この記事では、UNIVERSITÀ DEGLI STUDI DI PADOVA and AALEN HOCHSCHULE FÜR TECHNIK UND WIRTSCHAFTが発行した論文「INVESTIGATION ON THE EFFECTS OF INNOVATIVE MELT TREATMENTS ON MICROSTRUCTURE AND MECHANICAL BEHAVIOUR OF DIECAST AL ALLOYS」を紹介します。
1. 概要:
- タイトル: INVESTIGATION ON THE EFFECTS OF INNOVATIVE MELT TREATMENTS ON MICROSTRUCTURE AND MECHANICAL BEHAVIOUR OF DIECAST AL ALLOYS
- 著者: Alberto Dal Maso, Prof. Dr. Ing. Lothar H. Kallien, Prof. Ing. Franco Bonollo
- 出版年: 2011 – 2012 学年度
- 出版ジャーナル/学会: UNIVERSITÀ DEGLI STUDI DI PADOVA, CORSO DI LAUREA MAGISTRALE IN INGEGNERIA DELL’INNOVAZIONE DEL PRODOTTO
- キーワード: ダイカスト, アルミニウム合金, 溶湯処理, 微細組織, 機械的挙動, Al2O3粒子, インサイチュプロセス
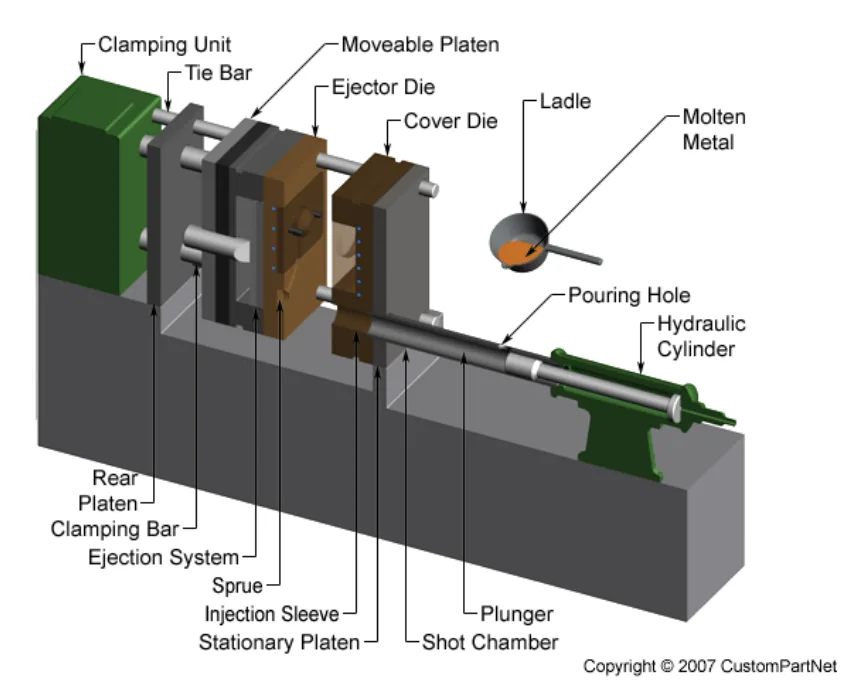
2. 概要または序論
革新的で高性能な材料の研究は、多くの分野の開発において重要な役割を果たしています。材料特性を向上させるための一般的な戦略の1つは、相補的な材料を組み合わせて優れた性能を達成することであり、これは複合材料研究の根底にある原則です。金属基複合材料(MMC)は、その性能と加工の多様性から特に興味深いものです。本研究では、溶融アルミニウムに対する革新的な溶湯処理を調査し、溶融アルミニウム中に酸化アルミニウム(Al2O3)粒子をその場生成し、溶融物中に分散させて凝固金属に組み込むことを目的としています。Al2O3を強化材として使用することの二重の利点、すなわち、アルミニウム合金の硬度、強度、弾性率を向上させる機械的強化と、より微細な微細組織を得ることによって合金性能を向上させる結晶粒微細化剤としての利点について検討します。本研究では、純アルミニウムおよびAl-Cu合金に対する処理の効果を調べ、パーマネント金型鋳造と高圧ダイカスト(HPDC)の両方で試験を実施しました。HPDCプロセスは、Al、Mg、Zn基合金部品の製造に不可欠であり、特に自動車やその他の大量生産産業で用いられています。真空や半凝固金属鋳造などのHPDCにおける最近の進歩は、鋳造品質を向上させています。Al-Cu合金は、その強度と延性で知られており、析出硬化によって強化され、展伸材と鋳造材の両方で広く使用されています。しかし、熱間割れ感受性や腐食の問題も抱えています。溶湯処理は、溶融アルミニウムにアルゴンと酸素を注入し、Al2O3粒子を生成および分散させ、合金特性と微細組織を向上させることを目的としています。
3. 研究背景:
研究テーマの背景:
革新的な材料の開発は工学において重要であり、金属基複合材料(MMC)は、その強化された特性と多様な加工性により、ますます重要性を増しています。アルミニウム合金、特にAl-Cu合金は、展伸材と鋳造材の両方で不可欠であり、高い強度と靭性を提供します。高圧ダイカスト(HPDC)は、Al、Mg、Zn基合金部品の製造に不可欠なプロセスであり、特に自動車産業やその他の大量生産産業で広く用いられています。ダイカストアルミニウム合金の機械的特性を向上させ、欠陥を低減することは、現在も研究が進められている分野です。
既存研究の現状:
材料科学における既存の研究は、複合材料における材料の組み合わせなどの手法を通じて材料特性を向上させることに焦点を当てています。金属基複合材料、特にAl2O3のようなセラミック相で強化されたものは、強度、硬度、高温性能の向上について十分に文書化されています。先行研究では、インサイチュ法およびエクスサイチュ法で製造されたAl2O3強化MMCが検討されています。また、Al2O3粒子はAl-Cu合金において結晶粒微細化剤として作用し、熱間割れを低減する可能性があることも研究で示されています。真空アシストHPDCや半凝固HPDCなどのHPDCの革新は、欠陥を低減し、部品品質を向上させることを目的としています。しかし、金属マトリックス中にナノスケールの強化材を生成および分散させるための費用対効果が高く、工業的に拡張可能な方法の開発には課題が残っています。
研究の必要性:
HPDCとAl-Cu合金の進歩にもかかわらず、熱間割れ感受性、多孔性、耐食性などの限界が依然として存在します。機械的特性が向上した金属マトリックスナノコンポジット(MMNC)を製造し、低い破壊靭性や被削性などの限界を克服することが重要な研究分野となっています。既存のMMC製造法の多くは、費用がかかり、従来の製造環境での使用が複雑です。ダイカストアルミニウム合金の特性を向上させるための、費用対効果の高い効果的な方法、特に強度を向上させ、微細組織を微細化し、HPDCのようなプロセスにおける熱間割れ感受性を低減する可能性のあるAl2O3のような強化粒子のその場生成と分散が求められています。本研究は、より要求の厳しい構造用途に適したダイカストアルミニウム合金の性能を向上させるための、革新的で費用対効果の高い溶湯処理の必要性に取り組むものです。
4. 研究目的と研究課題:
研究目的:
主な研究目的は、溶融アルミニウム中にAl2O3粒子をその場生成する革新的な溶湯処理の実現可能性を調査し、この処理がダイカストアルミニウム合金の微細組織と機械的挙動に及ぼす影響を評価することです。これには、生成されたAl2O3粒子が凝固金属中に保持されるかどうか、およびそれらが機械的特性にどのように影響するかを評価することが含まれます。
主な研究内容:
- 溶融アルミニウムへのアルゴンと酸素ガス混合物の注入を伴う革新的な溶湯処理は、Al2O3粒子をその場生成するのに効果的か?
- この溶湯処理は、凝固時に保持される溶融アルミニウム中のAl2O3粒子の分散につながるか?
- このインサイチュ溶湯処理は、純アルミニウムおよびAl-Cu合金の微細組織にどのような影響を与えるか?
- 溶湯処理は、パーマネント金型鋳造とHPDCの両方で製造されたダイカスト純アルミニウムおよびAl-Cu合金の機械的特性(引張強度、耐力、伸び)にどのような影響を与えるか?
- この溶湯処理は、製造コストや複雑さを大幅に増加させることなく、ダイカストアルミニウム合金の特性を向上させるための実行可能な方法となり得るか?
5. 研究方法
研究デザイン:
本研究では、革新的な溶湯処理がアルミニウム合金に及ぼす影響を評価するために実験計画法を採用しました。溶湯処理は、攪拌しながら溶融アルミニウムにアルゴンと酸素ガス混合物を注入することからなります。実験は、誘導炉と脱ガスユニットを用いた小規模および大規模のセットアップで実施されました。処理時間、ガス流量、インペラーサイズ、および鋳造方法(パーマネント金型およびHPDC)を系統的に変化させ、それらの影響を評価しました。
データ収集方法:
- 機械試験: パーマネント金型で鋳造された試験片およびダイカストプレートから機械加工された試験片に対して引張試験を実施し、引張強さ(UTS)、耐力(YS)、および伸び(A)を評価しました。
- 顕微鏡観察: 光学顕微鏡を使用して合金の微細組織を分析し、結晶粒組織と相分布を調べました。
- コンピュータ断層撮影(CT): CTスキャンを用いて、鋳造試験片内の多孔質含有量と分布を評価しました。
- 密度測定: アルキメデスの原理に基づく天秤を使用して試験片の密度を測定し、多孔質の別の尺度を提供しました。
- 化学組成分析: スパーク発光分光分析(S-OES)を用いて、合金の化学組成を検証しました。
分析方法:
- 定量的分析: 引張試験データを統計的に分析し、溶湯処理と鋳造方法が機械的特性に及ぼす影響を判定しました。CTスキャンと密度試験からの多孔質測定値を機械的特性データと相関させました。
- 定性的分析: 光学顕微鏡およびCT画像からの微細組織分析を用いて、溶湯処理が結晶粒微細化、相分布、および多孔質形態に及ぼす影響を定性的に評価しました。
- 比較分析: 処理合金と未処理合金、および異なる方法(パーマネント金型対HPDC)で鋳造された合金の機械的特性を比較し、溶湯処理と鋳造プロセスの有効性を評価しました。結果は、EN AC-21100やAA 206.0 T4などの標準合金の仕様とも比較しました。
研究対象と範囲:
研究対象は、4種類のアルミニウム合金でした。
- 合金 1: 市販の純アルミニウム。
- 合金 2: AlCu4.6 (Al-4.6Cu)。
- 合金 3: AlCu5MnMg (Al-5Cu-0.45Mn-0.37Mg)。
- 合金 4: ZnとTiを添加したAlCu5MnMg (Al-5Cu-0.42Mn-0.27Mg-0.1Zn-0.023Ti)。
研究の範囲は以下を含みます。
- 溶湯処理: アルゴンと酸素ガス注入を用いた溶融アルミニウム中のAl2O3粒子のその場生成。
- 鋳造方法: パーマネント金型鋳造および高圧ダイカスト(HPDC)。
- 熱処理: 合金4 HPDC試験片に対する溶体化熱処理および自然時効。
- 機械的特性: 引張強度、耐力、および伸び。
- 微細組織特性評価: 光学顕微鏡およびCT多孔質分析。
6. 主な研究成果:
主な研究成果:
- 溶湯処理とAl2O3生成: 溶湯処理プロセスは、溶湯表面に発泡スラグを一貫して生成し、酸化物、おそらくAl2O3の生成を示唆しました。しかし、微細組織分析では、いずれの合金においてもアルミニウムマトリックス中に分散したAl2O3粒子は確認されませんでした。
- 合金1(純アルミニウム)の機械的特性: ArまたはAr + O2による溶湯処理は、純アルミニウムの機械的特性を大きく変化させませんでした。引張強度と伸びの変動は、溶湯処理自体ではなく、多孔質と金型温度の変動に起因すると考えられました。
- 合金2(AlCu4.6)の機械的特性: 銅の添加は、合金1と比較して合金2の強度を大幅に向上させました。HPDC合金2は、パーマネント金型鋳造品よりも高い強度と伸びを示し、これはより速い冷却による微細組織に起因すると考えられました。両方の鋳造方法で「のこぎり歯状」の応力-ひずみ曲線が示され、これはCuAl2相による可能性があります。
- 合金3(AlCu5MnMg)の機械的特性: 合金3は、合金2と比較して強度がさらに向上しましたが、伸びは減少しました。HPDC合金3は、パーマネント金型鋳造品よりもわずかに高い強度を示しました。「のこぎり歯状」挙動は合金3では観察されませんでした。
- 合金4(ZnとTiを添加したAlCu5MnMg)の機械的特性: 合金4は、HPDCのままの状態では、安定した耐力とパーマネント金型鋳造品と比較して高いUTSを示しました。熱処理(T4)はHPDC合金4の強度を大幅に向上させ、AA 206.0 T4合金に匹敵する特性を達成しましたが、伸びは低いままでした。
- 多孔質: 多孔質は、すべての合金と鋳造方法において機械的特性に影響を与える重要な要因でした。CT分析により、多孔質レベルと分布の変動が明らかになり、引張強度と伸びに影響を与えていることが示唆されました。
提示されたデータの分析:
- 図 5.1, 5.2, 5.3, 5.4, 5.5, 5.6, 5.7: これらの図は、異なる溶湯処理(Ar、Ar+O2)およびインペラーサイズ(Ø 72 mm、Ø 185 mm)下での合金1の機械的特性(Rm、Ag)の時間変化を示しています。データは、溶湯処理による有意な強化効果を示しておらず、変動は多孔質と金型条件による可能性が高いことを示しています。
- 図 5.8, 5.9, 5.10: これらの図は、合金1のCT画像と多孔質測定値を示しており、多孔質の変動と多孔質と機械的特性の変動との相関関係を示唆しています。
- 図 5.16, 5.20, 5.21: これらの図は、パーマネント金型とHPDCで鋳造された合金2の機械的特性を比較しています。HPDCサンプルは、より高い強度と伸びを示しています。図5.21は、合金2の鋳造プロセスを比較し、HPDCの改善された特性を強調しています。
- 図 5.19, 5.22: これらの図は、合金2の応力-ひずみ曲線を示しており、「のこぎり歯状」挙動を示しており、パーマネント金型鋳造品でより顕著です。
- 図 5.26, 5.30: これらの図は、パーマネント金型とHPDCで鋳造された合金3の機械的特性を示しています。合金3は、合金2よりも強度が高いが、伸びが低いことを示しています。
- 図 5.35, 5.36, 5.38, 5.39: これらの図は、パーマネント金型、HPDCのまま、および熱処理されたHPDC状態での合金4の機械的特性を示しています。熱処理は、HPDC合金4の強度を大幅に向上させています。
図のリスト:
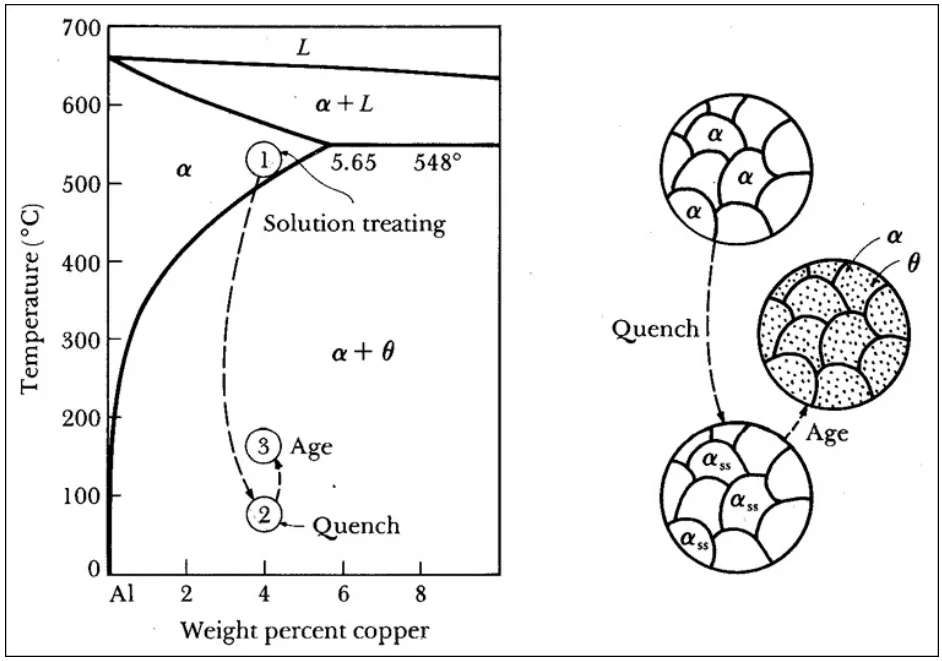
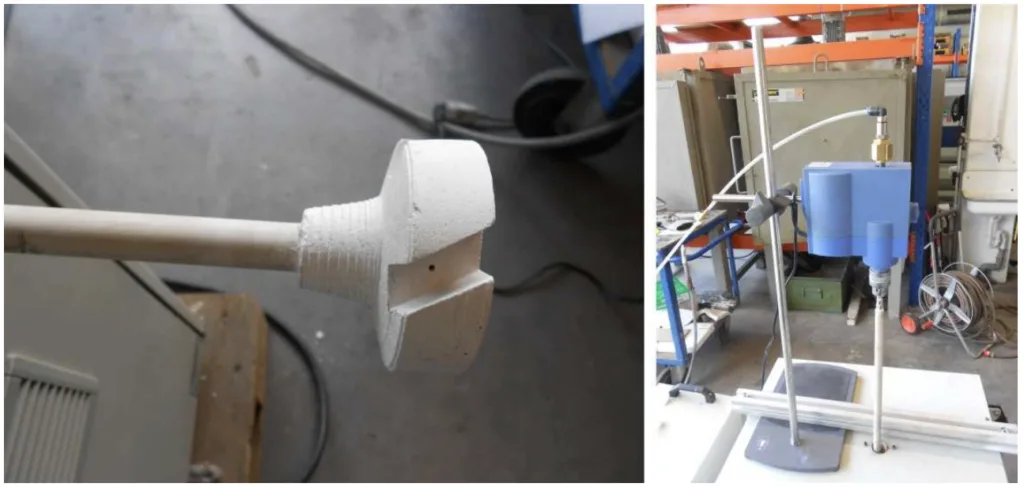
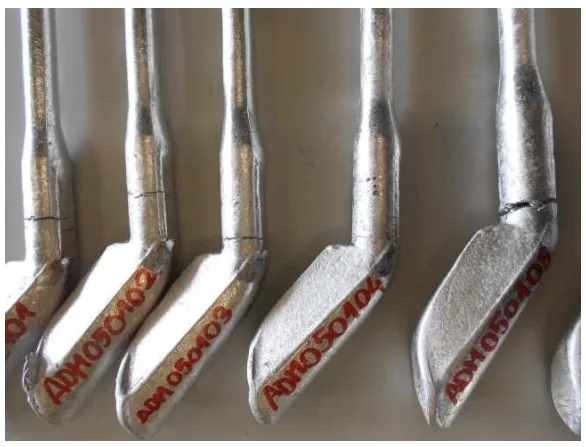
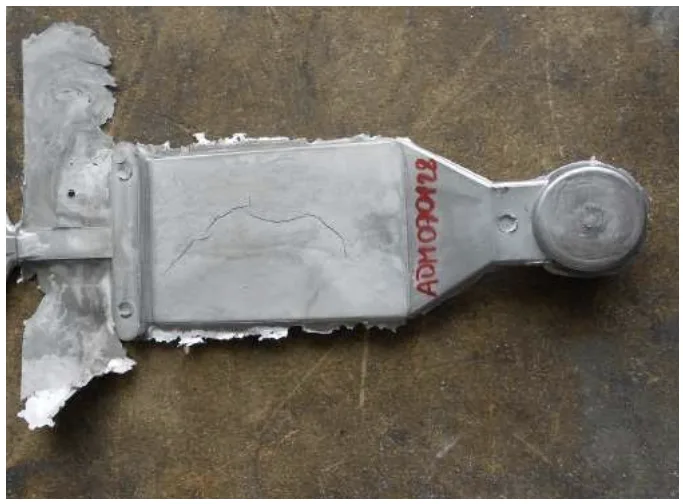
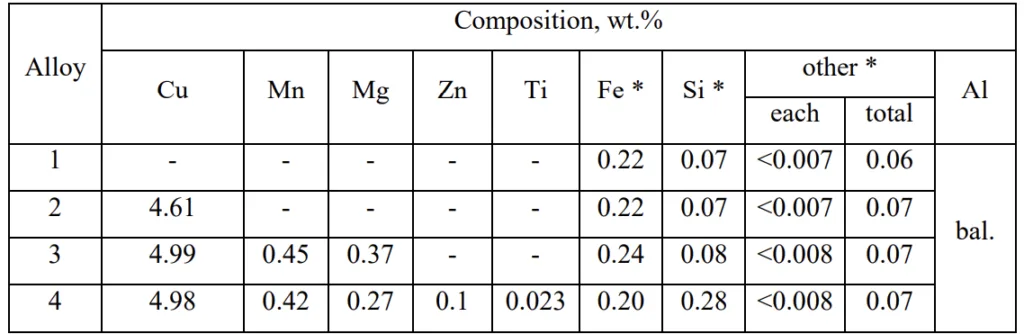
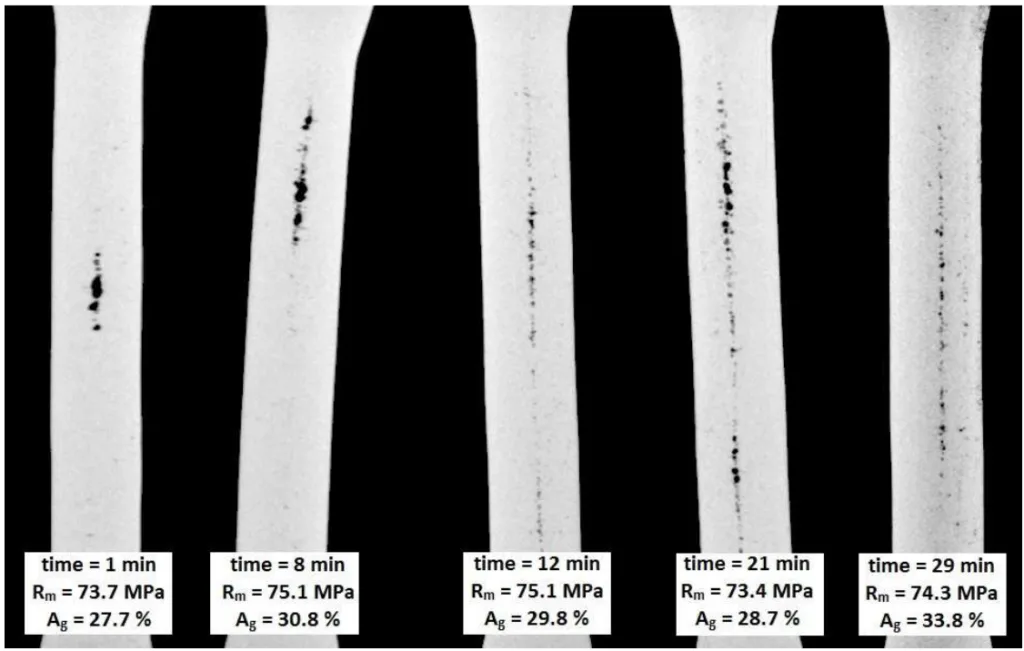
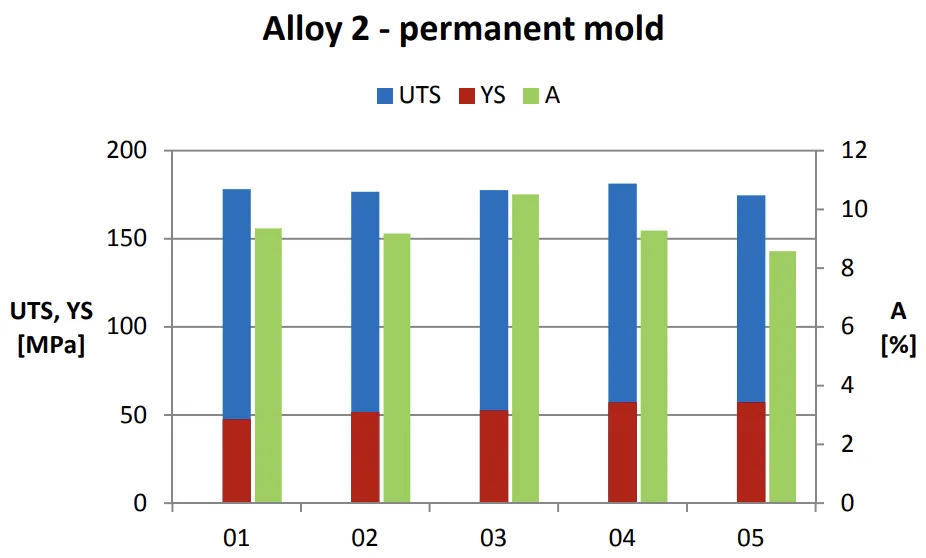
- Figure 1: プレスダイカストマシンの断面図
- Figure 2: 析出強化プロセスの図解
- Figure 3: 小型設備で使用したインペラーとミキサー
- Figure 4: アルミニウム溶湯浴の表面に形成されたスラグ
- Figure 5: 熱間割れの明らかな兆候を示すプレスダイカストで得られたプレート
- Figure 6: 合金1の機械的特性 - Ar + O2注入 - Ø 72 mm インペラー
- Figure 7: 合金1の機械的特性 - Ar + O2注入 - Ø 185 mm インペラー
- Figure 8: Ar + O2注入処理後の合金1の微細組織
- Figure 9: プレスダイカスト合金2試験片の破断点の分布
- Figure 10: 時効処理後の合金4の機械的特性
- Figure 2.1: HPDCで製造された部品:歯科用椅子の部品 (a)、医療用イメージャーの側壁 (b)、エンジンベースブラケット (c)、トランスアクスルハウジング (d)。
- Figure 2.2: ホットチャンバーHPDCマシンのレイアウト
- Figure 2.3: コールドチャンバーHPDCマシンのレイアウト
- Figure 2.4: ダイアセンブリの主な構成要素
- Figure 2.5: ショットスリーブとダイキャビティの両方から空気を抽出する真空システム
- Figure 2.6: Electronics GmbH製 StatVac 装置
- Figure 2.7: Vacural HPDCマシンのレイアウト
- Figure 2.8: 従来のダイカスト合金と半凝固ダイカスト合金の微細組織の比較
- Figure 3.1: アルフレッド・ウィルム (1869–1937)
- Figure 3.2: ジュラルミンは、その強度、靭性、軽量性から航空機や飛行船に採用されました
- Figure 3.3: Al-CuAl2 相図
- Figure 3.4: Al-Cu 合金の凝固
- Figure 3.5: 析出硬化プロセス
- Figure 3.6: 析出物を乗り越える2つのメカニズム
- Figure 3.7: 析出物半径が応力 σy に及ぼす影響
- Figure 3.8: 異なる時効硬化条件による挙動の変化
- Figure 3.9: Al-Cu 相のゾルバス
- Figure 3.10: ダイカスト部品に発生した熱間割れ
- Figure 4.1: 窒化ホウ素ブロックと機械加工されたインペラー
- Figure 4.2: 接着プロセスの2つの段階
- Figure 4.3: 炉に取り付けられた攪拌機
- Figure 4.4: ガス混合回路の概略図
- Figure 4.5: 処理中の大型スケールセットアップ
- Figure 4.6: Ø 185 mm インペラー
- Figure 4.7: インペラー周辺に凝固したスラグとるつぼ上の酸化物粉末
- Figure 4.8: グラファイトチューブに巻き付いたスラグ
- Figure 4.9: 溶湯表面から除去されたスラグ
- Figure 4.10: パーマネント金型鋳造引張試験片
- Figure 4.11: Weingarten GDK 200 HPDC マシン
- Figure 4.12: ダイカストプレートの製造に使用した金型
- Figure 4.13: パーマネント金型鋳造試験片の熱間割れ
- Figure 4.14: ダイカストプレートの熱間割れ
- Figure 4.15: ダイカストプレートのオーバーフロー上のエジェクターピンの跡
- Figure 4.16: 熱処理されたダイカストプレートの表面の水ぶくれ
- Figure 4.7: インペラー周辺に凝固したスラグとるつぼ上の酸化物粉末
- Figure 5.1: 合金1の機械的特性 – Ar + O2 による溶湯処理 – Ø 72 mm インペラーセットアップ
- Figure 5.2: 合金1の極限引張強度 – Ar による溶湯処理 – Ø185 mm インペラーセットアップ
- Figure 5.3: 合金1の最大荷重時の永久伸び – Ar による溶湯処理 – Ø 185 mm インペラーセットアップ
- Figure 5.4: 合金1の極限引張強度 – Ar および O2 による溶湯処理 – Ø 185 mm インペラー
- Figure 5.5: 合金1の最大荷重時の伸び – Ar および O2 による溶湯処理 – Ø 185 mm インペラー
- Figure 5.6: Ar で処理した合金1と Ar + O2 で処理した合金1の Rm の比較
- Figure 5.7: 合金1における Rm と Ag の変動の比較(Ag 値のトレンドフィルタリング後)– Ar + O2 による溶湯処理 – Ø 185 mm インペラー
- Figure 5.8: 合金1の引張試験片の一部における内部多孔質を示すCT画像
- Figure 5.9: 合金1の引張試験片の多孔質含有量 – Ar + O2 による溶湯処理 – Ø 185 mm インペラー
- Figure 5.10: 合金1の引張試験片のグリップセクションのCT画像 – Ar + O2 による溶湯処理 – Ø 185 mm インペラー
- Figure 5.11: 合金1の微細組織 – 溶湯処理なし – 100倍
- Figure 5.12: 合金1の微細組織 – 溶湯処理なし – 1000倍
- Figure 5.13: 合金1の微細組織 – Ar + O2 による溶湯処理 – Ø 72 mm インペラーセットアップ – 1000倍
- Figure 5.14: 合金1の微細組織 – Ar + O2 による溶湯処理 – Ø 185 mm インペラー – 100倍
- Figure 5.15: 合金1の微細組織 – Ar + O2 による溶湯処理 – Ø 185 mm インペラー – 1000倍
- Figure 5.16: パーマネント金型鋳造合金2の機械的特性
- Figure 5.17: パーマネント金型鋳造合金2試験片のCT画像
- Figure 5.18: パーマネント金型鋳造合金2試験片の多孔質含有量
- Figure 5.19: パーマネント金型鋳造合金2の応力-ひずみ曲線、「のこぎり歯状」挙動を示す
- Figure 5.20: ダイカスト合金2試験片の破壊点の分布
- Figure 5.21: 合金2の機械的特性 - 鋳造プロセスの比較
- Figure 5.22: ダイカスト合金2の応力-ひずみ曲線、パーマネント金型鋳造試験片と同様の「のこぎり歯状」挙動を示す
- Figure 5.23: 合金2の微細組織 – パーマネント金型鋳造 – 100倍
- Figure 5.24: 合金2の微細組織 – パーマネント金型鋳造 – 500倍
- Figure 5.25: 合金2の微細組織 – HPDC – 100倍
- Figure 5.26: パーマネント金型鋳造合金3の機械的特性
- Figure 5.27: パーマネント金型鋳造合金3のCT画像
- Figure 5.28: パーマネント金型鋳造合金3試験片の多孔質含有量
- Figure 5.29: ダイカスト合金3試験片のX線画像、中央の2つのサンプル内の熱間割れを示す
- Figure 5.30: ダイカスト合金3の機械的特性
- Figure 5.31: パーマネント金型とダイカスト合金3の降伏挙動の比較
- Figure 5.32: 合金3の微細組織 – パーマネント金型鋳造 – 100倍
- Figure 5.33: 合金3の微細組織 – パーマネント金型鋳造 – 1000倍
- Figure 5.34: 合金3の微細組織 – HPDC – 100倍
- Figure 5.35: パーマネント金型鋳造合金4の機械的特性
- Figure 5.36: 熱処理なしのHPDC合金4の機械的特性
- Figure 5.37: パーマネント金型とダイカスト合金4の降伏挙動の比較
- Figure 5.38: HT1後のダイカスト合金4の機械的特性
- Figure 5.39: HT2後のダイカスト合金4の機械的特性
- Figure 5.40: 合金4の微細組織 – パーマネント金型鋳造 – 100倍
- Figure 5.41: 合金4の微細組織 - パーマネント金型鋳造 - 1000倍
- Figure 5.42: 合金4の微細組織 – HPDC – 熱処理なし – 100倍
- Figure 5.43: 合金4の微細組織 – HPDC – 熱処理なし – 500倍
- Figure 5.44: 合金4の微細組織 – HPDC – HT1 – 100倍
- Figure 5.45: 合金4の微細組織 - HPDC - HT2 - 100倍
7. 結論:
主な調査結果の概要:
実験は、異なる条件とパラメータで実施されました。すべての場合において、溶湯処理により溶湯表面に発泡スラグが生成されました。スラグは、比重が小さく、おそらく内部に閉じ込められたガスが原因で浮遊する酸化アルミニウムの凝集に由来します。ArおよびAr + O2による溶湯処理後の合金1で得られた機械的特性に有意な差は見られません。Ar + O2による処理中に鋳造された試験片の伸びの正の進化が観察されましたが、得られた値はArで処理された同じ合金の値と同等でした。金型サイズ、温度、多孔質含有量と分布の影響が合金の機械的特性に見られました。合金1の微細組織は、結晶粒界および結晶粒内の丸い領域に凝固したAl/Al3Fe共晶相の存在によって特徴付けられます。溶湯処理なしの合金、Arで処理した合金、Ar + O2で処理した合金の間で顕著な変化は見られませんでした。インペラーサイズは微細組織に影響を与えませんでした。合金2の試験では、Cu添加の強化効果が合金元素として示されました。UTSとYSは伸びを犠牲にして向上しました。パーマネント金型鋳造試験片のUTSとAの測定値はEN AC-21100合金の仕様と一致していますが、YSは低くなっています。ダイカスト試験片は、より高い強度と伸びを示しますが、多くの欠陥、特に実際の強度に強く影響する熱間割れの存在に悩まされています。パーマネント金型とダイカスト合金2の両方で「のこぎり歯状」の応力-ひずみ曲線が示されています。CuAl2相の損傷メカニズムが原因である可能性があります。合金2の微細組織は樹枝状であり、CuAl2はAl/Al3Fe相とともに樹枝状晶間領域で凝固します。HPDCは、冷却速度が速いため、より微細な微細組織を持っています。合金3は、合金2と比較して強度が高くなりましたが、伸びは低くなりました。MnとMgの添加とCu含有量の増加は、歩留まり応力を大幅に増加させました。欠陥は値の変動性に影響を与えました。組成の低い均質性が、このデータの変動性の原因として提案されています。パーマネント金型鋳造合金3の機械的特性をEN AC-21000合金と比較しました。UTSと伸びは指定された範囲に達しましたが、YSはわずかに低くなりました。ダイカスト合金3は、データに同じ変動性を示しています。その機械的特性は、欠陥含有量によって強く影響を受けます。合金3の降伏挙動は、鋳造プロセスによって異なります。ダイカスト試験片のみが明確な降伏点を示しています。合金3の微細組織は樹枝状であり、CuAl2相とMg相がFeとMnが豊富な相と交互になっています。ダイカスト微細組織は明らかに微細で等軸晶です。パーマネント金型鋳造合金4は、合金3と同様の機械的特性を示しています。熱処理なしのダイカスト試験片は、より微細な微細組織のおかげで、より高いUTSと伸びを示しましたが、YSはわずかに低くなりました。合金3と同様に、鋳造プロセス間の降伏挙動の違いが検出されました。熱処理された合金4は、自然時効プロセスのおかげで機械的特性が大幅に向上しました。自然時効期間後の溶体化熱処理とUTSおよびYSの両方で、AA 206.0 T4合金の指定値に達しました。HT1とHT2の間で機械的特性に差は見られませんでした。伸びは最適な値よりも常に低いですが、指定された最小値よりも高くなっています。説明は、試験片の欠陥性に見られます。合金4の微細組織は、他の合金では検出されなかった相の存在を明らかにしました。これは、合金3ですでに示されている他の相に加えて、Znの添加によるものと考えられます。熱処理された微細組織では、CuAl2とMgはもはや検出できません。一般に、強化効果は、調査した溶湯処理に起因するものではありません。明らかに、処理中に生成されたすべての酸化物は溶湯表面に残っています。試験したAl-Cu合金の機械的特性は影響を受けず、熱間割れ感受性は改善されませんでした。Al2O3粒子は顕微鏡写真では確認されませんでした。
研究の学術的意義:
本研究は、アルミニウム合金中にAl2O3粒子をその場生成するための革新的な溶湯処理の実現可能性に関する包括的な調査を提供します。調査結果は、処理がスラグ形成によって証明されるように酸化物を効果的に生成する一方で、試験されたパラメータを使用してアルミニウムマトリックス内にAl2O3強化材の所望の分散を達成しないことを示しています。本研究は、溶湯処理の限界と、ダイカストアルミニウム合金、特にAl-Cuベース合金における処理パラメータ、微細組織、および機械的特性間の複雑な相互作用の理解に貢献します。従来のダイカストプロセスにおけるその場強化戦略の実施における課題を浮き彫りにしています。
実用的な意義:
結果は、調査された溶湯処理が、現在の形態では、Al2O3粒子強化を介してダイカストアルミニウム合金の機械的特性を向上させるための実用的に実行可能な方法ではないことを示唆しています。本研究は、特にAl-Cu合金において、多孔質と熱間割れを管理するために、金型温度や冷却速度などの鋳造パラメータを最適化することの重要性を強調しています。調査結果は、熱処理、特にT4処理が、HPDC Al-Cu合金(合金4など)の強度を大幅に向上させ、AA 206.0 T4などの確立された高性能合金に匹敵するものにすることの有効性を裏付けています。
研究の限界と今後の研究分野:
主な限界は、酸化物形成にもかかわらず、アルミニウムマトリックス内でのその場Al2O3粒子分散を達成できなかったことです。今後の研究では、溶湯処理プロセスの修正を検討する必要があります。
- ガス注入パラメータの最適化: Al2O3の核生成と分散を促進するために、ガス混合比、流量、および注入方法を変化させます。
- インペラー設計と攪拌条件: スラグ形成と溶湯表面の破壊を最小限に抑えながら、乱流と酸化物粒子の分散を向上させるために、インペラーの形状と攪拌速度を改良します。
- 代替インサイチュ反応: Al2O3の生成と分散をより効果的に促進する可能性のある、異なる反応性ガス混合物または前駆体を調査します。
- ナノ粒子安定化: 溶湯処理および鋳造中のAl2O3ナノ粒子の凝集を安定化および防止する方法を検討します。
- プロセスのスケーラビリティと費用対効果: 強化されたダイカスト部品の大量生産のために、工業的にスケーラブルで経済的に実行可能な溶湯処理方法の開発に焦点を当てます。
- 熱間割れに関するさらなる調査: Al-Cu合金の熱間割れメカニズムを理解し、HPDCにおけるその緩和のための効果的な戦略を開発するために、さらなる研究が必要です。おそらく、微細組織制御または合金改質を通じて。
8. 参考文献:
- [1] K.U. Kainer, Basics of Metal Matrix Composites
- [2] C. Borgonovo, Aluminum Nano-composites for Elevated Temperature Applications, Worcester Polytechnic Institute, Worcester, USA
- [3] C. Borgonovo, Makhlouf M. Makhlouf, Synthesis of die-castable nano-particle reinforced aluminium matrix composite materials by in-situ gas-liquid reactions, Worcester Polytechnic Institute, Worcester, USA
- [4] A.A. Hamid, P.K. Ghosh, S.C. Jain, S. Ray, Processing, Microstructure, and Mechanical Properties of Cast In-Situ Al(Mg,Ti)-Al2O3(TiO2) Composite, Metallurgical and Materials Transactions A, vol. 37A, Feb. 2006
- [5] North American Die Casting Association - www.diecasting.org
- [6] CustomPartNet – www.custompartnet.com/wu/die-casting#equipment
- [7] ASM Handbook, ASM International, vol. 2
- [8] UC RUSAL – www.aluminiumleader.com/en/around/transport
- [9] I. J. Polmear, Aluminium Alloys - A century of age hardening, Materials Forum Vol. 28 – 2004
- [10] J.R. Greer, Handout AlCu, www.jrgreer.caltech.edu
- [11] Prof. F. Bonollo, Leghe di alluminio: approfondimenti metallurgici – Trattamenti termici, Dipartimento di Tecnica e Gestione dei Sistemi Industriali - Università di Padova, Vicenza, Italy
- [12] Alcan AA206 Primary Foundry Alloys, Alcan Primary Products Corporation Inc.
- [13] S. Li, Hot Tearing in Cast Aluminium Alloys: Measures and Effects of Process Variables, Worcester Polytechnic Institute, Worcester, USA
- [14] S. Bao, K. Tang, A. Kvithyld, M. Tangstad, Wettability of Aluminum on Alumina, Metallurgical and Materials Transactions B, vol. 42B, Dec. 2011
- [15] E.G. Fuchs, A Roósz, TTD-Diagrams for the Homogenization of As-Cast Structures, Z. Metallkunde, Vol. 63, pp. 211-214 (1972)
- [16] Prof. F. Bonollo, Prodotti Metallurgici Innovativi e Multifunzionali, Dipartimento di Tecnica e Gestione dei Sistemi Industriali - Università di Padova, Vicenza, Italy
- [17] www.matweb.com
- [18] www.keytometals.com
- [19] www.aviometal.com
- [20] www.wikipedia.org
9. 著作権:
- この資料は、"Alberto Dal Maso"氏の論文:「INVESTIGATION ON THE EFFECTS OF INNOVATIVE MELT TREATMENTS ON MICROSTRUCTURE AND MECHANICAL BEHAVIOUR OF DIECAST AL ALLOYS」に基づいています。
- 論文ソース: [ドキュメントにDOIは記載されていません]
この資料は上記の論文を紹介するために作成されたものであり、商業目的での無断使用は禁止されています。
Copyright © 2025 CASTMAN. All rights reserved.