, Journal of Manufacturing systems, Vol. 24 No. 1, pp. 55-67.
- George, M. L., Maxey, J., Rowlands, D. T., & Upton, M. (2004). Lean six sigma pocket toolbook. McGraw-Hill Professional Publishing.
- Gupta, S., Modgil, S. and Gunasekaran, A. (2020), “Big data in lean six sigma: a review and further research directions”, International Journal of Production Research, Vol. 58 No. 3, pp. 947-969.
- International Organization for Standardization. ISO 13.053-1: Quantitative methods in process improvement – Six Sigma Part 1: DMAIC methodology. Genebra: ISO, 2011.
- Kahraman, C., and Büyüközkan, G. (2008), “A Combined Fuzzy AHP and Fuzzy Goal Programming Approach for Effective Six-Sigma Project Selection”, Journal of Multiple-Valued Logic & Soft Computing, Vol. 14 No. 6.
- Karlsson, C. and Åhlström, P. (1996). “Assessing changes towards lean production", International Journal of Operations & Production Management.
- Kwak, Y. H., and F. T. Anbari. (2006), “Benefits, Obstacles, and Future of Six Sigma Approach”, Technovation, Vol. 26 No. 5–6, pp. 708–715.
- Mancilla-Escobar, J., Maccasi-Jaurequi, I., Raymundo-Ibañez, C. and Perez, M. (2020, March). Layout Lean model of production management based on change management to improve efficiency in the production of packaging in auto parts sector SMEs. In IOP Conference Series: Materials Science and Engineering (Vol. 796, No. 1, p. 012014). IOP Publishing.
- McLachlin, R. (1997), “Management initiatives and just-in-time manufacturing”, Journal of Operations management, Vol. 15 No. 4, pp. 271-292.
- Mishra, Y., Sharma, M. K., Yadav, V., Meena, M. L. and Dangayach, G. S. (2021), “Lean Six Sigma implementation in an Indian manufacturing organisation: a case study”, International Journal of Six Sigma and Competitive Advantage, Vol. 13 No. 1-3, pp. 76-100.
- Panizzolo, R. (1998), “Applying the lessons learned from 27 lean manufacturers.: The relevance of relationships management”, International journal of production economics, Vol. 55 No. 3, pp. 223-240.
- Pinheiro, T. H., Scheller, A. C., & Miguel, P. A. C. (2013), “Integração do seis sigma com o lean production: uma análise por meio de múltiplos casos”, Revista Produção Online, Vol. 13 No. 4, pp. 1297-1324.
- PMBOK, G. (2008). Um guia do conjunto de conhecimentos em gerenciamento de projetos (guia pmbok®). Project Management Institute, Inc. EUA.
- Salah, S., Rahim, A. and Carretero, J. A. (2010), “The integration of Six Sigma and lean management", International Journal of Lean Six Sigma.
- Schroeder, R. G., Linderman, K., Liedtke C. and Choo, A.S. (2009), “Six Sigma: Definition and Underlying Theory.” Quality Control and Applied Statistics, Vol. 54 No. 5: pp. 441–445.
- Shah, R. and Ward, P. T. (2003), “Lean manufacturing: context, practice bundles, and performance", Journal of operations management, Vol. 21 No. 2, pp. 129-149.
- Shokri, A. (2019), “Reducing the scrap rate in manufacturing SMEs through lean six sigma methodology: An action research”, IEEE Engineering Management Review, Vol. 47 No. 3, pp. 104-117.
- Snee, R. D. (2004), “Six-Sigma: The Evolution of 100 Years of Business”, International Journal of Six Sigma and Competitive Advantage, Vol. 1 No. 1: pp. 4-20.
9. 著作権:著作権
- 本資料は、[Giovanni Condé, Pedro Carlos Oprime, Pimenta, M.L., Sordan, J.L., Bueno, C.R.]の論文:[Defect reduction using Lean Six Sigma and DMAIC]に基づいて作成されました。
- 論文出典:https://www.researchgate.net/publication/362389760
本資料は上記の論文に基づいて要約作成されたものであり、商業目的での無断使用は禁止されています。
Copyright © 2025 CASTMAN. All rights reserved.